A Workflow to Repurpose Tree Forks
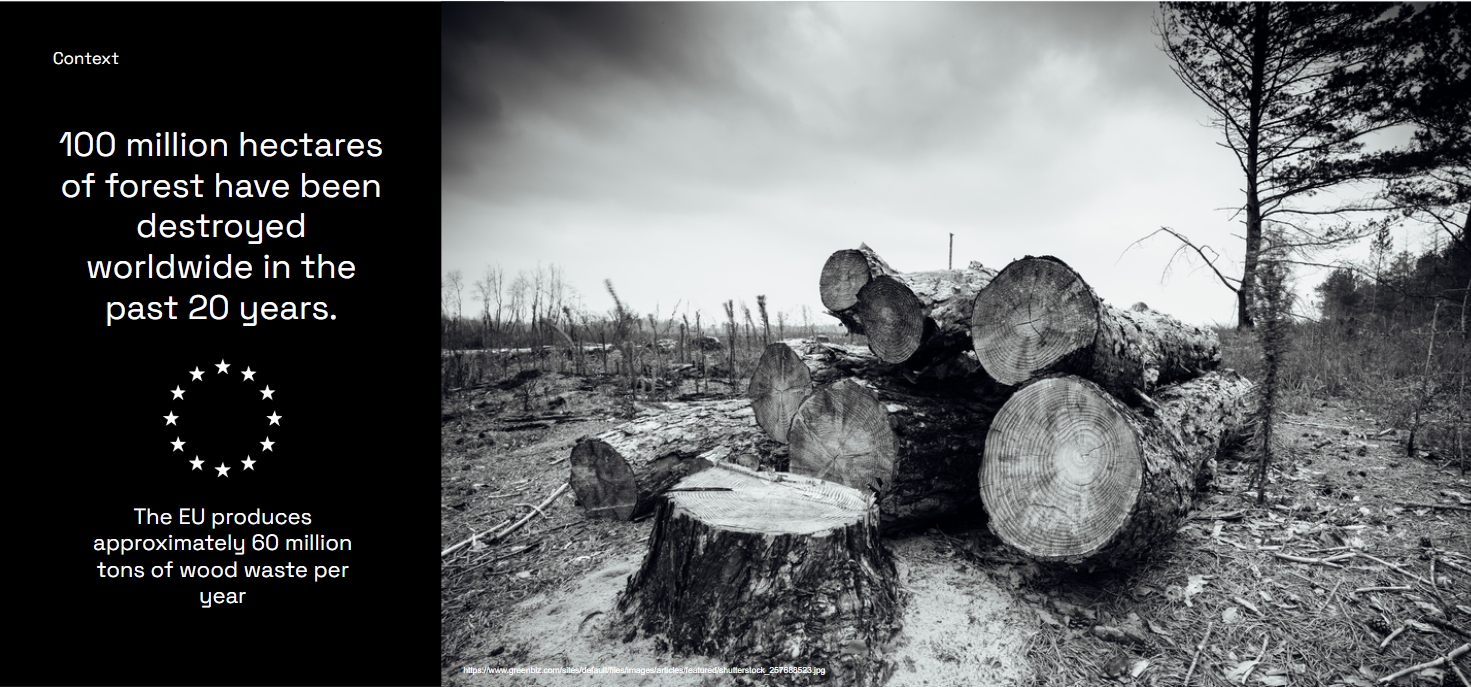
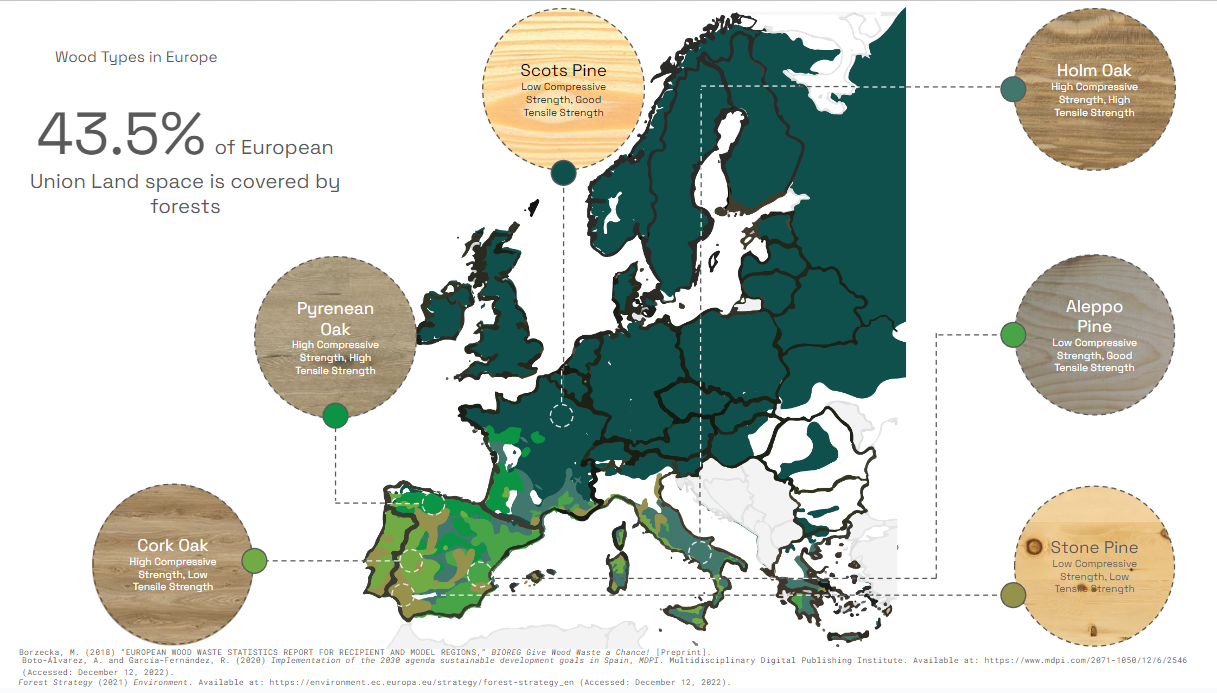
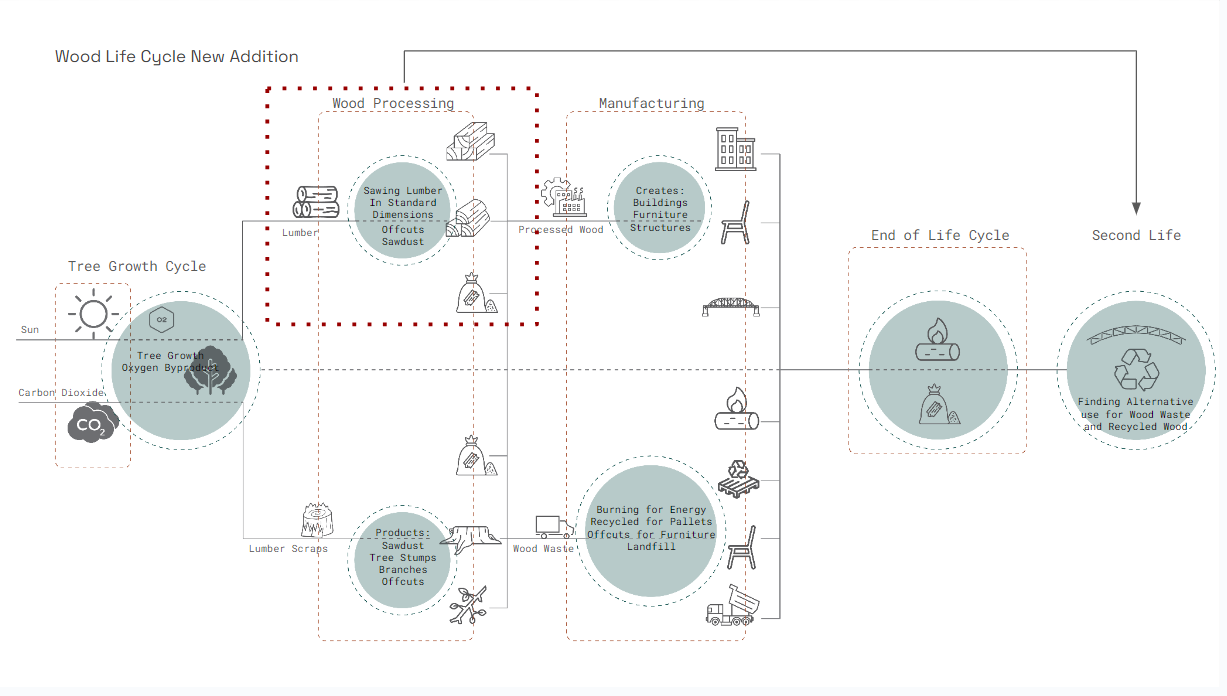
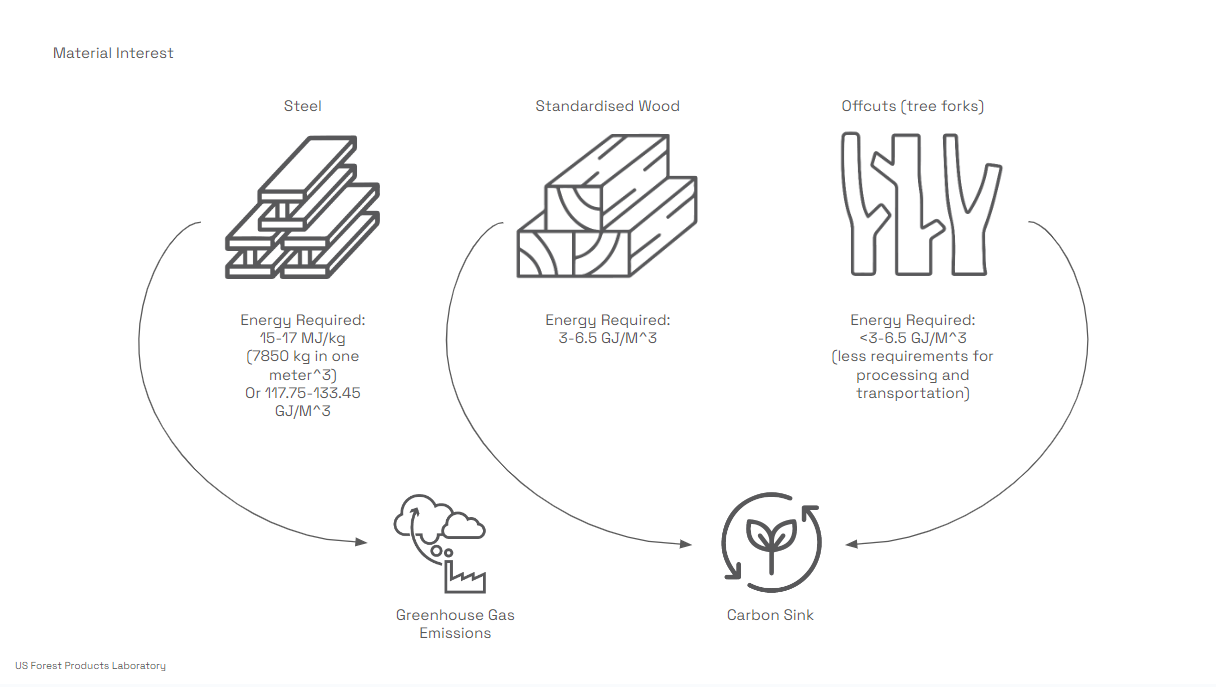
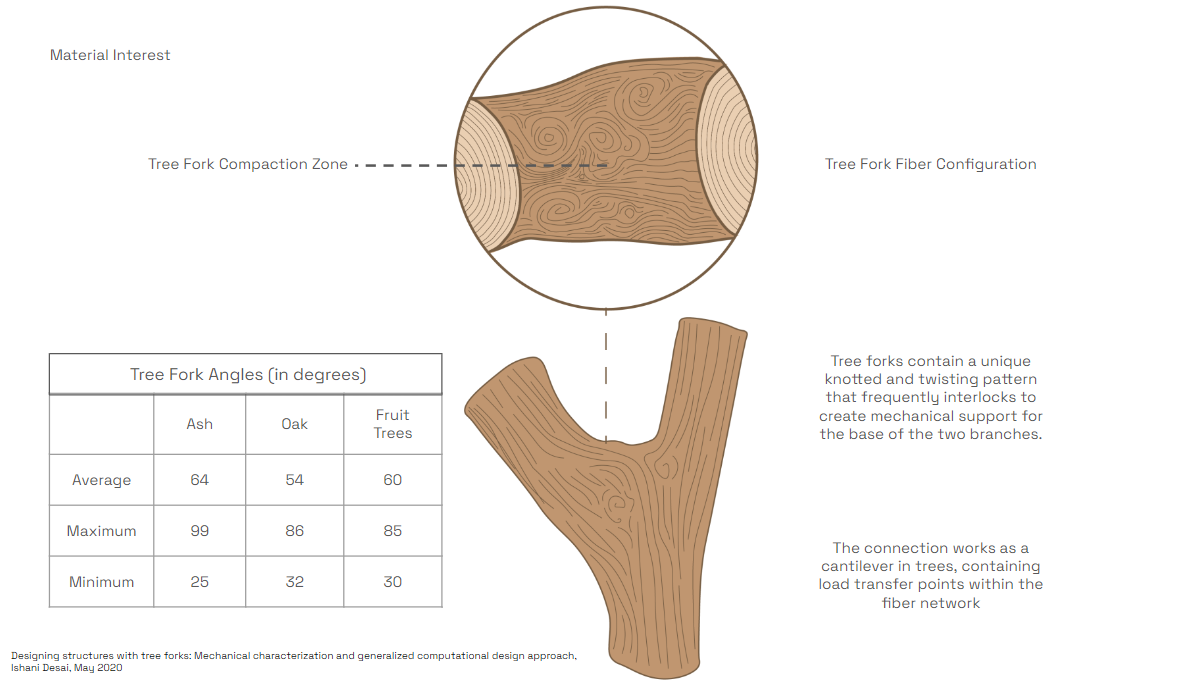
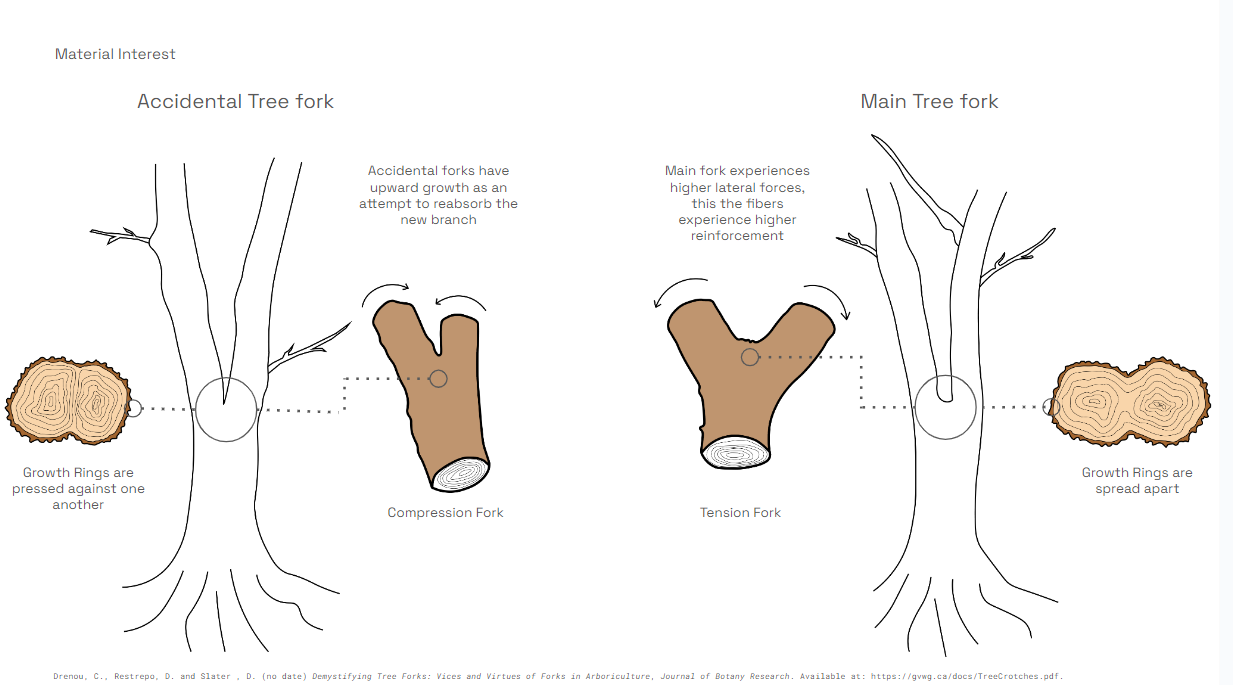
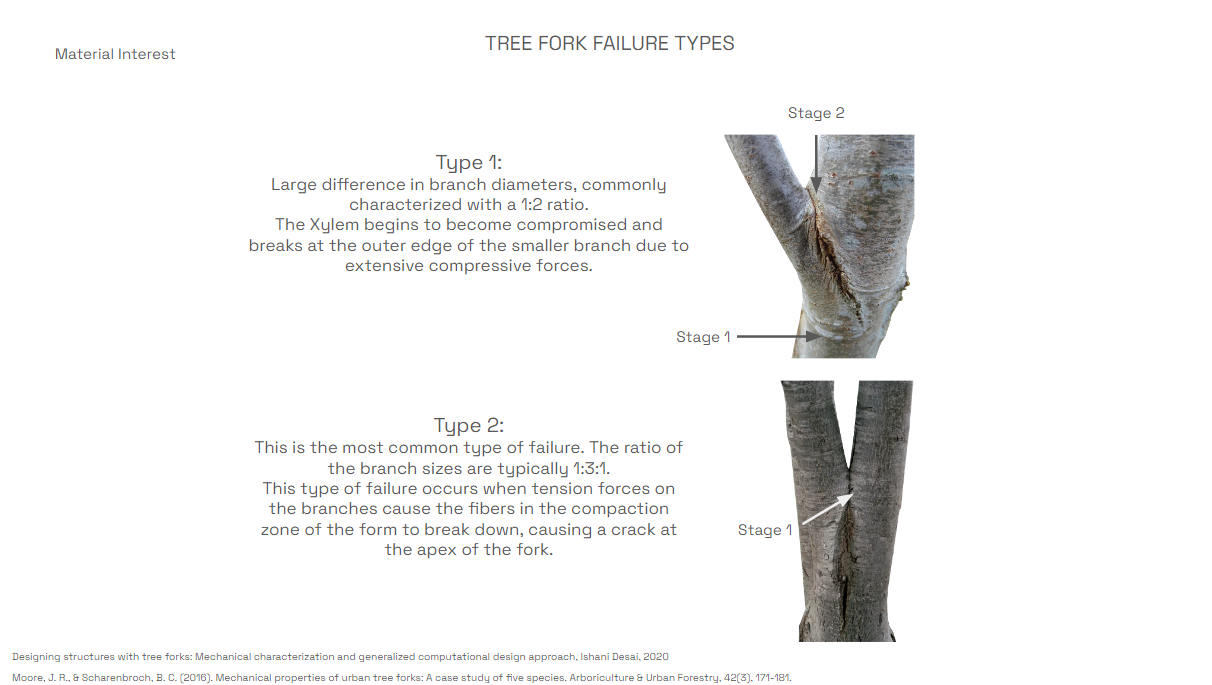
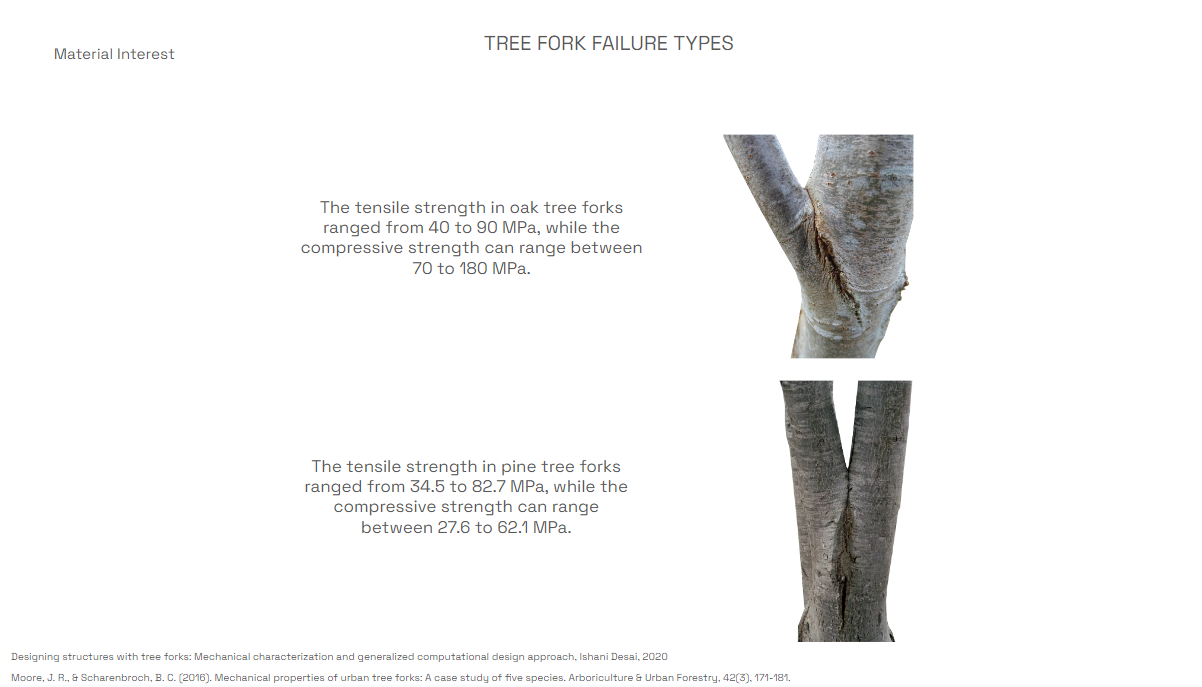
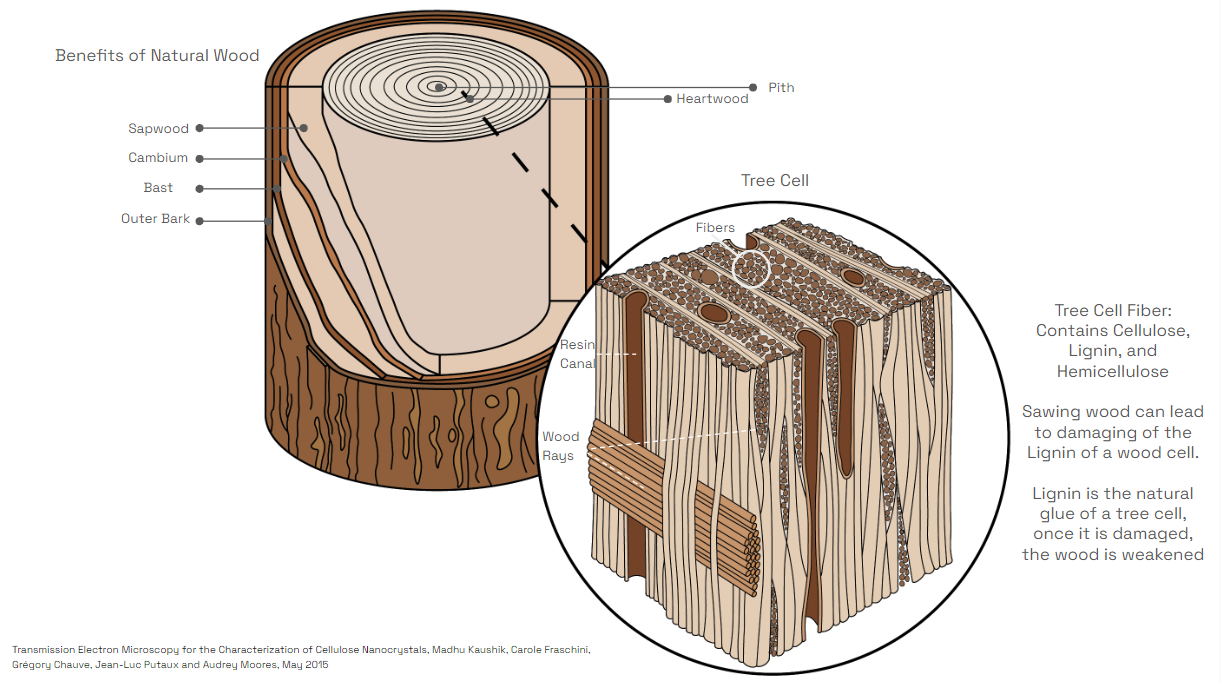
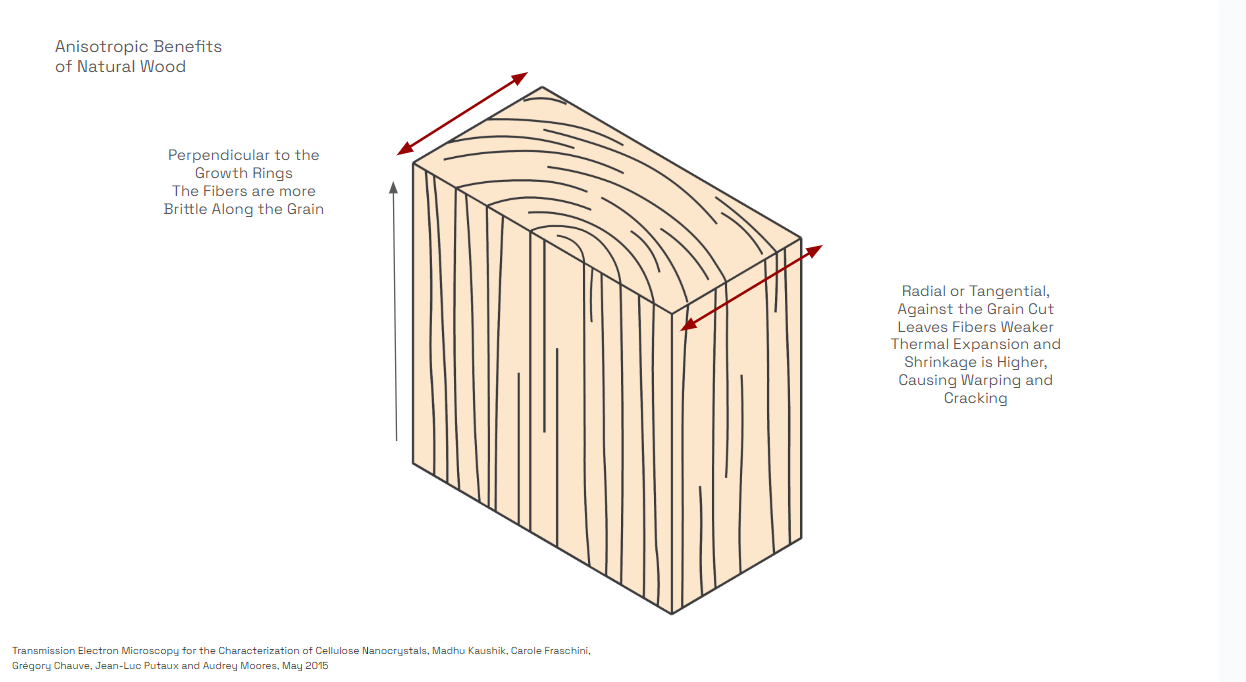
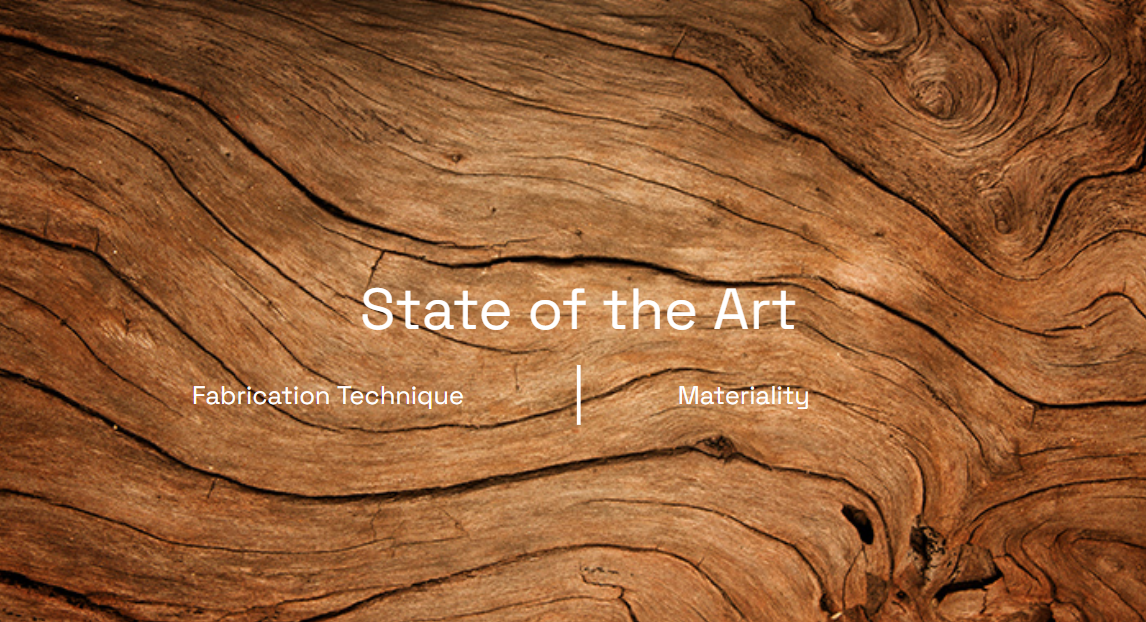
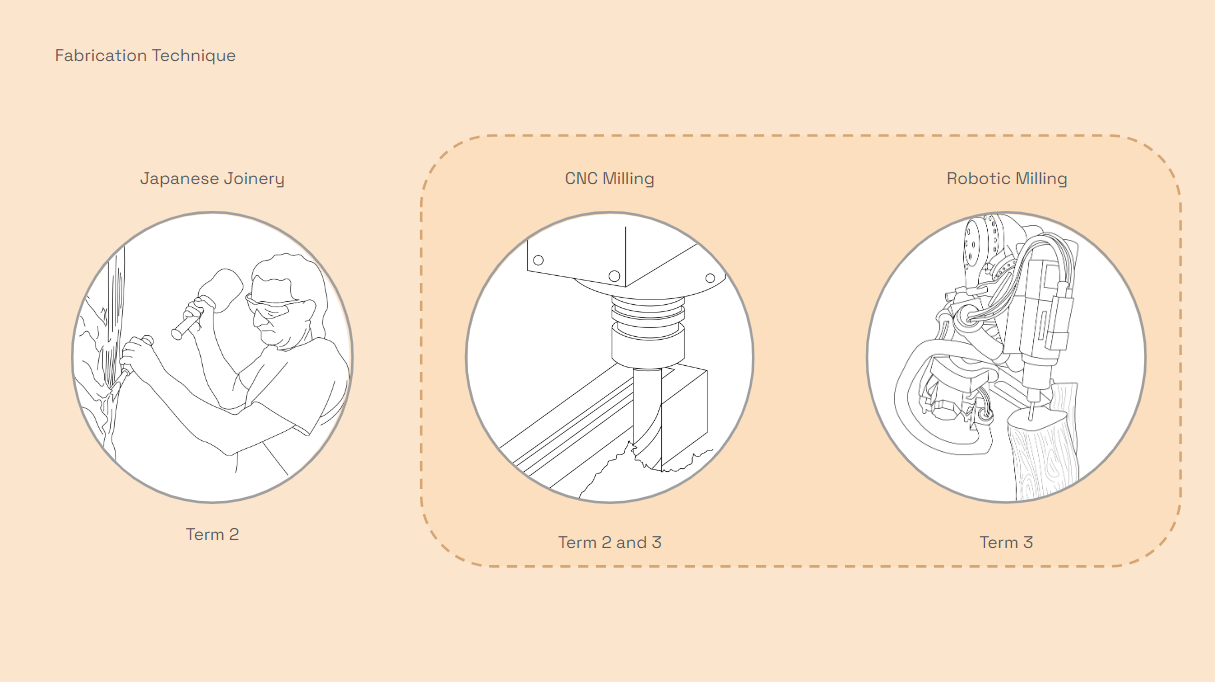
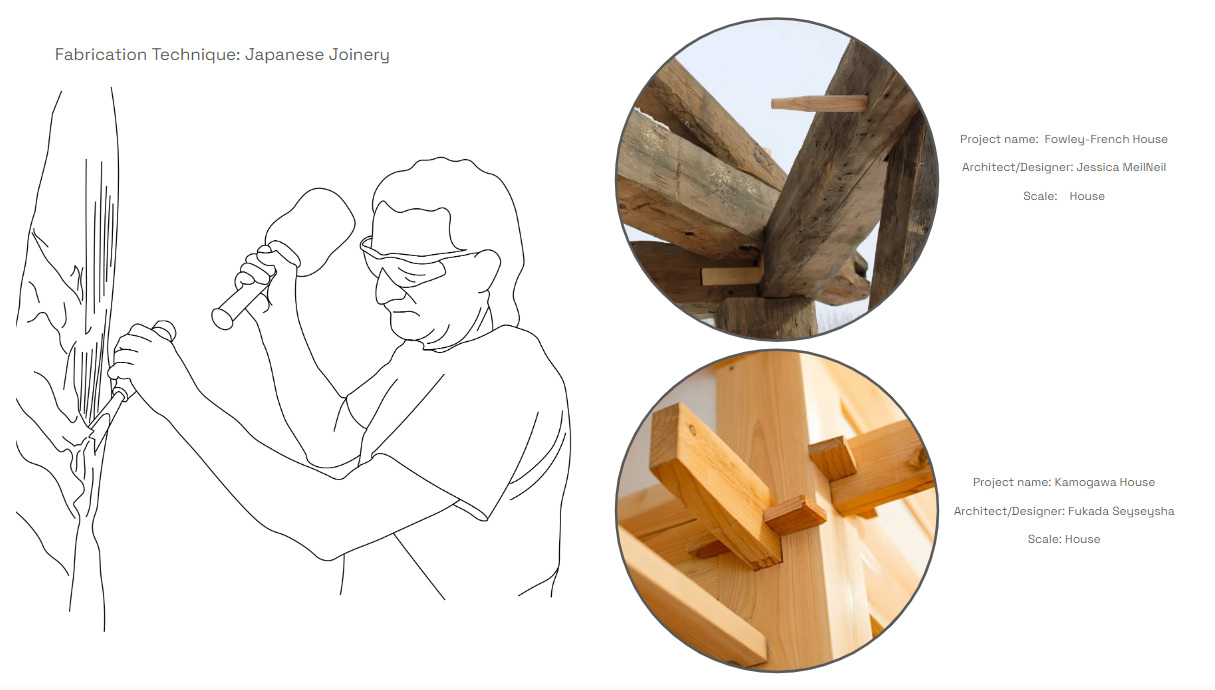
Hand fabrication or Japanese joineries have high customization and are very precise when done by a professional. This method’s drawbacks include the intense physical labor required and the amount of time it takes to master the craft.
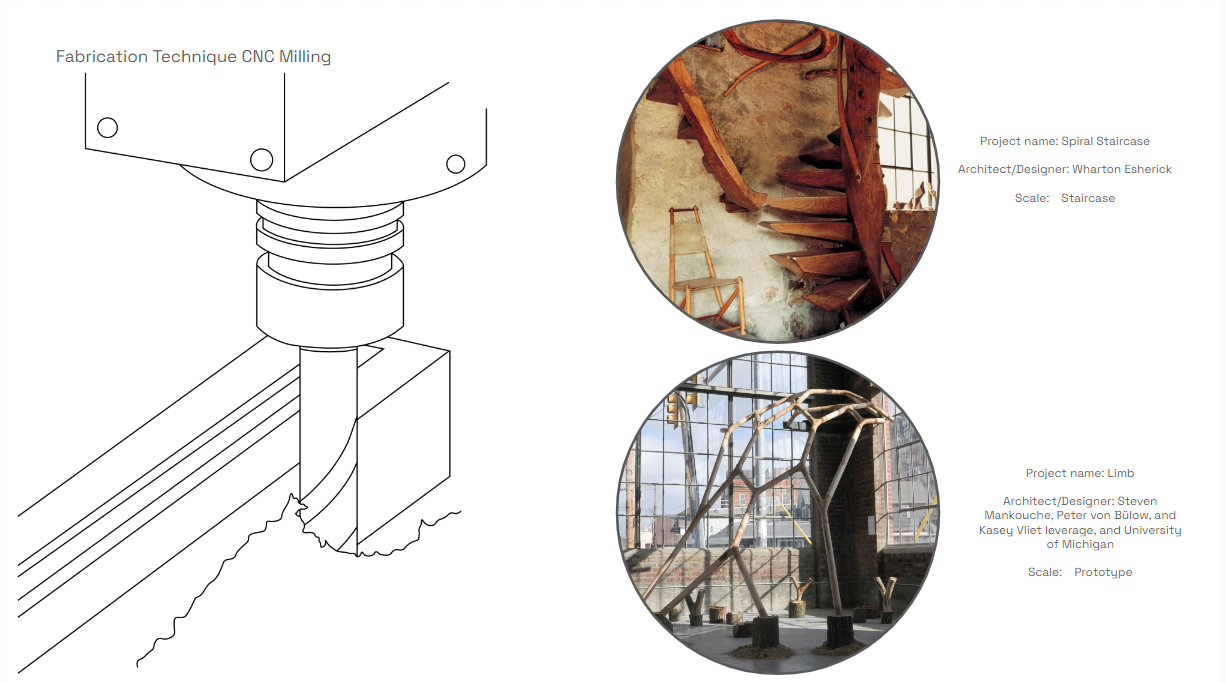
CNC Milling machines range from 3 to 5 axis and are a lot less manual effort than hand fabrication. They allow for good customization and standardization. It is ideal for a straight piece, but can be used on nonstandard wood as well.
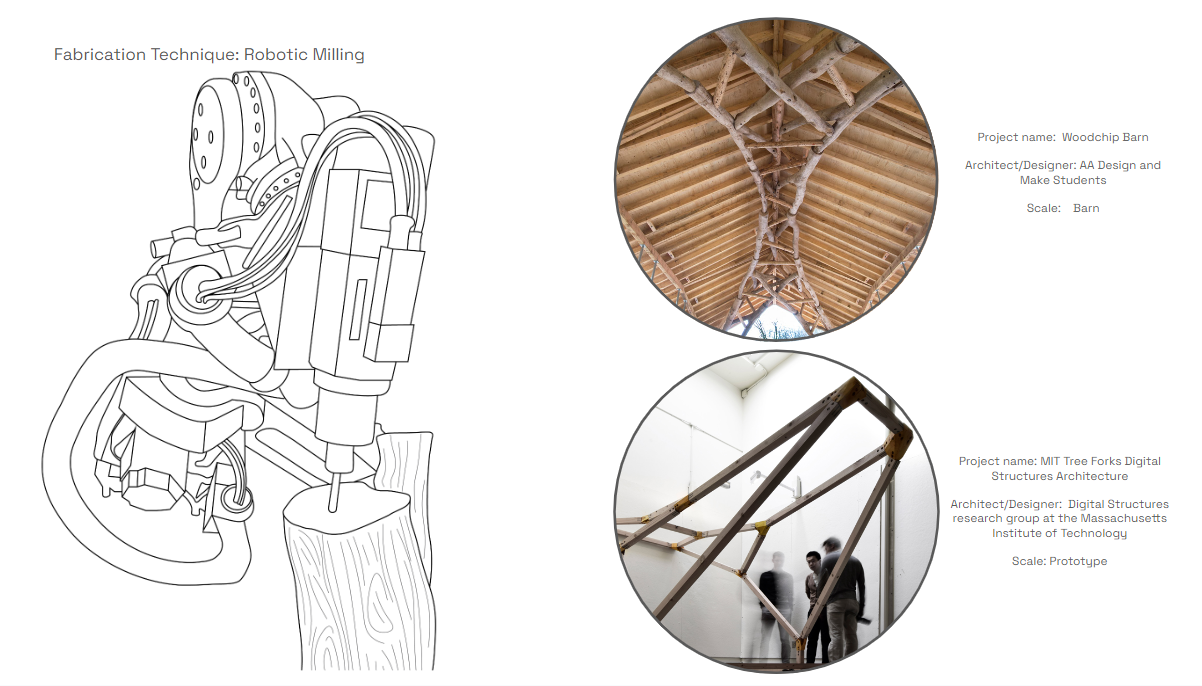
Robotic fabrication has high customizability and range of motion. It is ideal for hard to reach and non planar milling methods.
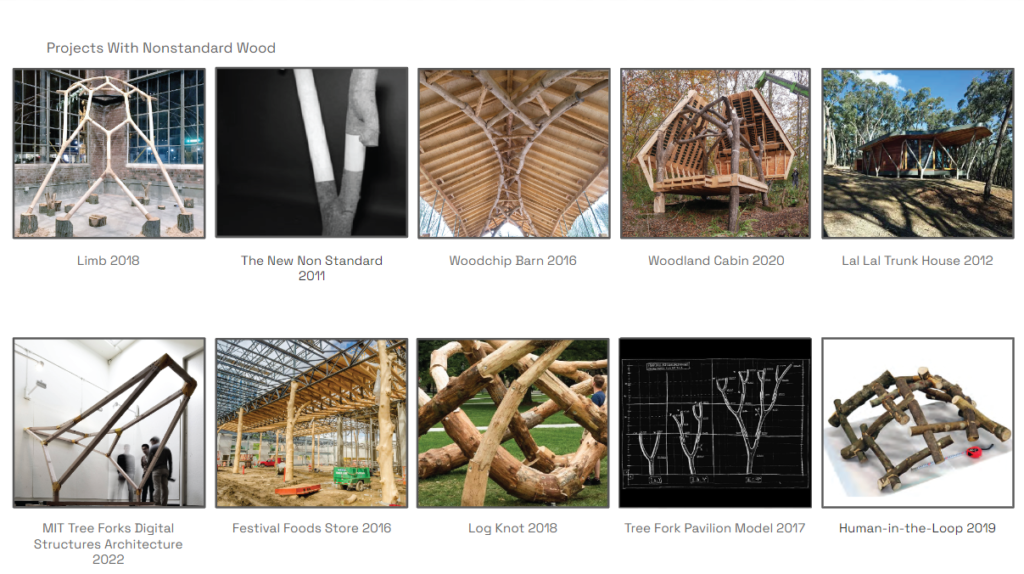
All of the research projects utilize nonstandard wood offcuts, with only four utilizing tree forks with all wood joineries.
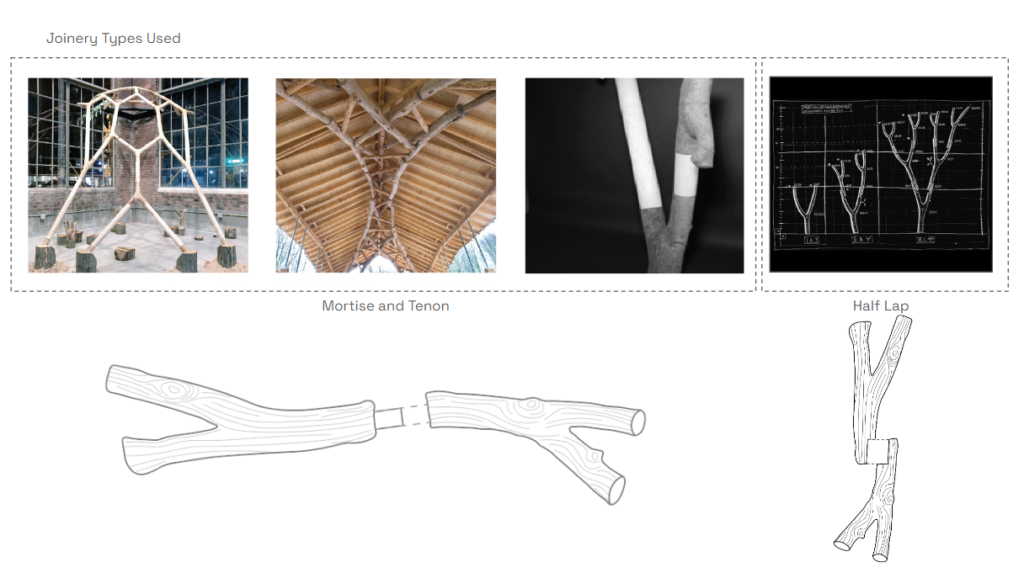
The main joineries explored in these state of art projects include mortise and tenon and half lap. None of the tree fork projects utilize more than one type of joinery connection.
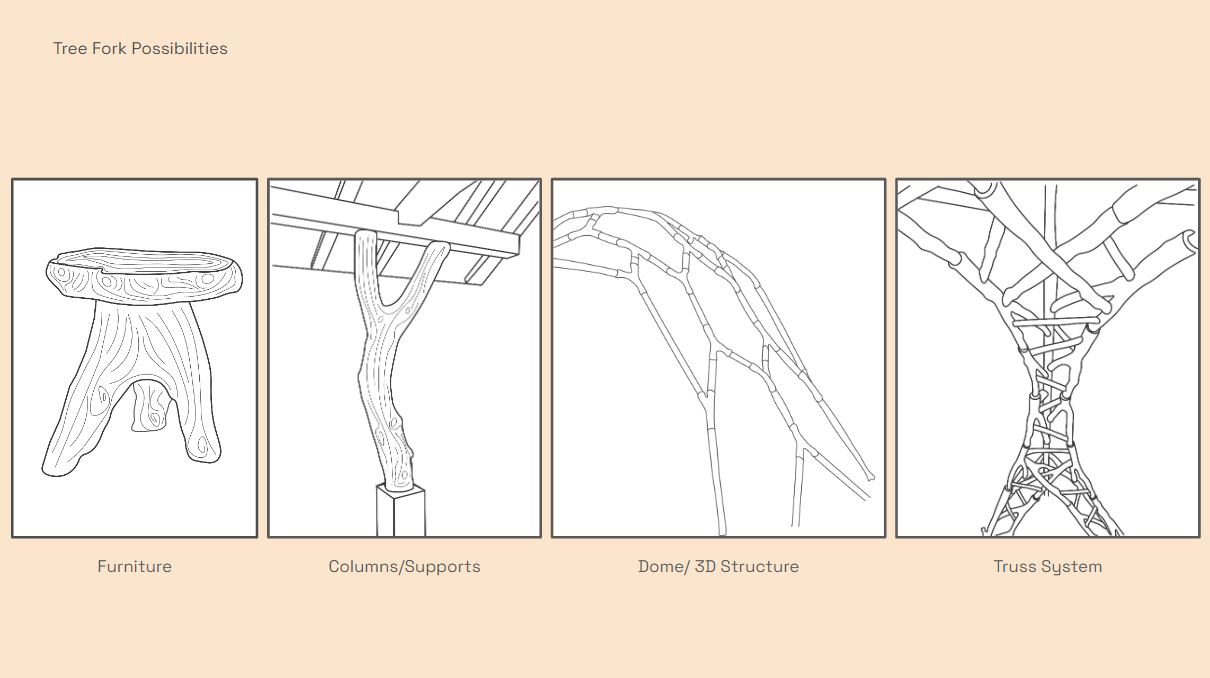
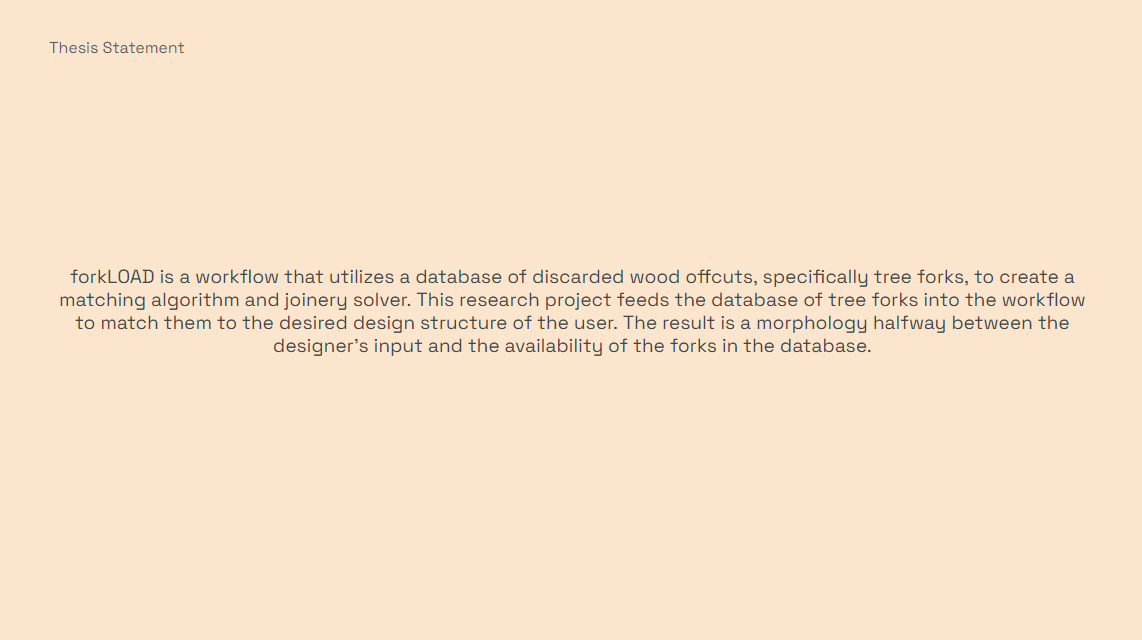
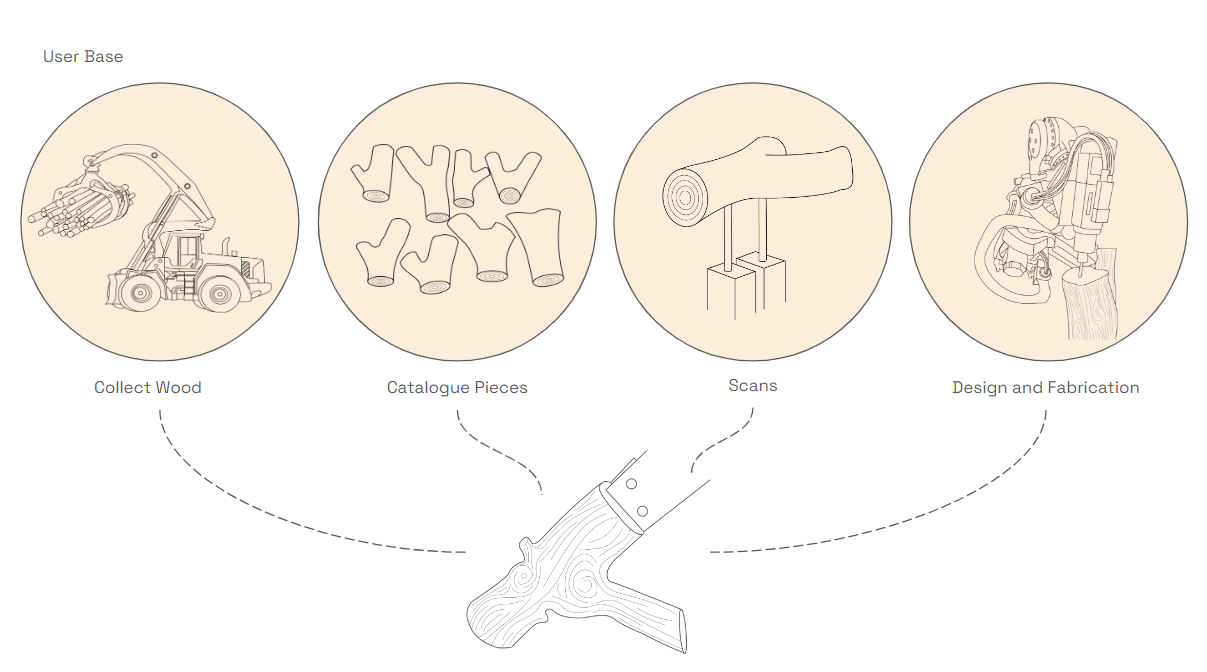
The User Base Works through the collection of wood to create a catalogue of pieces that are then scanned in order to be selected for the designs and fabrications of architects and designers.
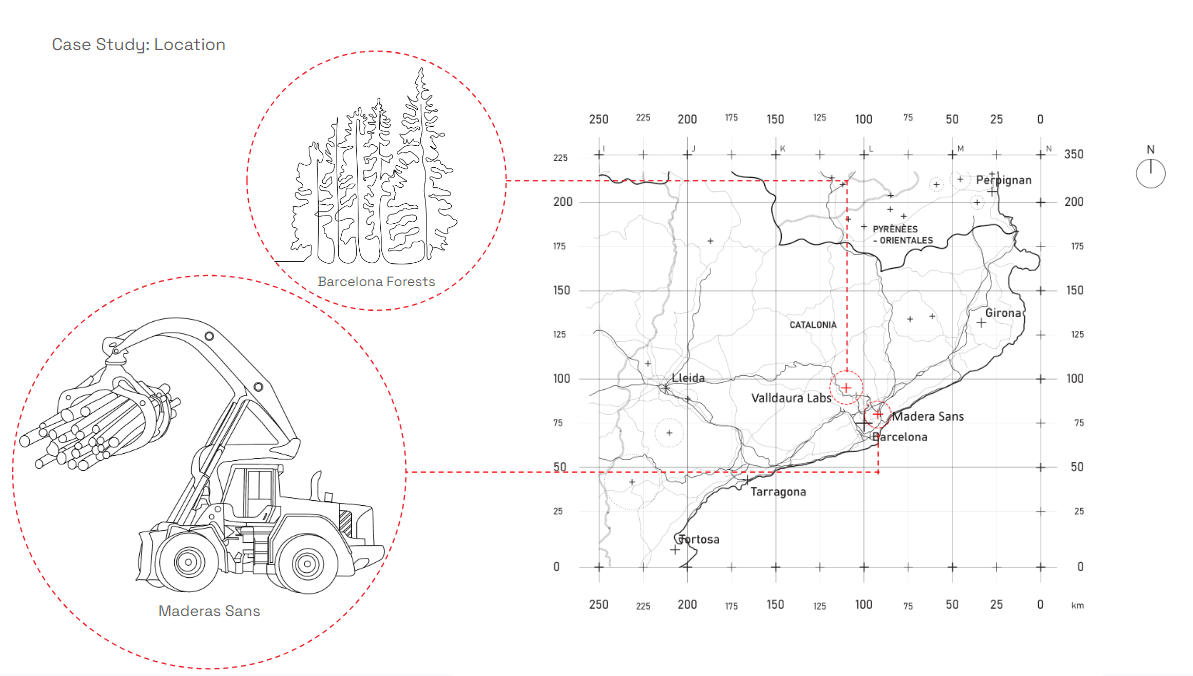
The location of our project is Madera Sans due to its proximity to Valldaura Labs.
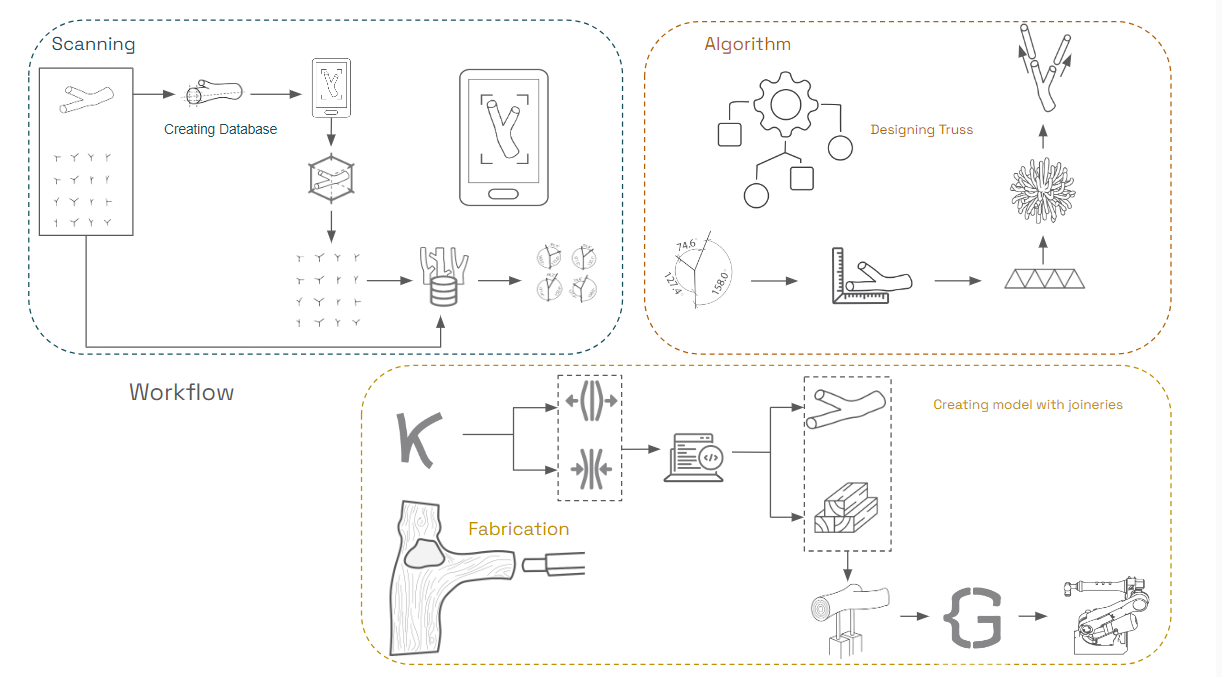
The Workflow is split into three separate parts.
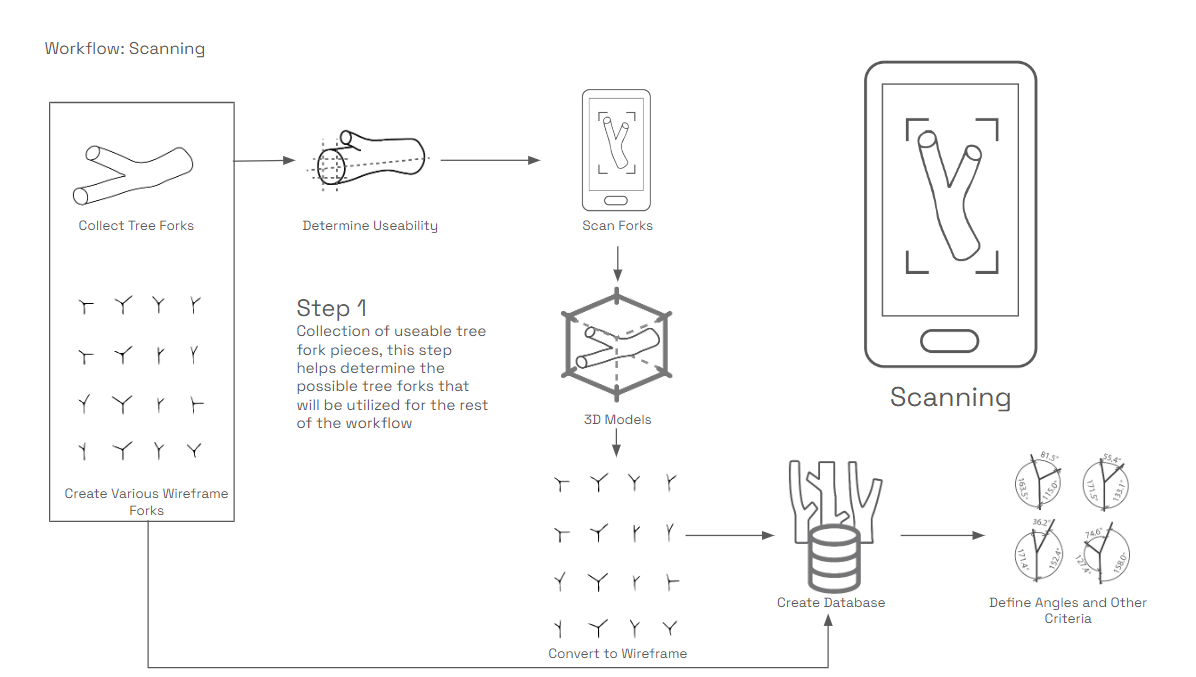
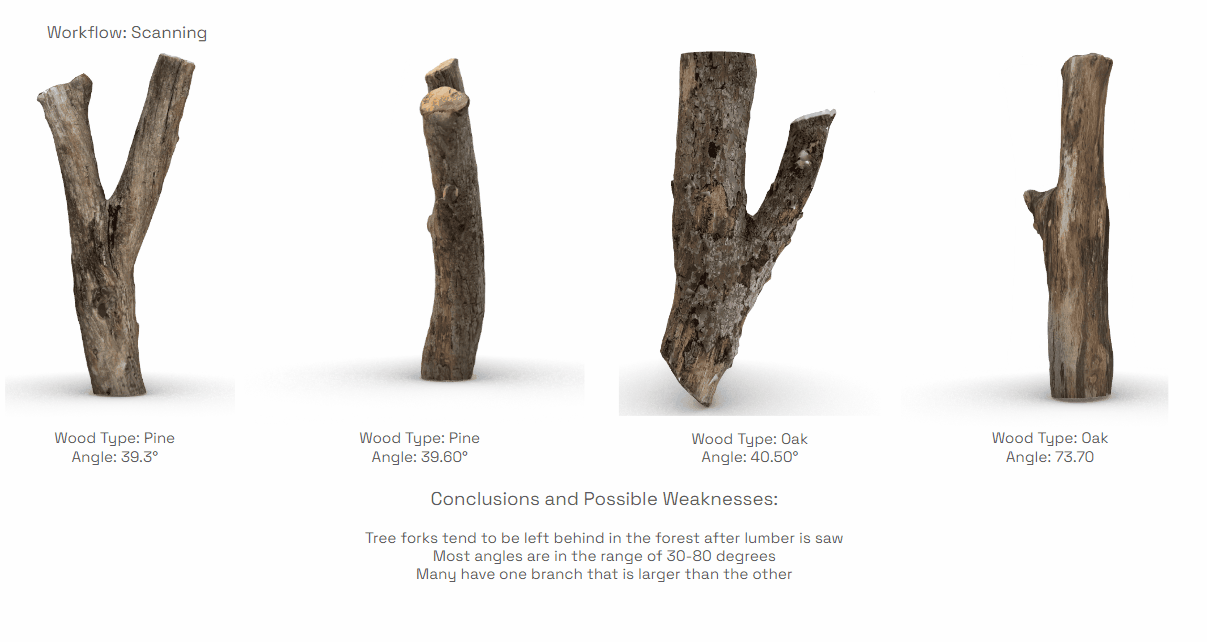
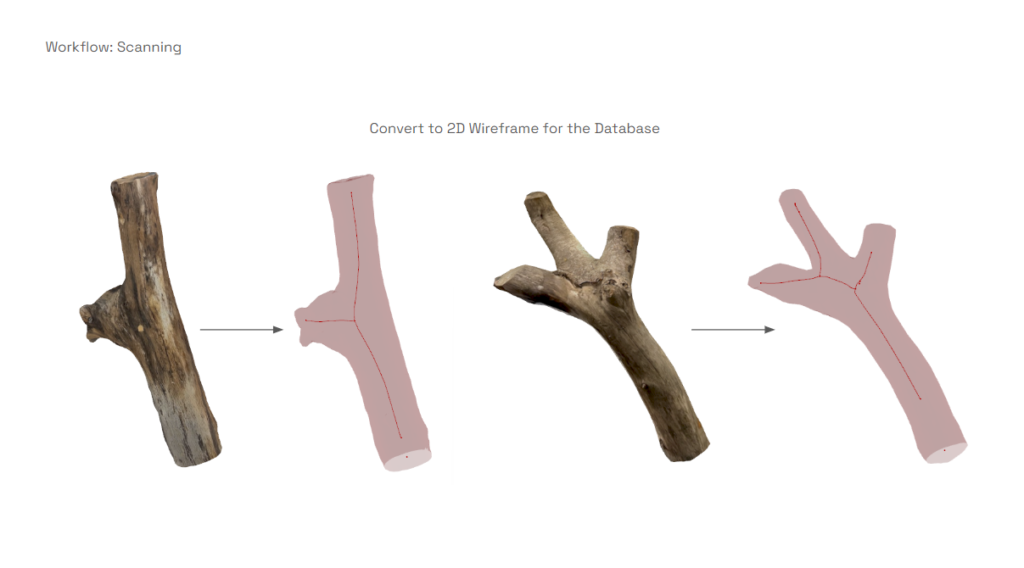
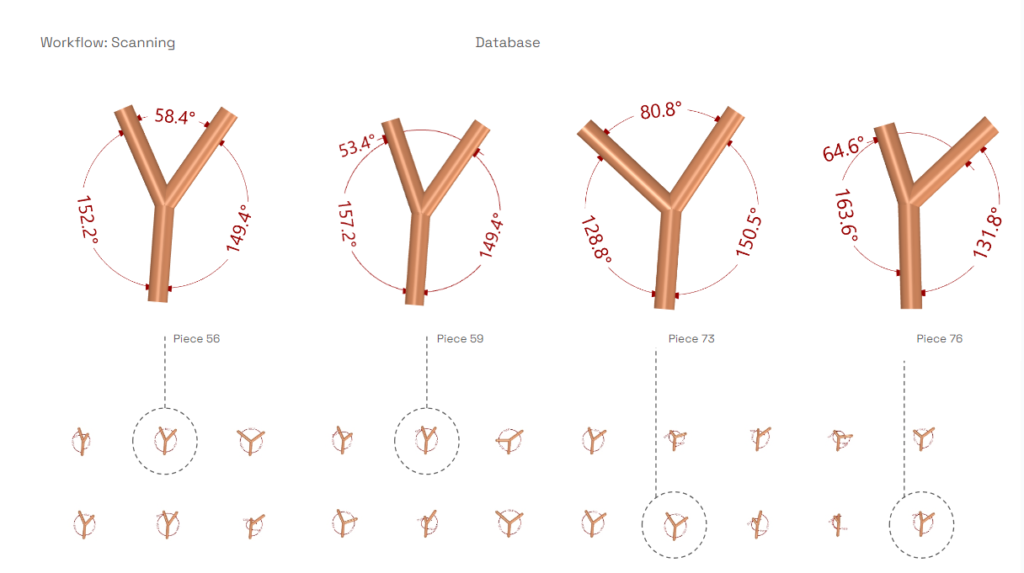
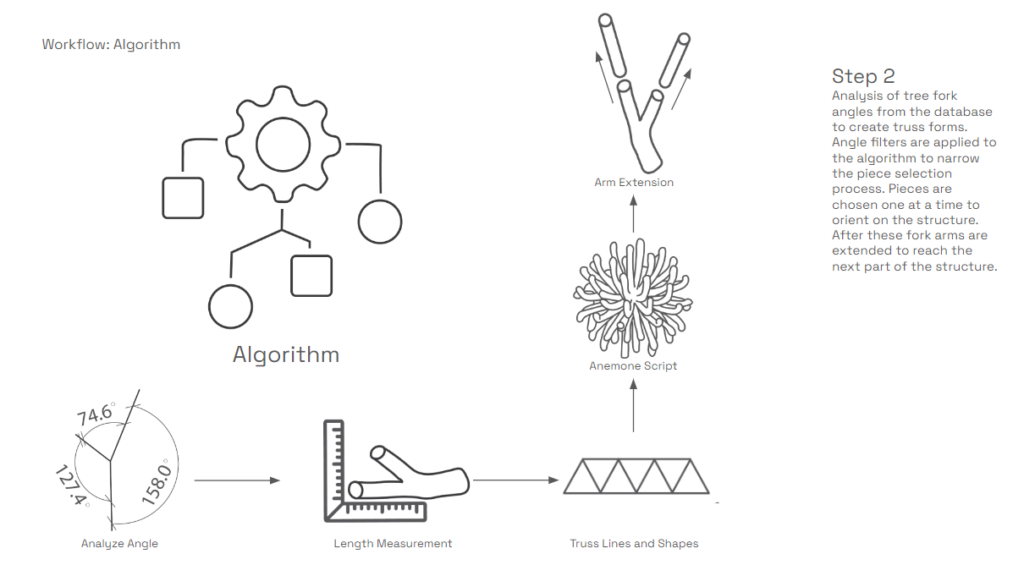
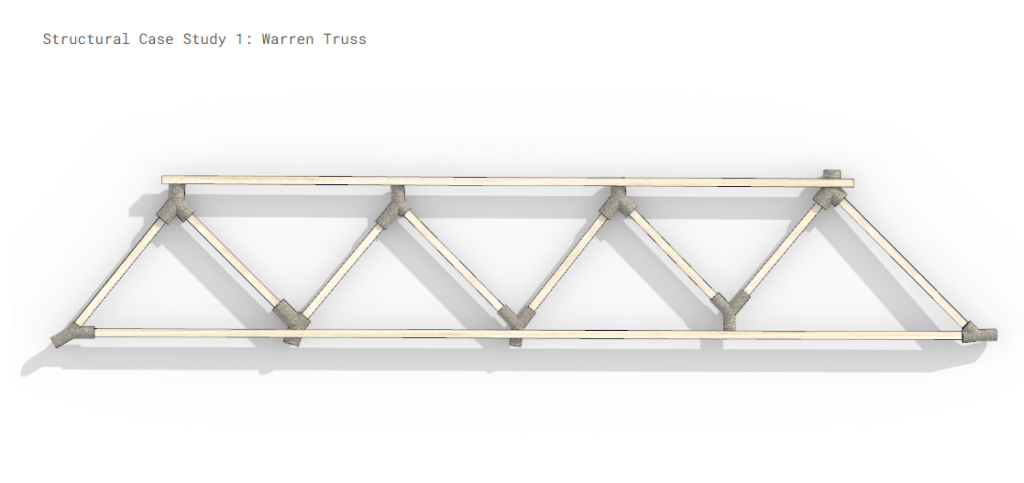
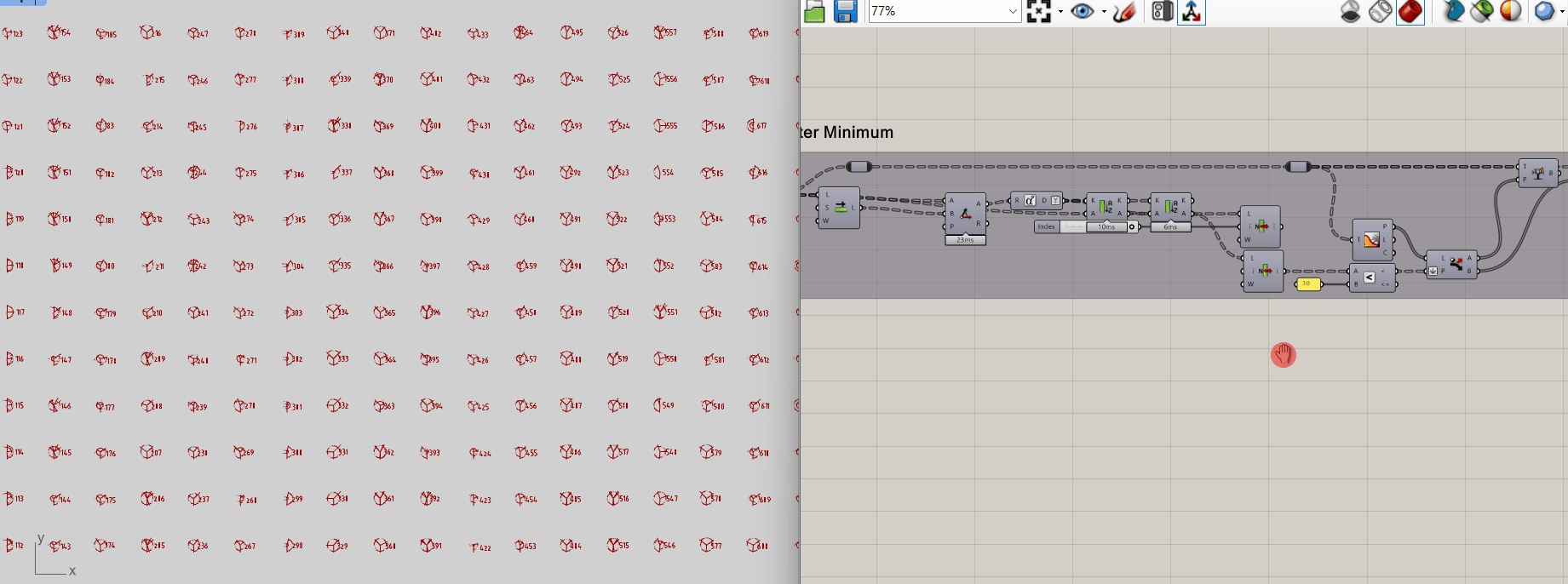
The grasshopper algorithm uses angle filters and length filters to select pieces to put in an anemone script for orientation matching.
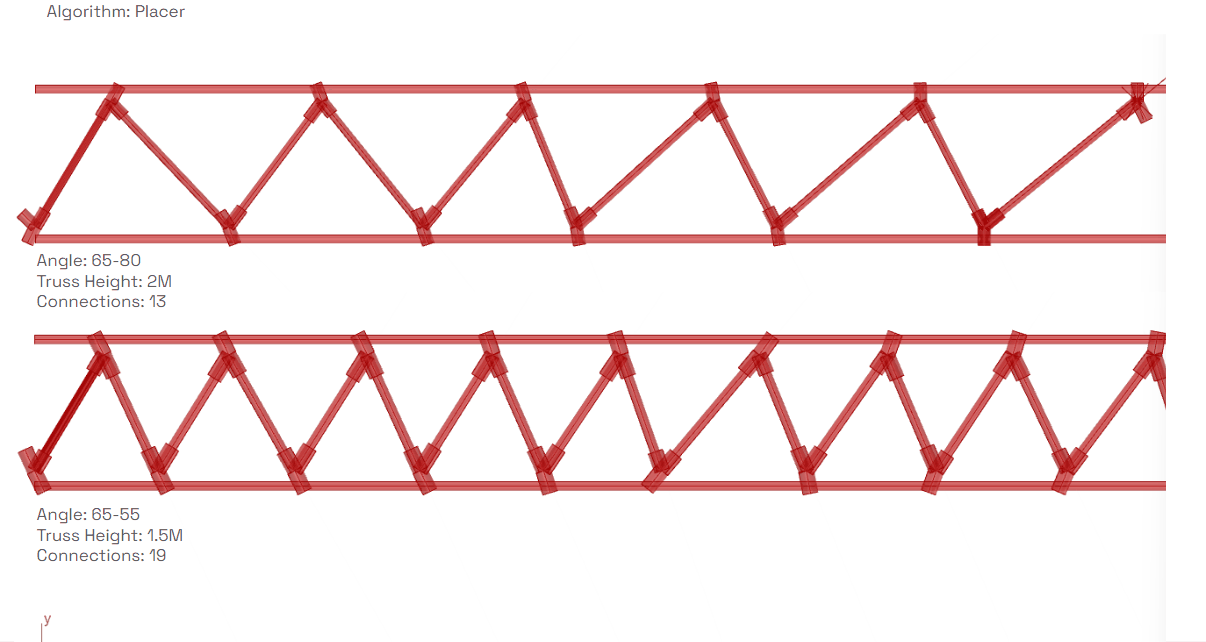
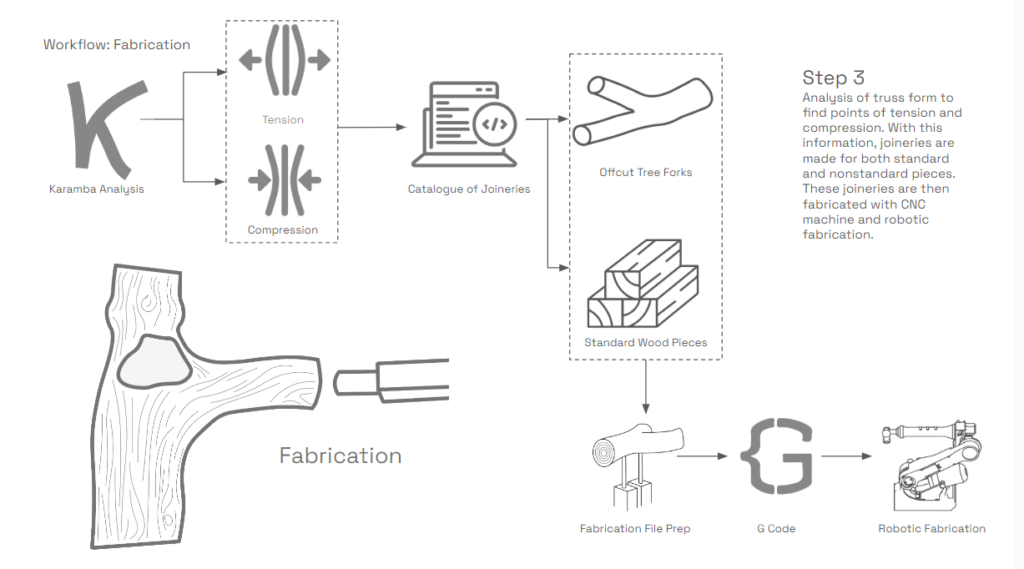
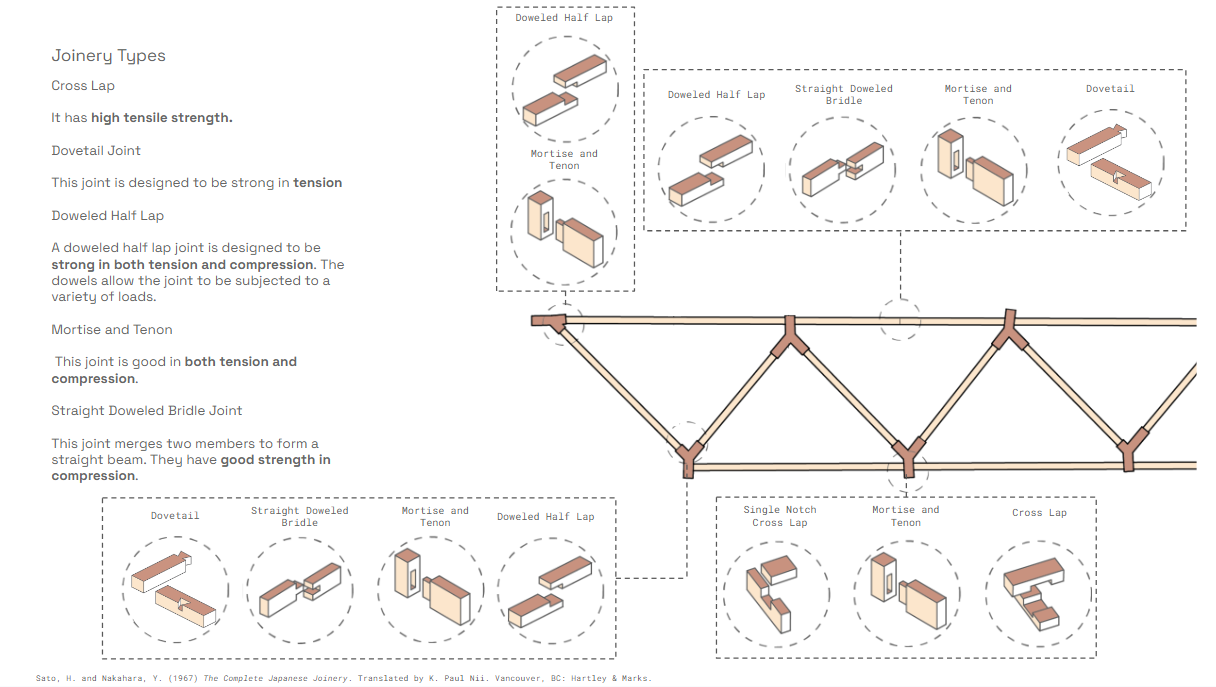

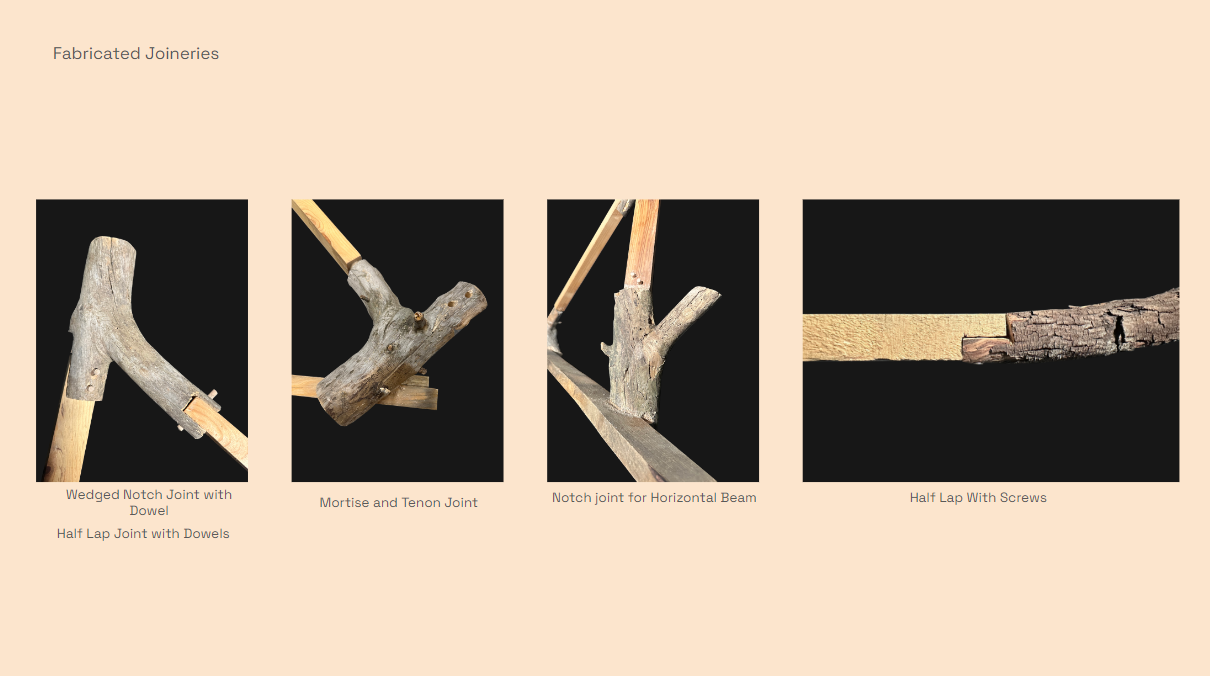
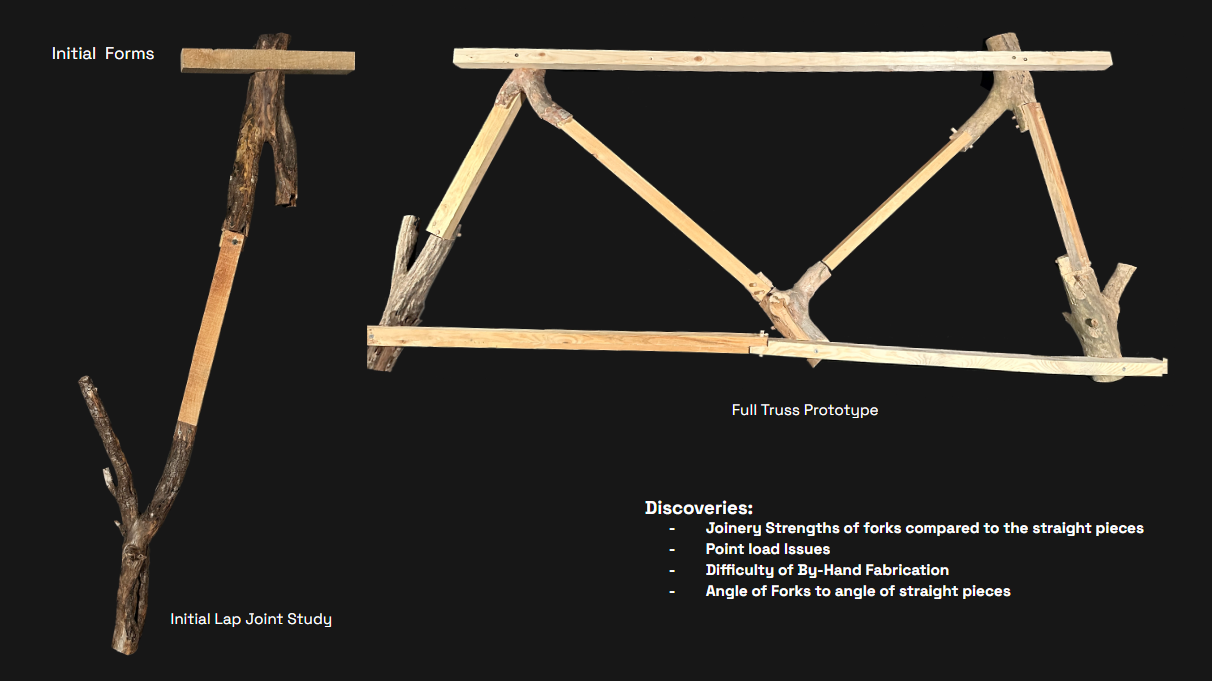
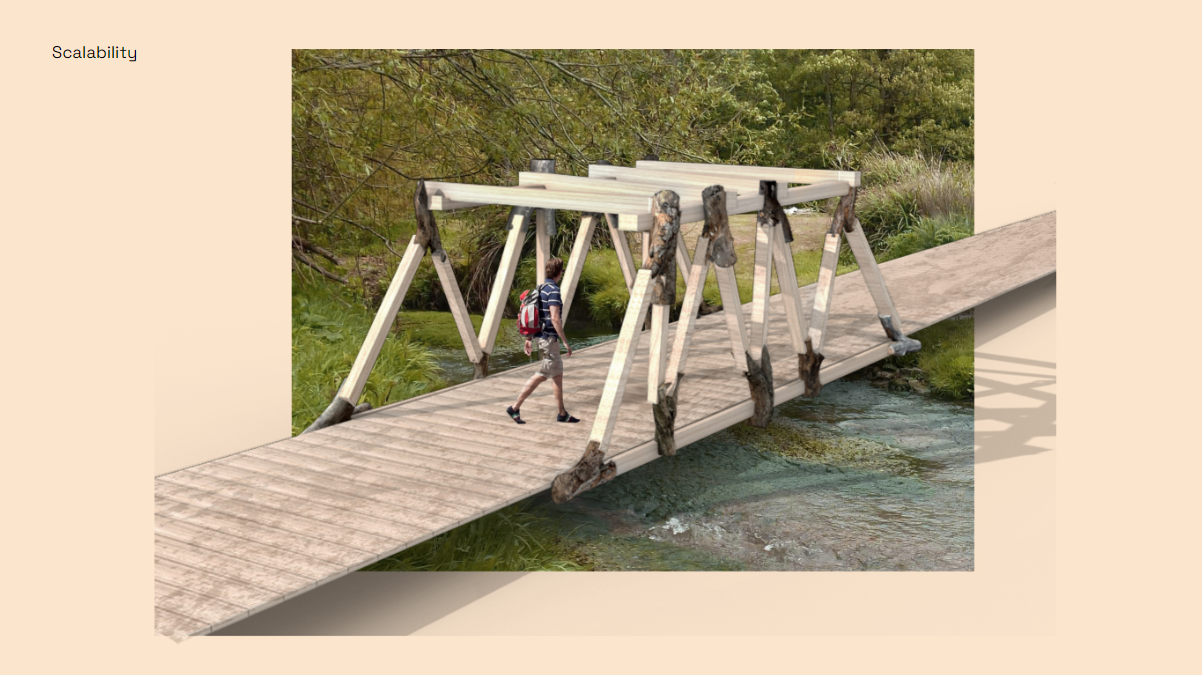
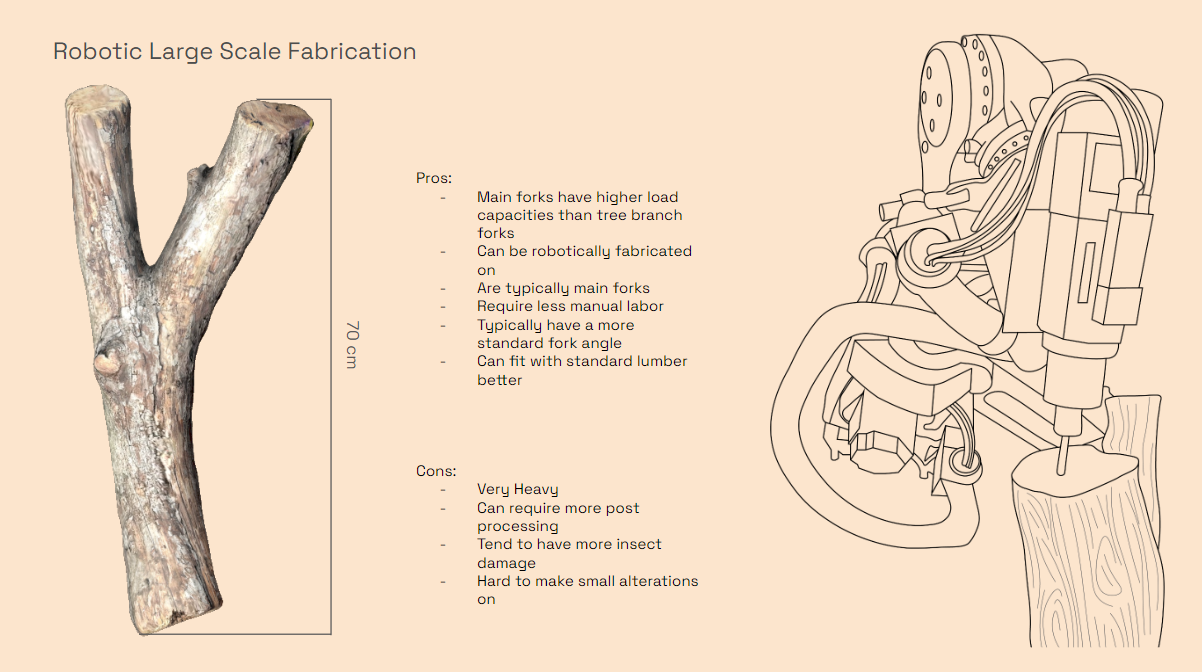
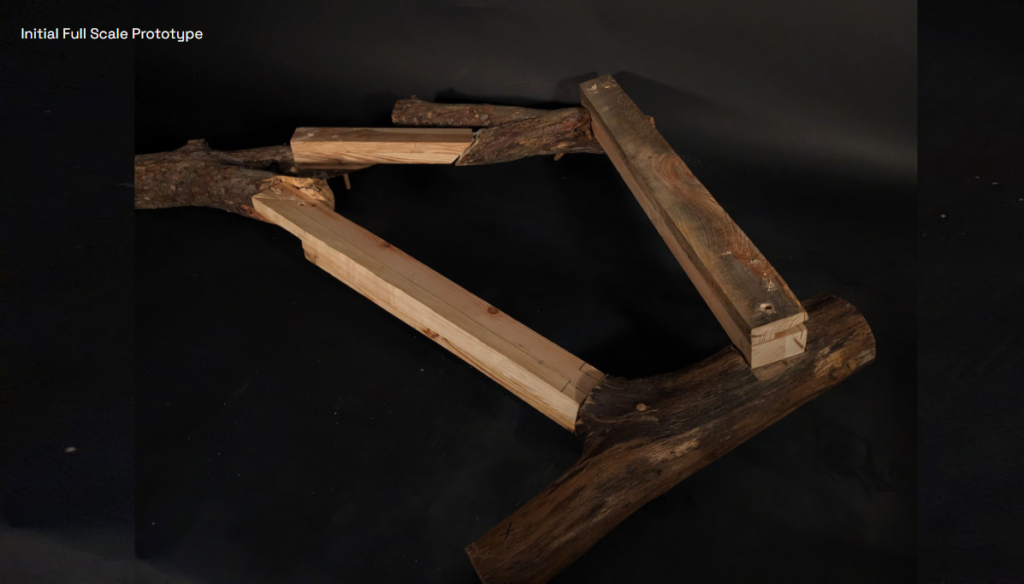
Initial triangle of truss design with algorithm.

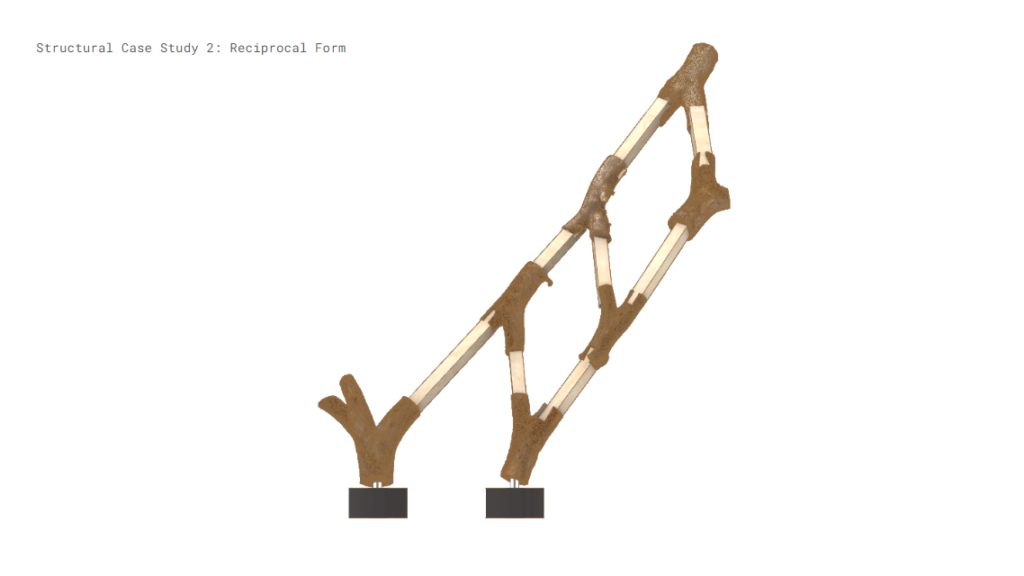
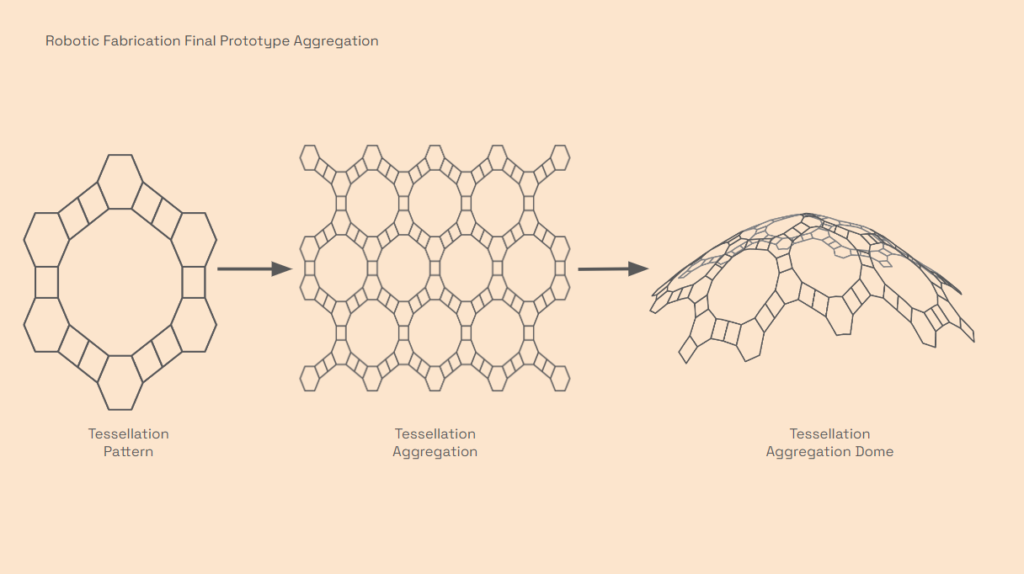
Tessellation form aggregation design for final prototype proposal.
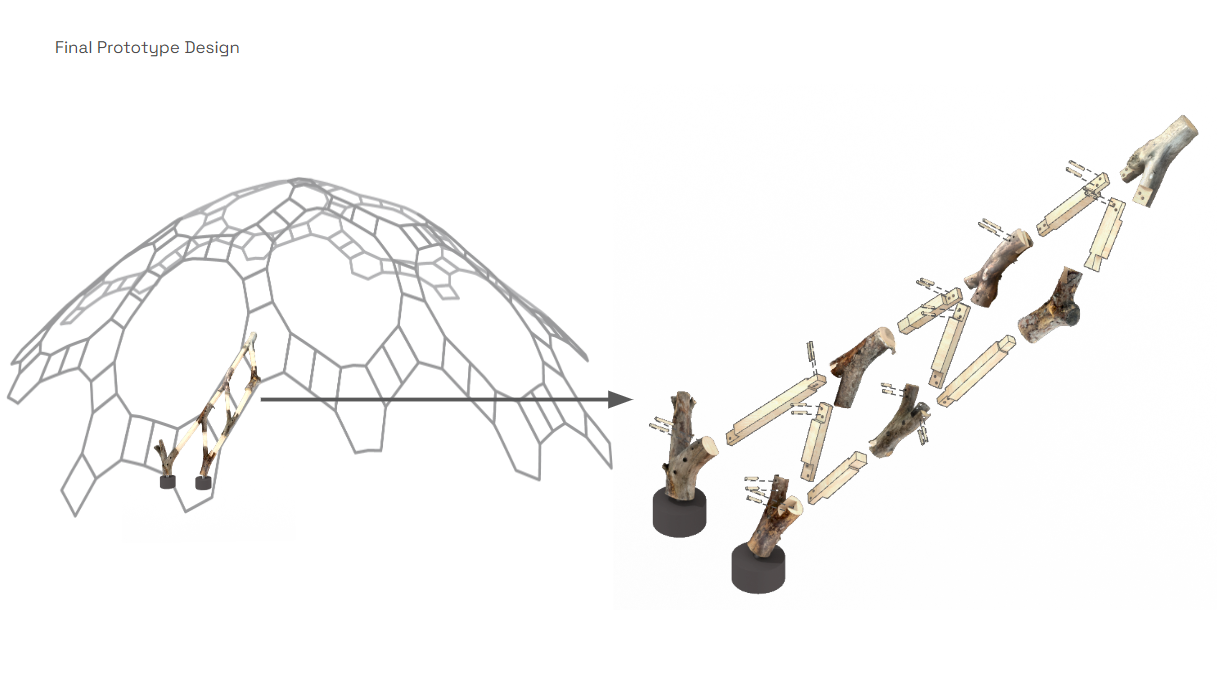
Portion of model to fabricate.
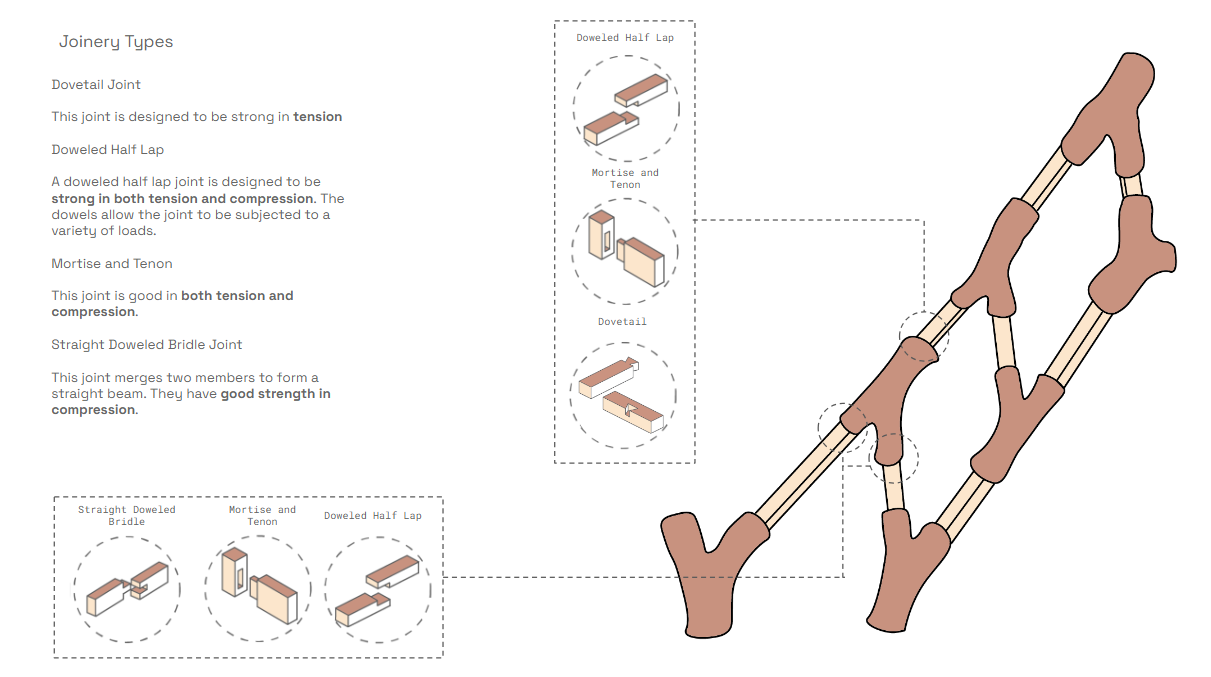
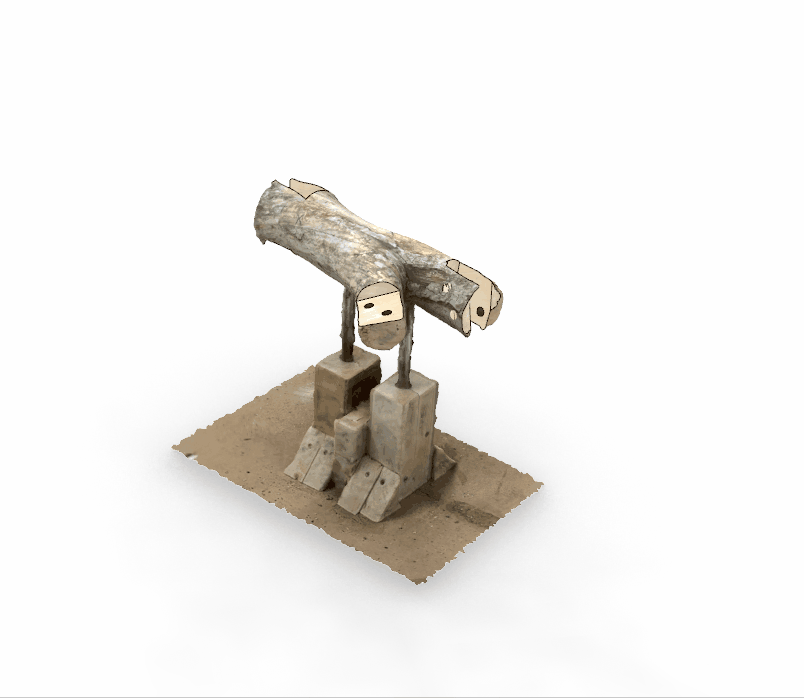
Joinery assembly with dowels and straight pieces.
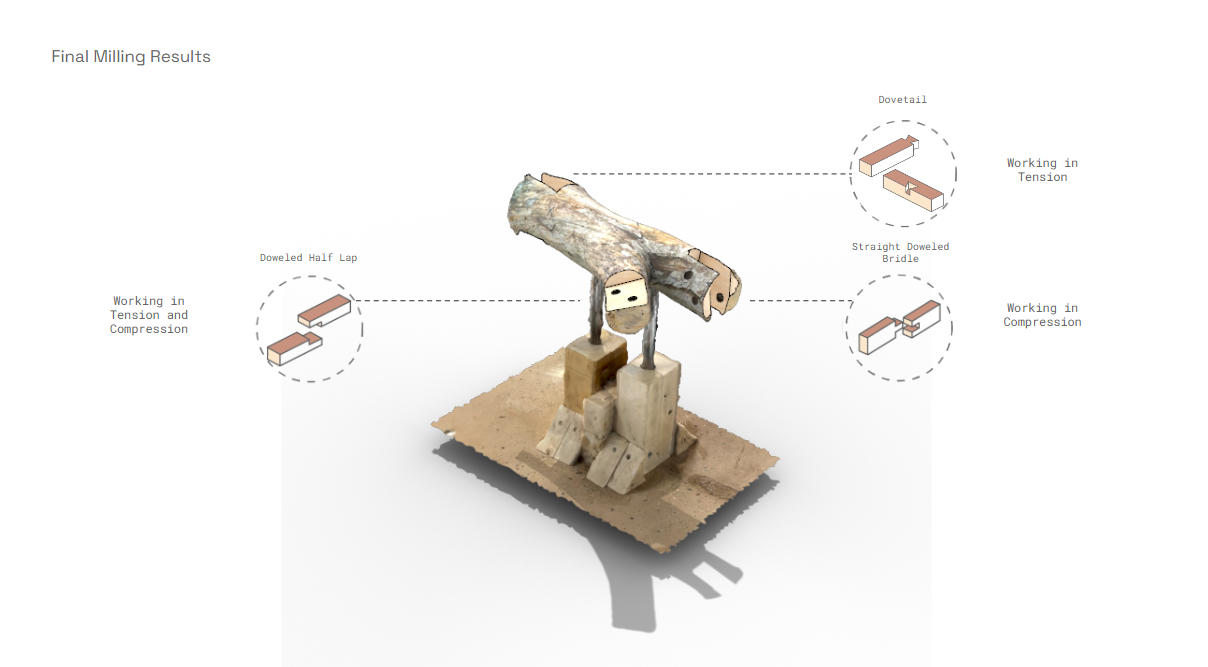
Final joineries for fabricated piece.
Link to Fabrication Video:
https://drive.google.com/file/d/15gTpi_2MOZ9shadsYBRO1fXJrkVZdudr/view?usp=sharing
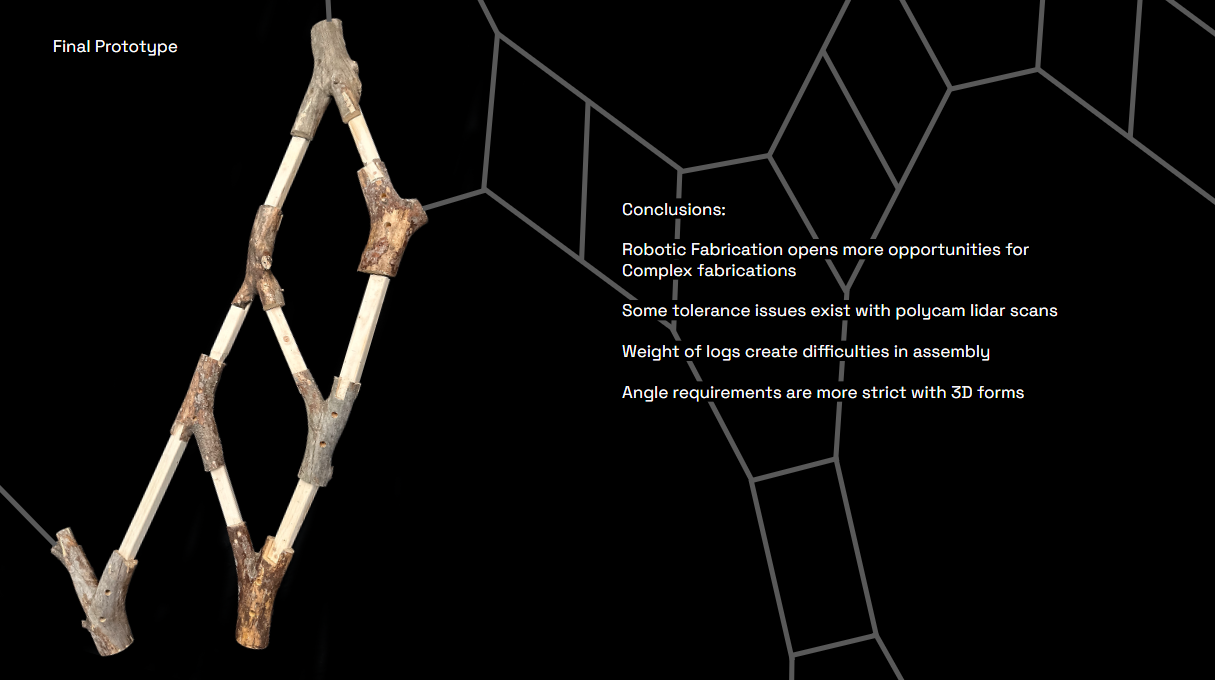
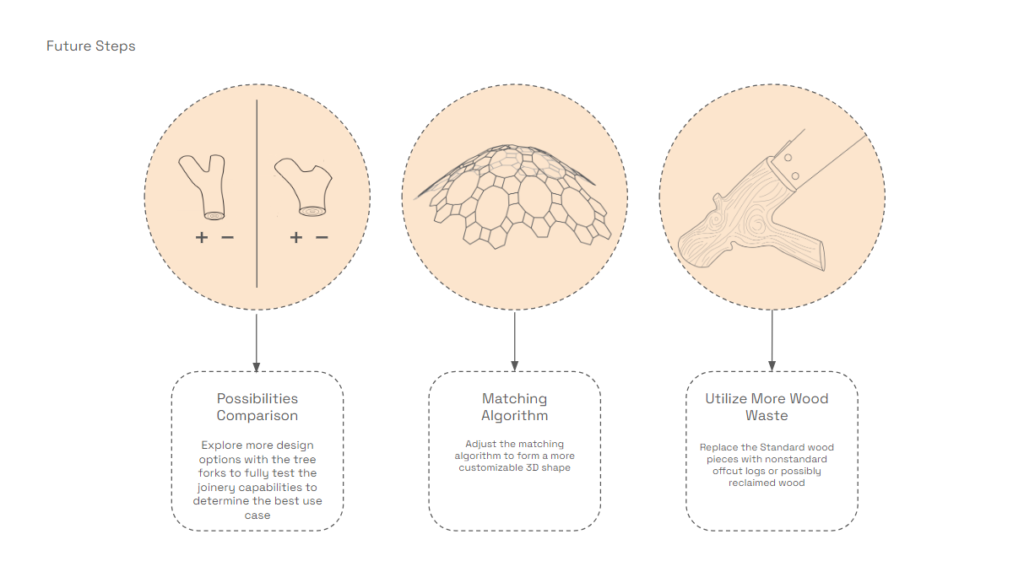
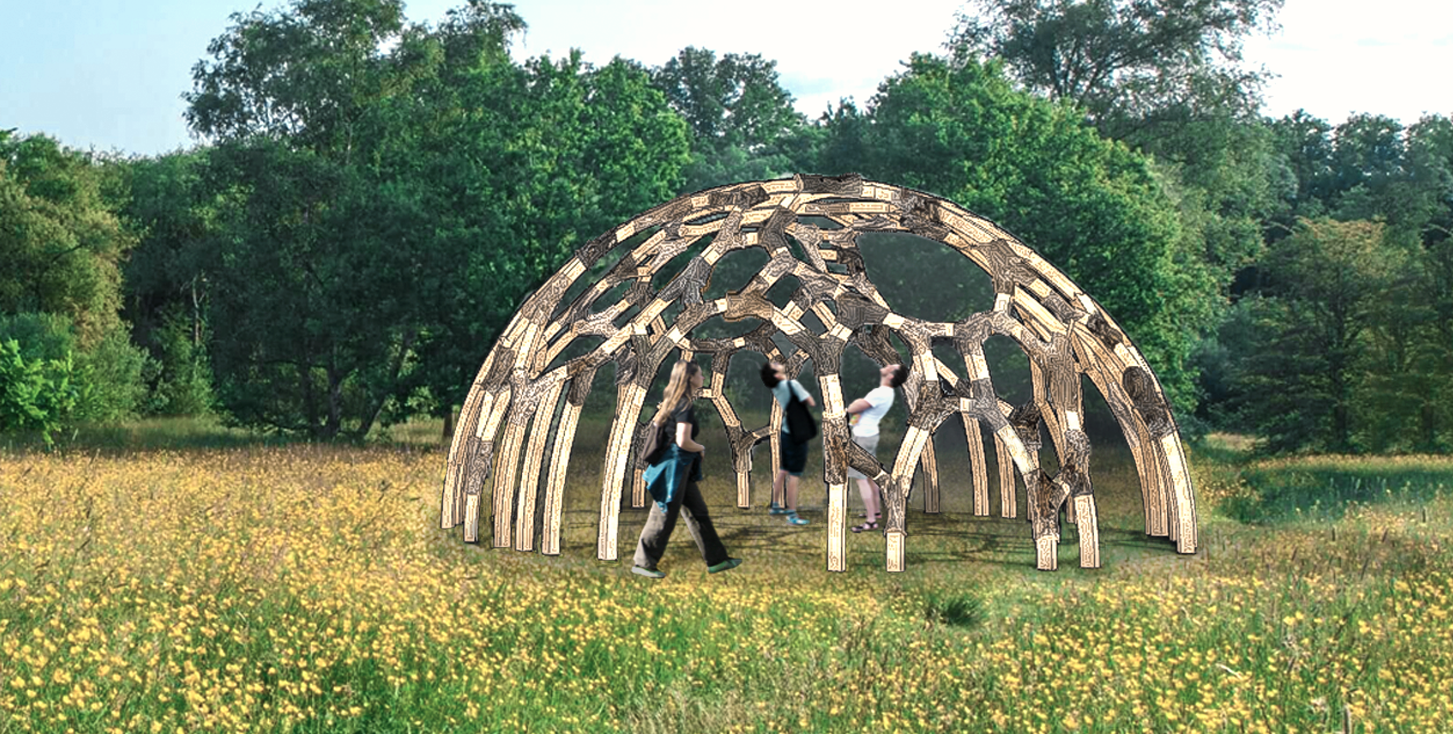