AIM \\
To create custom designed, 3D printed interior surface cladding, constructed of individual components with high quality surface finish and tolerance.
CONTEXT \\
Last term we designed a dual end effector that would have an extruder and a wire cutter within the same tool, allowing us to post process the 3D printed pieces to create a smoother surface and a better interlocking between the pieces. This technique would prevent deformation caused by shrinkage.
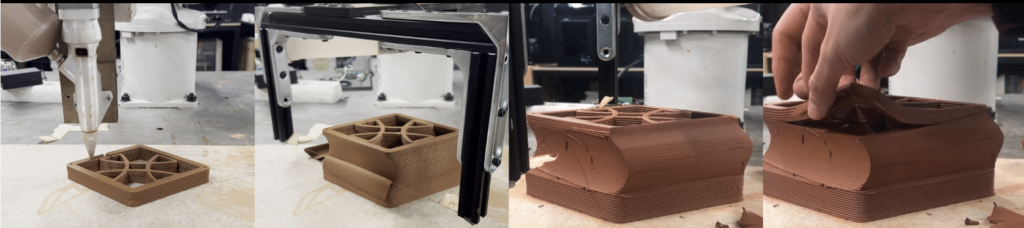
How do we use sensing to understand the deviation & shrinkage that is occurring between the digital model and the printed parts?
During last term , we identified some gaps that our methodology was lacking.
CONTEXT \\ RESEARCH GAPS
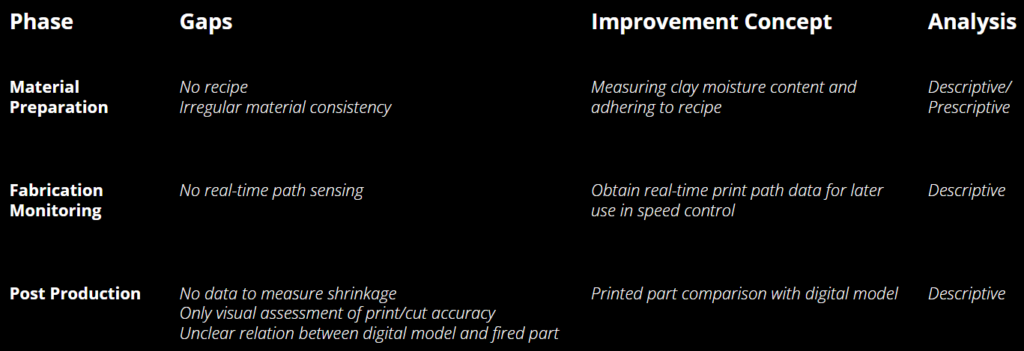
CONTEXT \\ STATE OF THE ART
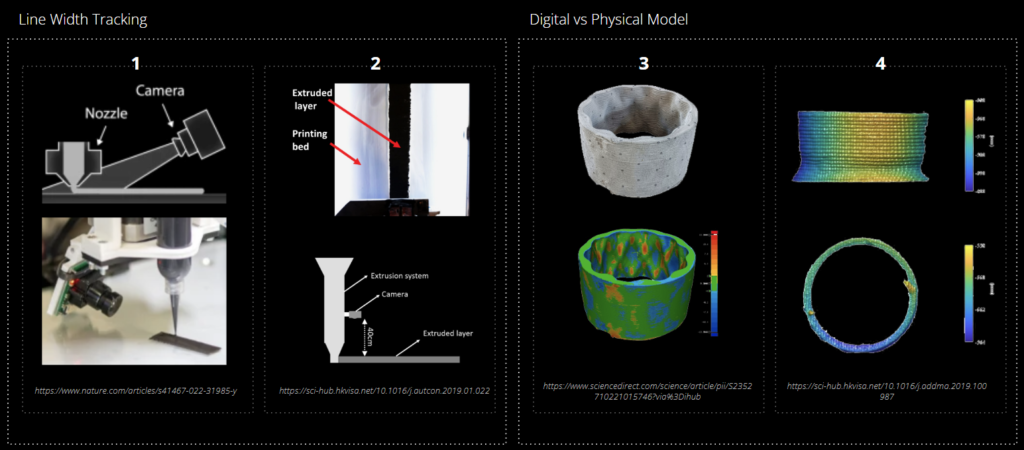
METHODOLOGY \\
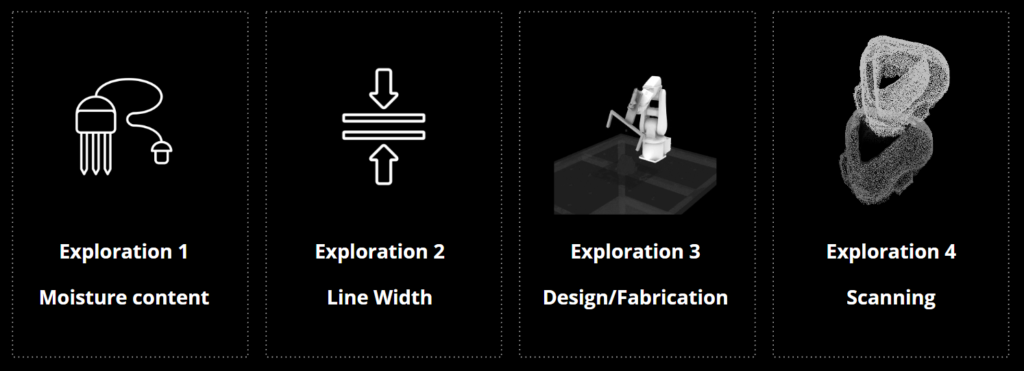
EXPLORATION 1 \\ MOISTURE CONTENT
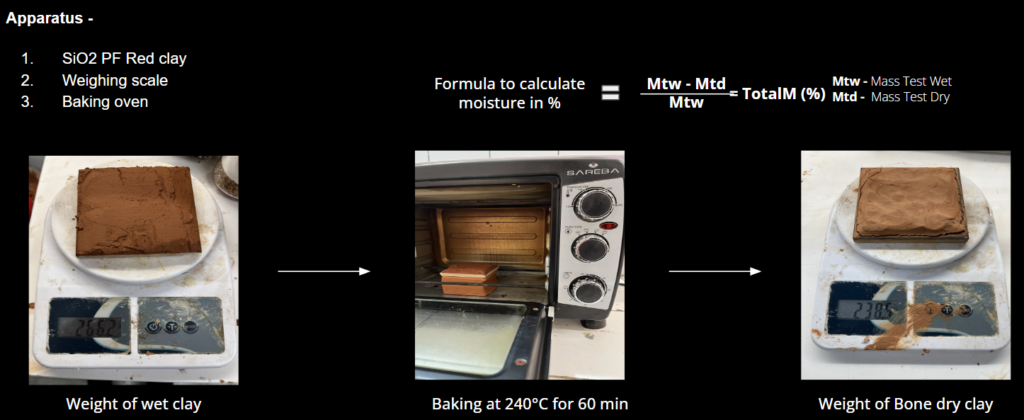
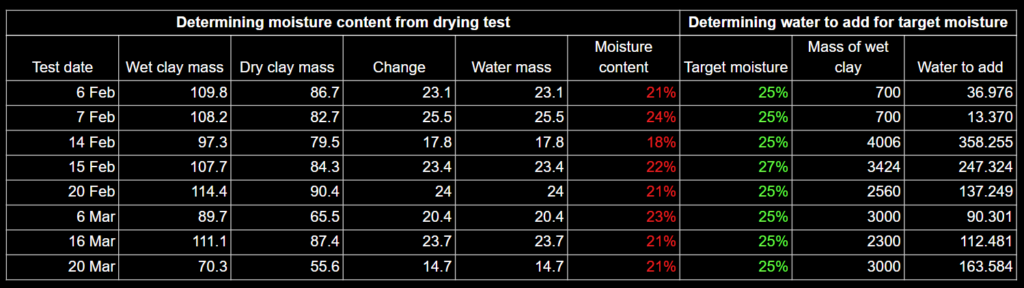
EXPLORATION 2 \\ LINE WIDTH TRACKING
WORKFLOW \\
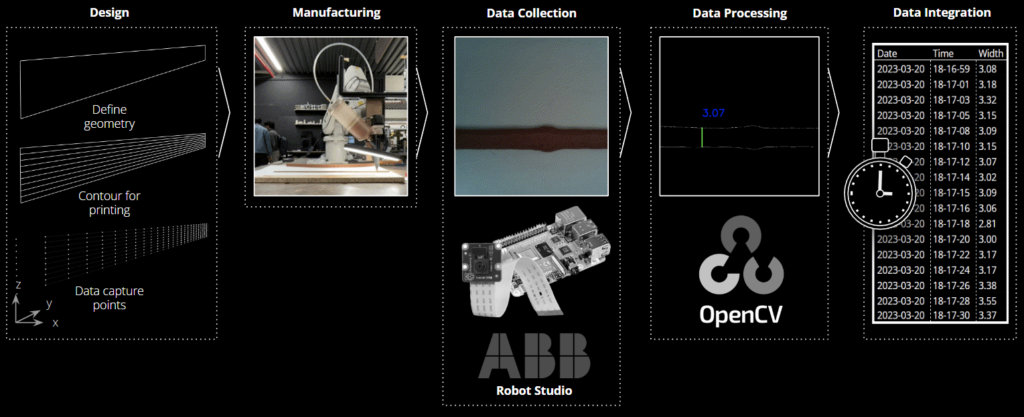
IMAGE PROCESSING \\
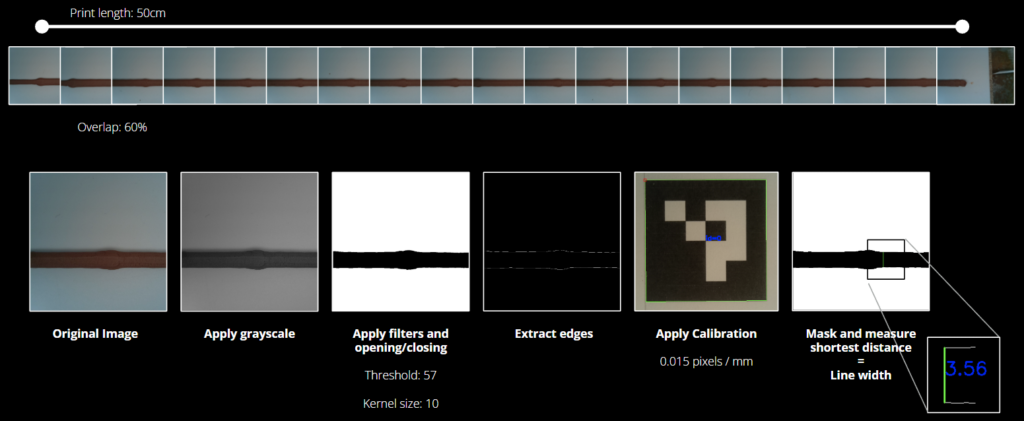
RESULTS \\
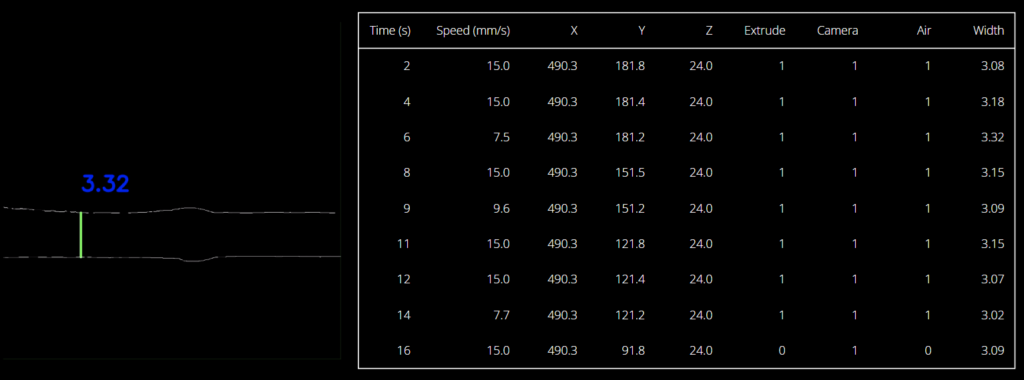
EXPLOARATION 3 \\ DESIGN
This term, we decided to create a more complex geometry in order to see where in the fabrication process we can apply the explorations before mentioned in order to have a more accurate physical model compared to its digital. For the geometrical generation of the pieces to fabricate, we used a from finding process to achieve the most optimal form inspired by the process of nature using algorithmic design by grasshopper and its plug-ins.
The geometry is discretized in different cells, treating them as individuals for fabrication.
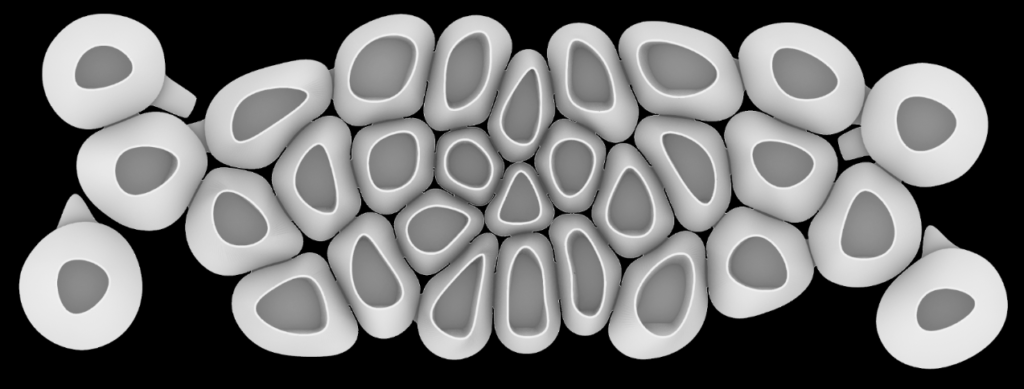
Each element is divided into 3 different parts, the base part where the interlocking between the pieces would happen, then the middle part that would cover the neighbouring pieces flanges and then the “dome” where the shelving would happen.
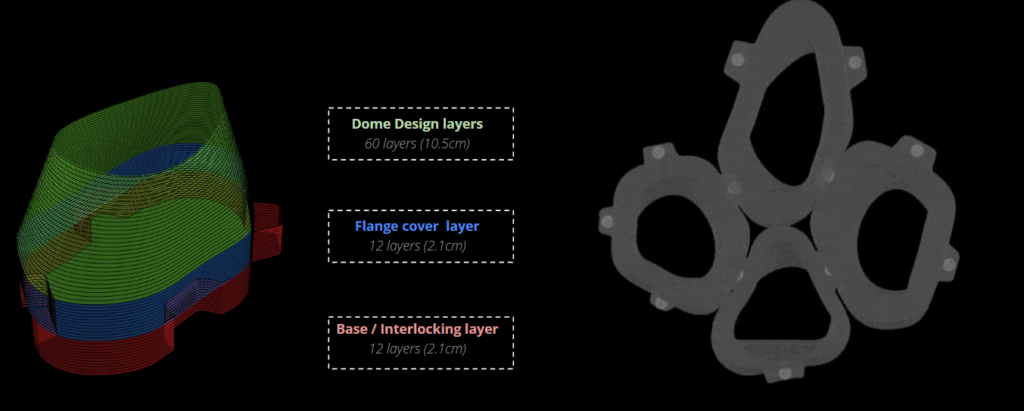
For the assembly, we designed flanges where some bolts would be placed in order to attach them to any surface. The overall geometry assembly strategy would start with the center piece, and then the neighbouring pieces in a concentric way.
WORKFLOW \\
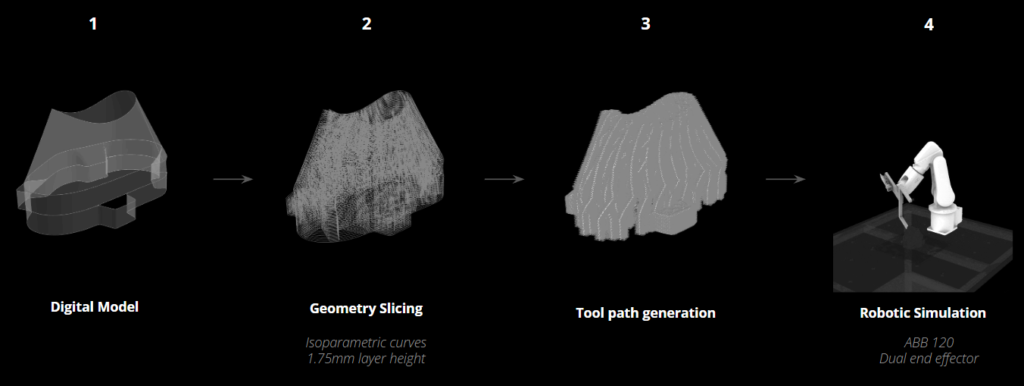
FINAL RESULTS \\
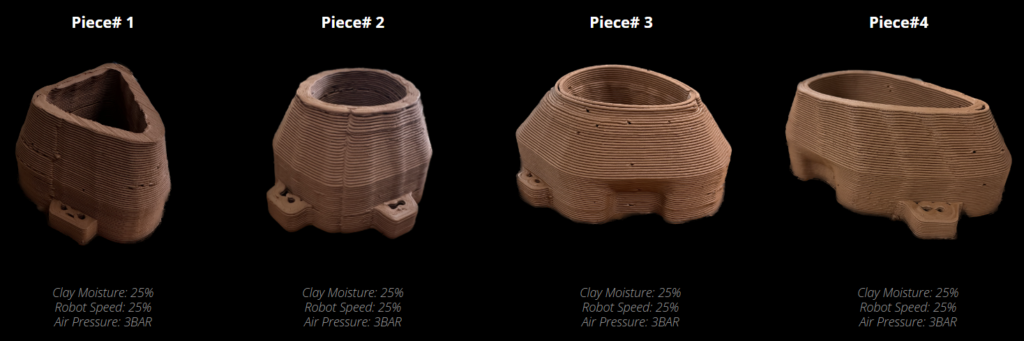
EXPLORATION 4 \\ SCANNING
SCANNING METHODS \\
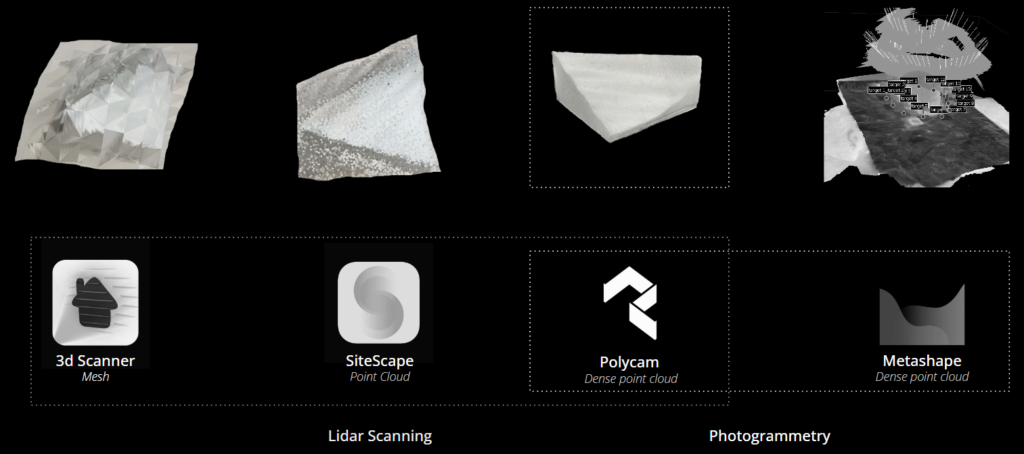
WORKFLOW \\
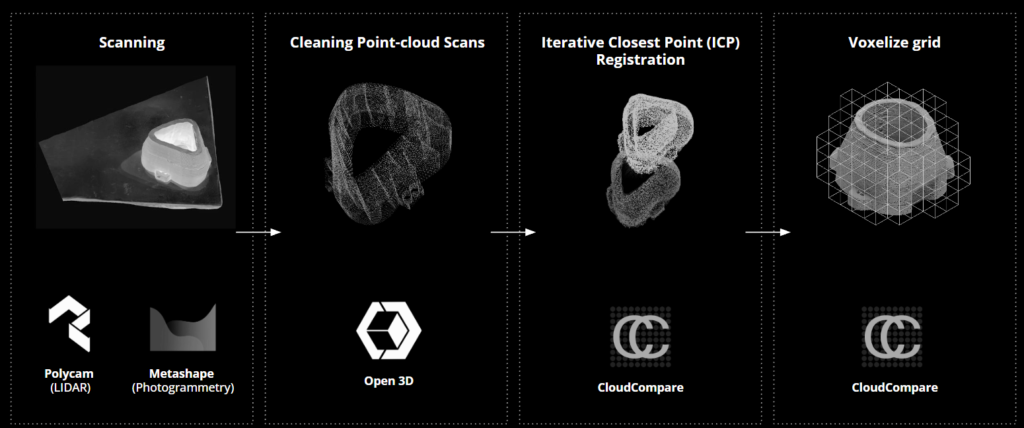
SCANNING SEQUENCE \\
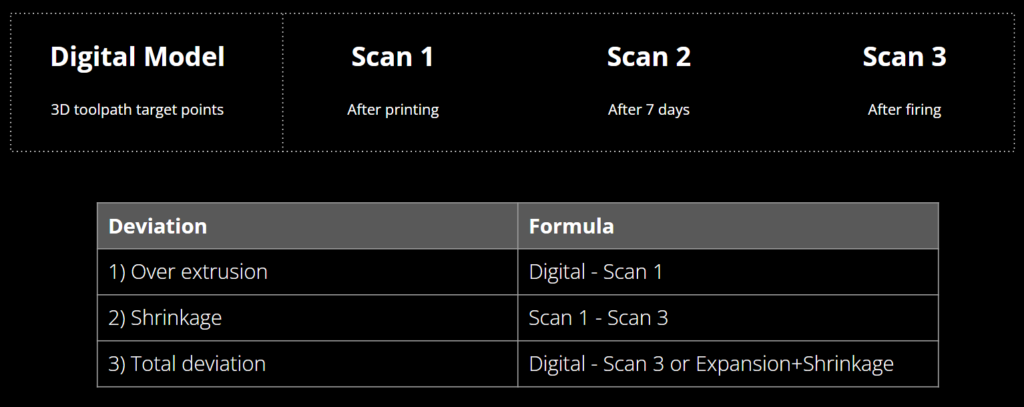
DATA PIECE 1 \\
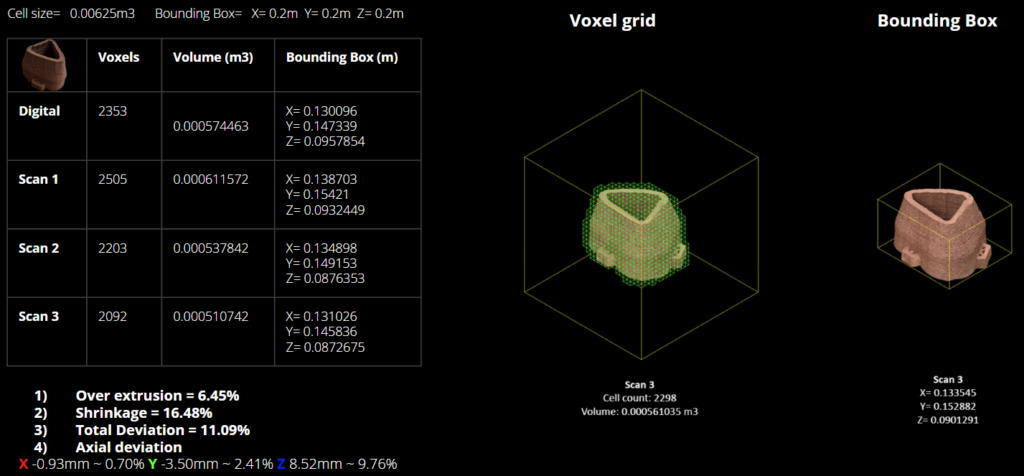
DATA PIECE 2 \\

DATA PIECE 3 \\
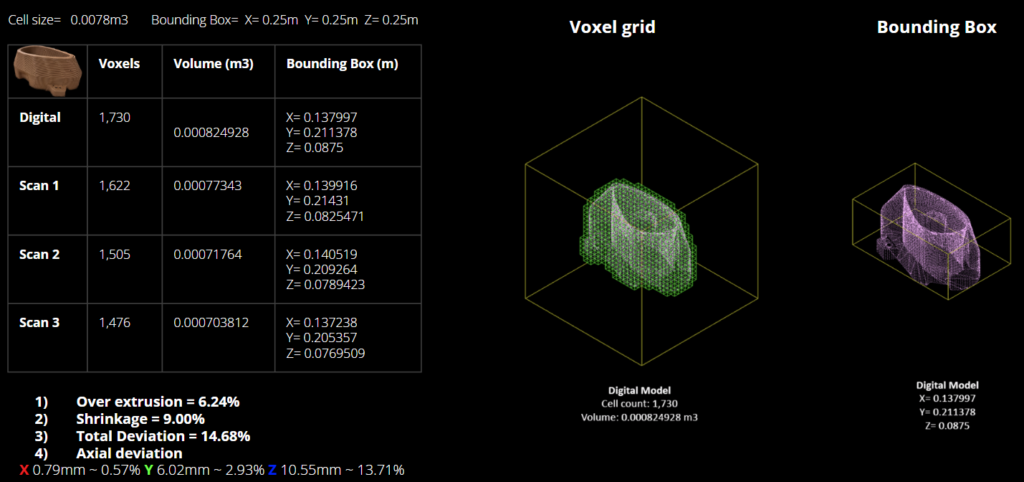
RESULTS \\
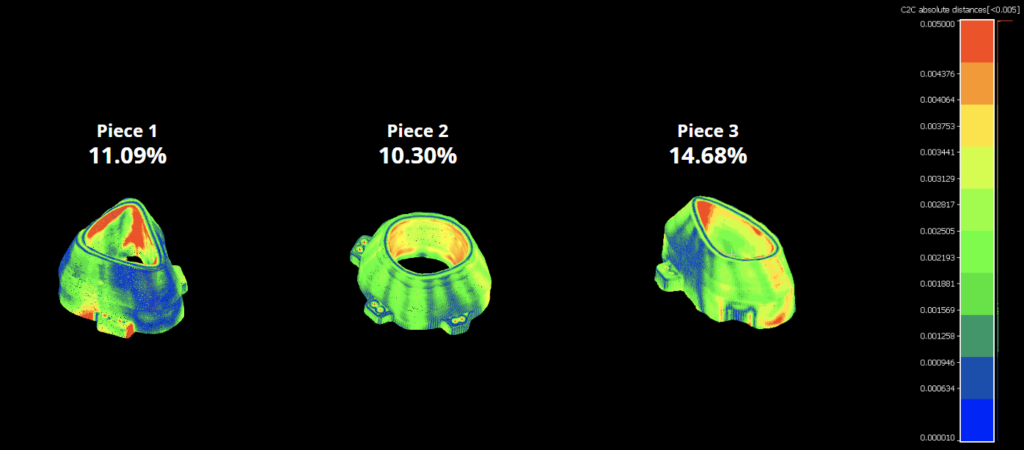
DATA INTEGRATION \\
PSEUDO CODE \\
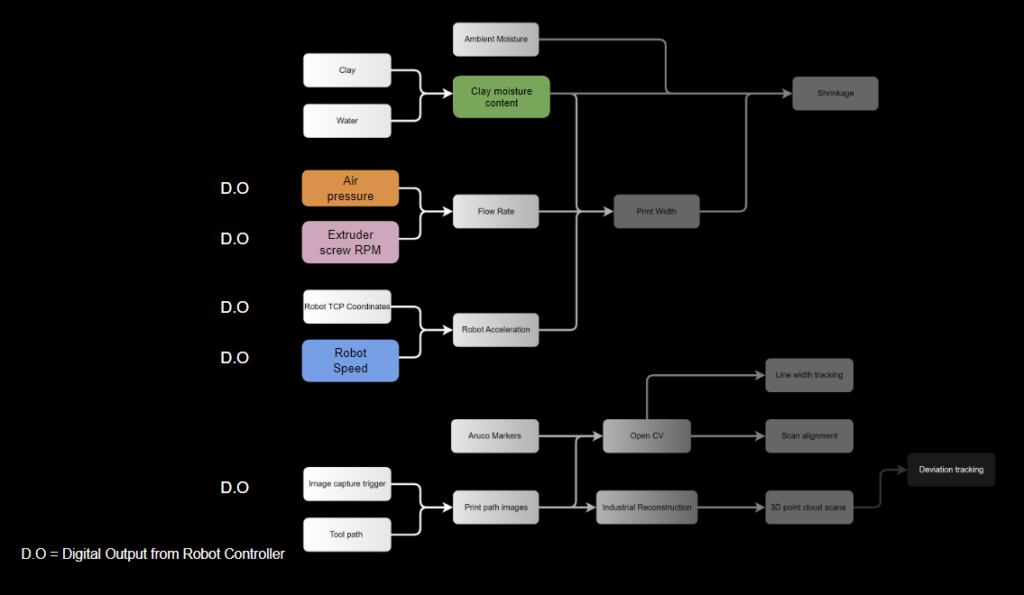
ROBOTIC CODE \\
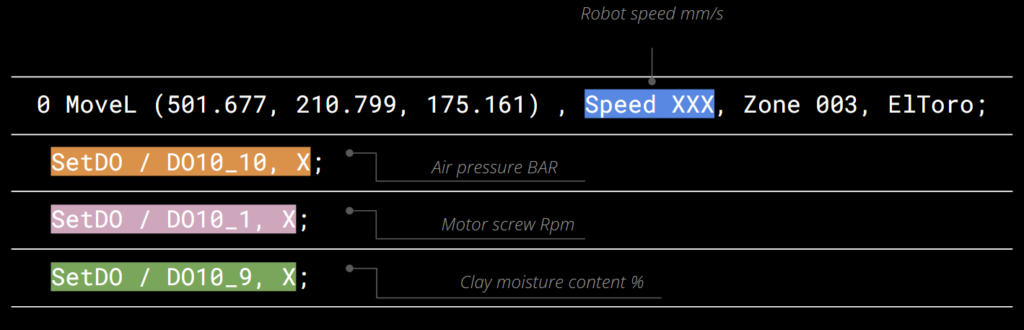
NEXT STEPS \\
- Exploration 1 (Material Sensing): Introduce moisture sensors and environment sensors to have full control of the consistency of the clay mixture during printing.
- Exploration 2 (Line-width tracking): Expand to include more complex geometries.
- Exploration 3 (Design): For wire cutting the sides we will add a rotating base to expand the range of wire cutting possibilities.
- Exploration 4 (Quality Control Sensing) : Automate the scanning process using ROS and ABB 120, integrating a depth camera for industrial reconstruction.
- Integration of additional parameters into G-Code for improved control of manufacturing processes