Envisioning a self-sustained colony on Mars, our primary focus is on revolutionizing transportation within the red planet. Sustainability is our guiding principle as we design an efficient transportation system that seamlessly connects habitats across various clusters. Incorporating Tensegrity moving parts, Inflatable lightweight structures, and a Hexagonal Grid framework, our approach embraces a Kit-Of-Part methodology. Following this repeatable hexagonal pattern, all design elements can be easily connected with each other like a puzzle – in every possible direction – creating a seamless enclosed network for living and exploring a new habitation prototype on Mars.

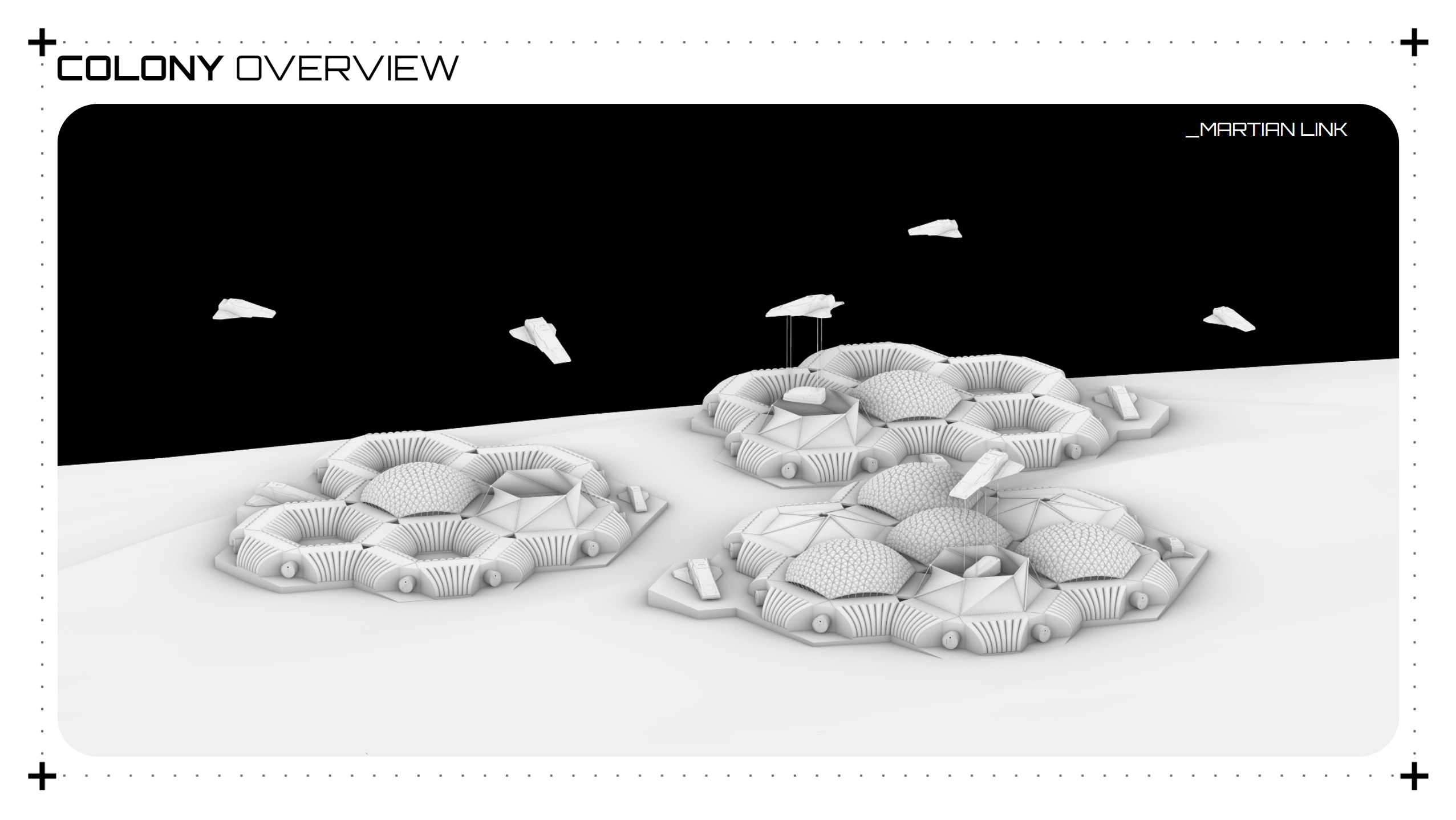
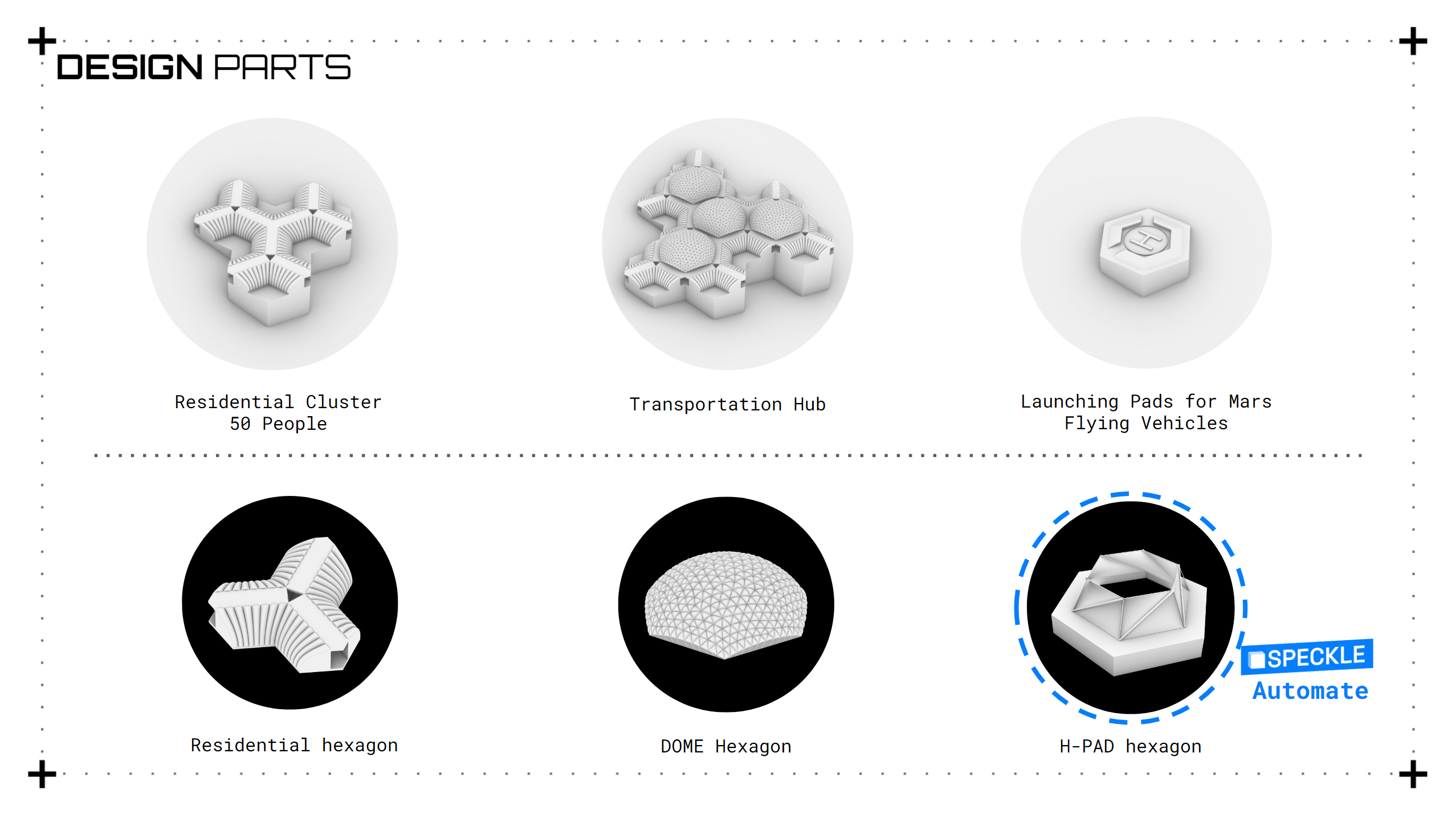
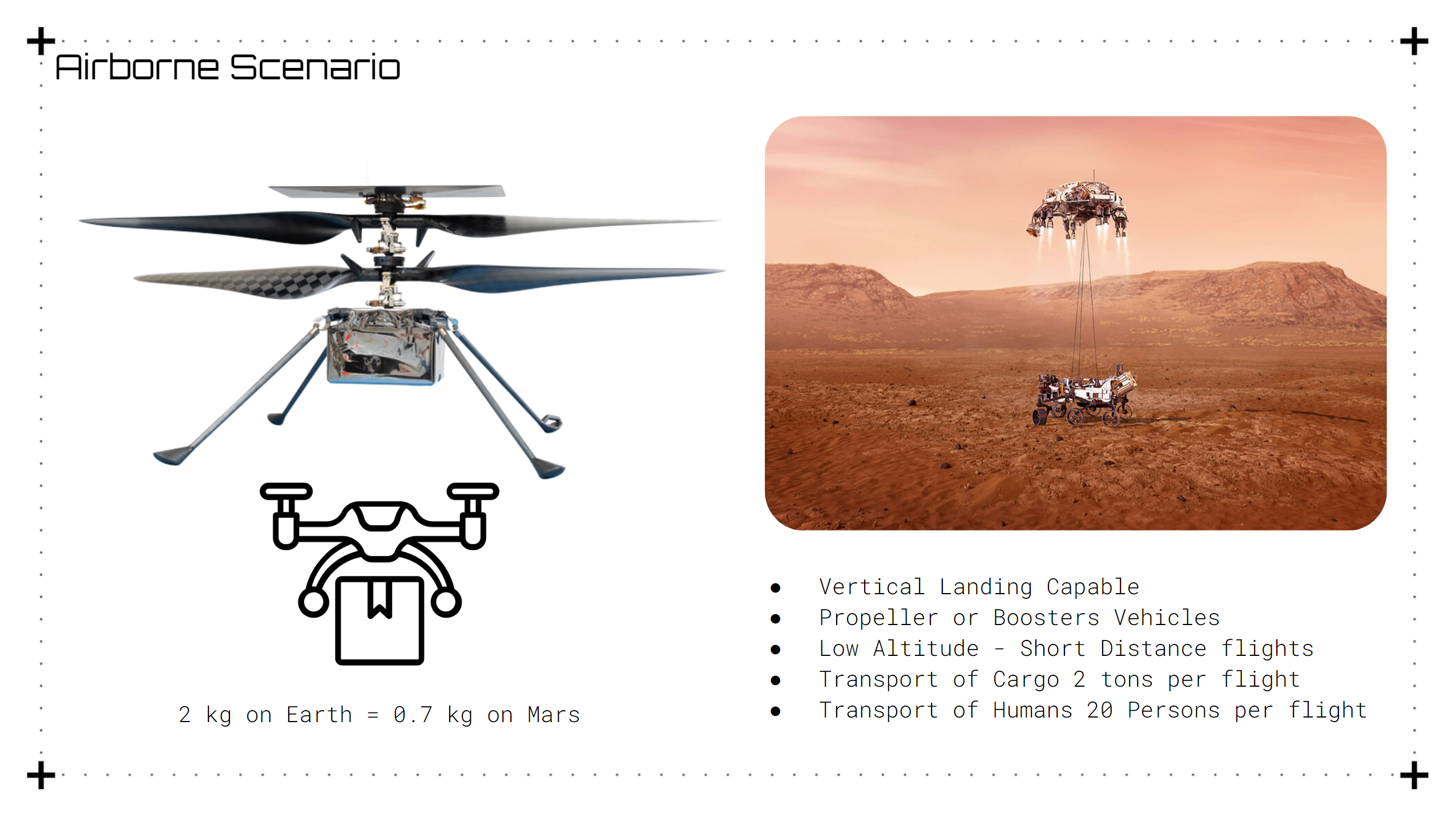
KIT OF PARTS
_Residential Pod
Our Hexagon Residential Unit comprises of 6 Pods designed based on the Hexagonal Grid system. From comfortable living quarters to lounge spaces, and laboratories, each pod has been detailed out with human ergonomics and furniture. Anchored by a sturdy rigid cable structure, our design ensures stability and resilience in the Martian environment. Wrapped around this framework is a lightweight skin material engineered for both protection and habitability. Comprising six layers of defense – including double membrane, PTFE layering, and vacuum spacing. With an outer shell-inner shell configuration and reinforced aluminum structure framing, our design effectively shields against radiation while maintaining structural integrity, with a thickness of 0.5-meter thickness. For the construction process, we’ve devised an efficient assembly method leveraging robotics and pre-made, flat-packed elements transported from Earth and assembled on the surface of Mars. This approach streamlines construction while minimizing the need for extensive manual labor in the challenging Martian environment. Upon arrival, rovers land on Mars to initiate groundwork for the colony’s establishment, locating optimal coordinates and marking designated areas for construction. Essential energy sources and infrastructure are swiftly established to sustain colony operations. Local regolith is utilized for 3D printing structural components, while inflatable structures are strategically installed to enhance habitability and functionality within the colony.

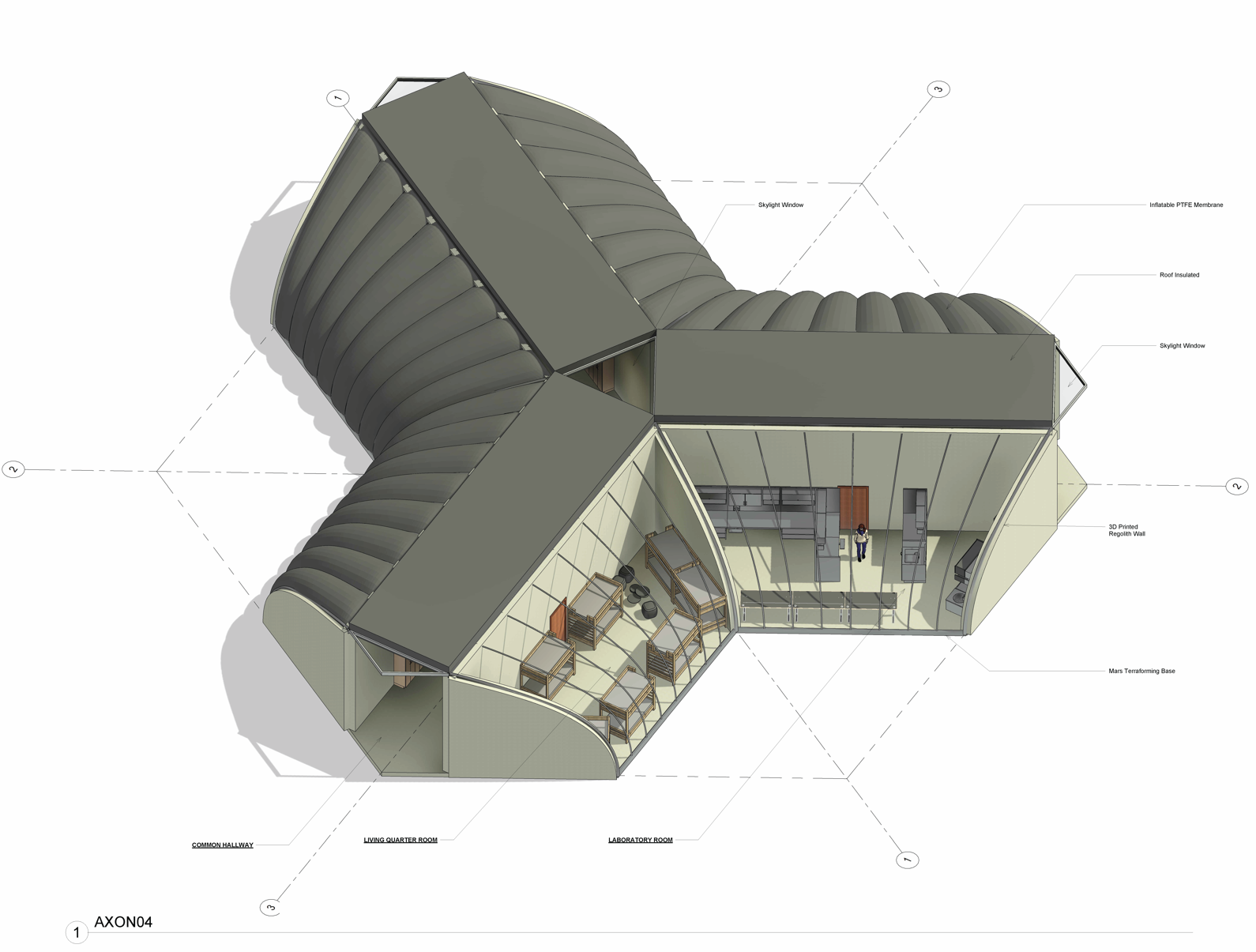
SPECKLE WORKFLOW
The geometry is transmitted to Speckle as individual Speckle components, each capable of being controlled through various filters tailored to Revit walls, Beams, Floors, and other architectural elements. This organization allows for precise management and manipulation of each component within the Speckle web environment, enabling integration and customization of the residential pod elements from any user of the online platform with a single link.
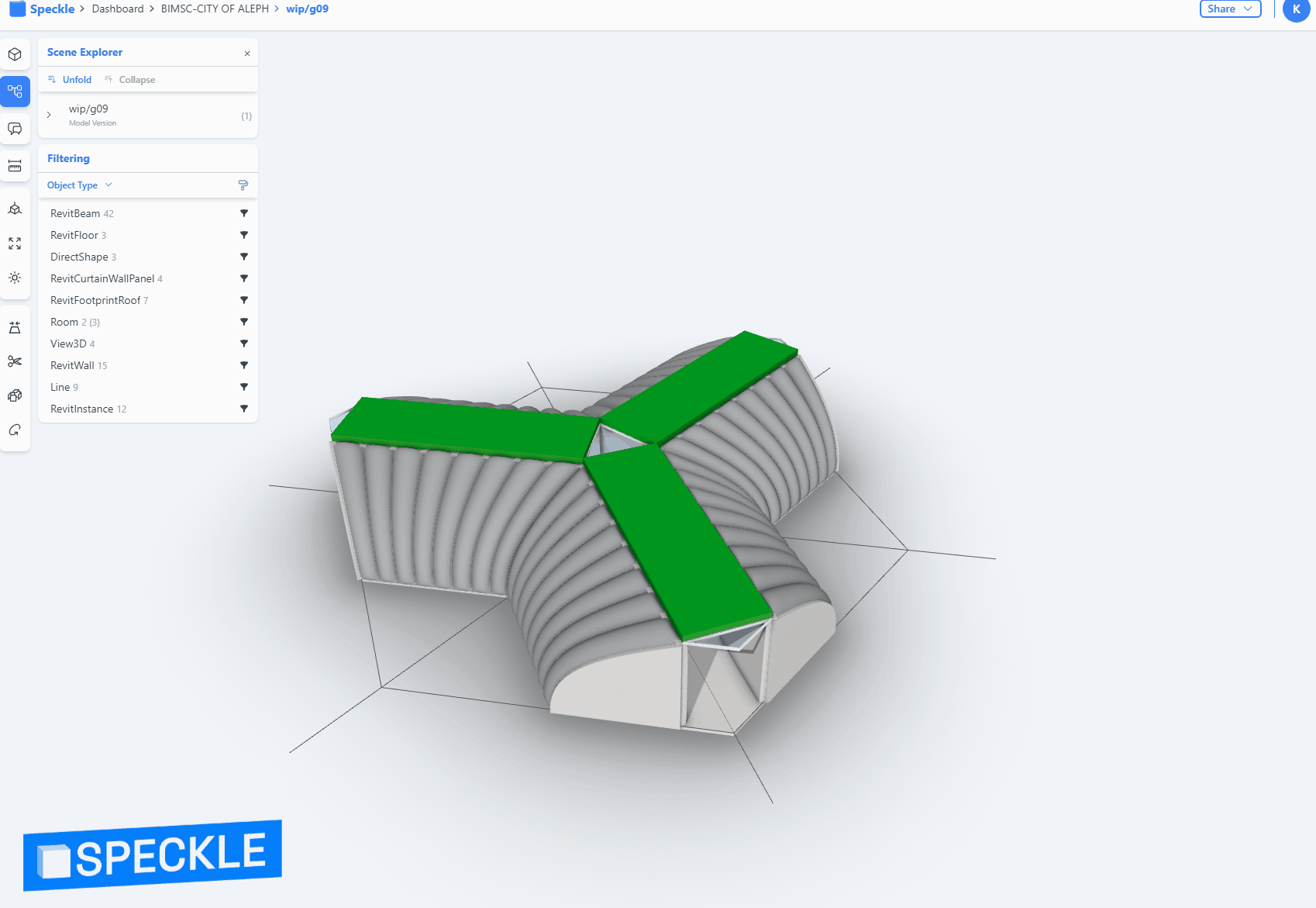
_Transportation Hub
Located at the heart of our Martian settlement, the transportation hub serves as a vital nexus, seamlessly connecting neighboring clusters, and acting as the living heart of the colony. Comprising of launching pads, airlock systems, transit facilities, a public plaza, and research labs, this central node facilitates movement and interaction among colonists. The hub’s design optimizes functionality, with launching pads situated on the periphery and central domes housing key functions such as the plaza, transit facilities, and research labs. Movement within the hub begins with transit services, progressing from ticketing areas to terminals, culminating at the research launching pads. Peripheral landing zones offer parking and service stations, minimizing human intervention on the Martian surface. The hub’s infrastructure integrates terraforming bases, 3D-printed walls, and structural members supporting the inflated domes, ensuring stability and durability in the harsh Martian environment. Launching pads feature tensegrity moving parts and pneumatic membrane coverings, while the central domes utilize a triangular steel structural framework to support inflatable membranes, providing both functionality and protection.
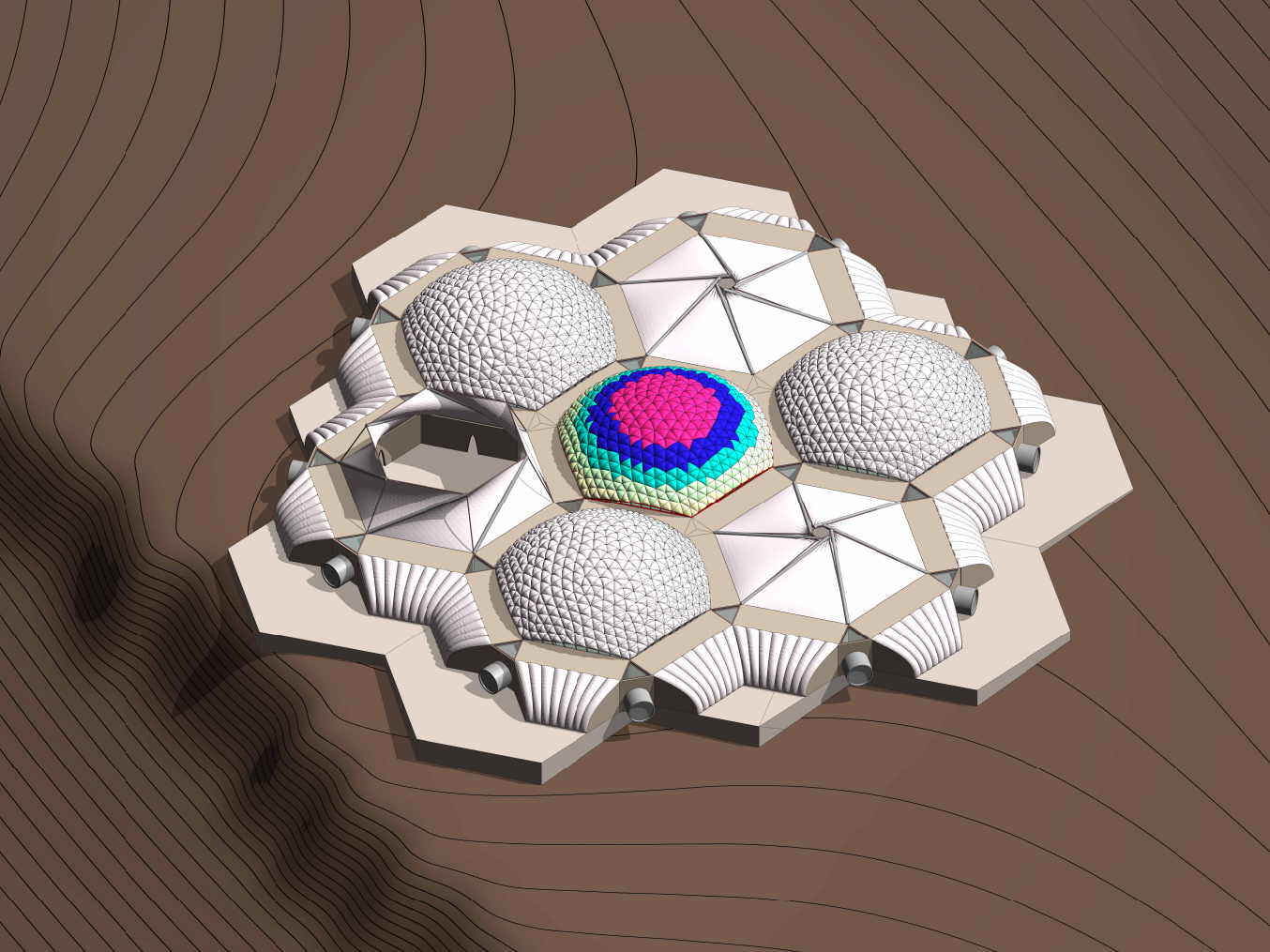
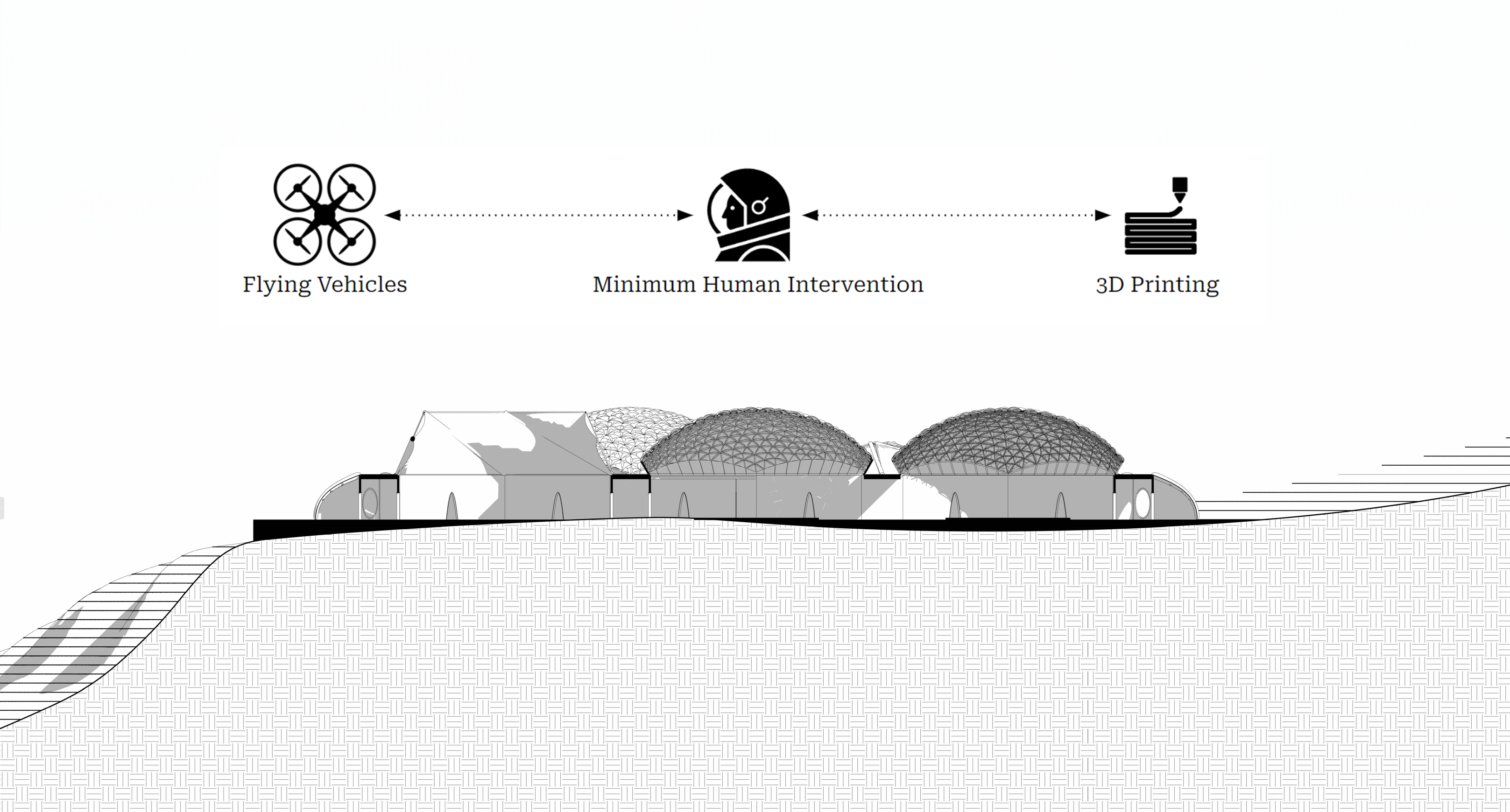
SPECKLE WORKFLOW
The geometry is sent to speckle as individual grouped components by material, phase of construction, type, and ID. Users can explore the model and its elements for a detailed understanding of the skin and the structural system underneath it through filtering.
_Helipad Infrastructure
The launching helipad hexagon is comprised of a 3D printed base supported by a tensile structure, operating on the principle of Tensegrity to enable deployable structures through controlled cable length. Utilizing Kangaroo simulation, we simulate the opening and closing of the launch pad to create an airlock mechanism, ensuring the safety and integrity of the structure. The helipad is specifically designed to facilitate the smooth arrival and departure of capsules, featuring a membrane controlled by cables and struts. This results in a lightweight and flexible structure that can withstand external forces while remaining stable and resilient. Additionally, it is equipped with a safe landing pad and a designated radio control zone to ensure safe and efficient operations within the Martian environment.
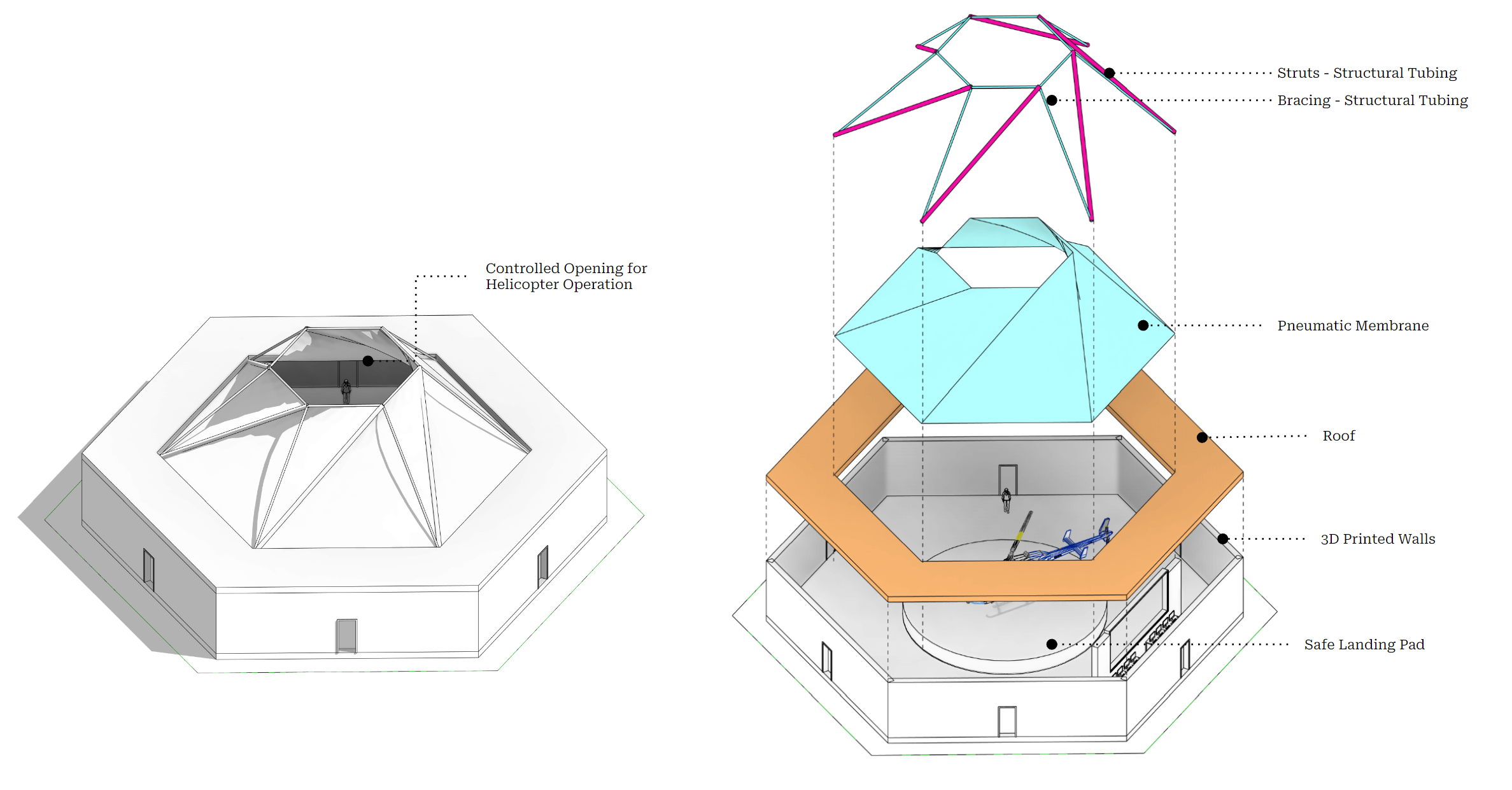
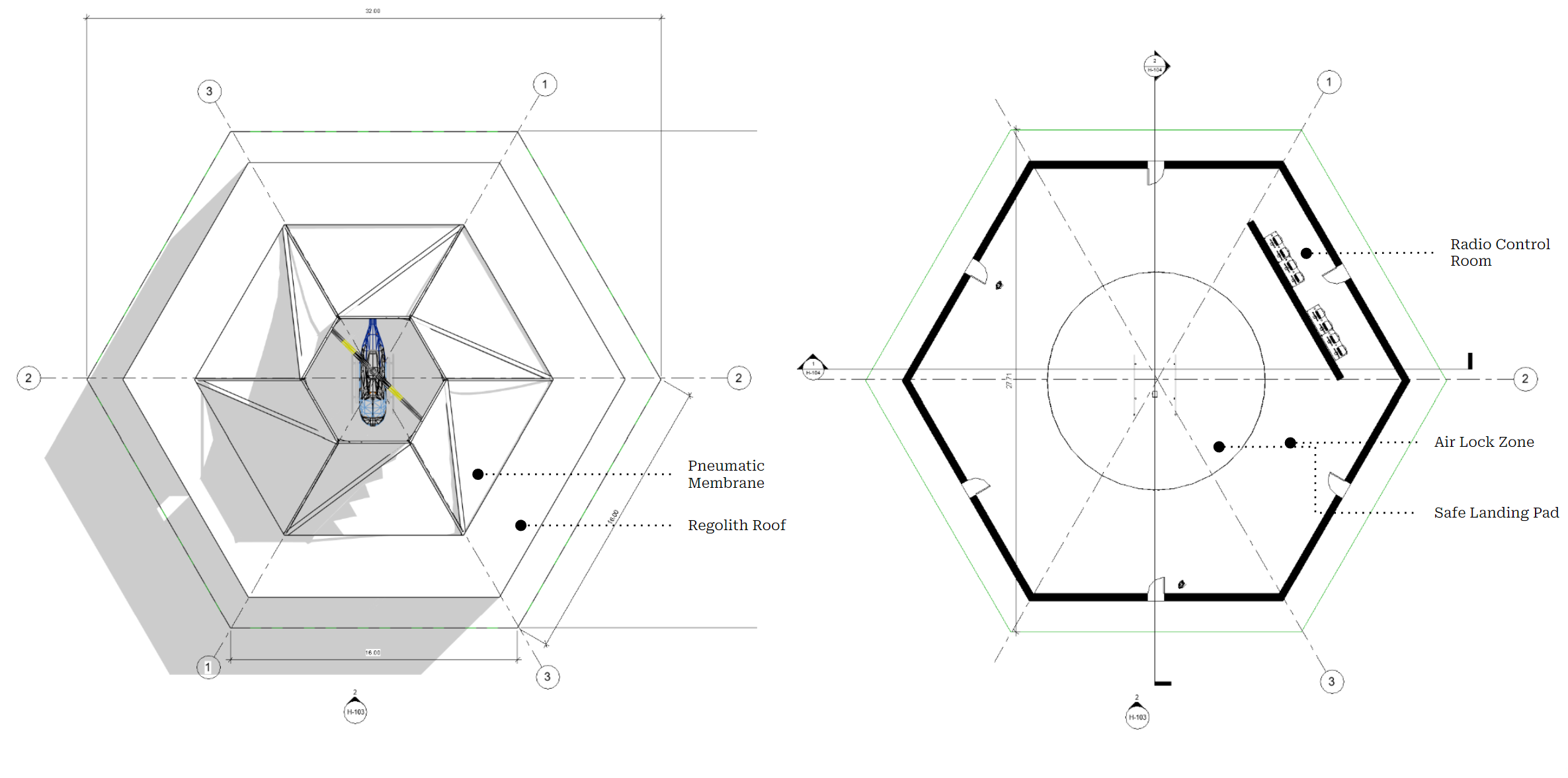
SPECKLE WORKFLOW
_Collaborative Workflow
Our Overall Workflow Diagram delineates our journey from project inception to completion, navigating through various phases along a defined Timeline. Beginning with the project brief and research on Mars architecture, we embarked on an in-depth site analysis to lay the foundation for subsequent tasks. Transitioning seamlessly into Master Planning, we outlined individual tasks and identified programs used by each team member, initiating our first Sketching Models.
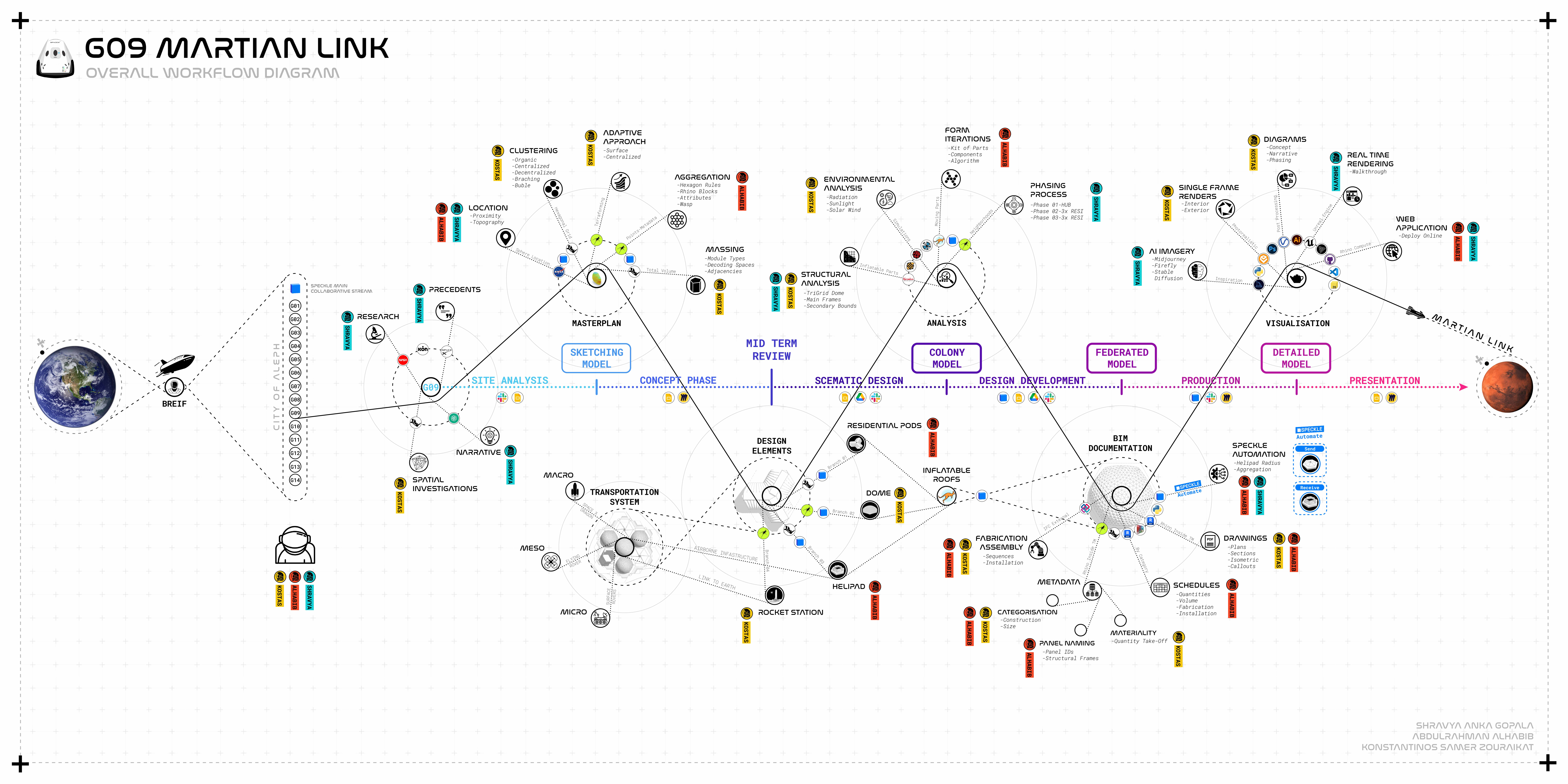
Progressing along the timeline, we entered the Design Concept Phase, splitting the project into distinct elements like residential structures, inflatable domes, helipads, and rocket stations. Simultaneously, our focus shifted to developing an efficient transportation system and initiating groundwork for documentation drawings, forging a crucial link between design and documentation.
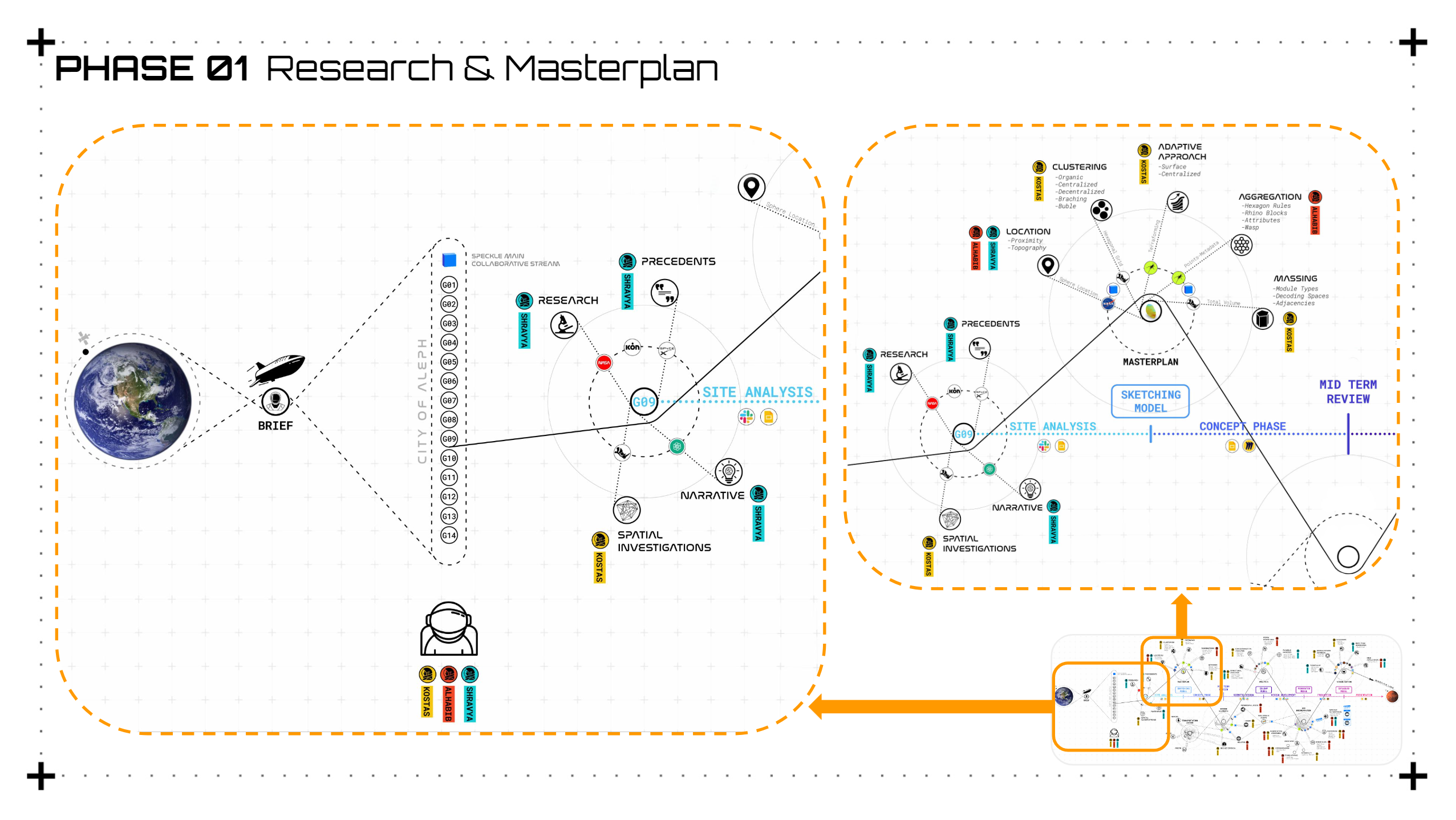
The introduction of the Speckle Automation Bot streamlined our processes, facilitating the generation of Drawings, Schedules, and Fabrication Details. As time progressed, we delved into the analysis phase, leveraging our evolving colony model for comprehensive environmental and structural assessments. The development of the Federated Model marked a significant milestone, propelling us into full production mode.
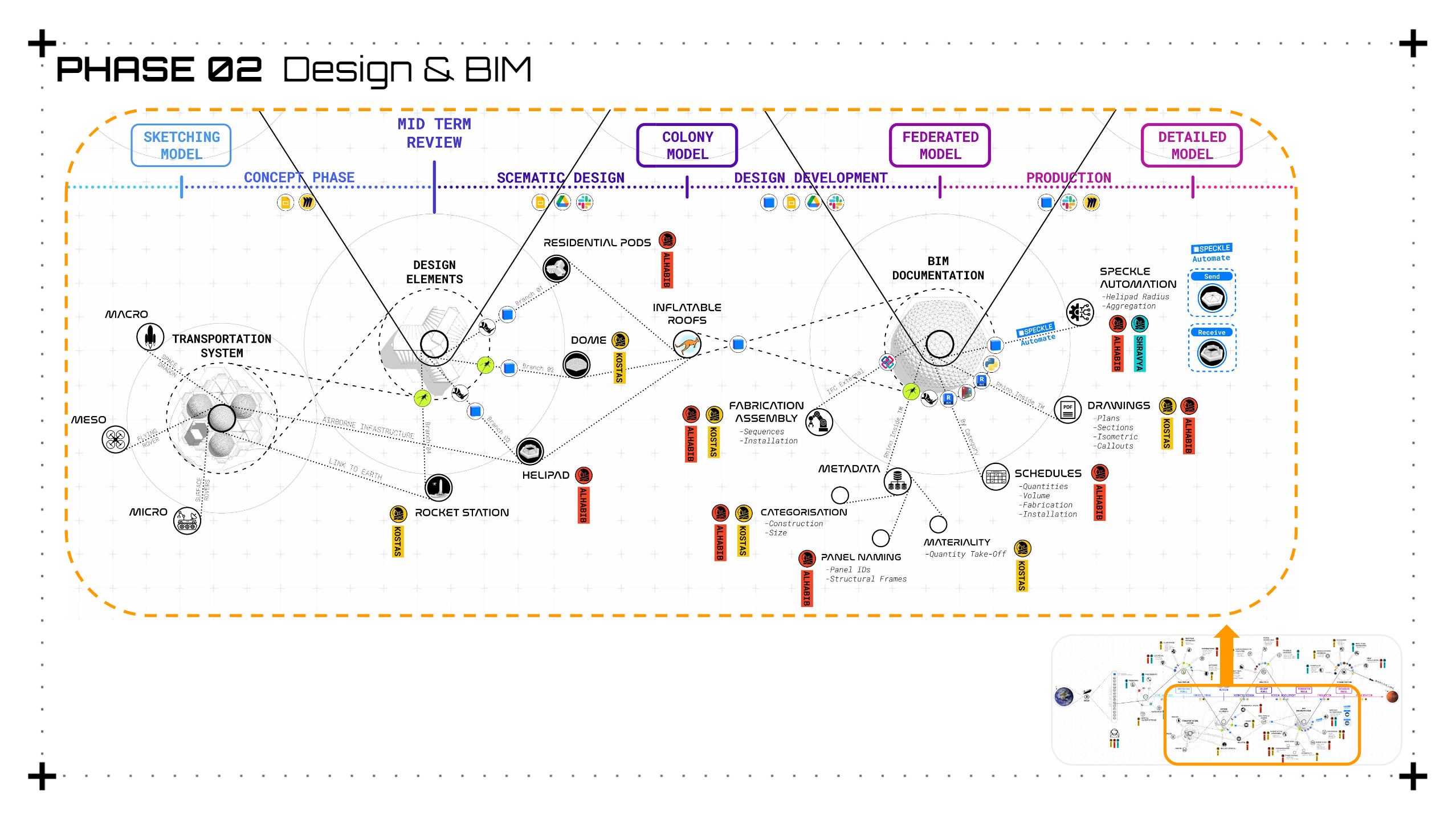
During this intensive phase, we dedicated efforts to refining renders, diagrams, and detailed models, culminating in the completion of our presentation. Each step along the timeline was executed with precision, contributing to the holistic realization of our architecture project on Mars.

_Detailed Workflow Data & Documentation
In the detailed data manipulation process, we start by defining the central point and hexagon types for site planning. We then choose the most suitable Aggregation combination and transmit these points through Speckle. In the next phase, we develop hexagon kits using different Grasshopper scripts and share them via Speckle. Additionally, we use Revit for detailed documentation of the hexagonal geometries. Moving forward, we combine the data points received through Speckle with the three geometry types to create a Federated Model. Each kit is assigned to its corresponding point within the model. Finally, we proceed to post-processing, BIM documentation, and presentation stages to further refine and present the data.
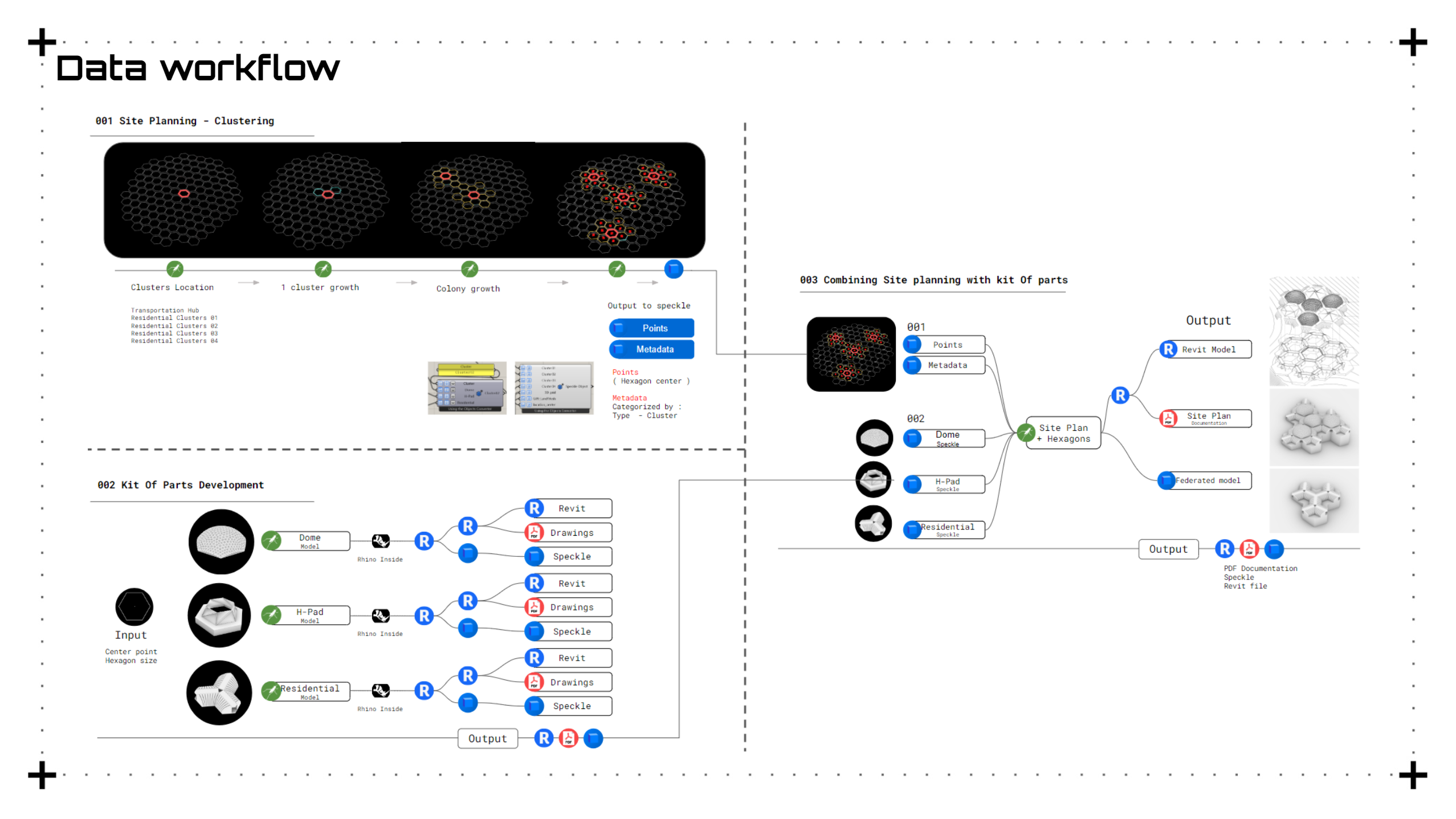
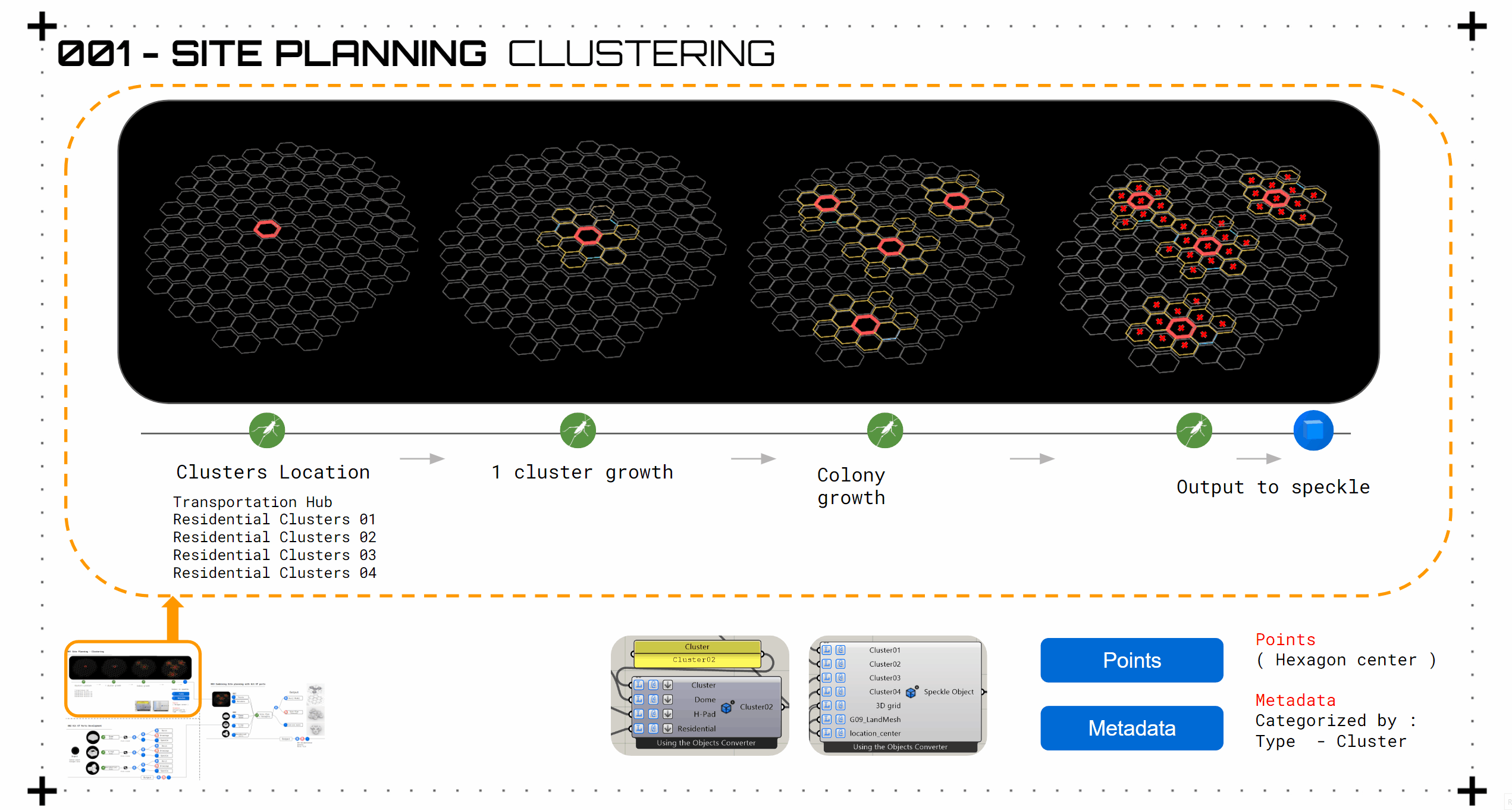
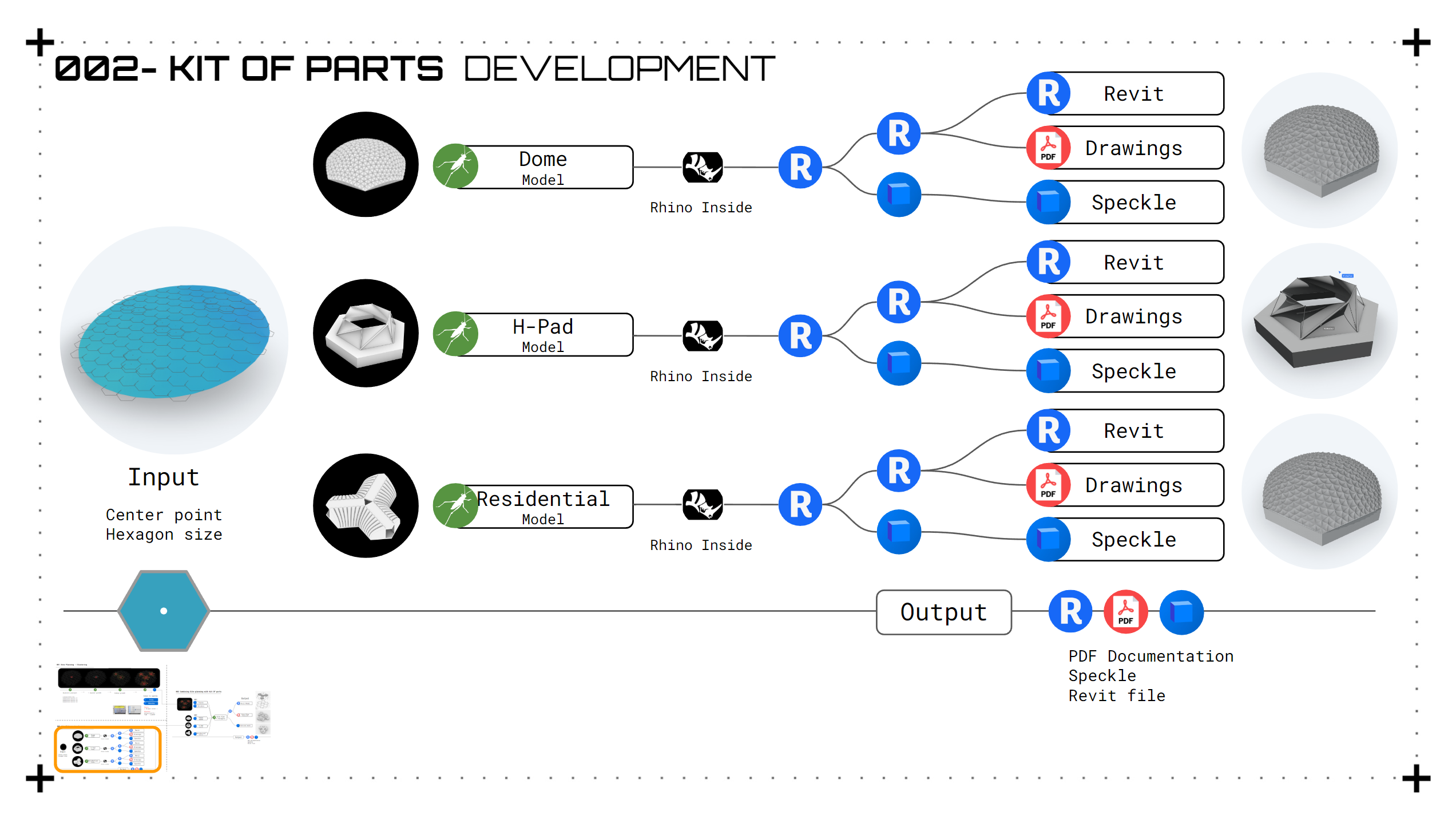
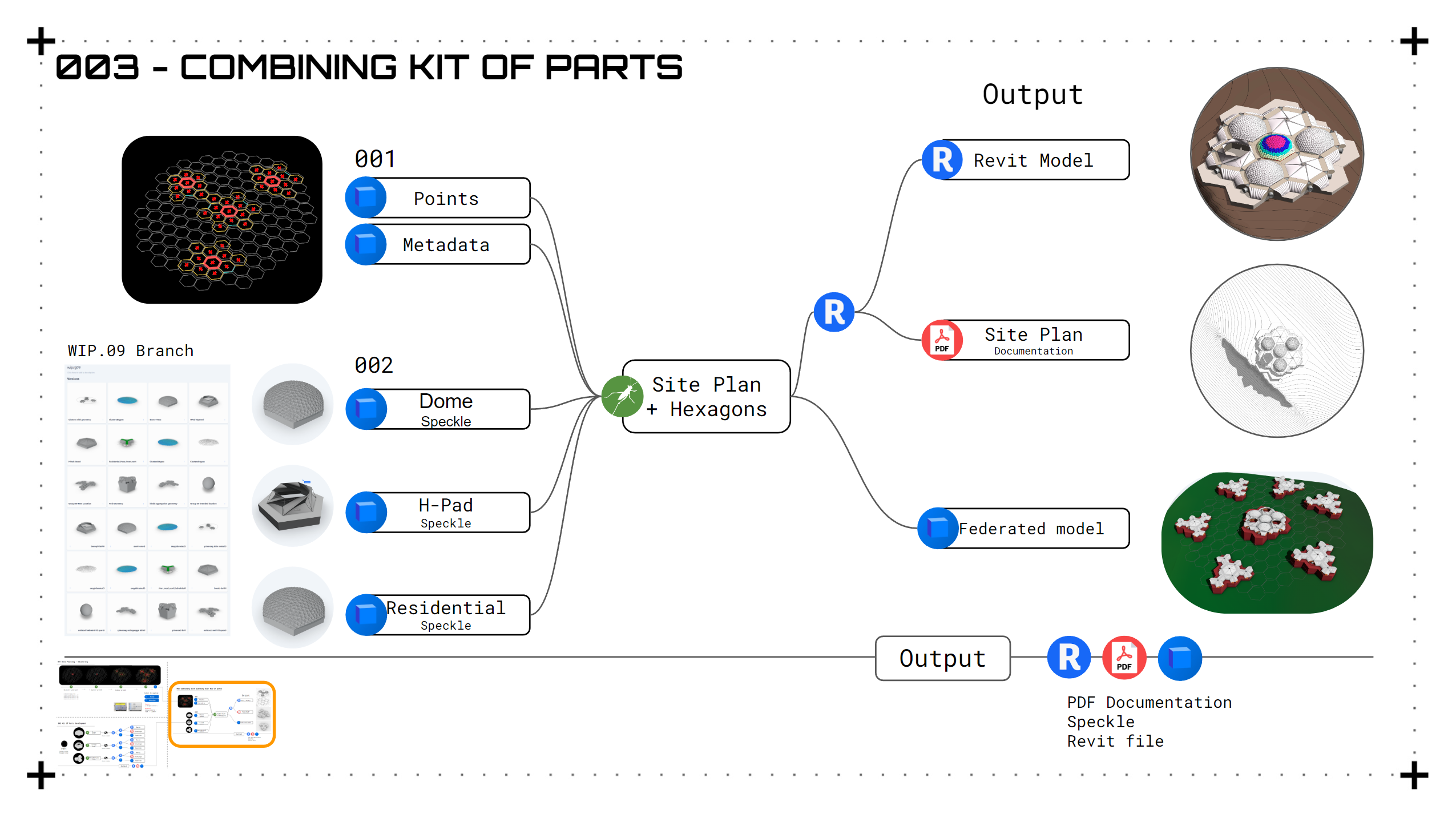
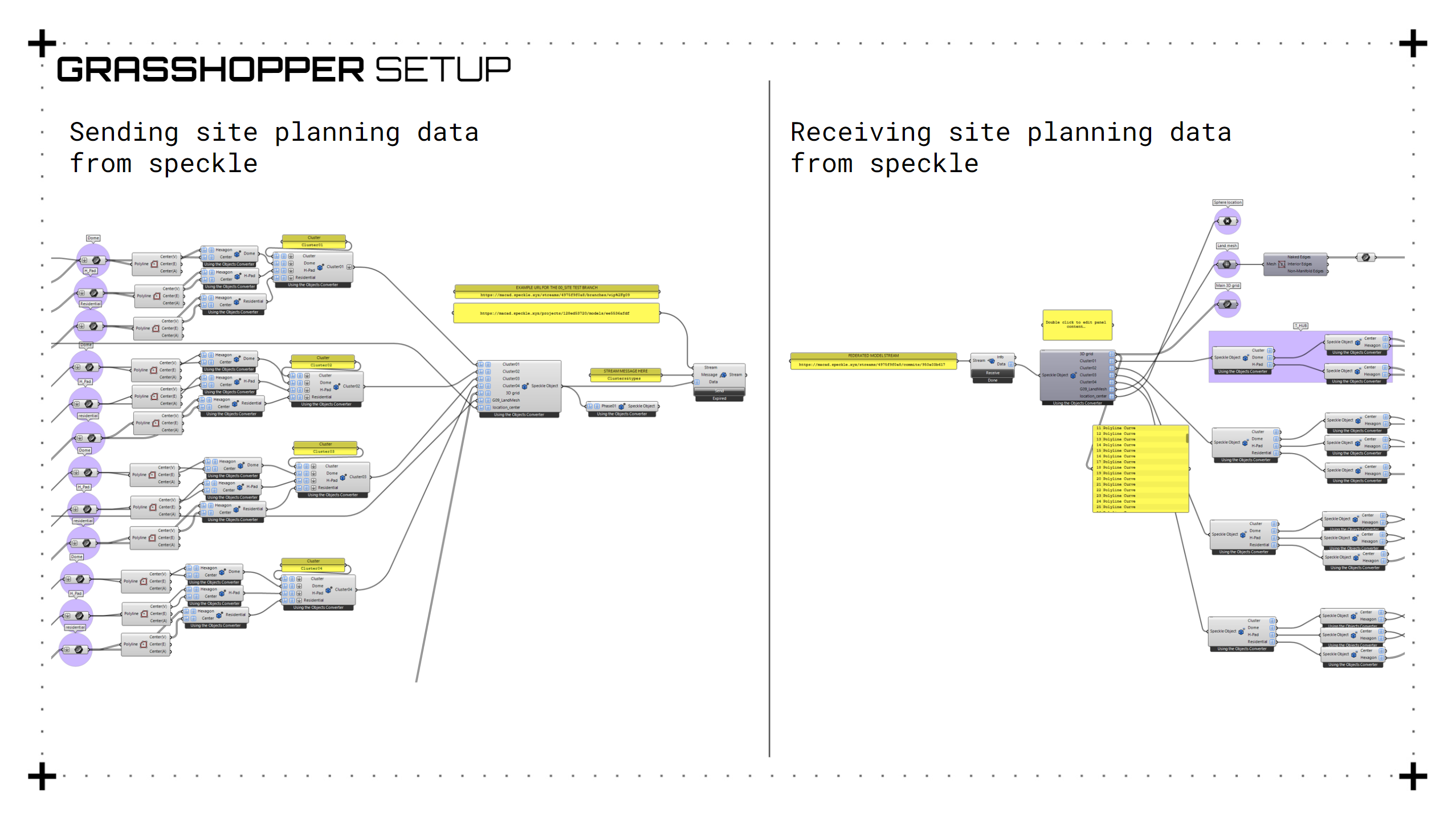
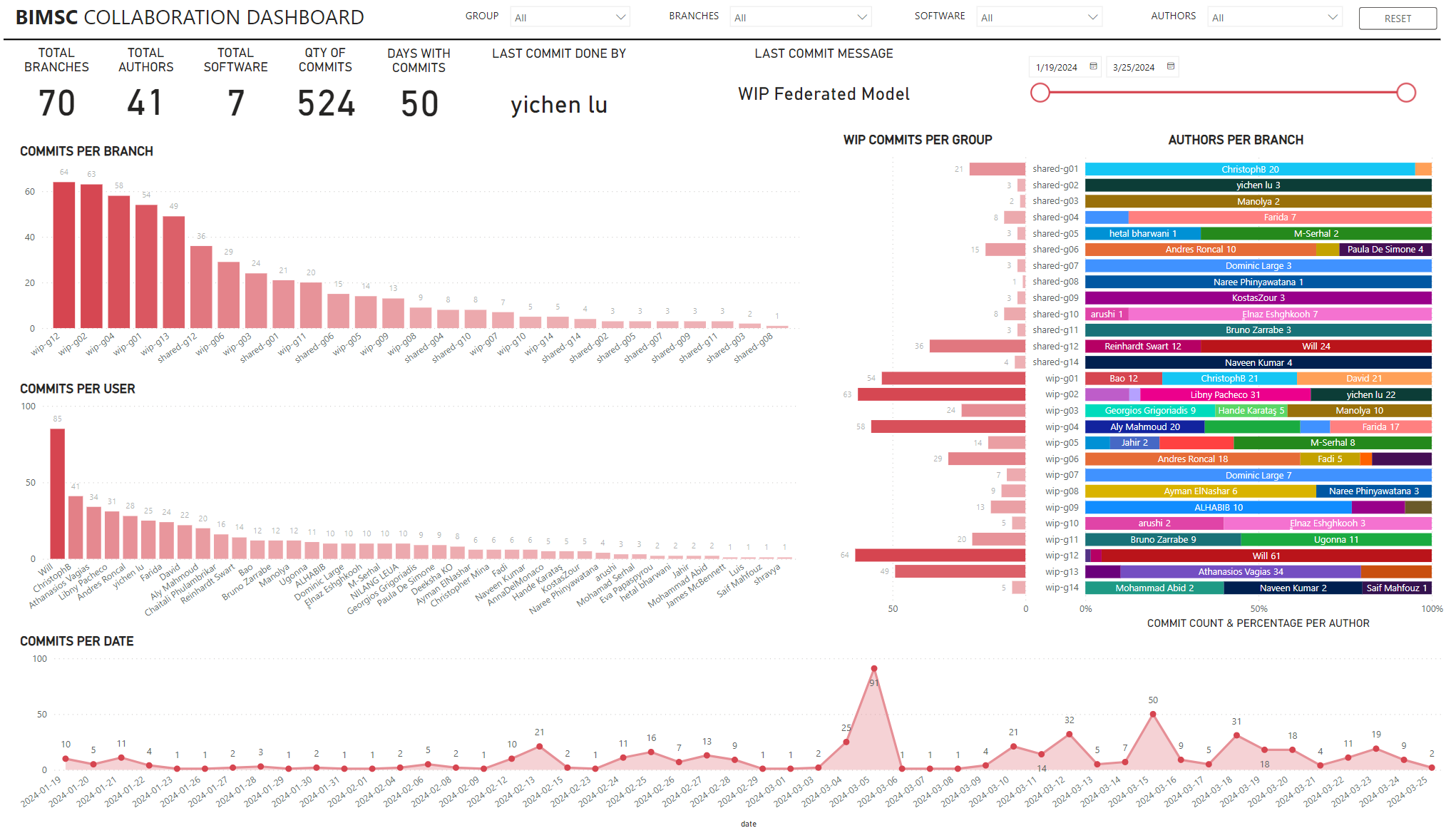
_Speckle Automation BOT
The Speckle Bot represents an integration of Grasshopper, Revit, Fly-io server, and Speckle, streamlining the workflow for controlling elements such as the opening of the helipad. Initially, accessing Grasshopper files for adjusting the opening size via Kangaroo simulation posed challenges for users. However, with the development of the bot, users can now effortlessly input the desired opening size as a Revit native parameter, send the information to a Speckle stream which is then processed and manipulated based in our Grasshopper definition which now leaves on the cloud (Fly-io) and then receive the new updated geometry into another Speckle stream which is directly linked with Revit and we see our final geometry right in our screen. No plugins No Rhino.Inside from the user is needed and that’s how we simplify complex processes for professionals from different backgrounds that use Revit.
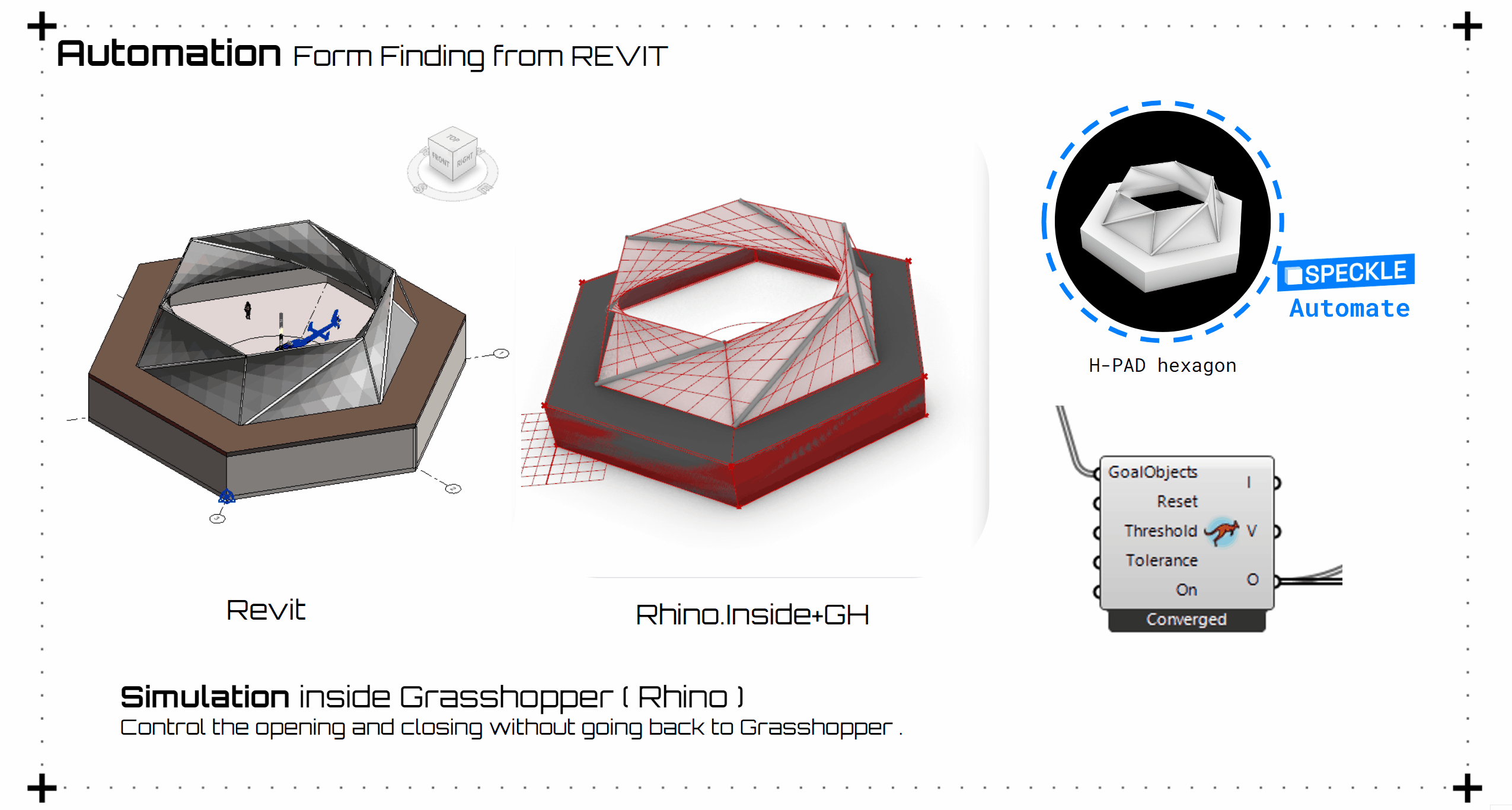
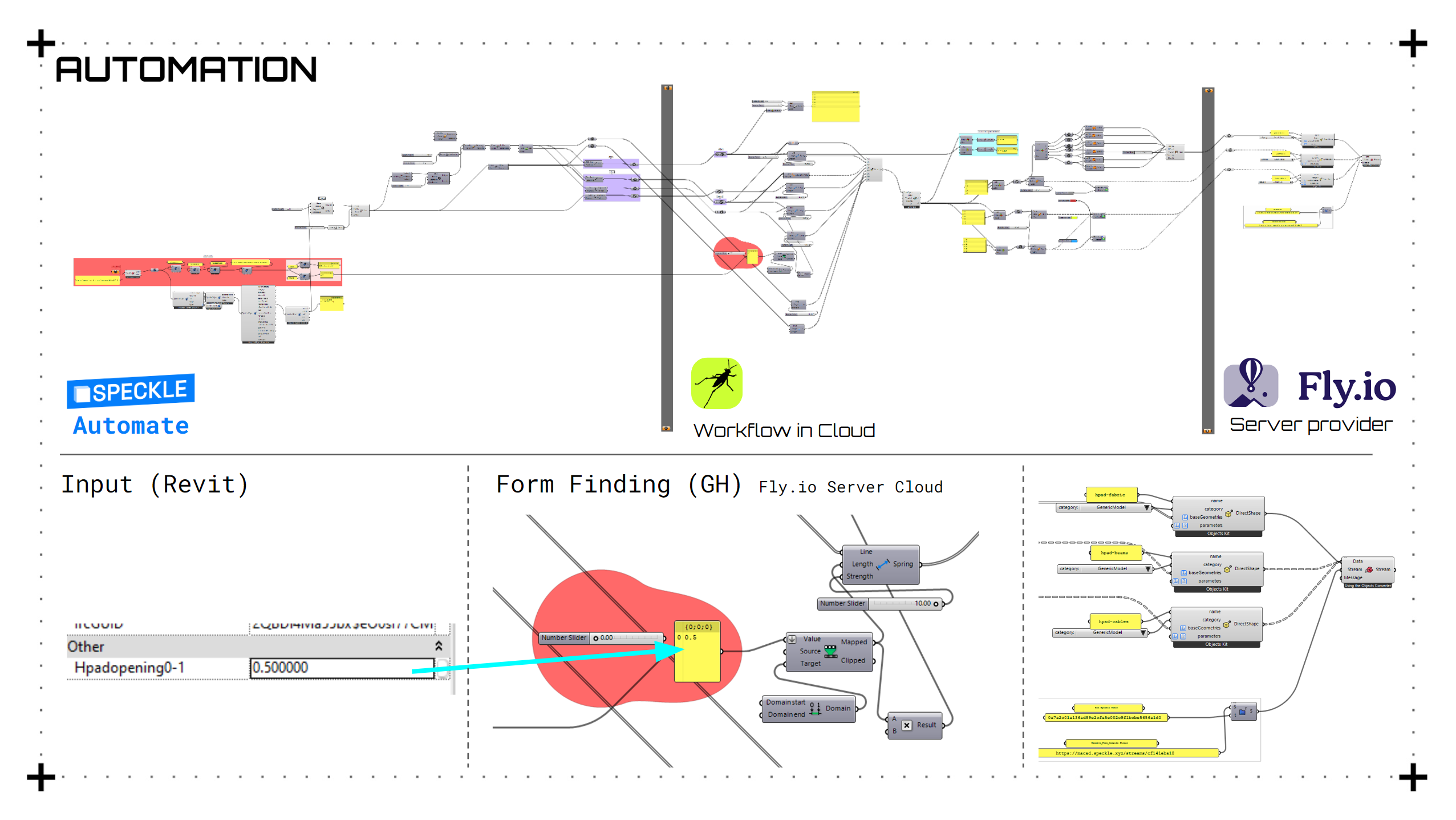
Speckle BOT Demonstration
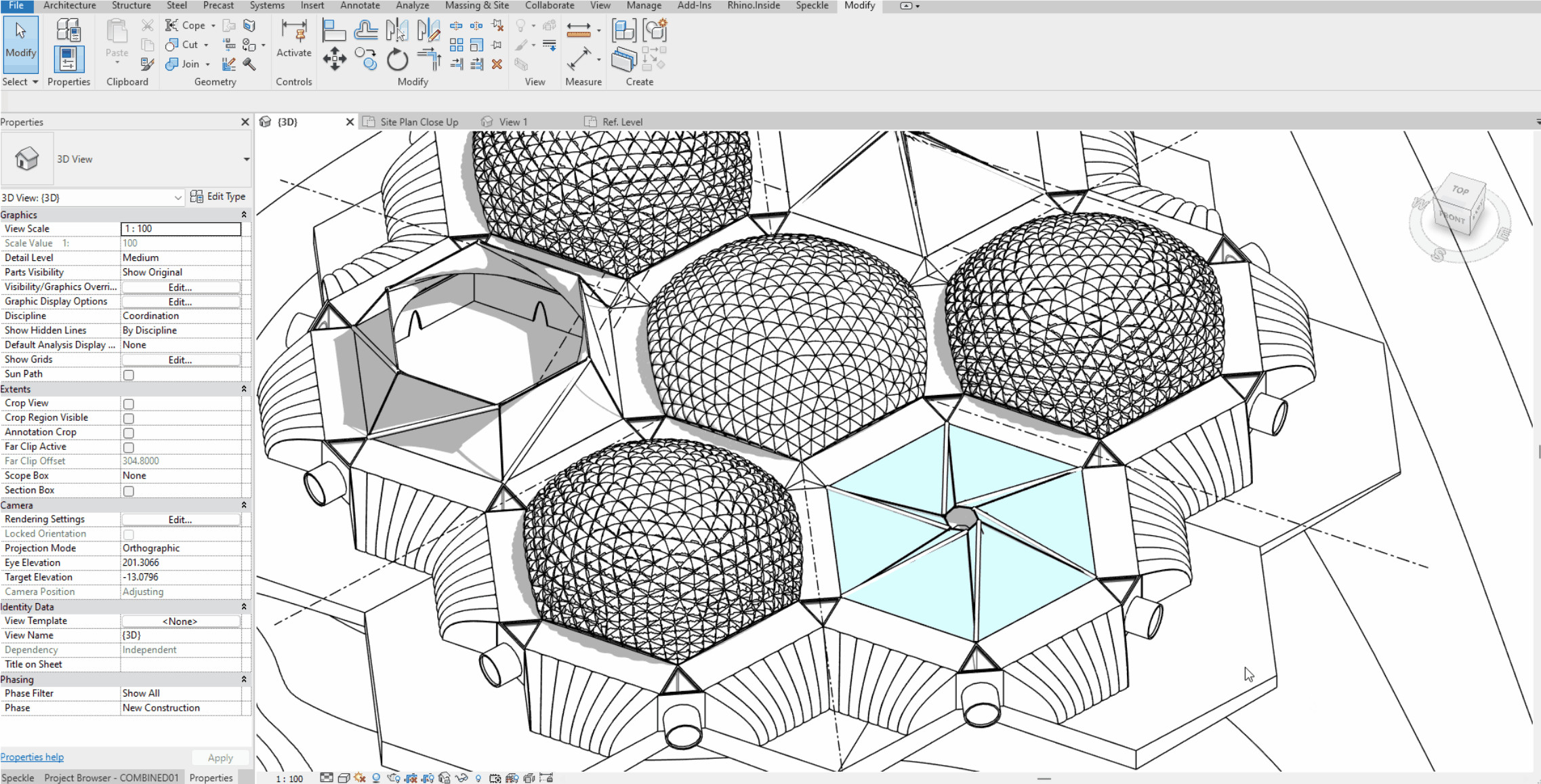