The construction industry has shown an increasing interest in adapting to more environmentally friendly materials, with wood gaining popularity as a natural and sustainable option for buildings. However, the wood industry contributes a significant percentage of energy consumption during the entire wood lifecycle, encompassing tree cutting, transportation to sawmills, and delivery to construction sites. Additionally, the timber production cycle for construction purposes often results in a substantial amount of wood offcuts and logs that do not meet the standards for the construction market and end up either buried, burnt or down-cycled in products of lower value. This study recognizes the pressing need to address the environmental impact of the timber industry by exploring the potential to add value to wood offcuts and utilize them within the building industry. Given the recent advancements in artificial intelligence (AI) across various technological domains, this paper aims to demonstrate the effectiveness of integrating AI technologies into computational design and digital fabrication, thereby enhancing the utilization of leftover wood in achieving an exemplary architectural surface.
Research Aim
Our goal is to achieve innovative and sustainable surface designs using marginalized wood offcuts. The research aims to develop a seamless material informed design, that follow the wood grains by utilizing modern digital scanning technology, data processing and digital fabrication.
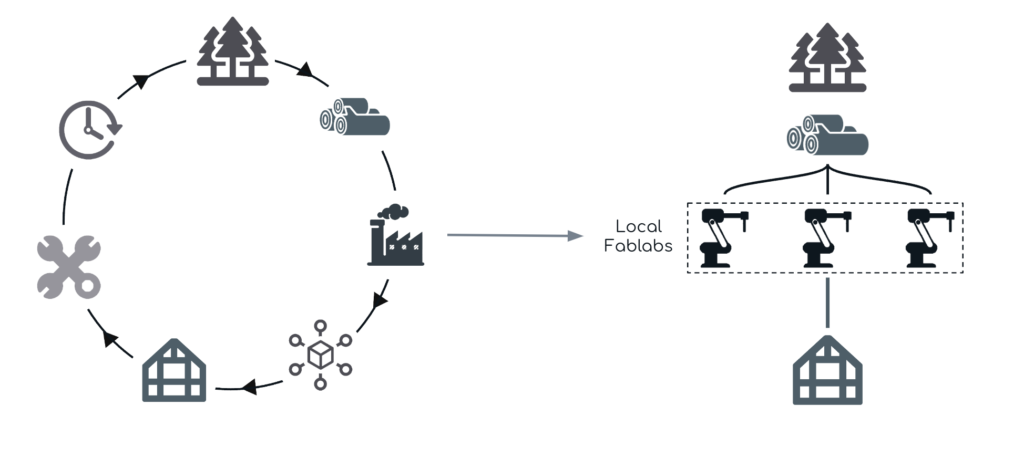
Research Methodology
The research comprises three primary sectors. The initial sector focuses on the development of a digital material library for irregular wood off cuts, utilizing advanced computer vision techniques to scan and process data. This process enables the creation of a comprehensive digital representation in both 2D and 3D dimensions, mirroring the physical wood planks. The second sector is the material to design, it involves material design exploration, utilizing a material-based design algorithm to unlock potential design opportunities derived from the created material library. The investigation spans from flat surfaces to single and double curved surfaces, exploring various levels of design freedom. Lastly, the design to fabrication sector investigates the discretization strategy of the final design, translating it into pre- assembled panels with varying finishes. The panels are equipped with alignment features to facilitate convenient on-site assembly, ultimately achieving the desired target geometry.
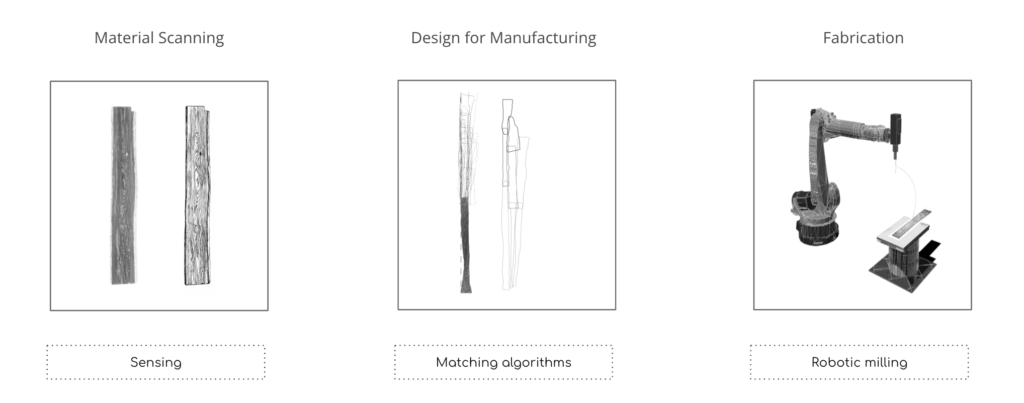
As a journey of exploration, the research focused on different levels of complexity of facades. Starting from normal edge matching and planks stacking on a flat surface, to more complex single directional curved surface and double curved surfaces as seen below.
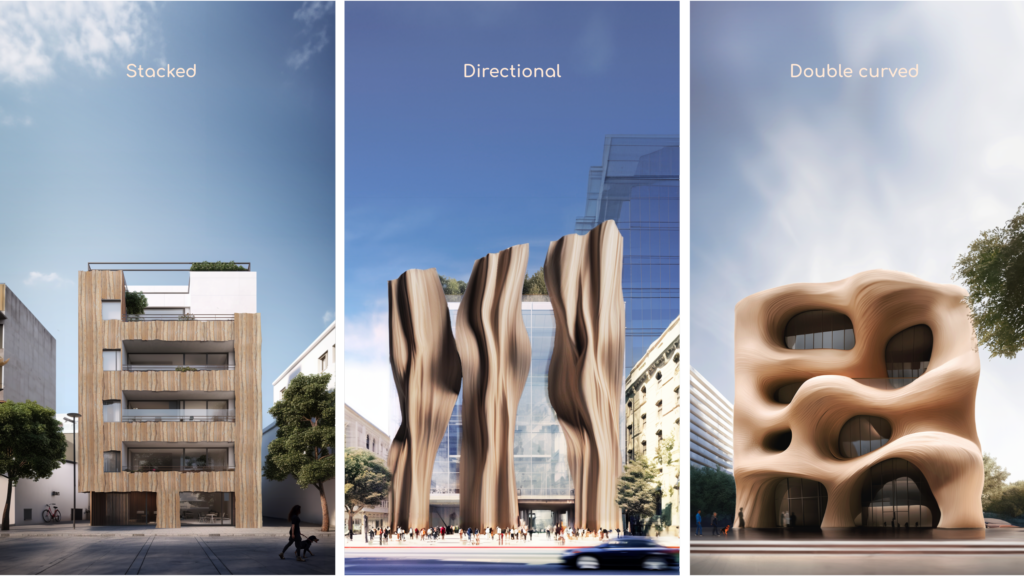
Material Scanning
The stage aims to collect data of the provided planks in terms of size, dimensions, timber grains and store them into a digital library for each provided off cut plank. The extracted data is validated, processed and collected all in one data package that are then transferred to the next stage.
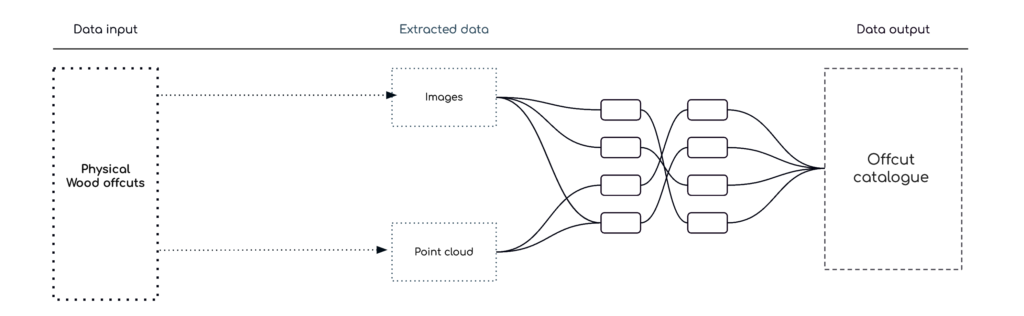
The 2D data extraction process is based on taking high quality images of the wood planks, unwarp the images to make sure it is the right scale with no distortion, then processing the image to extract the outer curves that represents each plank and last but not least a validation test is carried to make sure the data is identical to the real data of the planks as shown below.
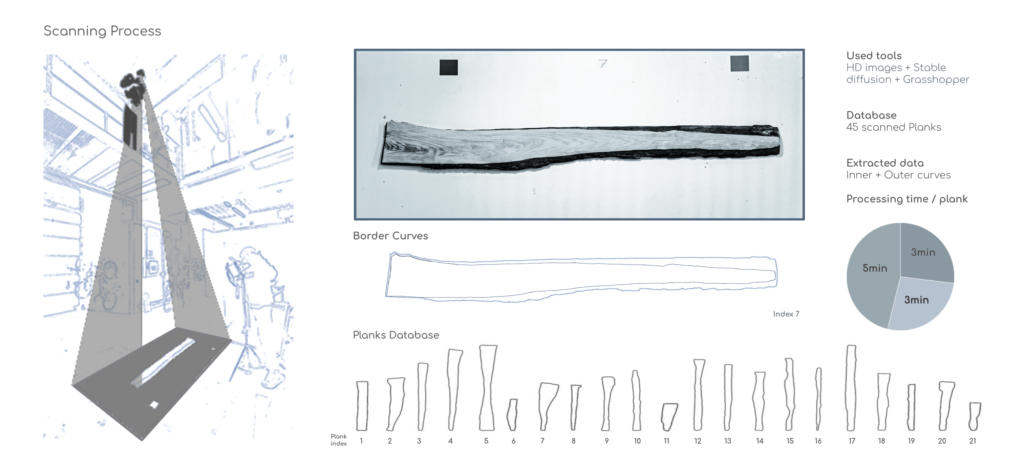
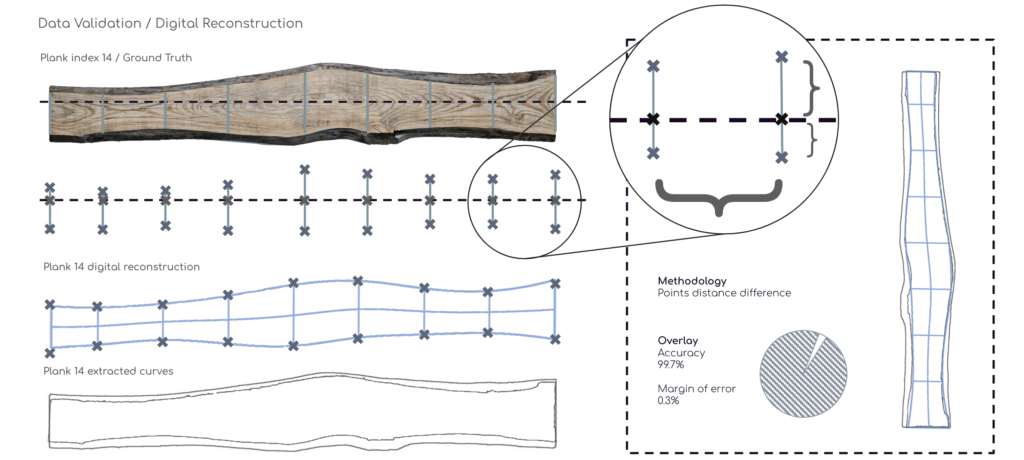
3D data extraction is based on photogrametric scanning
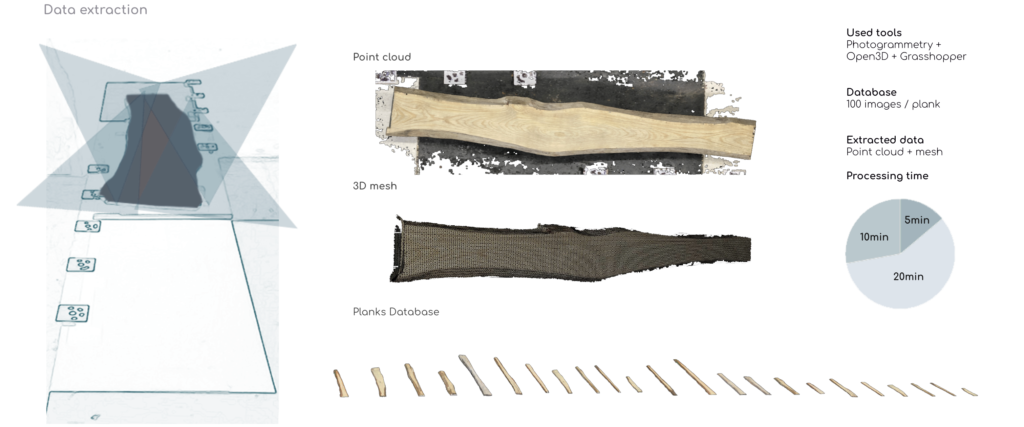
contact us
mail – [email protected] | instagram – re.al.form