UP-CYCLING CDW THROUGH RAMMED EARTH TECHNIQUE
The project promotes a circular economy for construction demolition waste (CDW), focusing on concrete and brick materials. It investigates the creation of a material system that integrates data-driven demolition mapping, innovative material reuse, robotic manufacturing and a meticulous approach to designing the life-cycle of the material. It uses the rammed earth technique to create durable panels and modular components from CDW, reducing environmental impact & enhancing resource efficiency.
By blending traditional methods with advanced technologies, the project delivers scalable, sustainable solutions, transforming building practices, reducing the accumulation of anthropogenic mass on the planet and promoting a regenerative, resilient built environment.
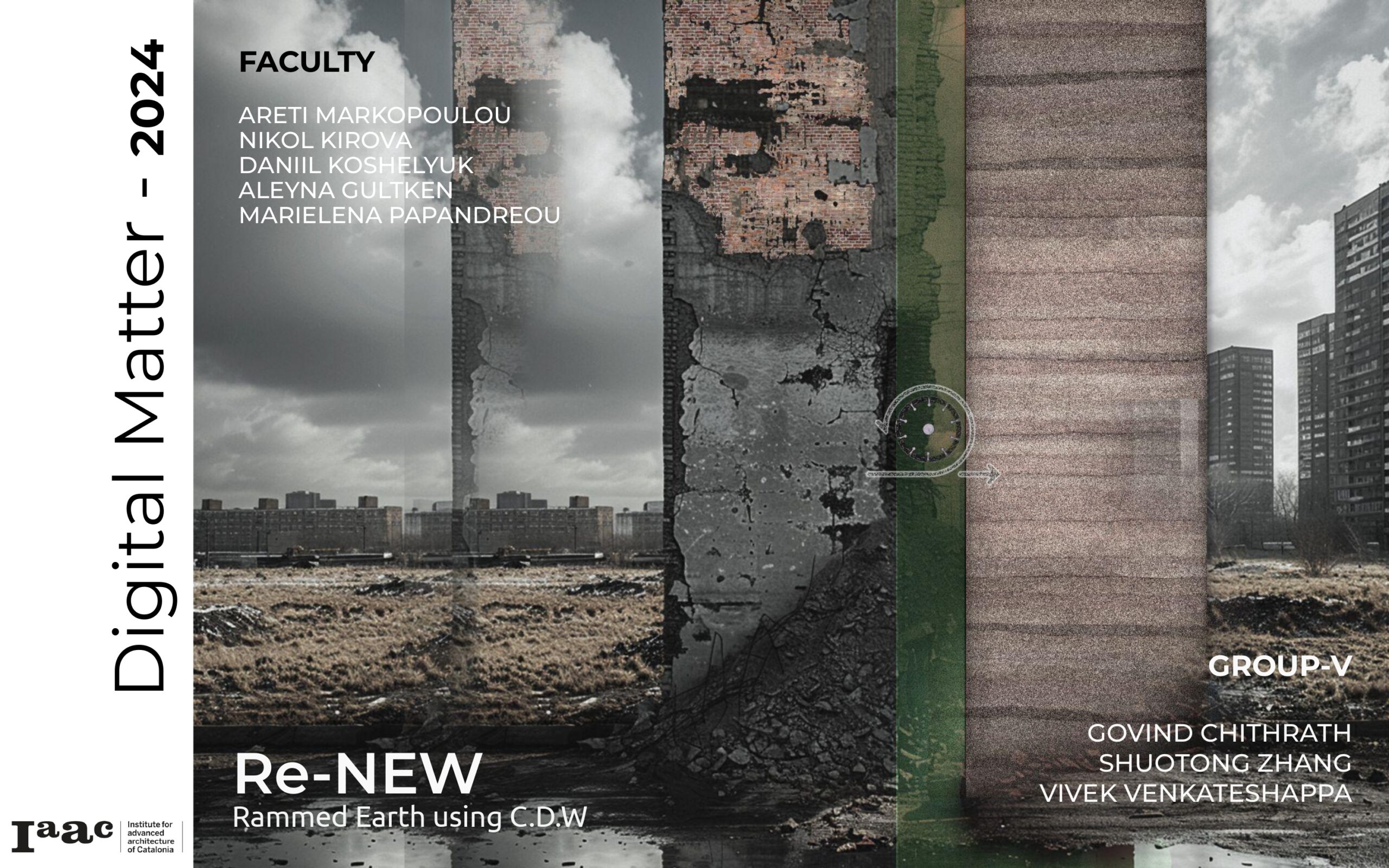
CONTEXT
In today’s fast-evolving urban landscape, the construction and demolition sectors pose significant environmental challenges. Their role in escalating carbon emissions and contributing to the accumulation of anthropogenic mass—particularly through vast amounts of construction demolition waste, predominantly concrete and brick—demands urgent attention.
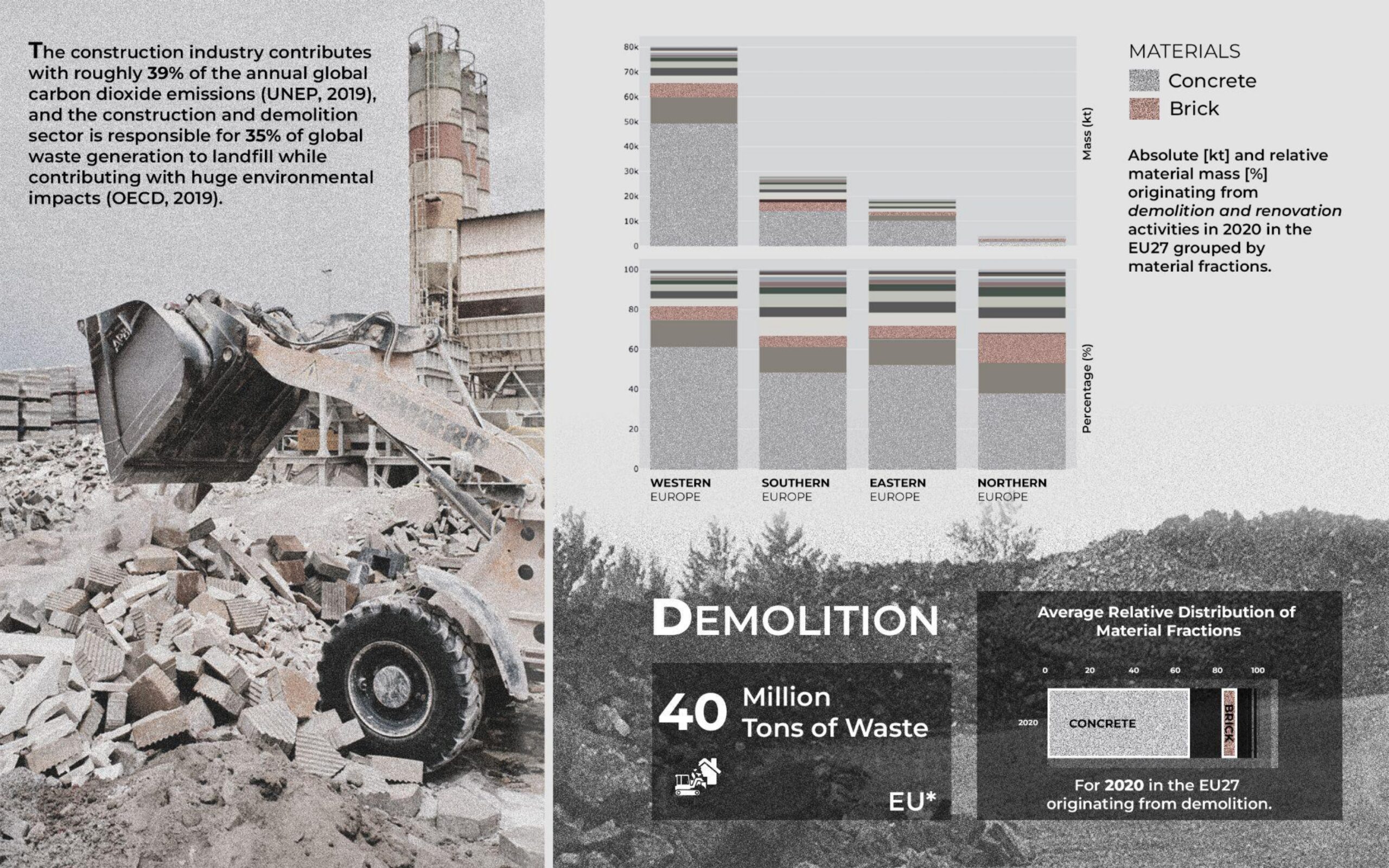
Spain’s recent enactment of Waste Law 07/22 reflects a pivotal response to these issues. The project is aligned to this framework and the country is taking the necessary steps to promote circular material usage. Our emphasis on utilising bricks and concrete arises from understanding the composition of CDW in Spain and the volume of it‘s footprints.
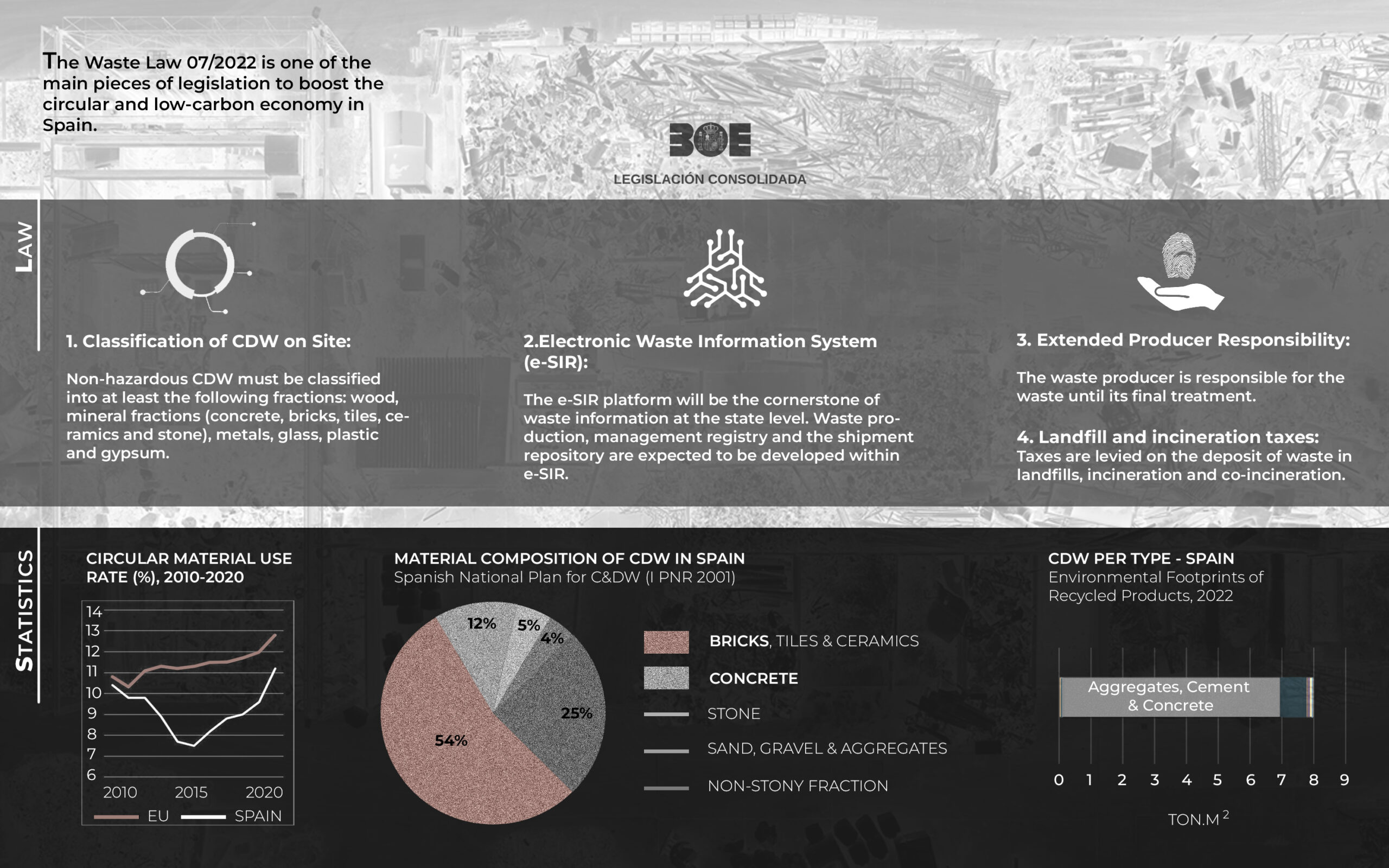
PROJECT OVERVIEW
In addressing the pressing environmental challenges of the construction and demolition sector, this project is structured around three transformative dimensions. First, we aim to re-think demolition through data-driven programming, optimising processes for efficiency and sustainability. Second, we focus on reusing materials by leveraging their compositions, thus minimising waste and promoting circular economy principles. Third, we embrace re-manufacturing through a robotic vernacular process, revolutionising the way materials are repurposed. Together, this approach strives to reshape the life-cycle of construction demolition waste, paving the way for a more sustainable future.
Together, this approach aims to reshape the life-cycle of demolition waste for a sustainable future.
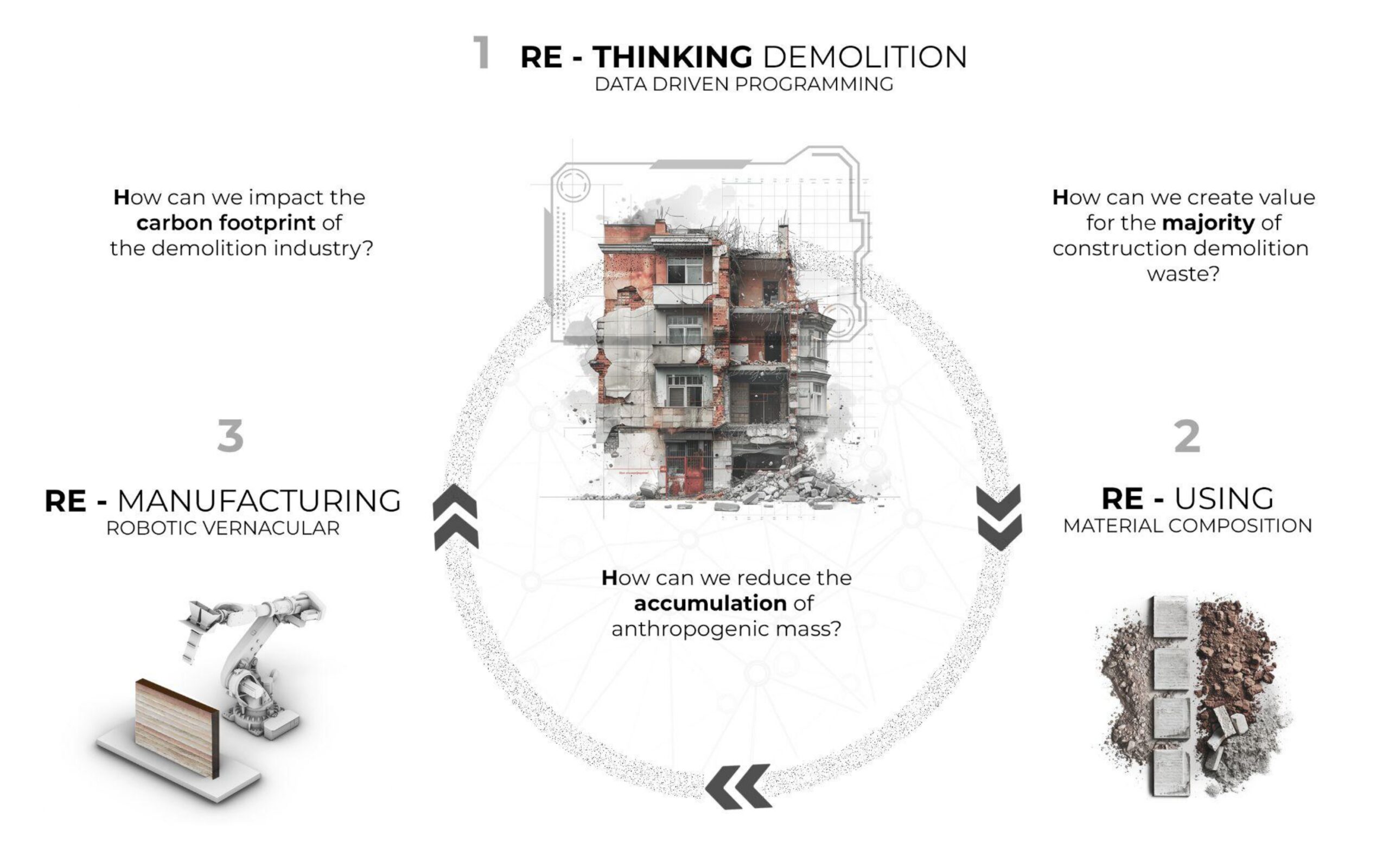
RE-THINKING DEMOLITION
In the process strategy, buildings are carefully analysed and segmented to extract specific quantities of concrete and brick. These materials are then meticulously processed into finer particles, ready for transport to facilities, whether on-site or off-site, based on the situation.
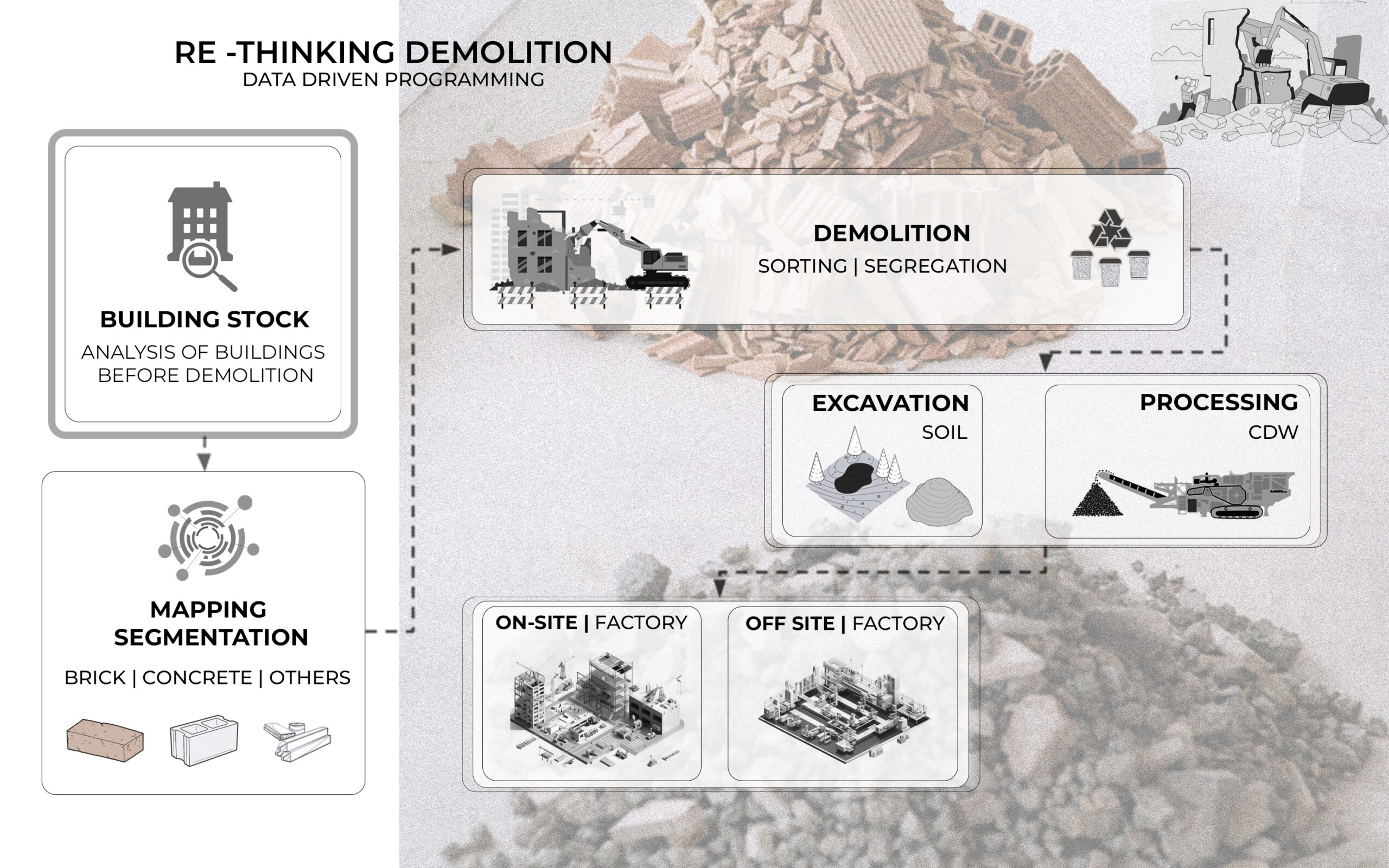
The project‘s core strategy for material mapping integrates advanced object detection systems powered by machine learning. Through the layering of cutting-edge strategies, the algorithms can be refined to achieve superior accuracy. This data serves as the foundation for strategic demolition planning, enabling efficient material utilisation.
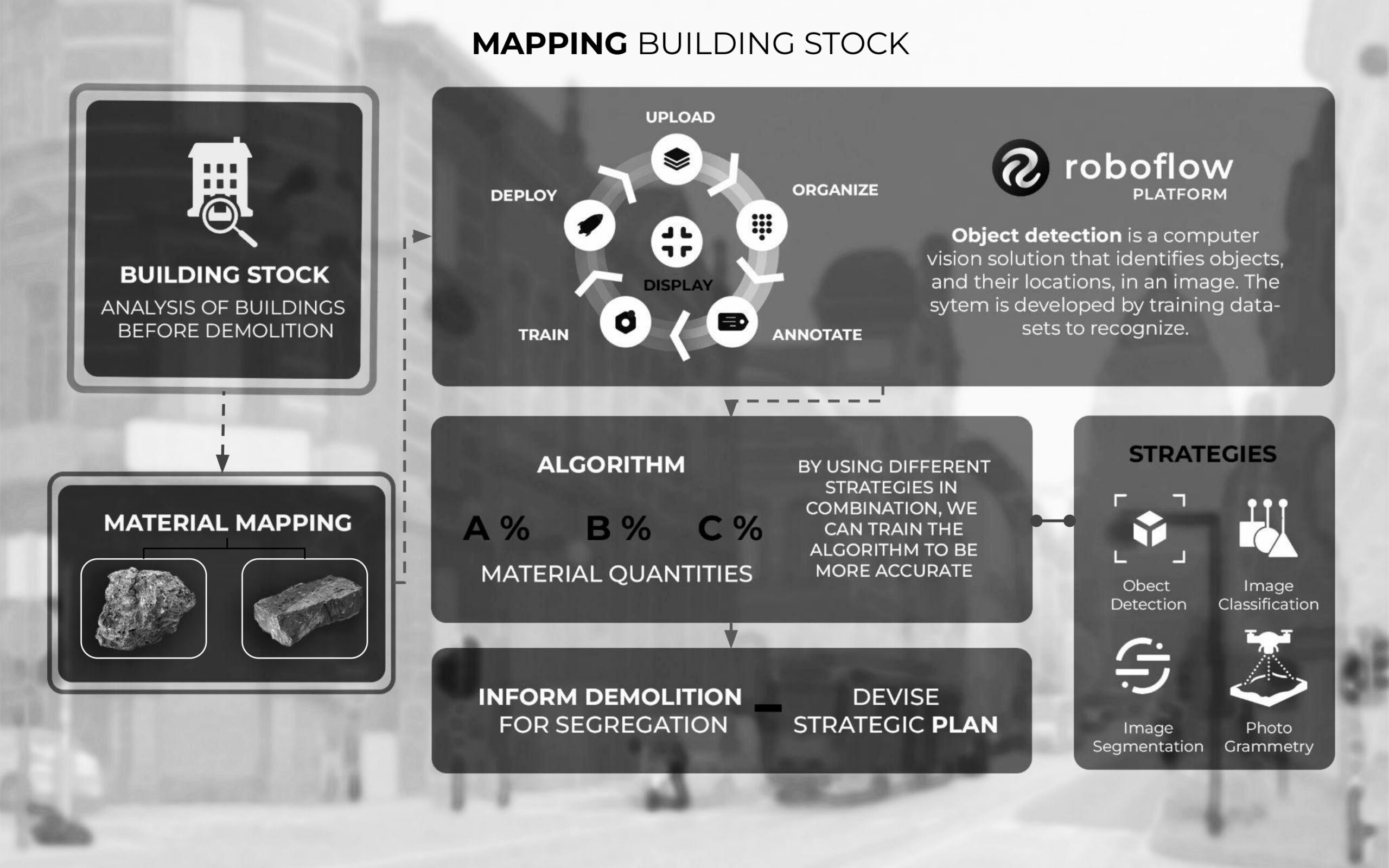
MATERIAL SEGMENTATION
Roboflow has been instrumental for the identification of core materials: concrete and brick. Leveraging its platform, we pre-process and augment data to train robust computer vision models. This allows us to accurately classify and categorise materials, enhancing our capability to manage and up-cycle them effectively in various applications.
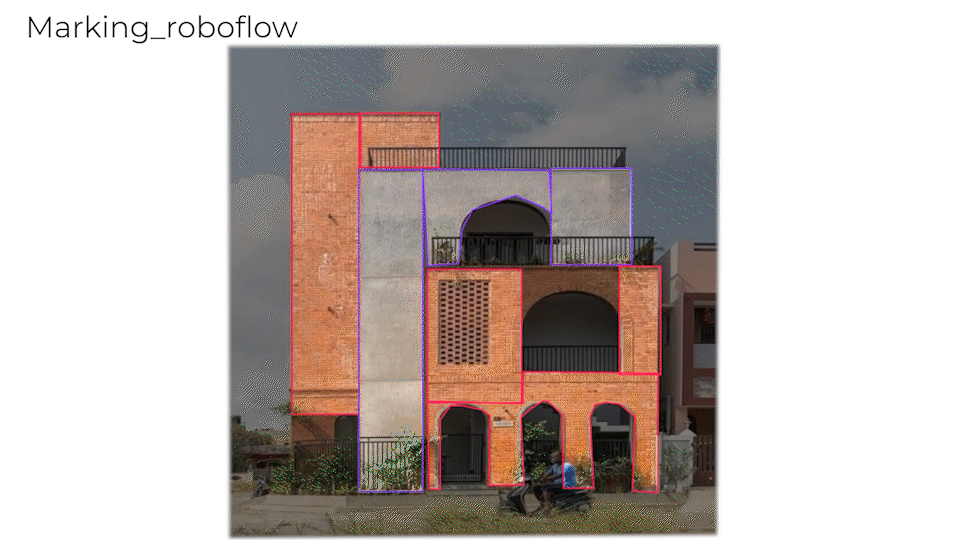

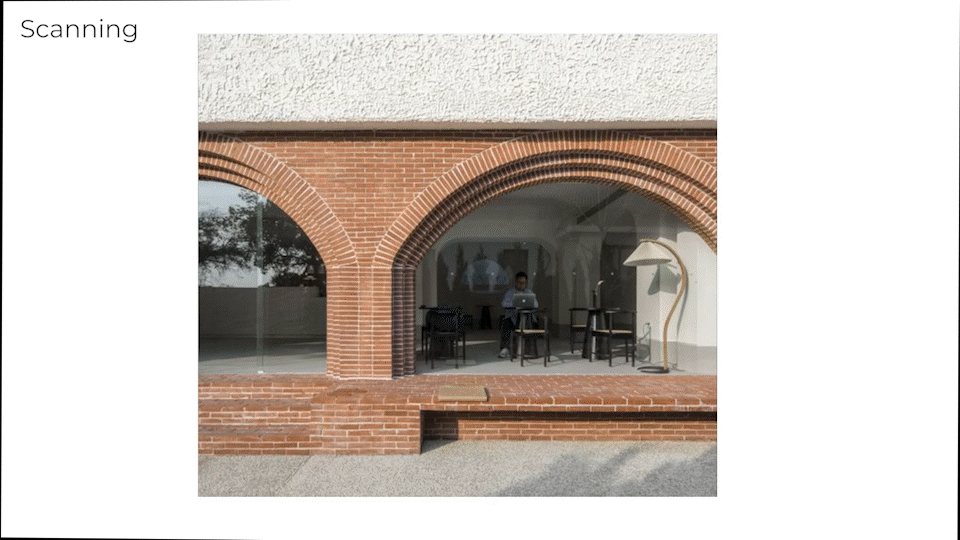

RE-USE
The project draws inspiration from rammed earth, a timeless vernacular technology. Explore the rich material composition and intricate processes inherent in this innovative approach, essential for shaping and setting up the fabrication framework required for strategic implementation.
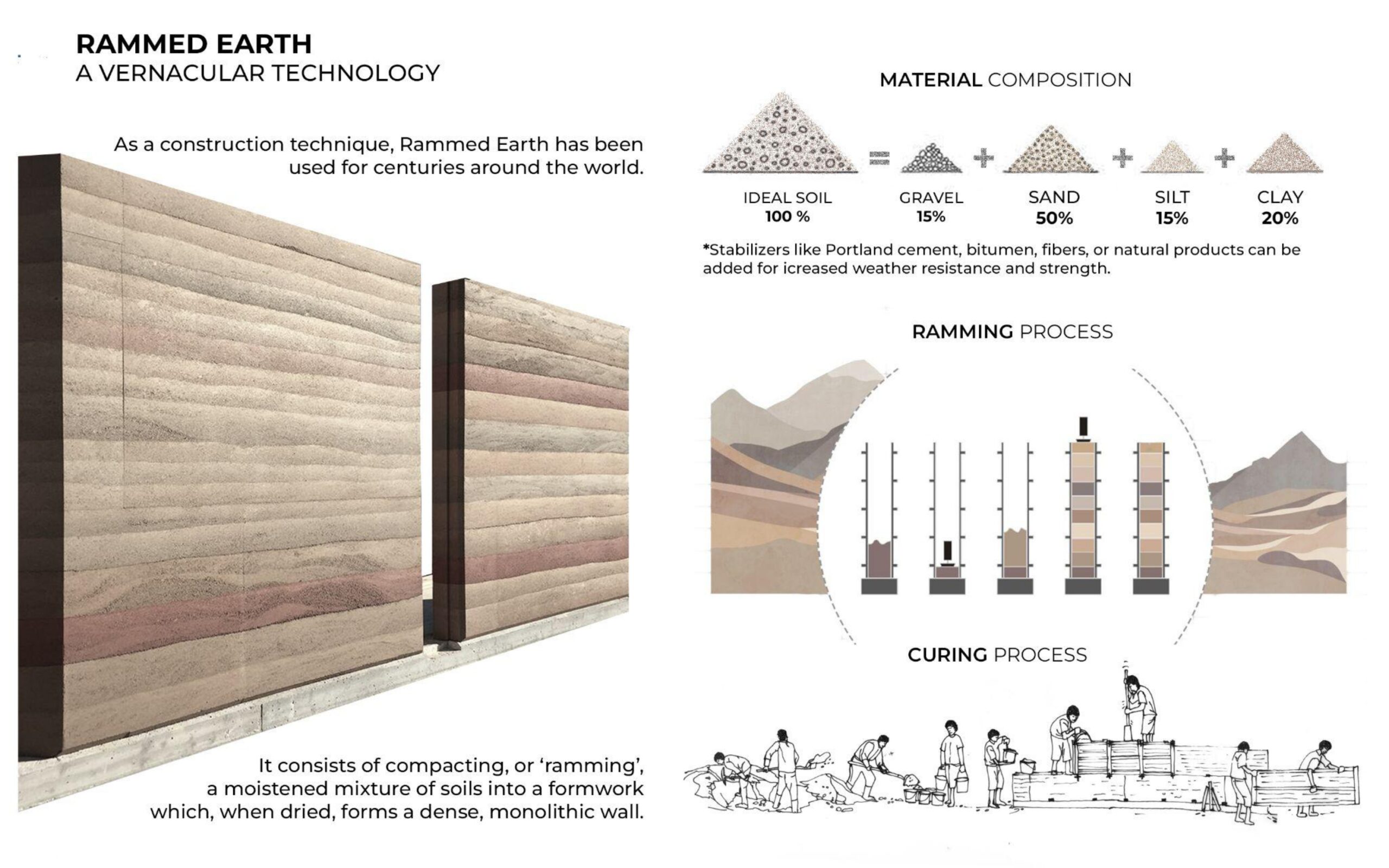
There is a meticulous artistry behind rammed earth construction. This overview through its in-situ process unfolds from the initial earth excavation and precise material sifting to the controlled pouring, methodical ramming, and careful removal of form-work. Each step showcases the craftsmanship and sustainable principles that define this ancient yet innovative building technique.
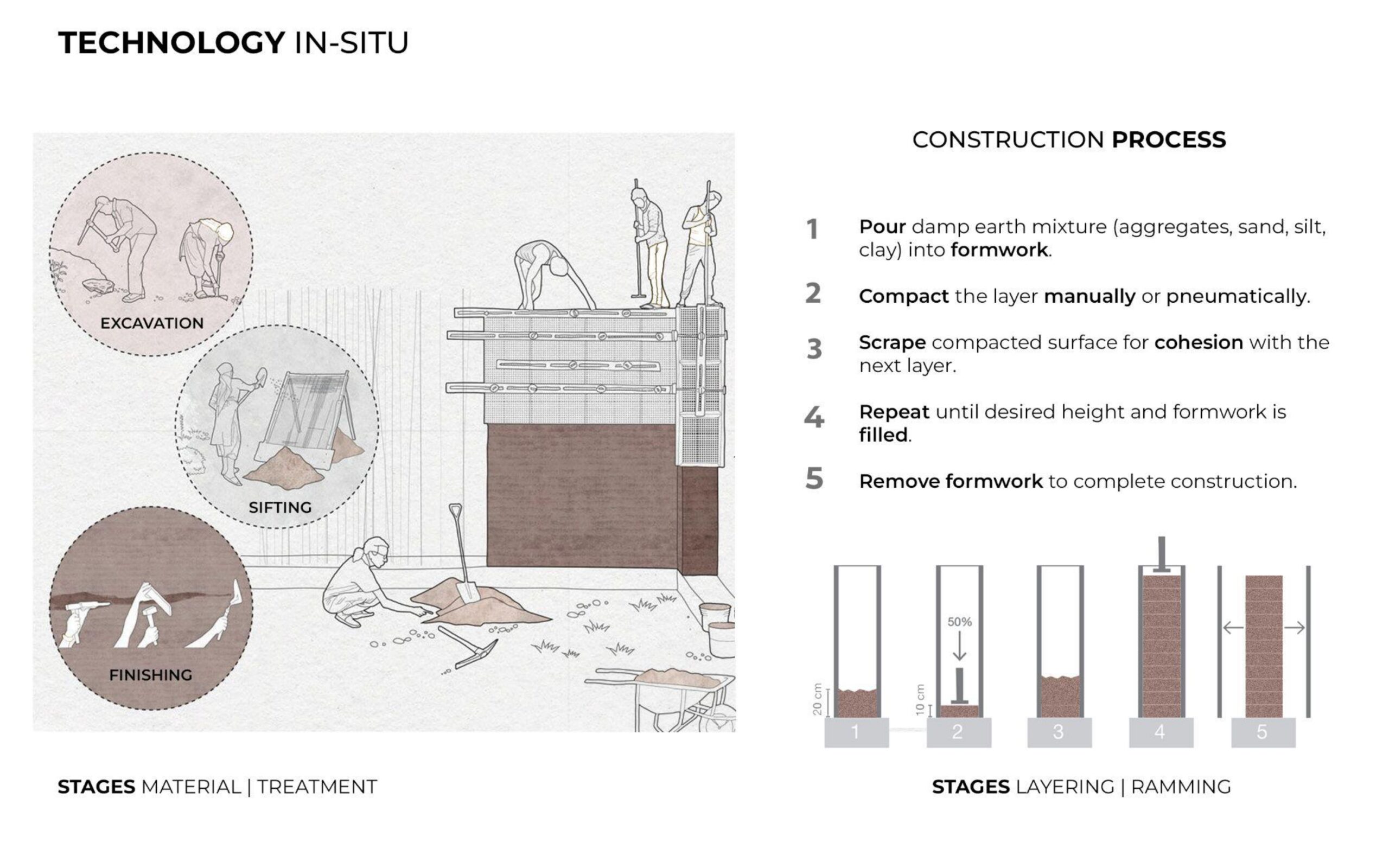
The streamlined process of prefabricated rammed earth, highlights modern efficiency. From standardised form-works and automated pouring to meticulous inspection, each step ensures quality and consistency. This approach tends towards standardisation, facilitating seamless transport and installation on-site. Balancing innovation with uniformity, it reflects the evolving challenge in the construction sector.
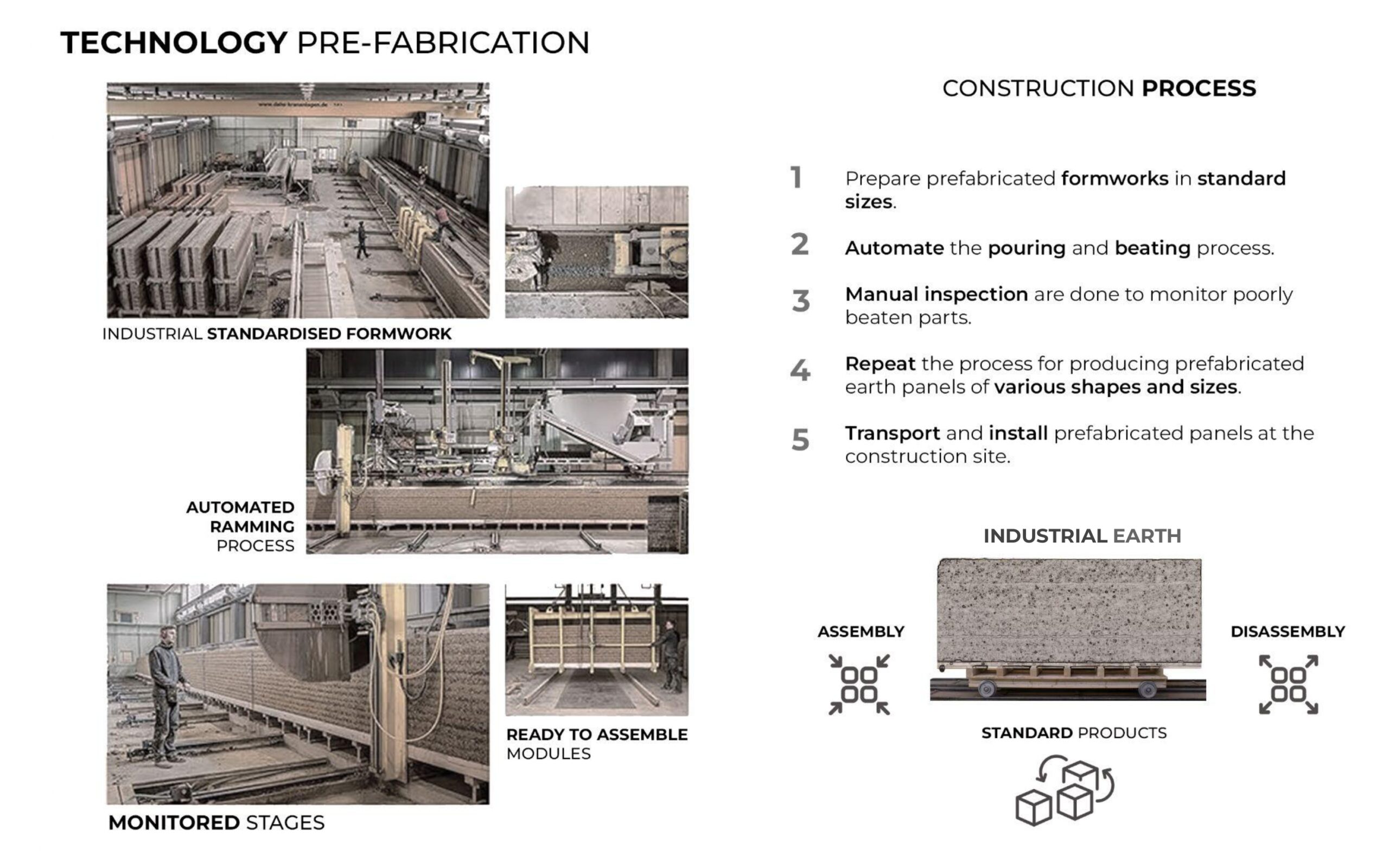
Modular components offer unprecedented flexibility in design, alongside customizabilty and ease of transport, ensuring superior quality control and minimal waste. With fast, efficient setup, this approach exemplifies sustainability, paving the way for cutting-edge prefabrication of customizable, environmentally-friendly products.
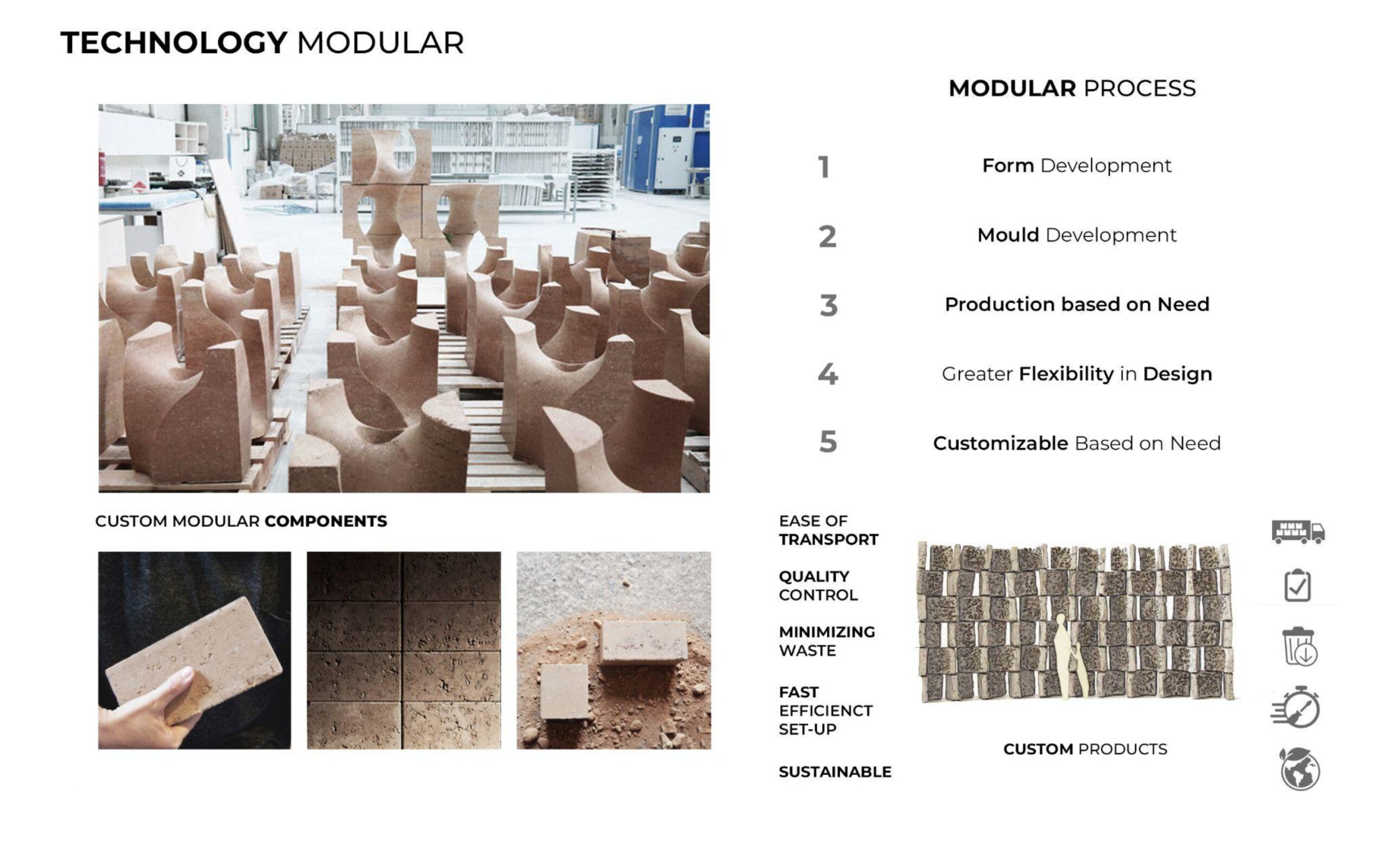
The illustrated process outlines a systematic workflow and material composition for the project‘s novel construction approach. Beginning with the collection and sorting of Construction and Demolition Waste (CDW), it progresses through stages of crushing, grinding, and precise soil testing to ensure optimal soil characteristics. The resulting blend of CDW, soil, and cement represents a significant advancement in sustainable material reuse and progressive construction methodologies.
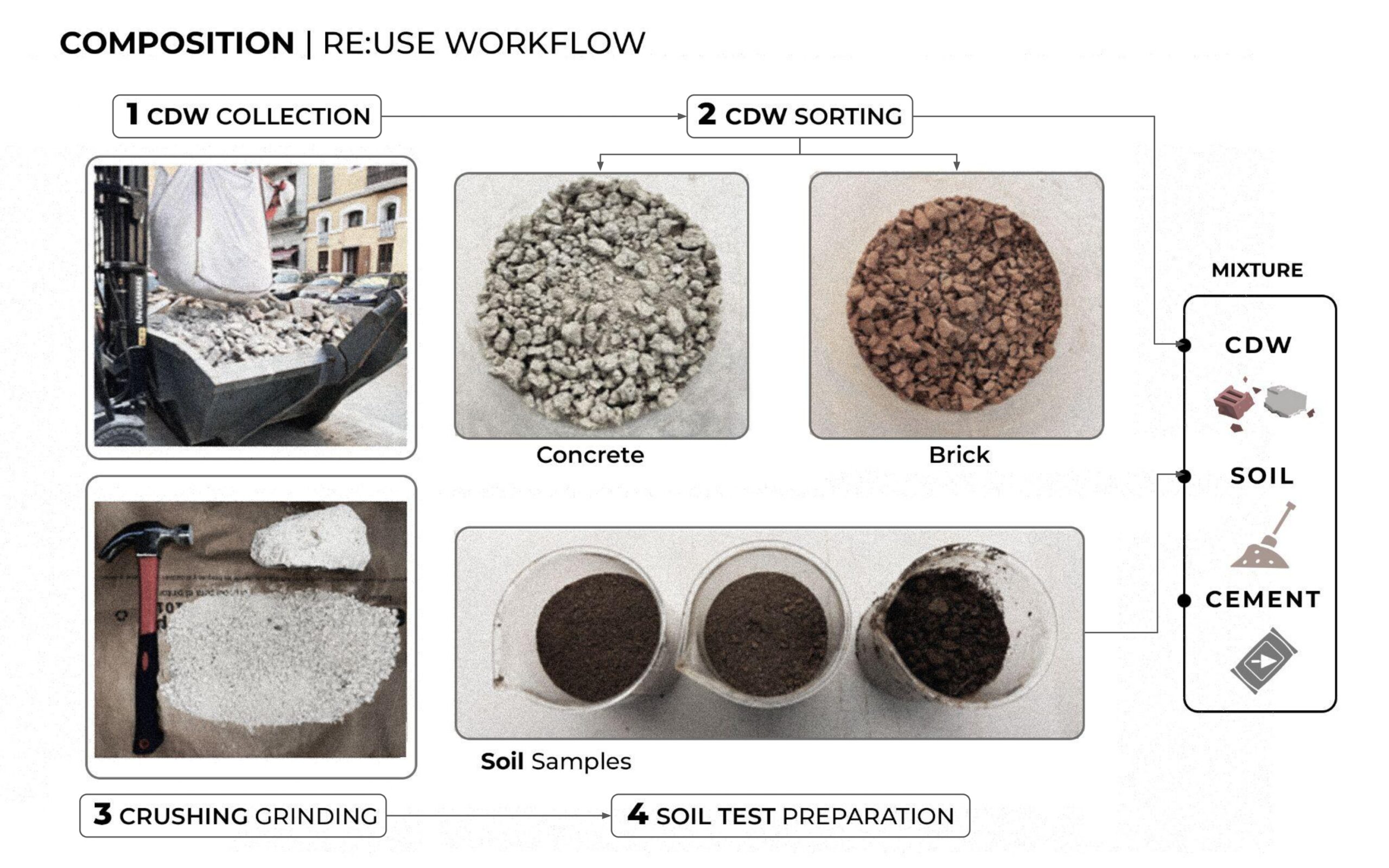
Highlighted are sedimentation tests on various soils and cube tests with different compositions, demonstrating the project‘s methodical evaluation of soil
characteristics and material performance. These tests lead us to a greater understanding of the material and it‘s nature.
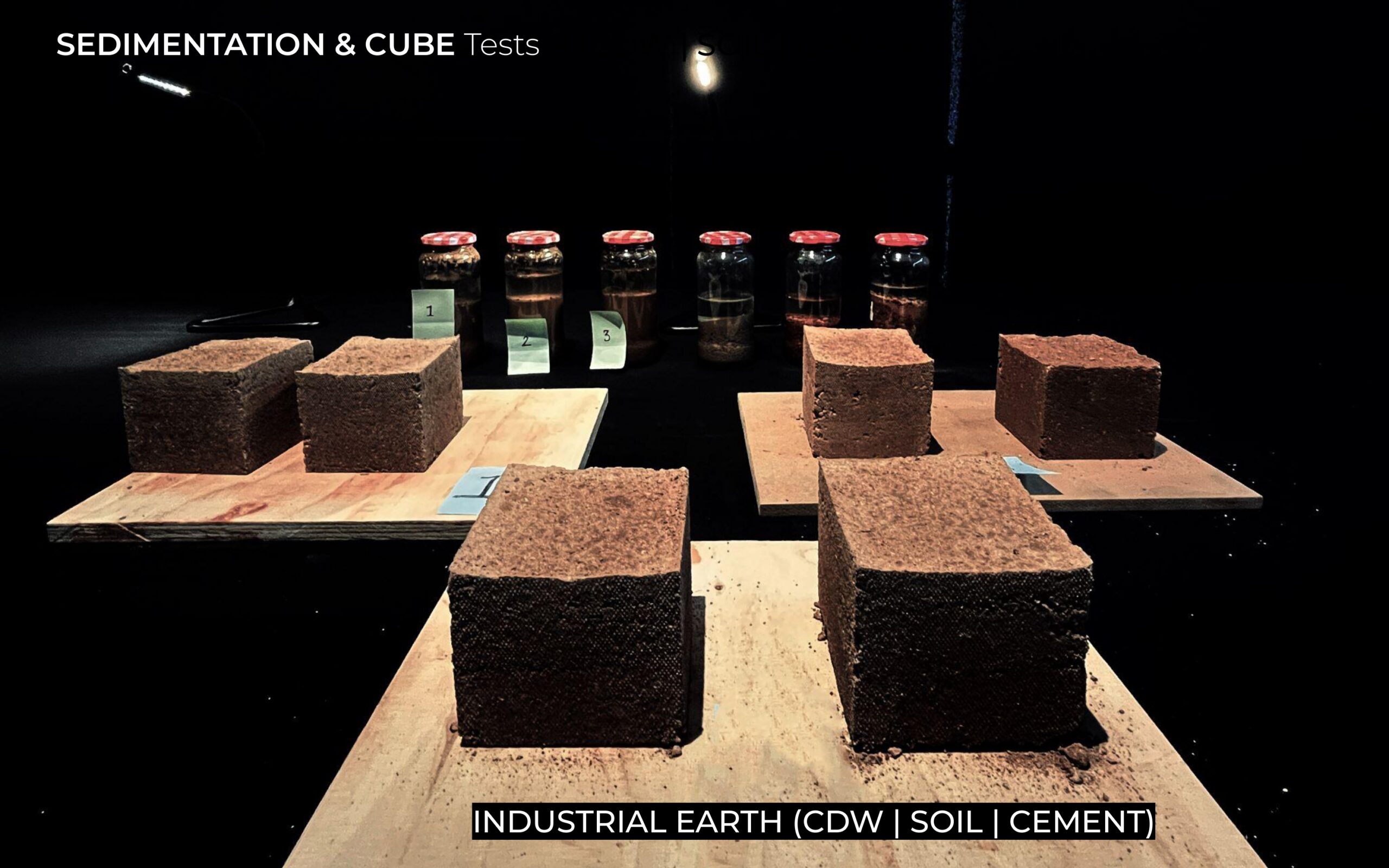
Presented are compressive strength analyses of different mixtures, showcasing their impact on material performance. Developed with varying strengths, these mixtures enable the choice of different performances based on specific needs, optimising solutions for diverse usage scenarios.
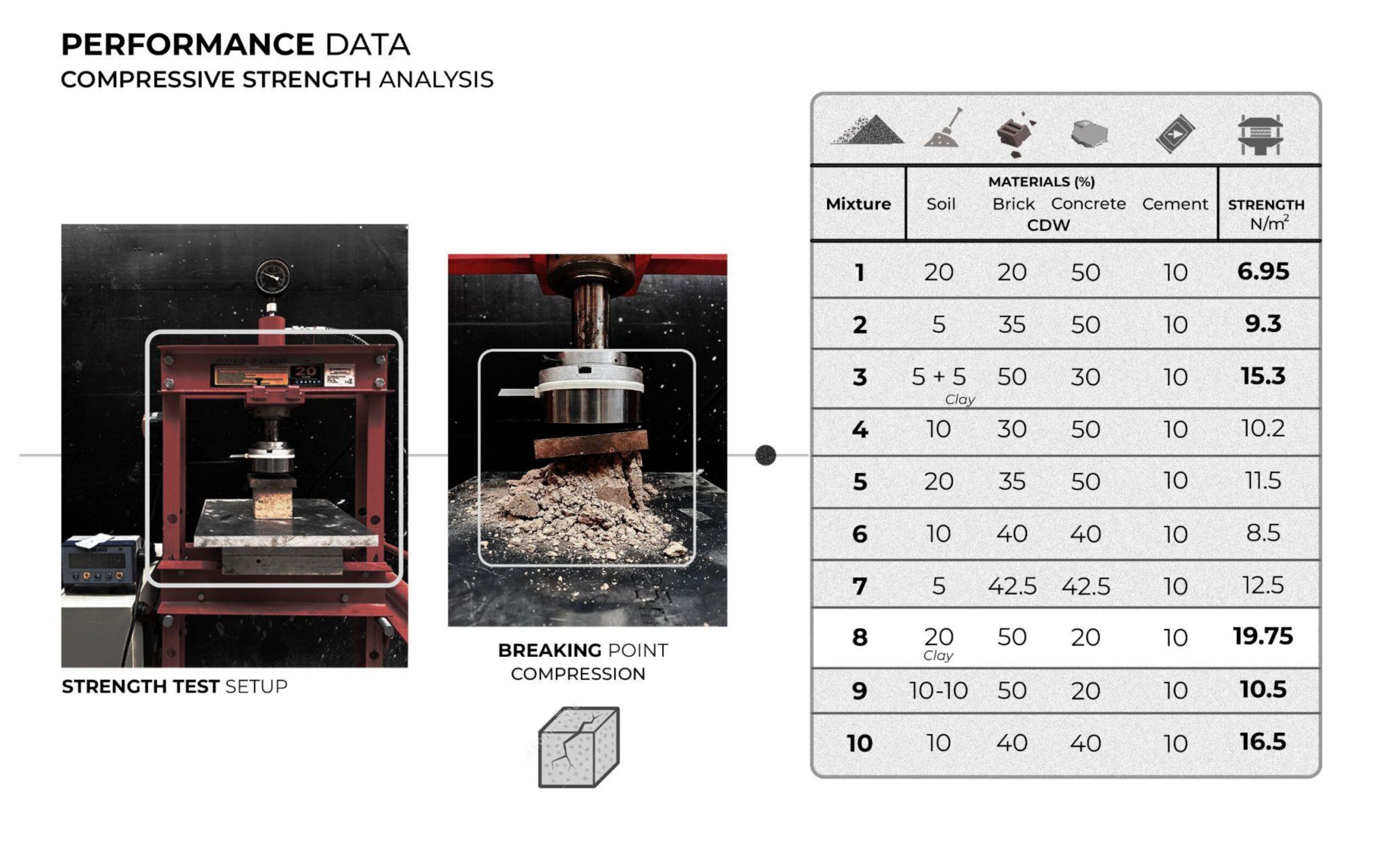
Comparative analysis of compressive strength against stabilized rammed earth, unstabilized rammed earth, concrete, and brick masonry demonstrates our
material‘s capability to compete effectively. This validates its viability and positions it as a comparable choice for modern building applications.
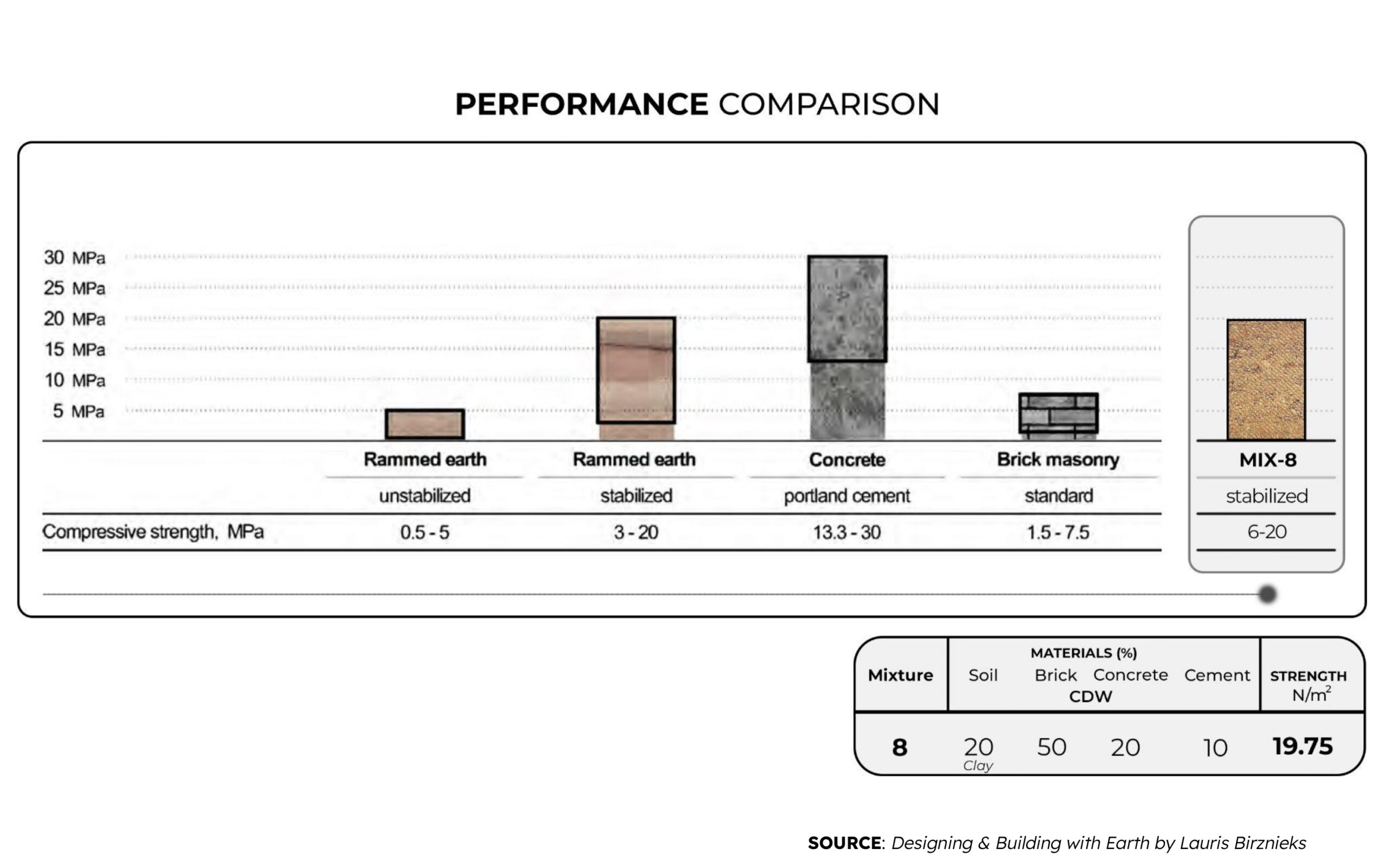
RE-MANUFACTURING
Overall, this structure provides a comprehensive outline of the foundational infrastructure for a modern manufacturing facility. The overview highlights key processes in the manufacturing workflow, shedding light on the potential for automation in critical stages such as CDW processing, diverse mixture mixing, and robotic material deposition with automated ramming. Recognising this automation potential is pivotal as we aim for more efficient and scalable production methods.
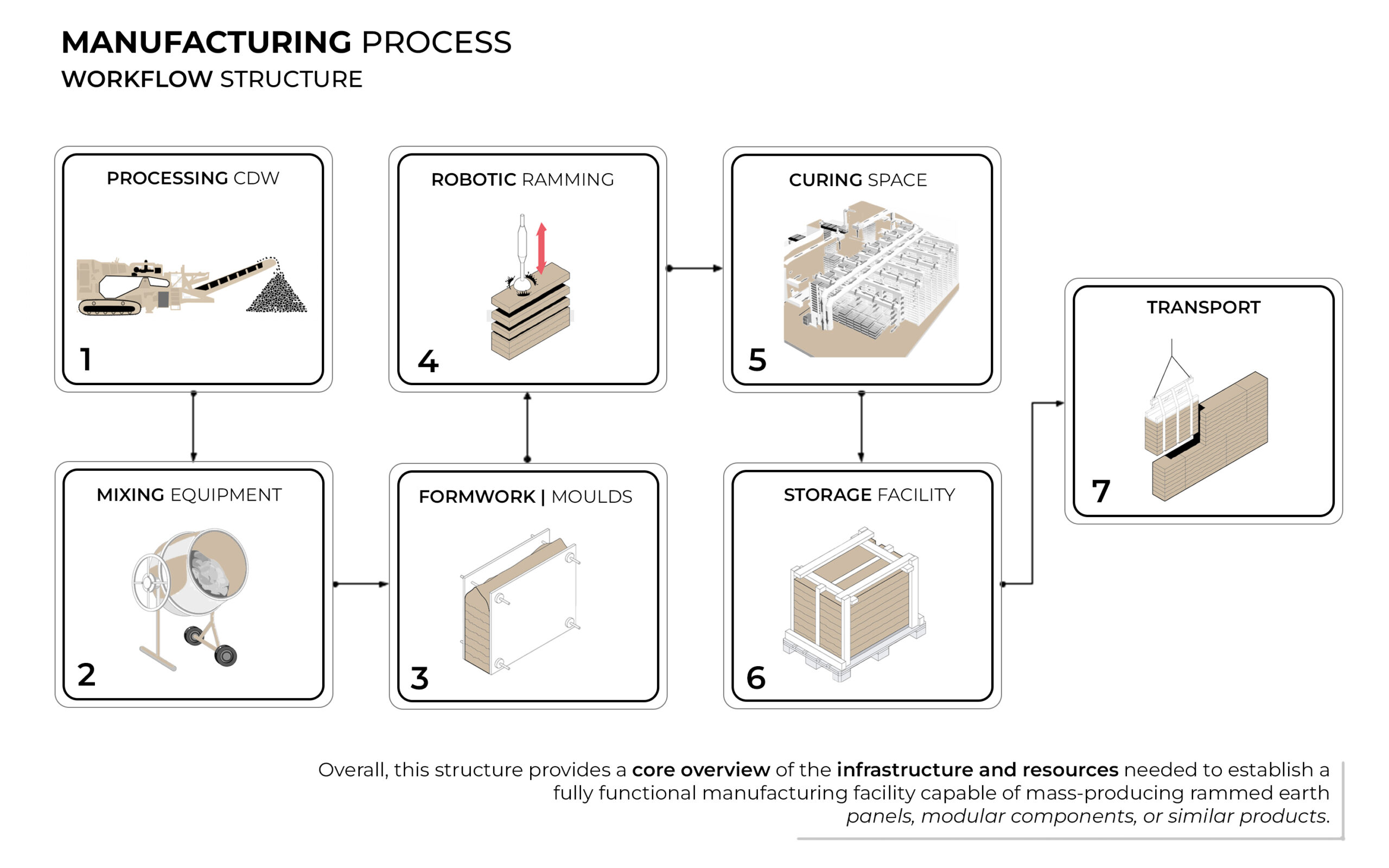
This gives us an overview of the infrastructure setup for processing segregated concrete and brick from Construction and Demolition Waste (CDW). Operations occur at both on-site pop-up and off-site industrial factories, encompassing segregation, filtration, crushing, grinding, and component manufacturing. This setup supports the production of diverse components with varying compressive strengths.
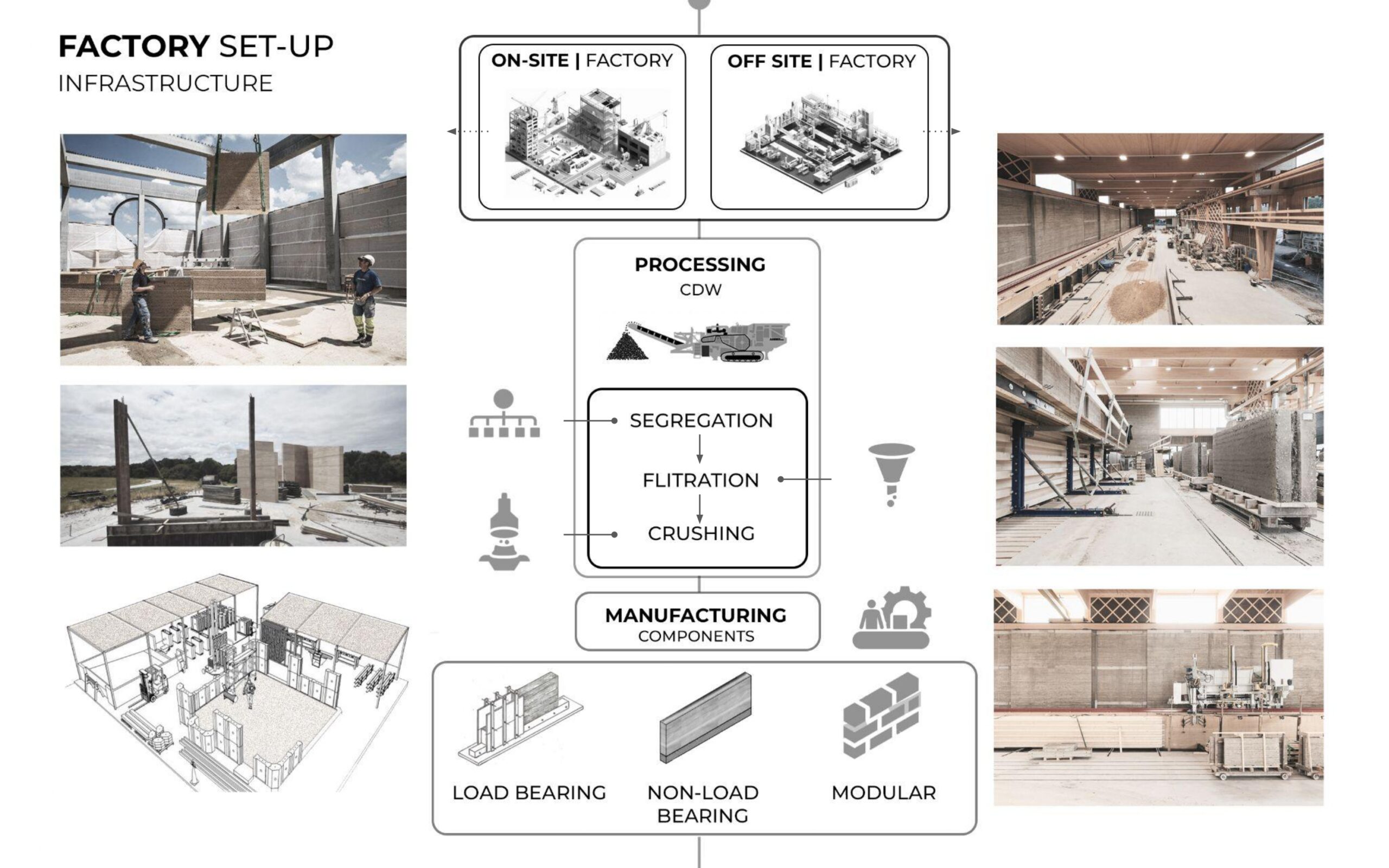
MATERIAL LIFE-CYCLE
// Charting a Sustainable Path: Designing the material life-cycle to foster circular economies and minimize linear processes. //
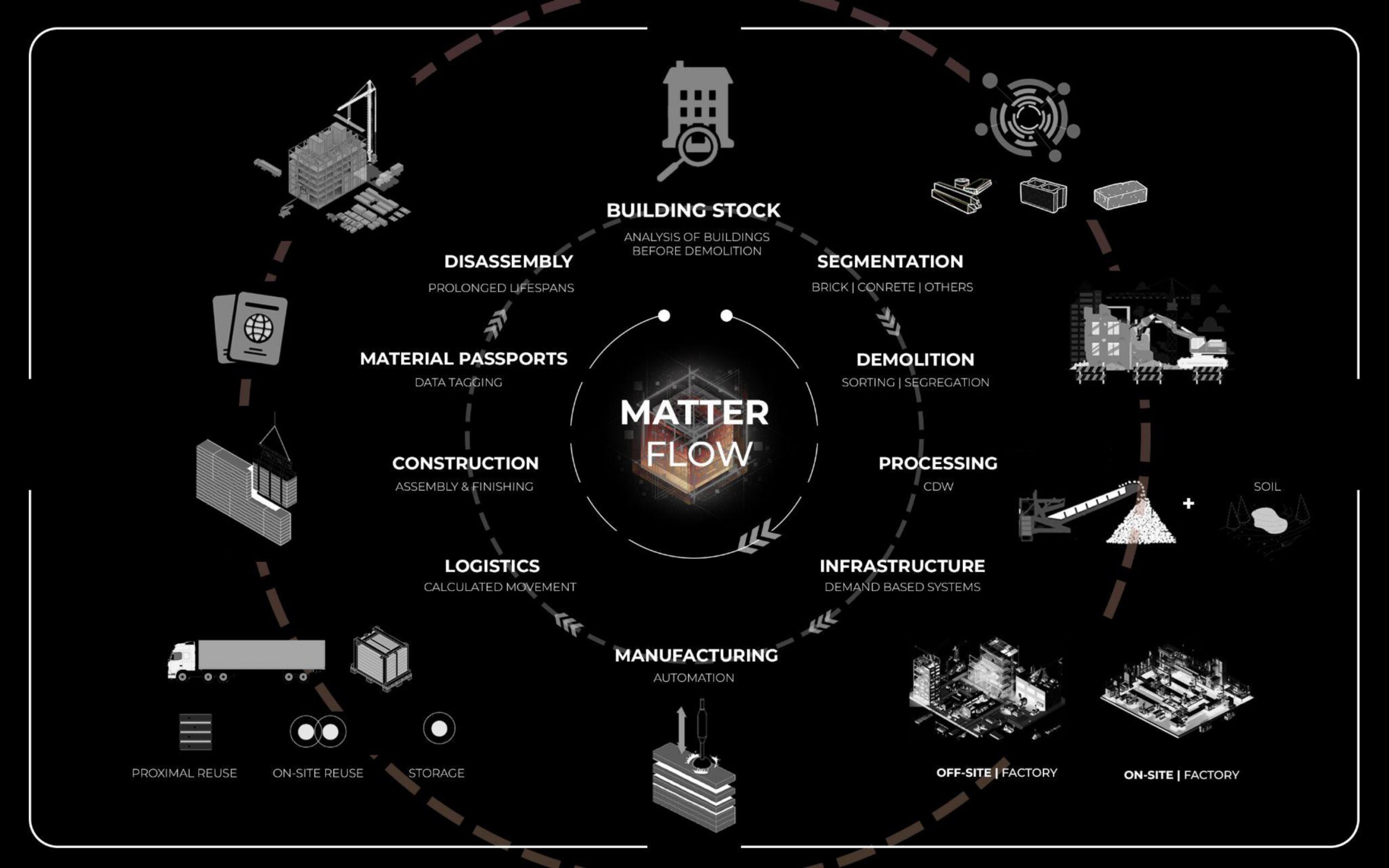
DESIGN INTERVENTION
With the advent of a novel material, it‘s important to define the ways in which you engage with the material, in order to better understand it. This chapter is a descriptive and visual look at how this engagement has been designed to explore in terms of:
1. DESIGN TYPOLOGIES
2. MATERIAL GRADING – FUNCTION & AESTHETIC
3. PRODUCT LINES
Focused on the design of Wall Systems within the building envelope, this image highlights our strategic engagement with versatile architectural elements. Leveraging our material‘s superior compressive strength, we explore the potential for creative expression within these structural confines.
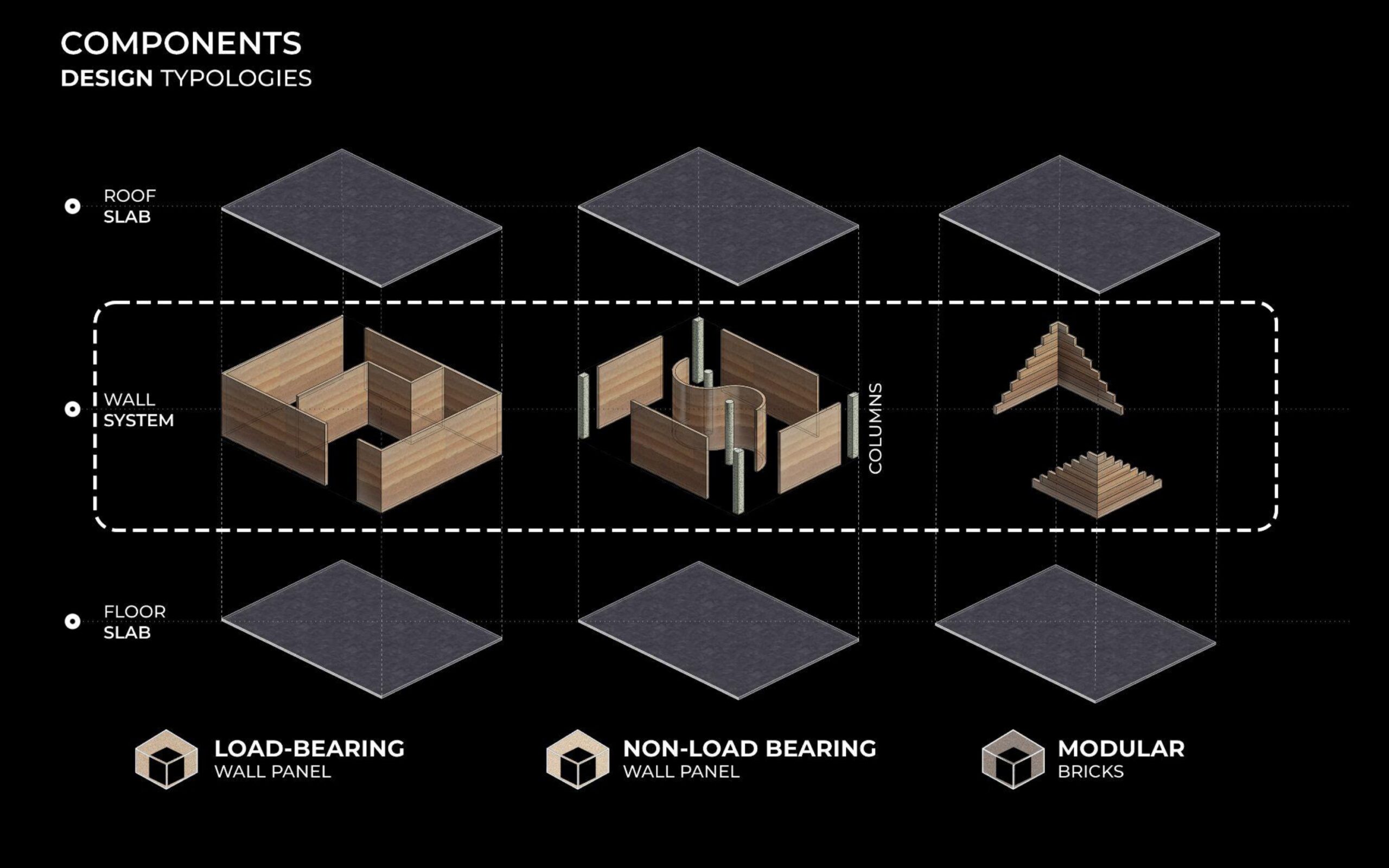
Exploring structural grading with compositional mixtures of varying strengths and aesthetical grading through oxide pigments, puts together a product that‘s both versatile and consumer-expansive.
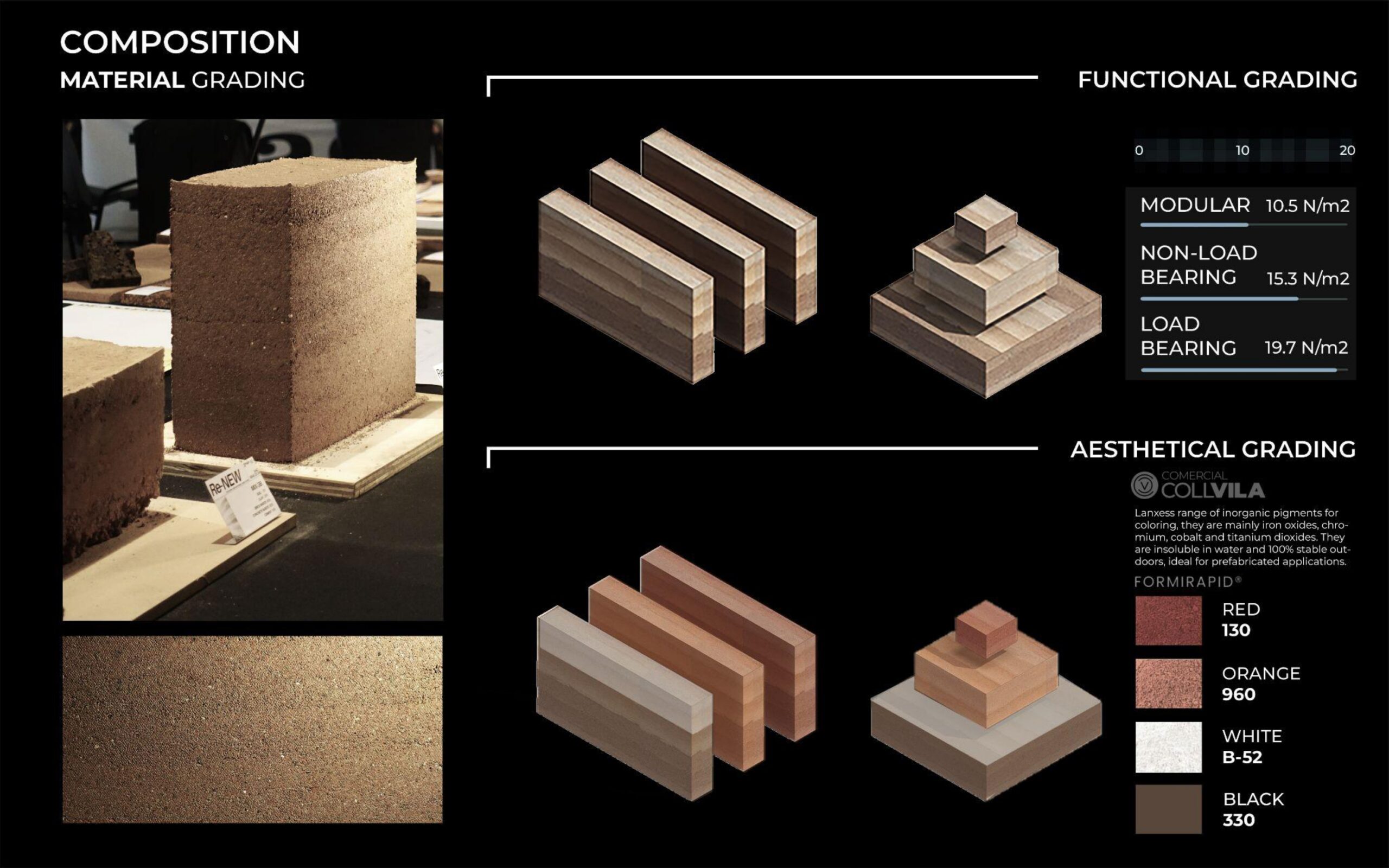
As a new material emerges, it‘s essential to methodically explore its potential through design, gaining insights into its inherent qualities and limitations. Through three distinct prototyping approaches, we aim to uncover diverse applications and pave the way for innovative construction solutions.
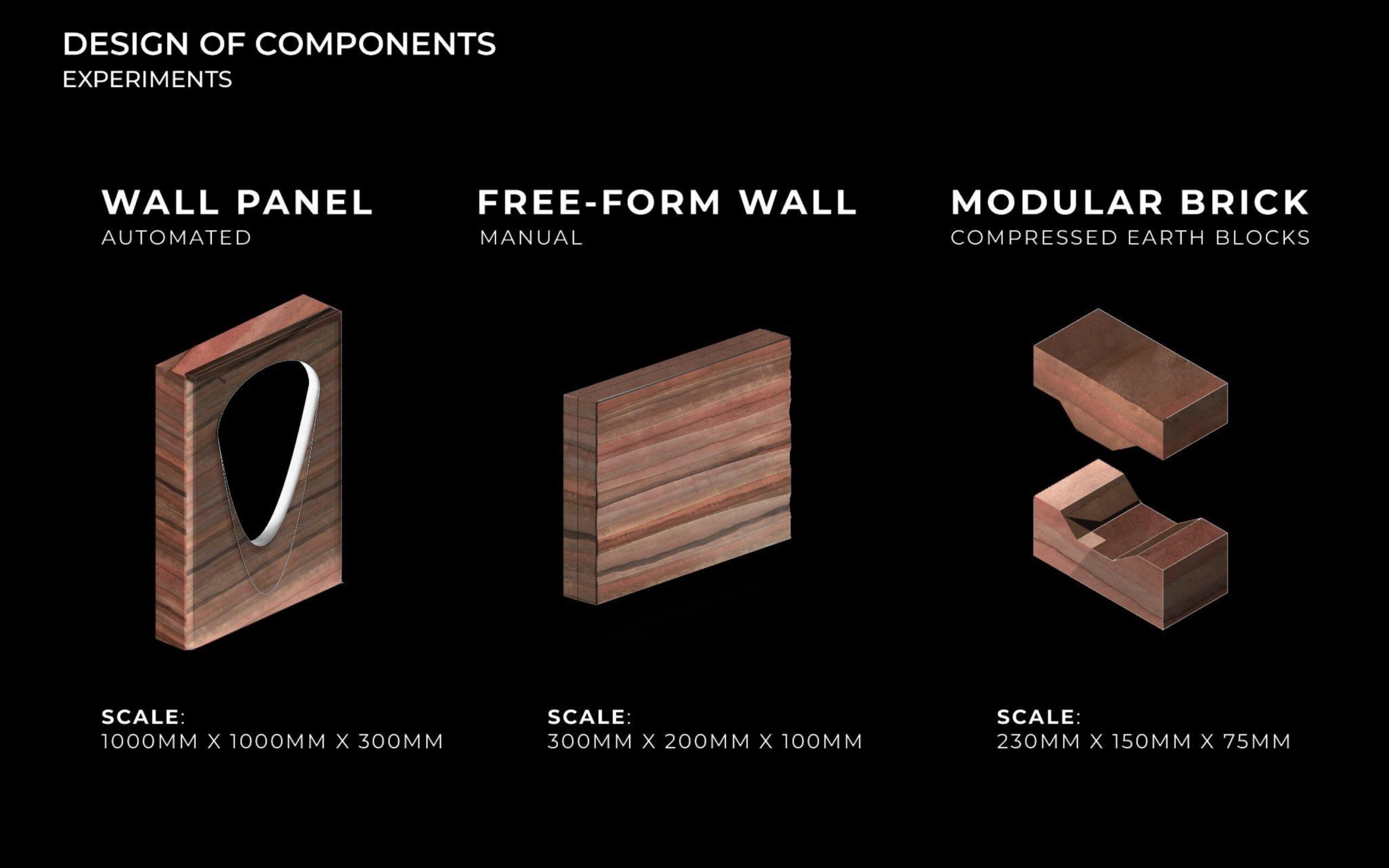
As we scale up, our exploration focuses on optimising the structural form. This involves strategic design to effectively integrate varying strengths of mixtures into cohesive forms. This exploration enables pushing the boundaries of design and material integration in construction.

The prototype emerges from a nuanced understanding of the material, blending subtle curvatures in the form-work to evoke a sense of organic flow, anchored by a central void to gauge structural integrity. Atop this, we employed aesthetic grading through a deliberate deposition strategy based on volume and elevation.
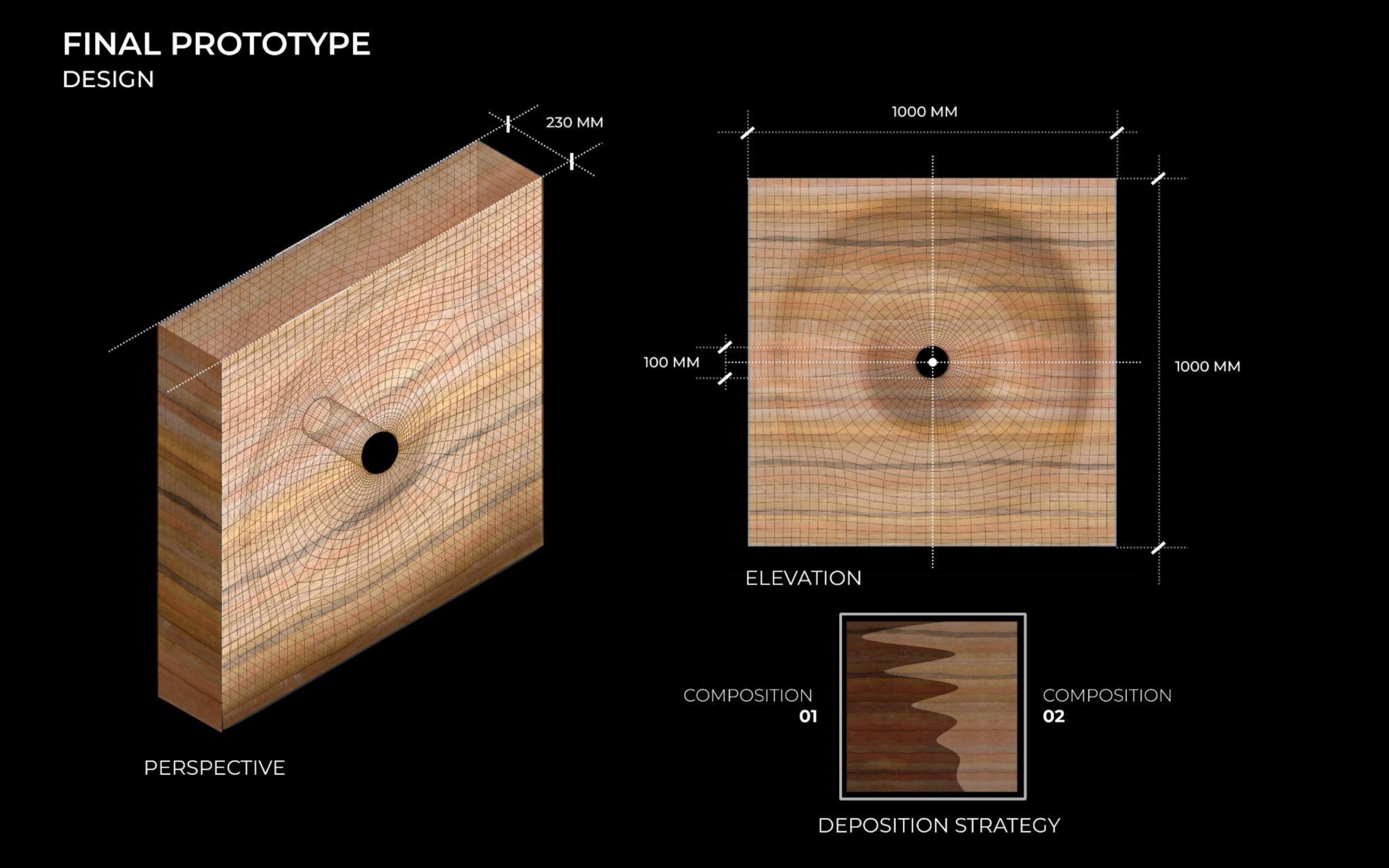
ROBOTIC FABRICATION
The process behind the material generation is an intensive and rigorous activity and the automation of these processes is crucial for the system to be easily implemented.
This lead us to explore automation, in terms of:
- PNEUMATIC RAMMING
- SELECTIVE DEPOSITION
- ROBOT COLLABORATION
Embracing automation as the cornerstone of our fabrication strategy, we optimize efficiency across time, cost, scalability, and labor requirements. By implementing Selective Deposition for precise functional and aesthetic enhancements, alongside automated pneumatic processes, we elevate our production capabilities.
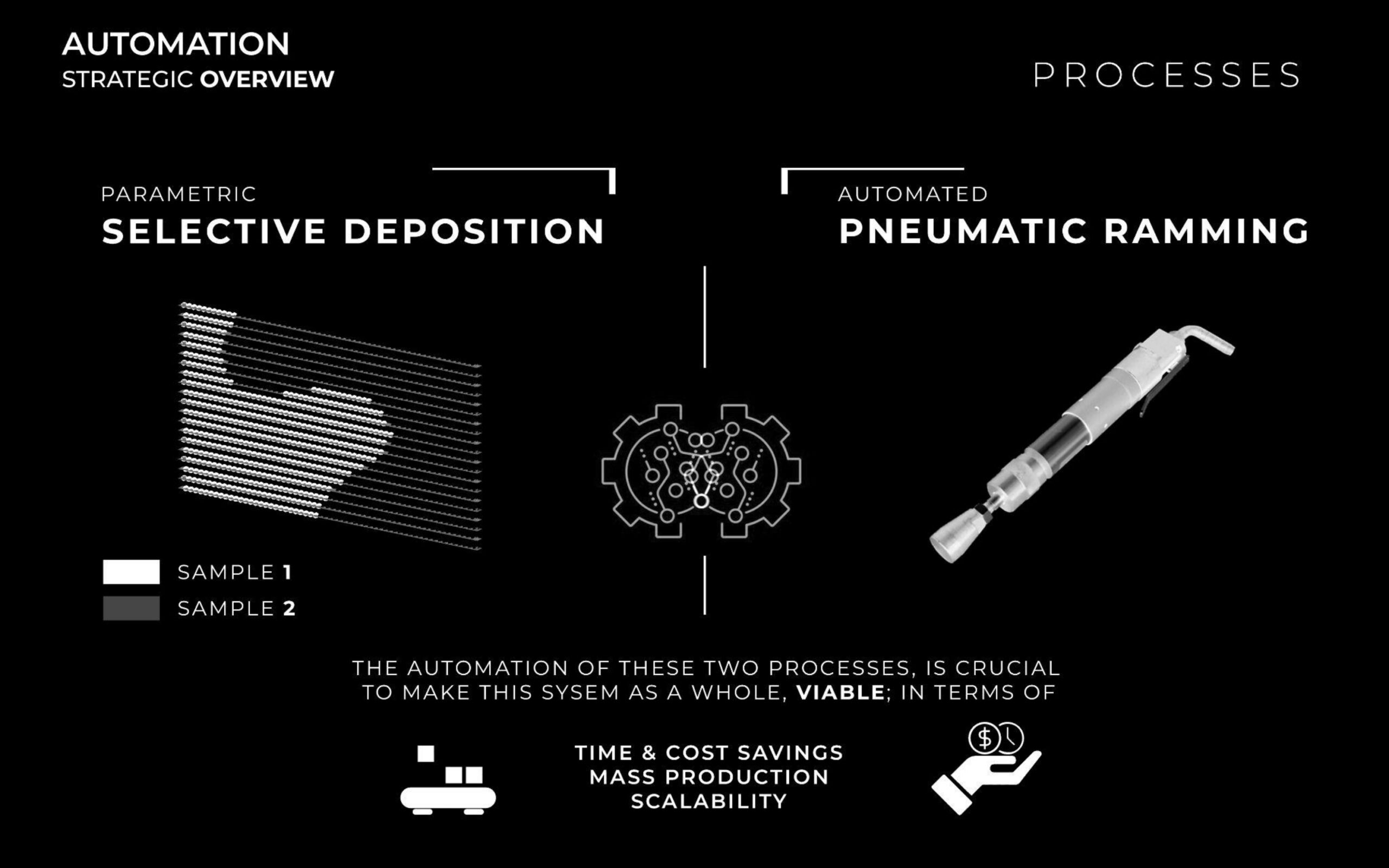
An integrated end-effector combines these functions. This axonometric shows their assembly—simple in concept yet complex in execution. Using two material tanks, selective deposition is achieved through controlled material release with a piston system. Attaching a pneumatic rammer to the robot flange ensures stable ramming, complemented by a nozzle with a plow-tip leveller for uniform material layering.
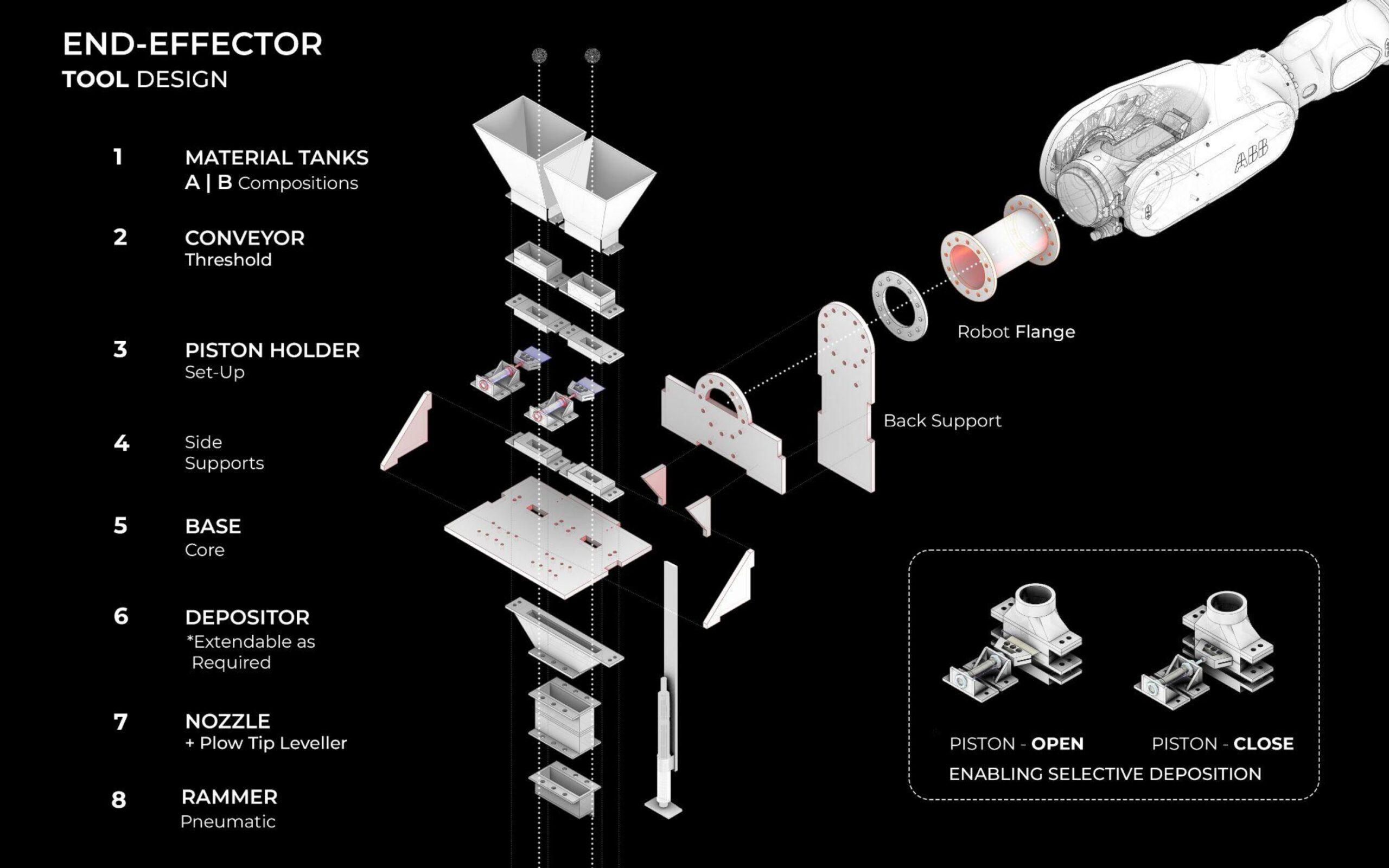
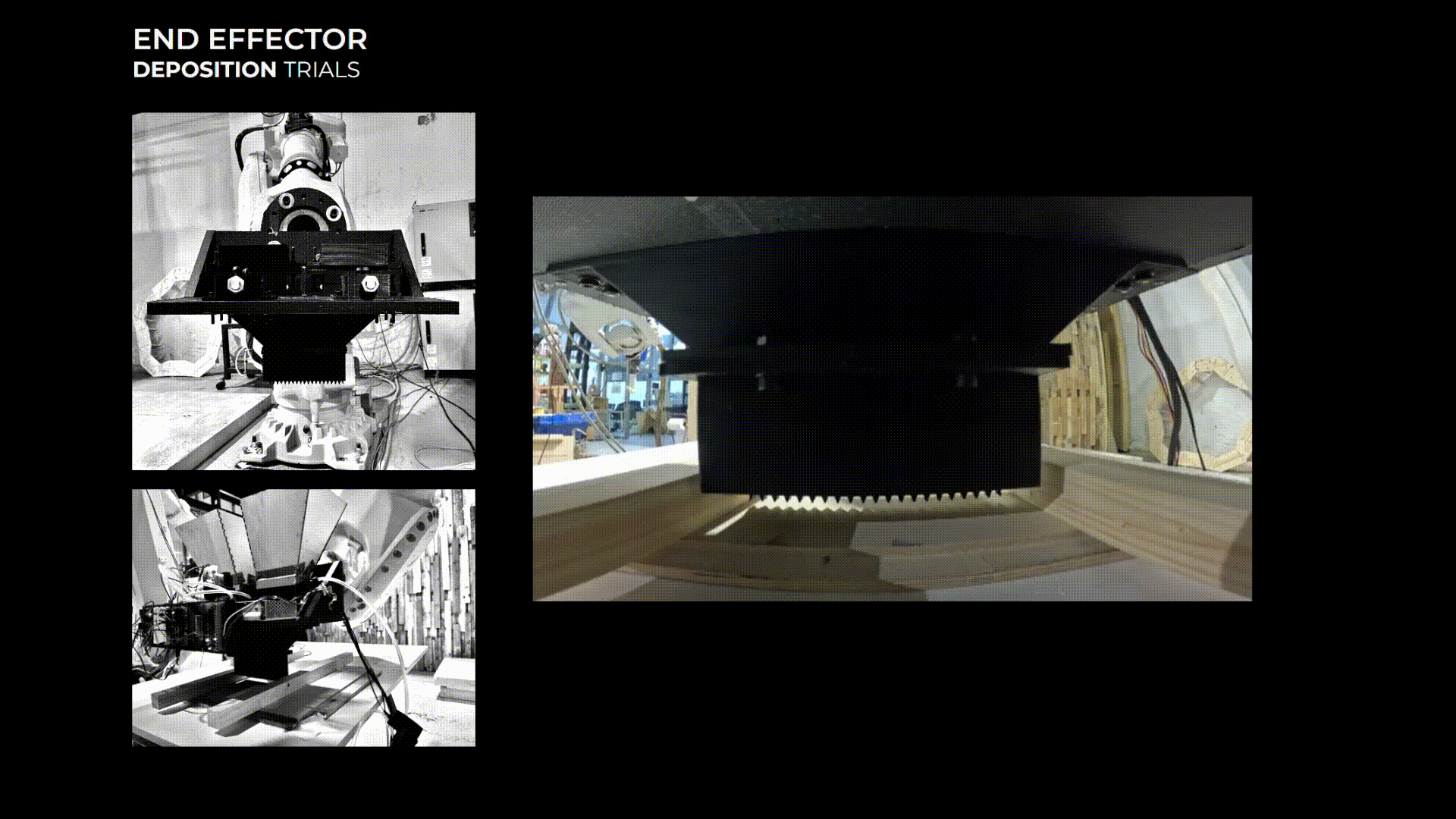
FABRICATION PROCESS
The successful fabrication of the prototype demonstrates the viability of integrating advanced automation and innovative material strategies. Leveraging selective deposition and automated pneumatic ramming, we achieved greater control and time savings. This showcases scalable manufacturing possibilities and underscores the material‘s adaptability and structural integrity.
INTERFACE