AIM
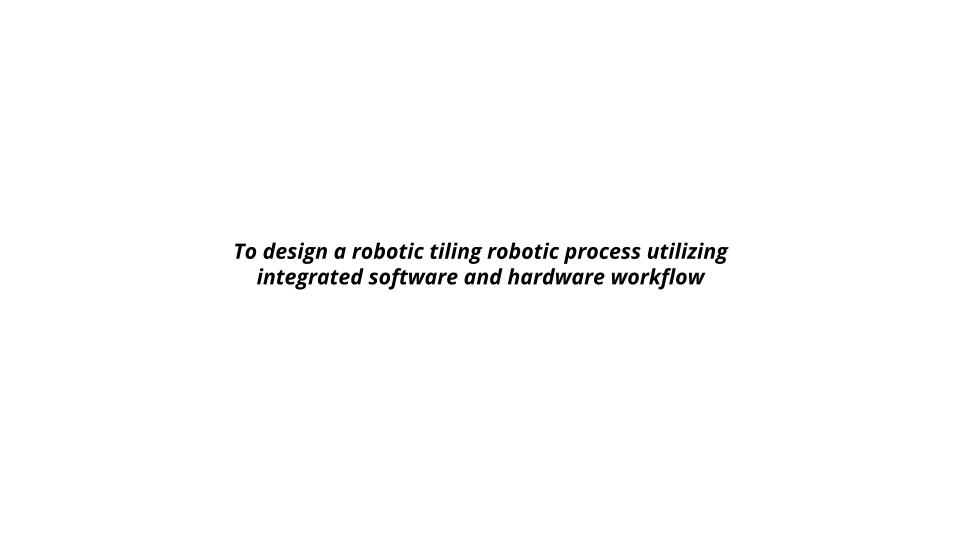
DESIGN
The three distinct design methodologies we explored employed grayscale image mapping, where the gray areas functioned as attractors and filters for colored circles. Our second experiment focused on employing curves as generators for the spatial arrangement and packing of a variety of larger circles. The third methodology extended our exploration to the incorporation of non-circular geometries, allowing for their strategic remapping onto the designated surface.
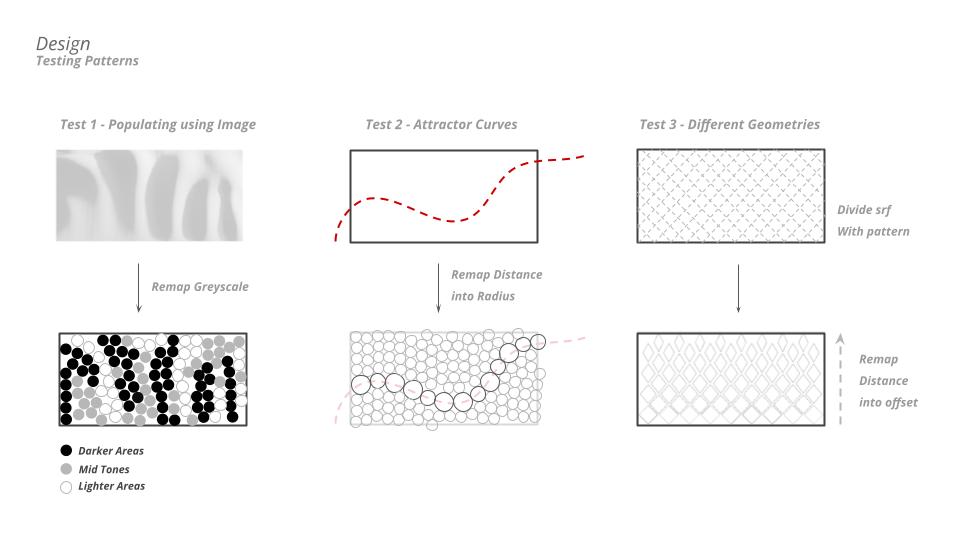
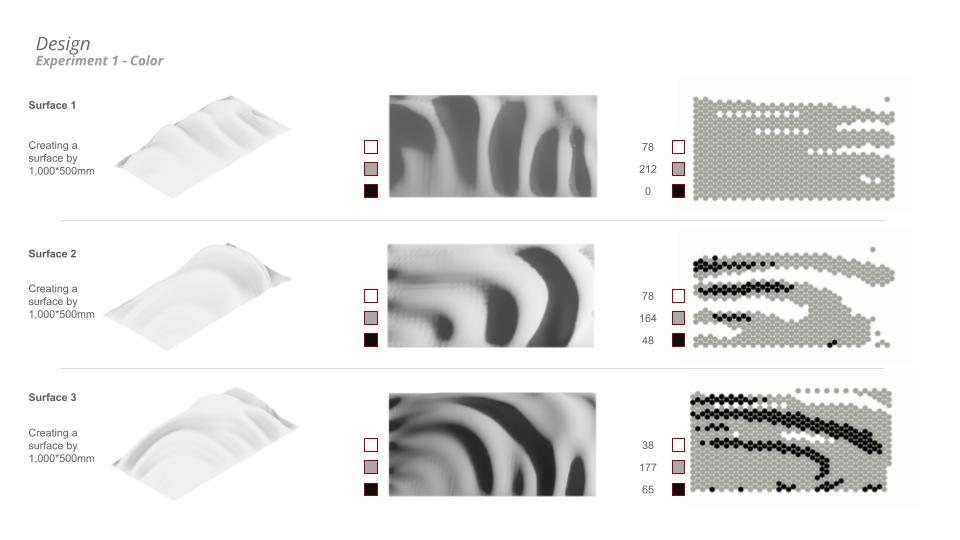
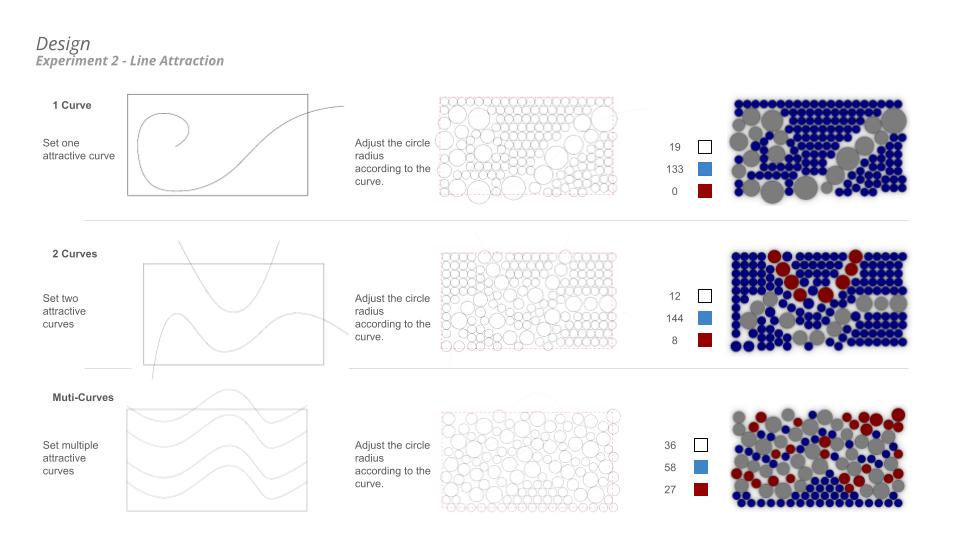
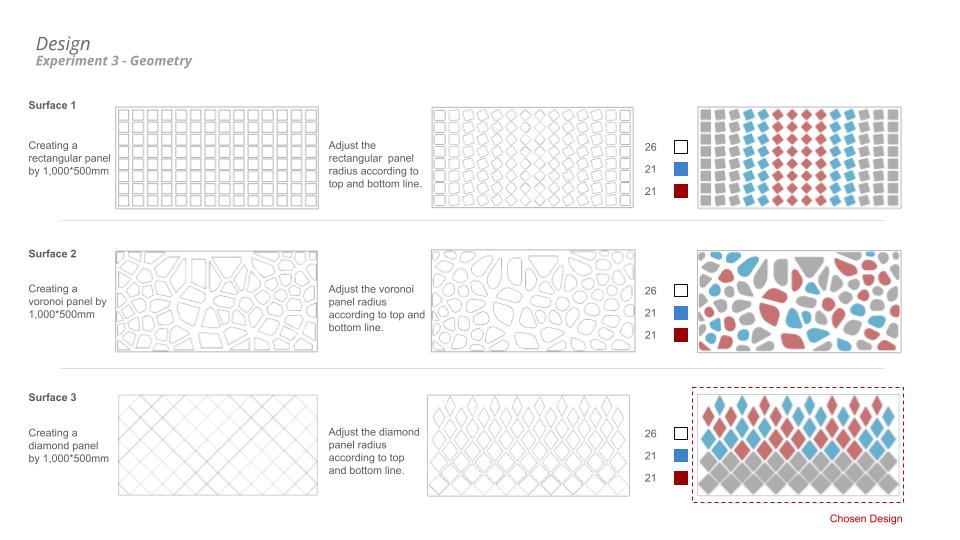
The decision to select the non-circular design approach was based on its superior capabilities to facilitate the exploration of rotation and size recognition. This aspect was particularly crucial for its integration with a robot employing OpenCV for image processing. This advanced design choice enables a more nuanced interaction with geometric forms, allowing the robot to accurately interpret and respond to a variety of shapes and sizes through advanced image analysis techniques.
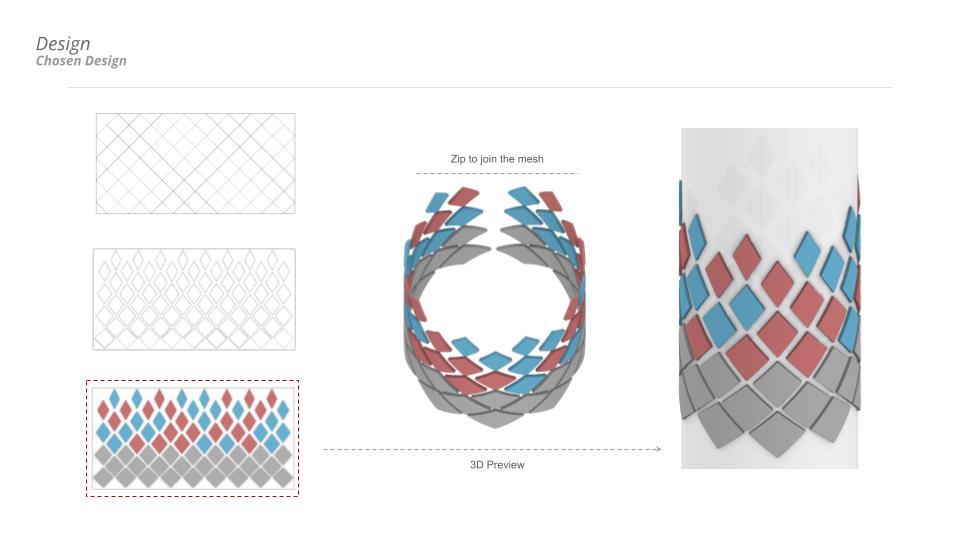
FABRICATION
Upon selecting a design, the fabrication workflow initiated with the nesting and packing of tiles for CNC machining. Subsequently, the development of code for size and color recognition was undertaken in Python, intended for integration with Rhino through the ETH Open Source Plugin CompasFab. This streamlined process facilitated the automation of the robotic pick-and-place operation, enabling the seamless translation of the digital design into its physical counterpart, thus achieving a level of autonomy in the recreation of the design from digital to physical form.
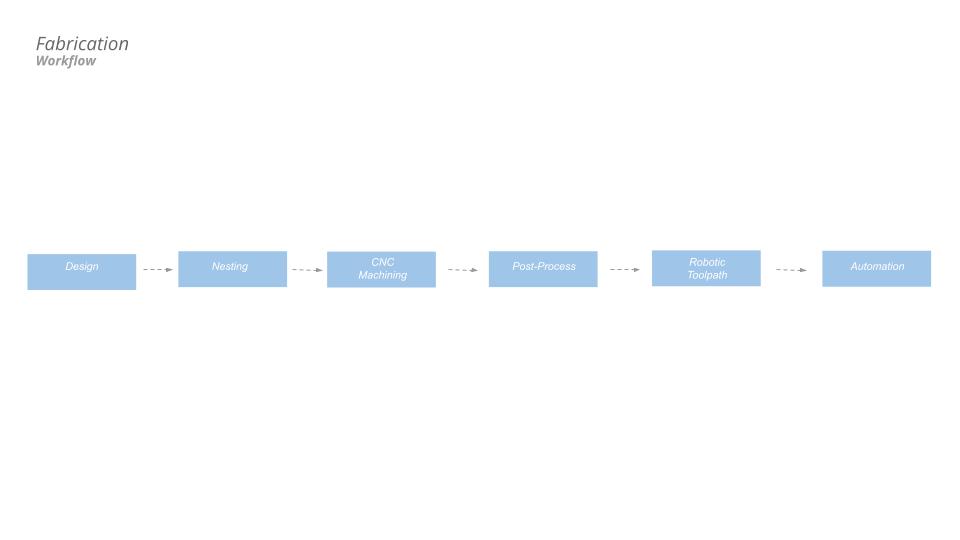
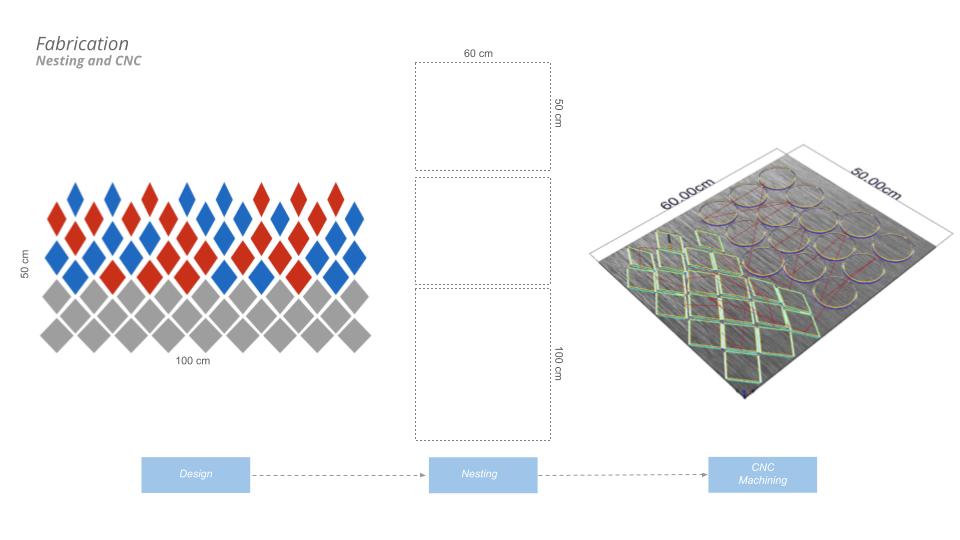
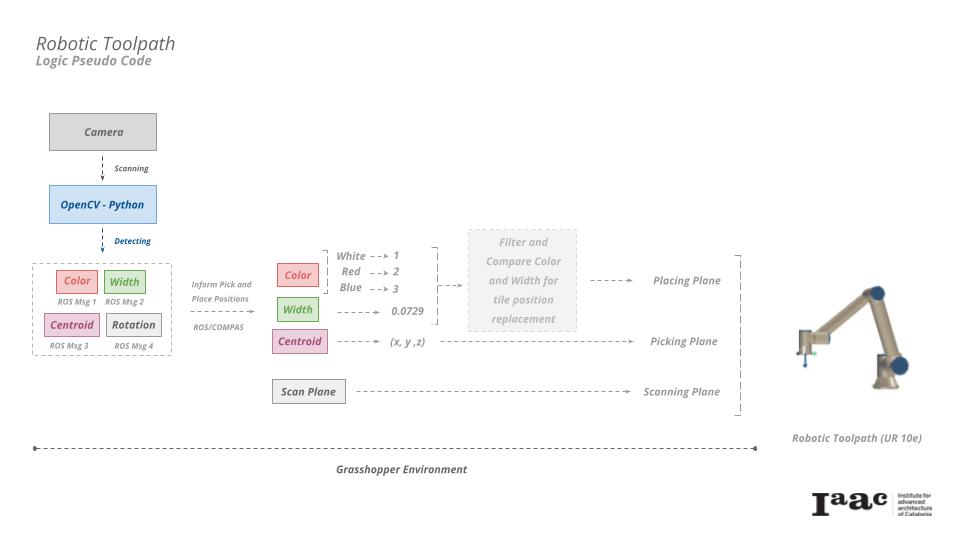
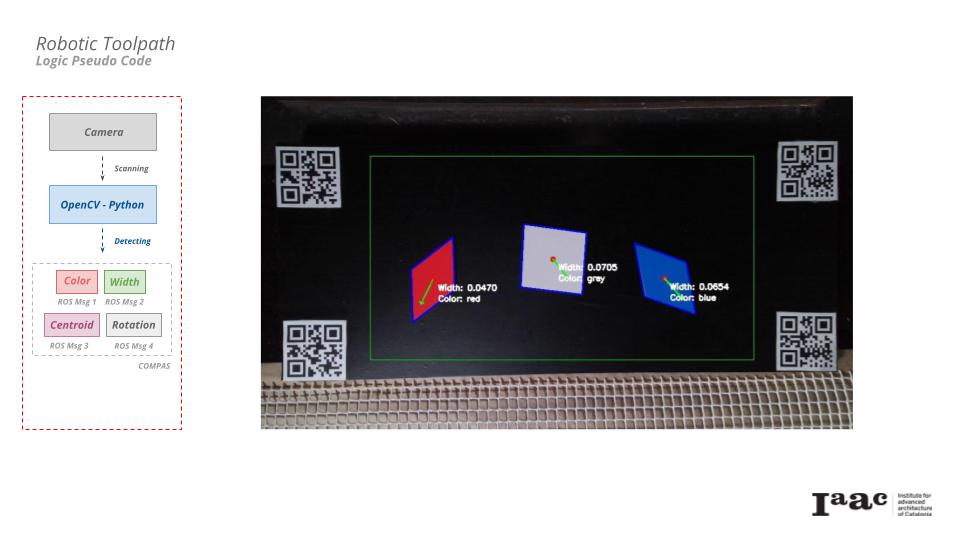
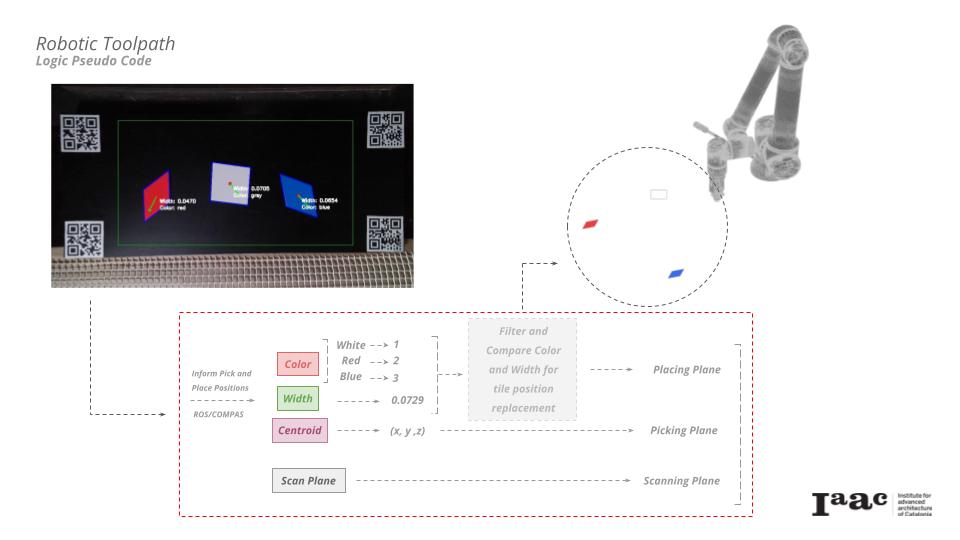
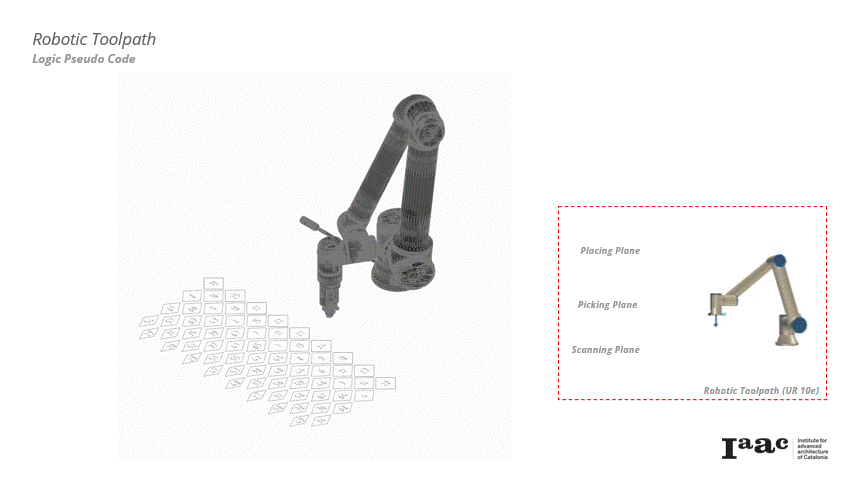
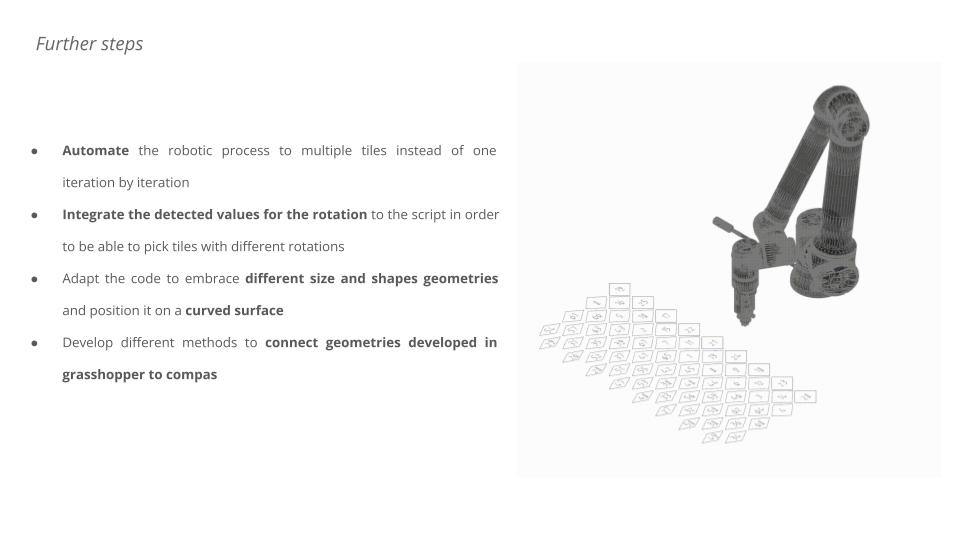
References
This workshop is based on the following prior work:
- Aikaterini Toumpetski, Nikolaos Maslarinos. Non-planar Upcycled Robotic Tiling. ETH Zürich, MAS 2021/22 Thesis Project, October, 2022. https://www.masdfab.arch.ethz.ch/2021-22-t3-work
- Tom van Mele, et al., COMPAS: A framework for computational research in architecture and structures, http://compas.dev (2017-2024). doi:10.5281/zenodo.2594510. URL https://doi.org/10.5281/zenodo.2594510
- Gonzalo Casas et al., COMPAS FAB: Robotic fabrication package for the compas framework, https://github.com/compas-dev/compas fab, Gramazio Kohler Research, ETH Zurich (2018-2023). doi:10.5281/zenodo.3469478. URL https://doi.org/10.5281/zenodo.3469478
- Angel Muñoz, Alexandre Dubor. Workshop 2.1: Mosaic // Sharp edge. IAAC Blog. February, 2021. https://www.iaacblog.com/programs/workshop-2-1-mosaic-sharp-edge
- Gramazio Kohler Research. Mobile Robotic Tiling. Gramazio Kohler Research (2016). https://gramaziokohler.arch.ethz.ch/web/e/forschung/257.html