Structural Materials
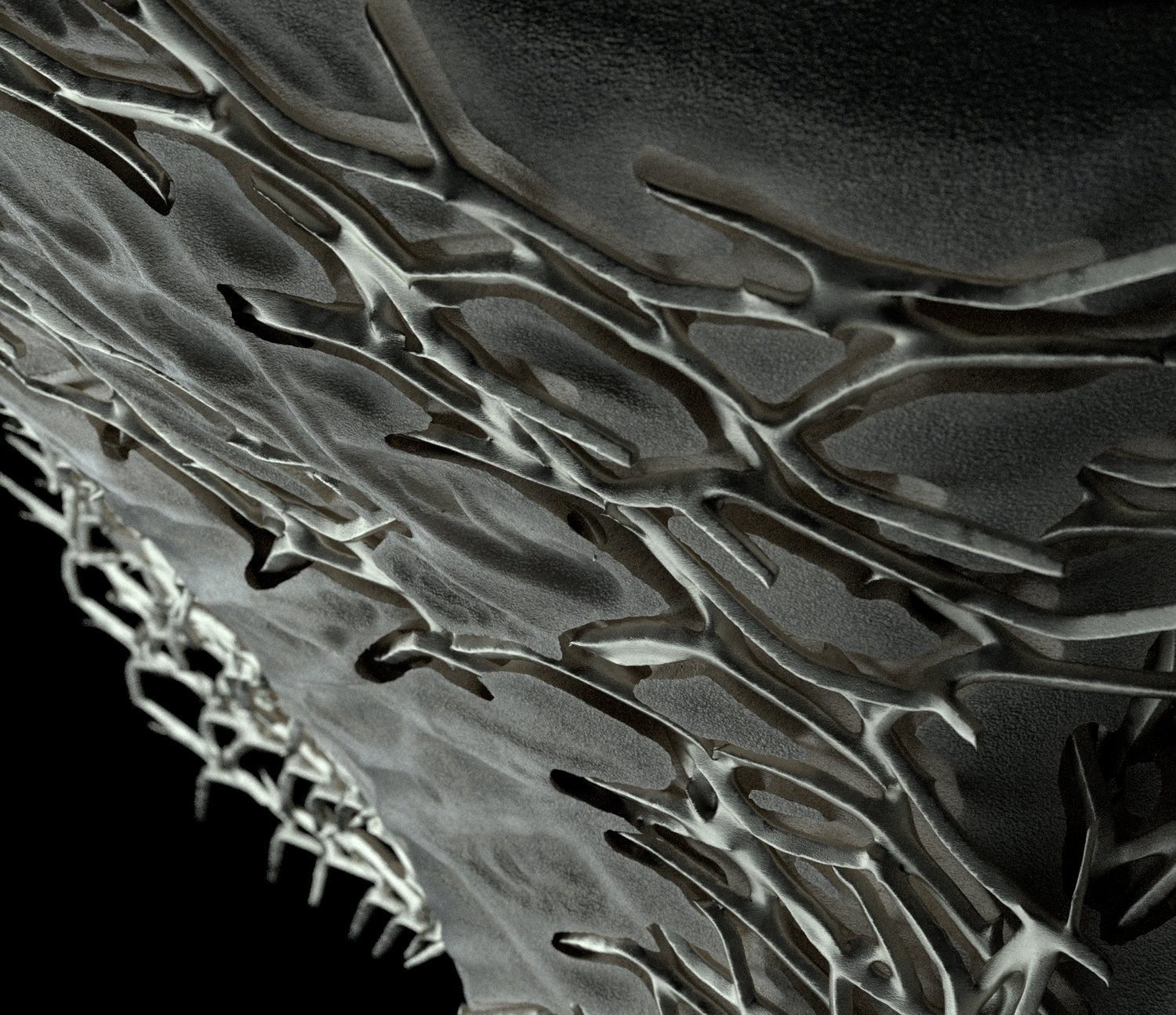
source: www.rolandsnooks.com
Is the scale of the projects in the experimentation on computational design fabrication an obstacle or an opportunity?
Since architects started to shed their skin on the conventional way in practice and caught the digital era, the abundance of application of digital design on the realization became joyful for the audience. Mario Carpo on the Second Digital Turn explained this period as CAD-CAM was started to use after the Industrial Revolution in the fabrication line but architects were not in the group of users, later the postwar world came with big demand in construction which could not afford customization. [1] For many years the construction field followed mass fabrication to respond to the needs of the world and use this as an excuse to stay in the conventional and repetitive zone. Finally, in the 90s mass customization, non-standard seriality, variability of market prices, and the production of non-standard items were introduced with the computational approach becoming more usual in design. This is the time when architects took off where they left off in the craftsmanship era.
The implementation of computation in architectural design came with the question of how to ‘fabricate’ these forms and with which material would serve the best to realize it as well as support the tectonics of the design. Zaha Hadid was one of the pioneers in the fabrication of complex forms, through her work we can see how computational geometry meets with its reality.
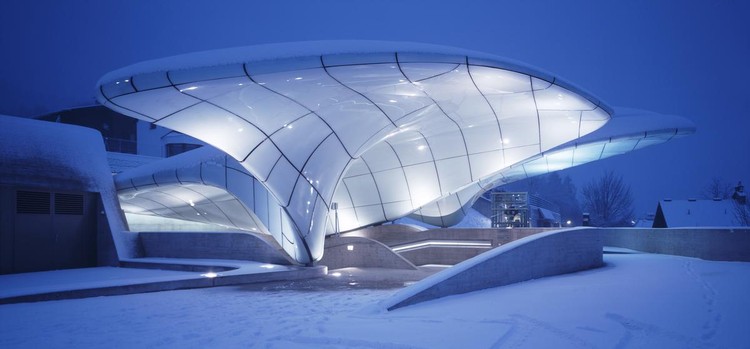
source: www.archdaily.com
The computational design comes with its novelty and boundaries. The designers became more specialized in the making of the form. The further they discover, the further they detail their work to realize them. However, Is the physical world ready to accommodate their creations?
The obstacles of this path:
The discoveries in digital design and digital fabrication come with their obstacles. From the design of Lattice Space by Bollinger+Grohmann (Sascha Bohnenberger, Klaas de Rycke, Agnes Weiland) [2] the designers faced the production demand in a specified time and a customized design required its settings in the fabrication field. The wanted curvy design was achieved with wood which is sustainable, easy to access, and use. The advancement in wood usage allowed so many structures to be built. But it has its limitations on tectonics. The customized design with its special joinery had the stress of realization in a very short time.
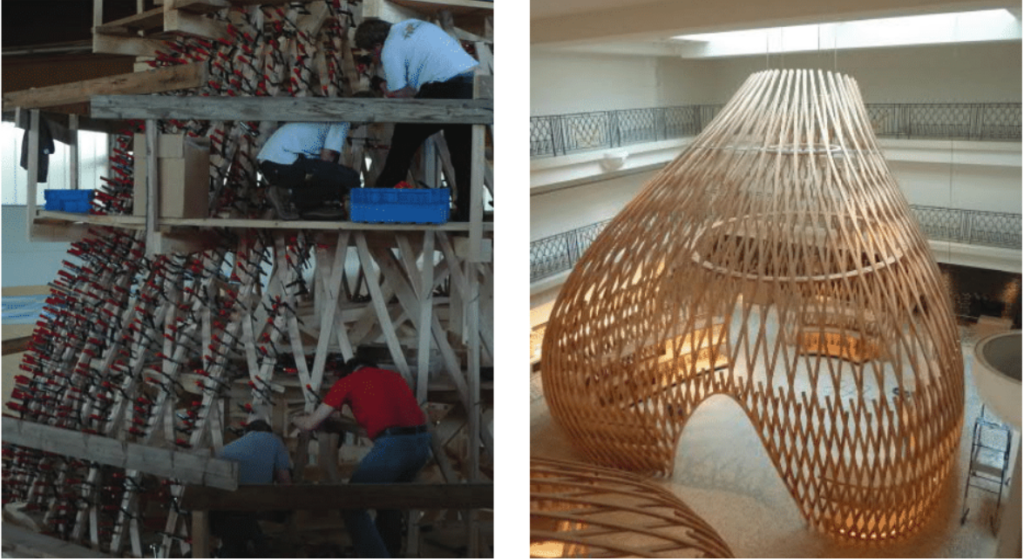
source: Lattice Spaces [2]
On the making of ITKE Pavilions, Jan Knippers, The limits of simulation: Towards a new culture of architectural engineering, [3] is mentioning that the team should be formed with interdisciplinary trained designers, and engineers. To exploit the potential of advanced materials systems, alternative engineering methods should be developed. Integration of simulation, physical tests, and online monitoring should be implemented in the workflow. The back-and-forth process of form-fabrication-material should be introduced. Learning from experimental engineering in the pre-nineteenth century would guide us to material testing and performance mock-ups, and experiences in earlier buildings.
On the exploration of the integration of carbon fibre structural networks within large-scale 3D-printed polymer architectural skins, Roland Snooks refers to achieved surface and structure relations with the 3D printing method by former work of ICD, Elytra Filament Pavilion, ETH Zurich, and Politecnico di Milano. [4] Their approaches all explore the deposition of structural material without the use of molds and in doing so create new possibilities and limitations. These projects are realized with polymers and composites which has allowed for efficient and rapid experimentation. His 3D printed complex form achieves an integration of structural heuristics within algorithmic behaviors; strengthening a thin and lightweight surface with corrugation and curvature; integration of composite materials to create a structural lattice intertwined within the surface itself. However, he is mentioning the design was only fabricated with one material. The broader research aim is to explore and expand the potential of geometries created through a variety of materials within additive manufacturing, and to reveal inherent strengths and characteristics of this construction which cannot be achieved through other means.
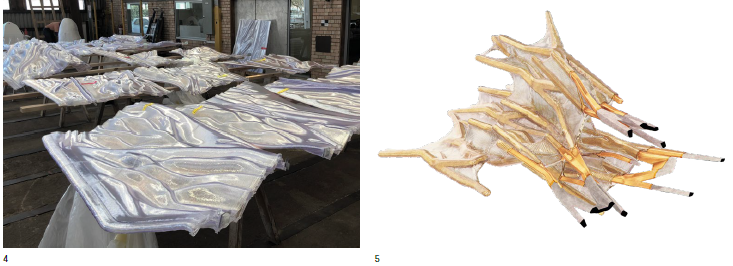
source: www.rolandsnooks.com
The contribution of material enhancement could be supported by nanomaterials and biomaterials.[5] Those materials are used in electronics the most, which are small in scale. Architecture and the construction world are not approaching experimentation on material because of their conventional road-taking. Also, the 20-year period on research to market resonates as material research is not finding a place in the construction market.
The dilemma is happening between; achieving the computational form, fabricating, and the environmental aspect of the used materials.
The newly introduced workflow design, 3D modeling, and the back-and-forth process between computational geometry and material behavior and fabrication.
Work done for Sagra da Familia’s completion explains the contribution of this workflow. The chief architect of Sagrada Familia, Faulí says. “This model couldn’t be produced before, primarily for technical reasons—advances in computer power, precise 3D scanning of the existing building, and 3D prototyping allowed us to work at a scale and a level of detail hitherto impossible to achieve.”
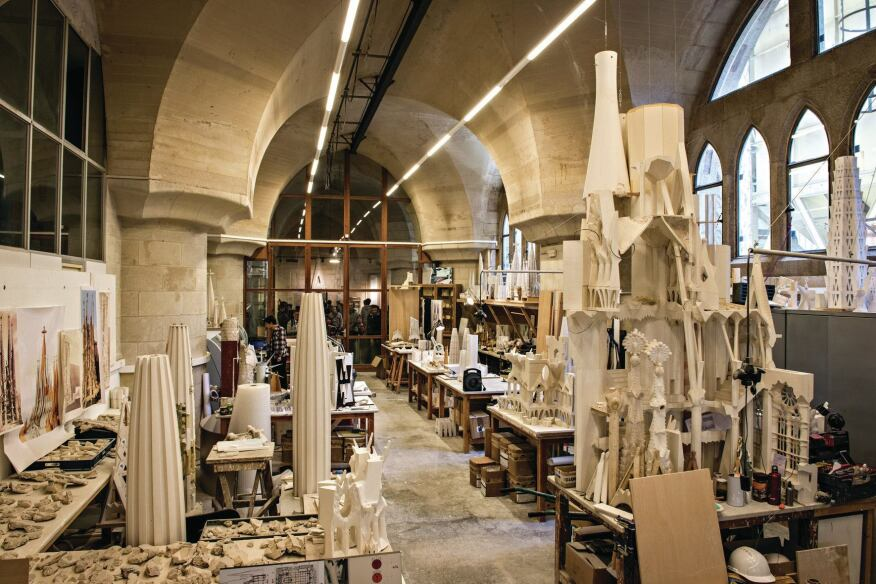
source: www.architectmagazine.com
The obstacles to fabrication are material variety, time limitations, modest scale, skilled workers/ manufacturers, and hard-to-achieve geometries. In the example of Fabricate 2017, [6] the collected studies show the solution seeking to these addressed problems. Robotic fabrication and Additive Manufacturing are solutions to some of the problems. Also with this approach, the complex form fabrication doesn’t need additional casting, or molding which is environmentally supportive. But this approach comes with restrictions in scale and material. Especially in scale, the productions are not going further than pavilion size, furniture, or building façade. But on the other hand, is this a restriction? The size of the prototype is allowing faster production. The designer can invest in the fabrication in a short time and material in small amounts. This method is leading to more experimentation, flexibility, and freedom therefore plenty of iterations on design are obtained. Seeing these designs on a building scale would be groundbreaking. But not getting lost in the problem-solving for the transition from industry-standardized construction to this field requires more practice in the realization of complex computational forms.
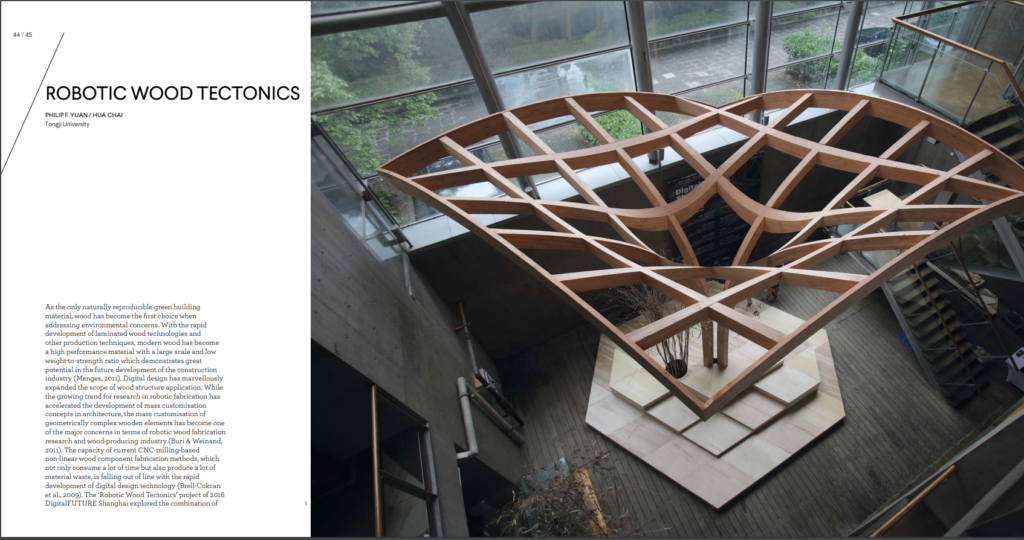
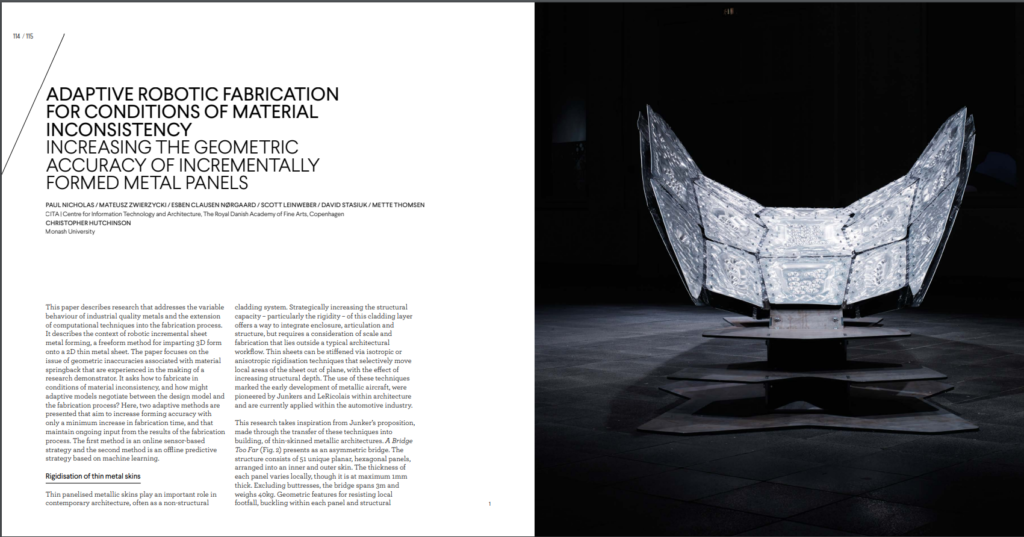
Meanwhile, even for similar or different reasons, some of today’s building scale designs achieved the non-standard, fully customized, environmentally friendly molding in the realization of material, etc. Trufa by Ensemble Studio is using straw as a mold and later a cow is hollowing out the mold to expose the structure. The house and restaurant by Junya Ishigami is utilizing the earth for concrete molding. Green Corner Building by Studio Anne Holtrop is using sand to cast the big blocks of the facade and ground of the structure.
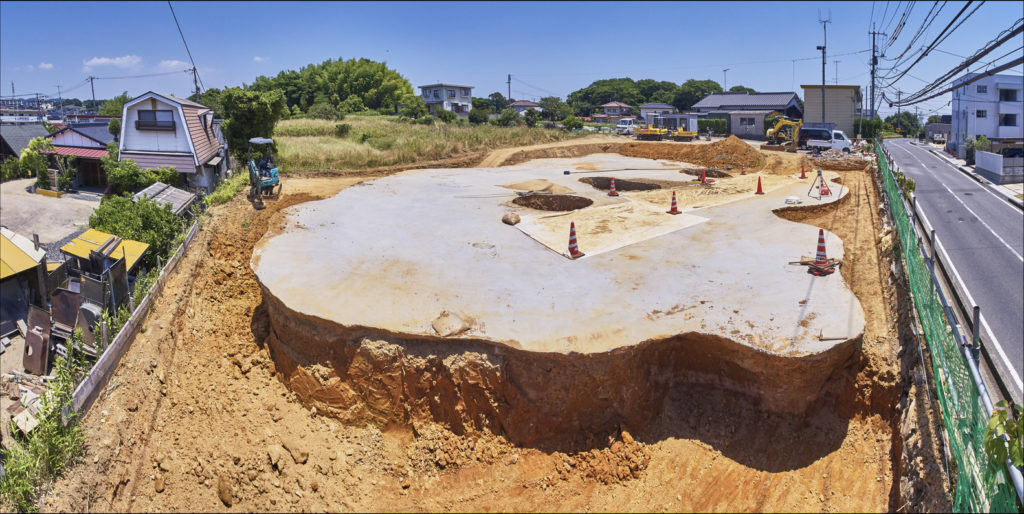
source: www.archdaily.com
In conclusion, towards the new applications of computational form, structural materials and their relation to fabrication will be the focus of diverse research. In this journey, we should enjoy the possibilities and opportunities of design iterations.
References:
[1] Carpo, M. (2017). The Second Digital Turn. MIT Press.
[2] Bohnenberger, S., Rycke, K., Weiland, A. (2011). Lattice Spaces: Form optimization through customization of non developable 3d wood surfaces. eCAADe 2011: Respecting Fragile Places, 751-758. http://ecaade.org/downloads/ecaade2011-lowres.pdf
[3] Knippers, J. (November 2017). The limits of simulation: Towards a new culture of architectural engineering. Technology | Architecture + Design, 1(2):155-162. https://www.tandfonline.com/doi/abs/10.1080/24751448.2017.1354610?journalCode=utad20
[4] Snooks, R. (April 2020). Printed Assemblages: A Co-Evolution of Composite Tectonics and Additive Manufacturing Techniques. Fabricate 2020: Making Resilient Architecture, 202-209. UCL Press. https://www.jstor.org/stable/j.ctv13xpsvw.31
[5] Pacheco-Torgal, F., Labrincha, J.A. (November 2013). The future of construction materials research and the seventh UN millennium development goal: A few insights. Construction and Building Materials, 40: 729-737. https://www.sciencedirect.com/science/article/abs/pii/S0950061812008185?via%3Dihub
[6] Menges, A., Sheil, B., Glynn, R., and Skavara, M. (2017). Fabricate: Rethinking Design and Construction. UCL Press. https://www.uclpress.co.uk/products/89026#