Crafting performative structures through robotic earth injection in dynamic fiber scaffolds
Terraweave is an architectural research project that explores how robotic additive manufacturing can enhance the performance of natural building materials. Conducted as part of the Master in Robotics and Advanced Construction at IAAC, the project investigates the integration of willow scaffolds and earth injection to create adaptive wall systems that respond to both structural and thermal requirements. Without relying on synthetic fixings or conventional assembly methods, Terraweave proposes a low-impact, reversible, and thermally efficient construction strategy. Rather than a single solution, it is a system of possibilities — adaptable, craft-based, and deeply responsive to context. By leveraging robotic processes with natural materials, it opens a dialogue between tradition and innovation, structure and climate, matter and method.
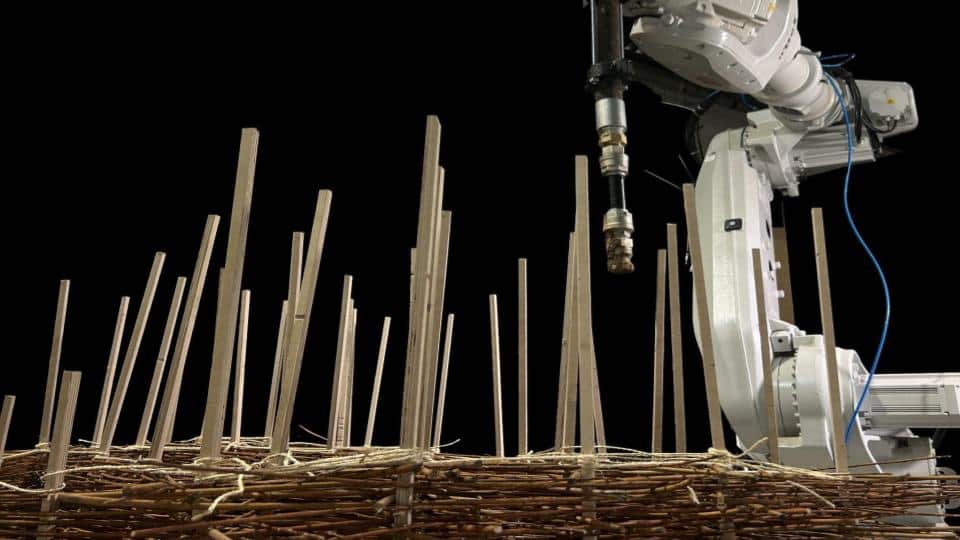
Confronting the Challenge of Extreme Heat
Urban areas like Barcelona are projected to experience up to 50 days of extreme heat per year by 2050 . Current building practices exacerbate these conditions: walls typically insulate passively and act as thermal traps, contributing to increased cooling demands. Terraweave responds by reimagining the wall not as a static barrier, but as an active, performative system capable of thermal regulation through integrated mass and controlled porosity .
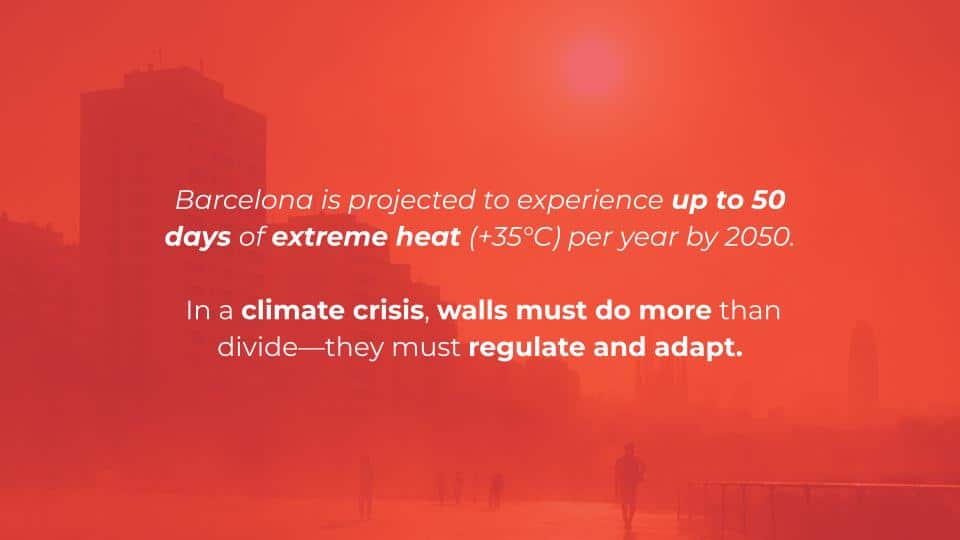
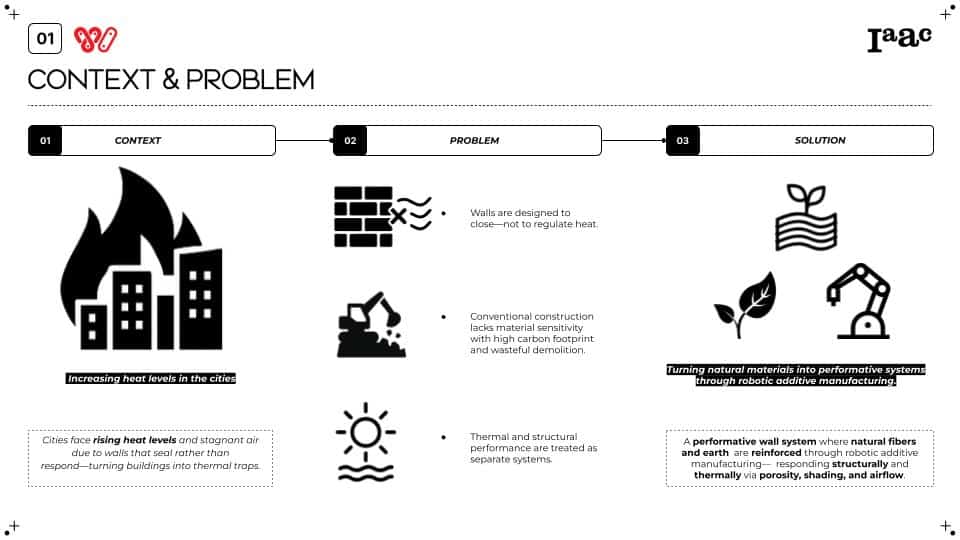
Revisiting Traditional Techniques through Robotics
The project draws inspiration from wattle and daub, a historical technique combining woven timber and earthen plaster. Terraweave reinterprets this tradition through robotic fabrication, coupling the tensile strength of willow with the compressive and thermal properties of earth. This hybridization allows for structural optimization and thermal performance within a singular, cohesive assembly .
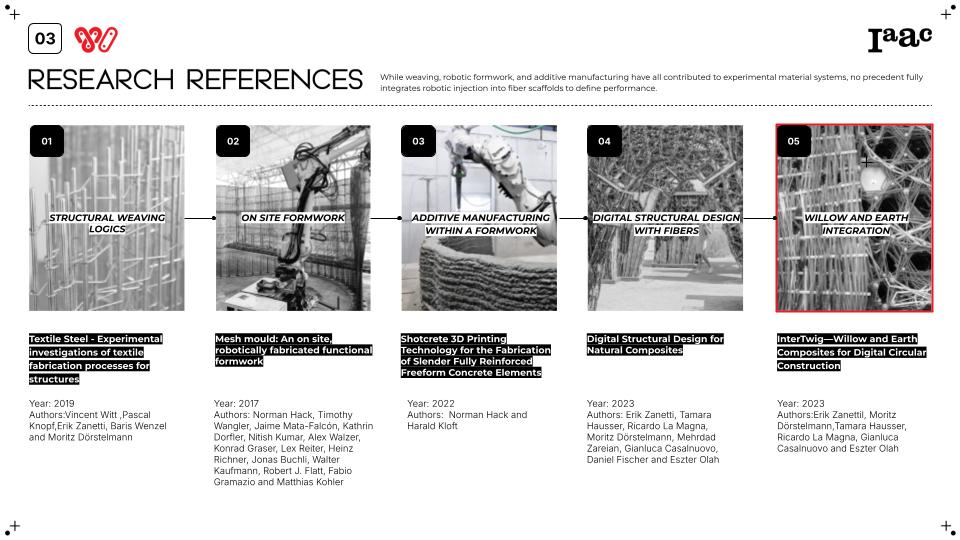
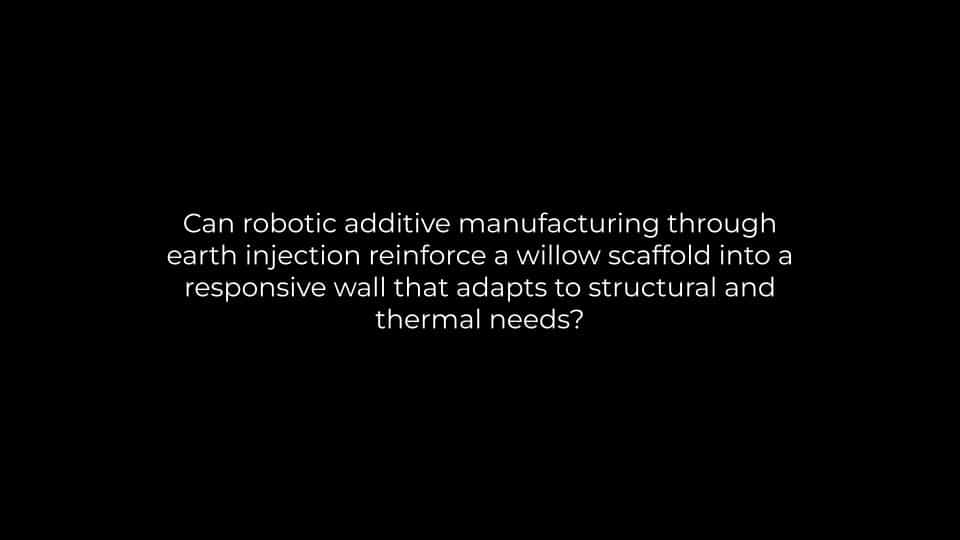
Material System
Two primary materials define the system: willow, a lightweight and flexible natural fiber, and earth, a compressive mass enhanced with natural additives like xanthan gum and casein. Willow is used to create a woven scaffold capable of bearing tensile loads, while earth is robotically injected to form a thermal mass and compression core . Material testing informed mixture ratios, curing conditions, and adhesion behavior between the components.
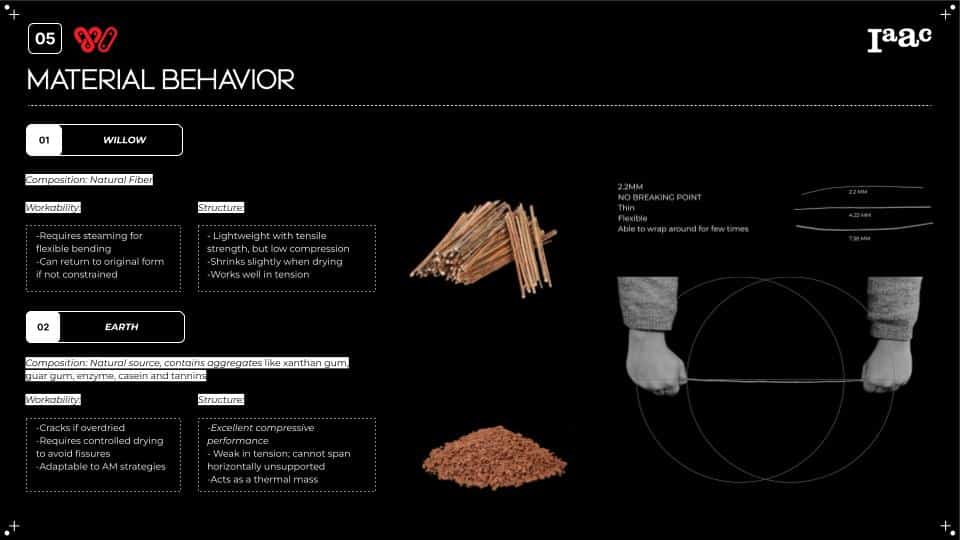
Project Intention
The core hypothesis is that weaving and robotic earth injection, though distinct in logic and role, can function as a hybrid construction strategy. Each contributes complementary properties: willow offers flexibility and geometrical structure, while earth provides mass, insulation, and reinforcement.
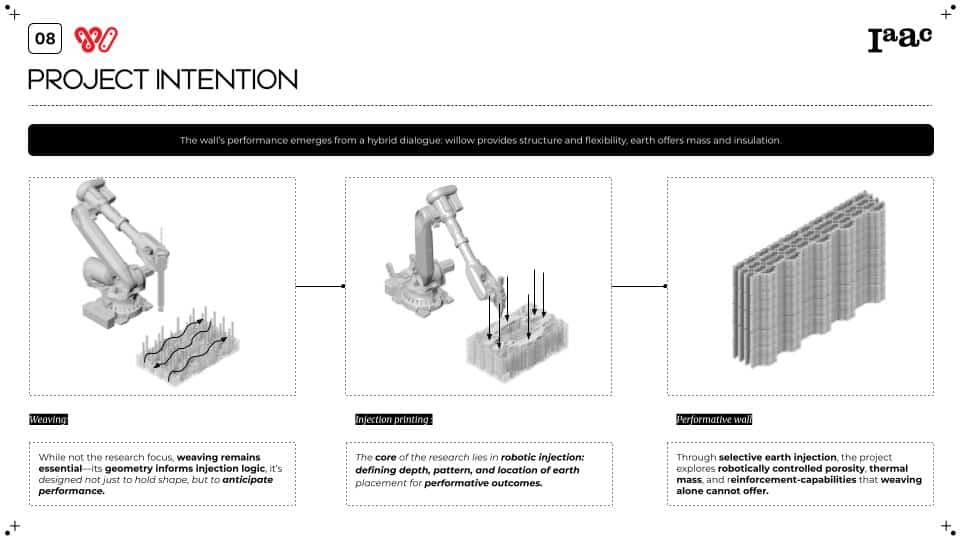
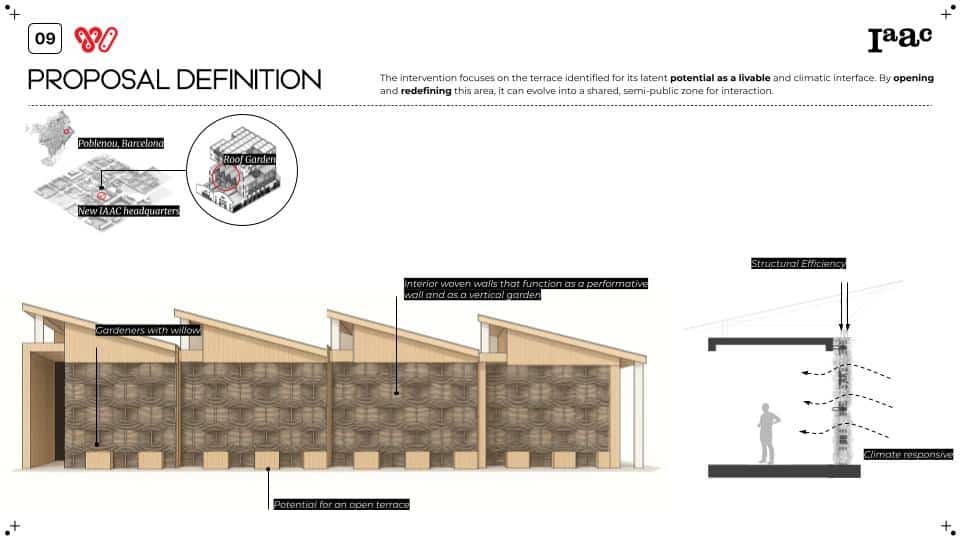
Structure System
This hybrid structural system integrates willow weaving, which provides tensile strength through dynamic tension, with robotic earth injection that delivers compressive strength. Together, they form a strong and thermally efficient wall.
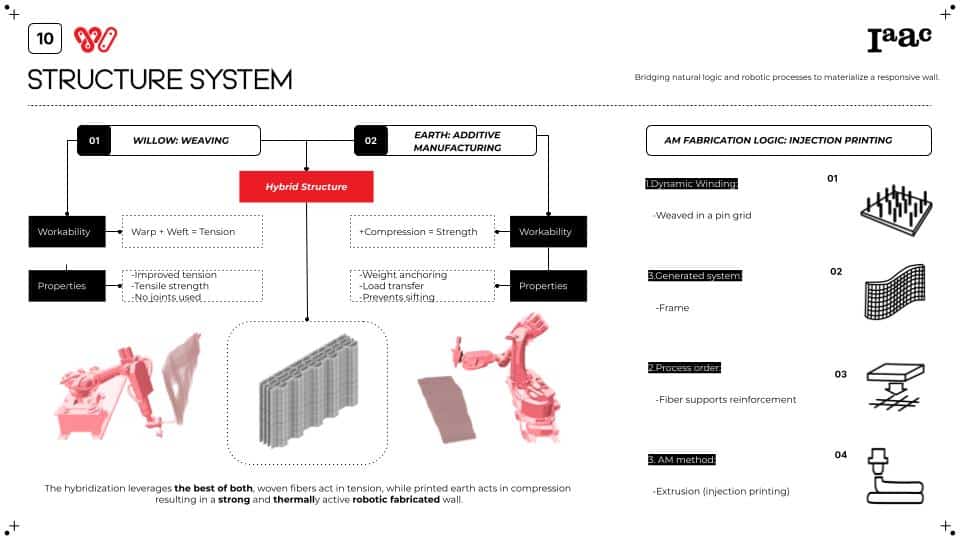
Workflow
1. Pre Fabrication Setup
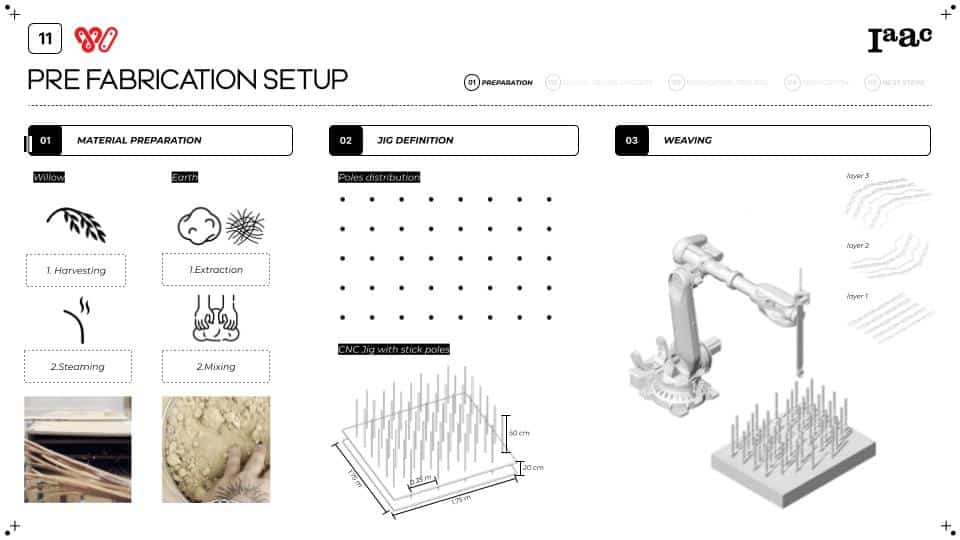
2. Digital Design Process
The project defines a 3D interlocked weaving logic optimized for thermal performance, structural behavior, and injection precision. A catalogue of ten configurations compares densities, pole spacing, and fiber use, highlighting geometric impact on performance and resource efficiency. This comparative study informs design adaptability and material optimization for hybrid earthen construction systems.
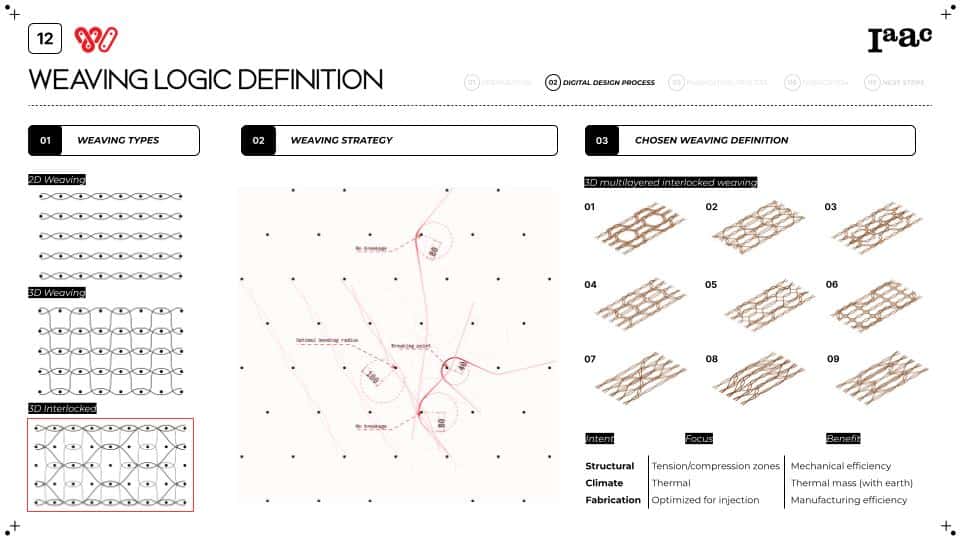
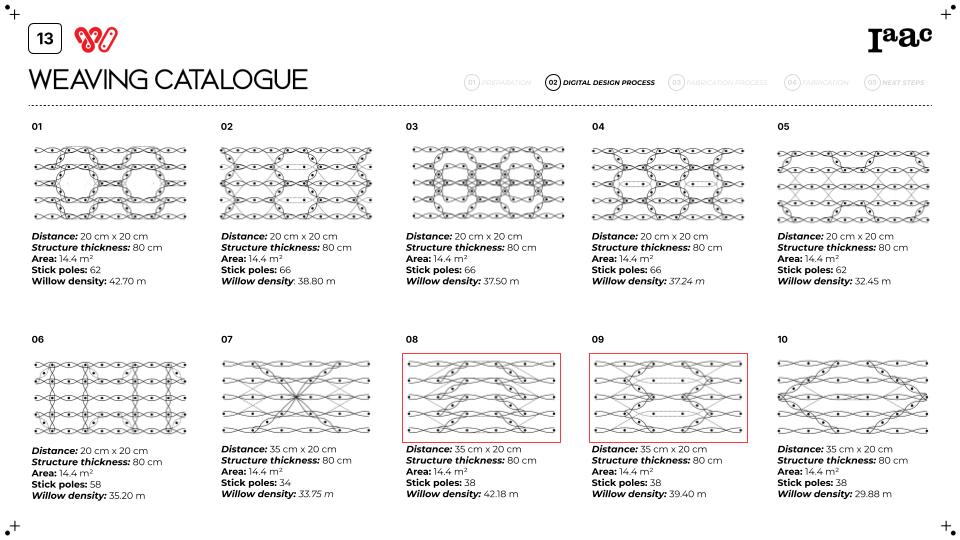
The injection strategy is carefully calibrated, with up to 30 injection points per module and defined parameters such as injection depth (30 cm), zone width (50 cm), and curing time (48 h), optimizing performance across 14 cavities per wall. FEM analysis confirms the thermal efficiency of the reinforced wall, reaching a U-value of 0.25 W/m²K—well below the regulatory limit—demonstrating that the willow-earth composite not only performs structurally, but also delivers measurable insulation benefits.
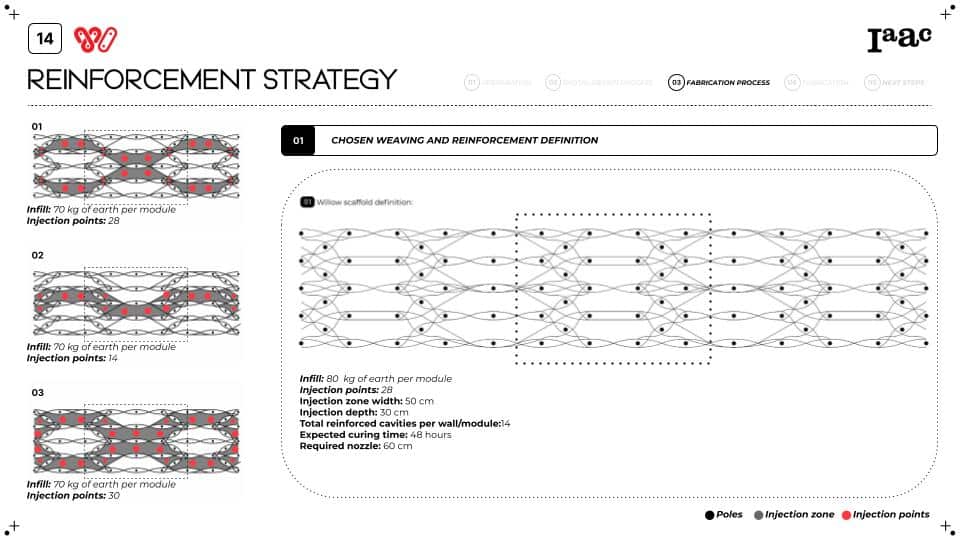
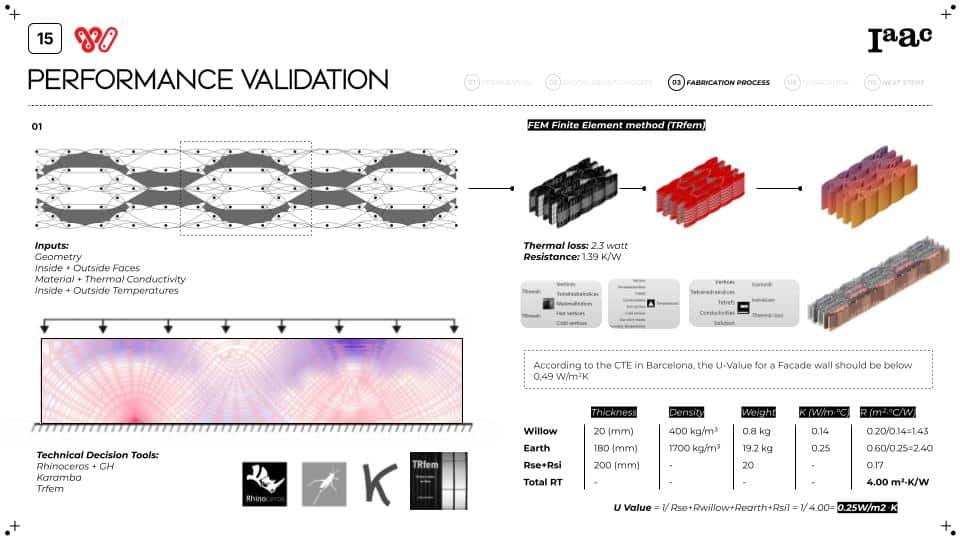
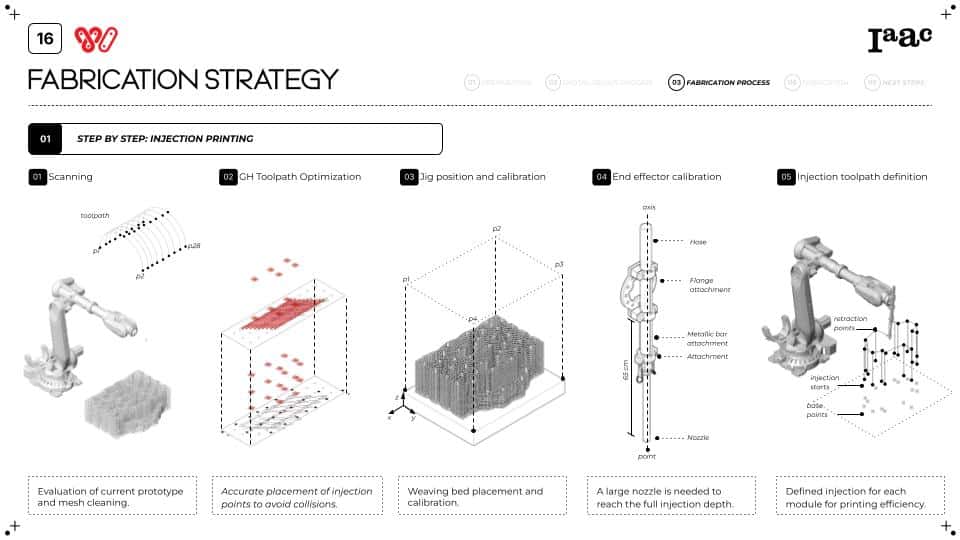
3. Fabrication
The fabrication process of the Terrawave module integrates robotic earth injection, a defined multilayered wall prototype, and a precise assembly logic. Clay and earth are injected using linear toolpaths controlled by ABB robotic arms. Modules incorporate cavities for water, electricity, and vegetation expansion. The modular strategy enables both vertical and horizontal aggregation, with joinery optimized for in situ or off-site robotic fabrication, ensuring scalability and ease of construction.
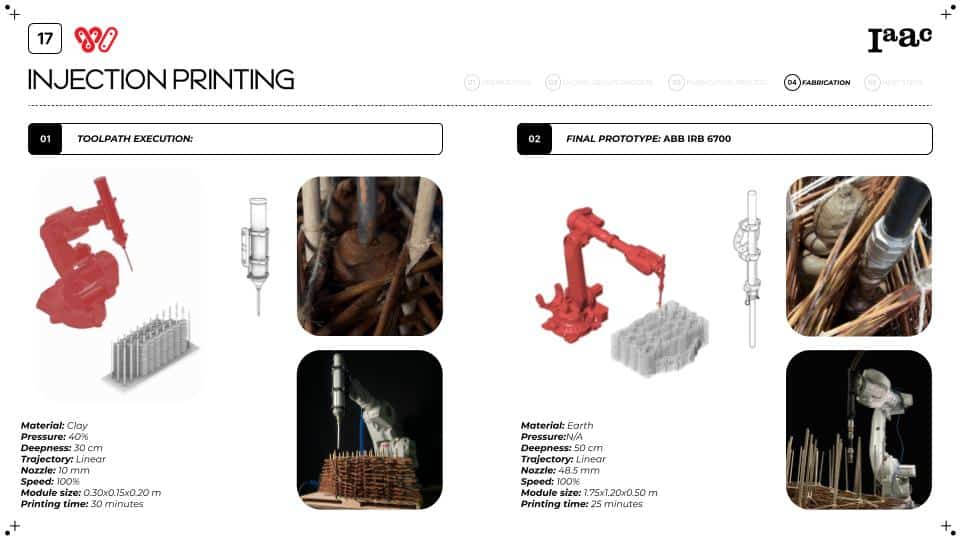
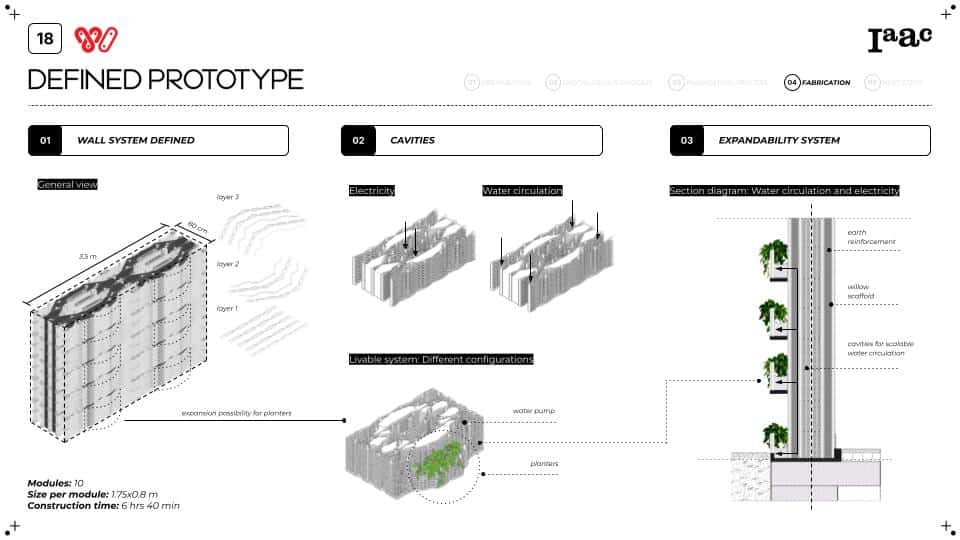
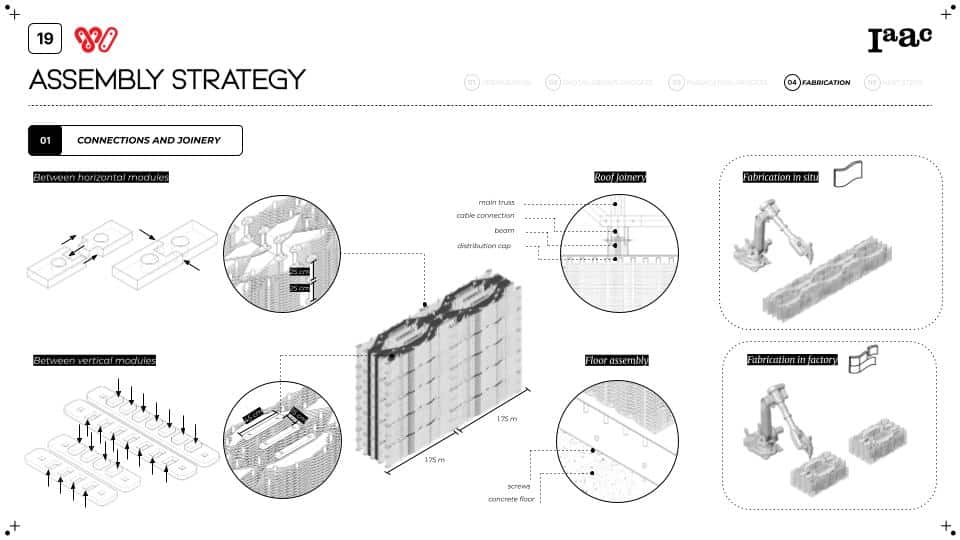
Our system: Adaptive configurations
Terraweave is designed as a modular and reconfigurable system, adaptable to diverse use cases including facades, interior partitions, and thermal buffers. Future development will explore full-scale deployment, increased robotic precision, and expanded functionalities such as integrated HVAC channels or photovoltaic support structures .
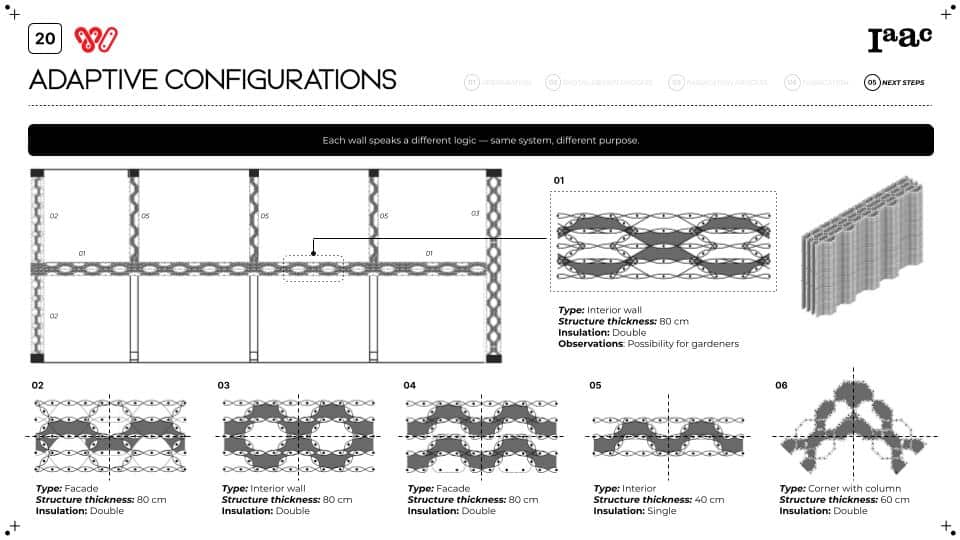
Conclusions
Terraweave proposes a new paradigm in wall construction—merging digital fabrication with natural materials to create responsive, climate-resilient systems. By leveraging the synergy between robotic control and material intelligence, the project offers a scalable and sustainable alternative to conventional walls, addressing the architectural needs of a warming world.
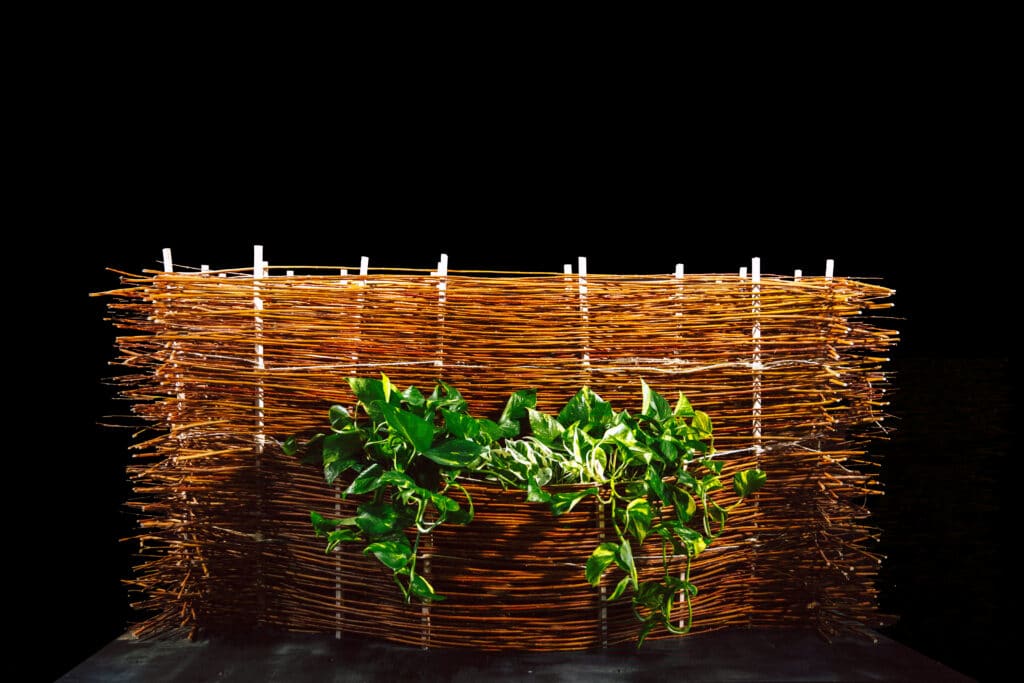
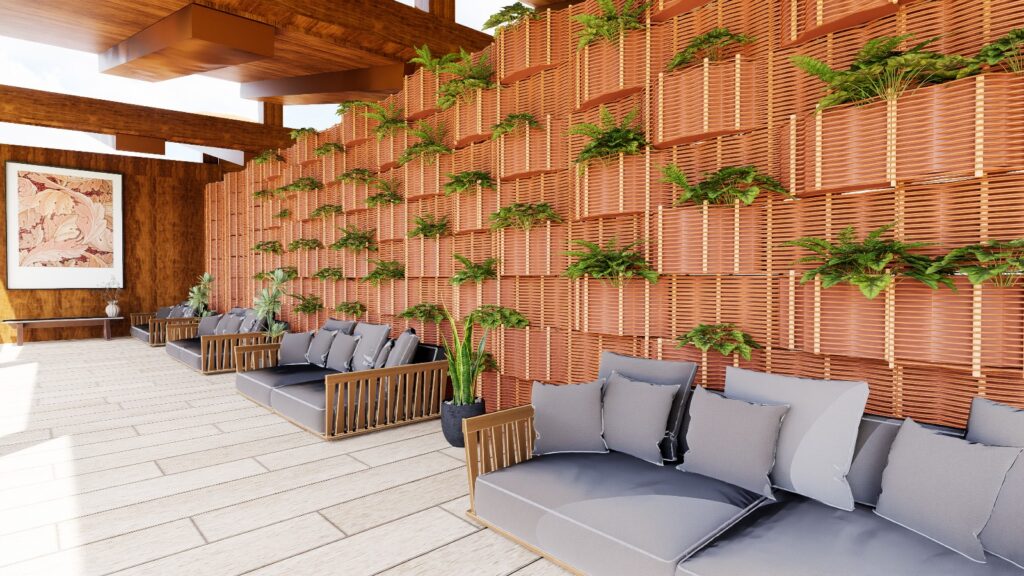
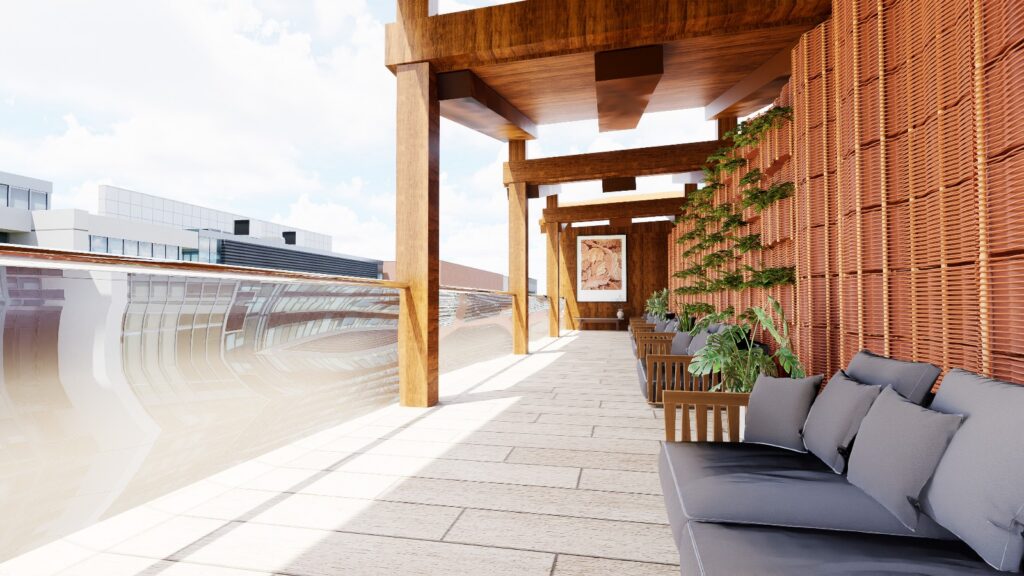
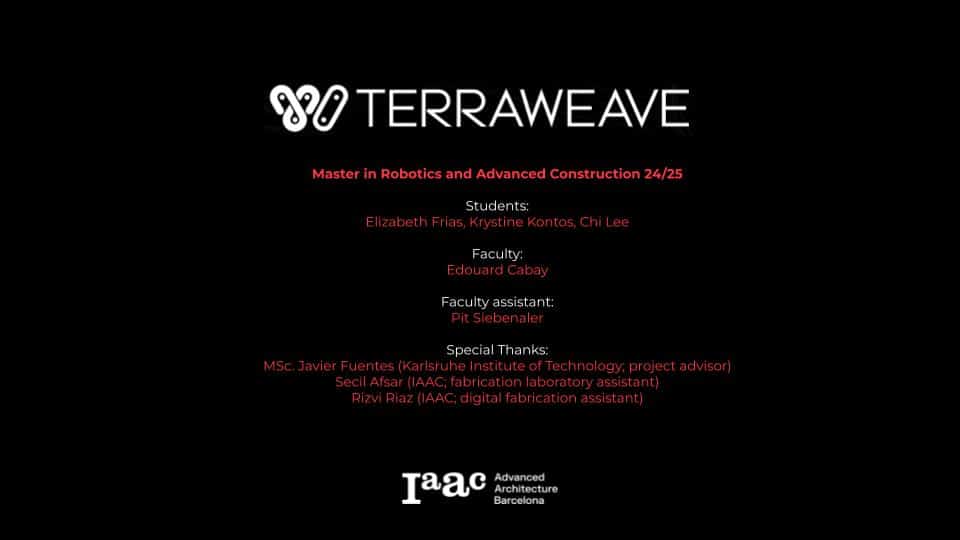