Leveraging Computer Vision for Sustainable Design with dimensional waste timber
Building upon the established design principles of disassembly explored in the prior semester, Timber Narratives this semester investigated the potential of computer vision and image analytics to further optimize material conditioning and manufacturing processes for dimensional waste timber. This iterative approach aimed to integrate data-driven design strategies by leveraging computer vision for data collection and analysis of critical parameters impacting final execution quality.
The inherent paradox of working with waste timber, a material with minimal embodied carbon, necessitated the development of a highly efficient robotic processing system. This system required balancing computational efficiency with processing accuracy to handle large volumes of this low-density material. While the concept of storing carbon in wood products offers environmental benefits, recent research suggests this storage is minimal compared to overall carbon emissions and cannot be used as a long-term offset strategy. Therefore, the focus of our robotic system shifted towards maximizing the processing efficiency of waste timber, recognizing that the embodied carbon emissions from construction materials are a far greater concern.
Our project aim is as follows:
“To develop an efficient processing strategy for end-of-life dimensional timber so that it can be repurposed in a design for disassembly workflow for temporary spaces.”
The design outcome for this project operates 3 tiers :
Tier 1: Component
At this level, each stick (component) can be separated into various ranges that correspond to how it has been scanned and processed.
The joinery design is standardized so that each component works universally with no collisions.
Tier 2: Sub-assemblies
The arrangement of the components makes the sub-assembly.
Tier 3: Global design
At this level, the components are assembled to meet various architectural contexts. Once the design reaches its end of use the sticks can be disassembled and used in a new design.
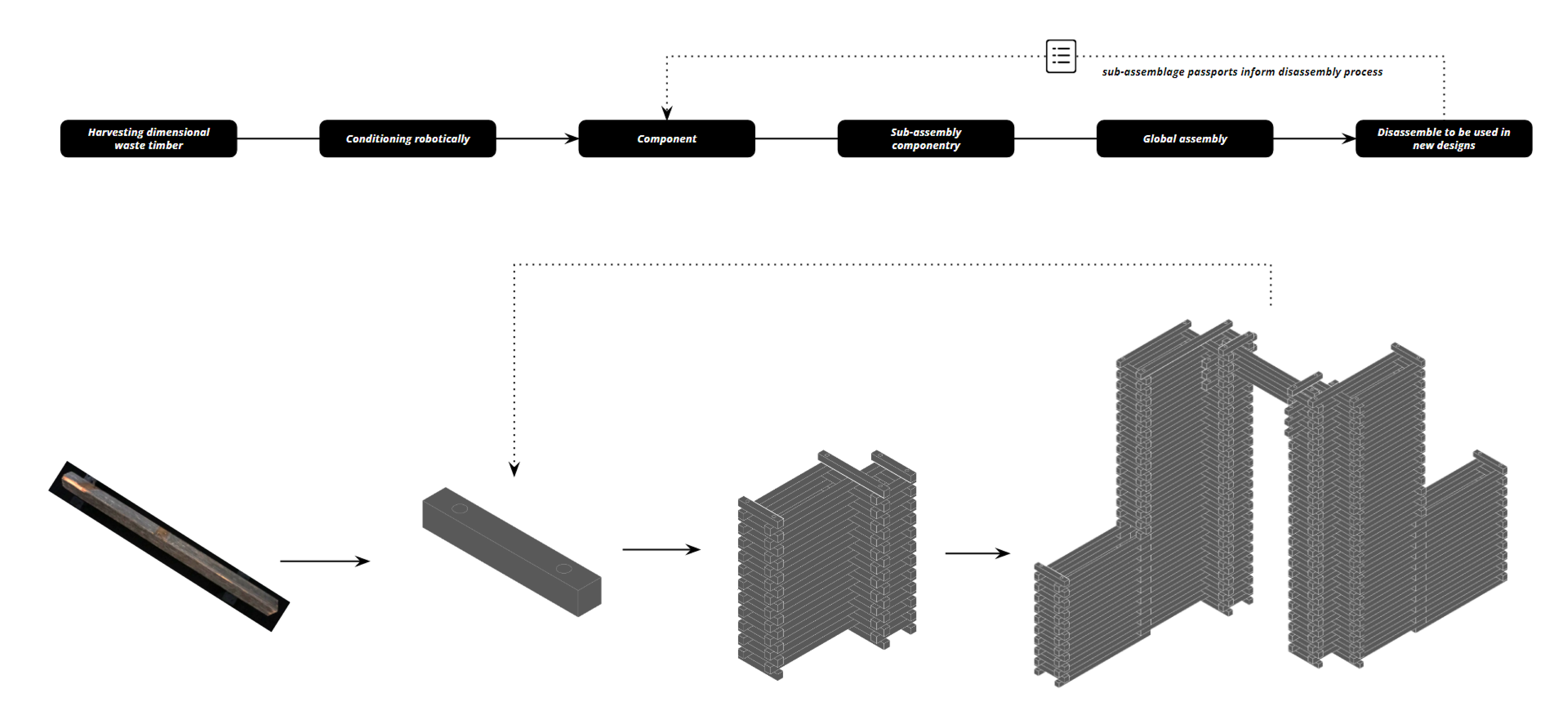
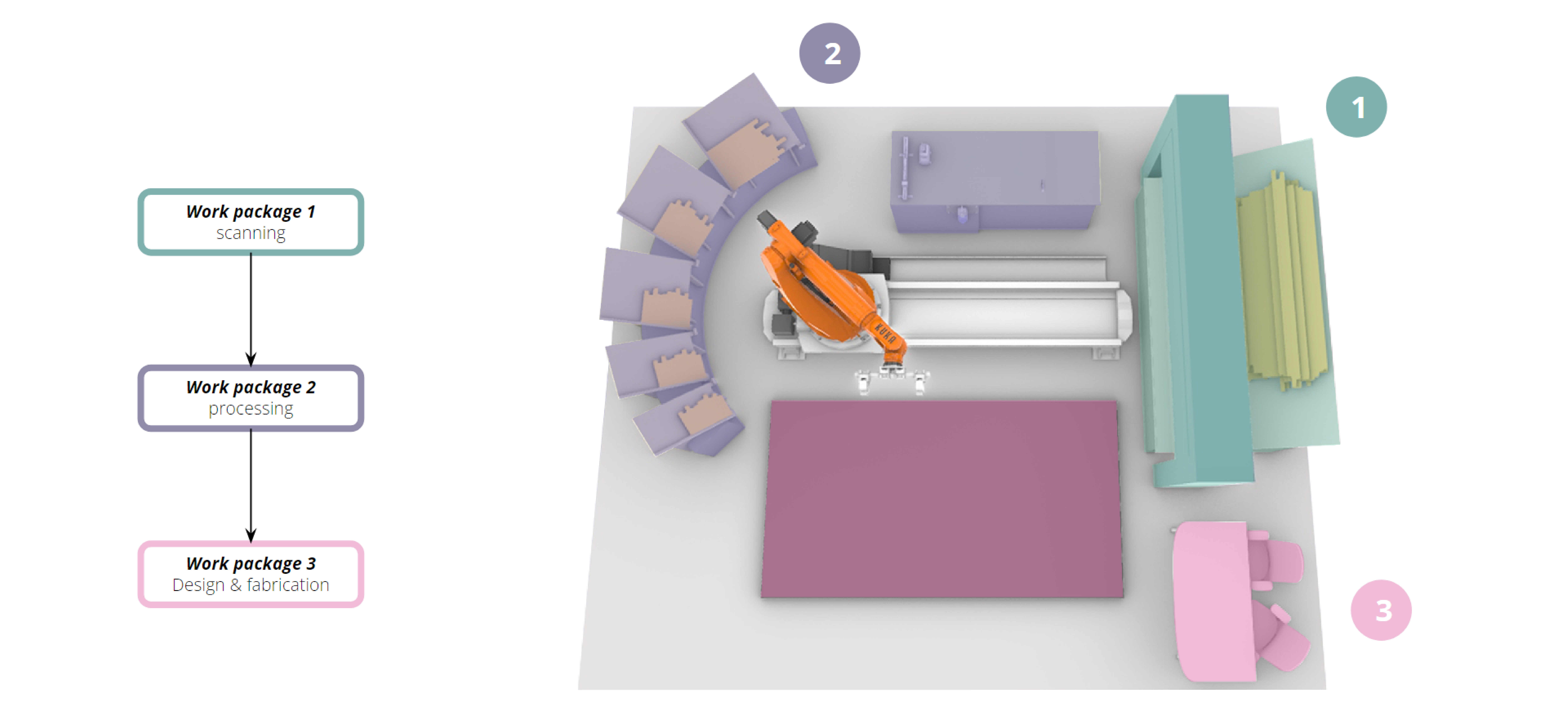
Our project comprises three main work packages: Scanning, Processing, Design & Fabrication. Each has a data type input that can be analyzed to produce a data output to inform the next process.
The workflow starts with scanning the waste timber with an RGB image to determine the overall length, usable length, defect points, and picking position for processing.
The next work package is processing were the sticks are robotically conditioned – meaning the defects points are removed, joinery holes are drilled, and placed in to the respective size range
Work package 3 is design and fabrication – here we work with the material inventory we have to construct the architectural piece.
State of the art
Urban Machine – Material conditioning
Urban Machine tackles wood waste in construction by employing robotics and artificial intelligence. Their robots efficiently extract nails, screws, and other fasteners from salvaged lumber. This innovative approach allows them to transform discarded wood into premium building materials, promoting a circular economy within the construction industry.
Embraced Wood – Regrading and Material passport.
Regrading: This involves reevaluating how wood is classified based on quality. Traditionally, minor imperfections might exclude wood from certain applications. Regrading could establish new criteria to allow using “imperfect” wood in suitable constructions, reducing waste. Thus, Regrading could allow more wood to be used in construction, reducing reliance on virgin lumber.
Material Passport: This refers to creating a record that tracks a material’s journey, including its source, properties, and any treatments it’s undergone. A wood passport would provide transparency about the wood’s origin and sustainability. Thus, builders and consumers get information about the wood’s environmental impact.
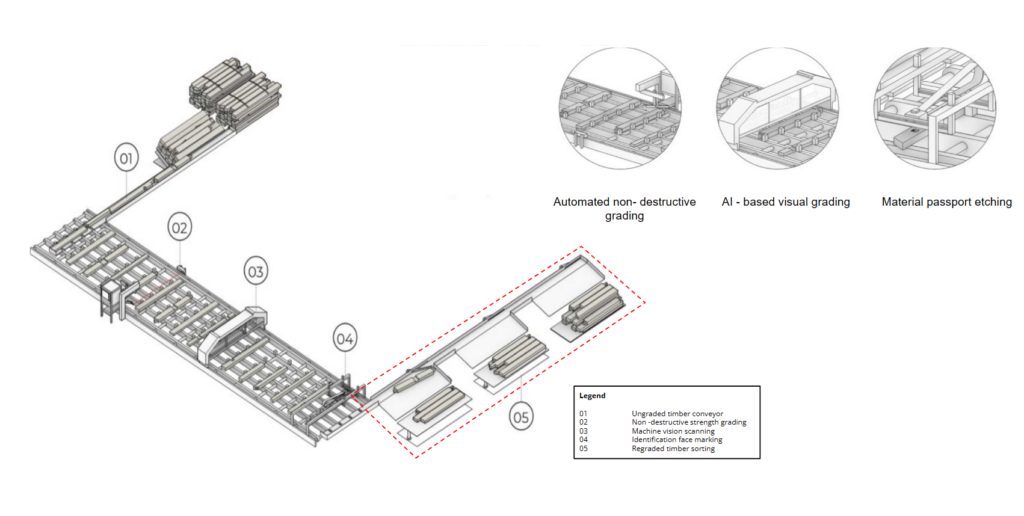
Decoded Disorder – Feature detection
Exploring the potential of readily available waste materials in the design process. Turning irregularities and imperfections inherent in waste materials into advantages through “adaptive algorithmic workflows.” This suggests using algorithms to design and adapt based on the specific characteristics of the waste material. Likely to develop scalable design methods using waste materials efficiently. Thus, promotes sustainability and reduce reliance on virgin resources.
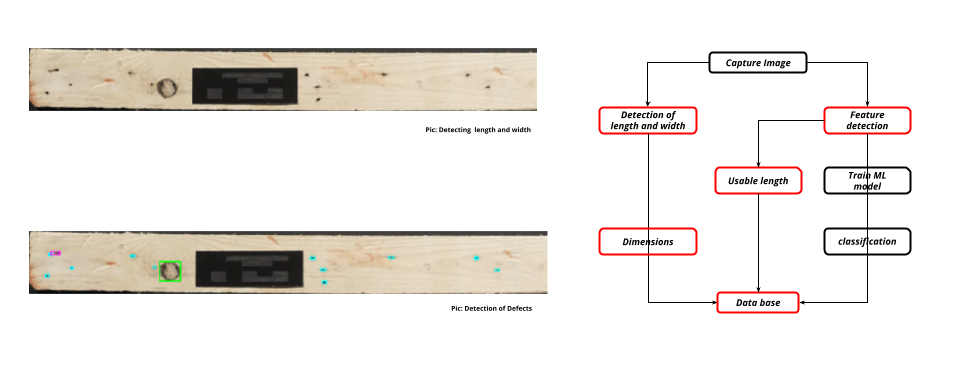
Cyber-Physical Robotic Process for Re-Configurable Wood Architecture – Connection system
The main concept tackles challenges in robotic construction, specifically regarding tolerances and potential errors during assembly.
- Concept: Design Localization – Focusing design on specific building sections or modules, ensuring each part is optimized for the construction location.
- Part-to-Part Localization: A system where individual pieces are designed to work together seamlessly through a specific joinery system. This reduces tolerance issues and minimizes errors during the robotic assembly process.
Benefits:
- Improved Accuracy: Precise design and joinery systems ensure parts fit together flawlessly.
- Reduced Errors: Localization minimizes the impact of slight variations in individual pieces.
- Efficient Robotics: The system allows robots to assemble structures with greater precision and consistency.
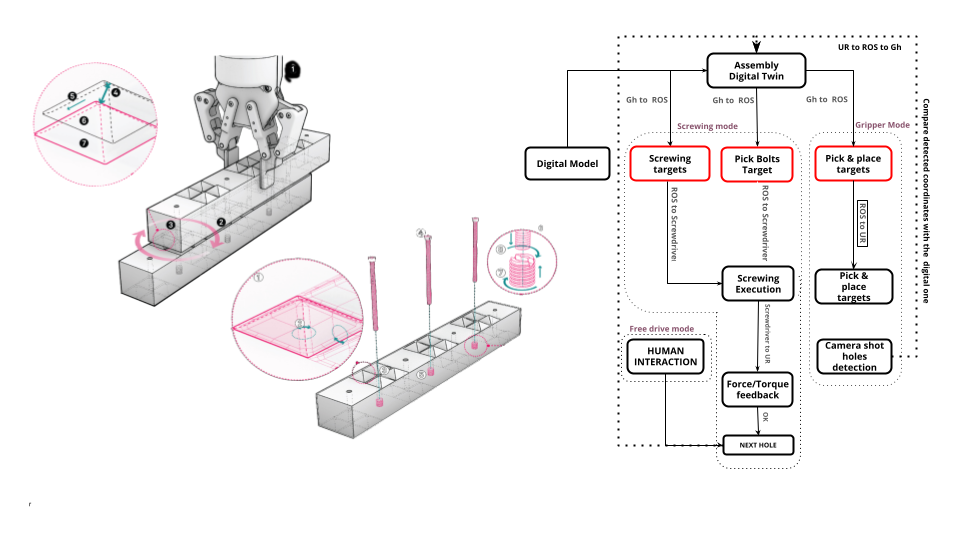
Design
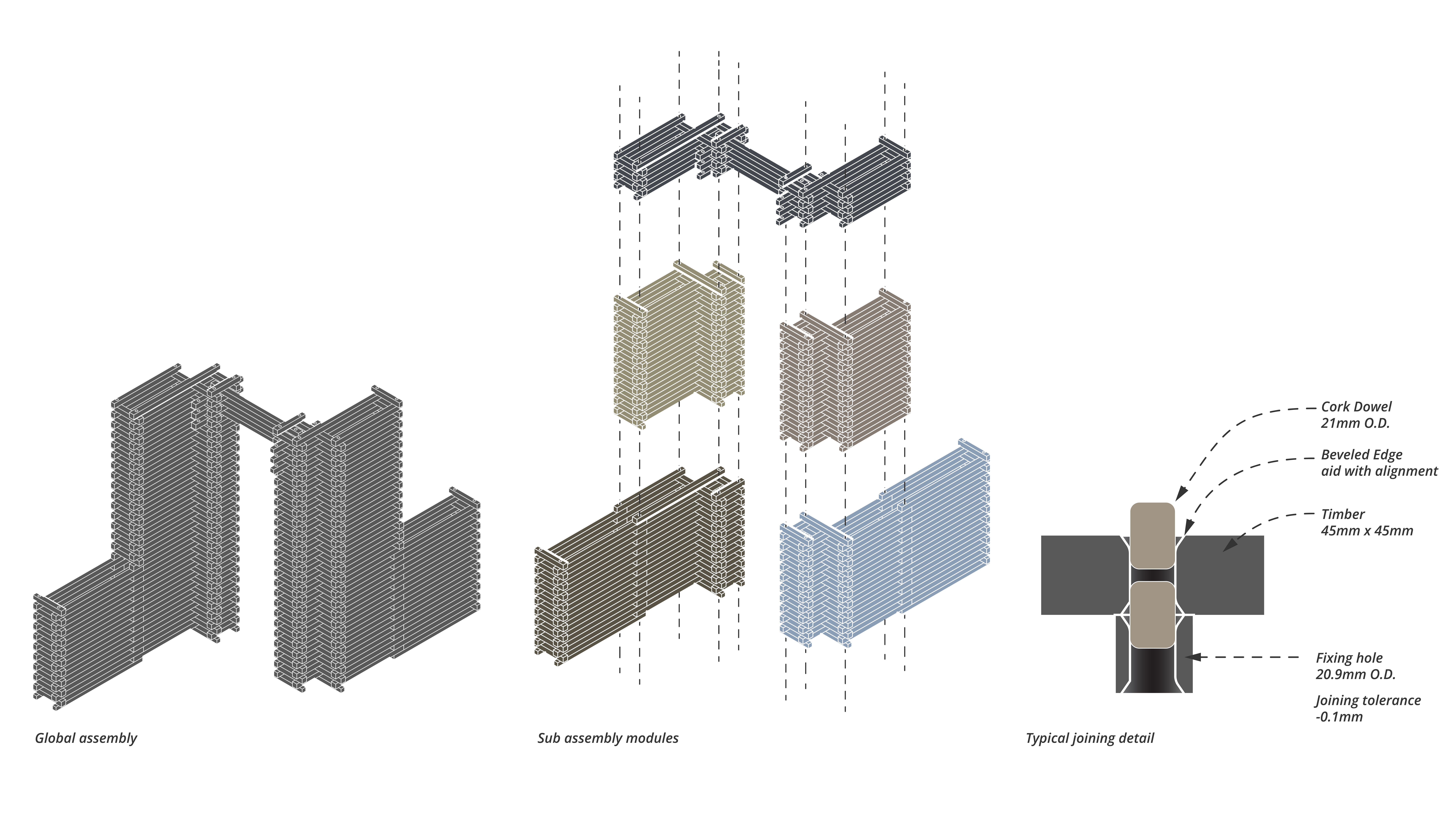

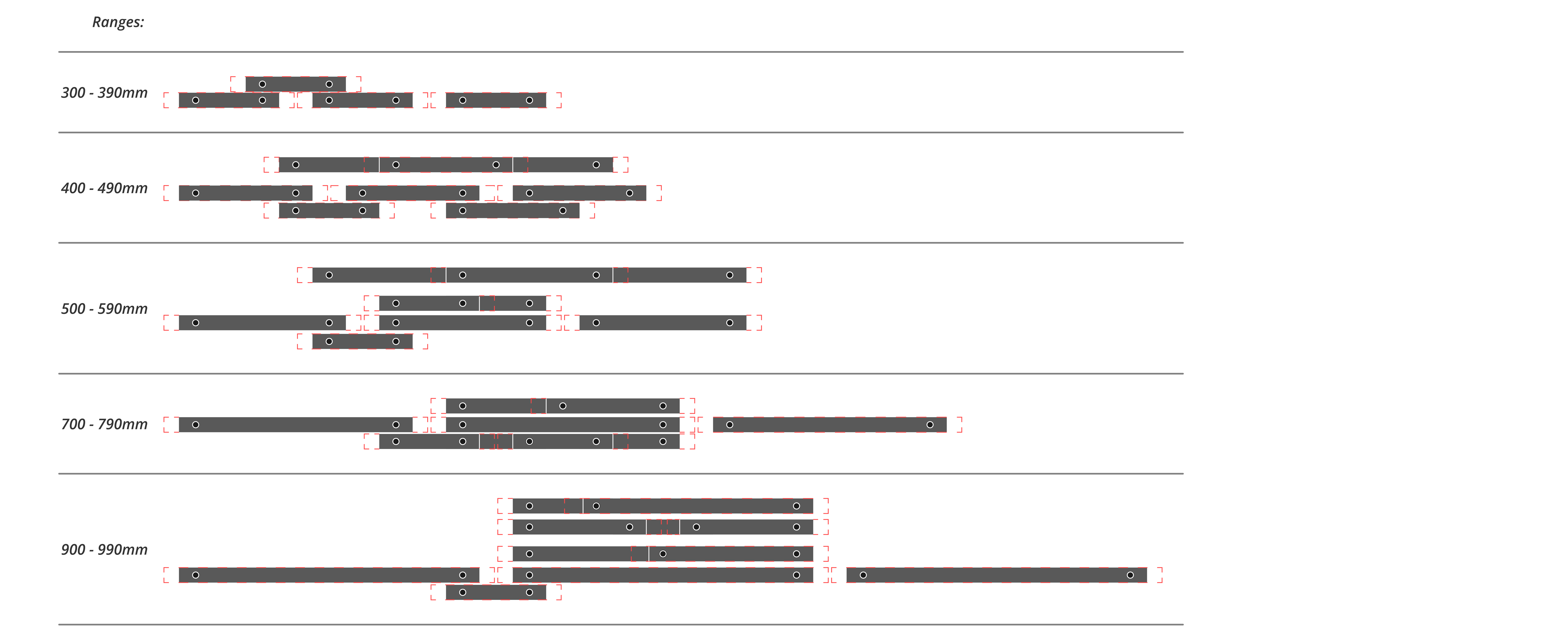
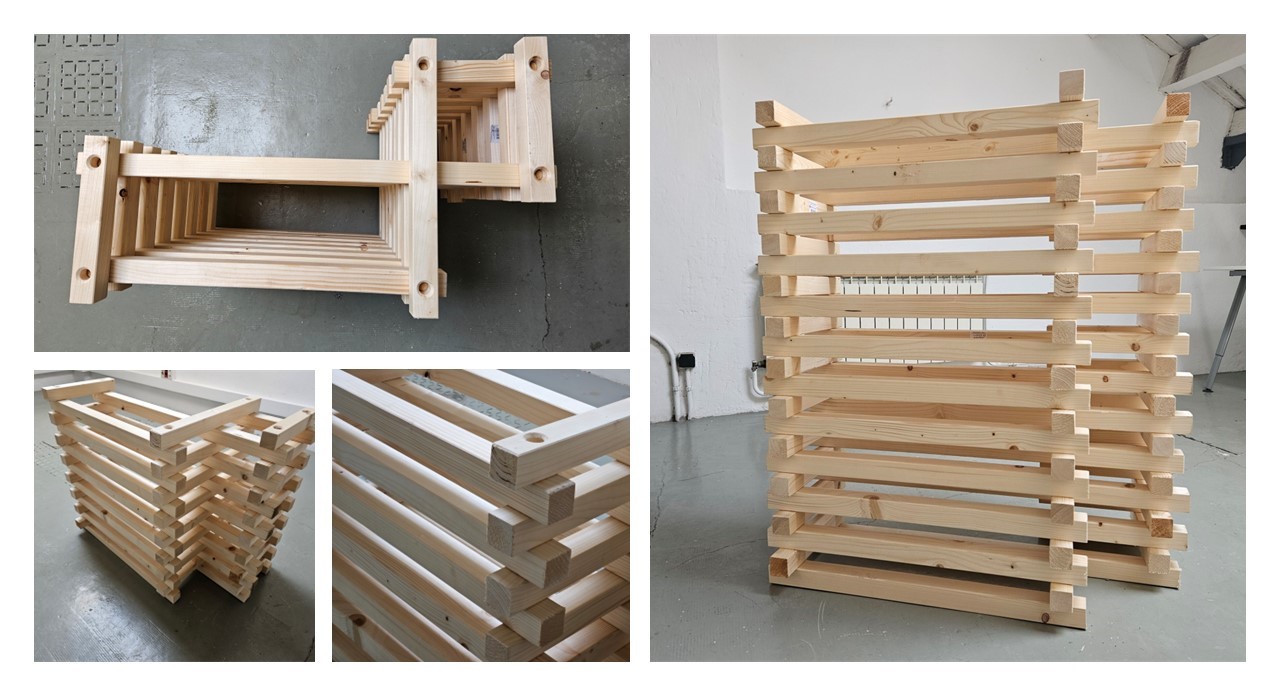
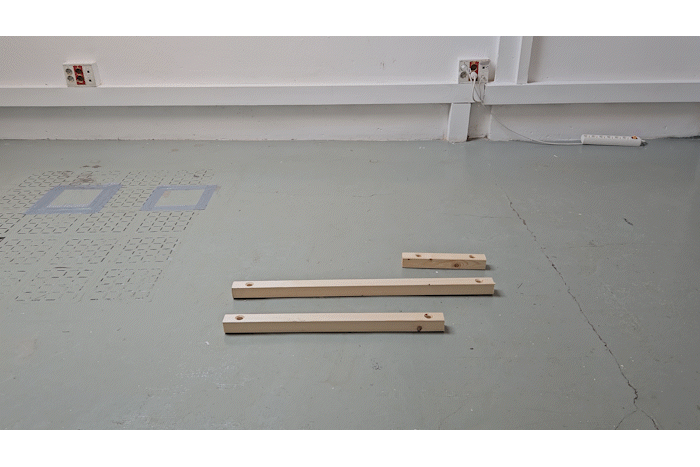
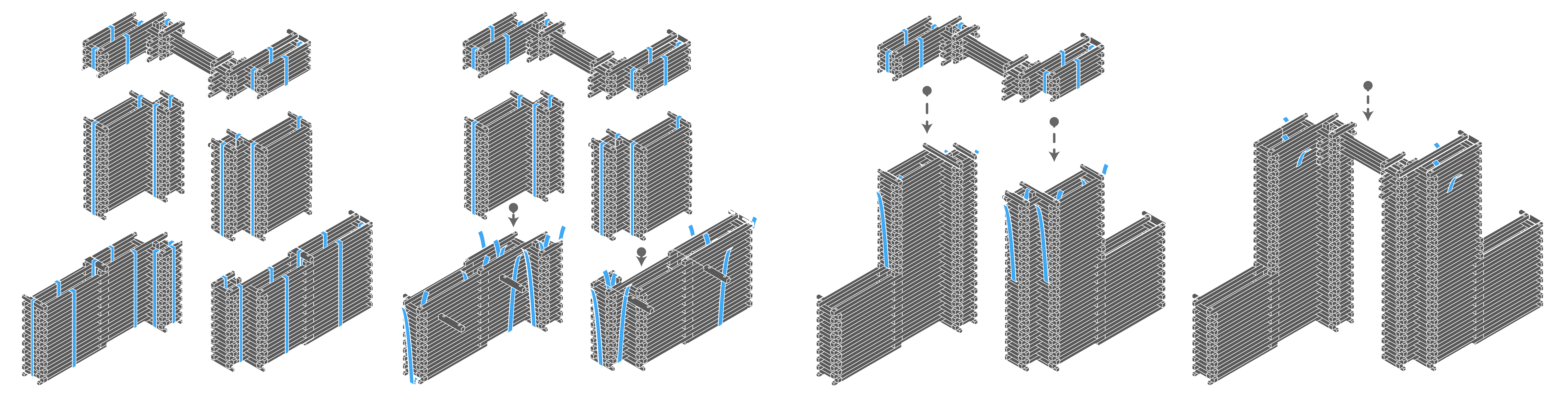
RENDERS
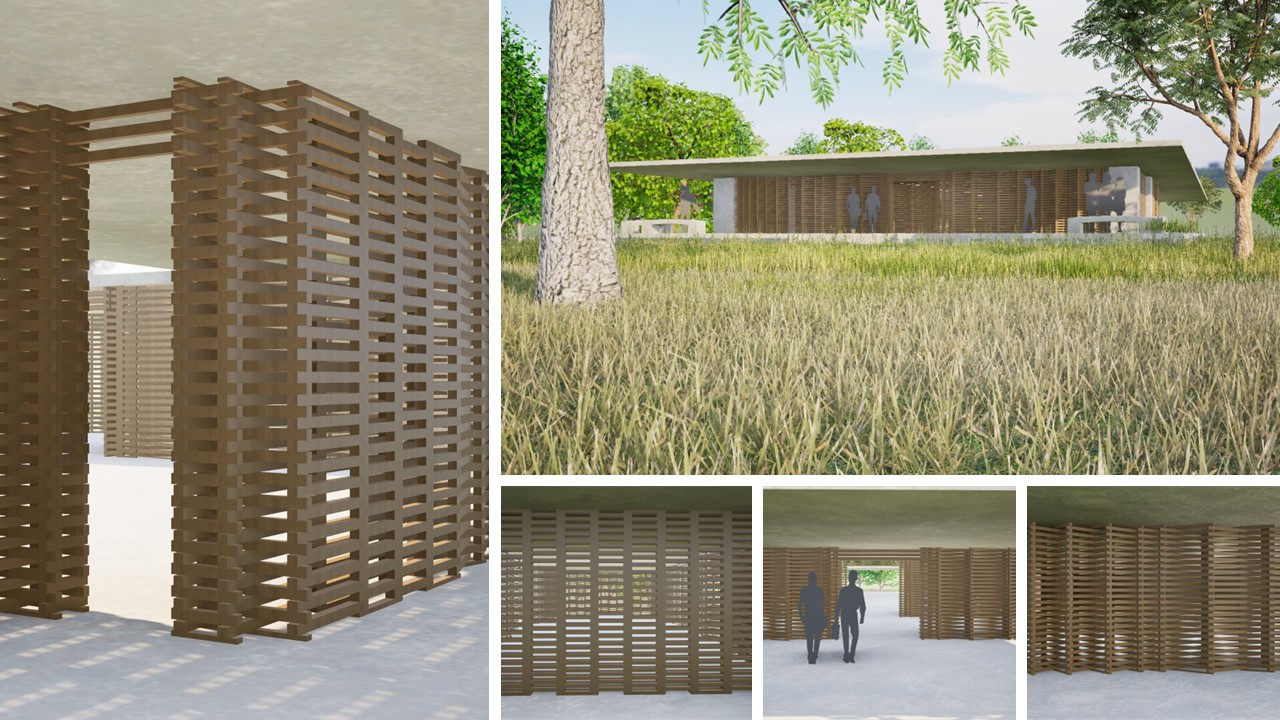
System architecture
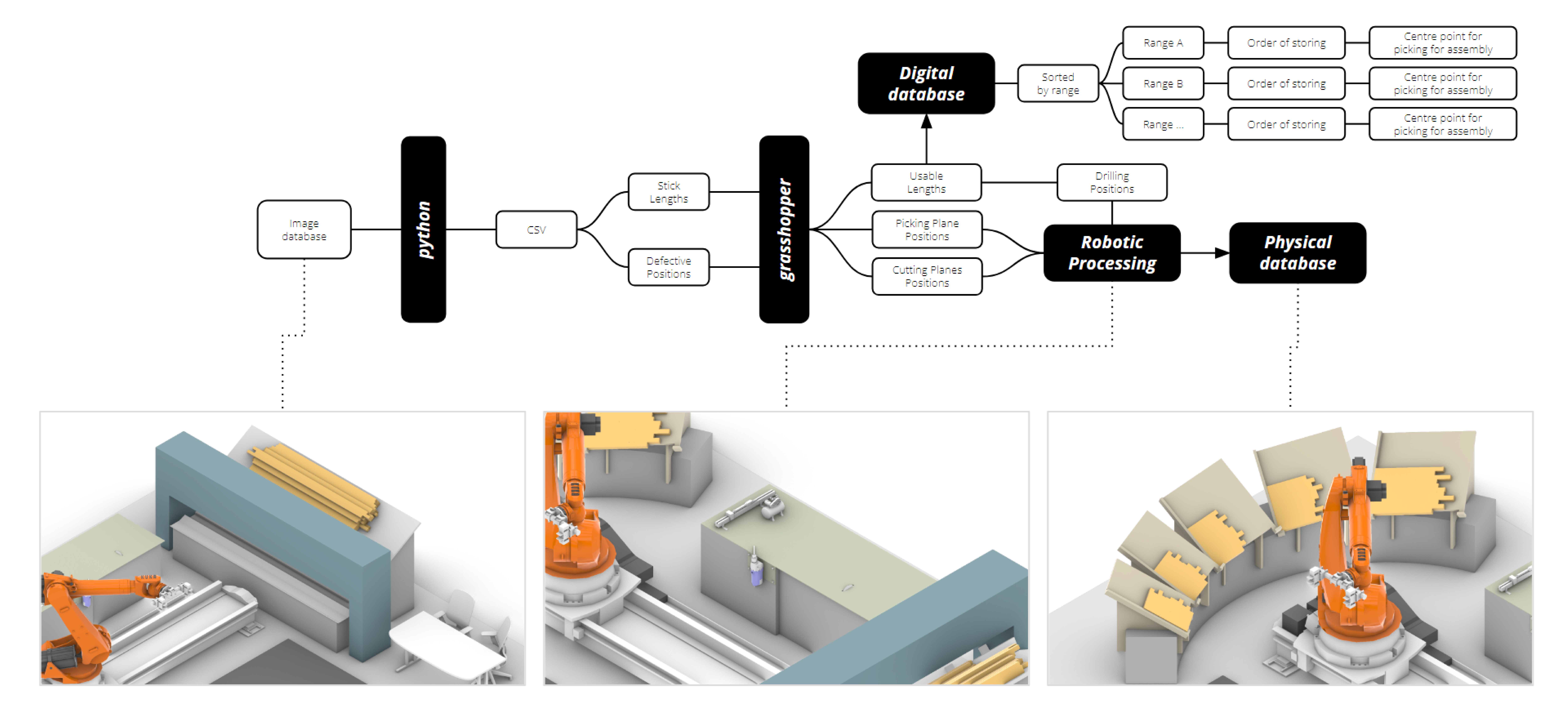
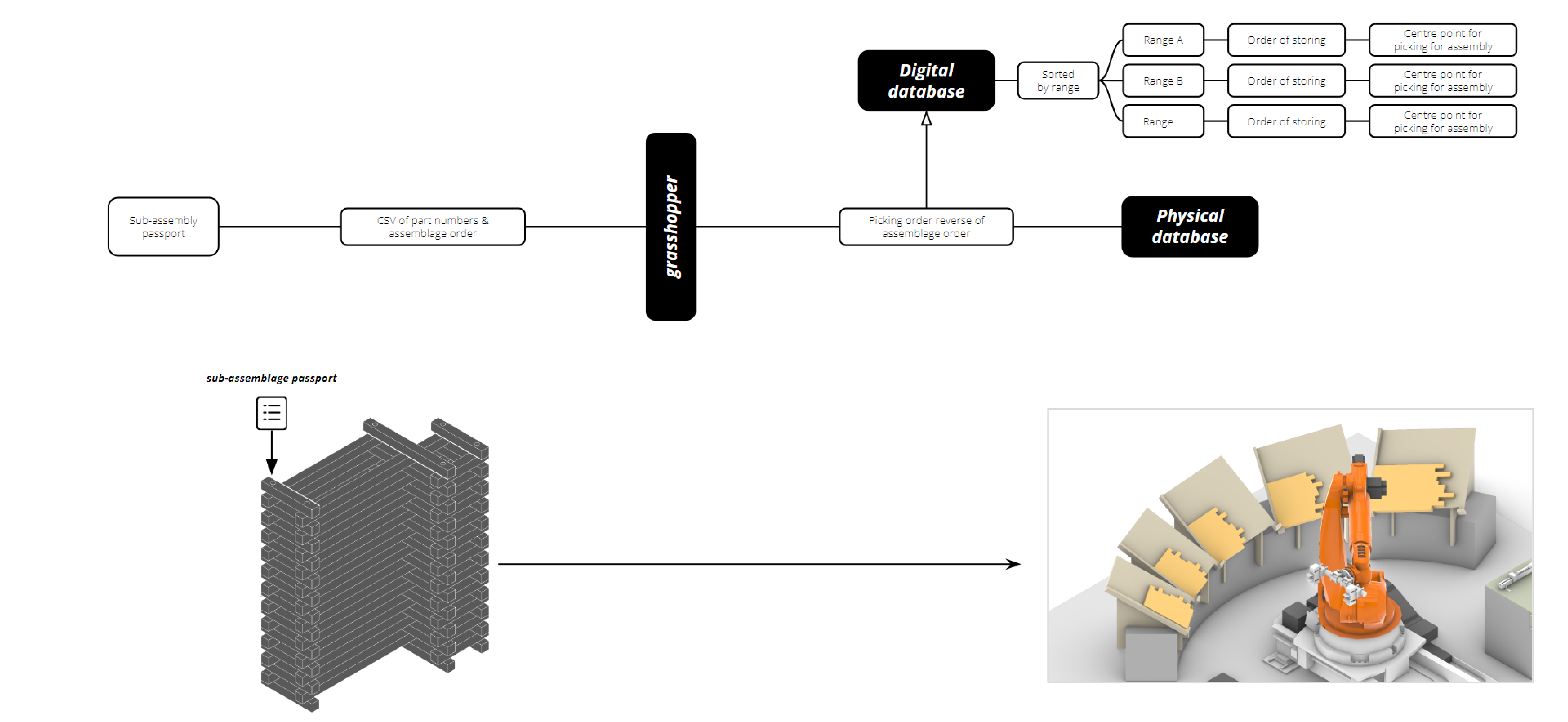
Scanning & processing
Computer Vision techniques were used to identify the defects and calculate the lengths of the pieces. The Python script analyzes images containing screws, employing OpenCV for image processing and OpenPyXL for data management. It begins by defining input and output directories along with an Excel file path. The find_screws function isolates screws within predefined regions of interest (ROI), and calculates their position in millimetres. The detected screw positions are logged in an Excel spreadsheet. The script iterates through each image in the input directory, processes them sequentially, and saves the processed images along with the extracted data. This automation streamlines screw detection and measurement tasks, enhancing efficiency in industrial or engineering applications.
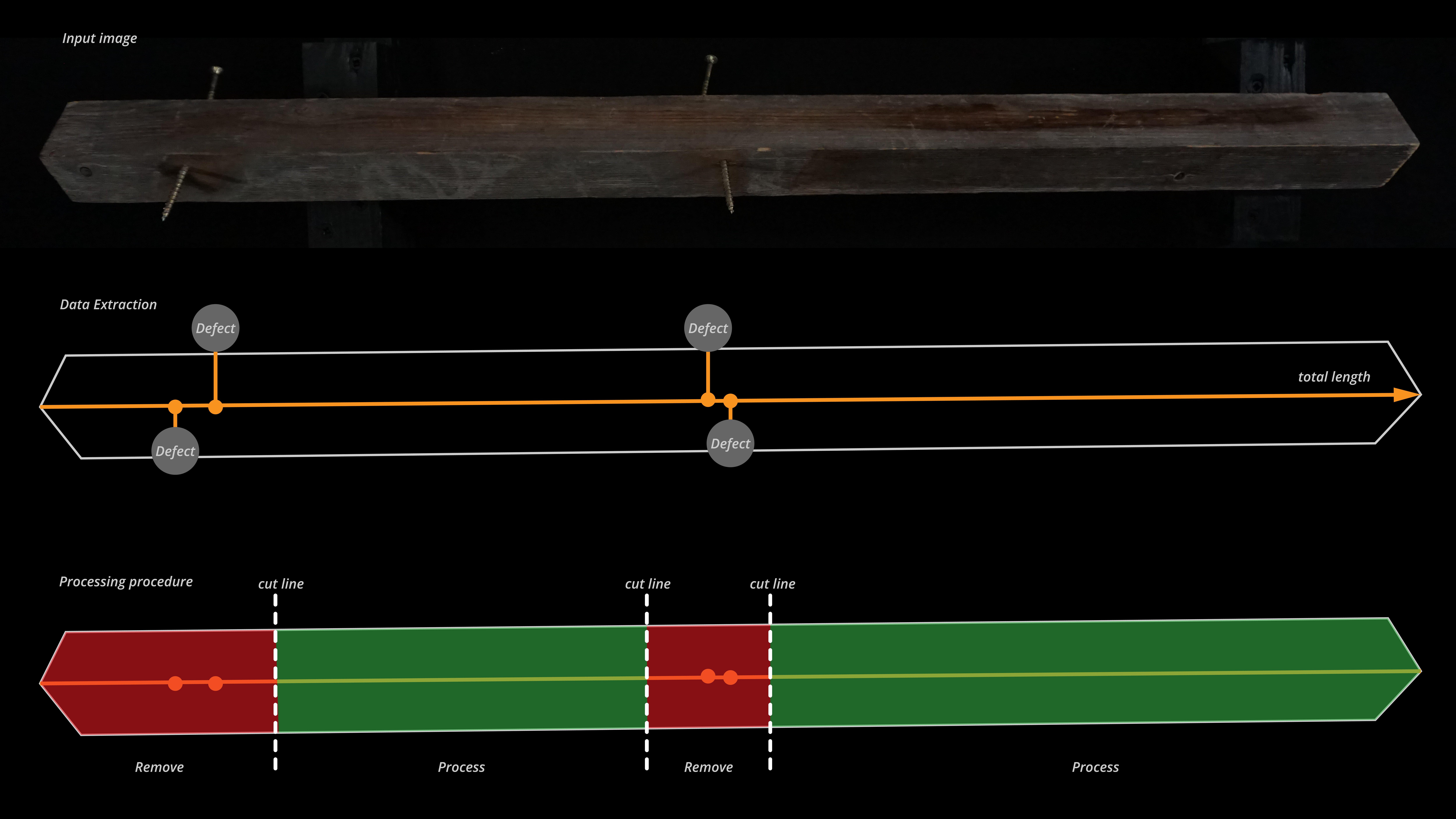
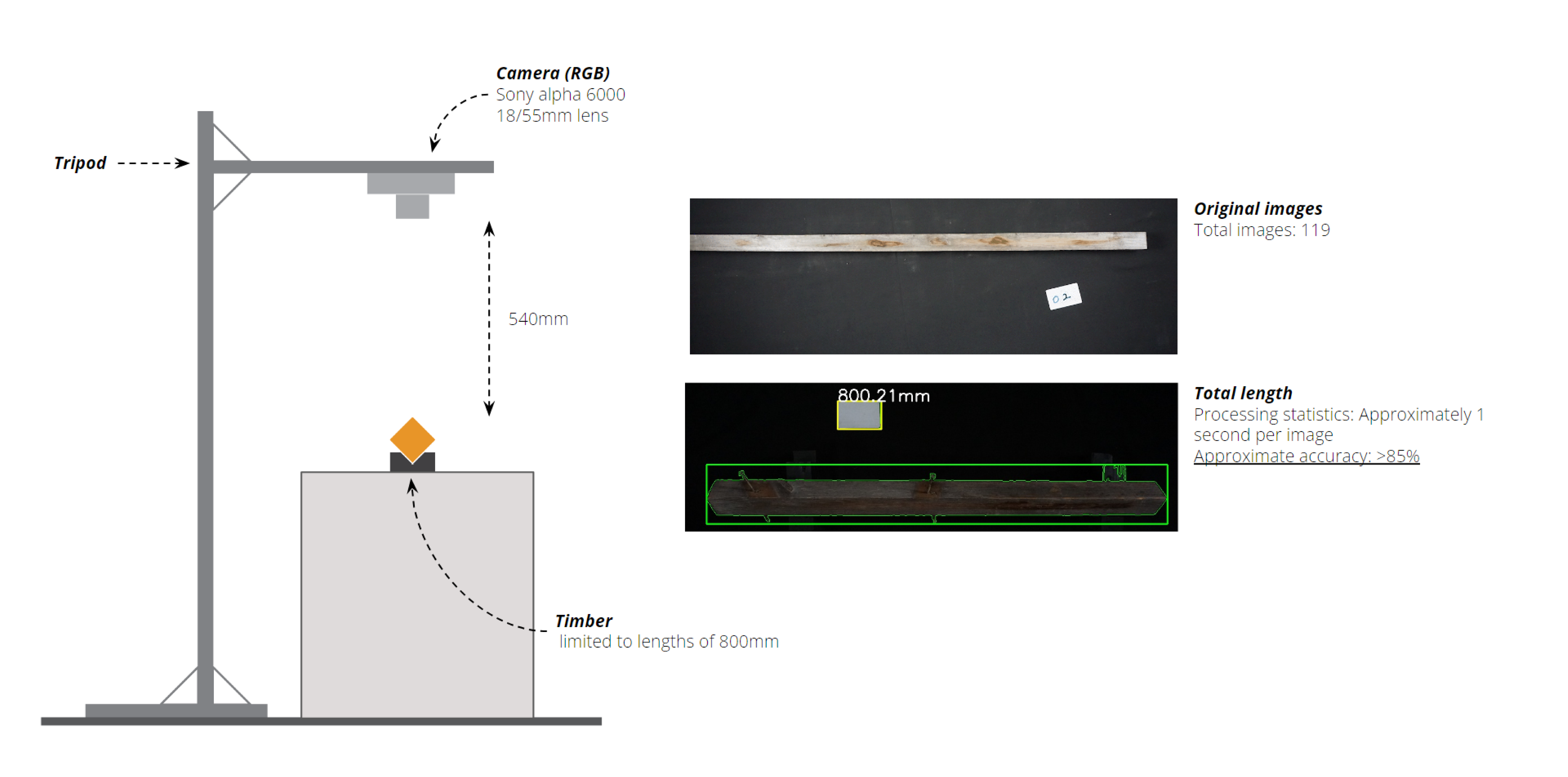


Processing
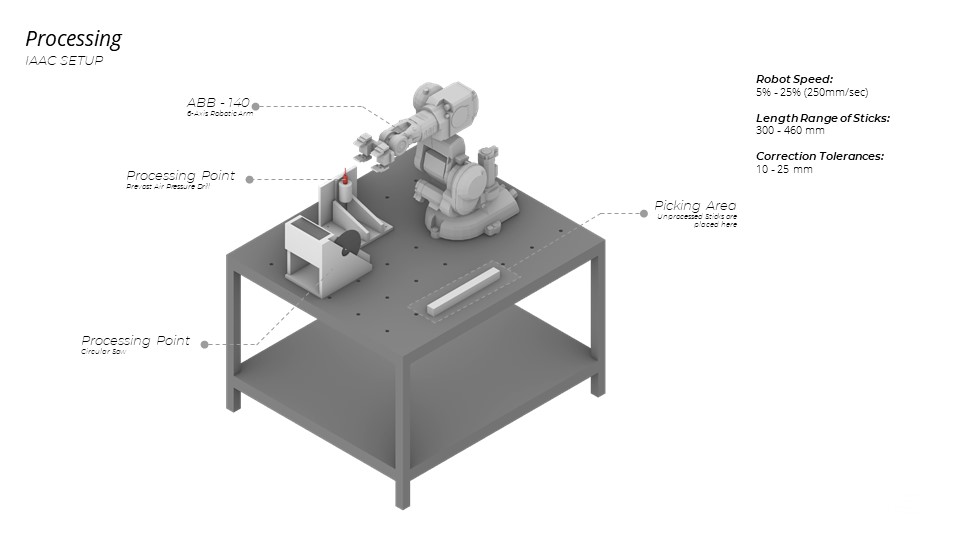
Fabrication
Assembly:
We have chosen a simple design for the fabrication process to create a proof of concept. The following are the details:
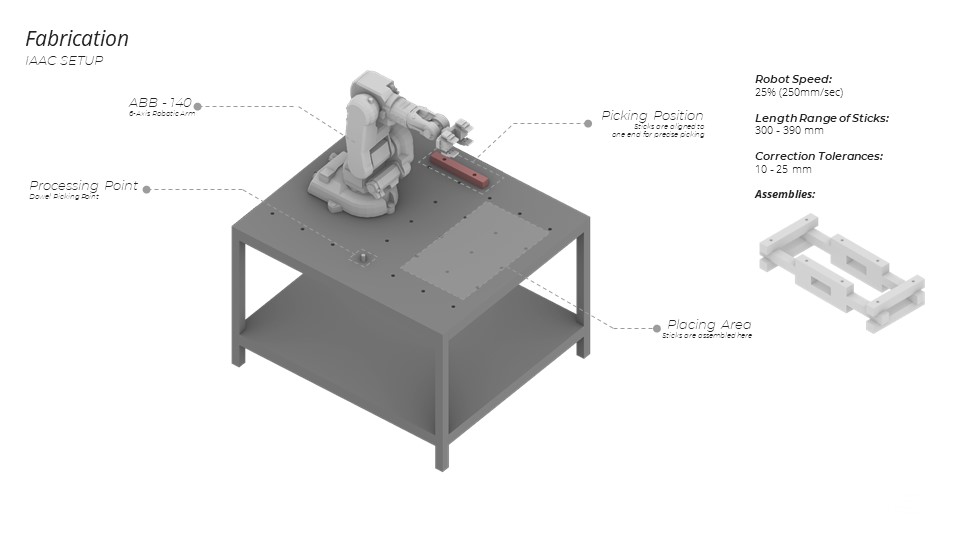
We have gone through over 20 iterations in the assembly process and have narrowed it down to the three most successful ones. Please see the assembly data below:
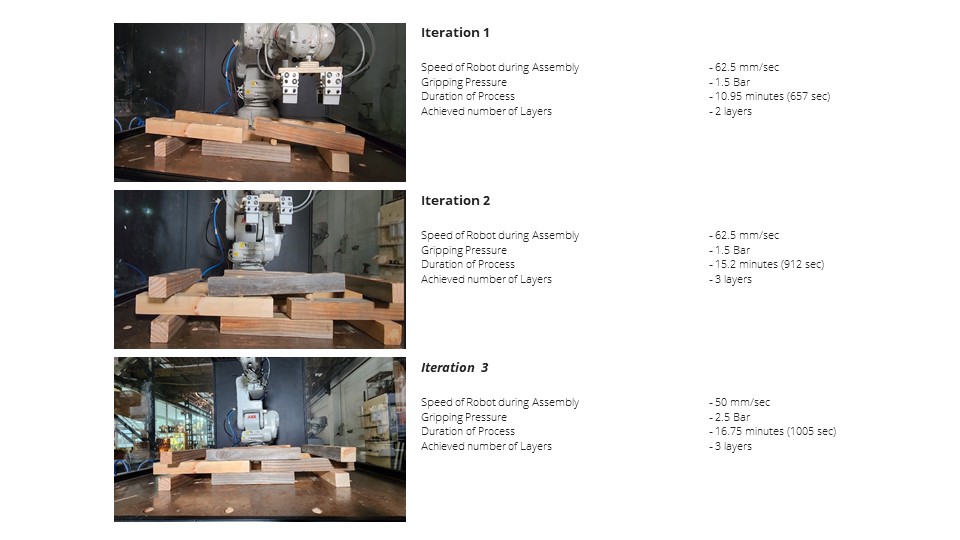
Disassembly:
After achieving positive results in the assembly phase, we attempted and successfully demonstrated the disassembly process. Using the same correction factor data we gathered over multiple assembly sequences, we were able to disassemble the object in a single attempt.