Aim
Our objective is to construct a wall with an emphasis on maximizing the utilization of construction and demolition waste, thereby minimizing landfill contributions. This will be achieved by incorporating a sustainable binder through advanced robotic processes.
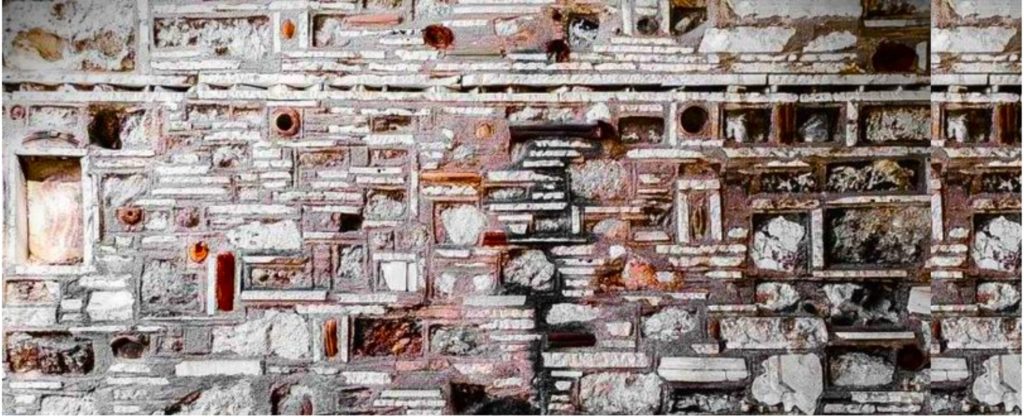
Context
Construction and demolition waste accounts around 30% of waste generated in Europe, making it the heaviest and most voluminous waste system. EU waste framework directive says reuse and recycle construction and demolition waste by 85% by 2025
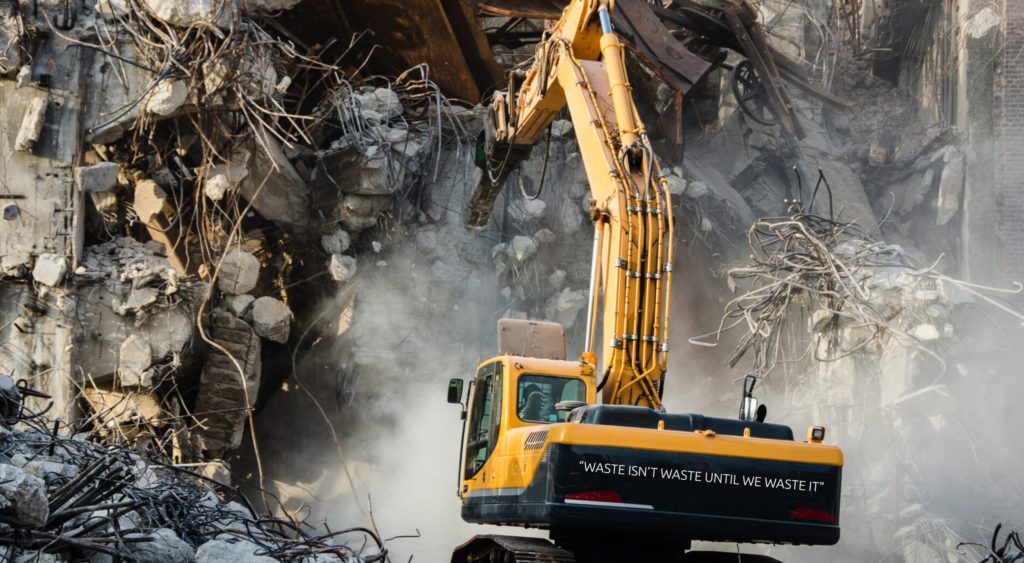
State of the Art
Stacking
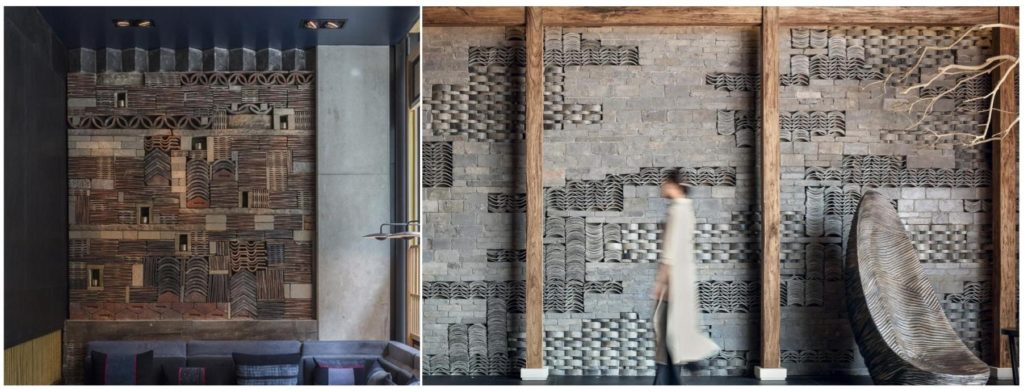
Pick and Place
State of the Art for Pick and Place from ETH Zurich
Binder
State of the Art for Impact Printing from ETH Zurich
Workflow
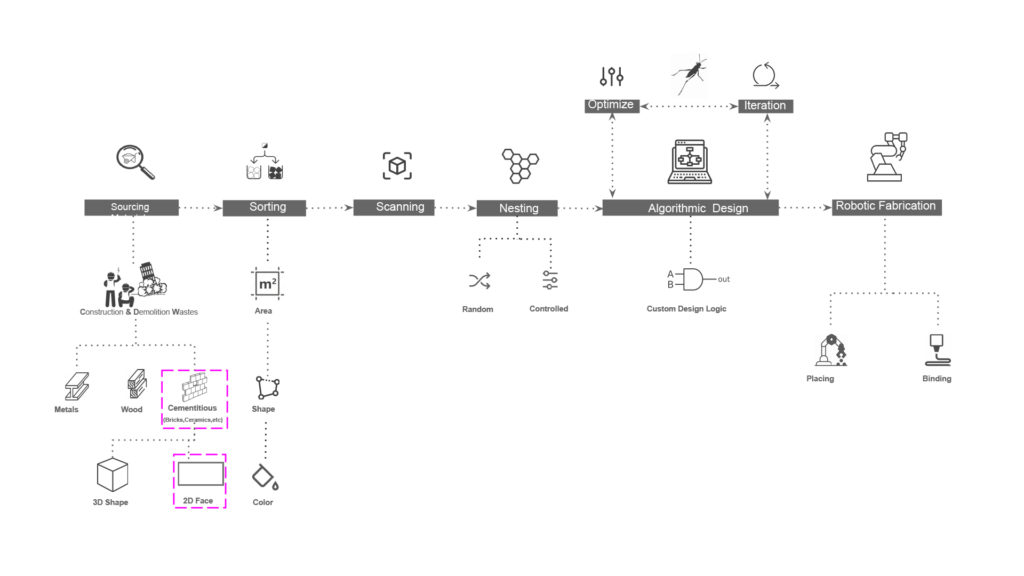
Nesting
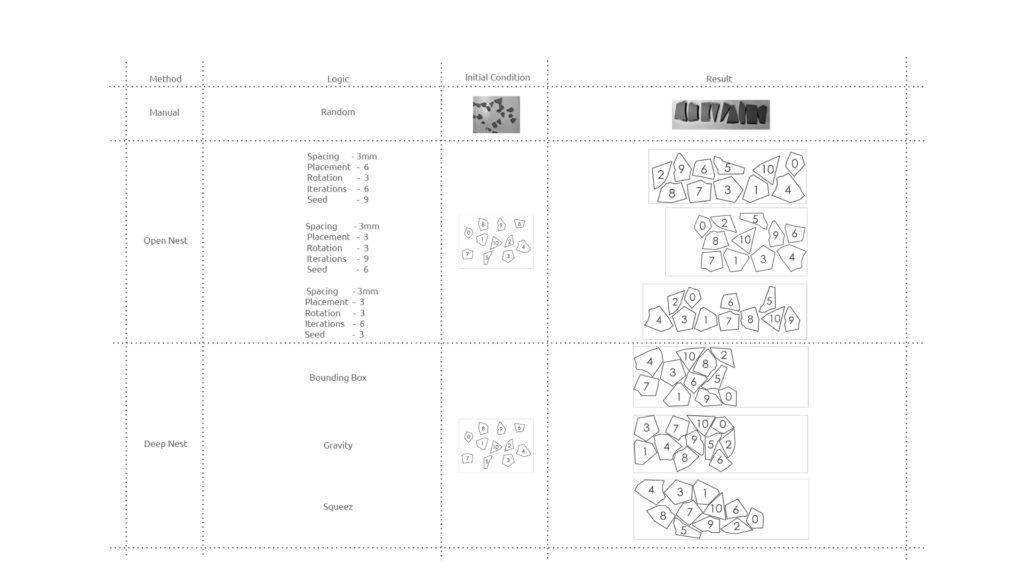
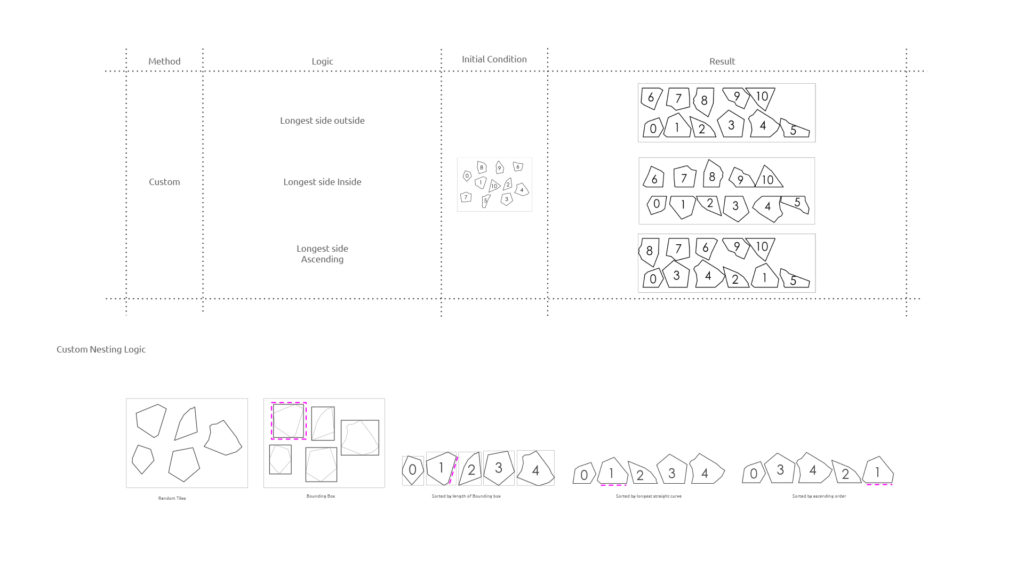
Nesting plays a crucial role in our design process. Initially, we experimented with Open Nest and Deep Nest. However, we encountered limitations in terms of flexibility, hindering us from achieving the desired outcomes. Consequently, we developed our custom nesting code, allowing us to manipulate the orientation of tiles in various directions. This is achieved by utilizing the bounding box, sorted by both the length of the bounding box and the longest straight curve within it, oriented according to our specified preferences.
Experiments with Pick and Place
After developing custom code, we integrated it into the robotic tool path and subsequently linked it to the robotic system. This simulation and video showcase the pick-and-place process utilizing our tailored nesting solution.
Binding Experiments with Impact Printing
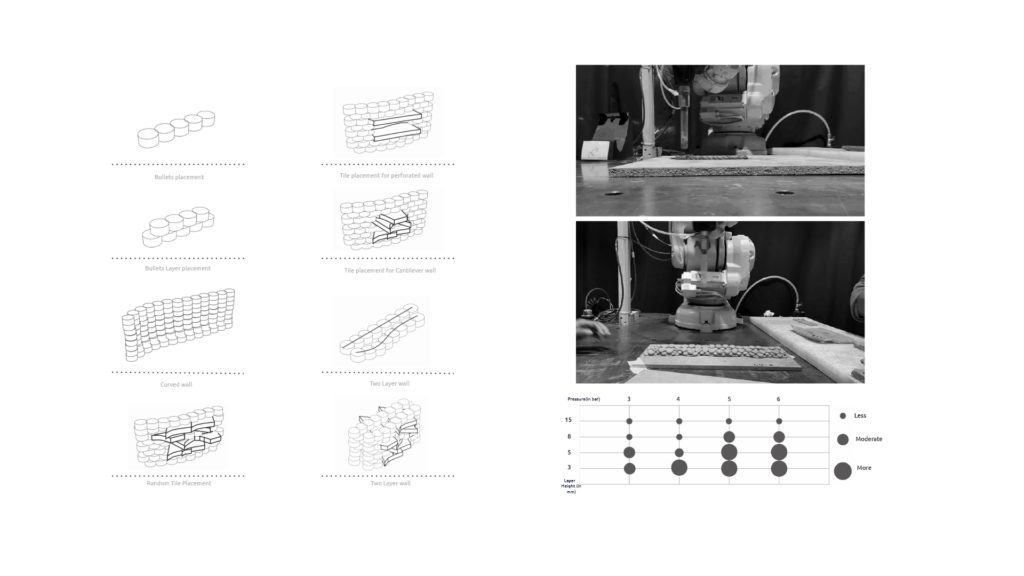
Initially, we manually positioned construction and demolition waste, experimenting with various tile placements on the wall, including random, perforated, and cantilevered iterations. Recognizing stability concerns, we introduced additional curvature to address this issue.
Process and Parameters of Impact Printing
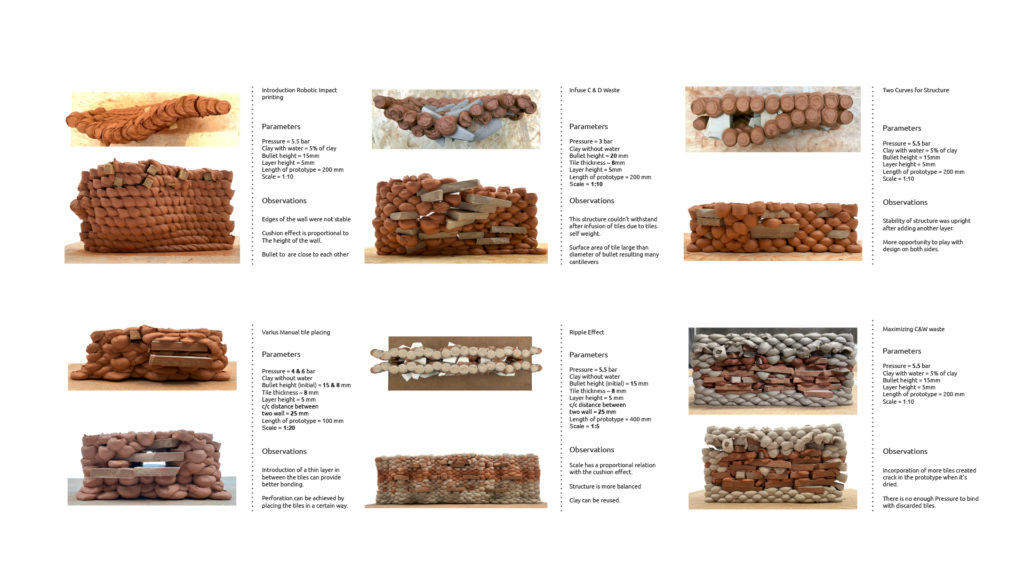
To exercise control over the binding process between clay and construction and demolition waste using impact printing, we modified various parameters such as pressure, clay viscosity, bed height, and bullet shooting height. However, we encountered challenges, including clay shrinkage, and observed the absence of a definitive velocity in our in-house end effector for effective binding with construction and demolition waste.
Binding Prototyping with Geopolymer
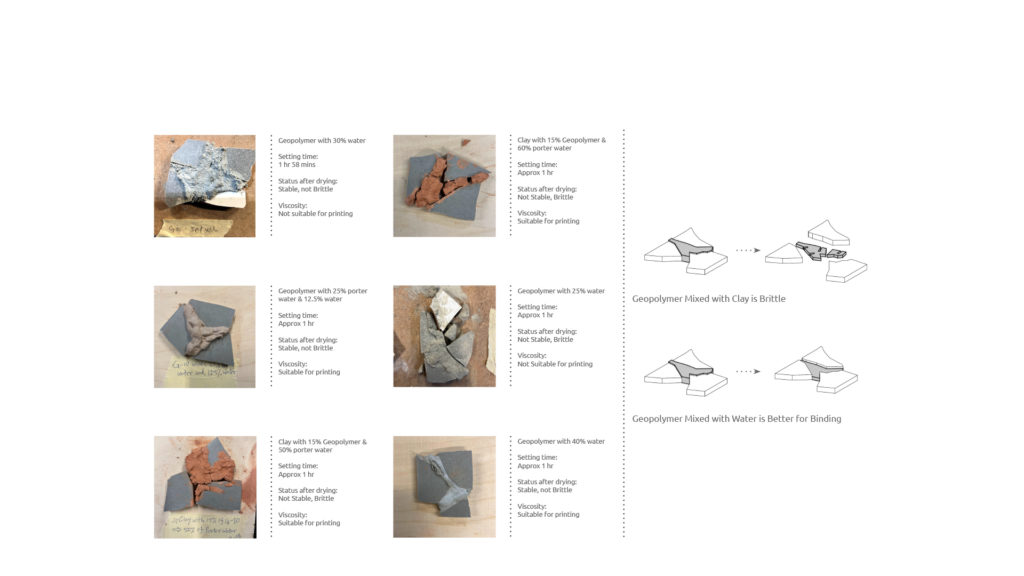
We are conducting tests to analyze various geopolymer binding behaviors by incorporating different proportions of water and potter water. Additionally, we are documenting the setting time in correlation with the binding characteristics.
Custom End Effector
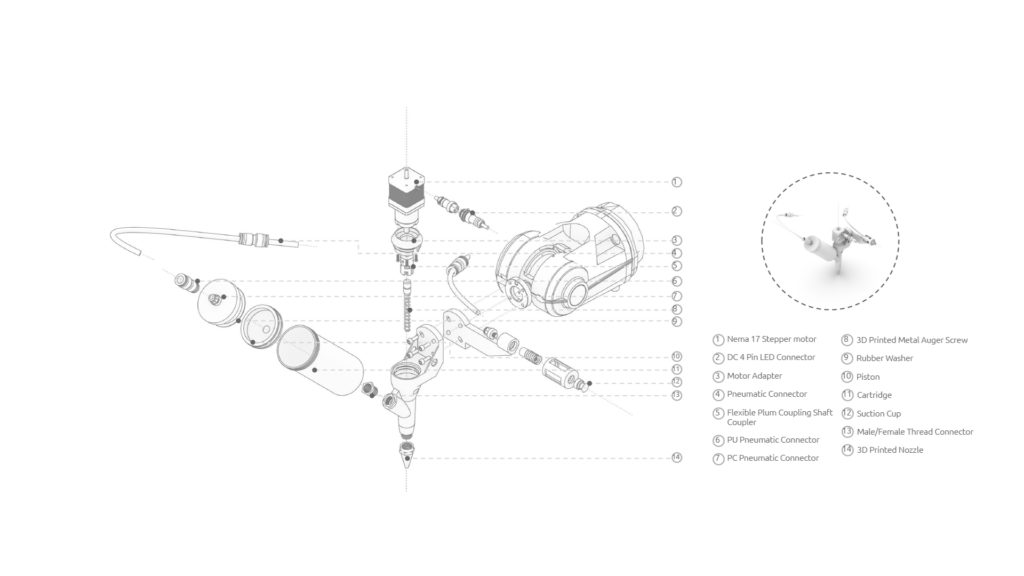
In accordance with our design specifications, we developed a customized end effector for the robot by integrating in-house designs. This involved the fusion of 3D printing with a suction cup mechanism, enabling a seamless transition to a fully automated process for enhanced efficiency.
Robotic Process with Geopolymer
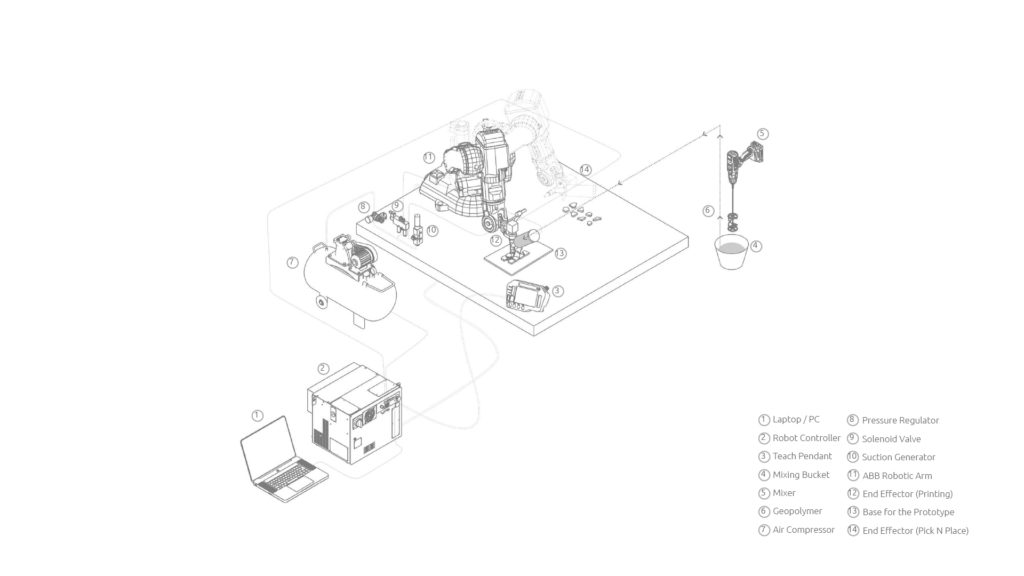
Robotic Pick & Place with Geopolymer 3D Printing simulation and video
Prototypes
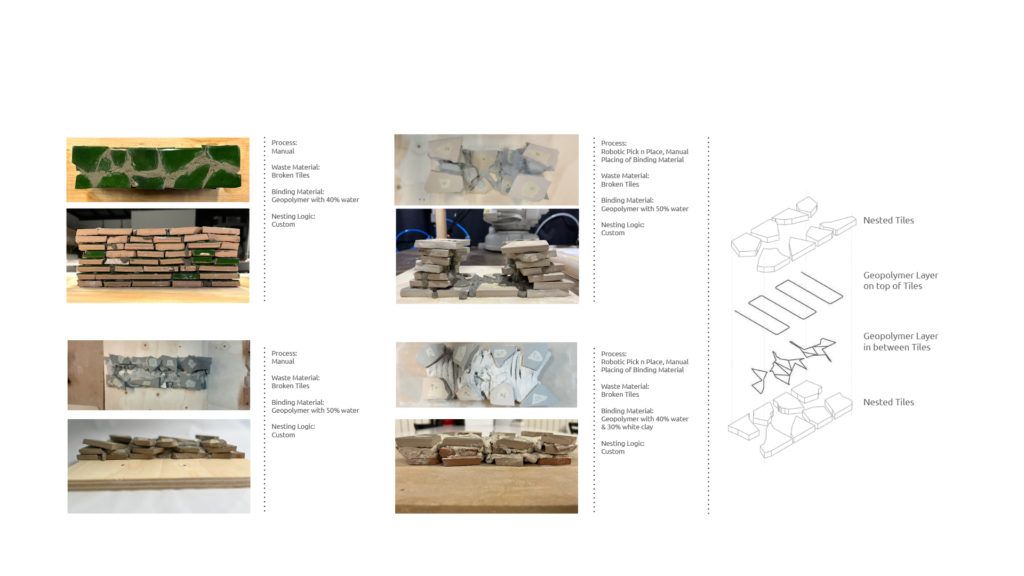
All of our prototypes focus on maximizing the utilization of construction waste by employing geopolymer as a binder. These prototypes were created using both manual and robotic processes. In the manual process, given the absence of a fixed height, we initially applied geopolymer between tiles and subsequently layered from the top to ensure stability.
Video
Future Steps
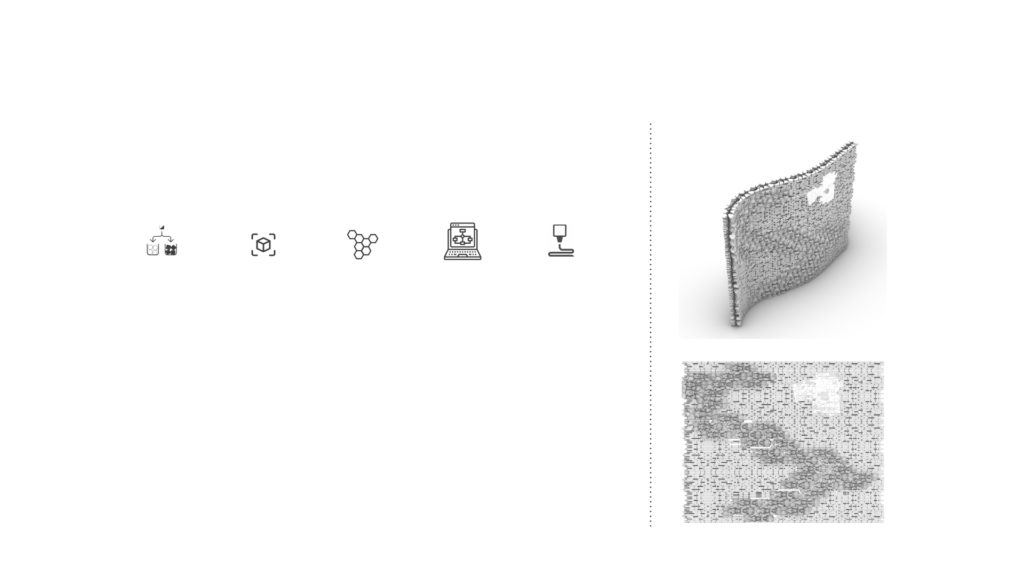
Prioritizing aesthetic excellence, we integrate elements such as curved walls and employ algorithmic logic to create diverse patterns using construction and demolition waste.
Explore complex geometries within construction and demolition waste.
Enhance the efficiency of the process by integrating scanning to achieve a seamless workflow.
We intend to transition from prototyping to scaling our designs in the future.