State Of The Art
Utilization of robotics within the additive manufacturing world is becoming more and more standardized as the needs of people and the environment are changing. The construction industry itself has to produce more efficient structures with very little to no waste, and the capabilities of robots to do this are very apparent. By being able to extrude material at a constant rate with measured curves one can control the amount of material being provided to each project with high accuracy. Adding to this the world’s need for new construction materials that can be made with a very low carbon footprint you get a recipe for what the future of robotics in the construction field will look like. One of these strategies is the utilization of multi-material 3D printing which would highly reduce the time necessary for material processing such as the formwork itself as well as post processing of individual material properties. Multi-Material allows for the mass customization of objects through the direct deposition of specific materials in very specific parts of the model that would allow the materials physical properties to be quantifiable in such space, for instance one can target parts of the model to receive more solar radiation than others and enhance the materials unique properties.
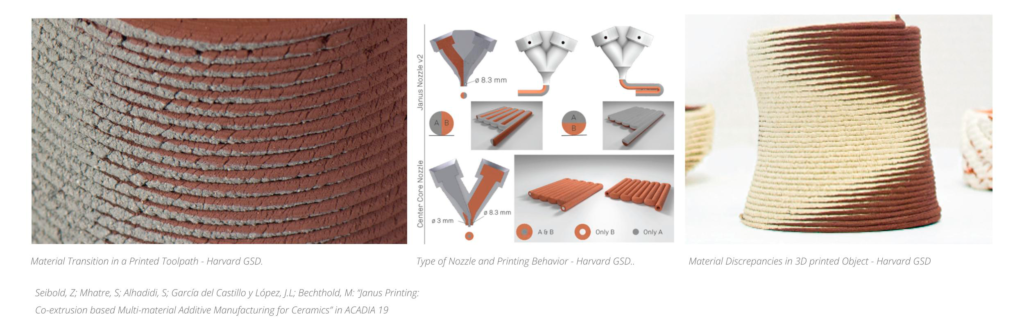
Figure 1 – MultiMaterial Additive Manufacture and Mass Customization
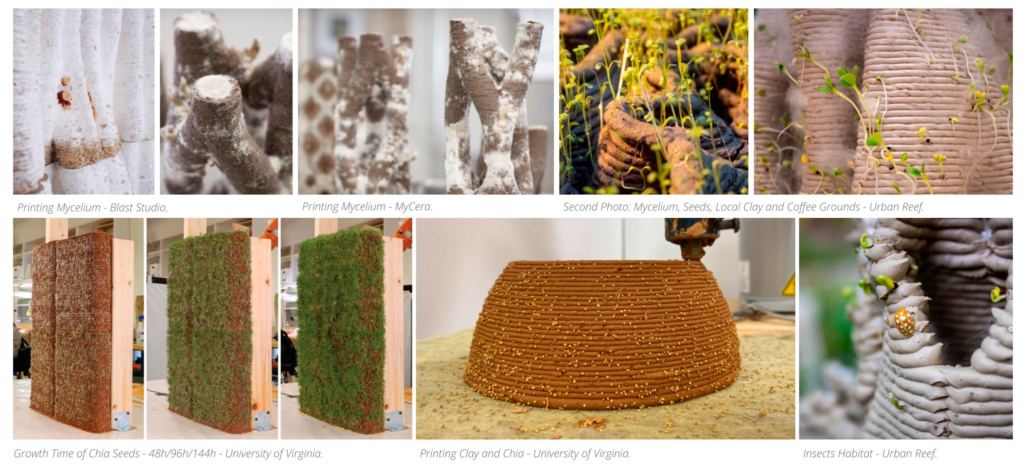
Figure 2 – References for Clay Printing with Chia Seeds and Mycelium
Design Strategy
Within the workshop of multi-material 3d printing w/ABB robots we explored the idea of utilizing a dual extrusion system with both Clay Infused w/Chia seeds and Mycellium in order to create a livable structural system. With a growing population the need for new sustainable agriculture is always growing, and within this realm of technology, complex vertical farming walls are indeed a real possibility. The Chia produced on a facade locally rather than a large field on the outskirts of the city would already start lowering carbon emissions and the mycelium structural properties makes it an ideal construction material. This model could be scaled to create more self-sustaining urban ecosystems, intertwining food production, sustainable construction, and modern urban living. As we underwent research on how both systems can work synchronously we discovered how mycelium ideal growing conditions involve complex geometry such as folds, buckles (peaks and valleys) for it to thrive as well as proper shading pockets, and the chias need for solar radiation for it to grow.
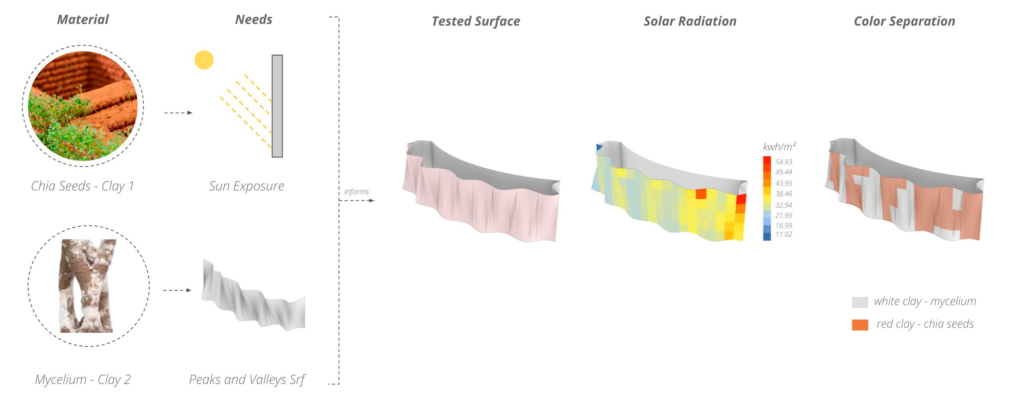
Figure 3 – Design Strategy Diagram
First Trial
Through the first trial printing using two different clay colors as a proxy material and the exploring complex geometry within Rhino a simultaneous exploration of how feasible overhangs are on the actual printer were made and how transition of materials can efficiently happen. In context a material like clay, overhangs above 25° can create issues as the clay does not dry immediately and can collapse on itself. The trial itself also helped us understand how the change of planes can alter the shift of colors from solid red, solid white and a gradient transition path from color to color and how the speed of the robot can affect the integrity of the print. As the diagram explains through this trial we utilized attractor curves, in order to control a rotation of color towards these two curves, the more transitions or change of planes you have within the robot, the more jerking motion you have which can create an unsatisfactory result while printing.
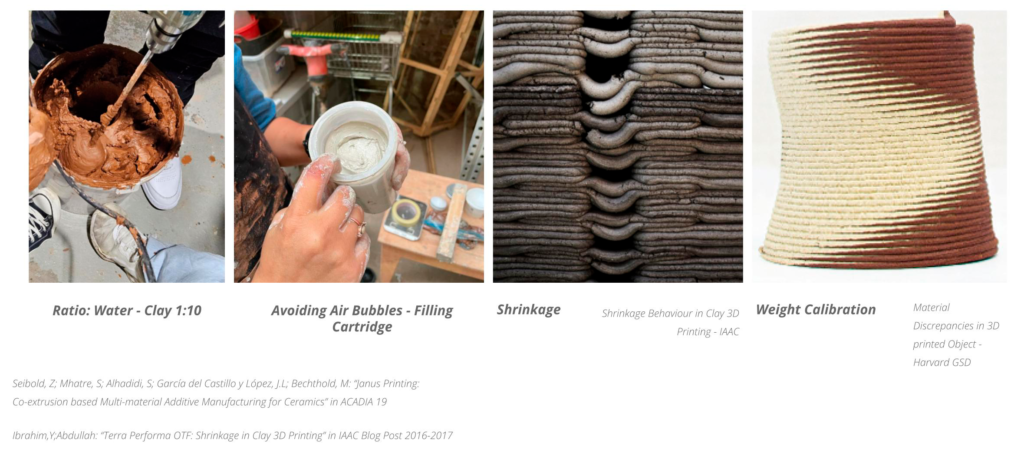
Figure 4 – Parameters to consider while 3D printing with Clay
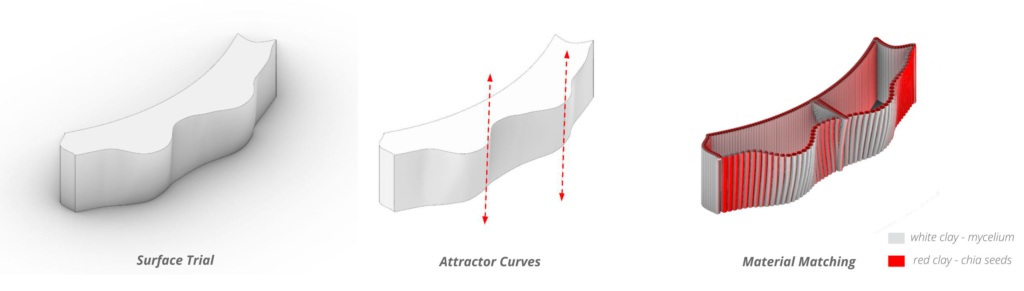
Figure 5 – Attractor Points to inform Rotation Angles
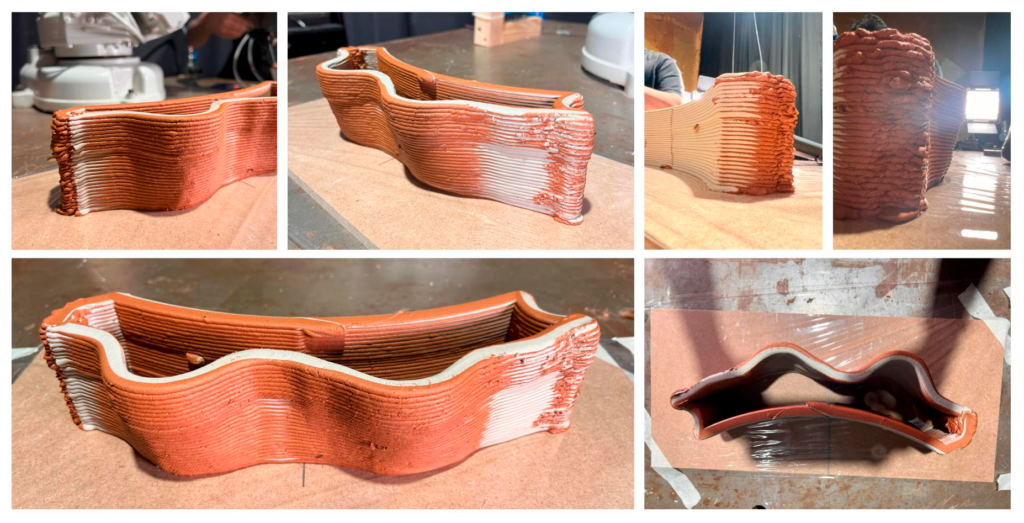
Figure 6 – First Prototype Printed
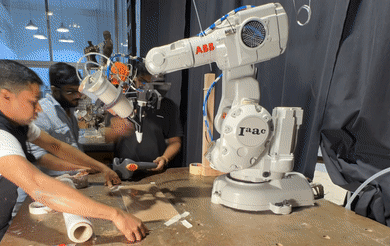
Figure 7 – Printing First Trial
Computational and Fabrication Strategy
By the learning curve we experienced in the first prototype we started systematically creating a series of fold paths as a growing strategy for the mycellium. These paths or “veins” as we call them would be able to reinforce the wall itself while also providing the necessary geometrical conditions for the mycellium to thrive in. After geometrical iterations developed with RhinoSubD we took the design and analyzed it using the Grasshopper Plugin Ladybug for a more thorough understanding if the folds did create cooler conditions for the mycellium which in fact did follow the geometries “undercuts” which can only be achieved only through the robotic process. As we printed brick by brick we increased the rate of overhang angle as it becomes evident on bricks 5 & 6 where these open cups for both mycellium growth and plant growth became a prominent feature within the design. The speed of the printing per brick remained relatively the same, running around 22% of the robots total speed; which was also a great learning curve especially with material like clay. Clay deposition especially when trying to run the robot faster, would leave thinner lines and thus causing the potential from having a weaker print due to the line thickness, all the the process was a great example of learning by doing and trusting the robotic process. This is very apparent during change of angles (colors/materials) as the transitional period from red to white and vice versa you get a developing gradient, otherwise at angle 0° you get a pure white color and at 180° you get a solid red color.
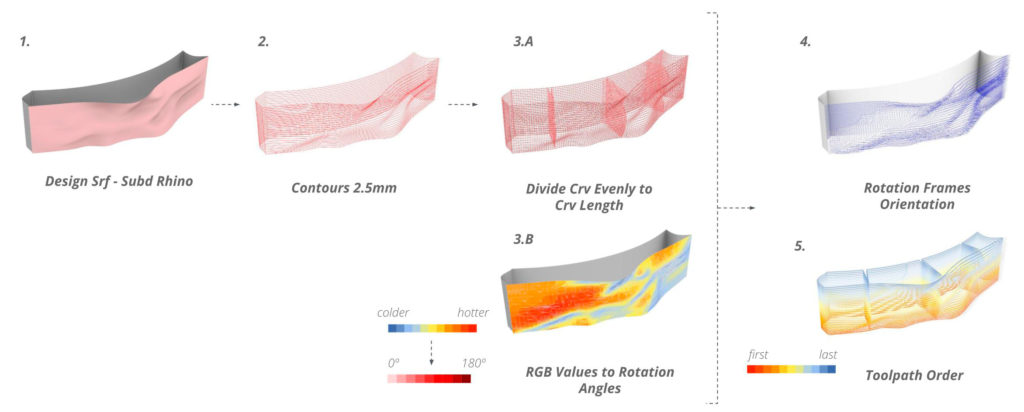
Figure 8 – Pseudo Code
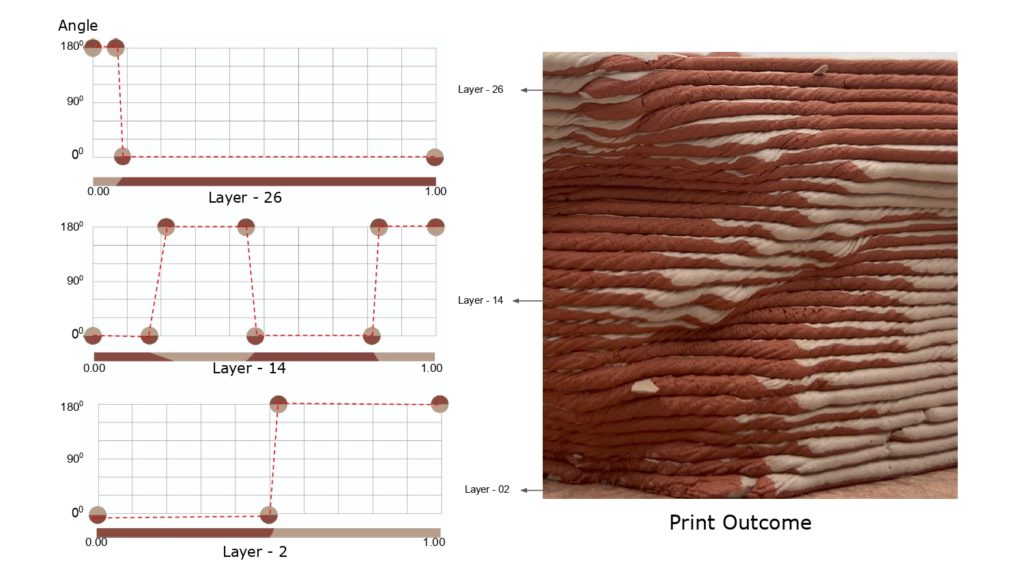
Figure 9 – Relationship between Rotation Angles and Clay Extrusion
Fabrication of the Brick
Constant variables that were necessary to take into account while fabricating each individual piece included the robots speed of printing, the slower the robot runs through the process the thicker the lineweight becomes and thus more structural (think shear wall), as the robot deposits more material per square mm than running the robot much quicker and leaving thinner lines and less material. The clay itself had to come from the same batch of mixing in order to get similar consistency of prints and production. A constant eye had to be on the robot continuously as sudden air pocket bursts could result in a less ideal print. With this in mind we found an average robot sprint of 22% to be ideal for the form we were after.
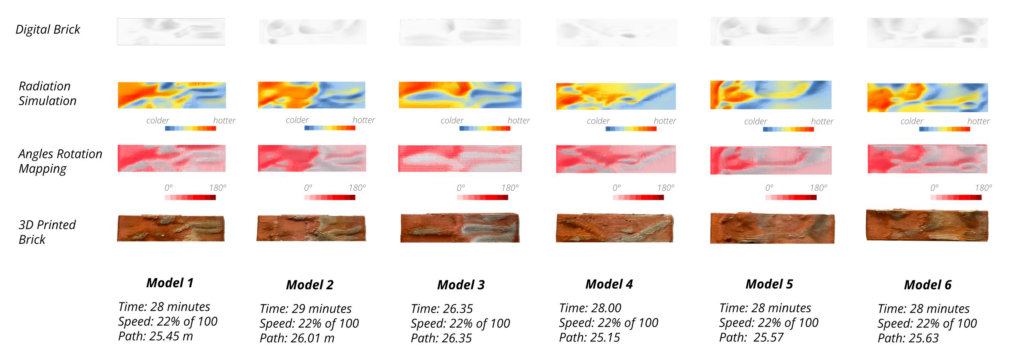
Figure 10 – Matrix with Computational and Fabrication Data of all bricks
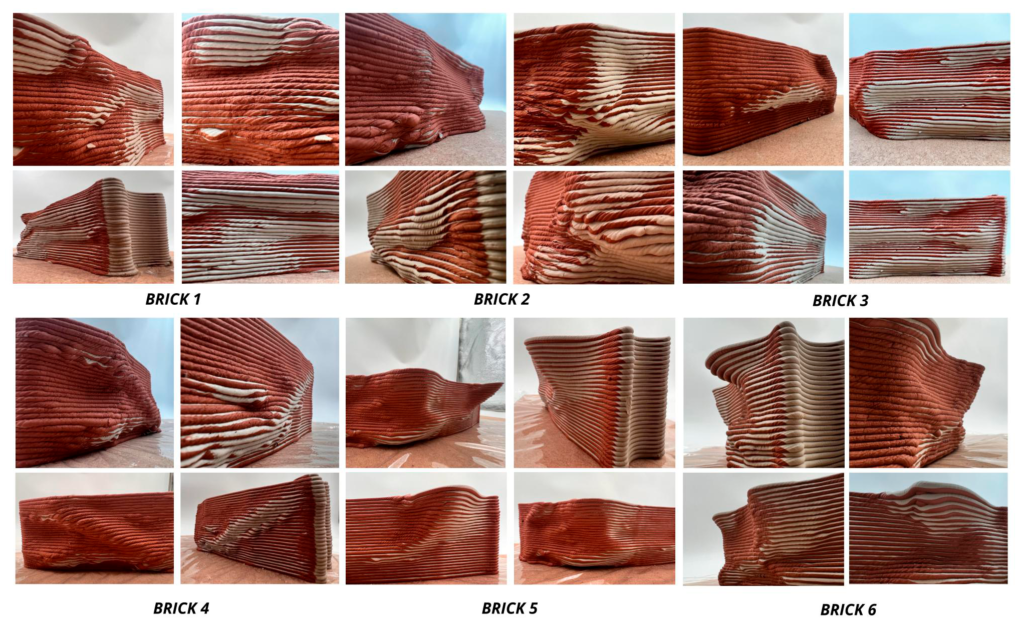
Figure 11 – Printed Bricks and Cantilevers Experimentation
From Digital to Physical
The most interesting features can be measured here, post printing of all bricks and with the clay properties, during assemblage we noticed there was a slight tilt of the bricks causing the structure to be somewhat unstable. Although not a major issue in future explorations, better handling of the material can possibly take place or do more research as to where this tilt starts occurring, was it the drying process, the printing process, or just normal shrinkage of clay that caused non-uniform drying. Even the end-effector can be redesigned to have a continuous extrusion rather than a 2 cartridge system or even that can limit longer prints (in some cases one would have to refill the cartridges and replace before a single print would be finished, although this is based on complexity and length of curves of individual components. Change of planes and how much length there is in between change of material will also be detrimental to the resolution of the printed piece, with most jerking movement a prints resolution can be somewhat sloppy due to the limitations of how fast a robot can change rotation axis while extruding the clay, simple steps such as reducing the number of points in the geometry can fix some of these issues as well as ignoring kinks (noise) in objects that involve complex meshes. Even more modifications of the end-effector can happen and a possibility of increasing the resolution of the ladybug analysis can increase by adding even more materials; in a future experiment printing with 4 materials is possible, the analysis can utilize the yellows and oranges as transitional materials rather than gradient shifts. With more prototyping and incorporation of machine learning into the printing process an ideal balance between speed, accuracy and clay drying process could be achieved.
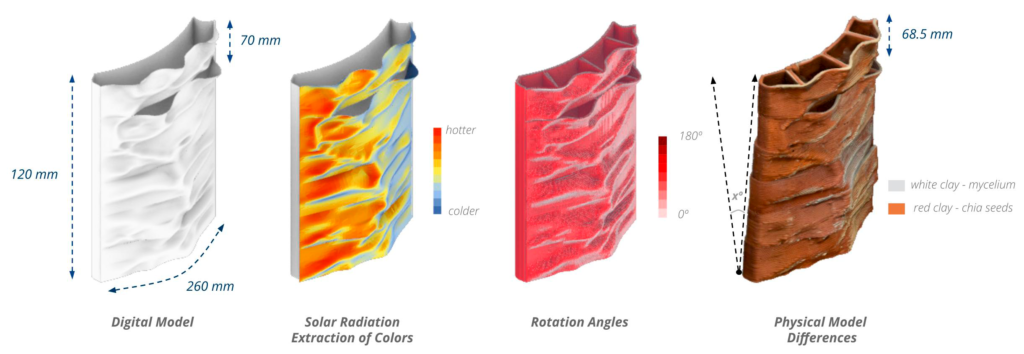
Figure 12 – Comparison between digital model and final prototypes
Architectural Application
As stated before some of the most prominent explorations within the idea of being able to 3D Print in both mycelium and Chia infused Clay, could revolutionize urban farming systems. Within the scale of a possible facade development, an idea using myceliums’ own natural growth algorithms we can create a possible shortest path script to design where the “veins” will define the cantilever areas, mass customization of the facade becomes relatively simple as well as it allow for a panelization system that will make installation an easier process as well. With the feasibility of 3D printing, a project will significantly minimize waste generated during the construction process, and both materials’ low carbon emissions would highly benefit an industry that is plagued with carbon emitting behemoths like concrete and carbon based products. Research is already underway on mycelial amazing structural properties which is being investigated as a viable alternative material, add to this the technology of Robotic 3d printing and you gain a methodology could notably contribute towards the fabrication of more sustainable, self-reliant, and environmentally amicable urban landscapes, exemplifying the metamorphic potential of contemporary technology when orchestrated creatively and responsibly.
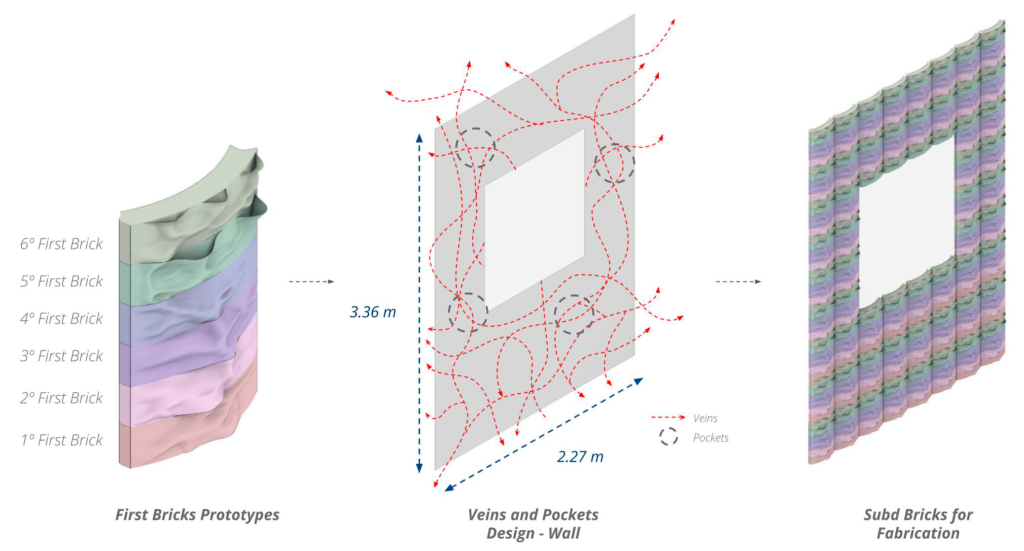
Figure 13 – Customization Strategy for walls and subdivision into bricks
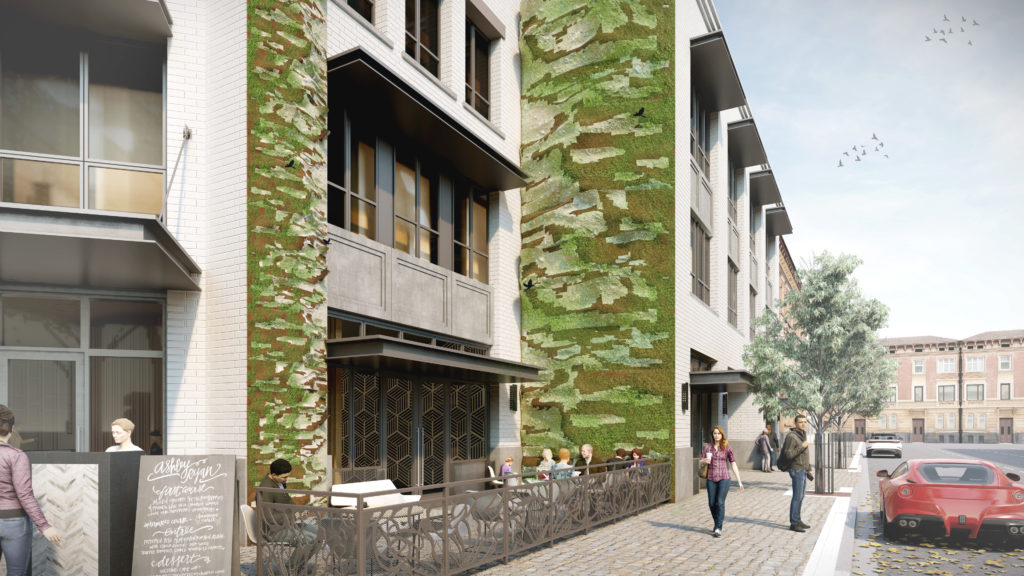
Figure 14 – Outer Facade Application of MultiMaterial Brick
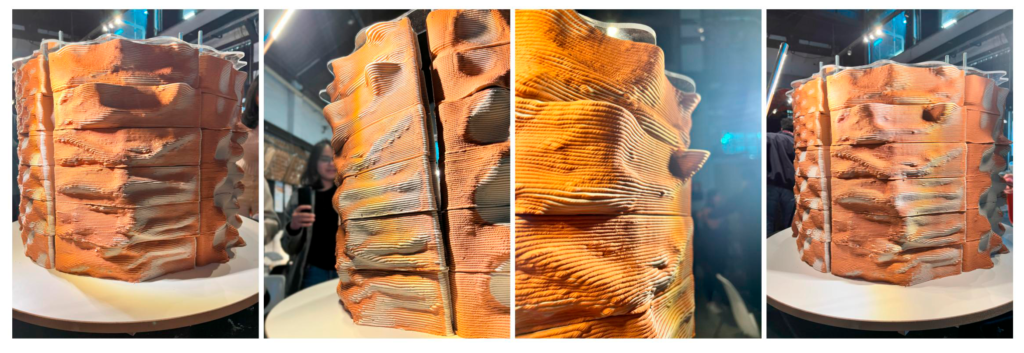