Introduction
As part of the workshop led by Javier Fuentes and Moritz Dörstelmann the Chair of Digital Design and Fabrication (DDF) at the Karlsruhe Institute for Technology (KIT), our team explored the potential of willow as an innovative material in architecture. This project merges sustainability, advanced design, and robotic technology to develop breathable and adaptive facade systems. The goal was to leverage willow’s flexibility, strength, and sustainability to redefine material efficiency and create functional architectural systems.
This project was driven by a multidisciplinary approach, combining historical insights, material research, and computational tools. It sought to develop facade systems that are not only aesthetically appealing but also contribute to environmental sustainability through natural ventilation and dynamic adaptability.
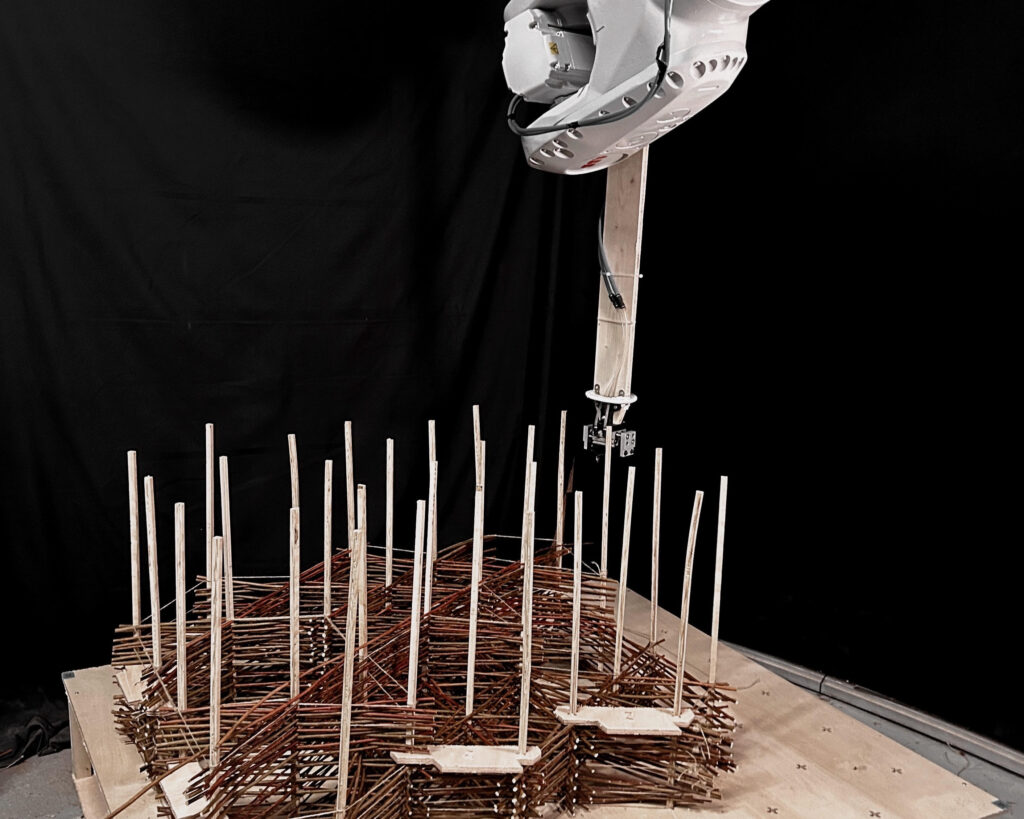
Concept
Our project revolved around the concept of core-less filament winding, a fabrication technique that eliminates the need for formwork and allows us to create unique, adaptable components. This approach encouraged us to think beyond traditional construction constraints and embrace designs that maximize material efficiency and sustainability.
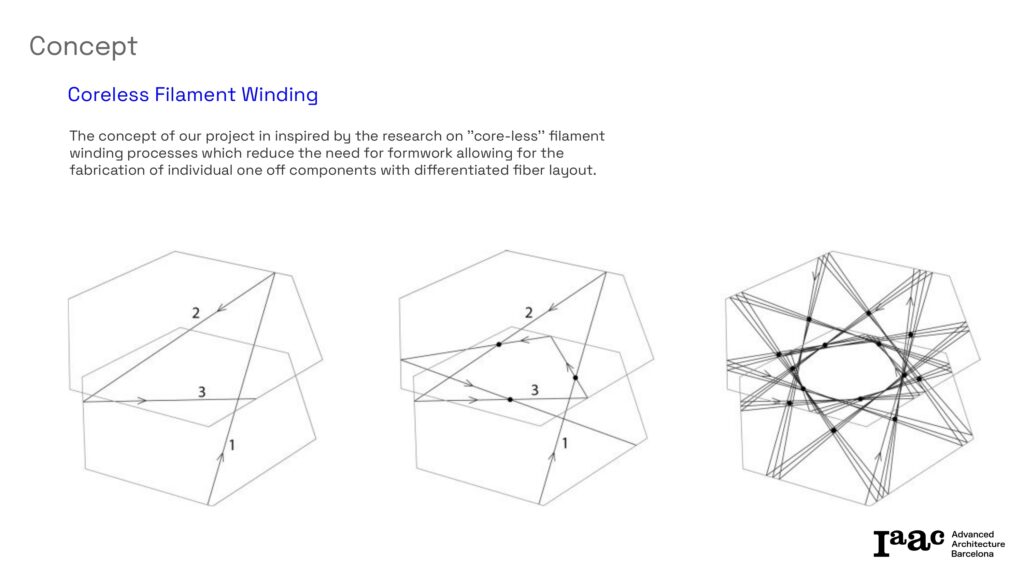
Design Process & Development
The journey from concept to fabrication involved a combination of computational modeling, material testing, and robotic simulation. We started by analyzing the geometry of the module and experimenting with different weaving patterns.
Here’s how we approached it:
a) Cataloging Weaving Patterns: We explored a range of weaving options, working through 18-layer designs that used up to 31 wooden sticks. These patterns were iteratively refined to optimize both stability and appearance.
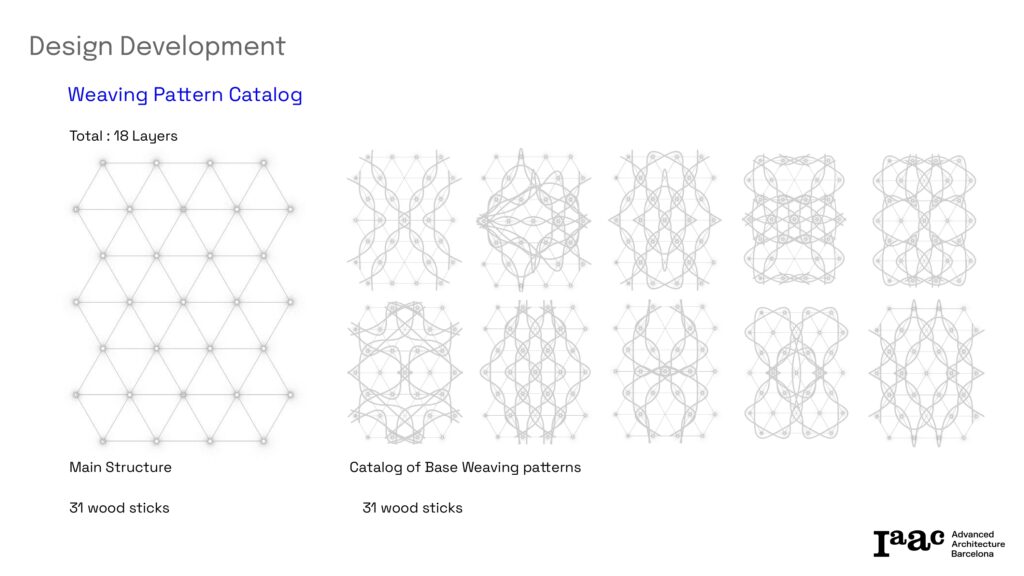
b) Choosing the best design approach: We explored with a few combinations of these patterns in order to choose the design that would fit best our concept, approach and stability.
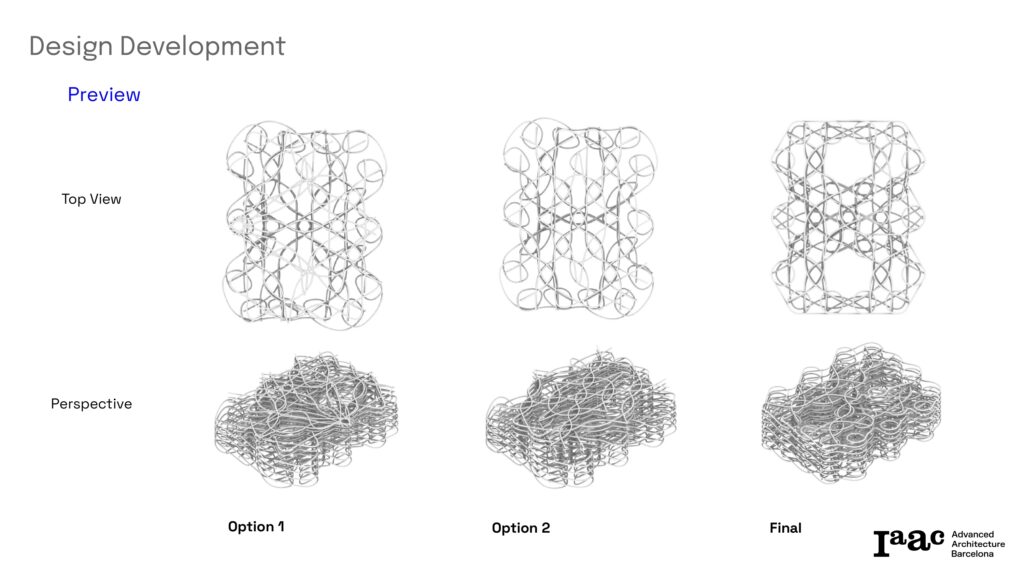
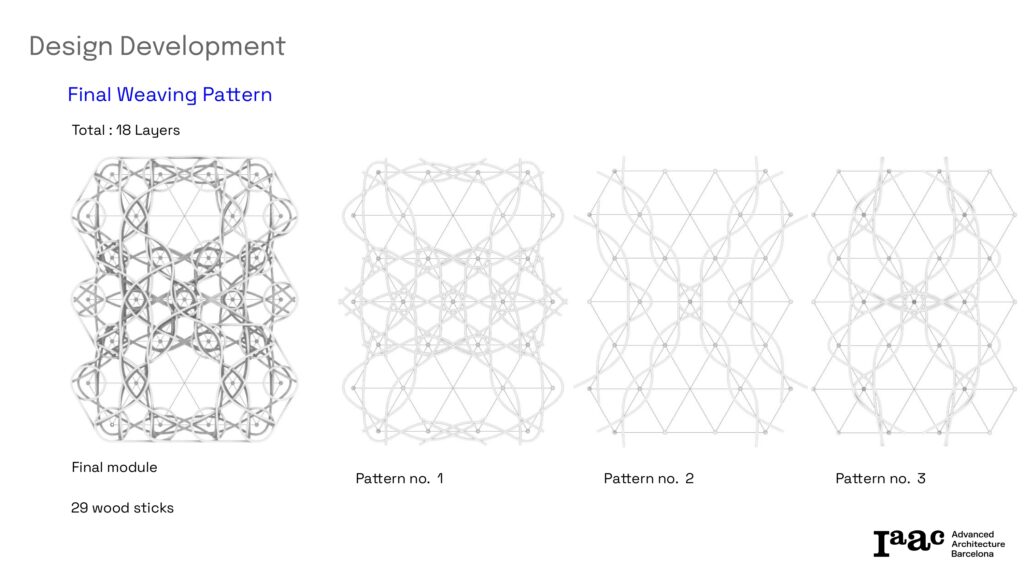
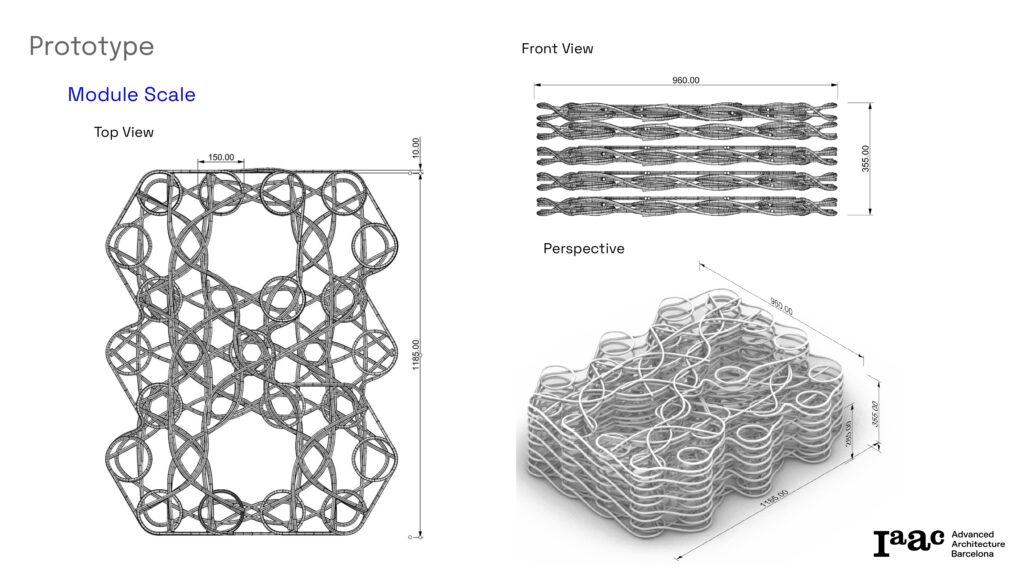
Fabrication Strategy
Fabricating the module was an exciting challenge that brought together material treatments, computational tools, and robotic precision.
We faced the task of adapting our designs for robotic fabrication. For example, we replaced curved toolpaths with segmented lines to accommodate the robot’s limitations and prevent errors during weaving, which ended up changing the geometry we had previously designed. Additionally, we carefully designed offset openings to ensure that the robot’s end effector wouldn’t collide with the wooden sticks during assembly. These adjustments allowed us to create a seamless process from digital design to physical construction.
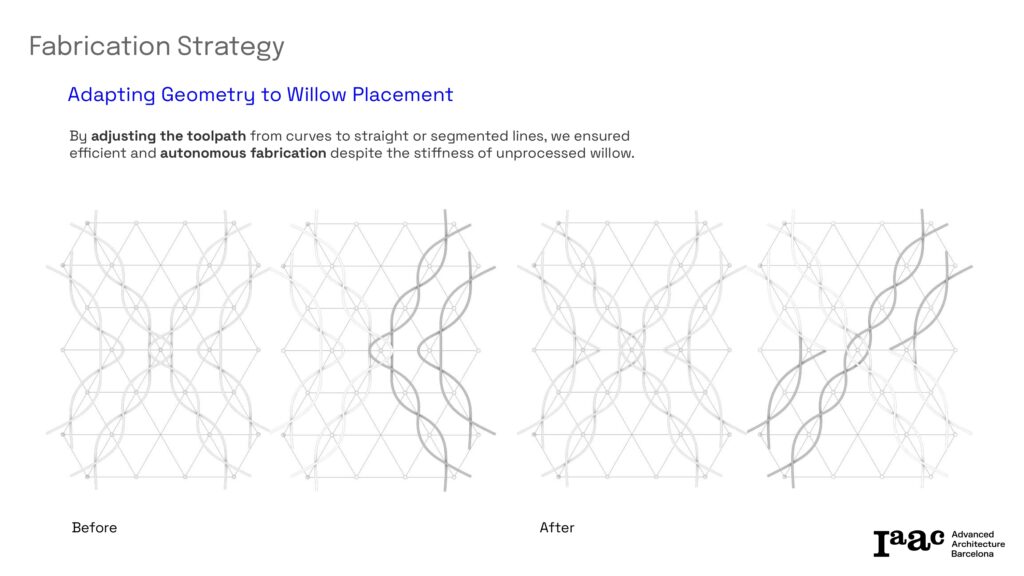
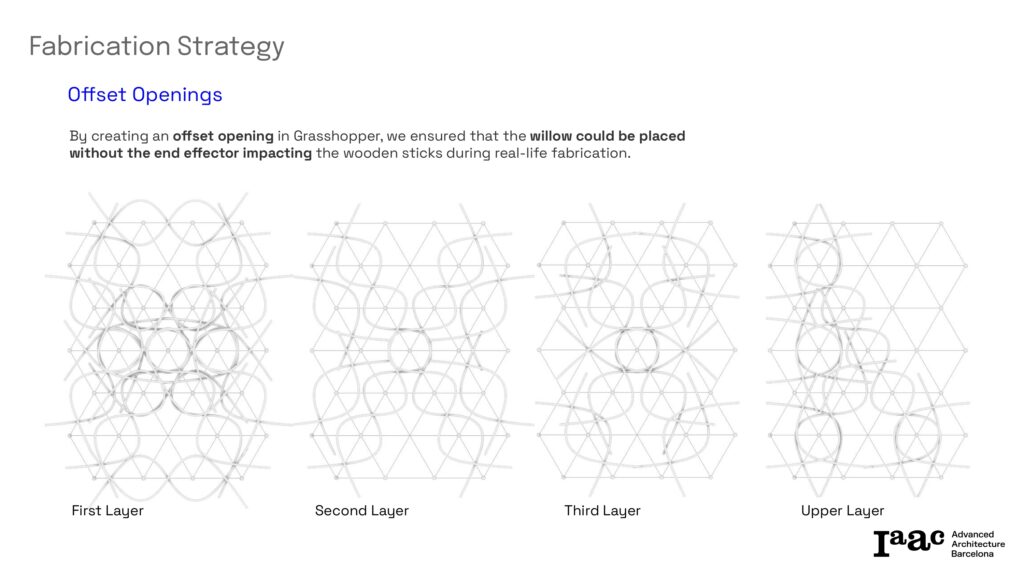
The final module featured a woven structure consisting of 18 layers and 29 wooden sticks. This design struck a balance between structural integrity and aesthetic elegance, showcasing willow’s natural flow and texture. The modular nature of the system allows it to scale up for larger architectural applications, making it ideal for facade systems.
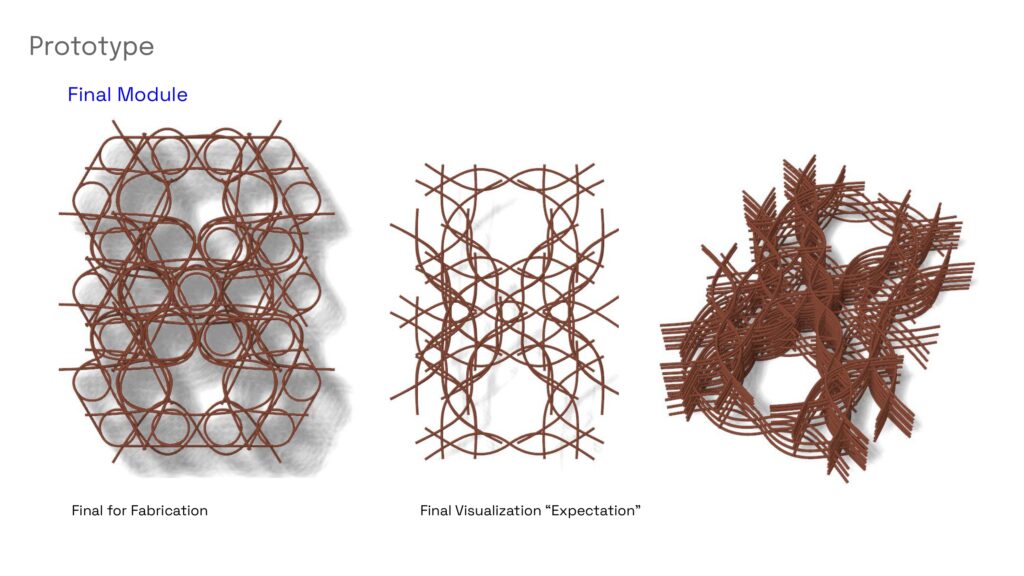
Fabrication Process
The fabrication process was a pivotal part of our project, showcasing the seamless integration of material preparation, robotic precision, and computational design. Our approach was centered on achieving an autonomous workflow where the robotic arm could independently manipulate and weave the willow into the designated patterns.
We began by steaming the willow to enhance its pliability. This treatment softened the fibers, reducing the risk of cracking during bending and ensuring a smoother weaving process. With the material ready, the robotic arm was programmed to execute the weaving autonomously. Using computational toolpaths generated in Grasshopper, the robot was capable of picking up individual willow pieces and placing them with precision in their designated positions.
The autonomous aspect of the process was key to the project’s success. It allowed the robot to handle repetitive tasks with high accuracy, such as layering and aligning the willow strands according to the pre-determined weaving pattern. By automating these steps, we minimized human intervention and ensured consistency across the module’s layers.
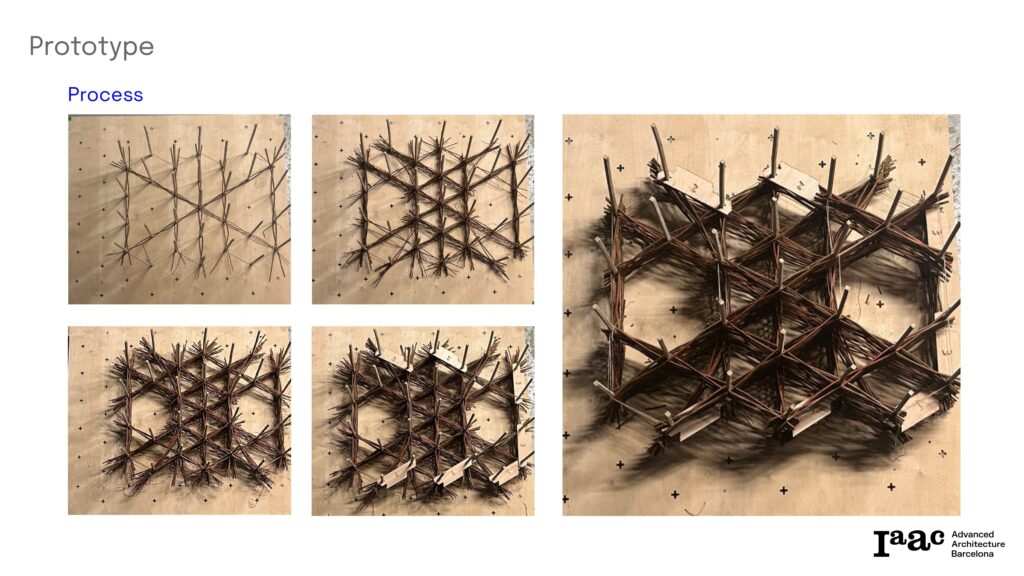
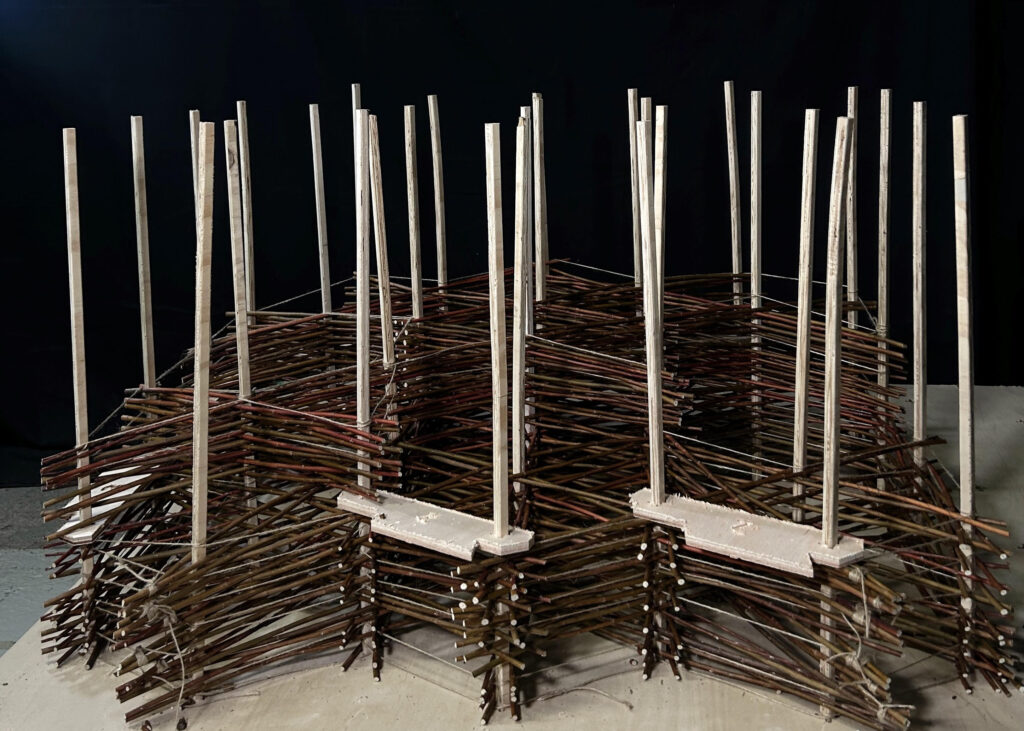
Architectural Applications
While our module was initially designed as a proof of concept, we also envisioned its future architectural applications. The panels we created could function as breathable facades, contributing to natural ventilation and energy efficiency in buildings. Here are some potential applications:
- Green Buildings: Our facade system could reduce reliance on air conditioning by enabling natural airflow, promoting sustainable design.
- Smart Cities: Integrated with IoT sensors, these panels could dynamically adjust to temperature and humidity changes, optimizing indoor comfort.
- Architectural Identity: The woven patterns add a unique aesthetic, blending natural materials with contemporary design to create visually striking buildings.
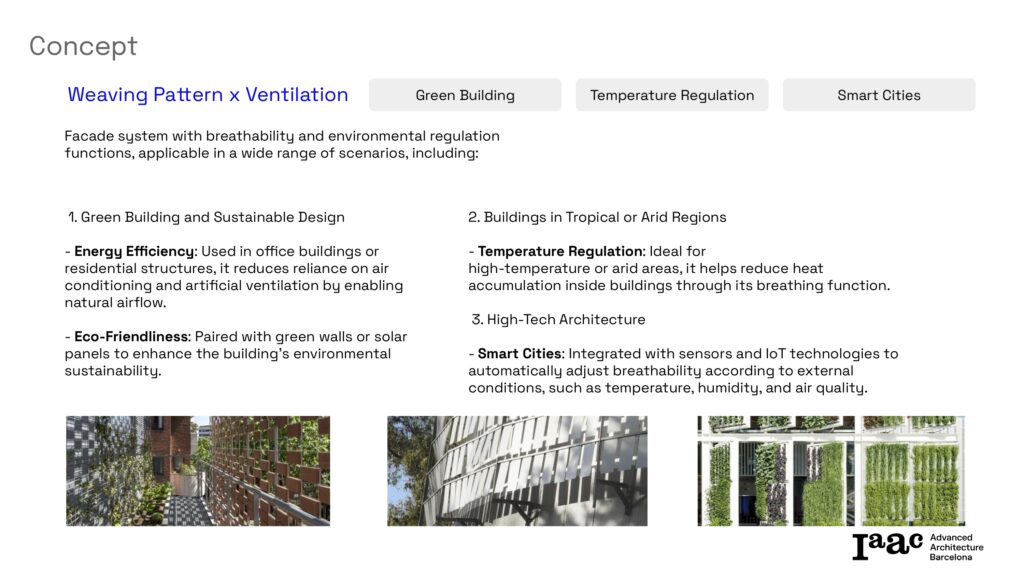
Breathable Facade System
One of the most exciting aspects of this project was envisioning how our modular willow panels could be integrated into real-world architectural systems. By combining natural materials with advanced robotic fabrication, we explored innovative applications for facades that prioritize sustainability, functionality, and aesthetics.
Our primary architectural application focused on creating breathing curtain walls—dynamic facade systems that allow natural ventilation while contributing to the building’s energy efficiency. These facades are particularly effective in regulating temperature, reducing reliance on artificial cooling systems, and promoting airflow.
Each module, with its woven willow pattern, acts as a filter that allows air and light to pass through. When aggregated, the panels form a cohesive system that adapts to environmental needs, offering both functional and aesthetic benefits.
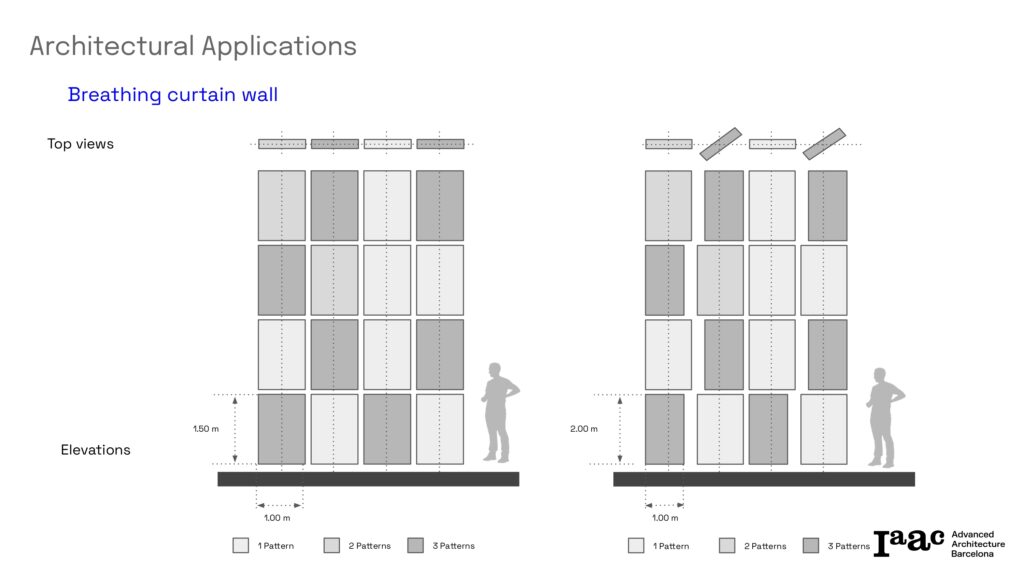
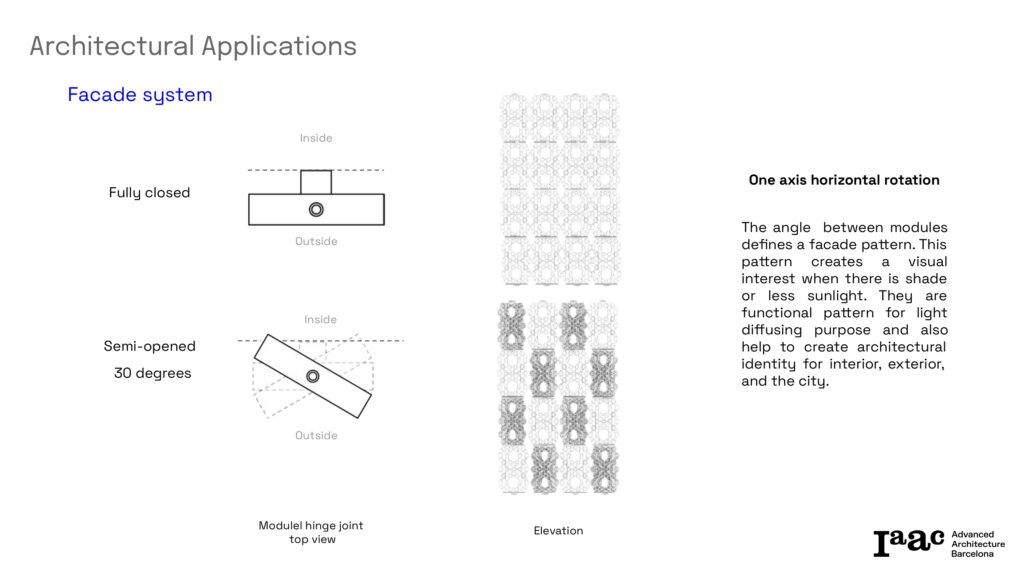
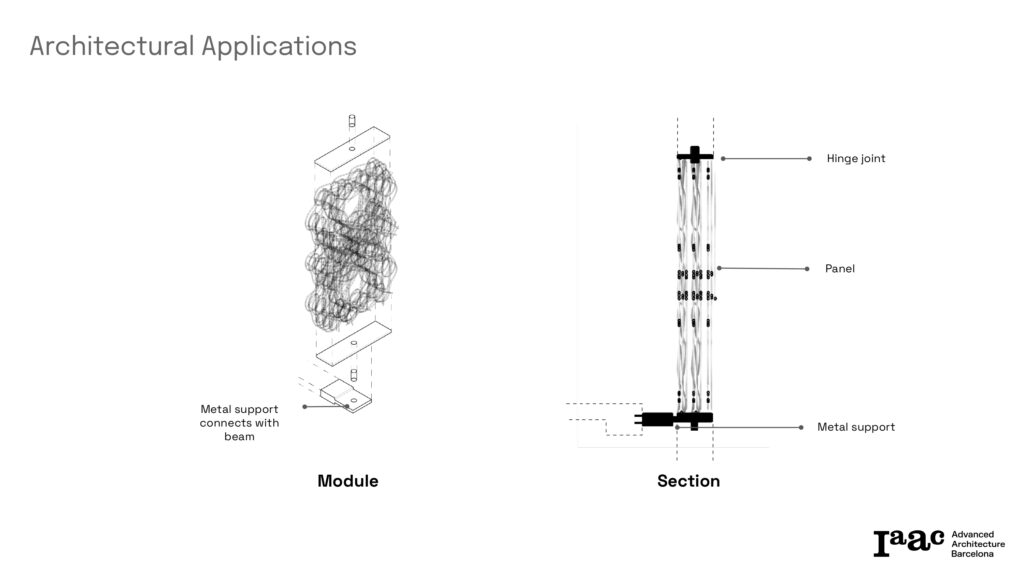
Our facade concept goes beyond static applications. By integrating the modules with kinetic systems, we envisioned facades that respond dynamically to sunlight and other environmental conditions. For example:
- Adjustable Modules: The panels could rotate horizontally or vertically to control the amount of light and ventilation entering the building. The renders demonstrate how the panels can transition between fully closed, semi-open, and fully open states to create varying levels of shading and airflow.
- Smart Integration: When combined with IoT technologies, the facade could adjust automatically based on external conditions such as temperature, humidity, and air quality, making it an ideal solution for smart cities and high-tech architecture.
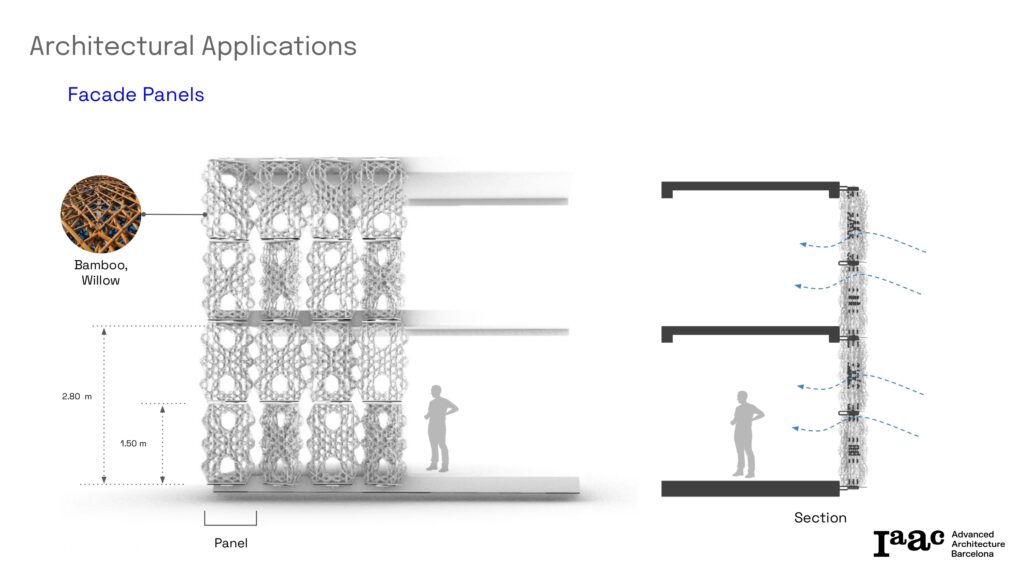
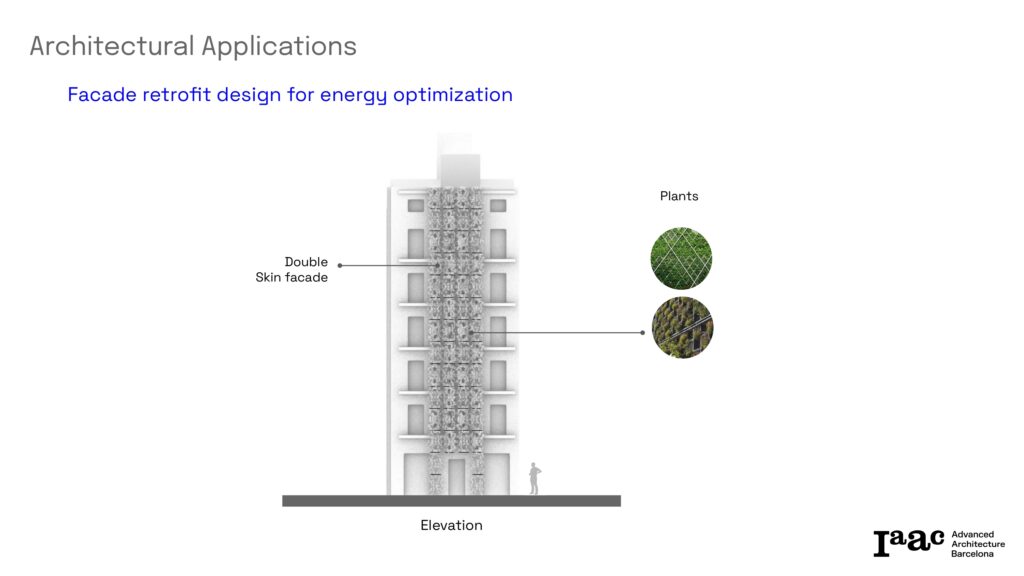
Conclusion
This project showcases the potential of natural materials like willow when combined with robotic fabrication. Through the creation of a woven module, we explored how traditional weaving techniques could be adapted using automation to achieve precision and scalability. While our work focused on developing the module, the digital proposal for a facade system demonstrates its potential for real-world architectural applications. This project highlights the possibilities of integrating natural materials into sustainable, energy-efficient designs and paves the way for further innovation in eco-friendly construction.