In the pursuit of a sustainable built environment, Timber Syntax demonstrates how reclaimed, non-homogeneous timber can be transformed into high-quality facade systems through a computational and robotic pipeline. Developed at the Institute for Advanced Architecture of Catalonia (IAAC), this project bridges waste reuse, advanced fabrication, and circular design to propose a new paradigm for timber architecture.
Context: Waste as a Resource
Manufacturing industries generate significant timber waste — offcuts, irregular sticks, and rejected elements that are usually downcycled or discarded. At Tallfusta in Barcelona, a considerable portion of raw timber is lost in manufacturing. Similar conditions were documented at IAAC Valldaura Labs, where rejected or off-sized pieces accumulate, representing a missed opportunity for reuse.
By analyzing these waste streams, Timber Syntax identified a chance to transform this reclaimed non-homogeneous timber into a valuable architectural resource.
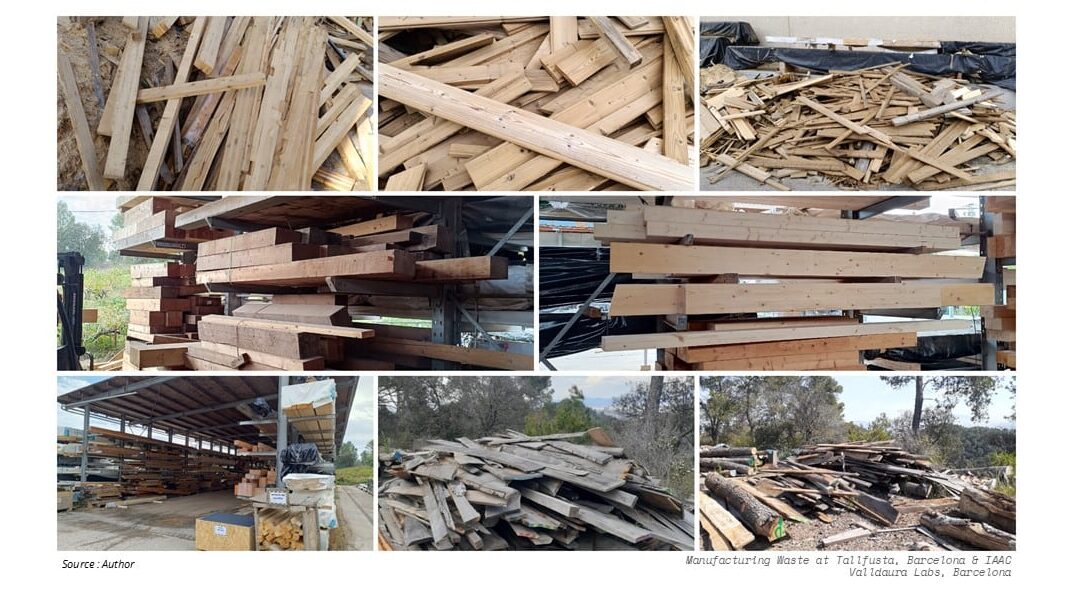
Research Aim and Approach
The project’s aim was to develop a computational and robotic strategy for reusing reclaimed timber in non-structural facade systems, minimizing excessive reprocessing. The approach included:
- Digital scanning and material database creation
- Digital twin modeling for stick representation
- Algorithmic distribution to maximize coverage
- Joinery definition for reversible, future-proof assembly
- Robotic assistance for placement and fabrication
This methodology was designed to support high reuse rates and to make use of otherwise discarded resources.
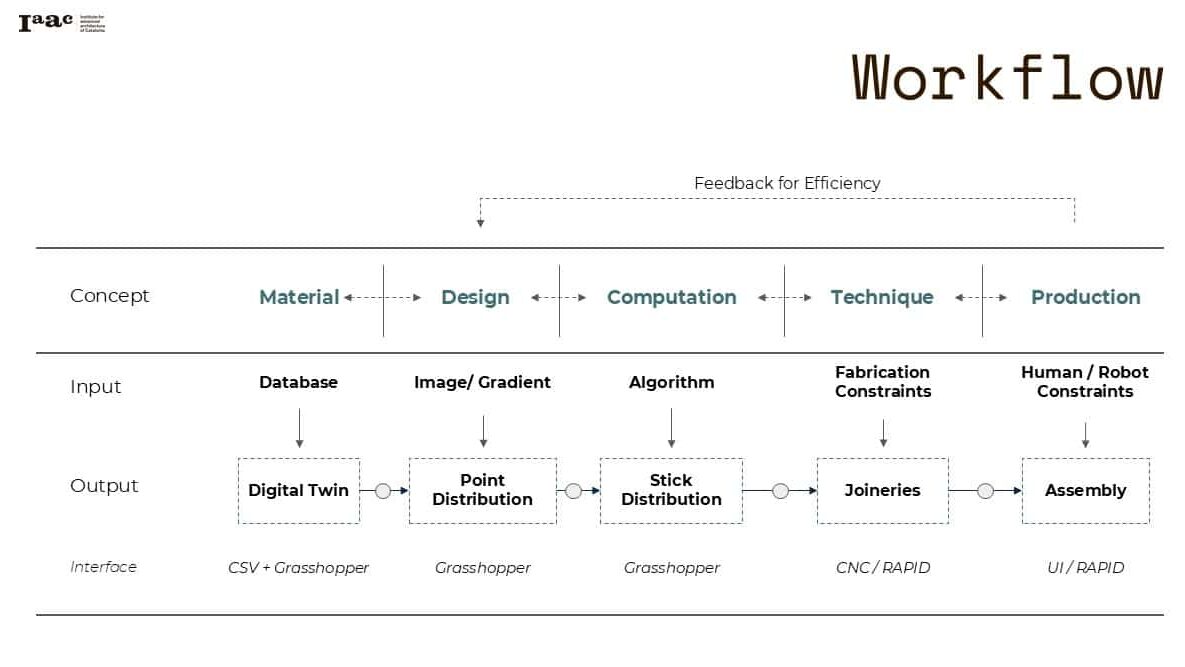
Computational Strategies
Unlike conventional timber construction, this project had to address random cross-sections, unpredictable lengths, and surface imperfections. The computational approach included:
- Density mapping from images to inform placement intensity
- Length maximization to minimize offcuts
- Joinery angle constraints for robotic feasibility
- Minimum spacing between joinery points to avoid weakening
Three distribution methods were tested:
- Kangaroo collision-based (IoU Achieved: 43%)
- Remeshing by color (IoU Achieved: 72%)
- Poisson disk sampling with variable density, which achieved the best domain match (IoU Achieved: 95%)
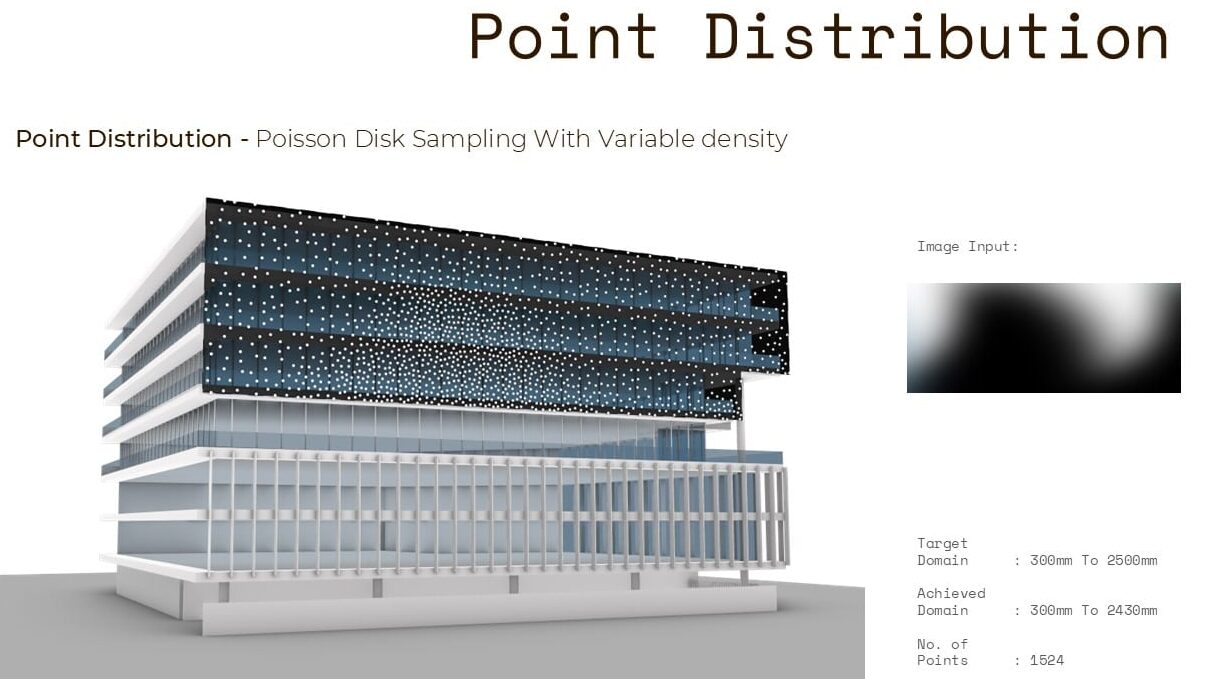
Joinery Experiments
Designing joineries was critical to preserve reuse potential. The joineries considered included notching, dowels, nails, and wooden pegs. Through algorithmic extraction of joinery zones, sticks could be connected while respecting strength and allowing future disassembly.
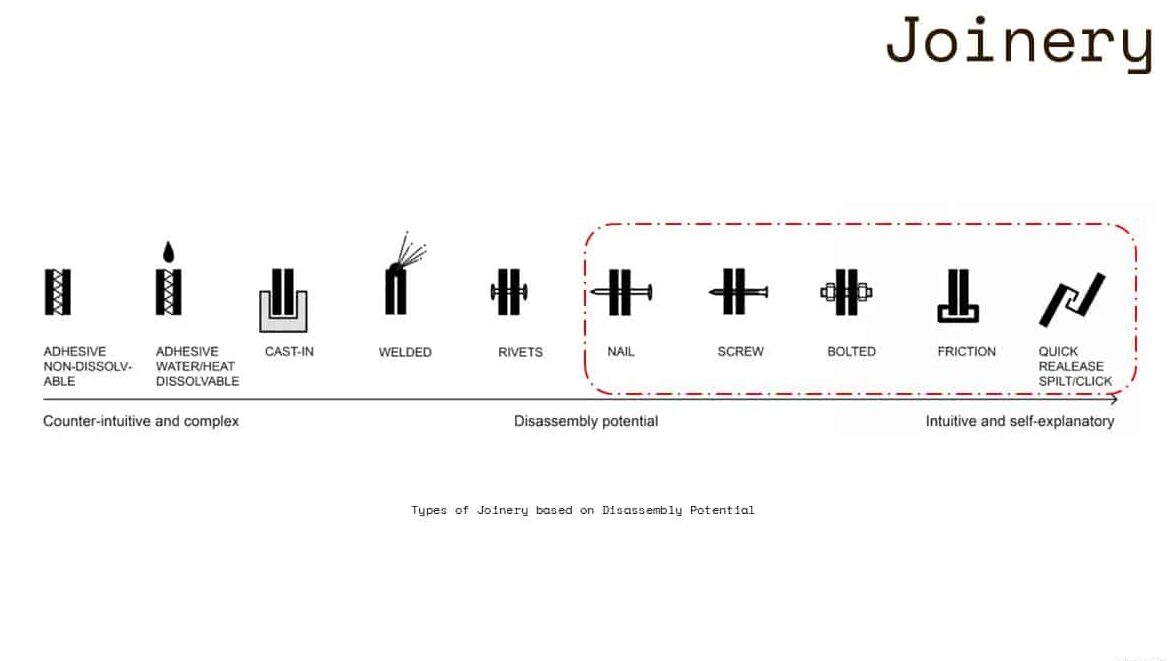
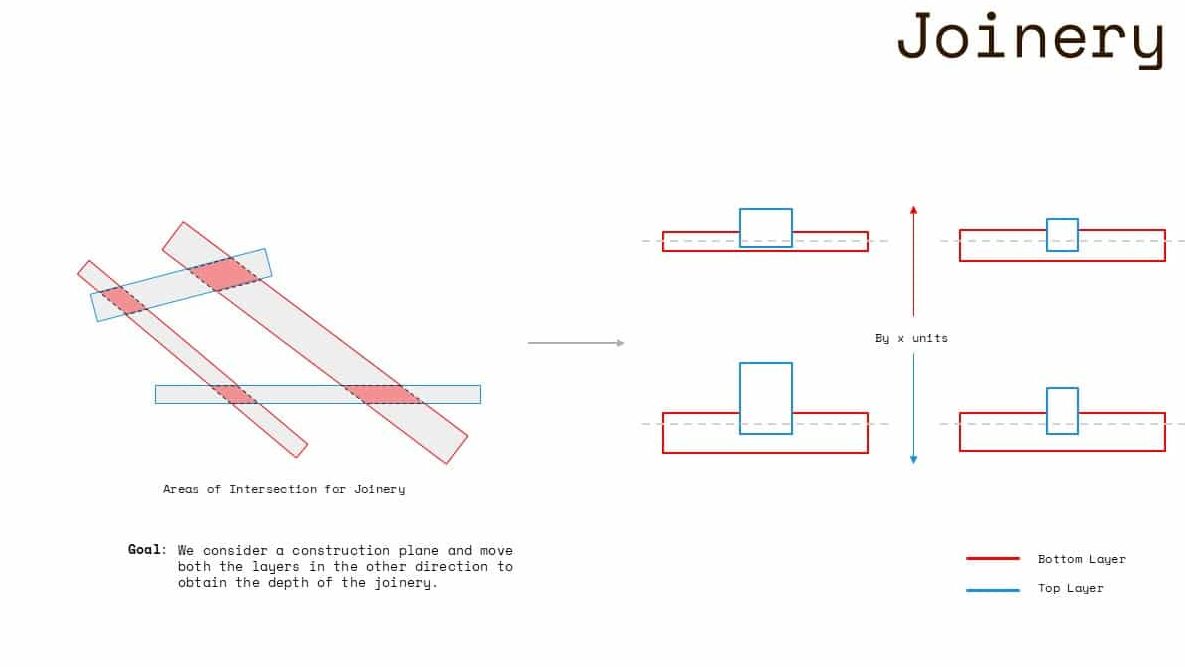
Algorithmic Assembly Strategies
Two principal algorithms structured the assembly process:
Dual-Layered Colonization
- Grew stick aggregations in layered patterns
- Optimized stick placement while checking collisions and angles
- Pattern similarity to target images: 35%
Multi-Layered Delaunay
- Used Delaunay triangulated edges for distributing sticks
- Controlled angles and joinery points
- Pattern similarity: 43%
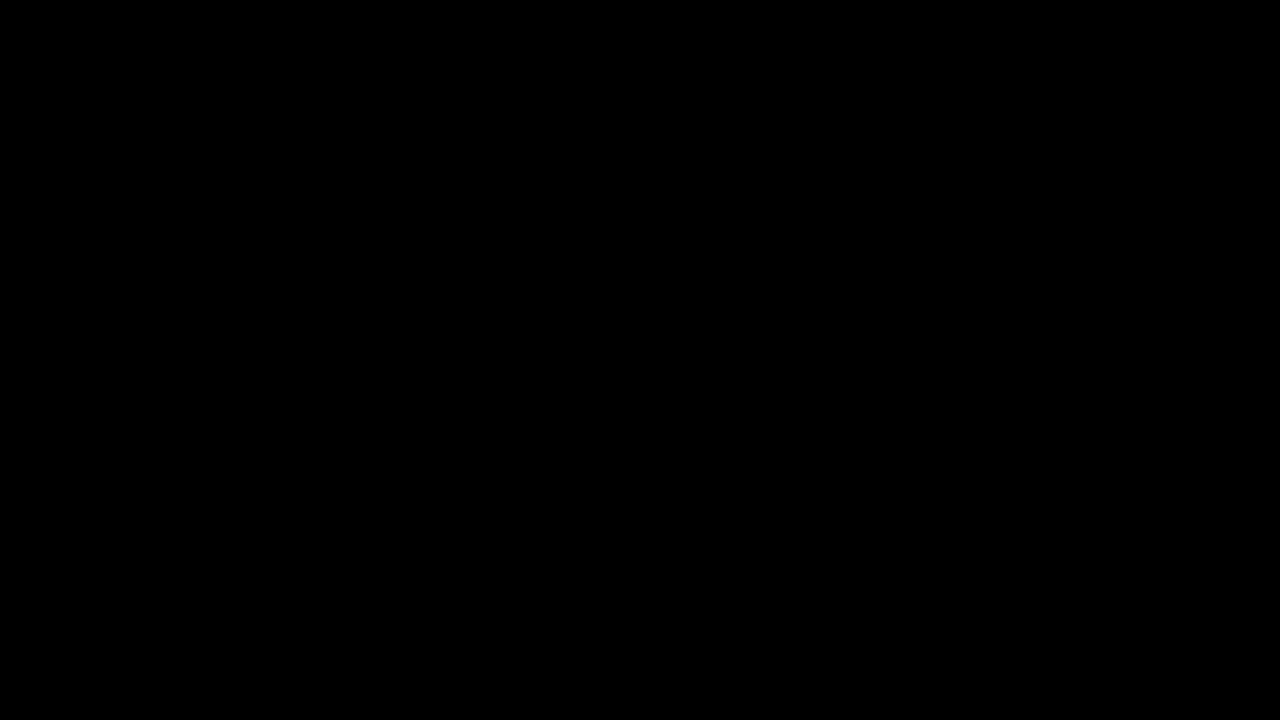
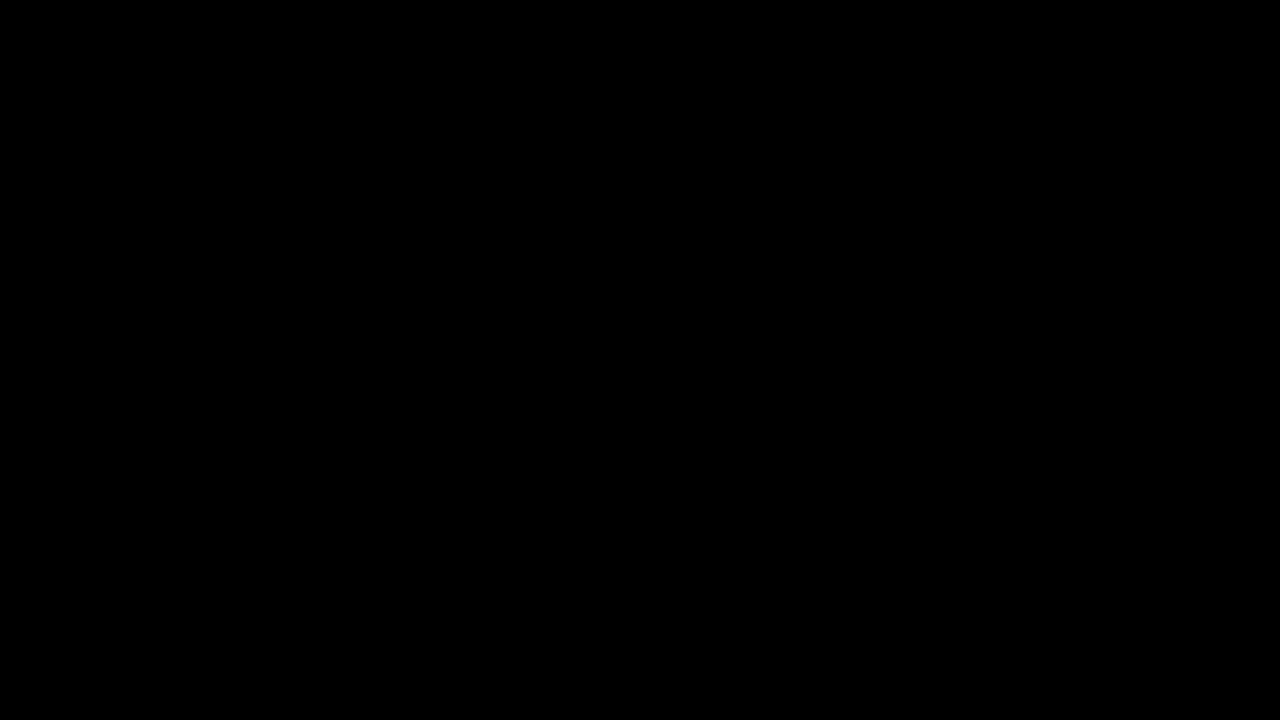
Physical Prototyping
Two prototypes at 1:1 scale validated the workflow:
- The colonization prototype showed an organic aggregation
- The Delaunay prototype demonstrated a geometric framework
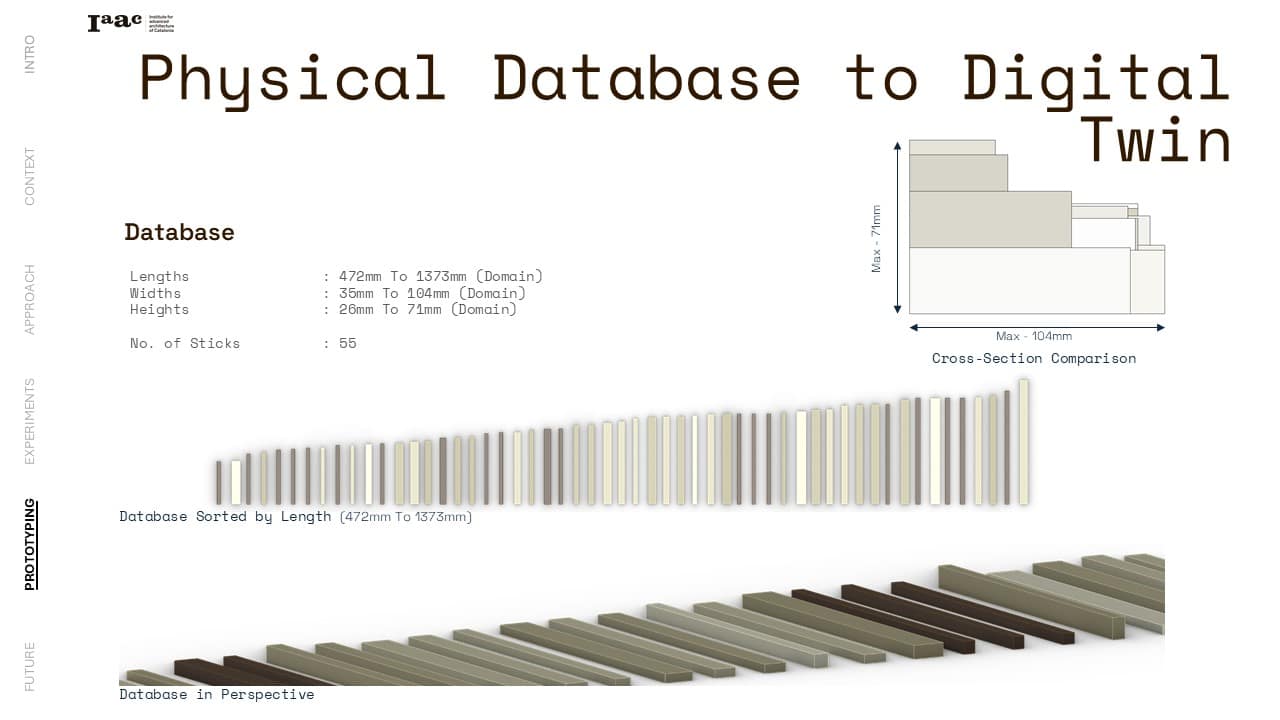
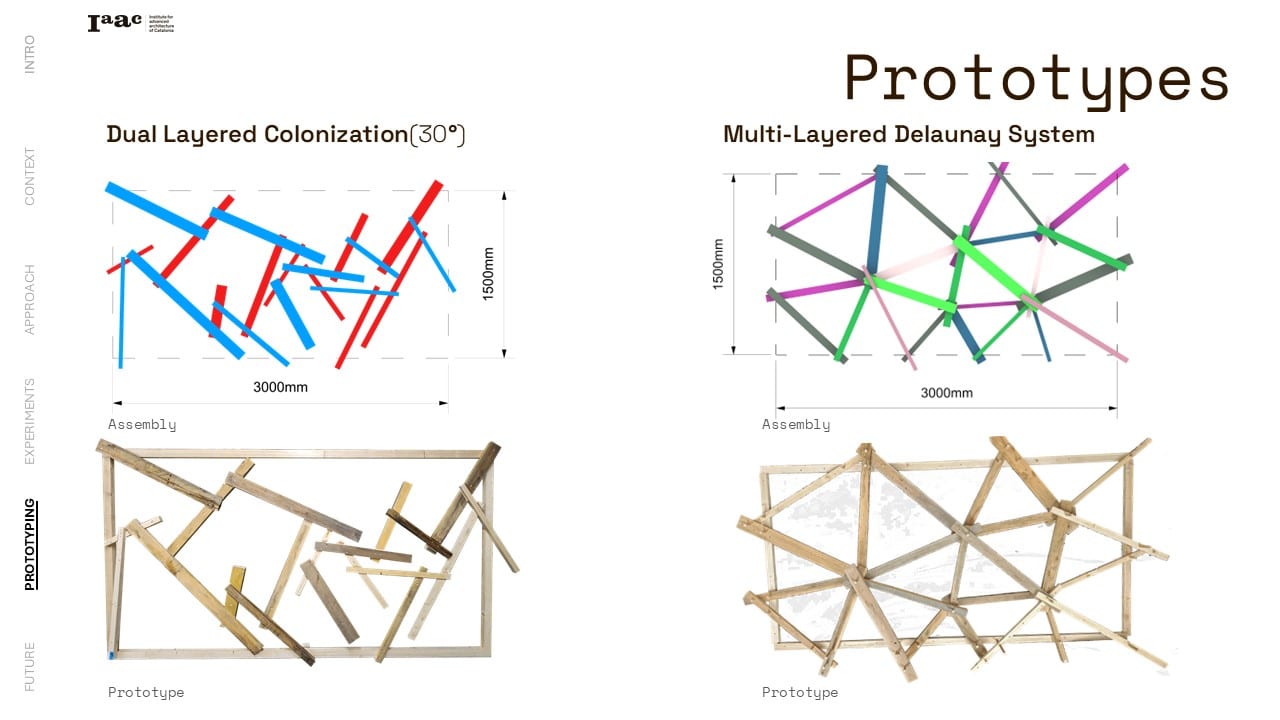
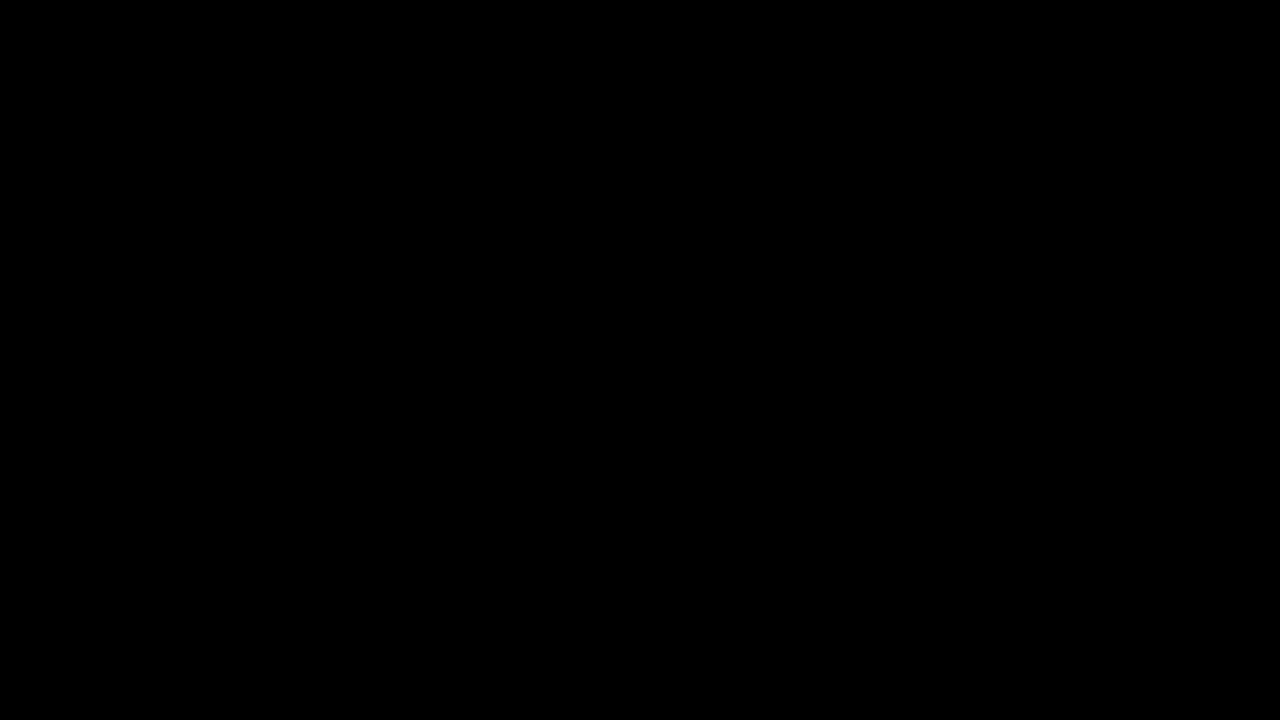
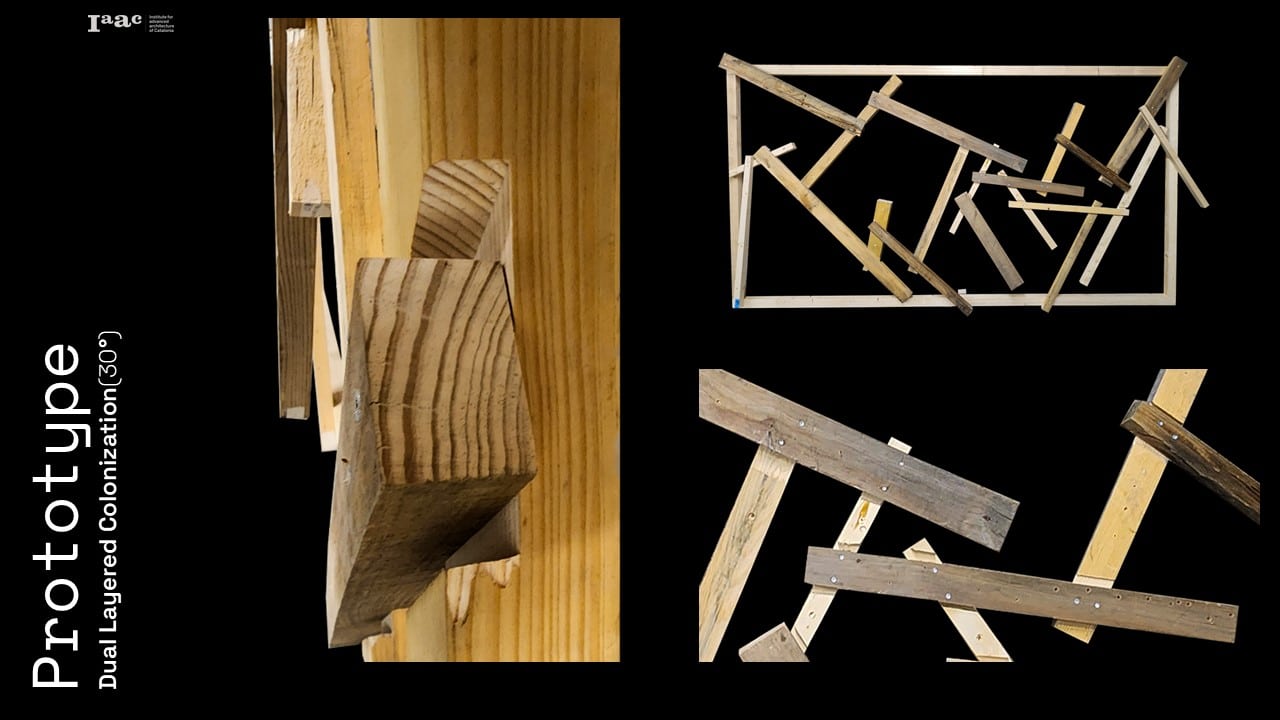
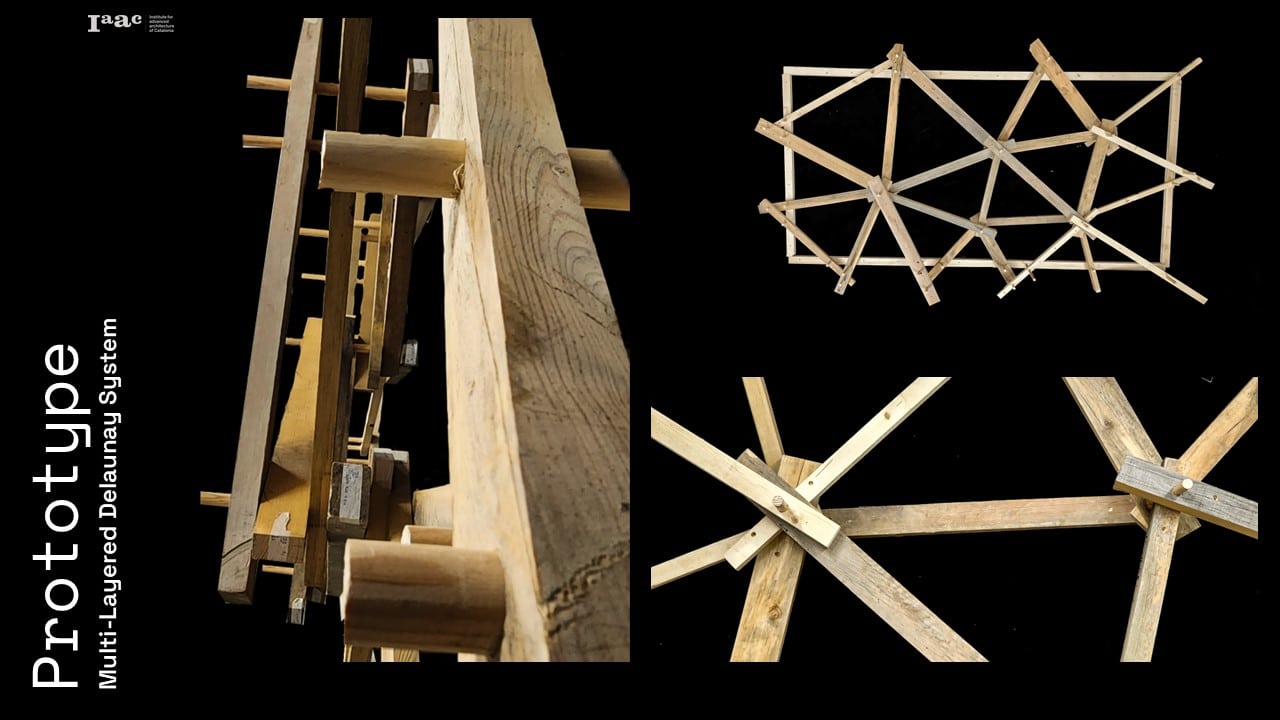
Bold keywords: full-scale prototype, robotic fabrication, digital-to-physical
Robotic Experiments
Robotic trials explored the feasibility of transforming digital logic into physical fabrication:
- Milling: tested surface preparation
- Dowel joinery drilling: validated positional tolerances
- Notch joinery fabrication: confirmed toolpath strategies
- Pick-and-place: tested gripper stability for sticks from 30–90 mm cross-sections
Bold keywords: robotic milling, robotic joinery, pick and place, industrial robotics
Evaluation and Future Prospects
The system’s performance was evaluated using a Jaccard-index–like overlap measure, with the Poisson disk sampling achieving 95% domain coverage. The Delaunay approach reached 43% pattern similarity.
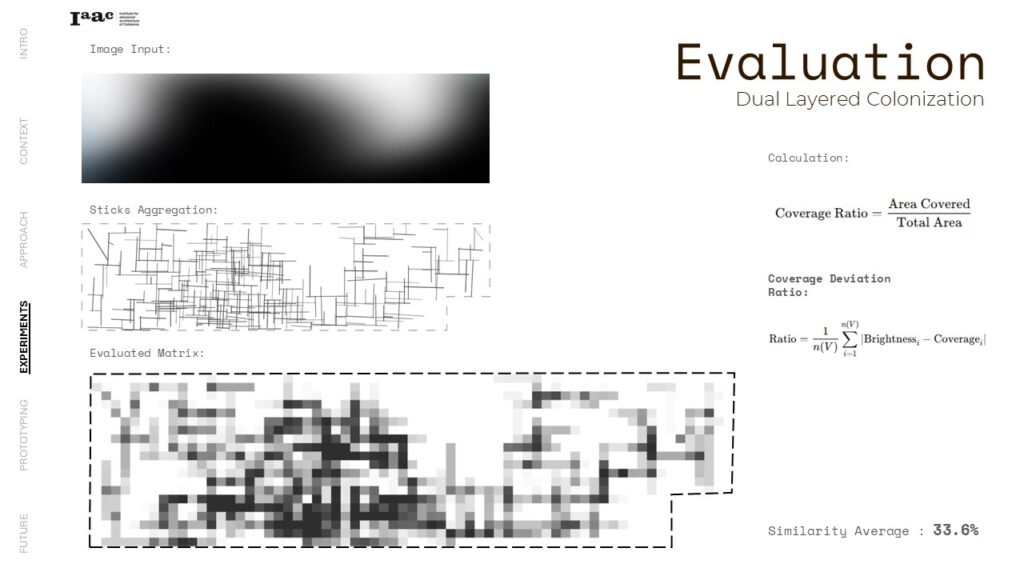
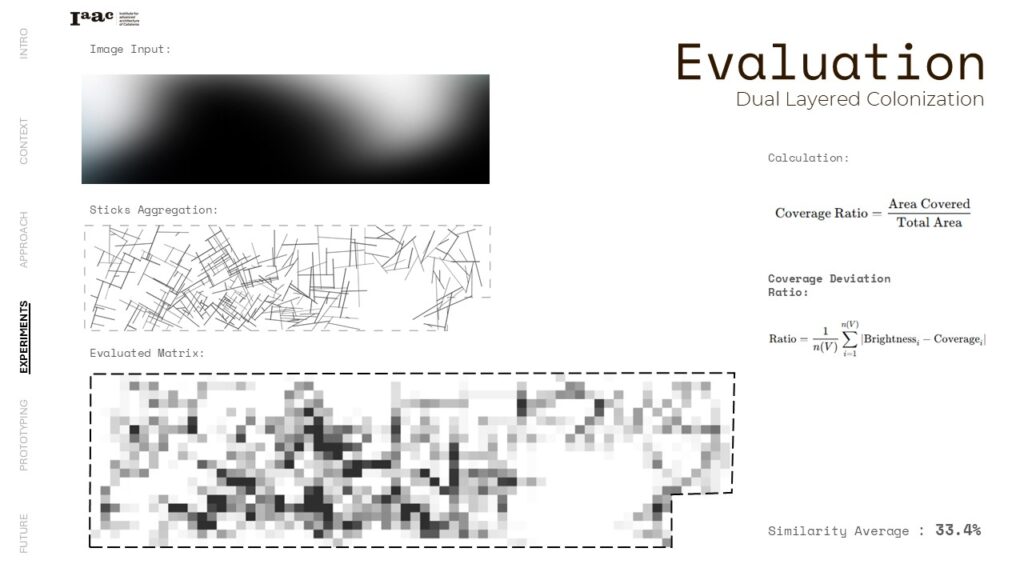
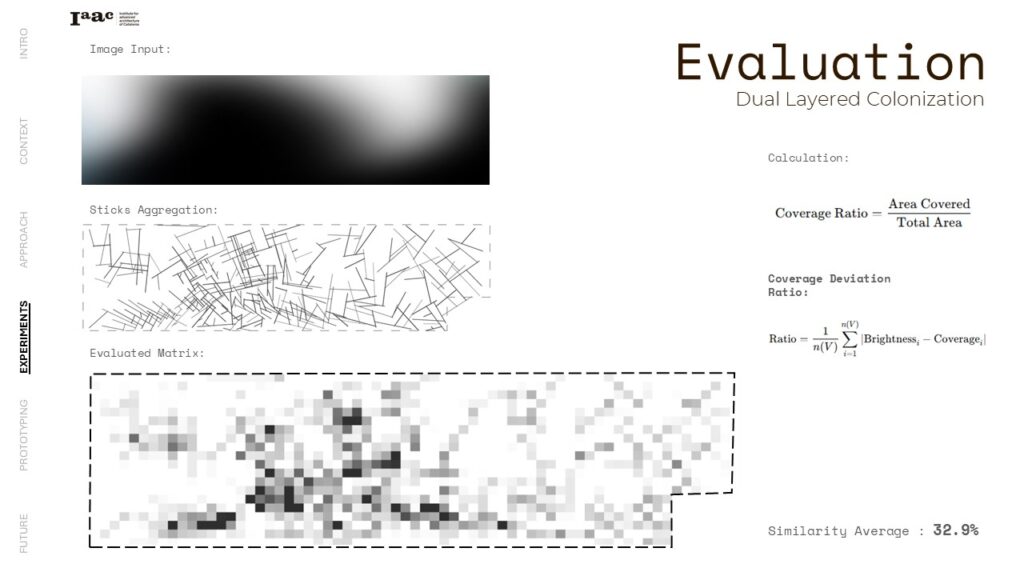
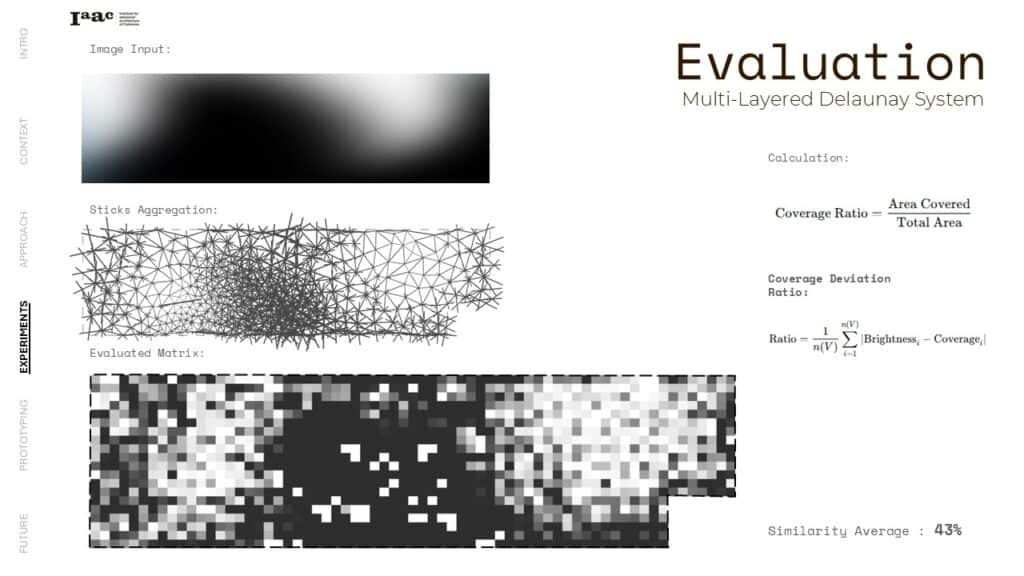
Future improvements could include:
- GPU acceleration
- Real-time scanning with tolerances below 2 mm
- Web-based configurators
- Carbon impact calculations showing CO2 savings
Conclusion
Timber Syntax demonstrates how a computational, digitally fabricated, and robotically assisted system can transform non-homogeneous timber into valuable facade assemblies with minimal waste. By embracing circularity, the project sets a powerful example for algorithmic architecture and carbon-responsible construction.
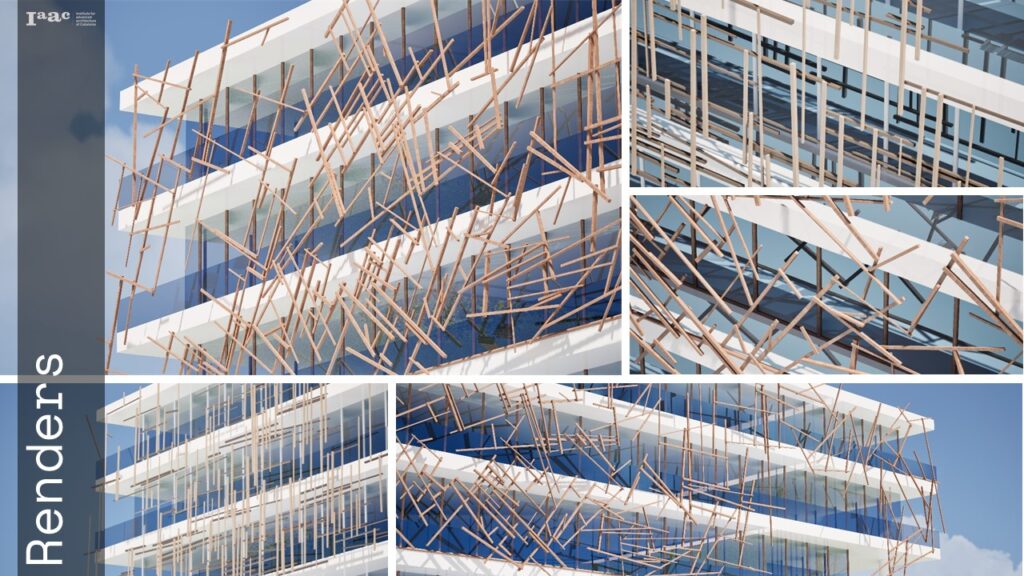