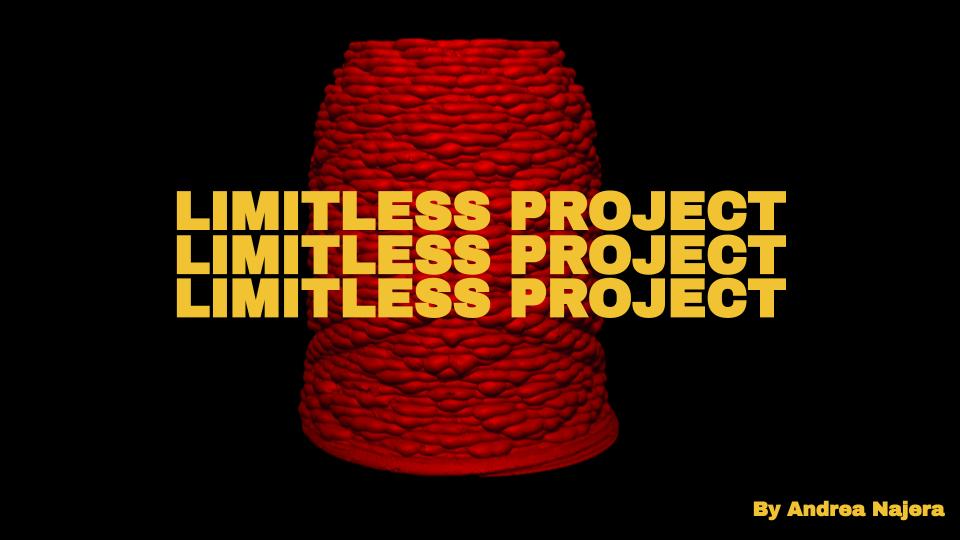
The industry of construction creates most of the waste in the world. By 2025 we expect to reach 2.2 billion tons globally.
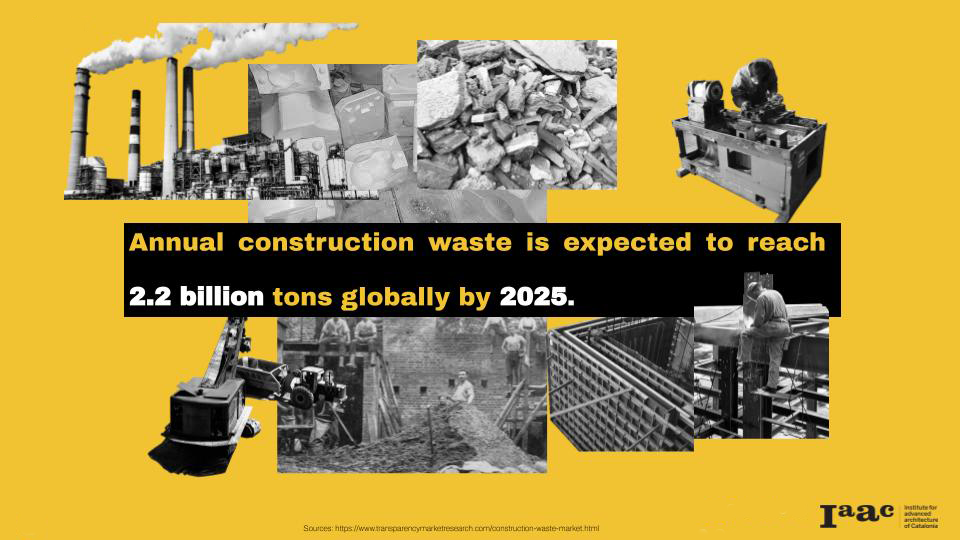
As a solution of this problem, industry 4.0 proposed the Additive manufacturing process, which is looking for the optimization of fabrication and construction adding layer by layer different materials; this process started being tested since 1930… I know impresive right
But what are the advantages of Additive Manufacturing?
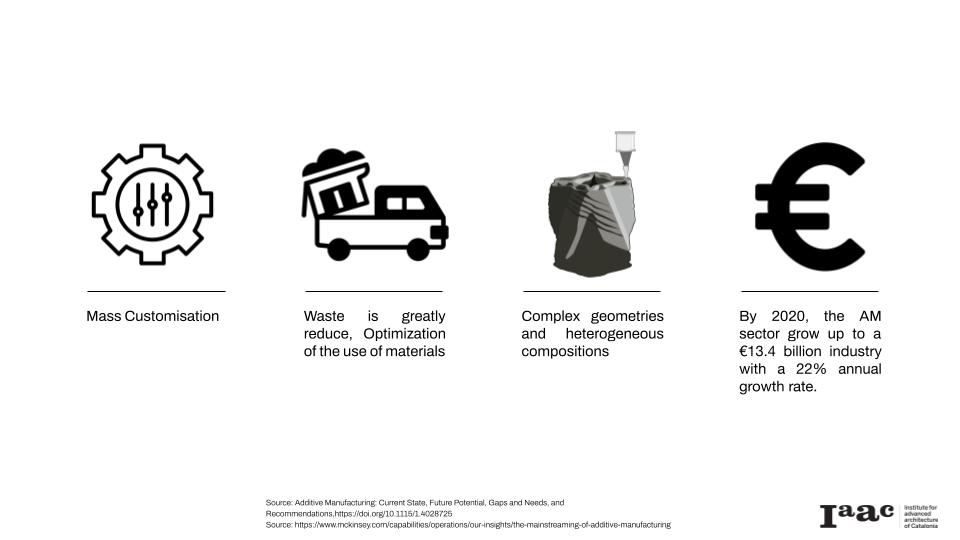
Sounds like a perfect technique right? … well the reality is different … The truth is that additive manufacturing is taught.
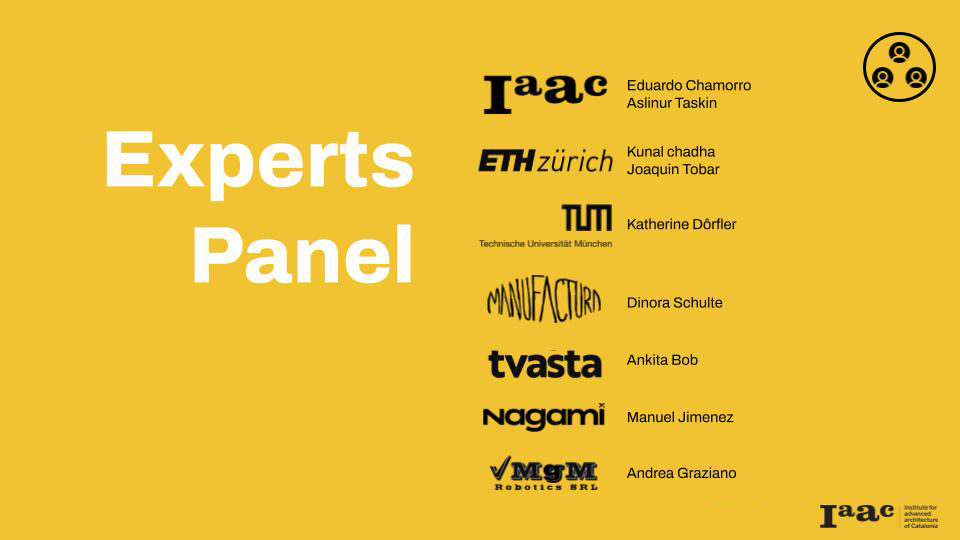
We found this three main important conclusions and common problems

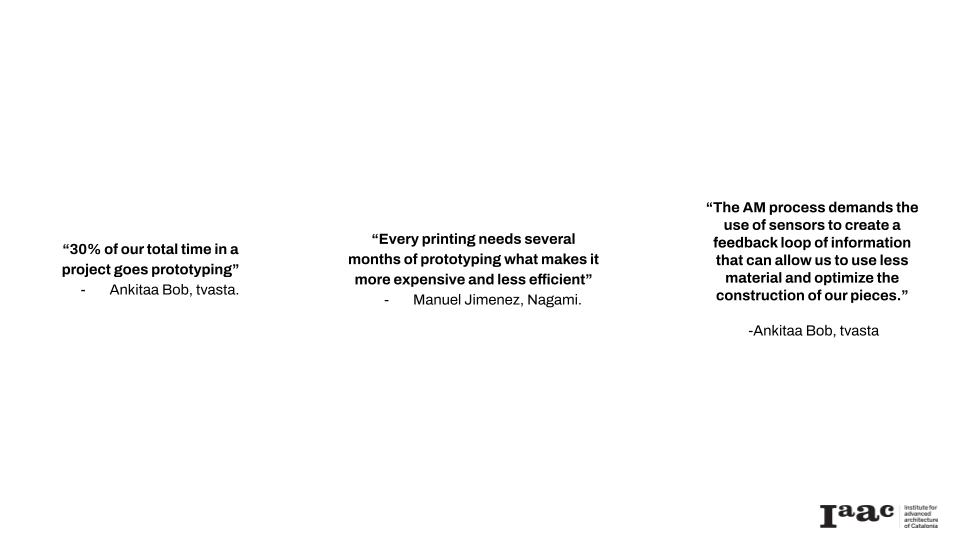
So… how can we mix the use of sensors into the 3d printing process to decrease the prototyping time? … after looking into different research papers we found similar approaches and variables that we can use as principles.
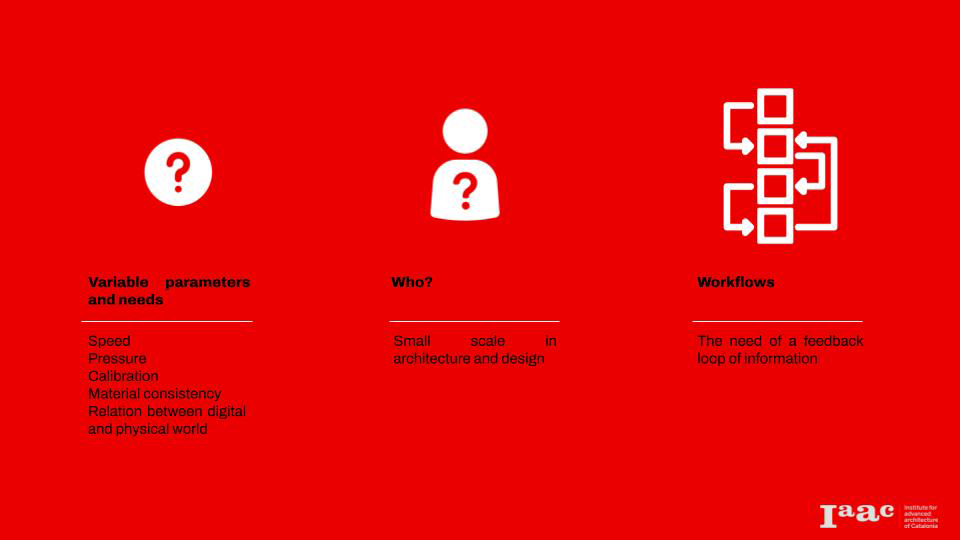
Here is when the Limitless project started being in the map, we are a tool that allows the monitoring, measure and documentation of the AM process at the memento of the printing, with the help of conventional cameras, analog sensors, robot data and open source technology. All of this with the purpose of adapting the toolpaths and features according to compensate deviation and reduce prototyping time.
Basically we are identifying problems getting the complete information about what was happening in the whole process to know … when it fails and why.
To be able to do this we did the next workflow of information.
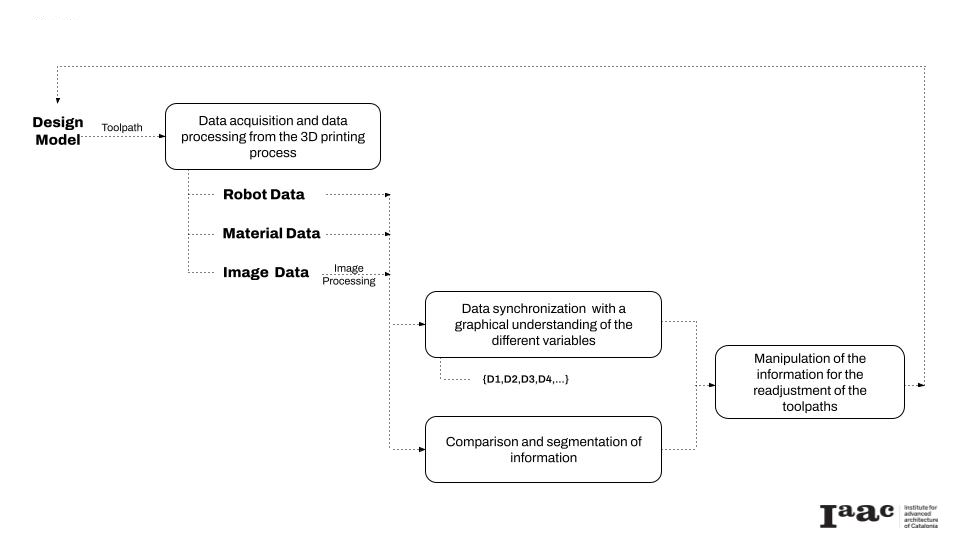
To start creating a Data set of the information of our process we need to have a Data Acquisition Structure that is build with seven different variables:
Robot Data: Recording of the TCP in relation with the gcode line. Position, orientation, TCP Speed, Time.
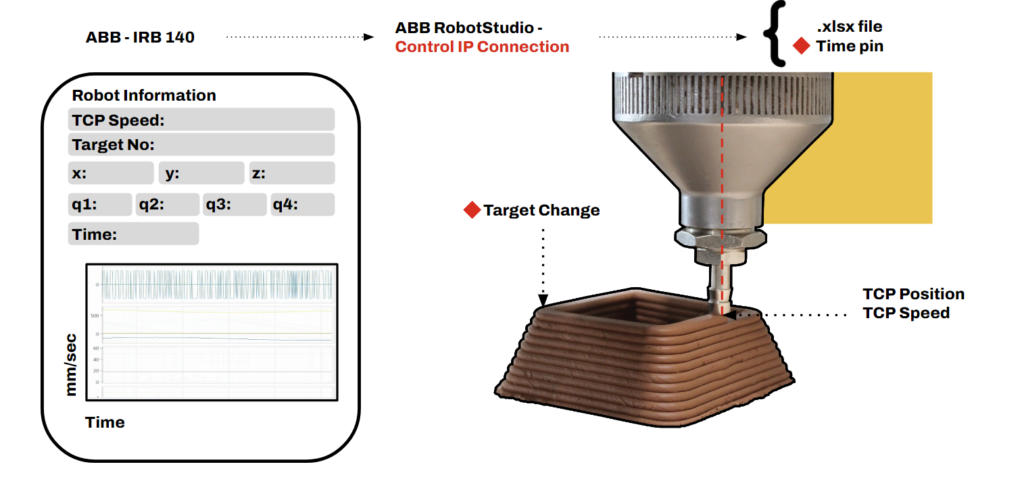
The Material data: in this case for the case of study we use clay so we add a moisture sensor to the mix to monitor the humidity of the material.
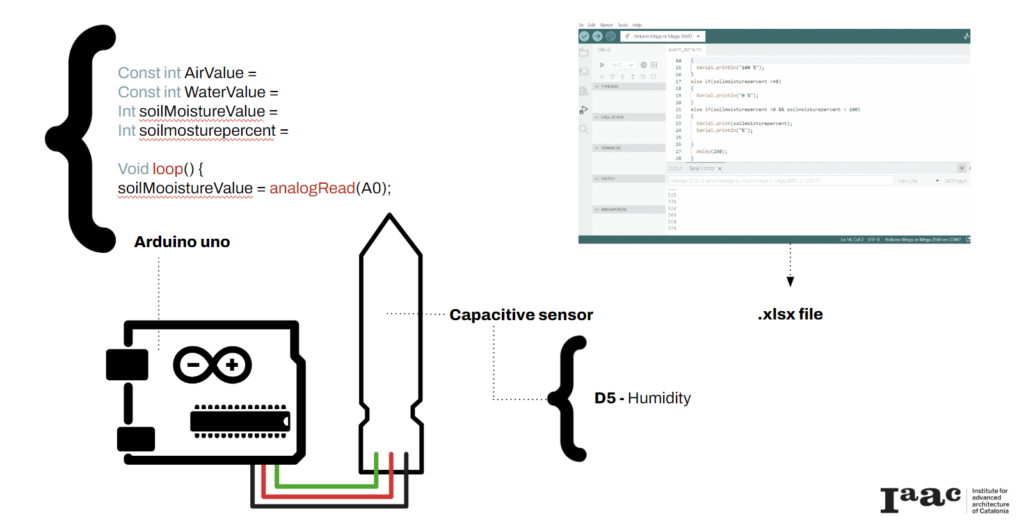
But … where is the computer vision part?
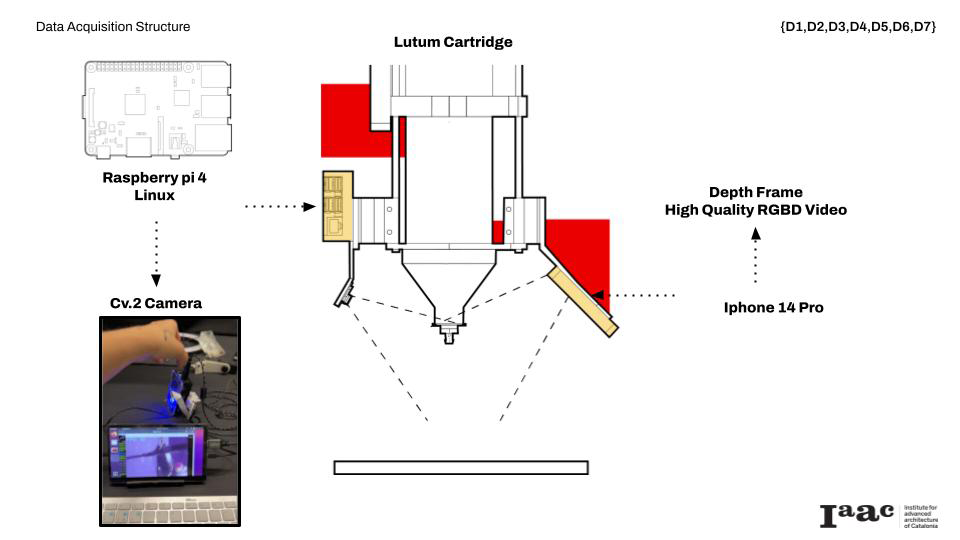
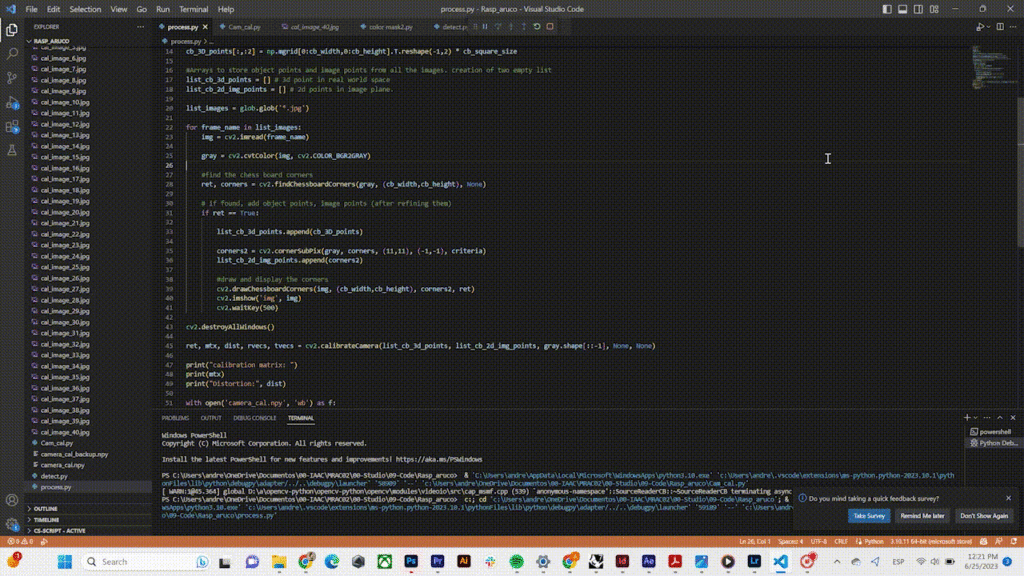
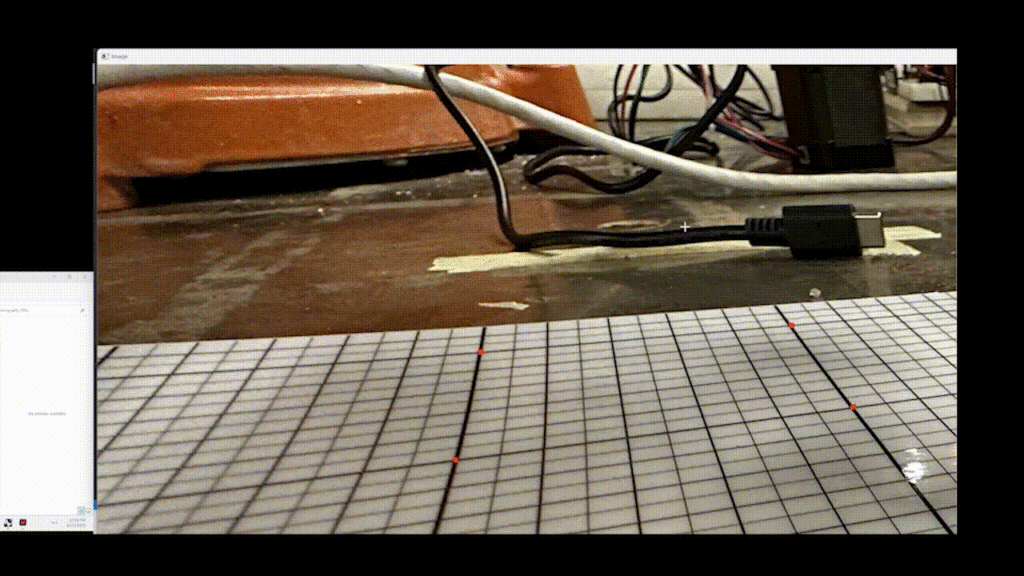
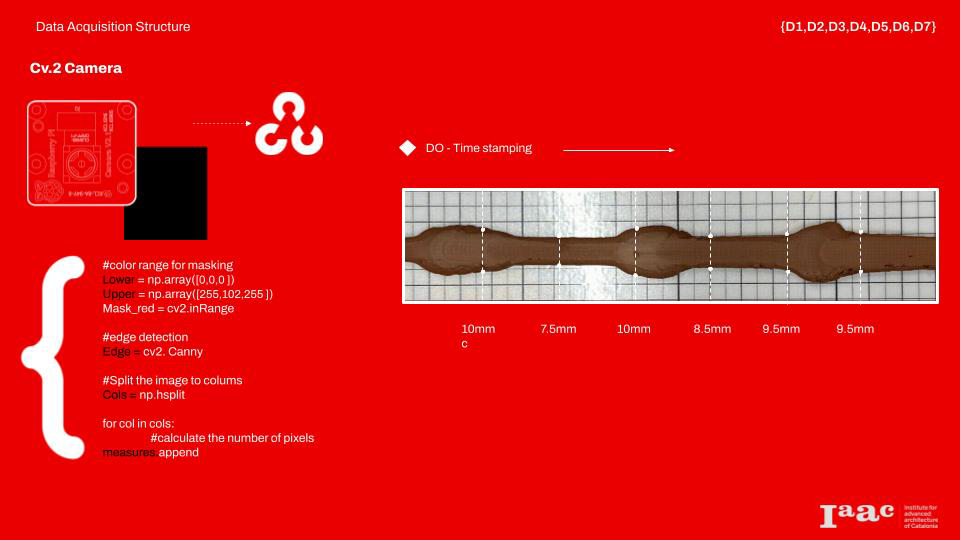
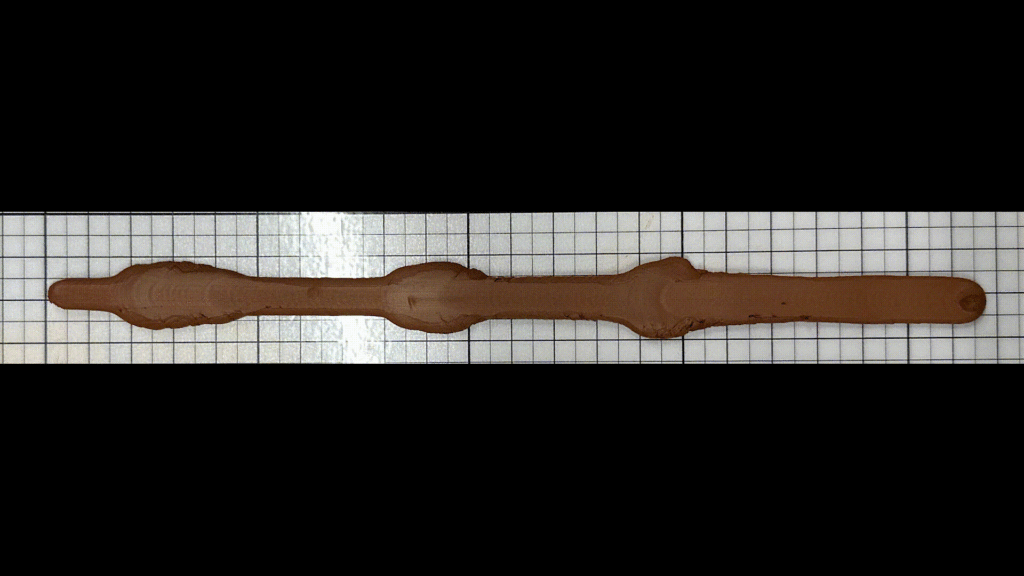
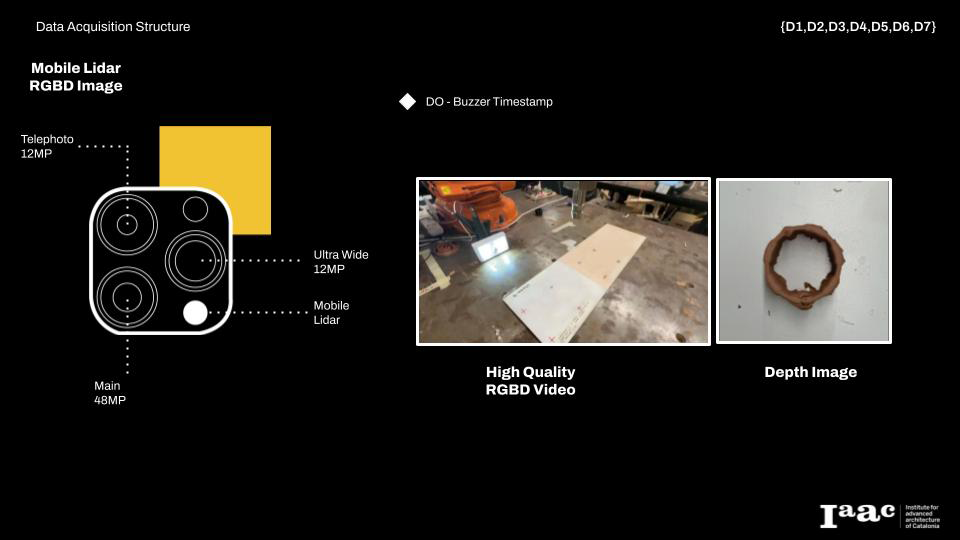
Finally… Our Data Set has all the information that we are looking for but now, how are we going to synchronize it? … All the Data from the different sources is synchronized by the time given by the Robot and the Do Activation.
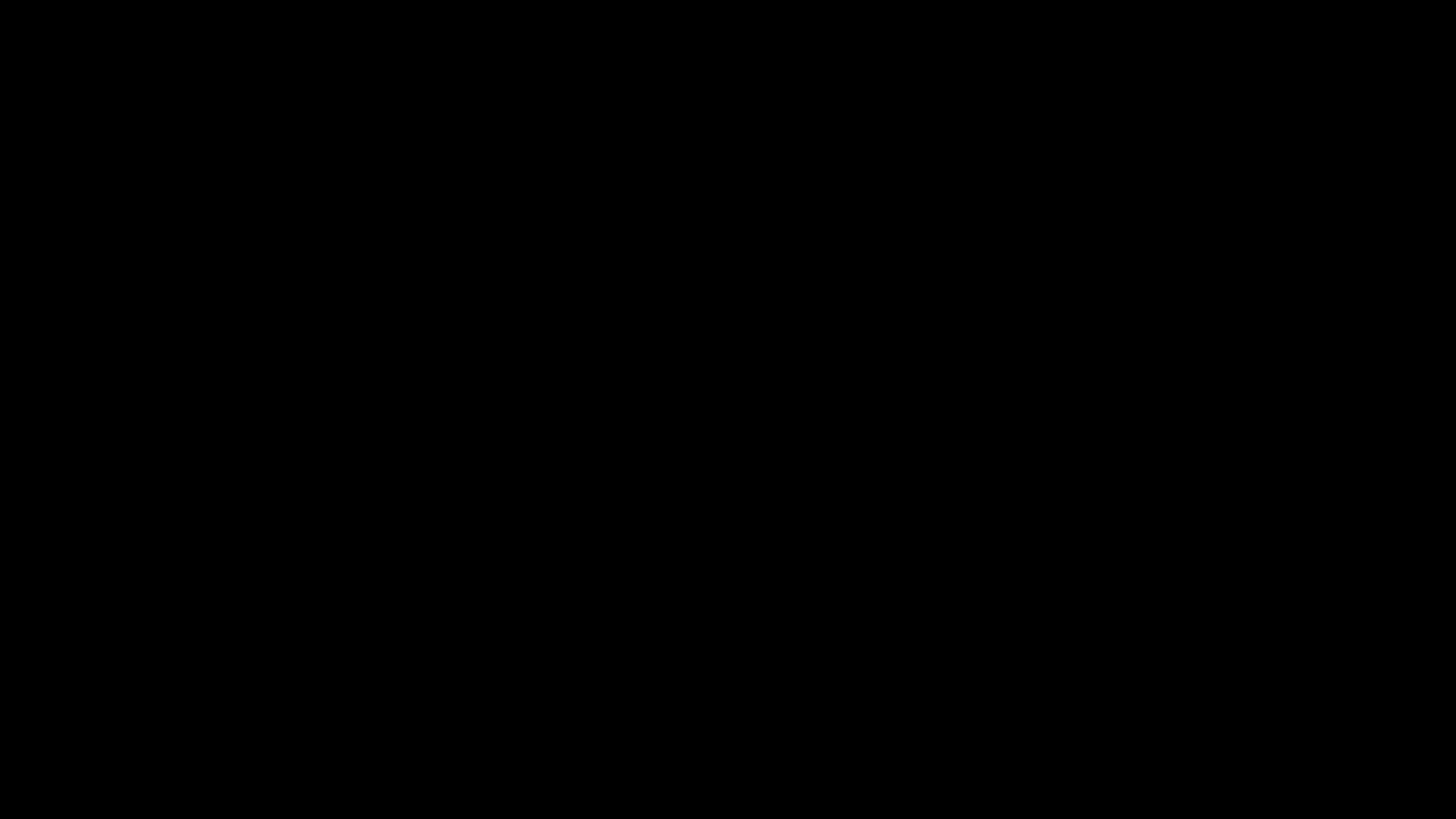
Now we are able to know the plane, when the fail happens, the physical position, orientation and speed of our robot and the width of our printing.
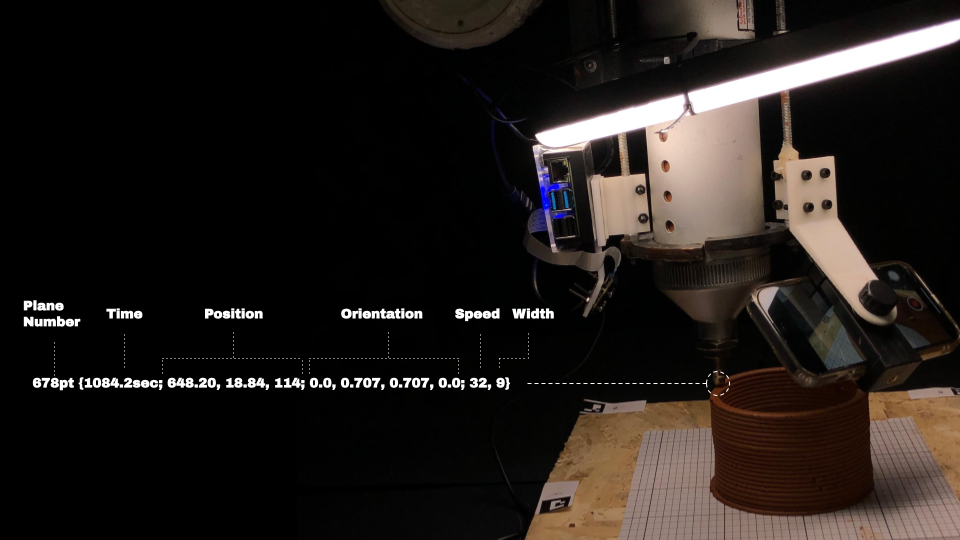
With all this understanding now we are able to also globally know and filter the planes in which we have an over extrusion or an under extrusion and what was happening, and create Libraries for future steps.
As a case of study we start playing with this new understanding, variating one value and taking the process to the limit of the printing.
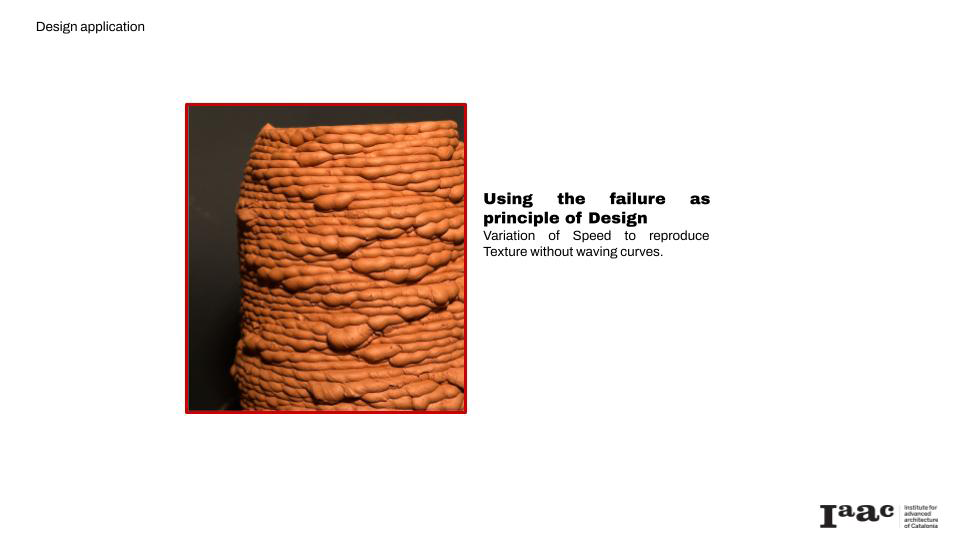
We start identifying where we can produce the fail points to get the width that we were looking for.
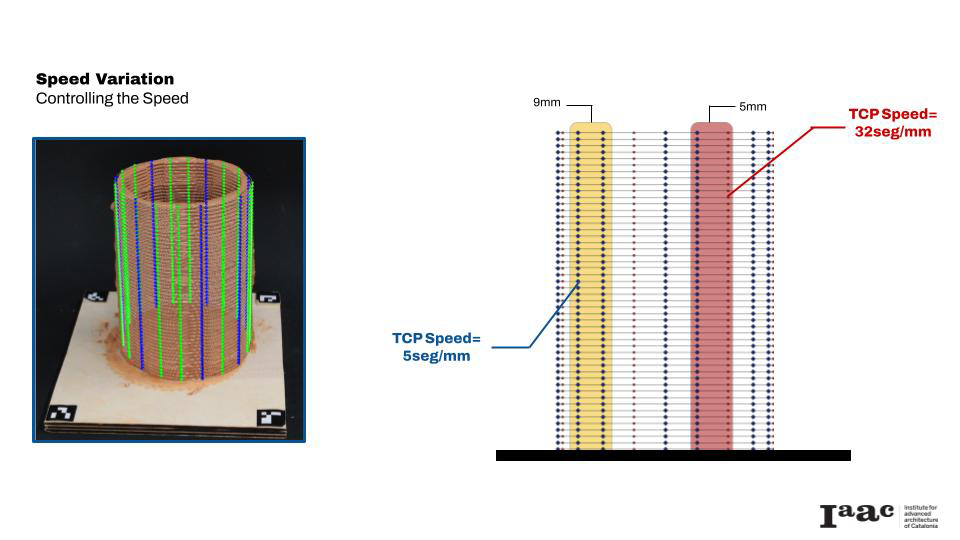
Then let’s make it more interesting and create a proper over extrude pattern witn speed variations. We set two different speeds, one in blue that is a robot physical speed of 5seg/mm and the one in red that is 32 seg/mm.
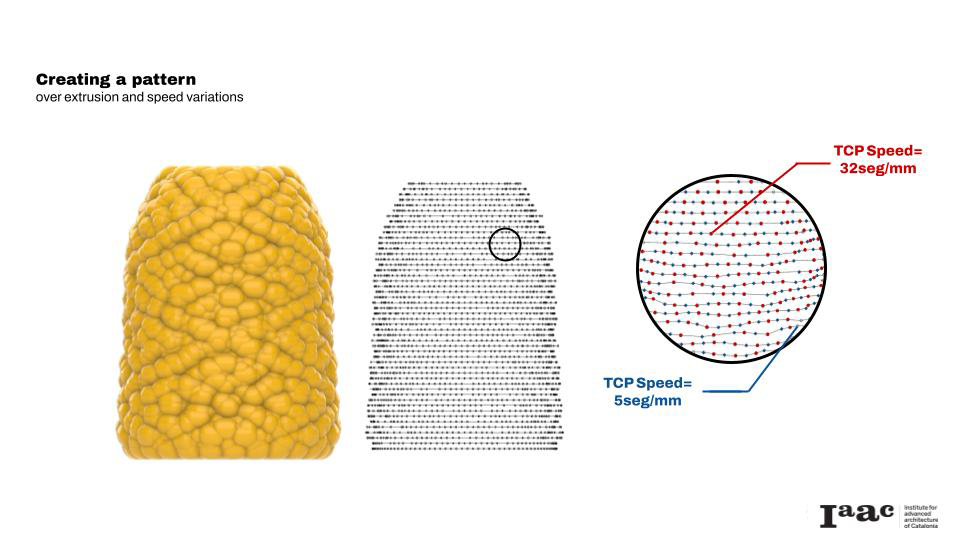
Having a full control of the speed in each point of our printing allow os to reproduce complex textures that can emulate even different materials
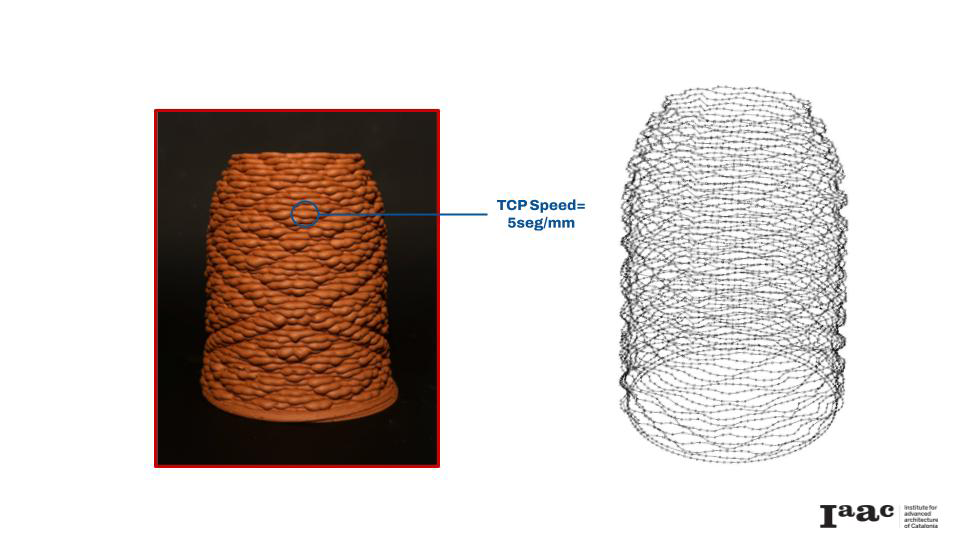
Further Implementation
Add Computer vision technology to our 3D printing process help us to decrease the prototype time.
The creations of libraries of information and RGBD images itself can will help with the training of new algorithms to predict future mistakes and me more accurate and efficient in the process.
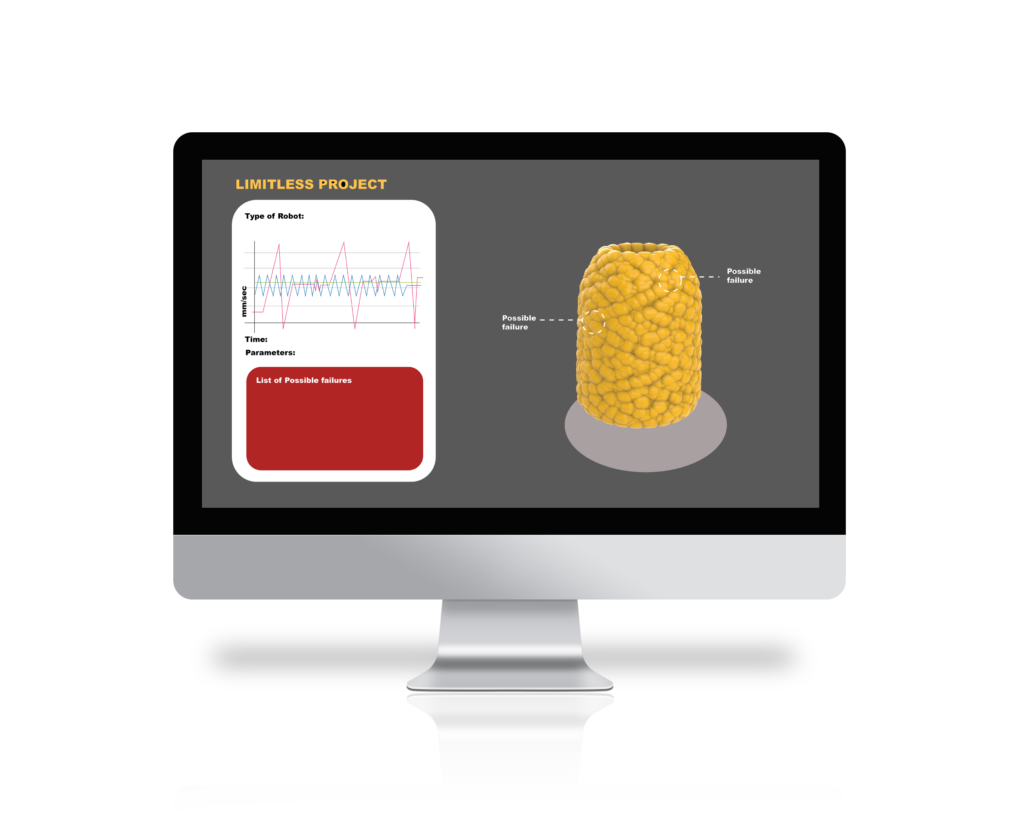
Limitless project is a project of IAAC, Institute for Advanced Architecture of Catalonia developed in the Master in Robotics & Advanced Construction 02, 2022-2023 by Andrea Najera. Faculty: Aldo Sollazzo, Alex Dubor.