In this class we were introduced to three fabrication techniques, Laser Cutting, 3D printing and CNC milling. In each technique we were tasked with creating prototypes of vertical facade elements that could be used in architectural applications. Every two weeks of the course we learned how to use each technology and then fabricated our own prototypes, concluding with three geometries.

For laser cutting, we were interested in the interlocking technique and wanted to experiment with material in our prototype. We gained inspiration from structures such as the Metropol Parasol in Seville, and Zahner Factory Expansion in Kansas City, which combine interlocking planes with more organic curved profiles. Our final geometry used a cut pattern in the wood that allowed it to be flexible, and was then interlocked through notches on an acrylic base.
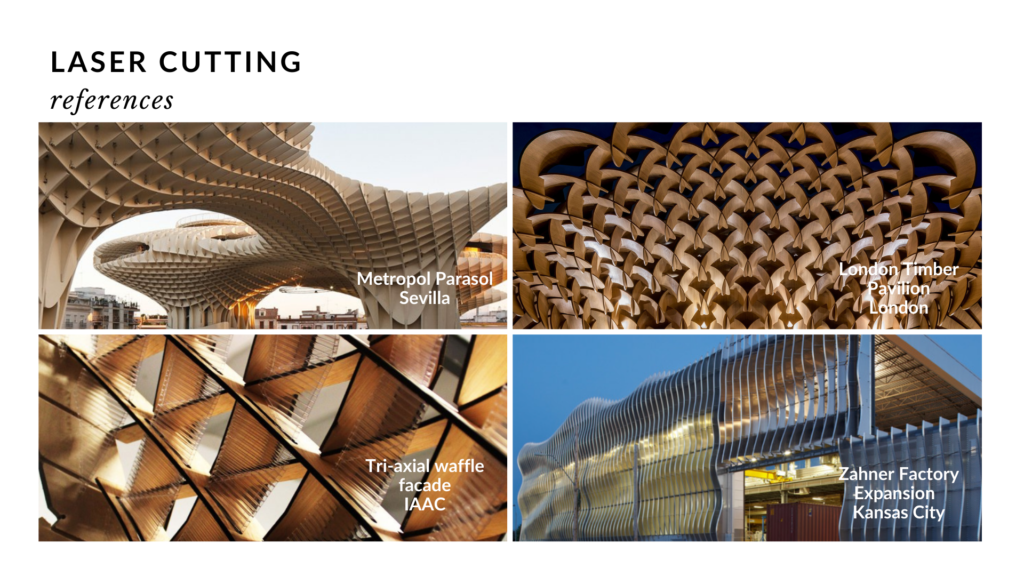
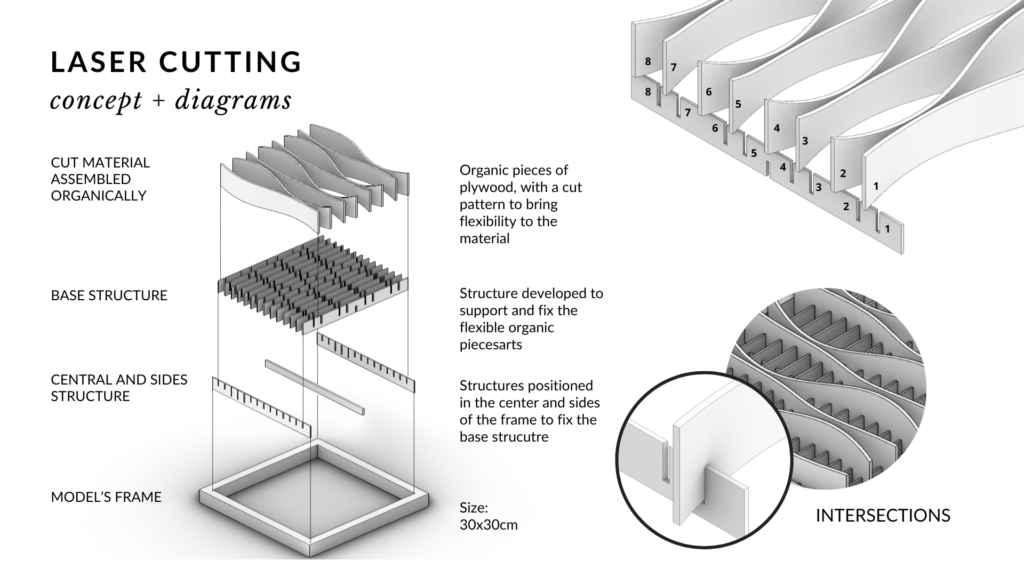
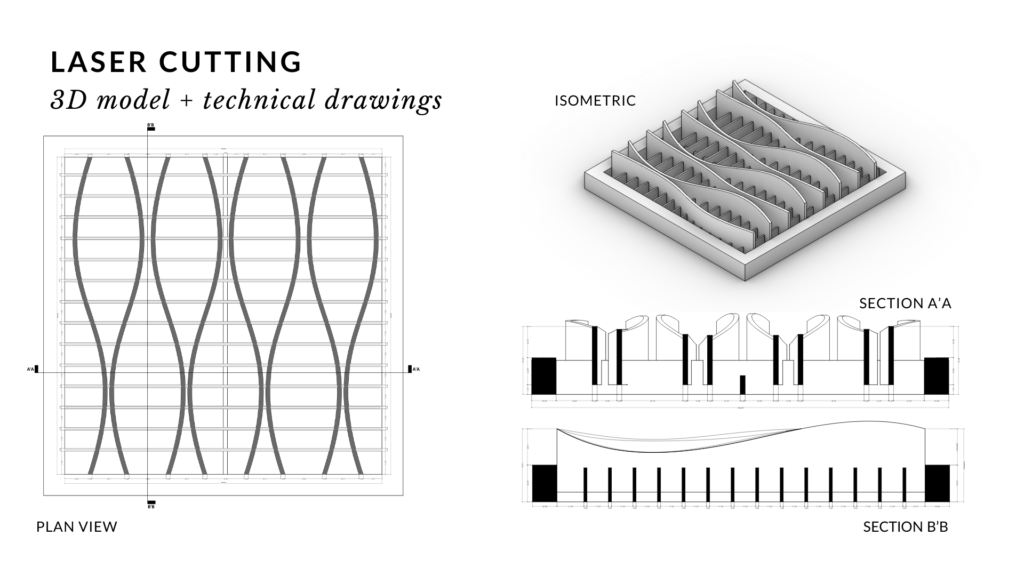
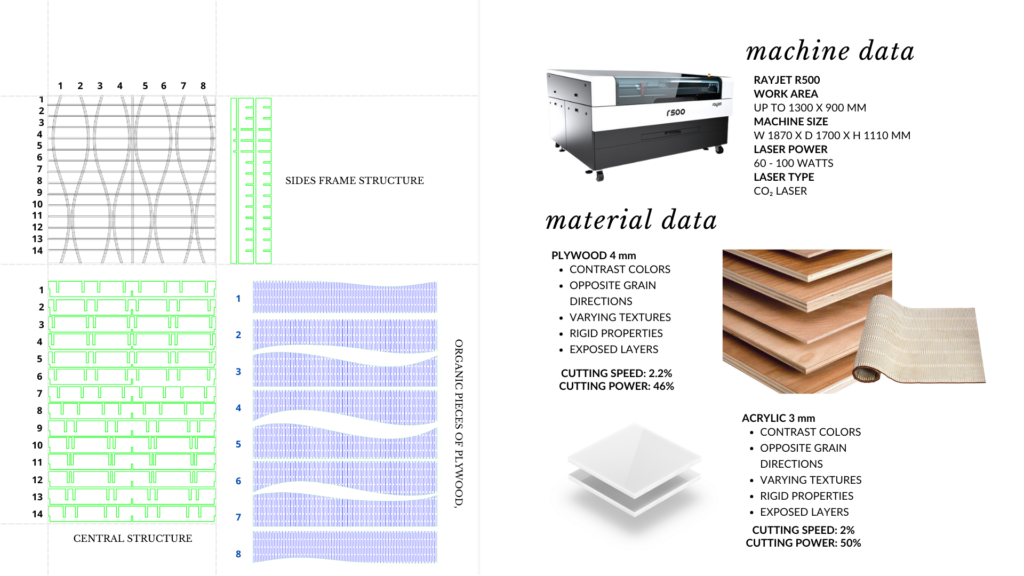
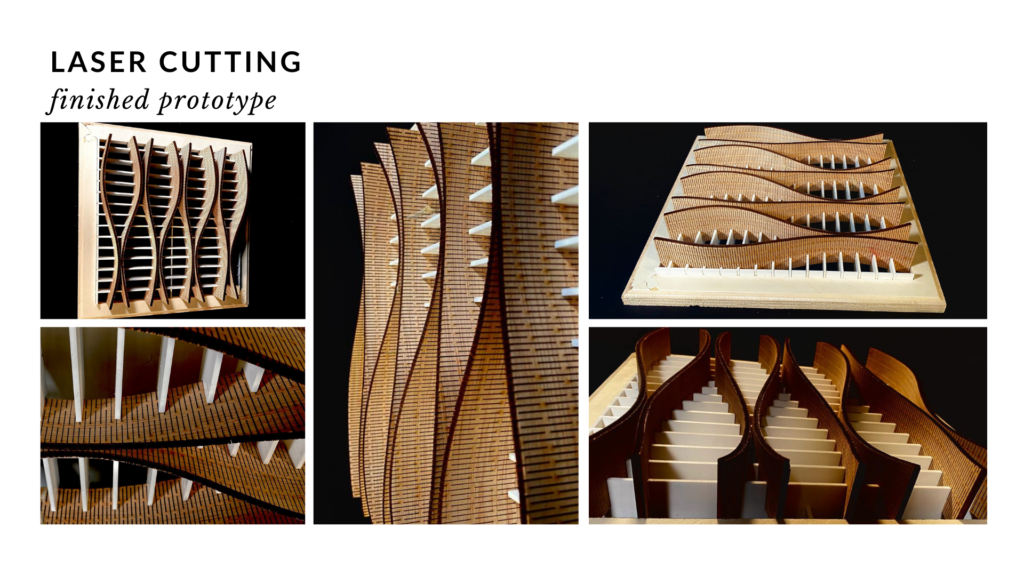
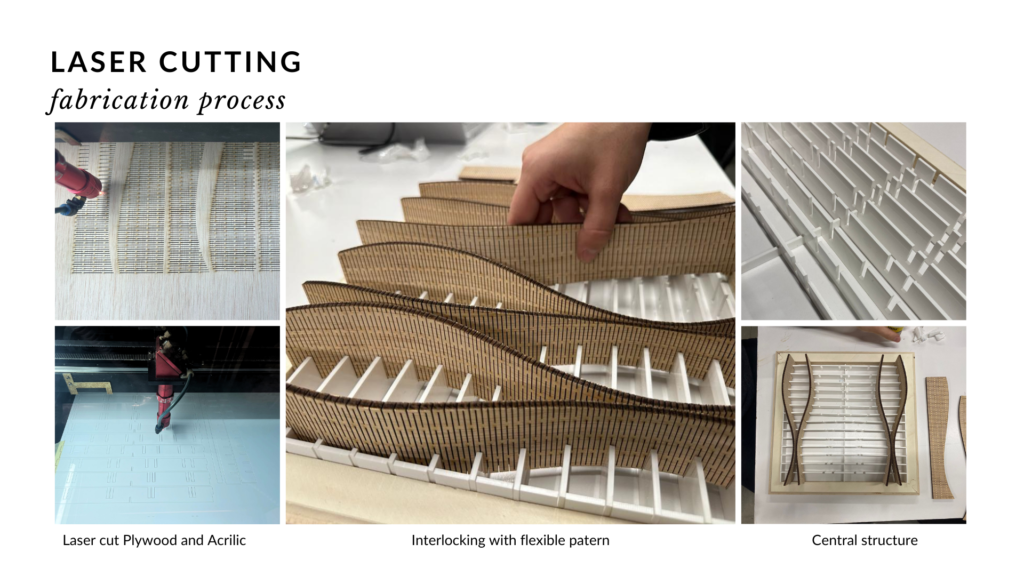
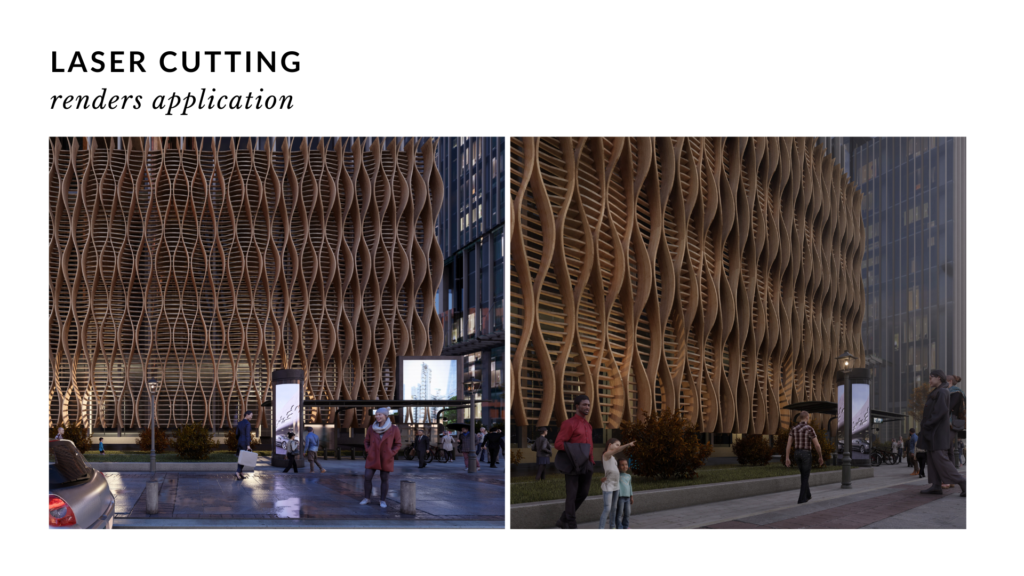

Next was 3D Printing, we were again inspired by an interlocking technique, but utilized it in the form of stacking. Referencing artist Brian Peters, we produced one 2D shape that would fit within itself repeatedly, and then extruded at various thicknesses to create a more dynamic geometry. We tested various scales and thicknesses and the result was a vertical element that could be used in an interior application such as a wall partition or art piece.
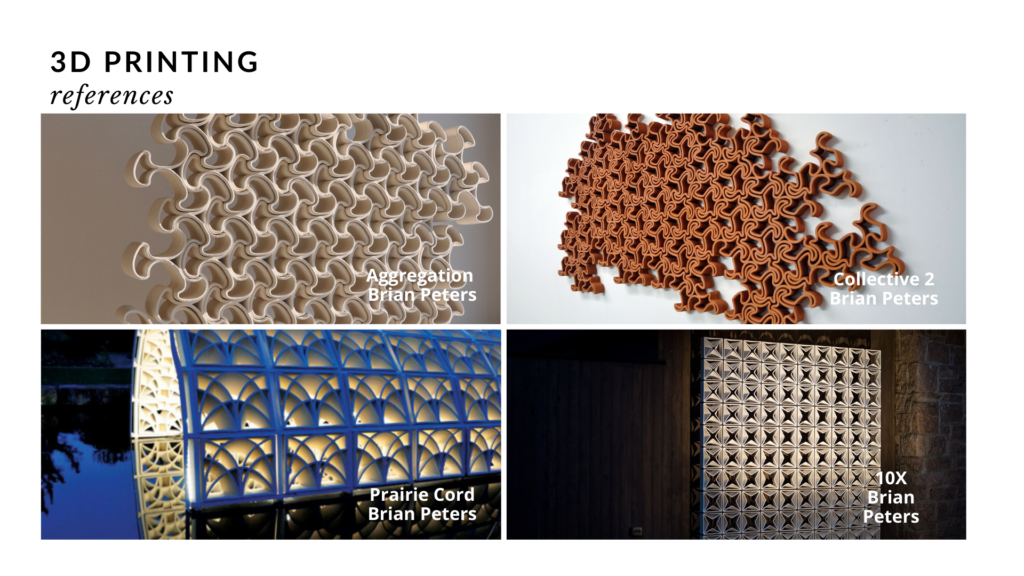
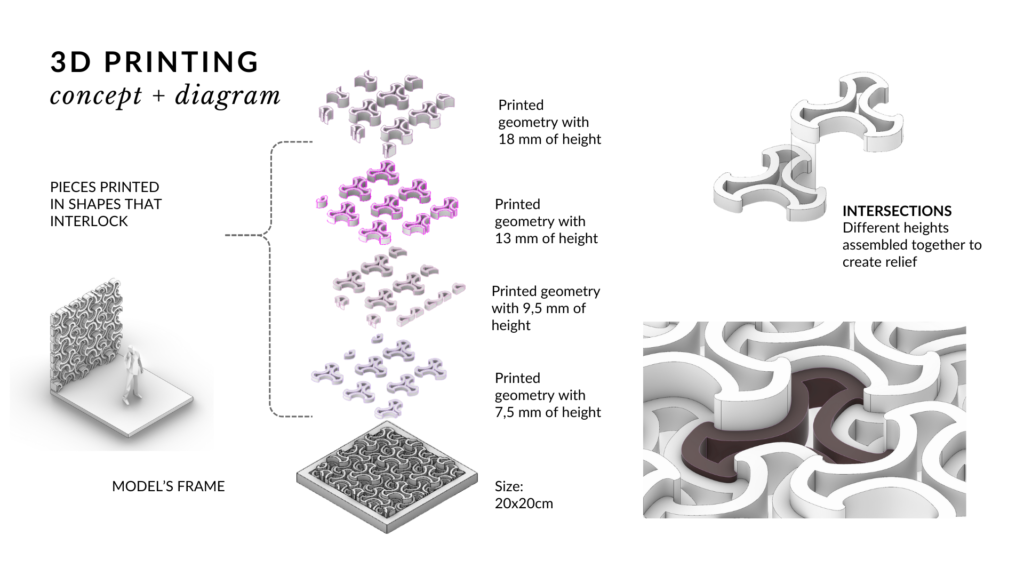
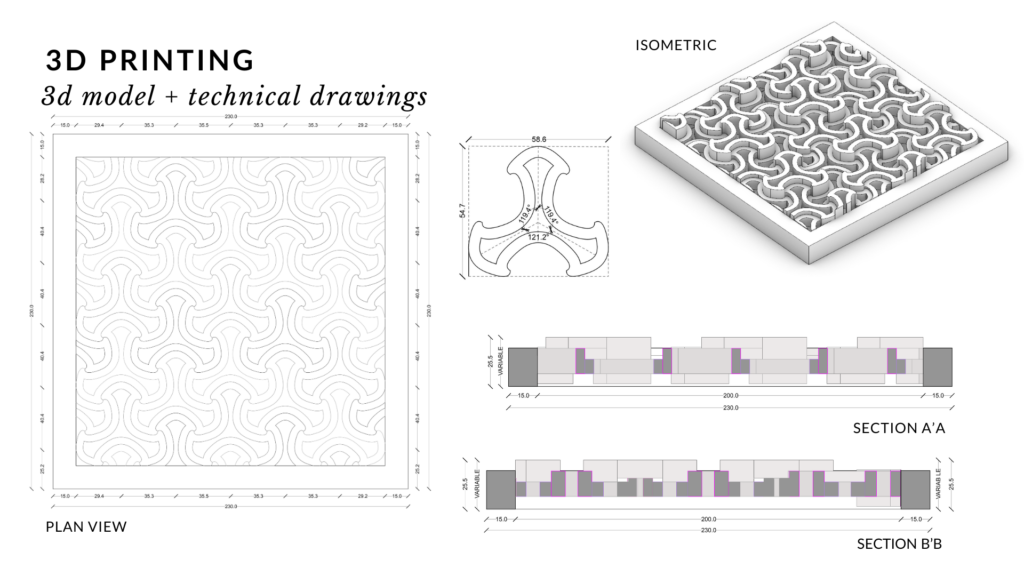
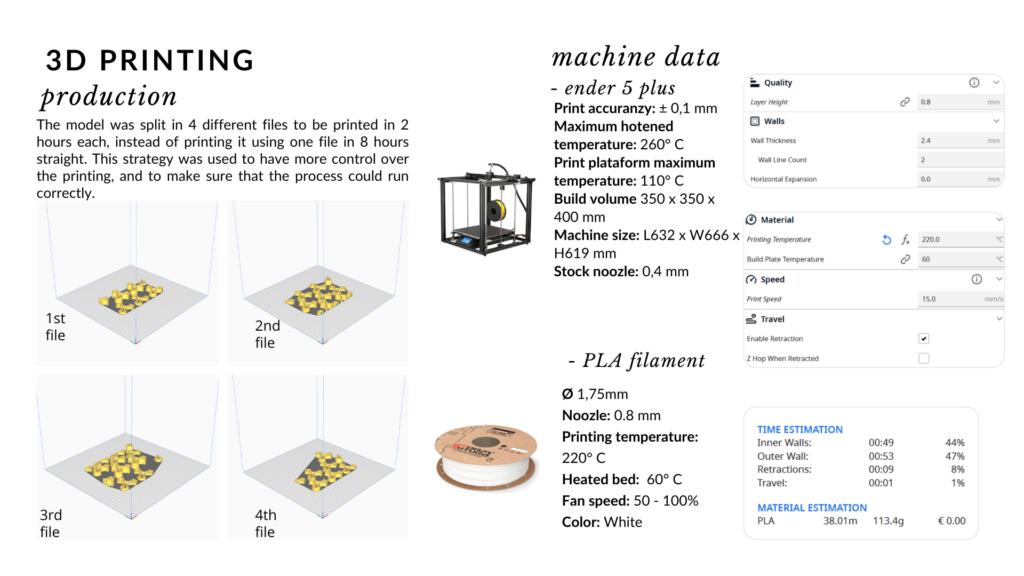
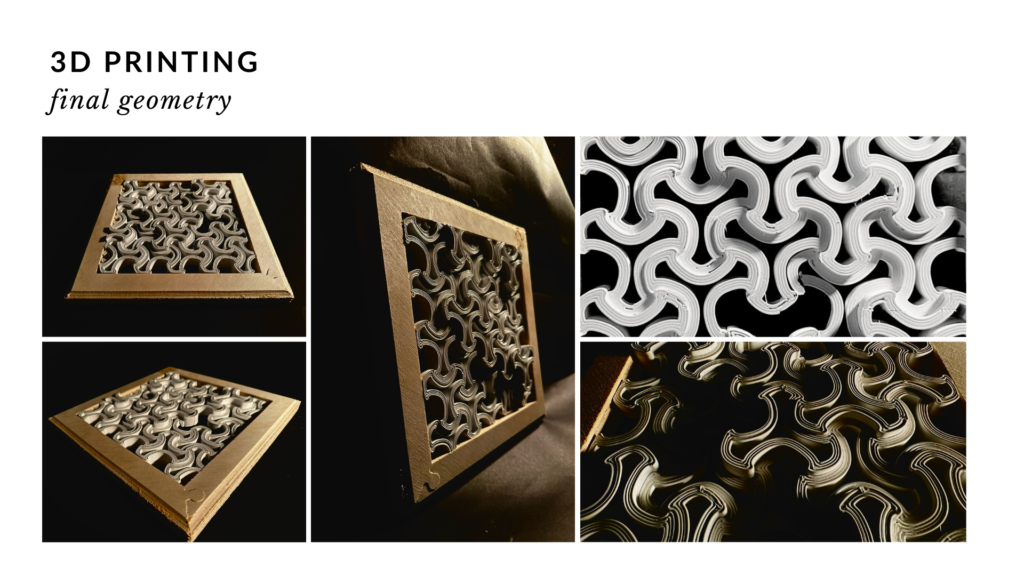
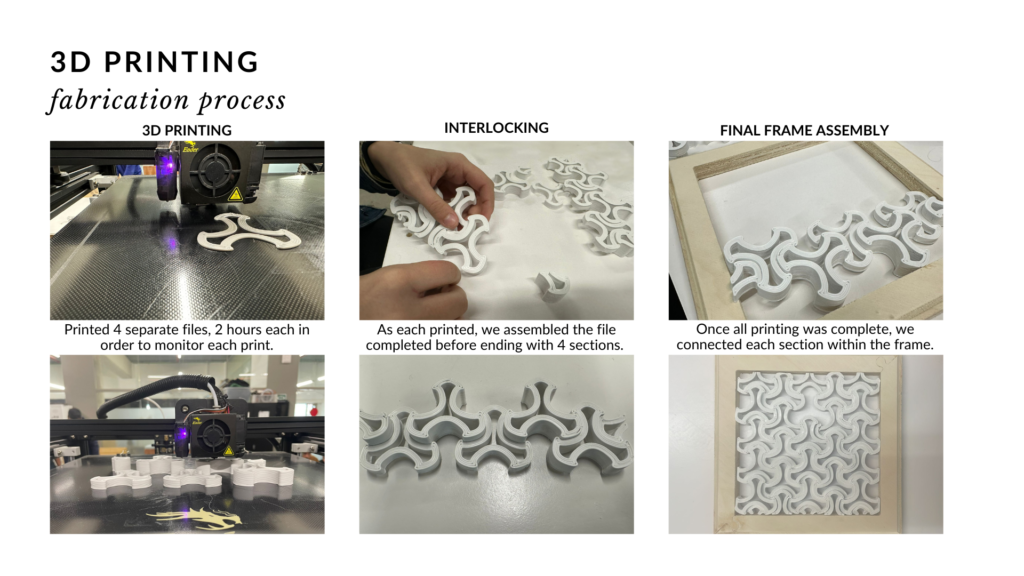
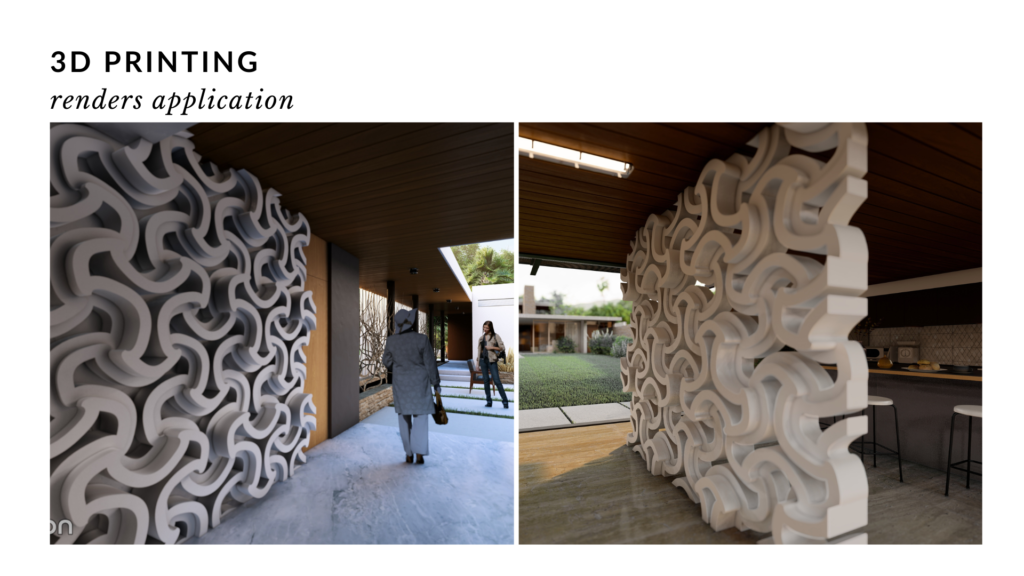

Lastely, with CNC Milling, we wanted to continue to utilize the dynamism of varying thicknesses, so we concluded with a parametric stepped pixel design inspired in part by the Regal Shoes technique by Nuru Karim. We experimented with scale as the stepped, right angle nature of the geometry would be compromised by the CNC’s round mill bit parameters, but we found that the smaller scale made this feature insignificant. For the material we chose plywood to highlight each layer of the material that was exposed with each step in the CNC.
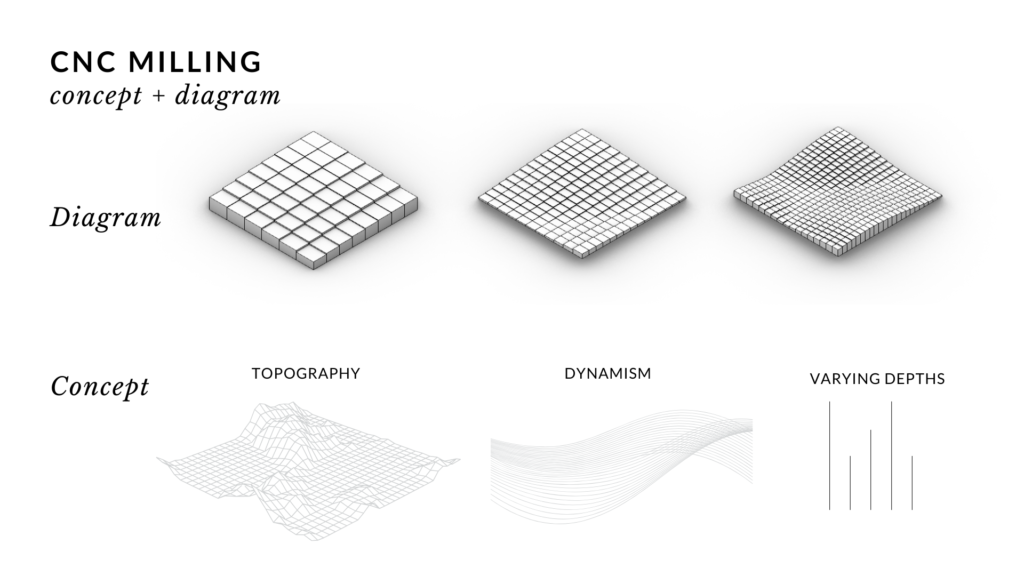
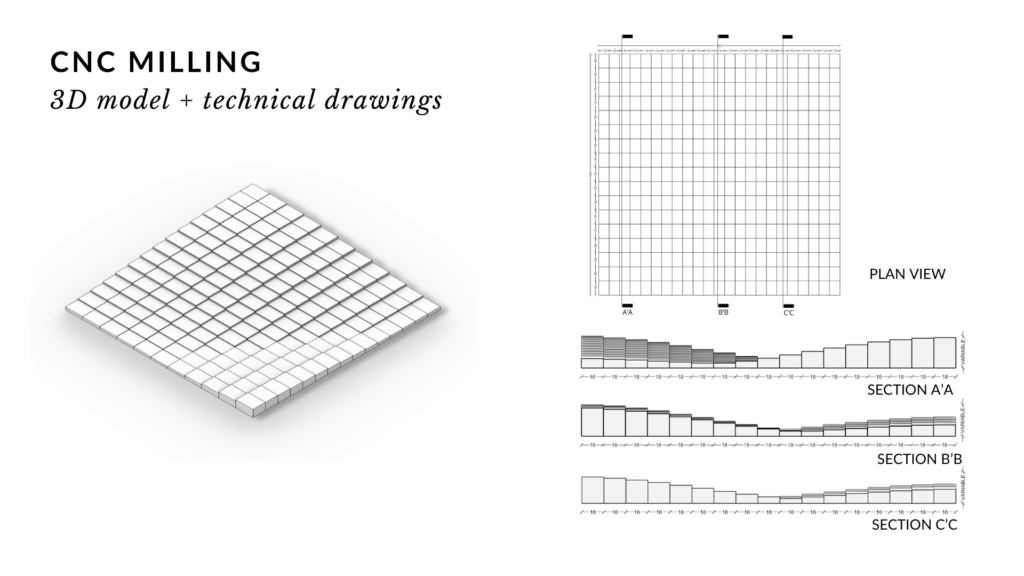
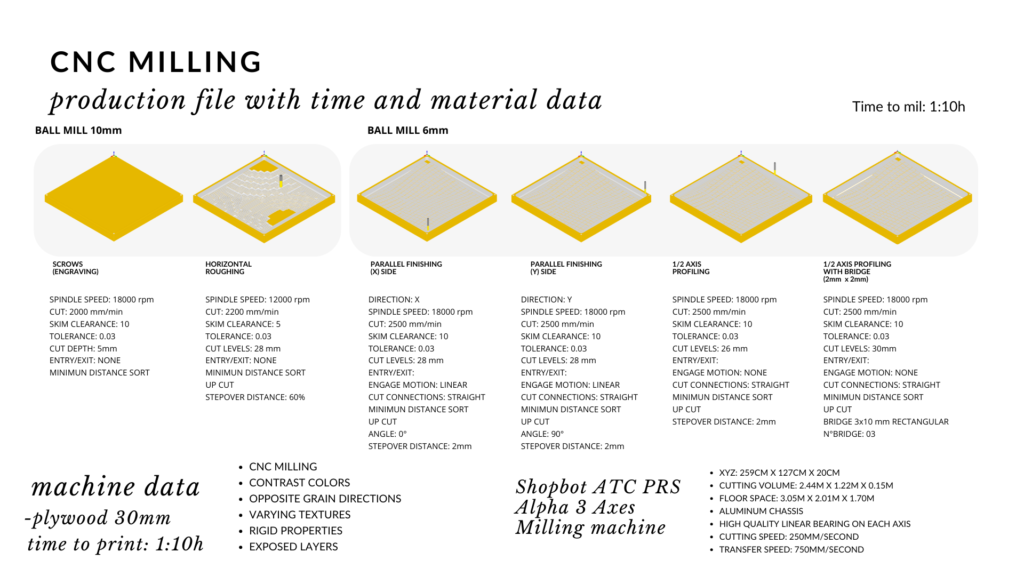
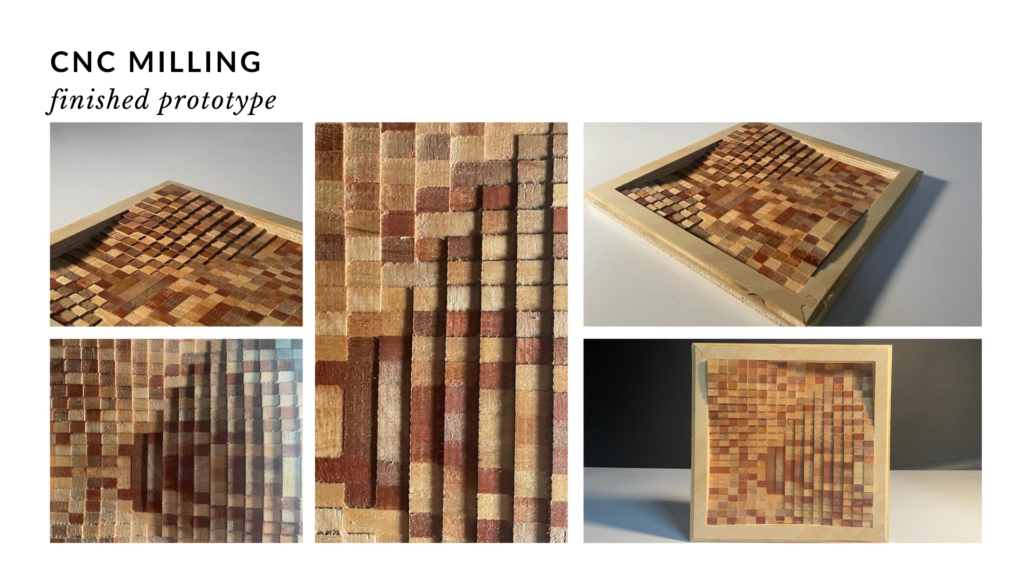

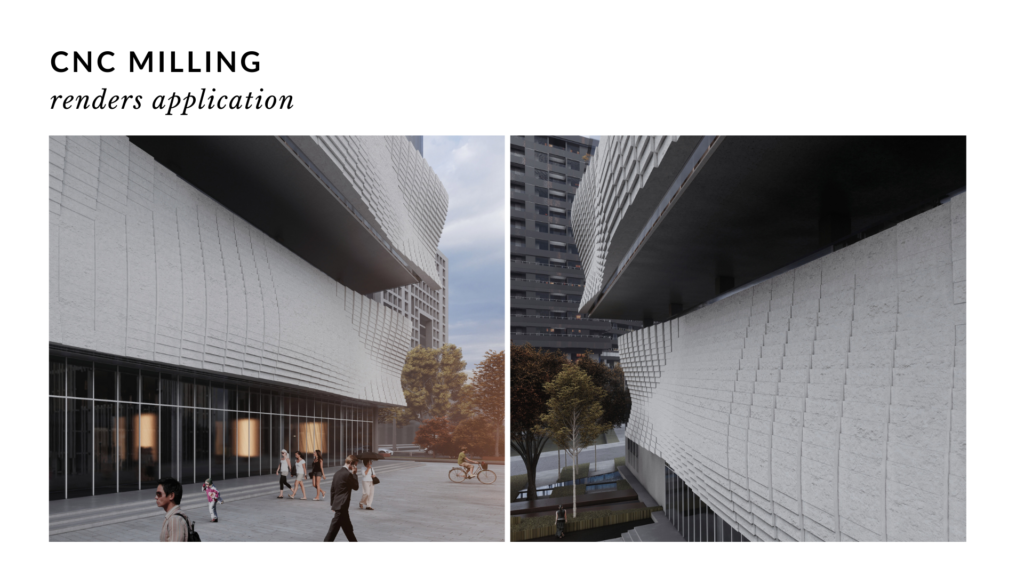
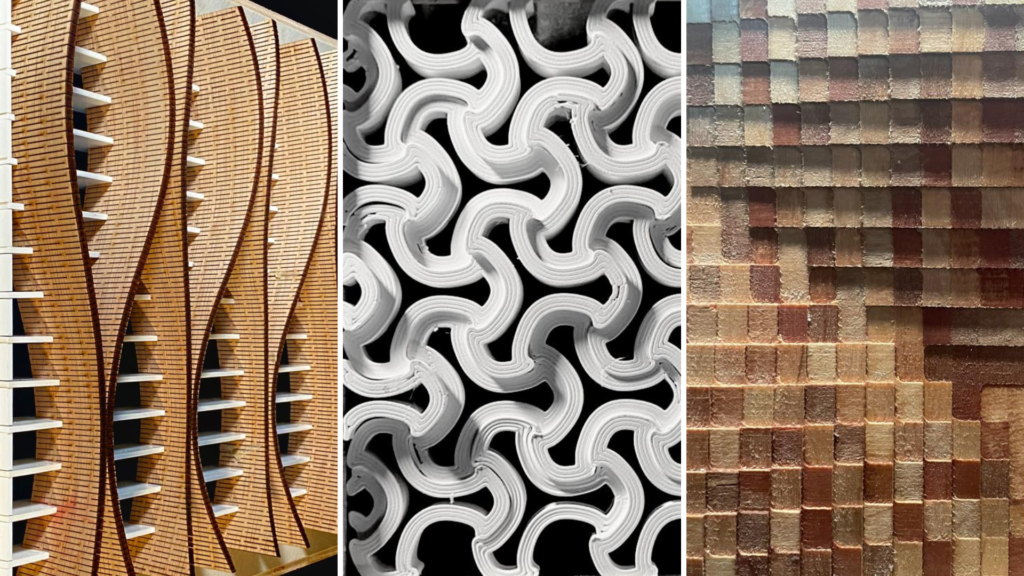