Team member(s): Govind Chithrath, Santosh Shenbagamoorthy, Krystyn Kontos , Aleksandra Kraeva and Lauren Deming
Modified by Lauren Deming on November 24, 2024
Ultimately, the goal is to develop more efficient means for harvesting and utilizing low-carbon footprint alternatives for construction.
Course Objective
- Learn the fundamentals of weaving principles and techniques.
- Create a method for addressing the varied properties of natural materials.
- Model the behavior and characteristics of natural materials.
- Convert traditional weaving methods and material inconsistencies into an automated digital fabrication process.
- Incorporate material properties and manufacturing constraints into the design.
- Apply assembly principles and a component-based approach.
Project Abstract
Autonomous Weaving with Raw Materials explores the intersection between weaving automation and the use of raw materials. After analyzing the tensile and elastic properties of various for tensile strength, durability, and availability, Javier Fuentes Quijano equips each group with willow reeds, theoretical inspiration, Grasshopper / C# code template, and physical parameters for developing unique inter-connecting building components. By combining the variability of a raw material to the precision of robotic automation, each group learns the limitations and advantages in each.
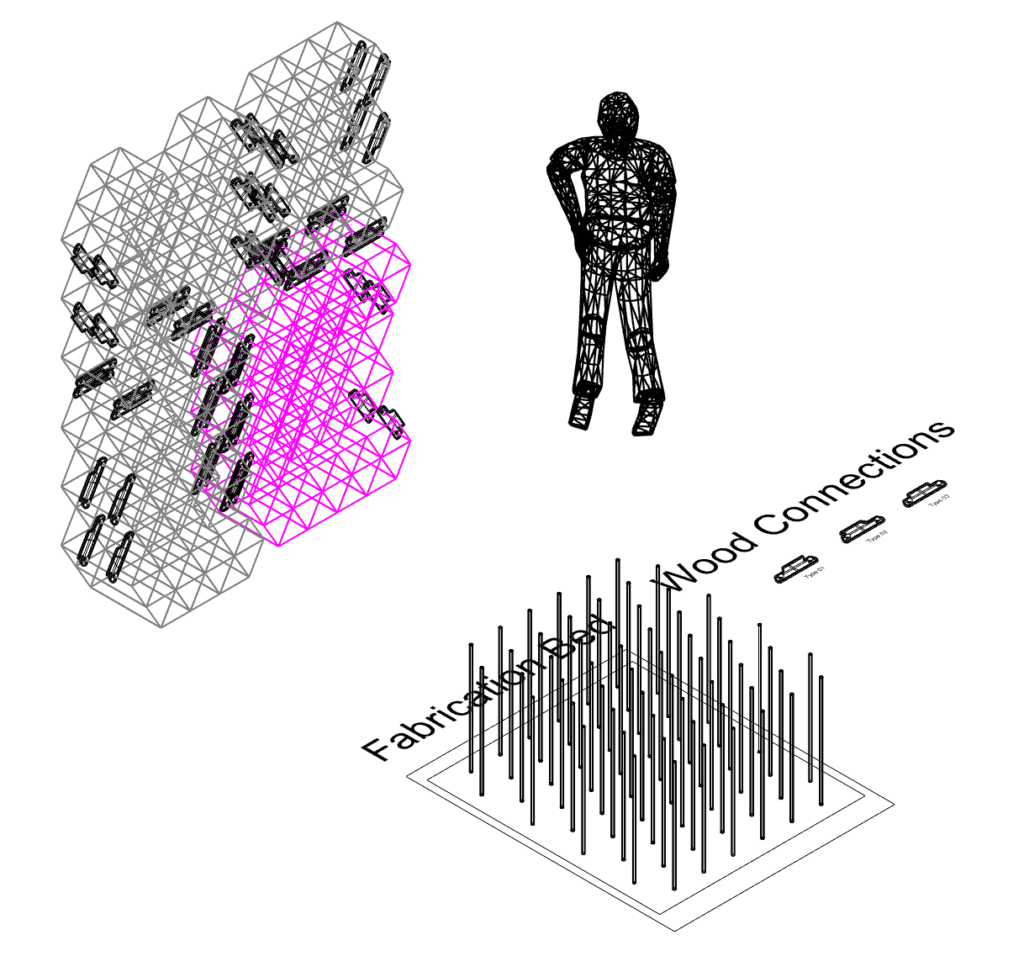
Concept
Given the scale and placement of our designated module in the four-module assembly, our team sought to furnish a building module that could structurally support the weight of adjacent modules. Strong equilateral joints spread evenly in a triangular truss to ensure resistance against various loads and forces. Strategic elimination of dense, redundant reed members could provide efficient use of the natural resource, lighten weight (for efficient transport), and facilitate a safer and perhaps re-usable building module.
With respect for the natural materials and organic aesthetic, our group borrowed geometric inspiration from natural patterns found in nature – the hexagon.
Process
Design
Within the confines of the loom-like fabrication bed, a series of vertical pegs, arranged in a triangular grid, provided the joints around which the willow weeds would bend and weave and drive the geometry. Every three layers create a hexagonal grid pattern unique to the ones above and below.
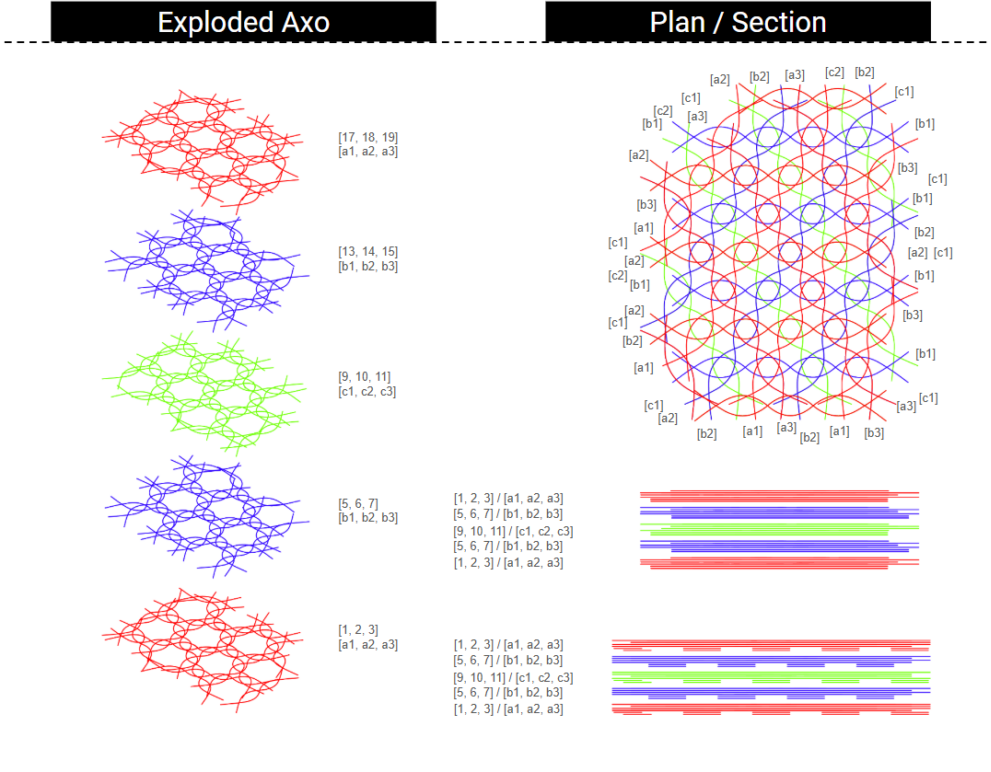
While this pattern ultimately disappears into the repetitive pattern of all layers merged, it yields a more efficient, lightweight version of a comparable aesthetic.
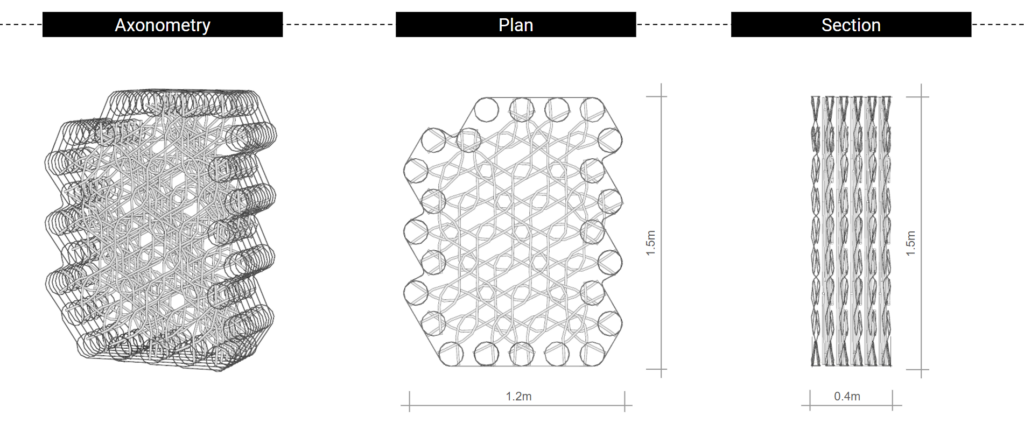
Simulation
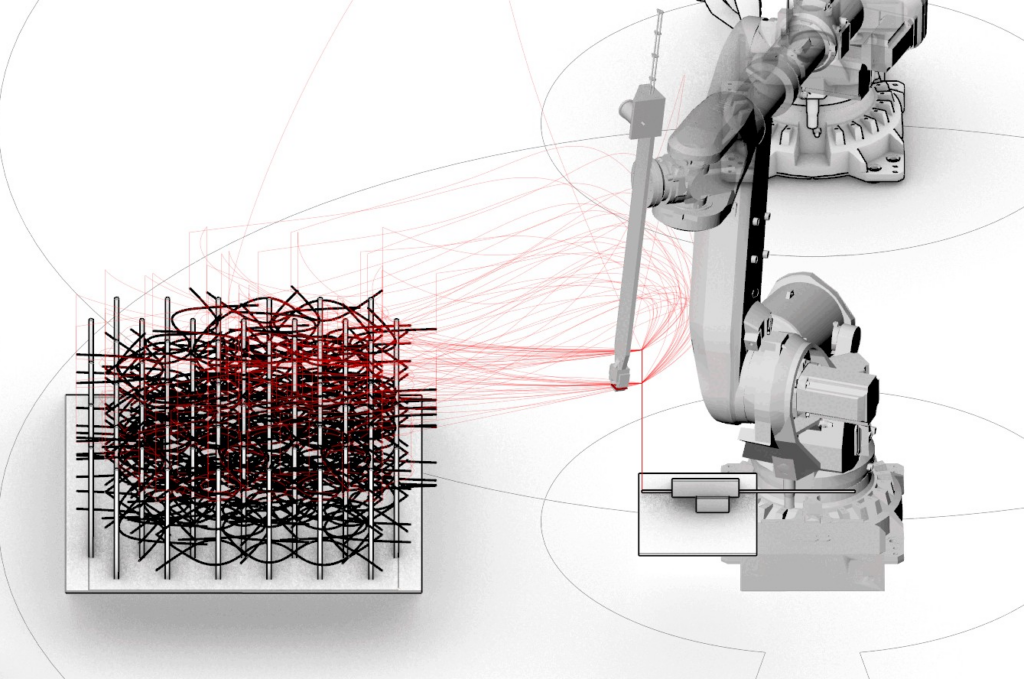
Fabrication
Prior to the willows being restored to their natural straight form for lasting construction, the willow reeds are steamed to ensure malleability during fabrication, while this adds to the energy used to complete the process, passive options (construction site climate and reed age) may create more conducive conditions, eliminating need for this process.
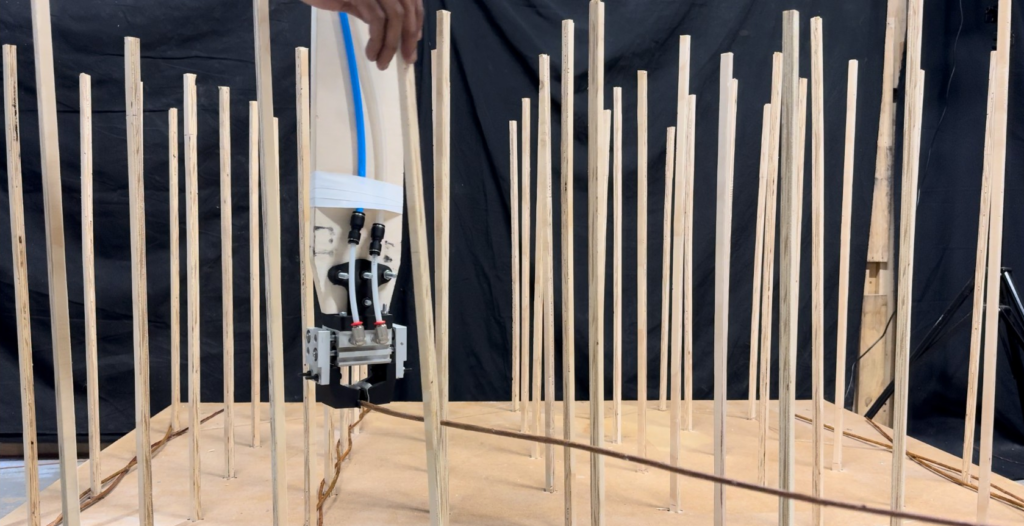
From simulation to implementation, collisions were mitigated by creating a wider toolpath allowing the robotic end effector to navigate around the vertical prongs of the fabrication bed while weaving each willow reeds.
Results
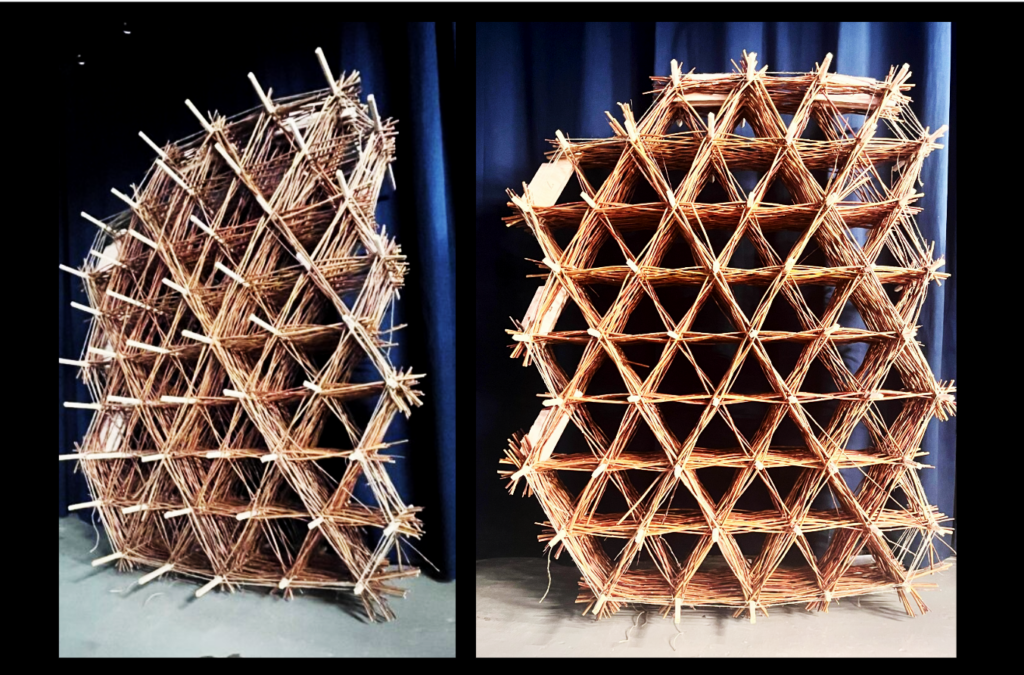
Potential Applications
Due to the strong, lightweight, and porous nature, the building component may have alternative applications for a building facade cladding system.
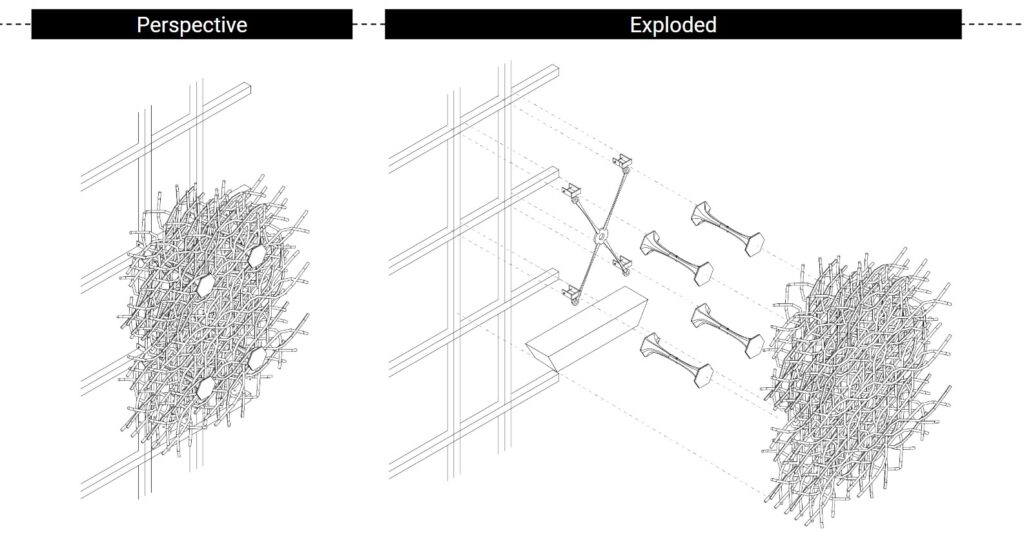
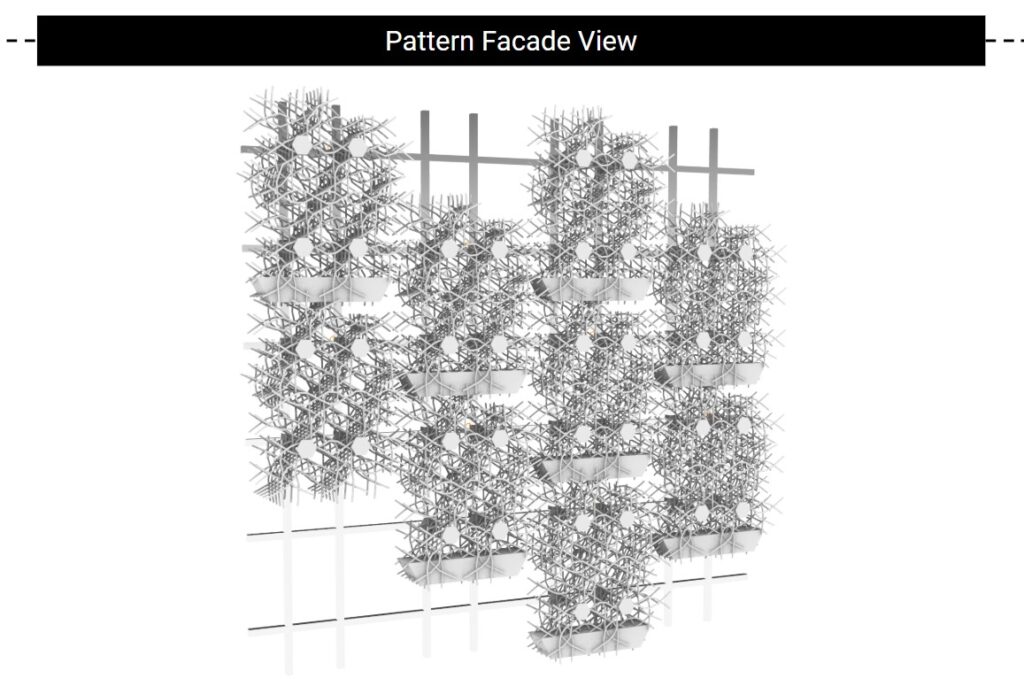
In addition to the visual and biophilic benefits, this cladding can feature natural air purification, and humidification. The cavities provide opportunities for cultivating both flora and fauna for human commensalism.
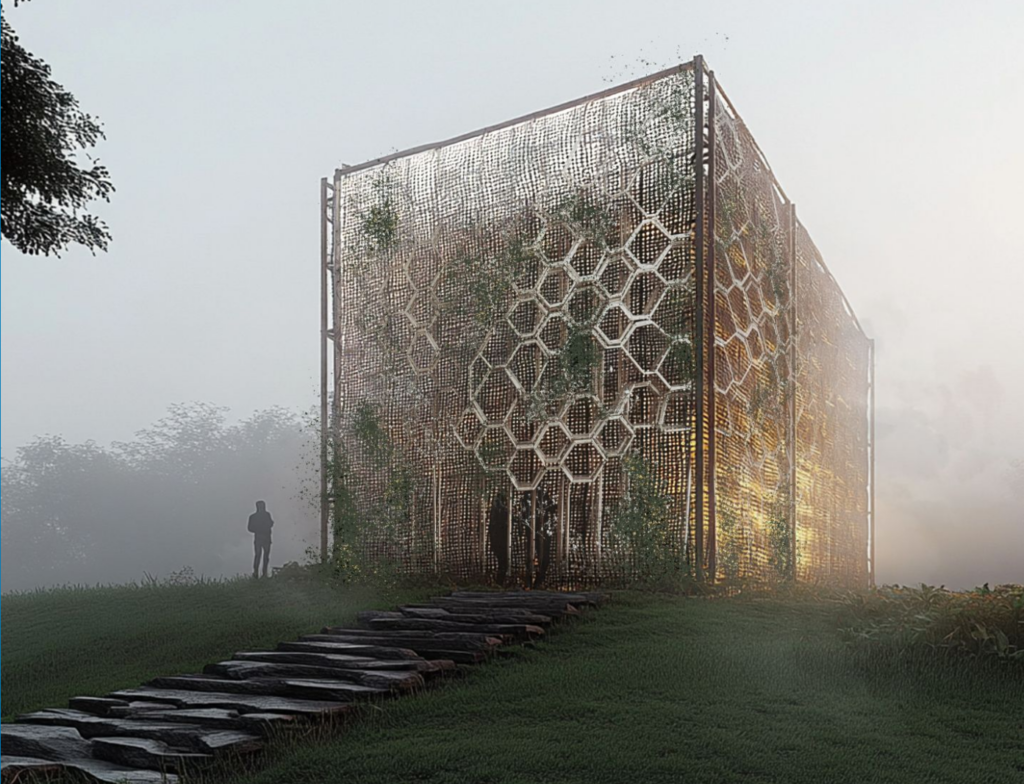
References
- InterTwig (2022). Das Fest – Karlsruhe.
- Digital Wicker (2022). Karlsruhe – Department of Architecture – Karlsruhe Institute of Techology.
- RecodeWicker. Pop-Up Campus (2022). Aachen – Pop-Up Campus.
- Architekturgeometrie, Digital Design III and Textile Steel (2022). Karlsruhe – Department of
- Architecture – Karlsruhe Institute of Techology.
- ReGrow Willow (2023). BUGA23 (Bundesgartenschau 2023) – Mannheim.
- Gil Pérez M, Guo Y, Knippers J (2022) Integrative material and structural design methods for natural fibres filament-wound composite structures: the Liv-MatS pavilion. Mater Des 217:110624
- Dawod, Mohamed & Deetman, Arjen & Akbar, Zuardin & Heise, Jannis & Böhm, Stefan &
- Klussmann, Heike & Eversmann, Philipp. (2020). Continuous Timber Fibre Placement: Towards the
- Design and Robotic Fabrication of High-Resolution Timber Structures. 460-473.