Introduction
In the face of the growing demand for sustainable construction, the integration of renewable materials with advanced fabrication techniques is essential for creating adaptable and efficient structures. Our team developed Terraweave, a project that combines willow and earth to create hybrid building components. By leveraging the natural properties of willow for flexibility and earth for strength, we explore how robotic weaving and additive manufacturing can enhance the material’s performance while maintaining environmental integrity.

We asked, what if we could combine robotic processes with renewable materials to create adaptable, efficient, and ecological construction methods? Could robotics be more than speed and automation — could it help us shape materials in ways that respect and enhance their natural properties?

Terra Weave is our answer — this is a system that integrates robotic fabrication with renewable resources, specifically willow and earth. Our research stands on three pillars: natural composites, digital design and fabrication. We looked closely at the anatomical behaviour of materials like willow and earth, and how their natural properties could be leveraged through robotic precision.

Willow offers unique advantages. It’s renewable, flexible, lightweight, and can be harvested yearly. Its tensile properties allow it to be woven and bent without breaking, making it perfect for forming curved geometries and distributing loads when integrated into a hybrid structure.
Earth complements willow beautifully – It is locally available, low-impact, and offers excellent compressive strength. When combined, willow manages tension while earth provides weight anchoring, load transfer, and prevents sifting — together improving the system’s structural behaviour.
Material Behaviour
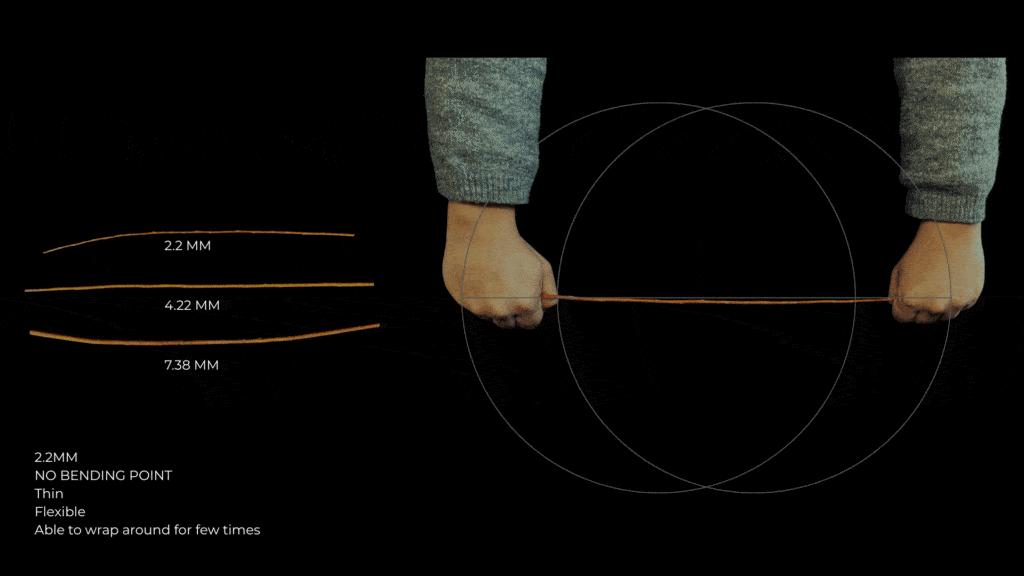
Willow weaving creates a highly adaptable framework. It responds to tension and bending, helping the structure work as a continuous skin without joints. Its geometry enhances load distribution, while the interlocking pattern prevents displacement under stress. Early tests focused on material deflection, breaking points, elasticity, and identifying the threshold where willow and earth could work together.

The system follows a four-phase process: first, weaving the willow; second, scanning the geometry to account for its irregularities and interpreting this data; third, applying additive manufacturing using earth-based mixtures; and finally, re-scanning for evaluation and adjustment.

We began with flat, small-scale prototypes using varying earth-water mixtures, spacing configurations, and nozzle sizes. As we iterated, we scaled up and modified the system earth-to-water ratios, and weaving densities. These adjustments directly affected deflection, material bonding, and load-bearing capacity.

Jigs were essential to controlling geometry. We developed flat jigs, 3D jigs with even and uneven configurations, and experimented with creating non-planar surfaces. CNC technology enabled us to produce precise forms to guide the willow weaving before robotic intervention. The process starts by steaming the willow to increase pliability, then weaving it directly into the jigs.

Afterward, we prepare the system for robotic printing by scanning the woven structure.

Using Grasshopper, we generated robotic toolpaths tailored to each woven geometry. The scan-to-path approach allowed us to adapt the printing process to the natural variability of the handmade weave, making each print specific to its weave’s geometries.

In this phase we tested two main methods: non-planar surface printing and injection printing. Surface printing worked well on flatter geometries, while injection printing was suited for more complex, non-planar forms, where precision and material concentration were key.

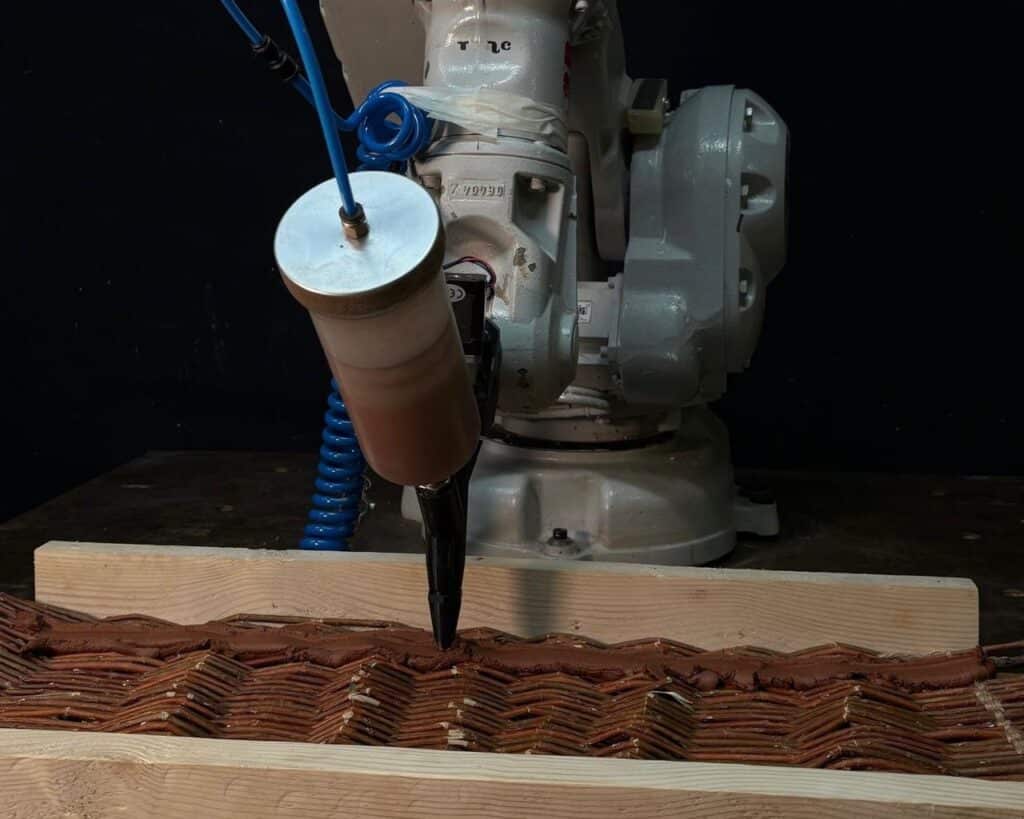
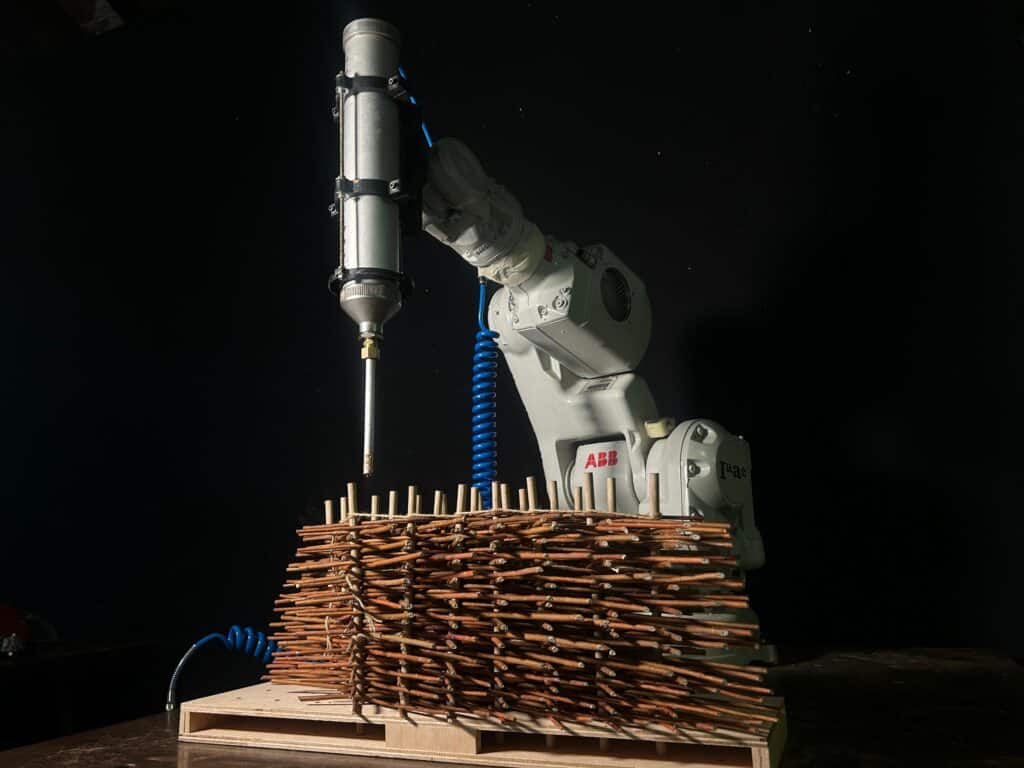
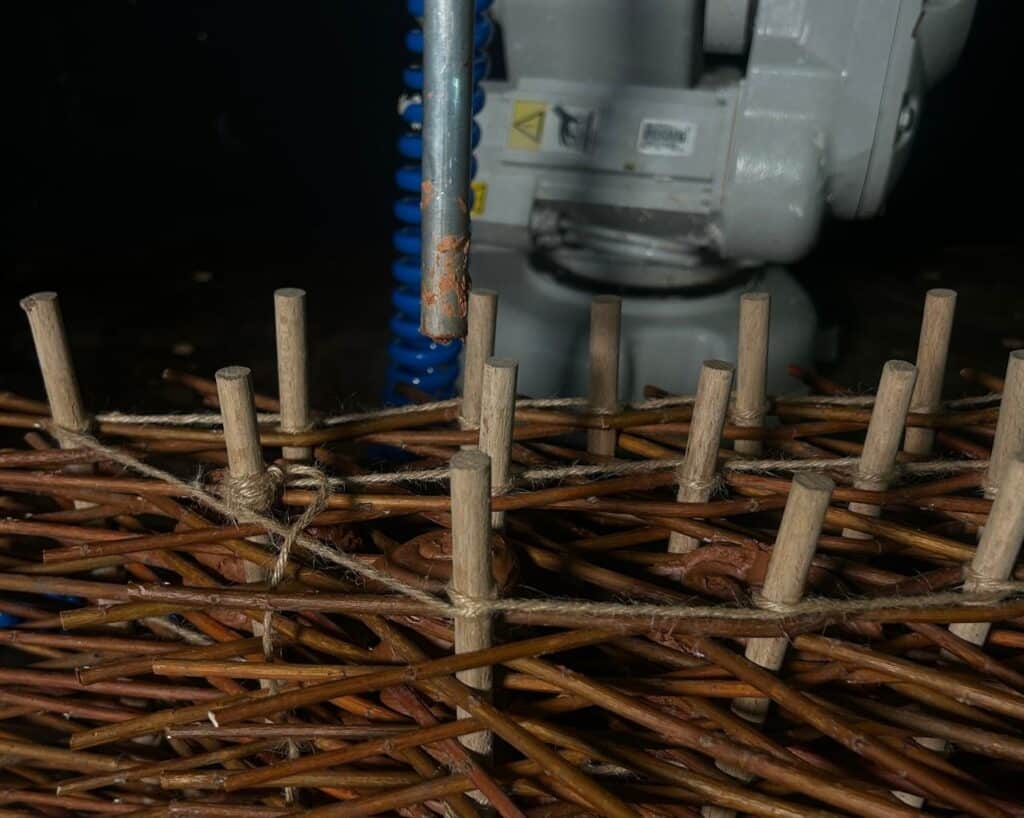
We observed that planar printing was well-suited for façade-like elements, offering flexibility but limited strength with clay. Injection printing performed better under concentrated loads, creating stronger, more structured components, especially in hybrid configurations. In our next tests, we will be testing with earth as opposed to clay, which was a limitation due to our end effector.

We observed that planar printing was well-suited for façade-like elements, offering flexibility but limited strength with clay. Injection printing performed better under concentrated loads, creating stronger, more structured components, especially in hybrid configurations.
The idea for the next term is to merge the best of the learning outputs of these two processes in order to apply it to our hybrid technique, on a larger scale. We plan to integrate dual-robot collaboration: one robot weaving willow, another printing earth. We also aim to develop a custom end-effector optimized for weaving-integrated additive manufacturing, enabling us to test full-scale hybrid structure
