Design References
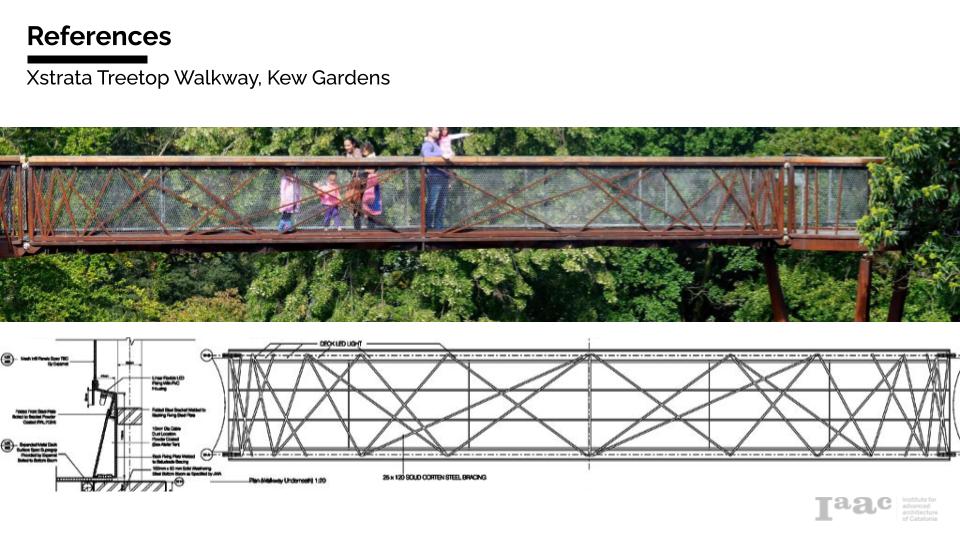
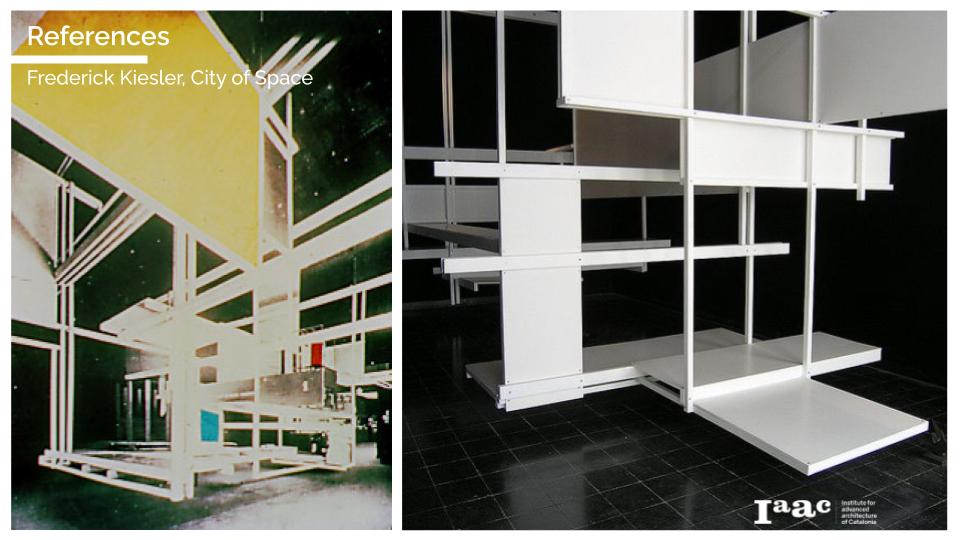
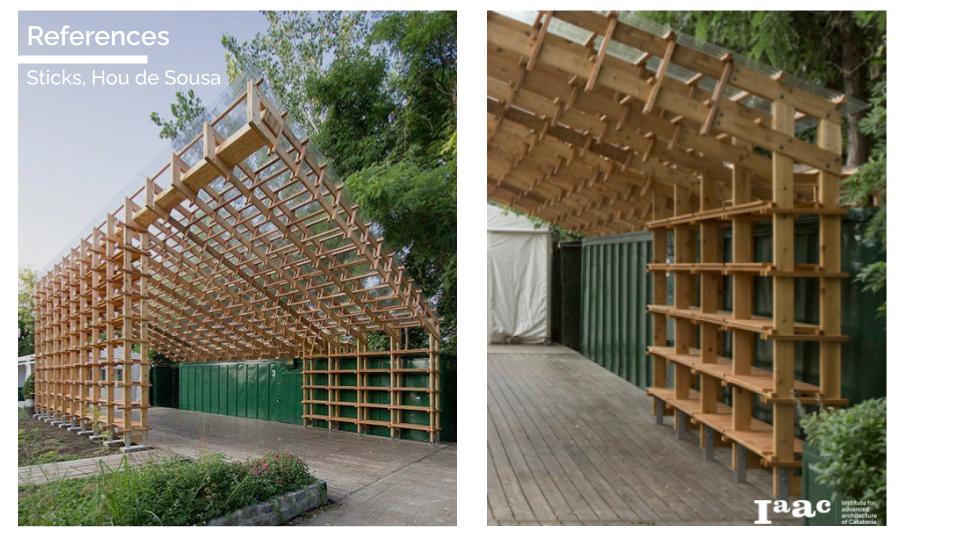
Design
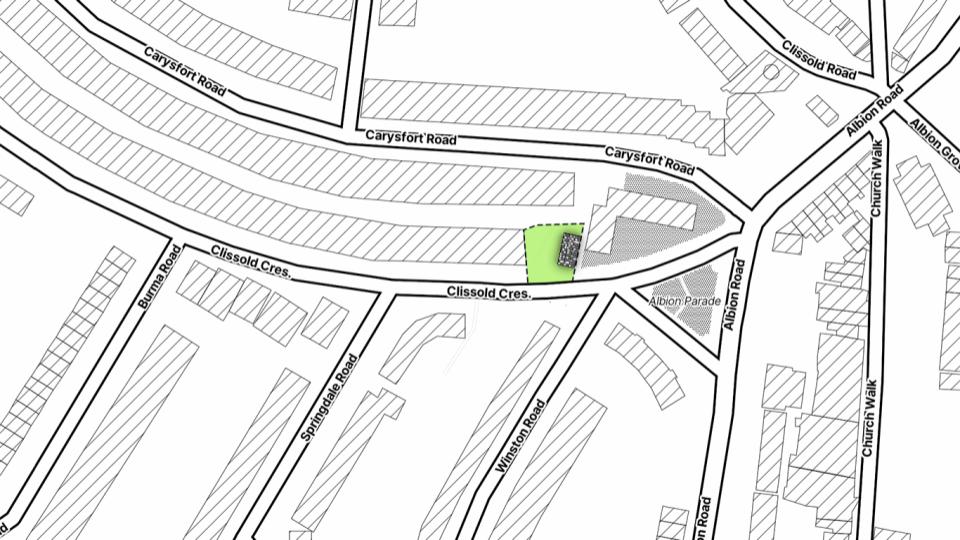
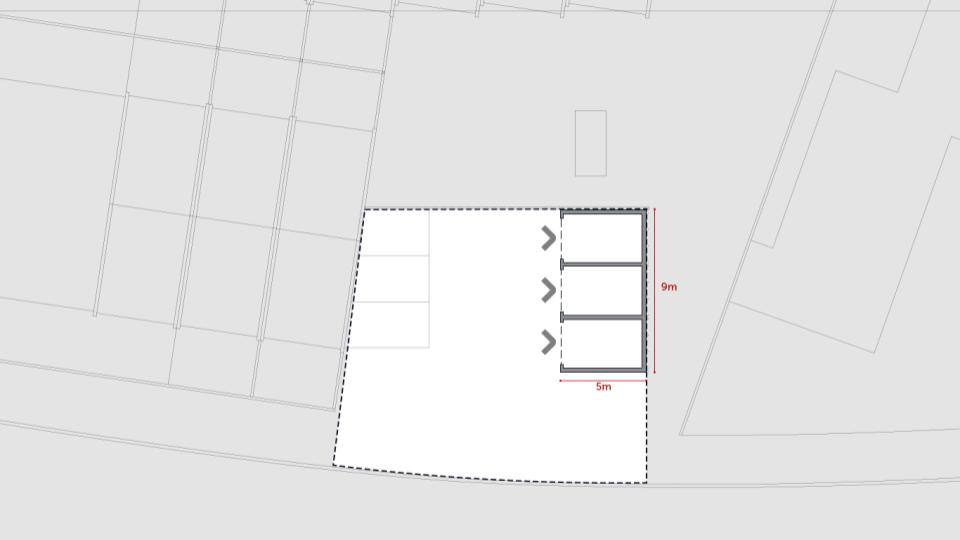
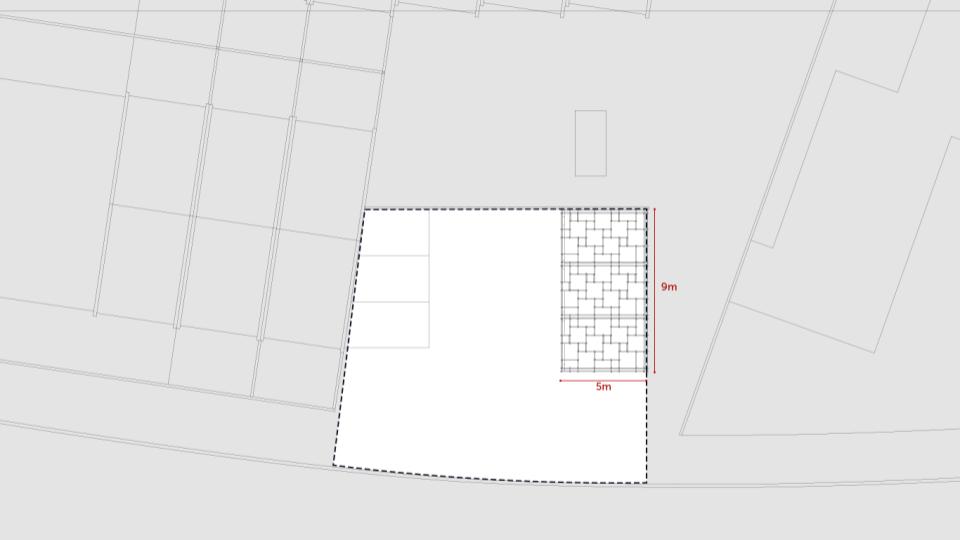
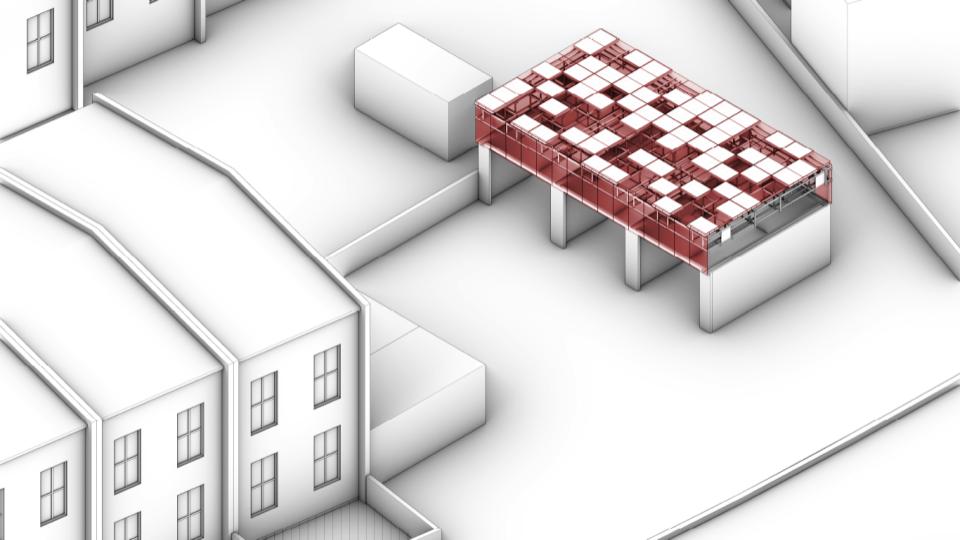
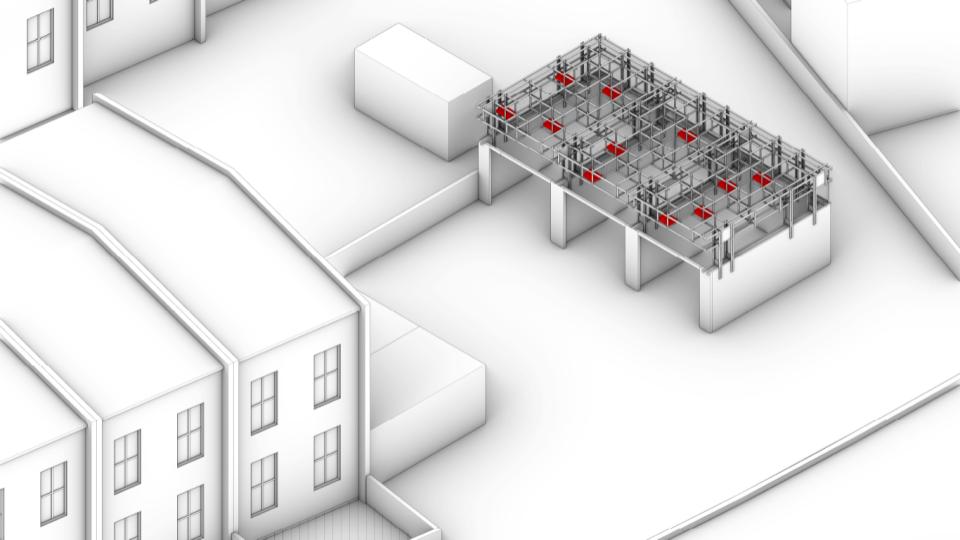
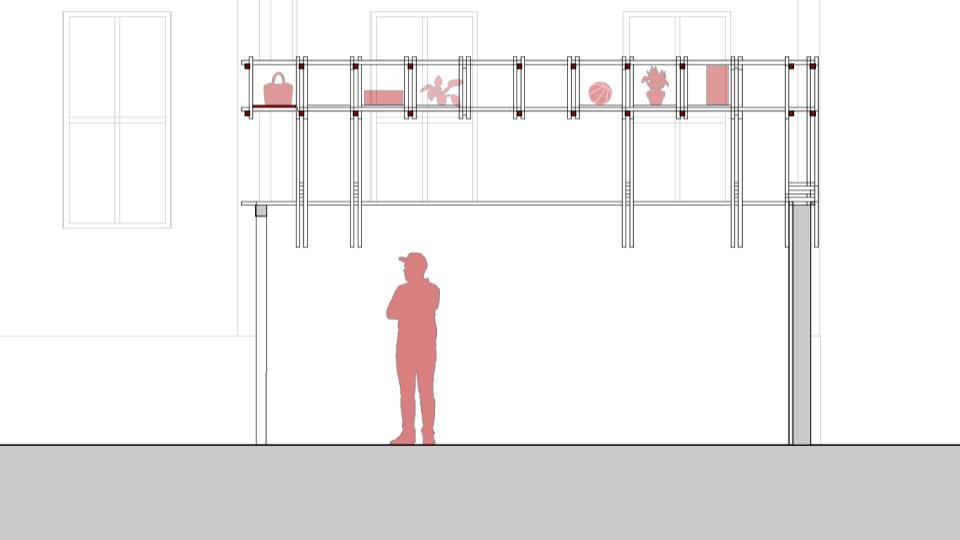
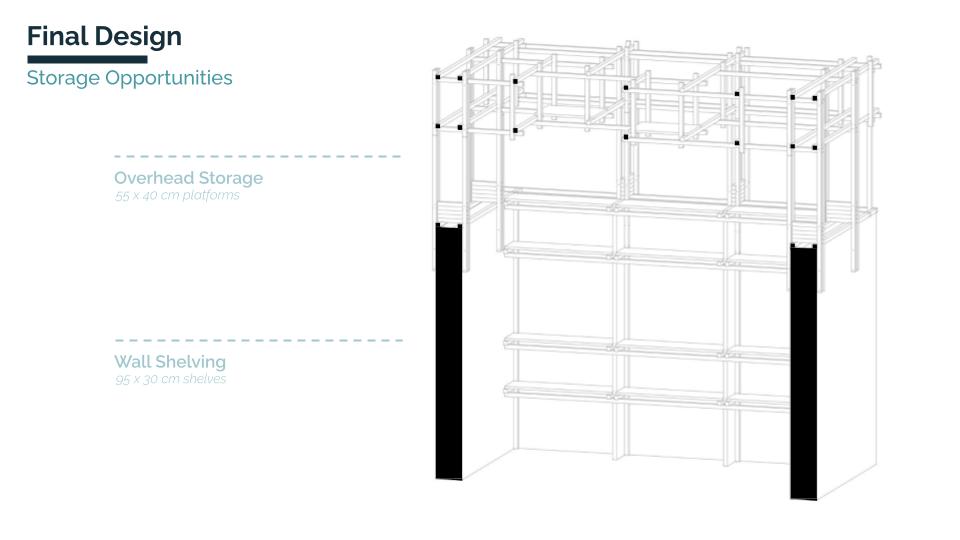
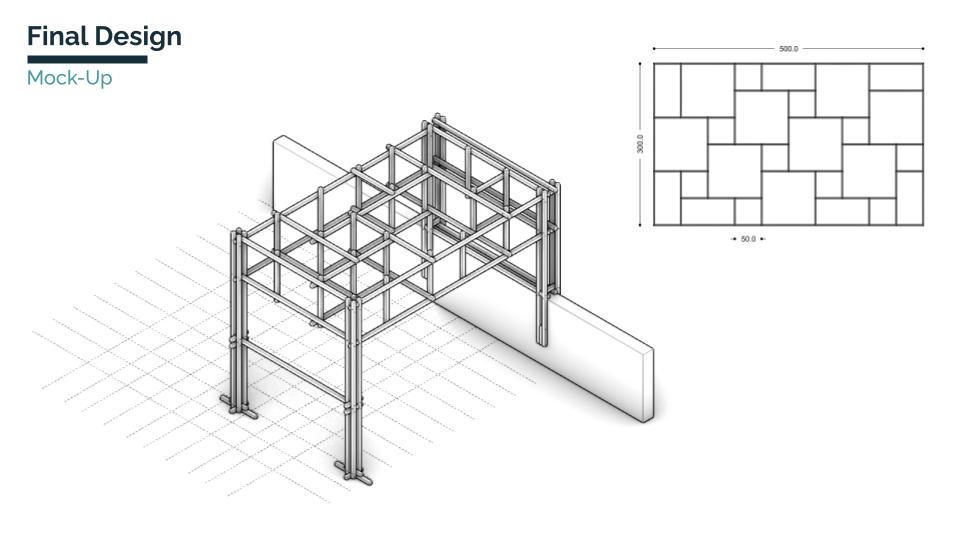
Simulations
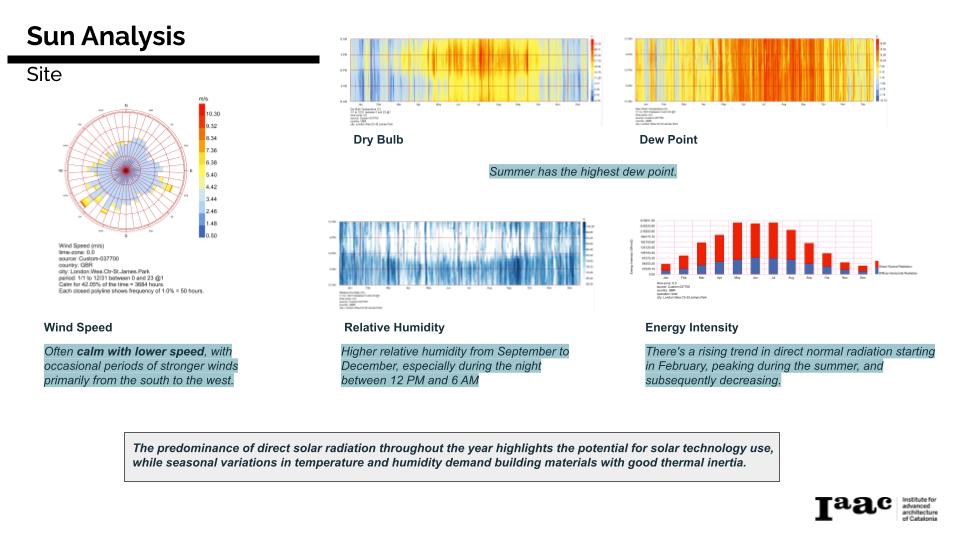
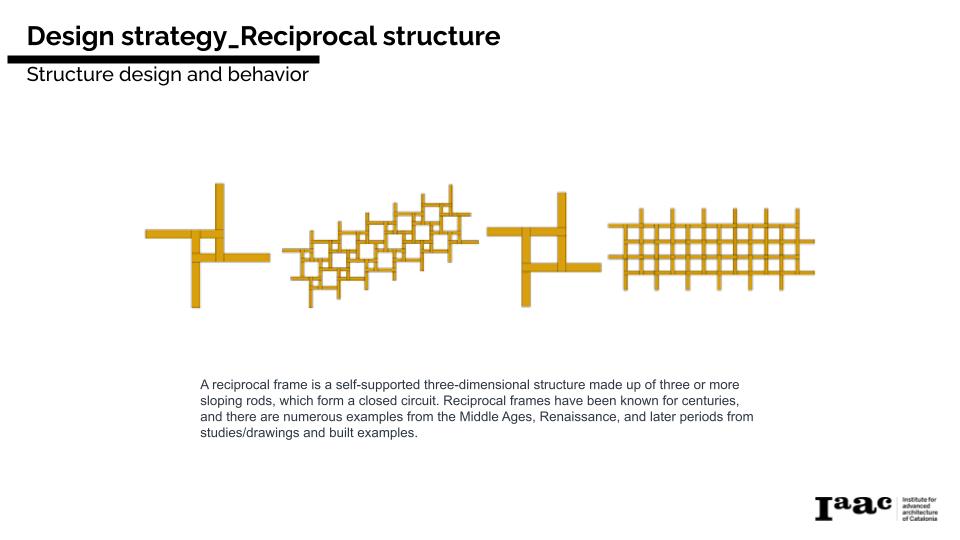
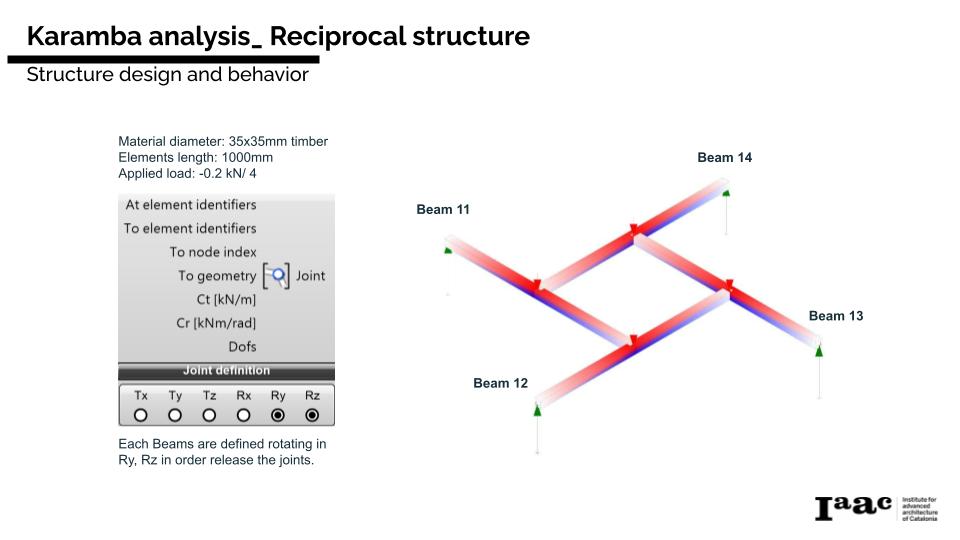
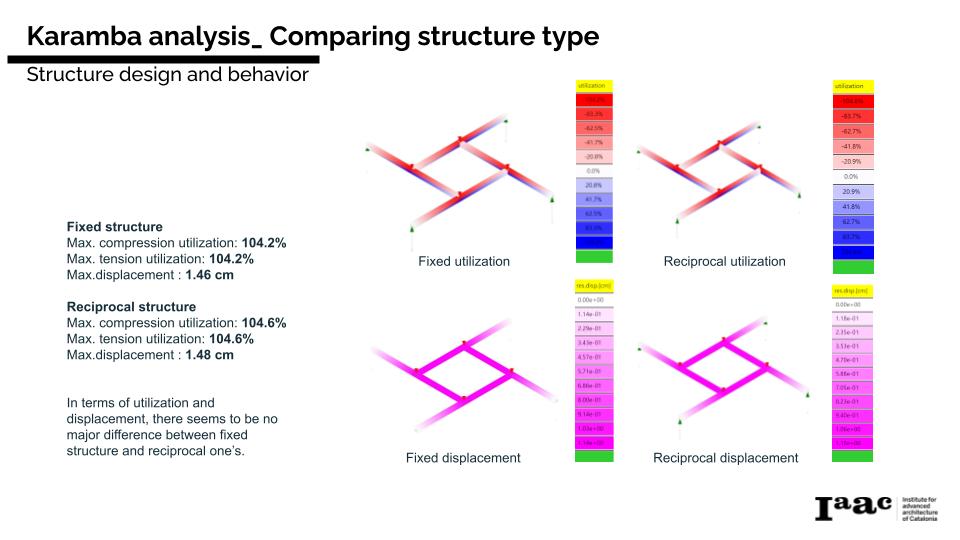
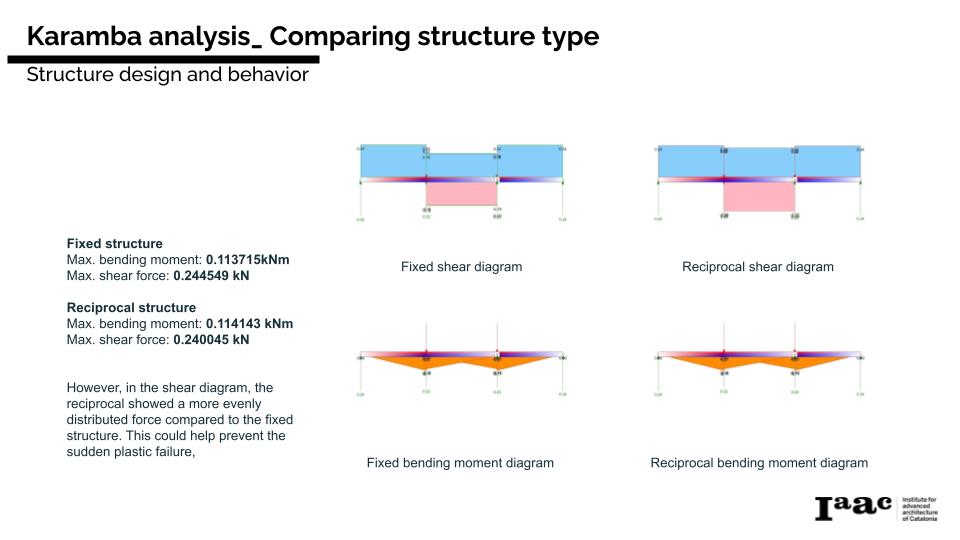
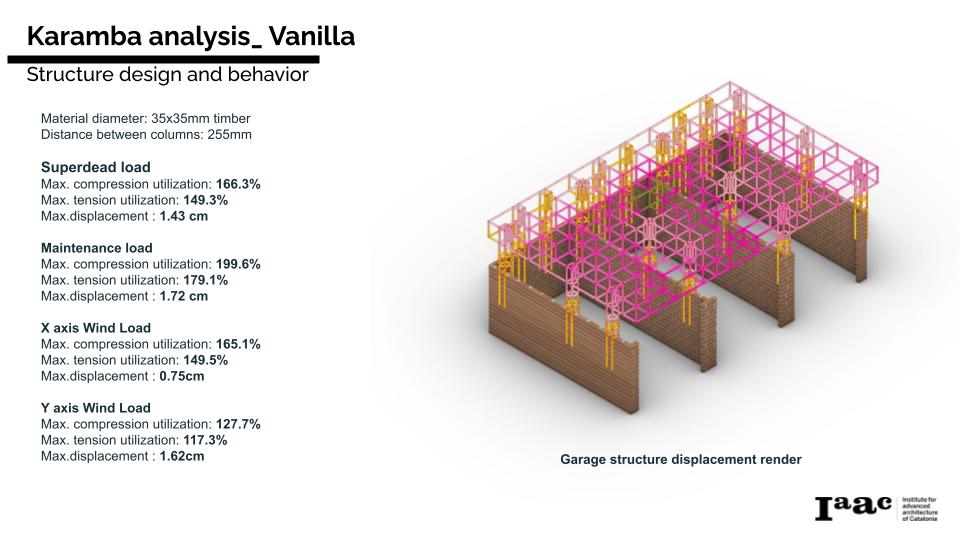
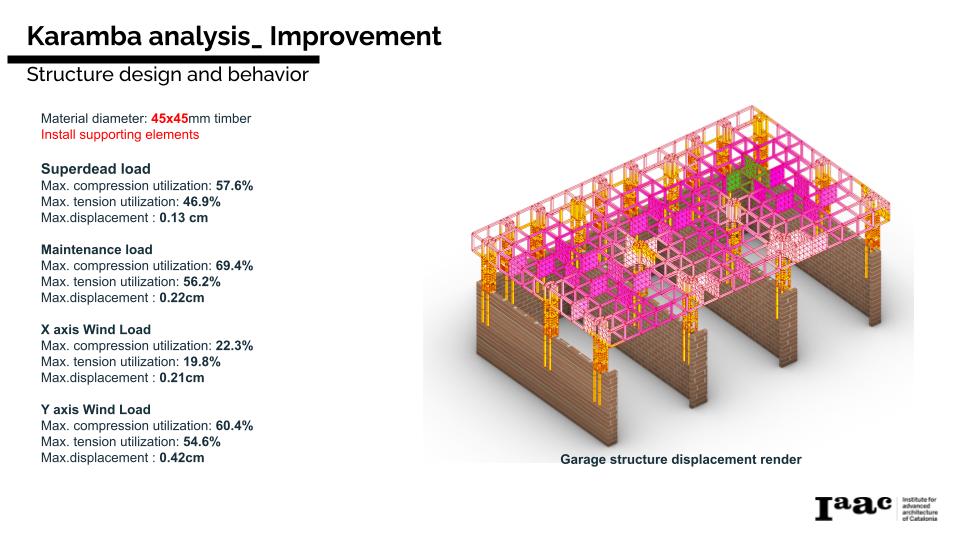
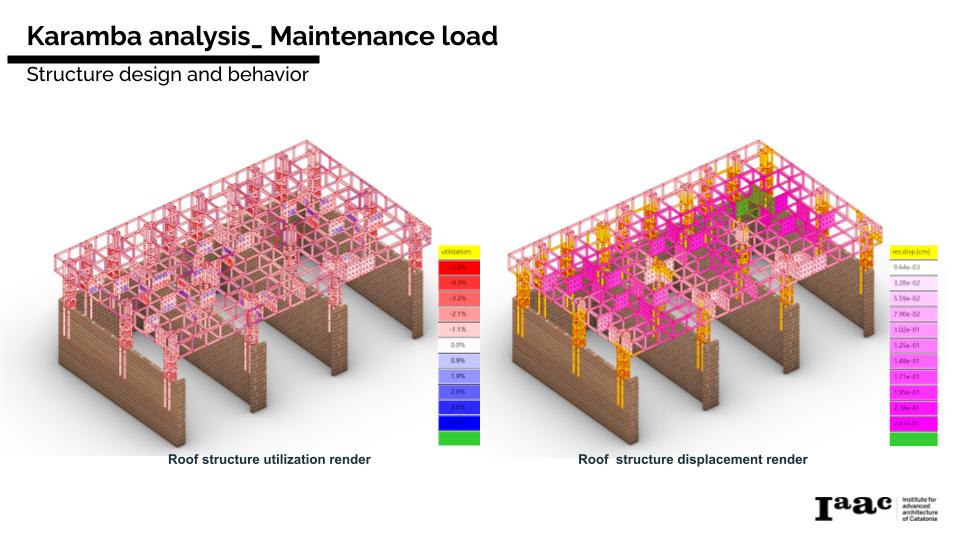
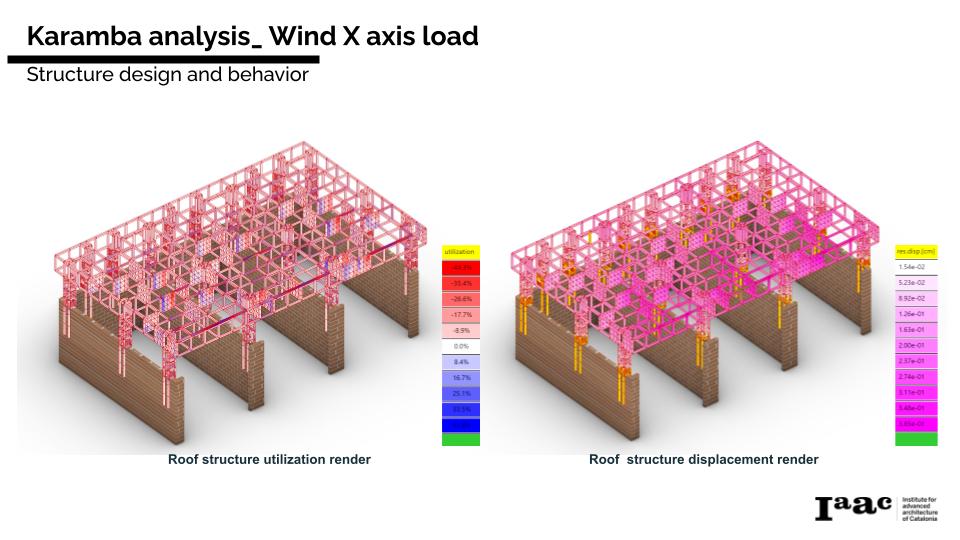

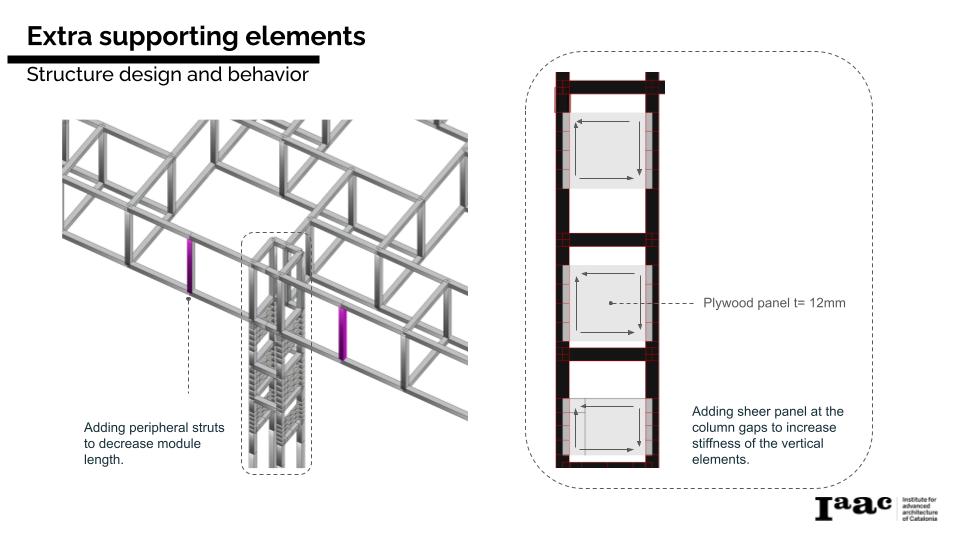
Cladding Composition
The Sandwich Panel is a combination of a top 6mm Polycarbonate Sheet with Dry Insulation and Cork forming our inner layers and to finish it off with a 6mm thk Polycarbonate Sheet at the bottom.
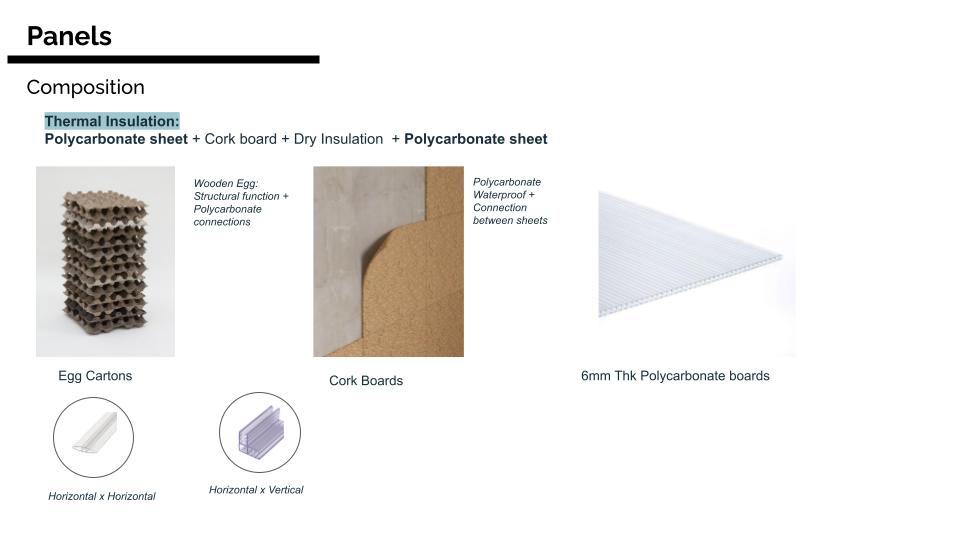
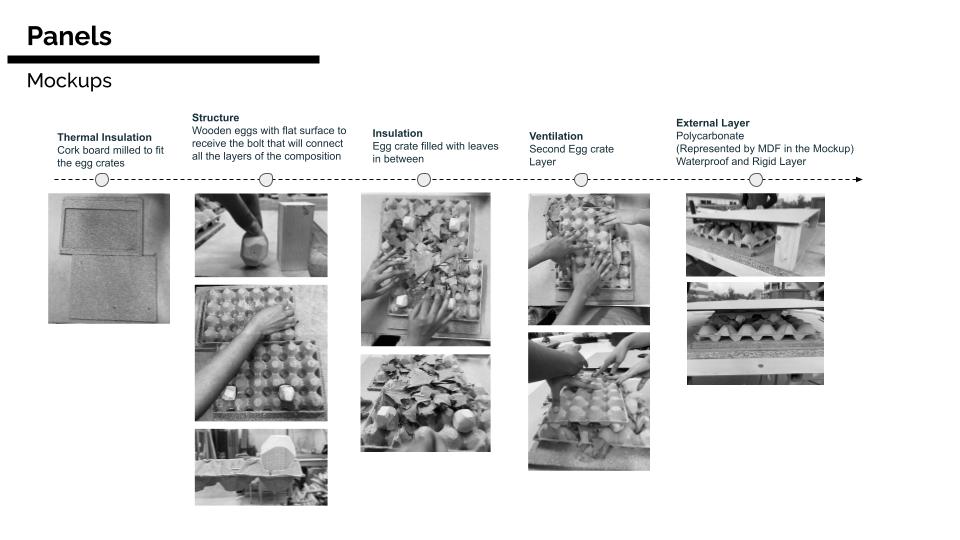
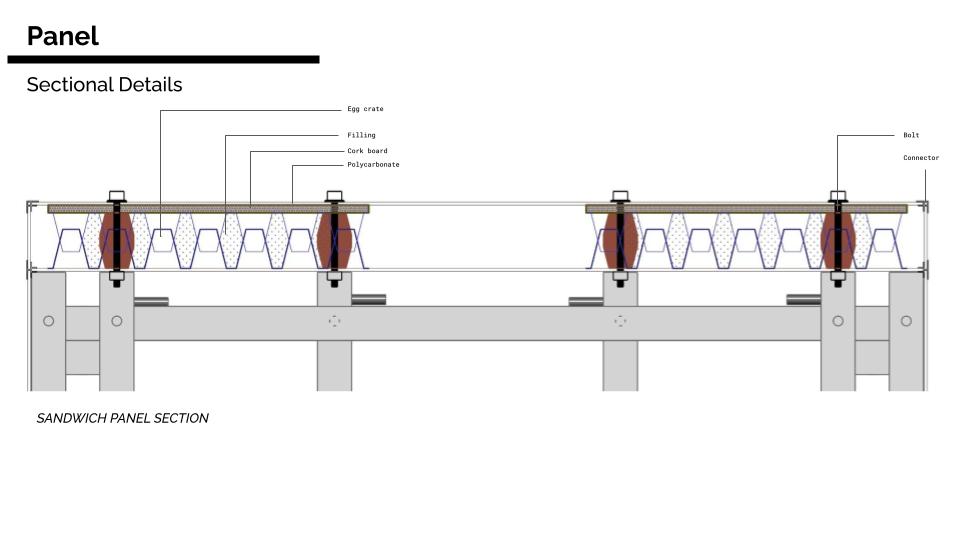
Fabrication Process
Using plywood as a base for dowels, which would serve as lateral support and boundary for the space designated for each wooden slat in the jig, a strategy was developed for drilling holes for dowels and bolts, and cutting according to the required sizes of the pieces needed for the wooden structure composition.
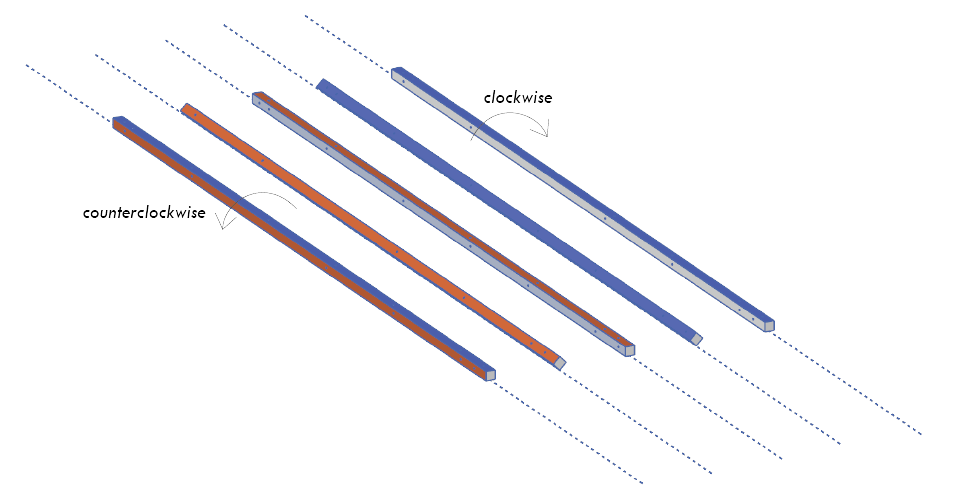
The first face to be crafted was called the “front”. After the necessary drilling and cutting, the wooden slats were rotated clockwise for drilling the second face. Then, the slats return to the “front” face and are rotated counterclockwise for finishing the piece.
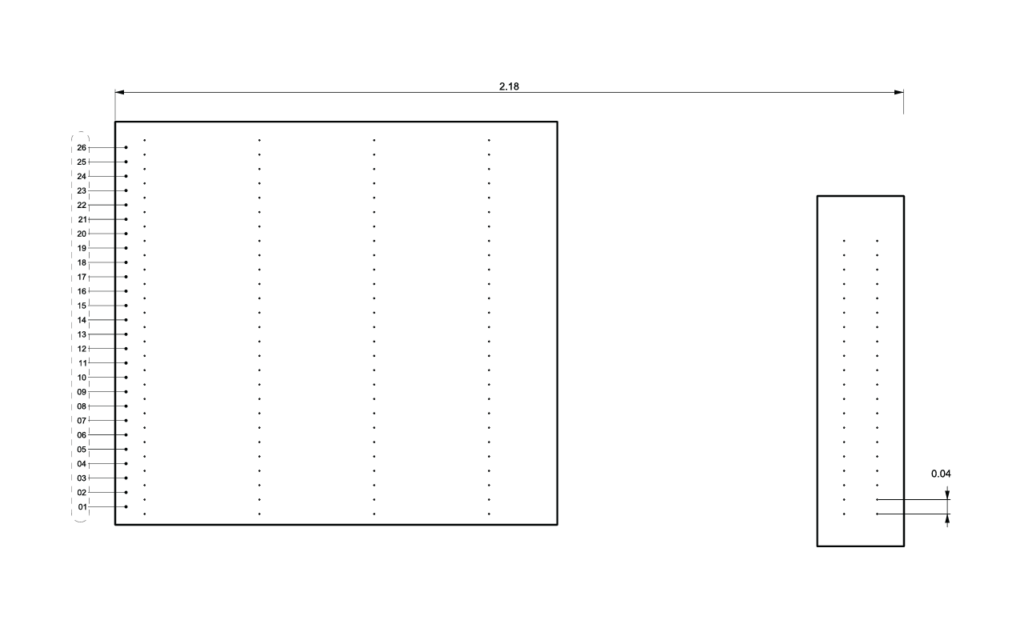
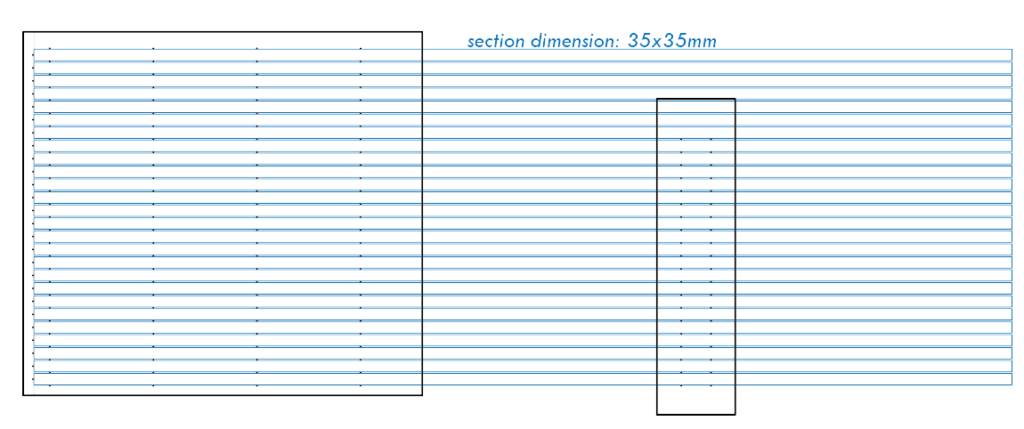
The process optimized the time for drilling the pieces and taught us the need for coding the faces of the wooden slats, as well as coding identical slats, in order to identify them efficiently in the subsequent assembly process. Additionally, we established a tolerance of 1mm for the space designated for fitting the 35x35mm section wooden slats, which in many cases, due to wood variation, made fitting difficult, requiring the use of a hammer to press the piece into the jig. While a good tolerance can facilitate fitting, it should be approached with caution to ensure the piece fits snugly and does not move during the use of the CNC machine.
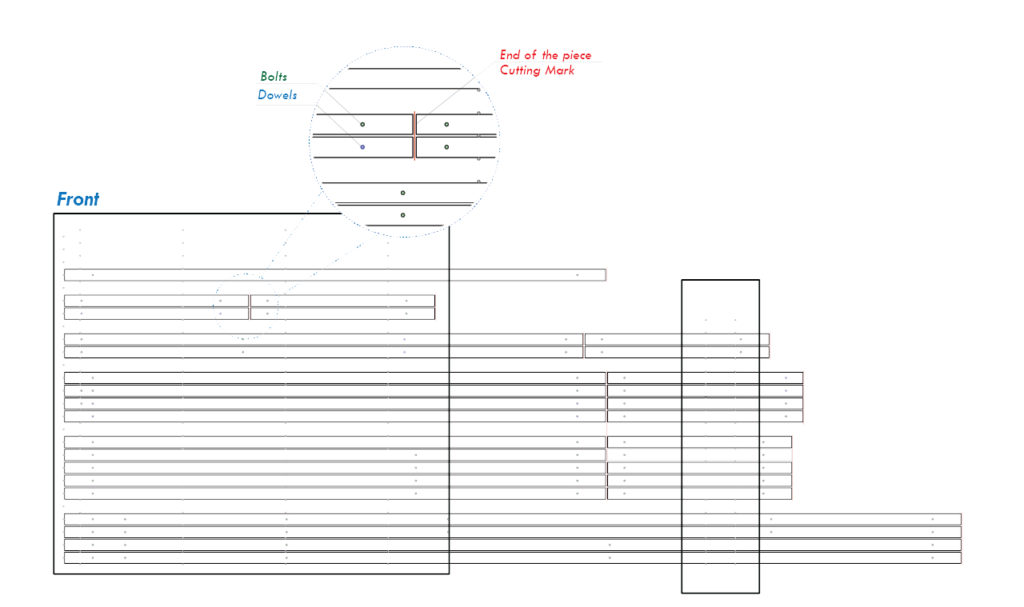
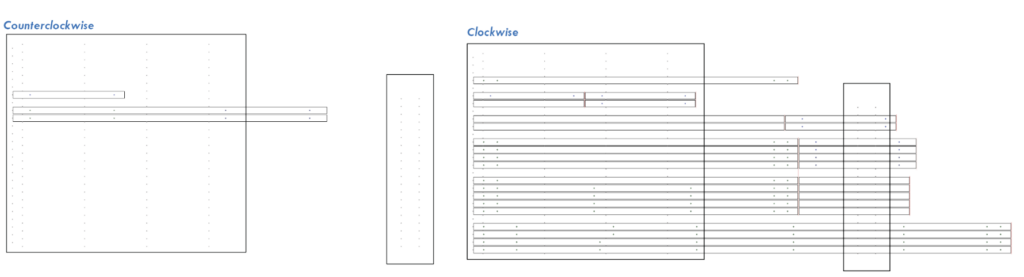
Cladding | Assembly and Fabrication
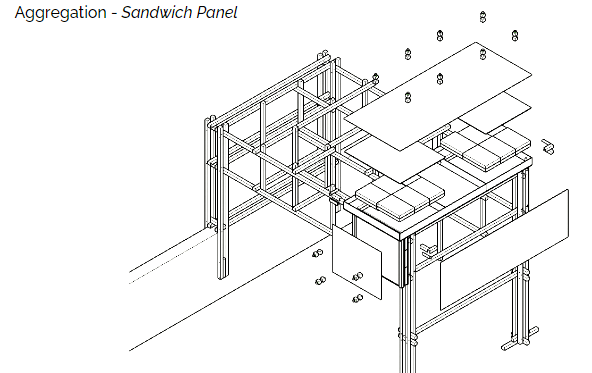
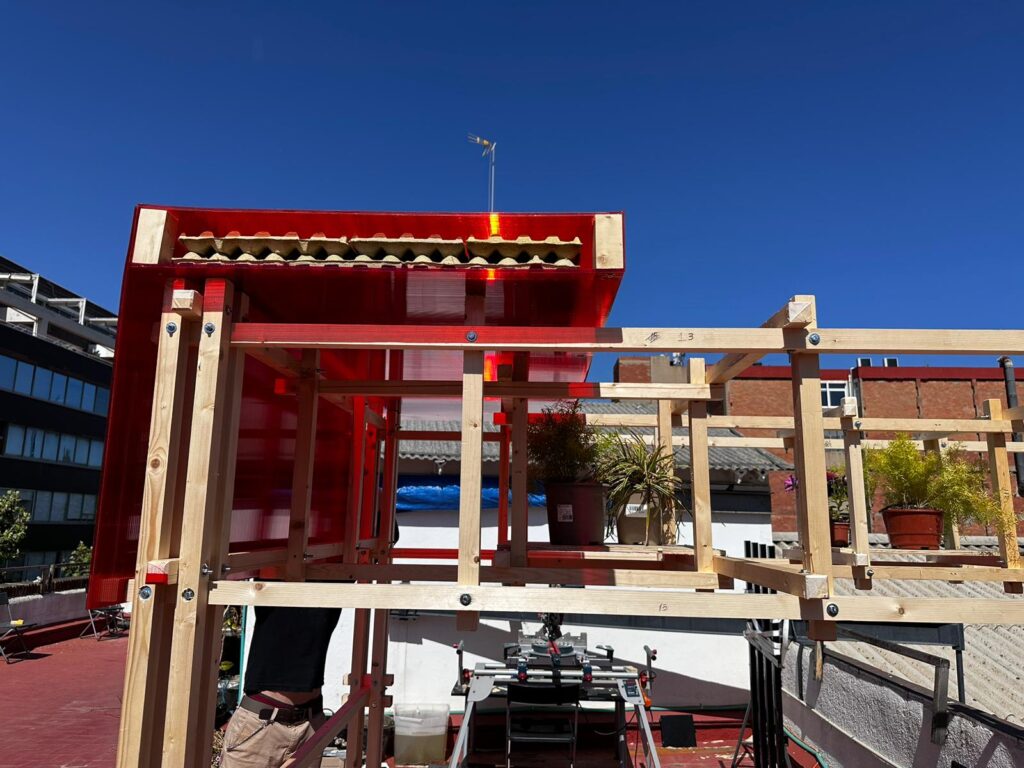
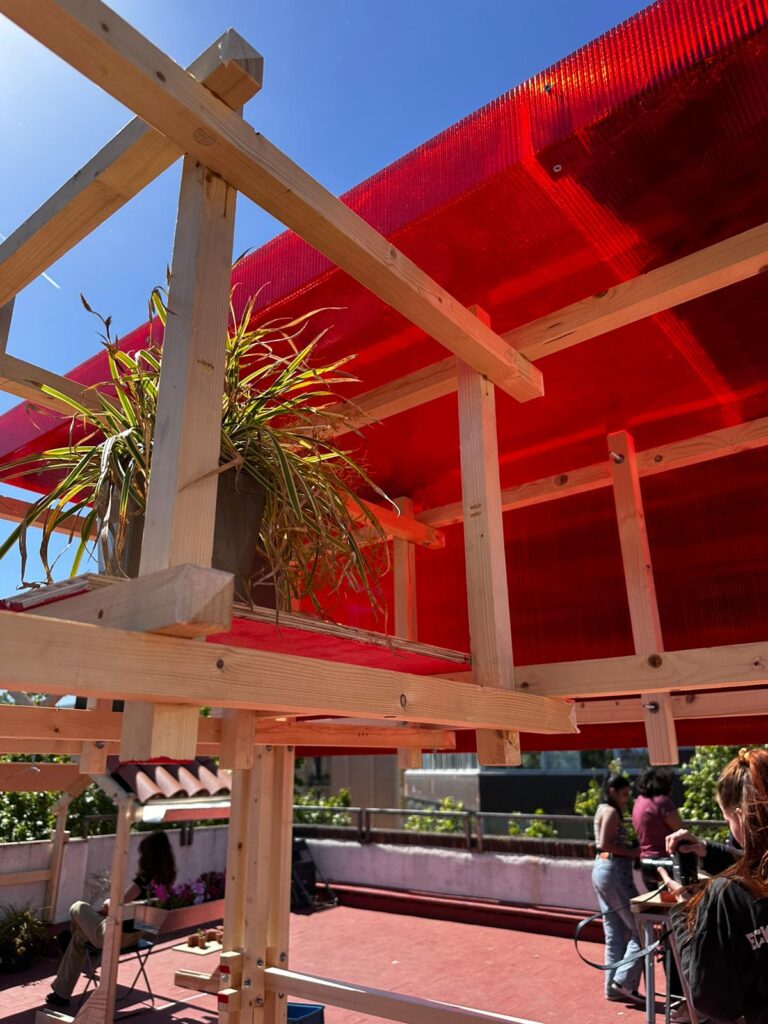
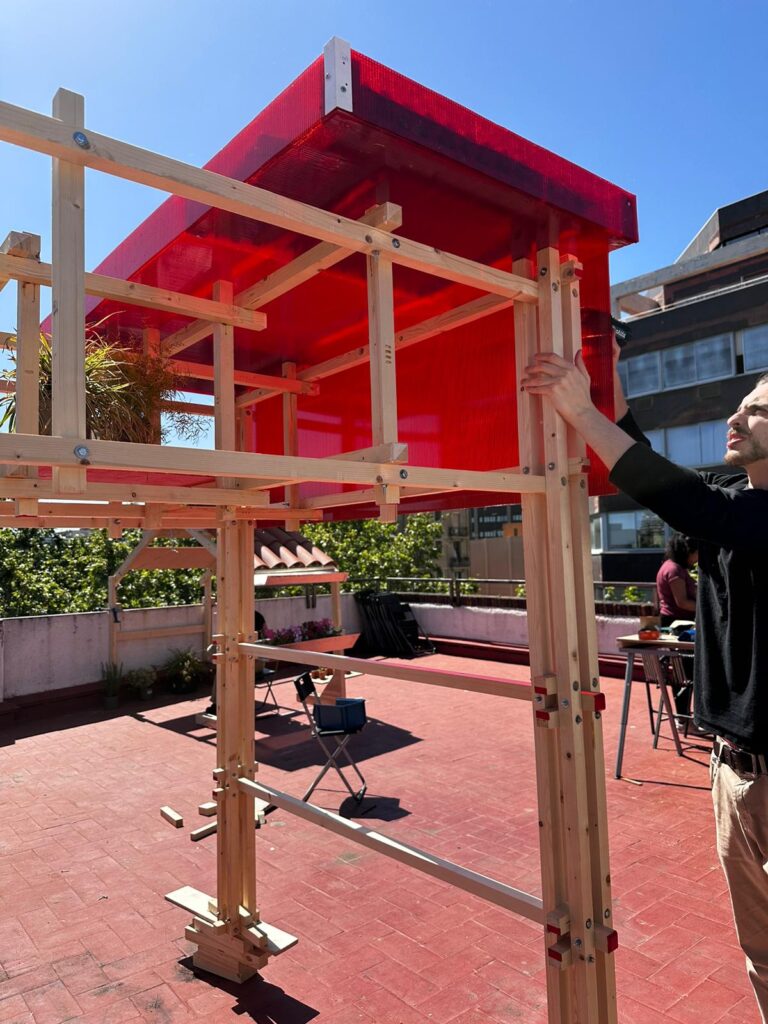
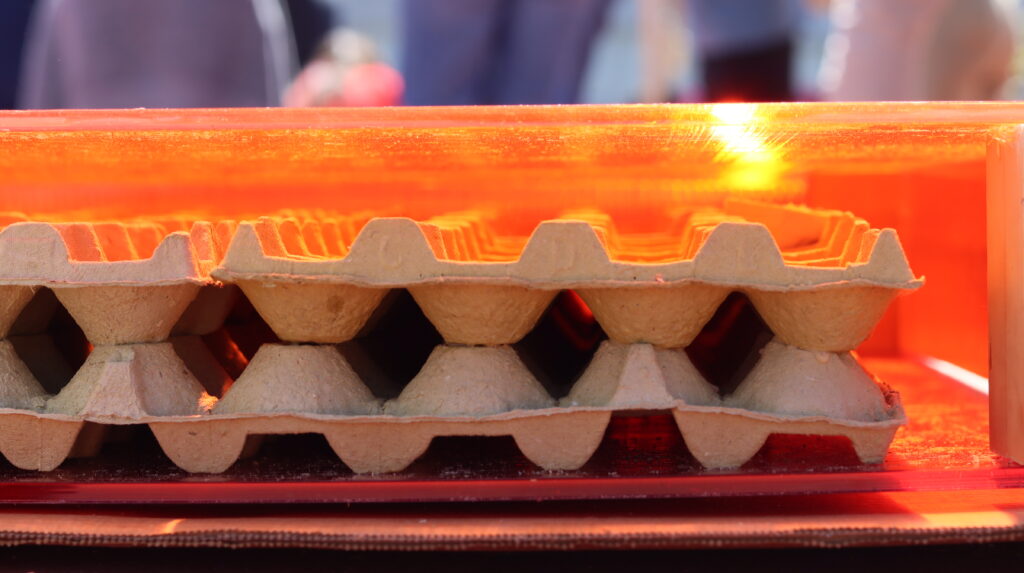
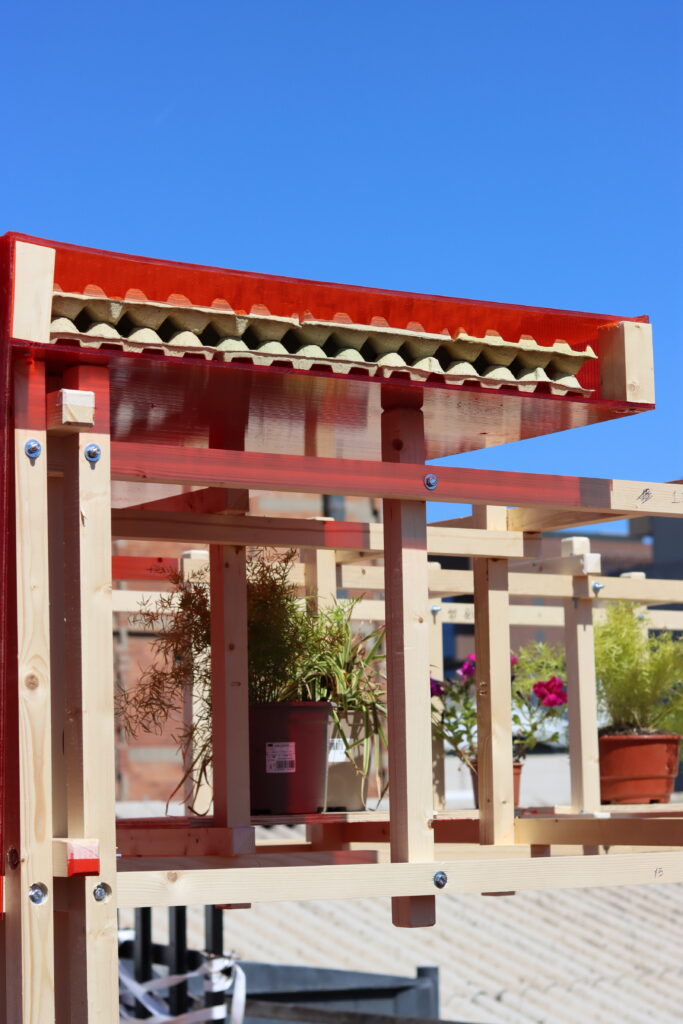
Assembly | Structure | Catalogue
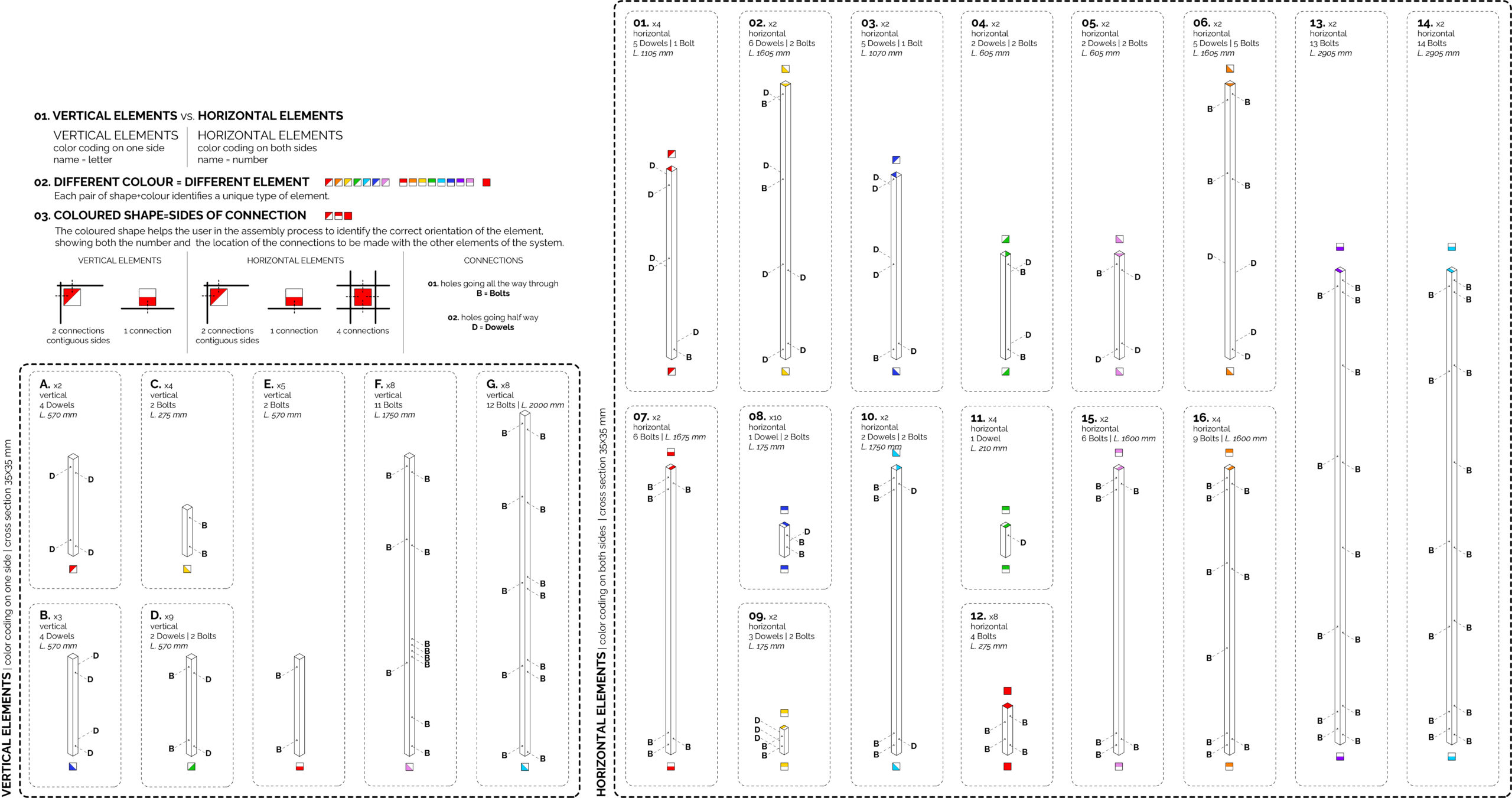
Assembly | Structure | Instructions
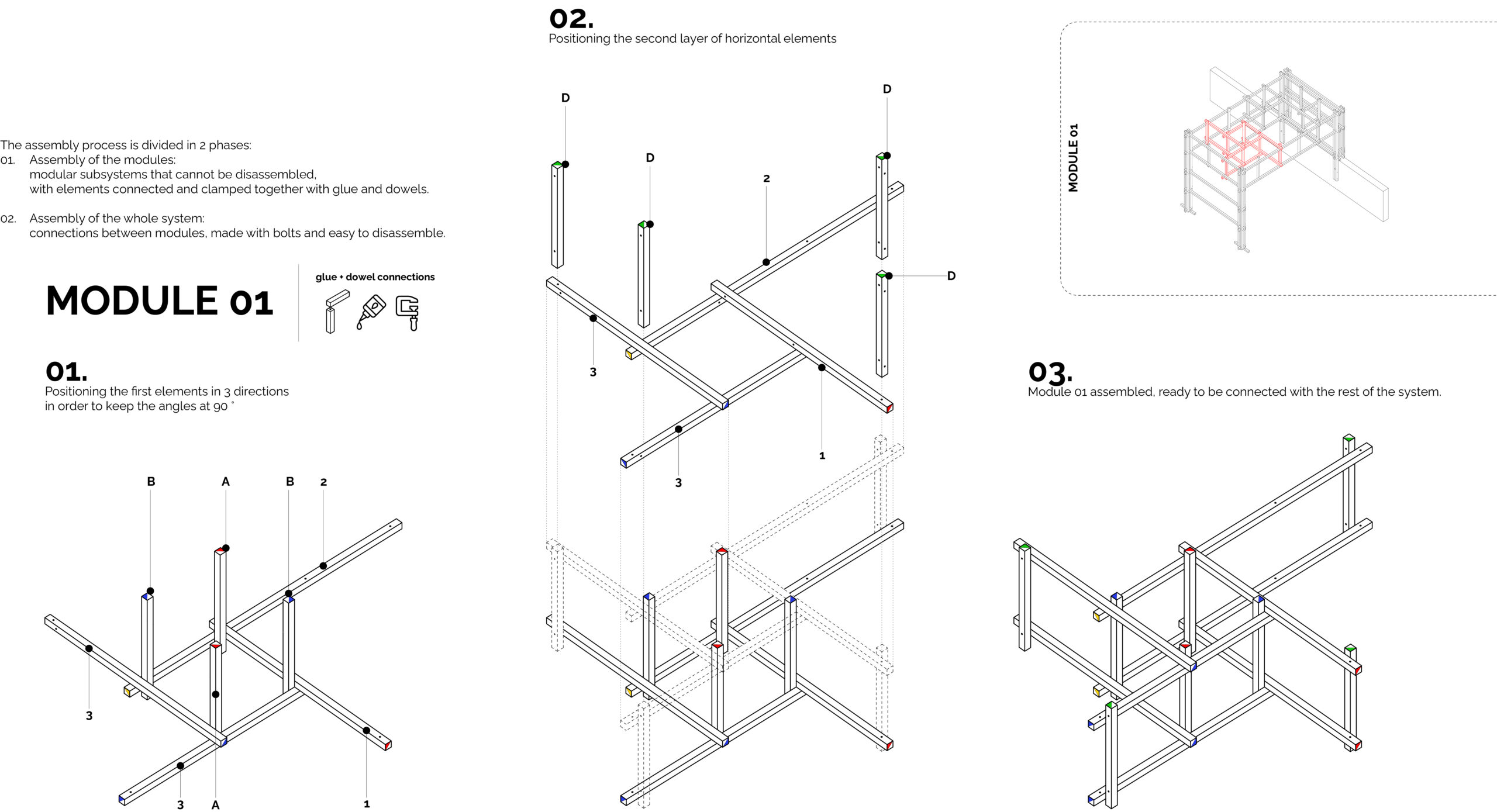
_____________________________________________________________________________________________________
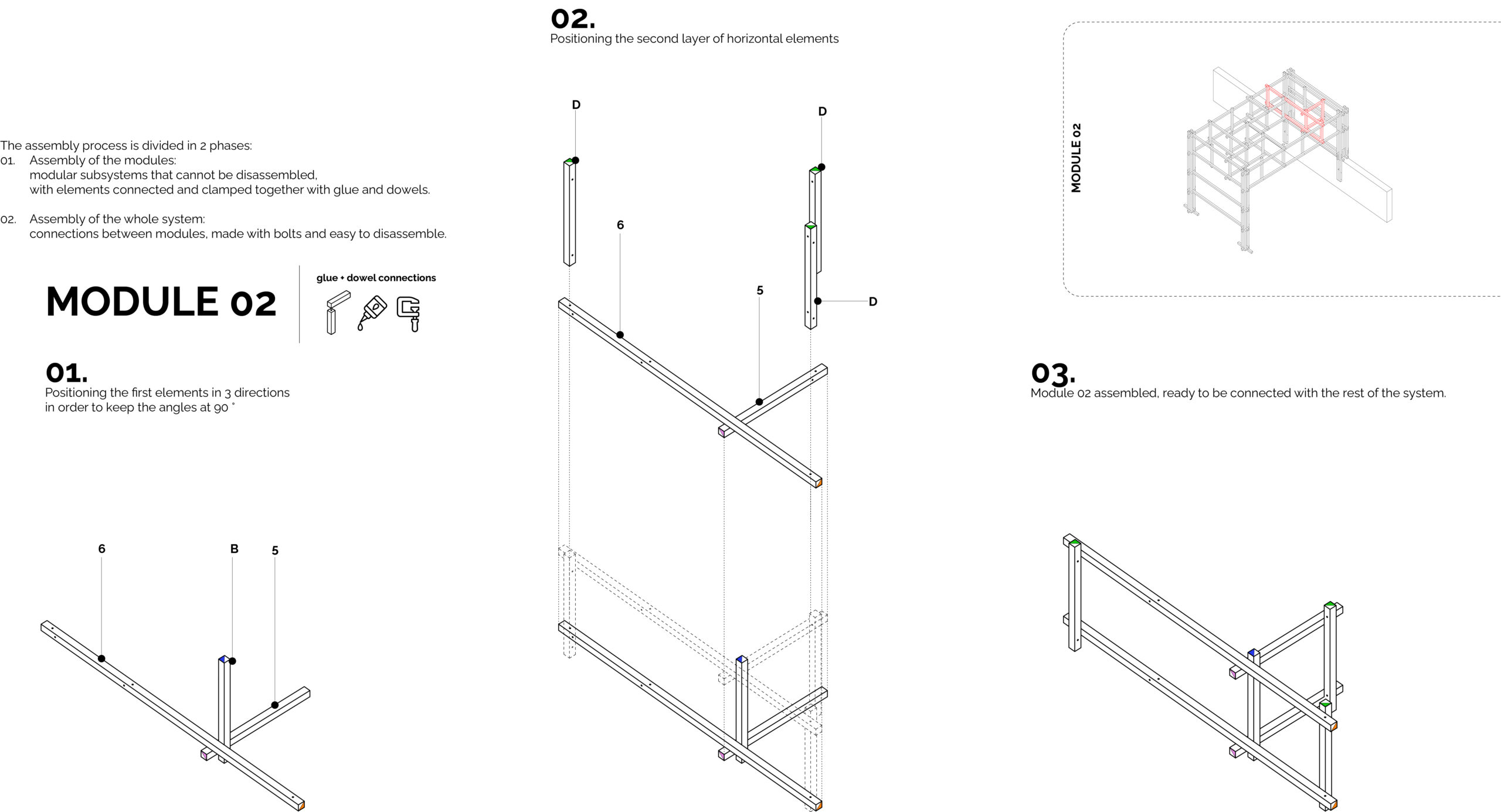
_____________________________________________________________________________________________________
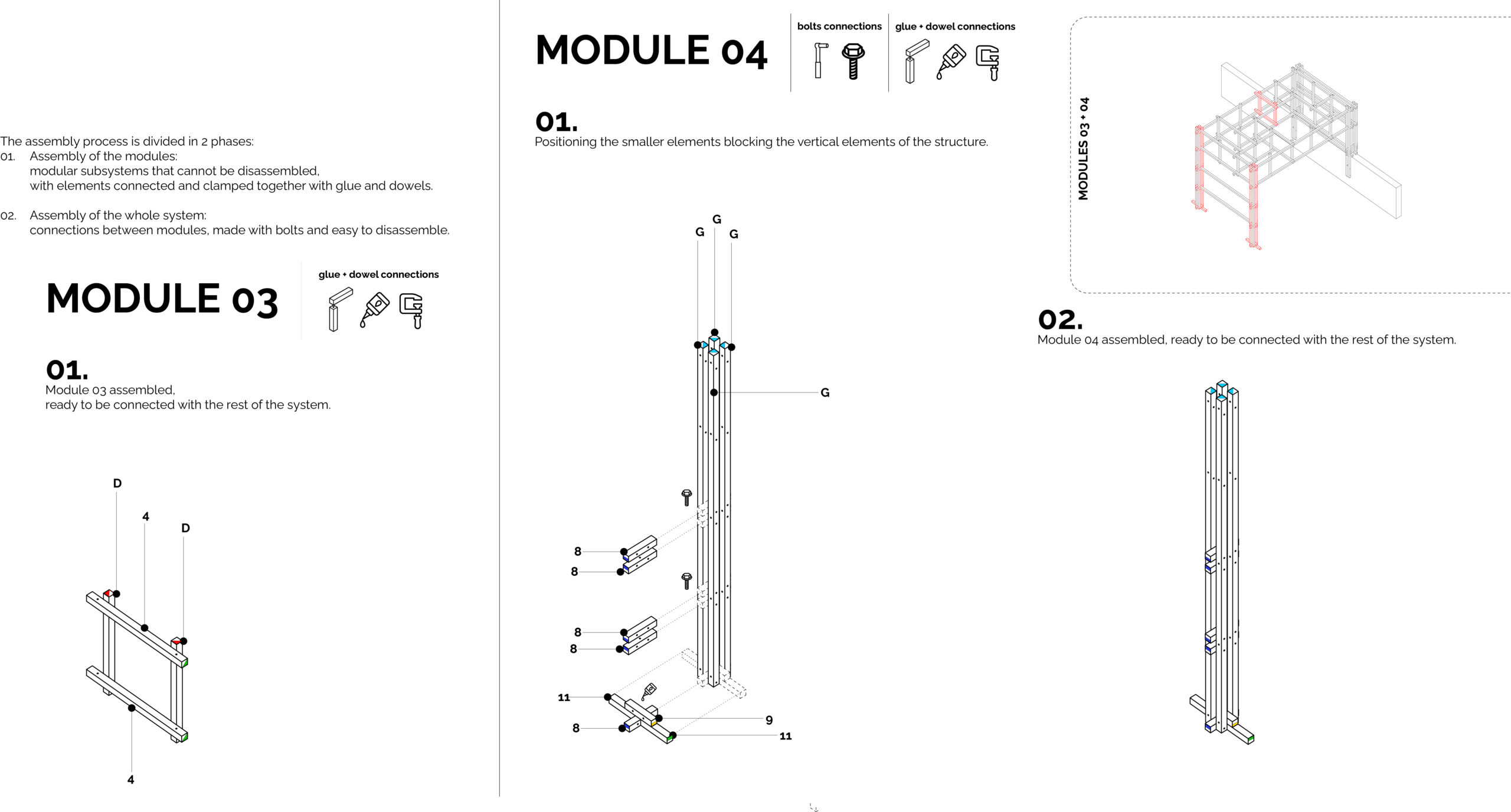
_____________________________________________________________________________________________________
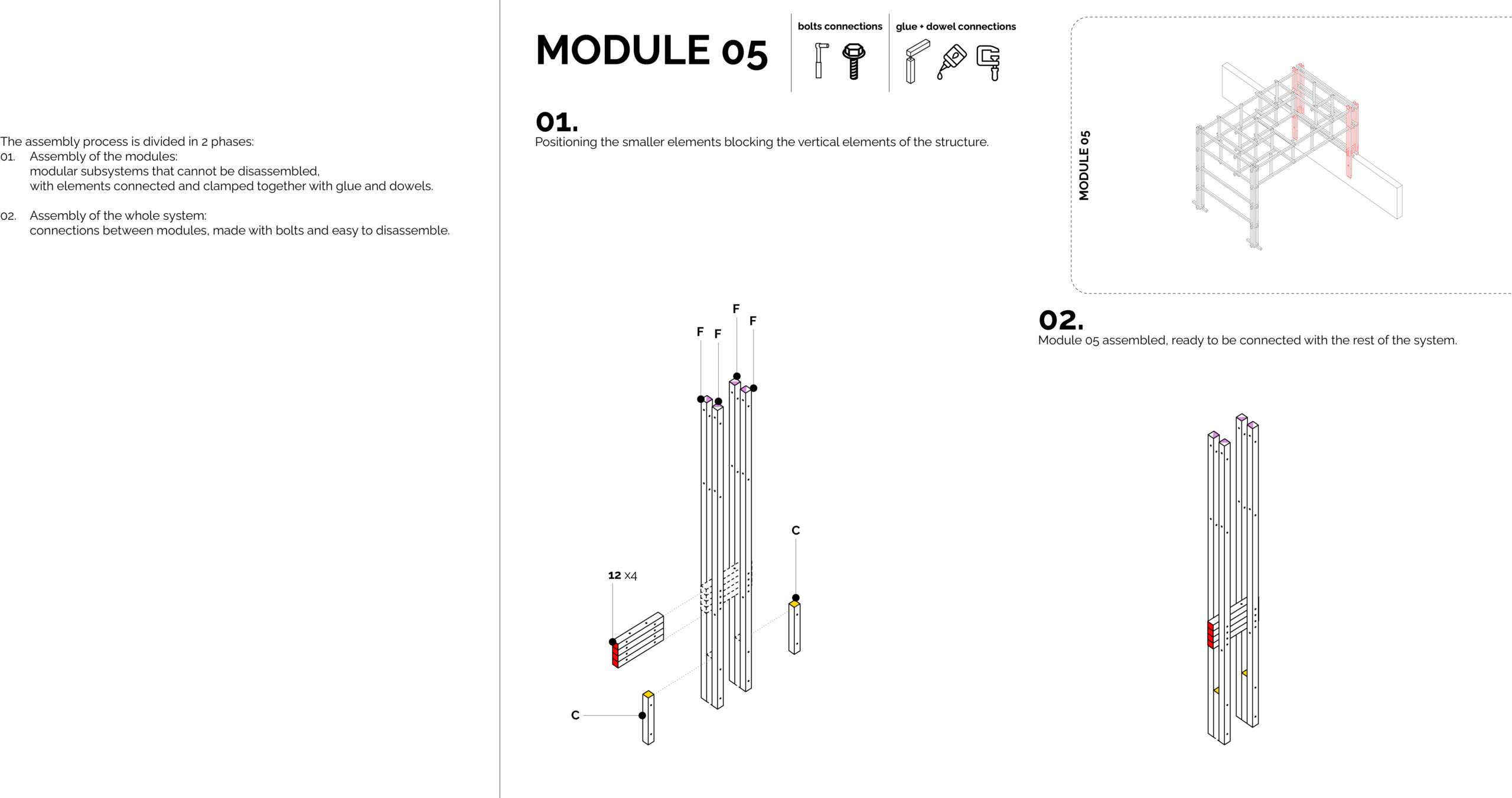
_____________________________________________________________________________________________________
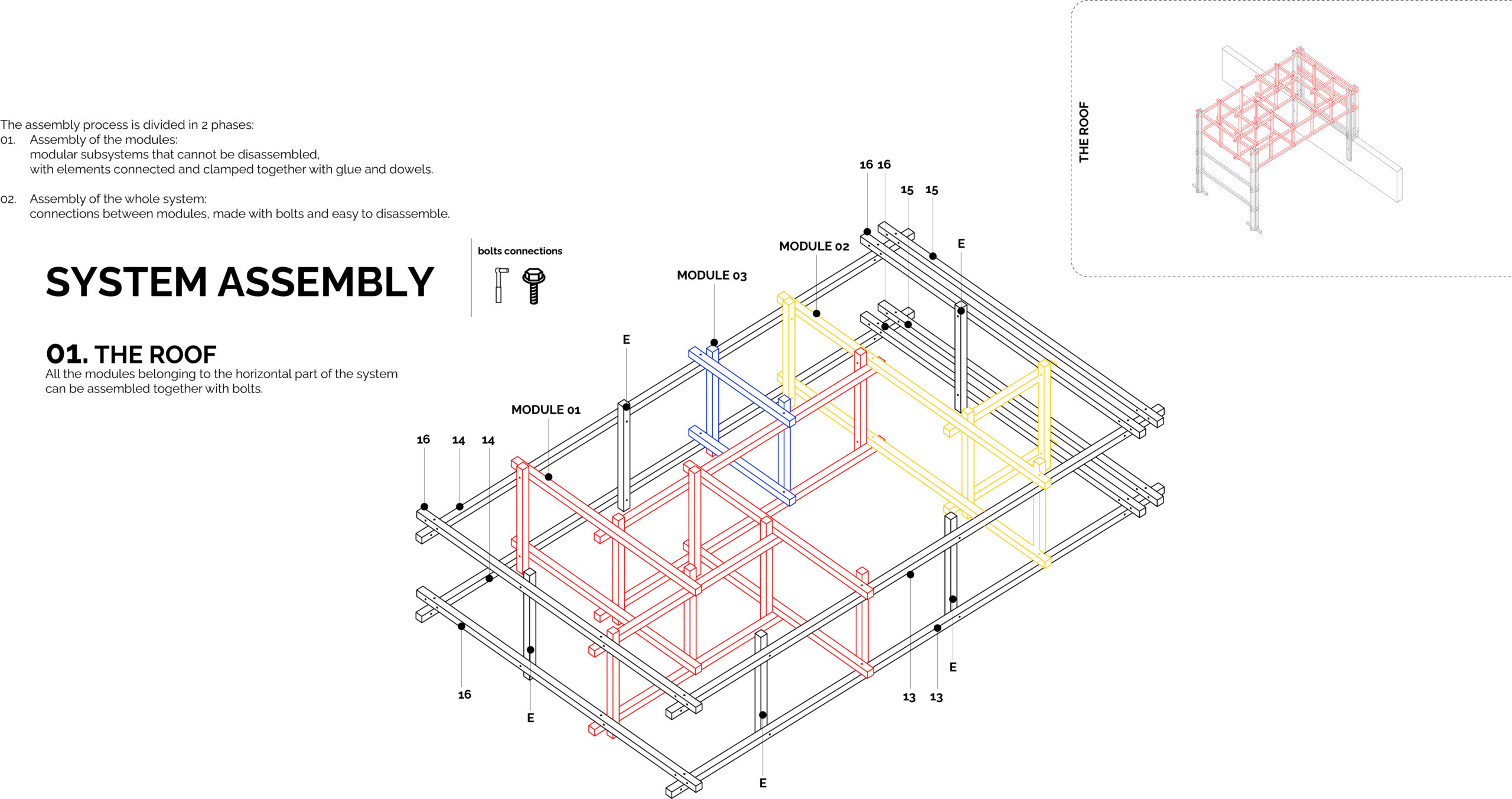
_____________________________________________________________________________________________________
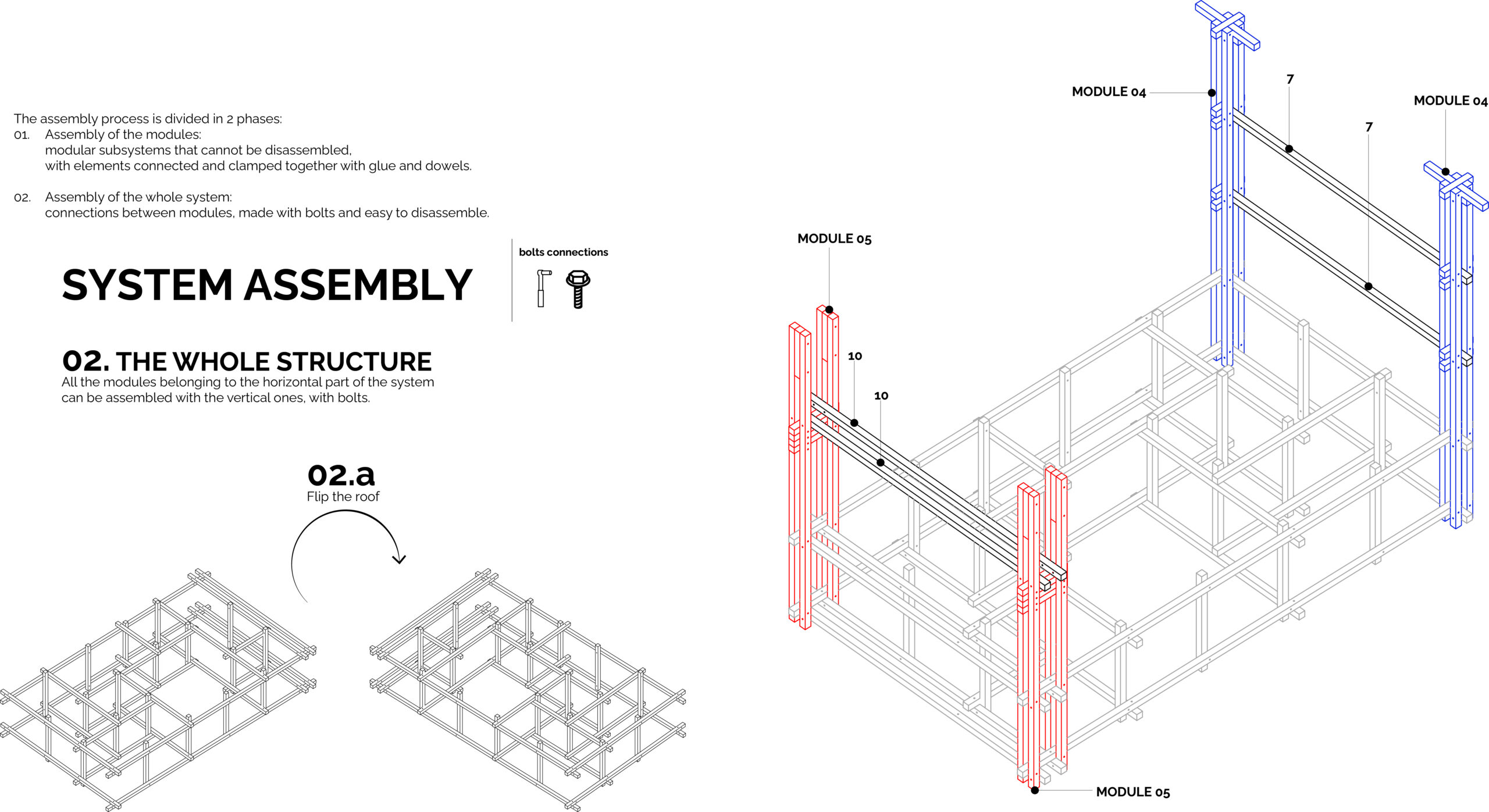
_____________________________________________________________________________________________________
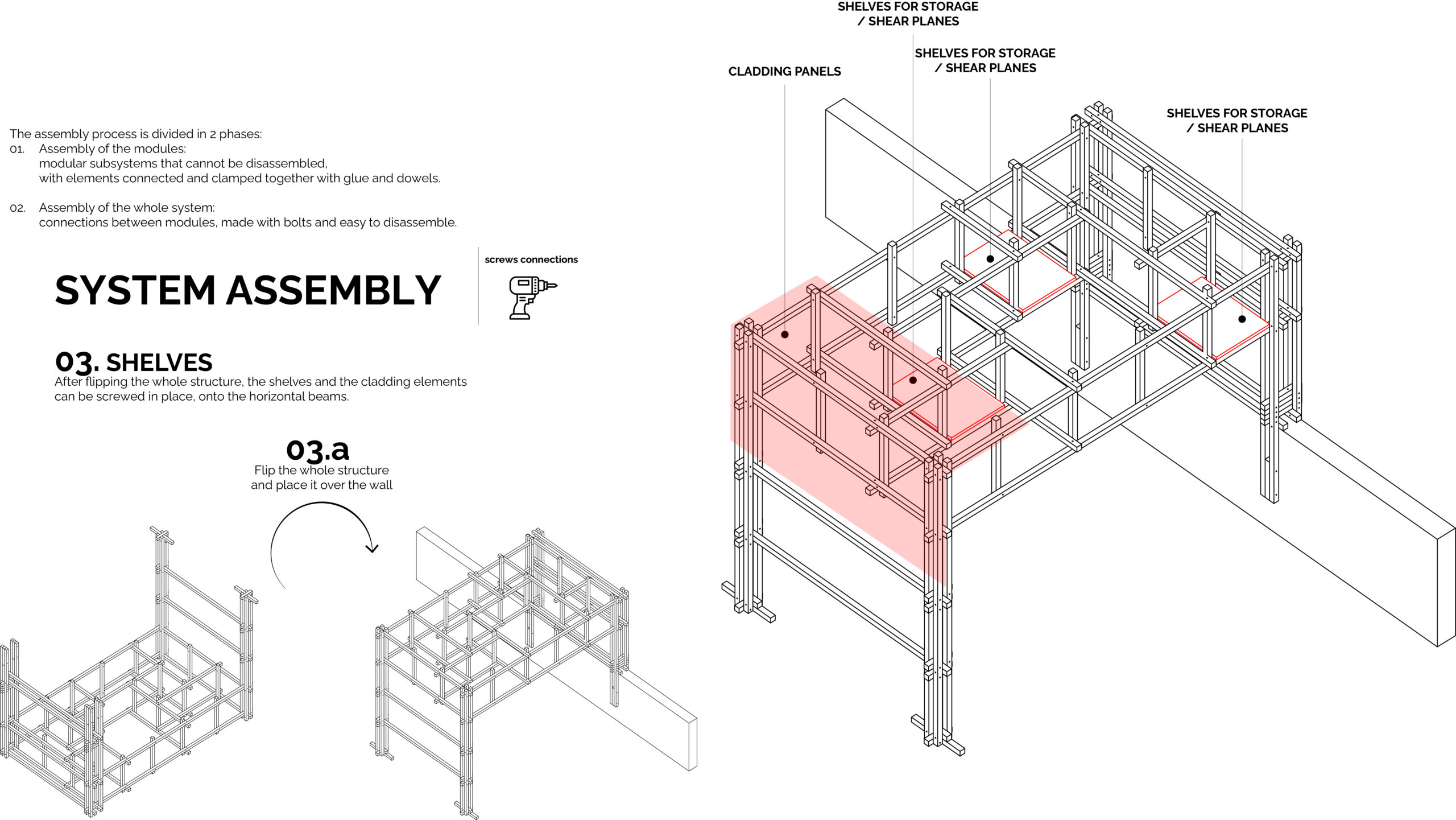
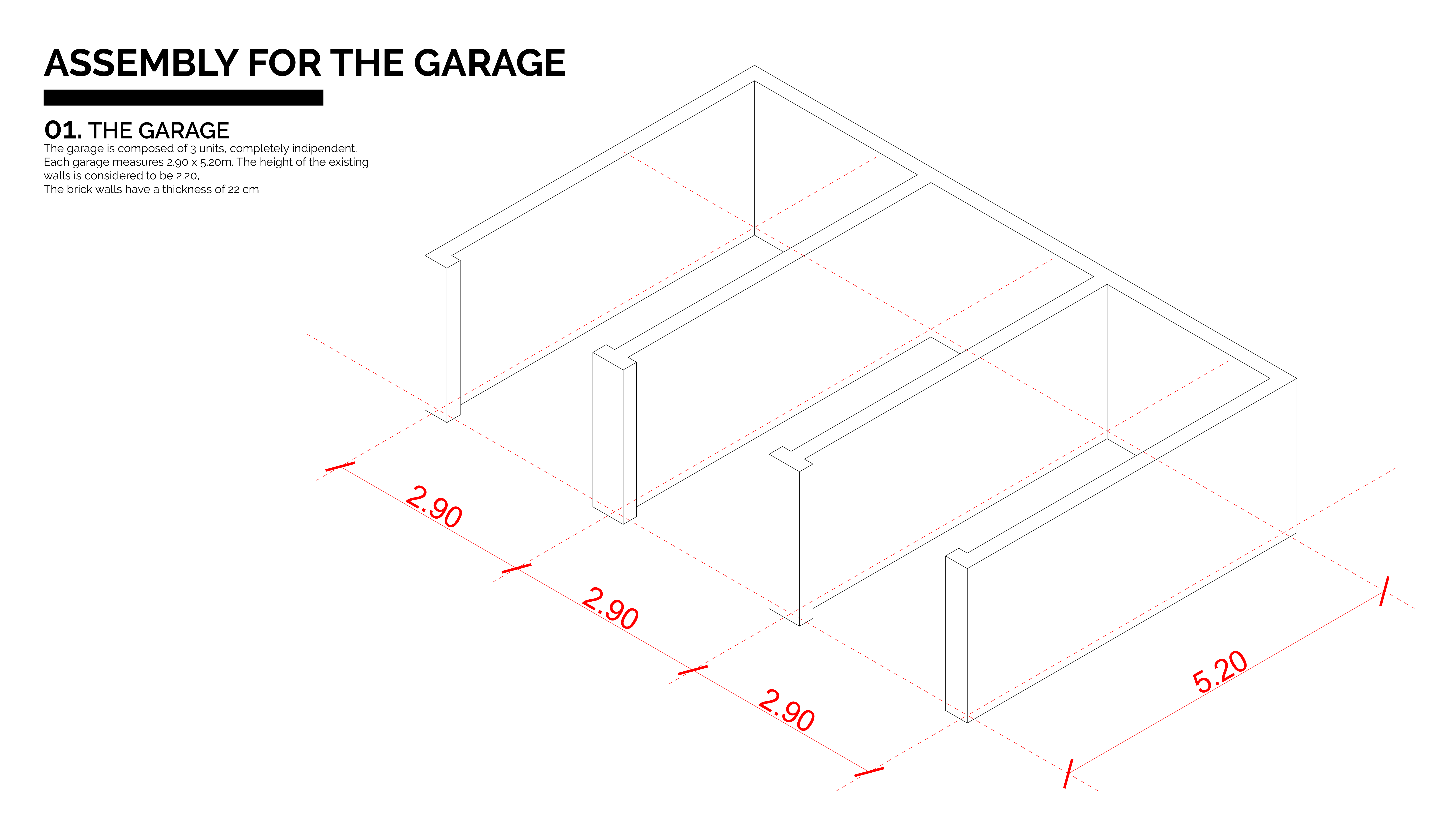
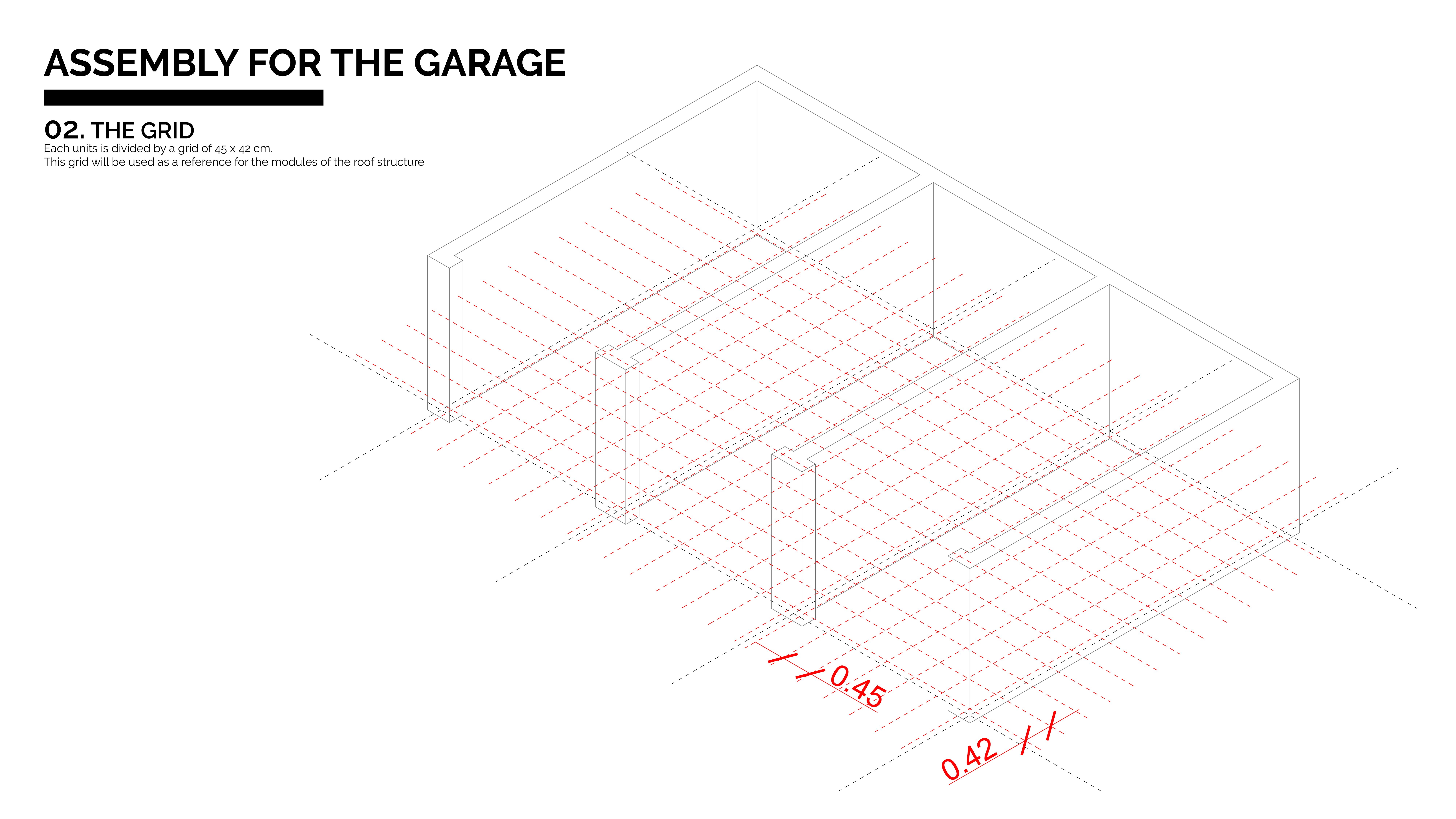
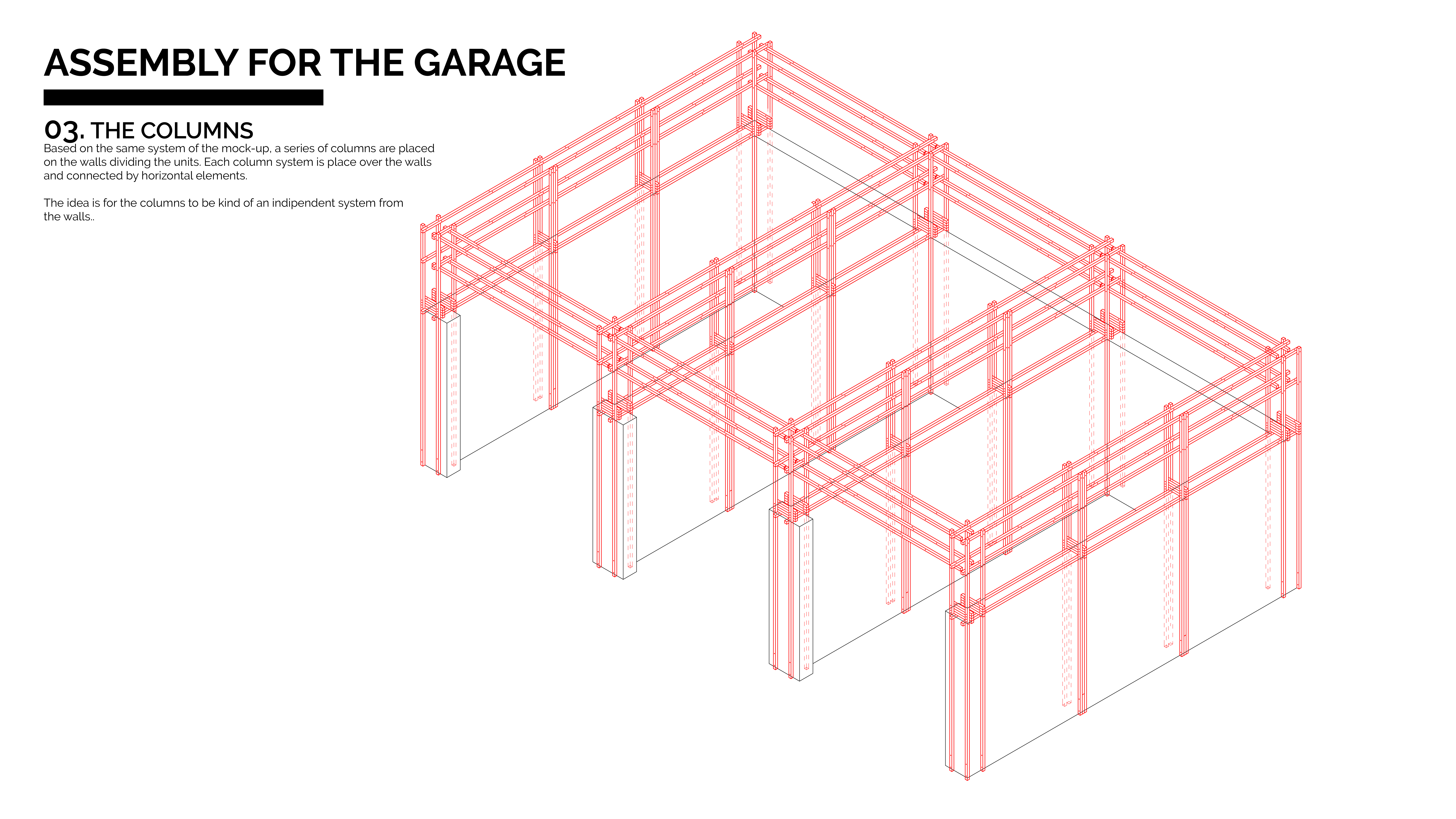
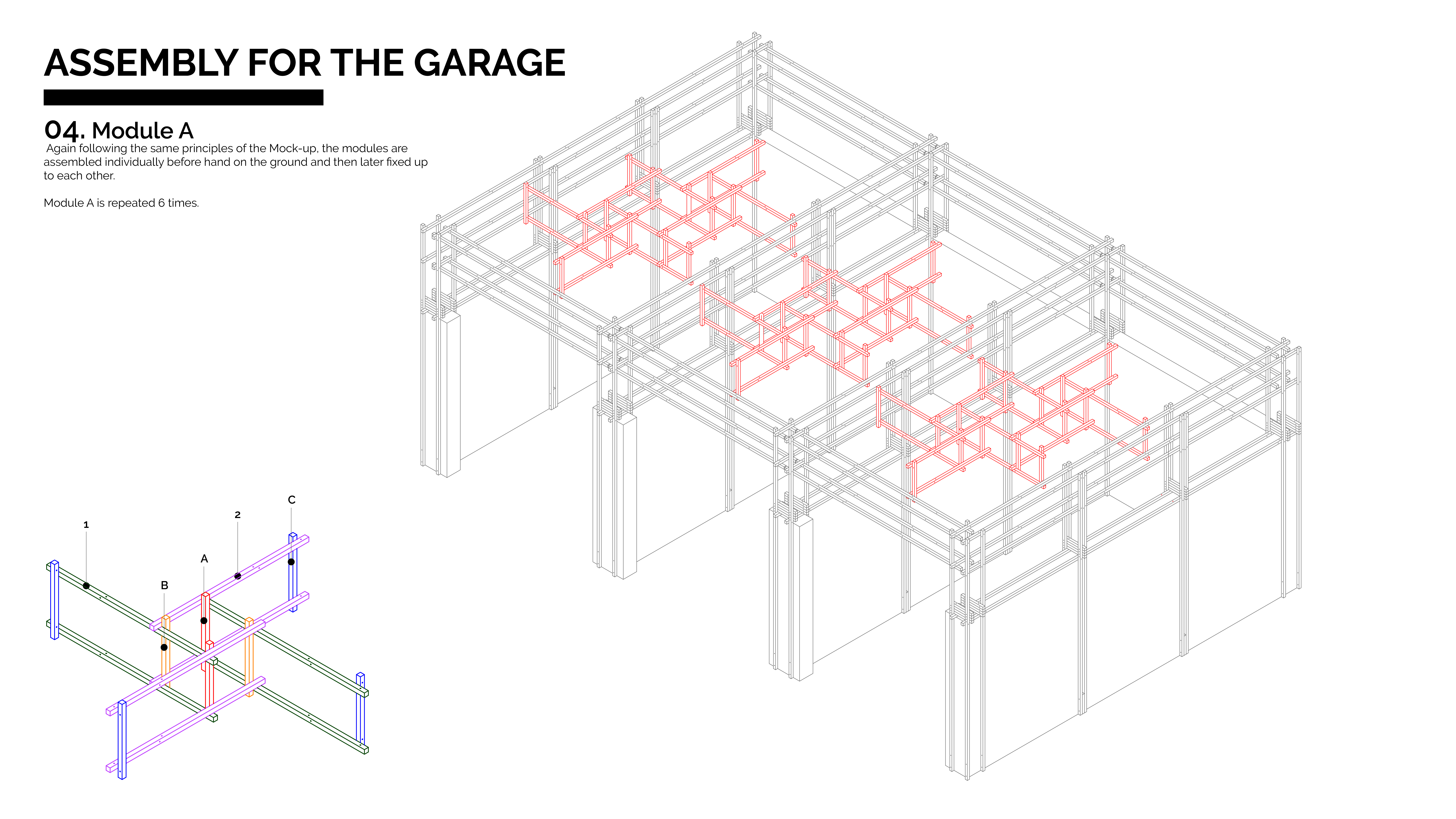
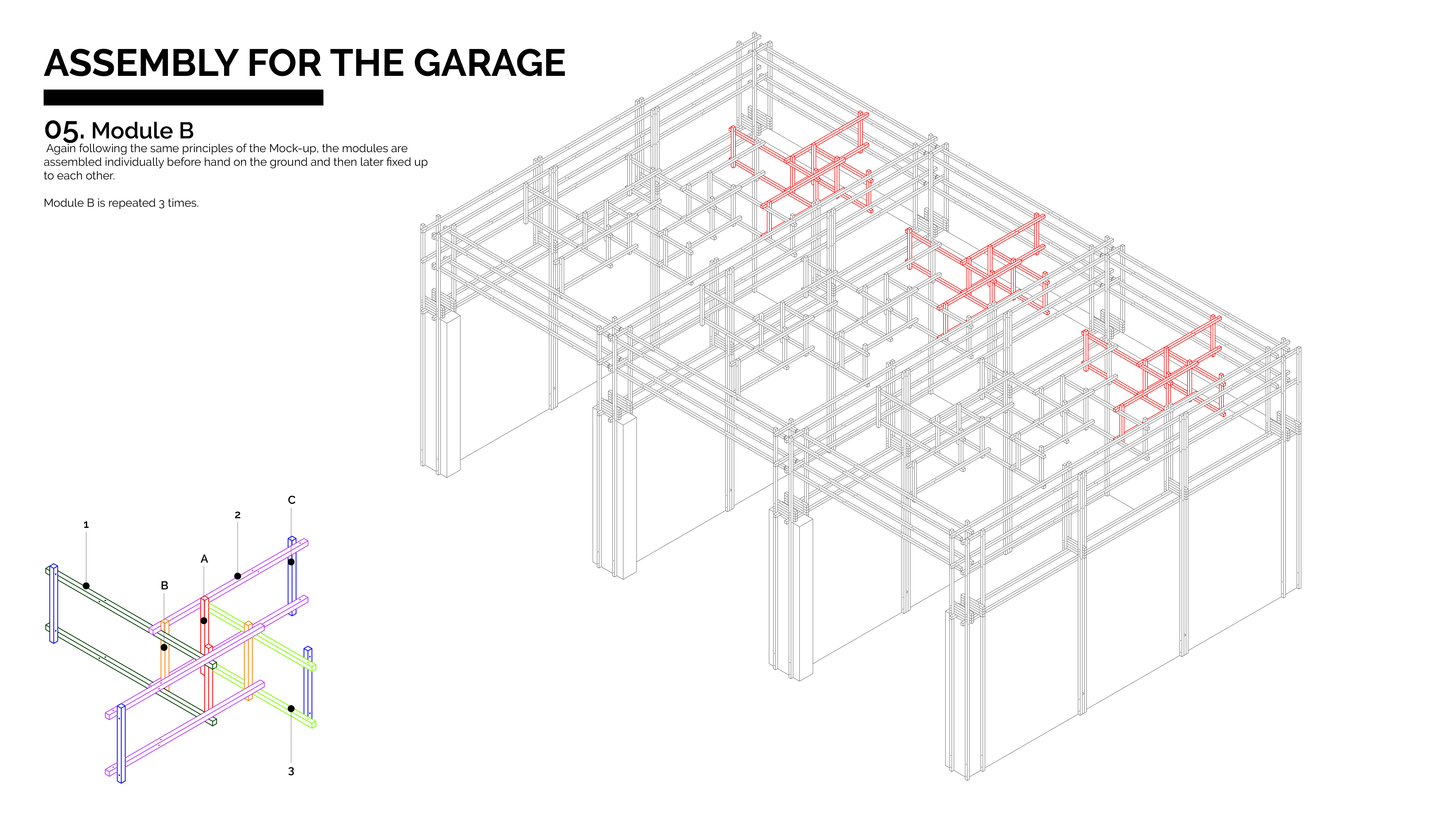
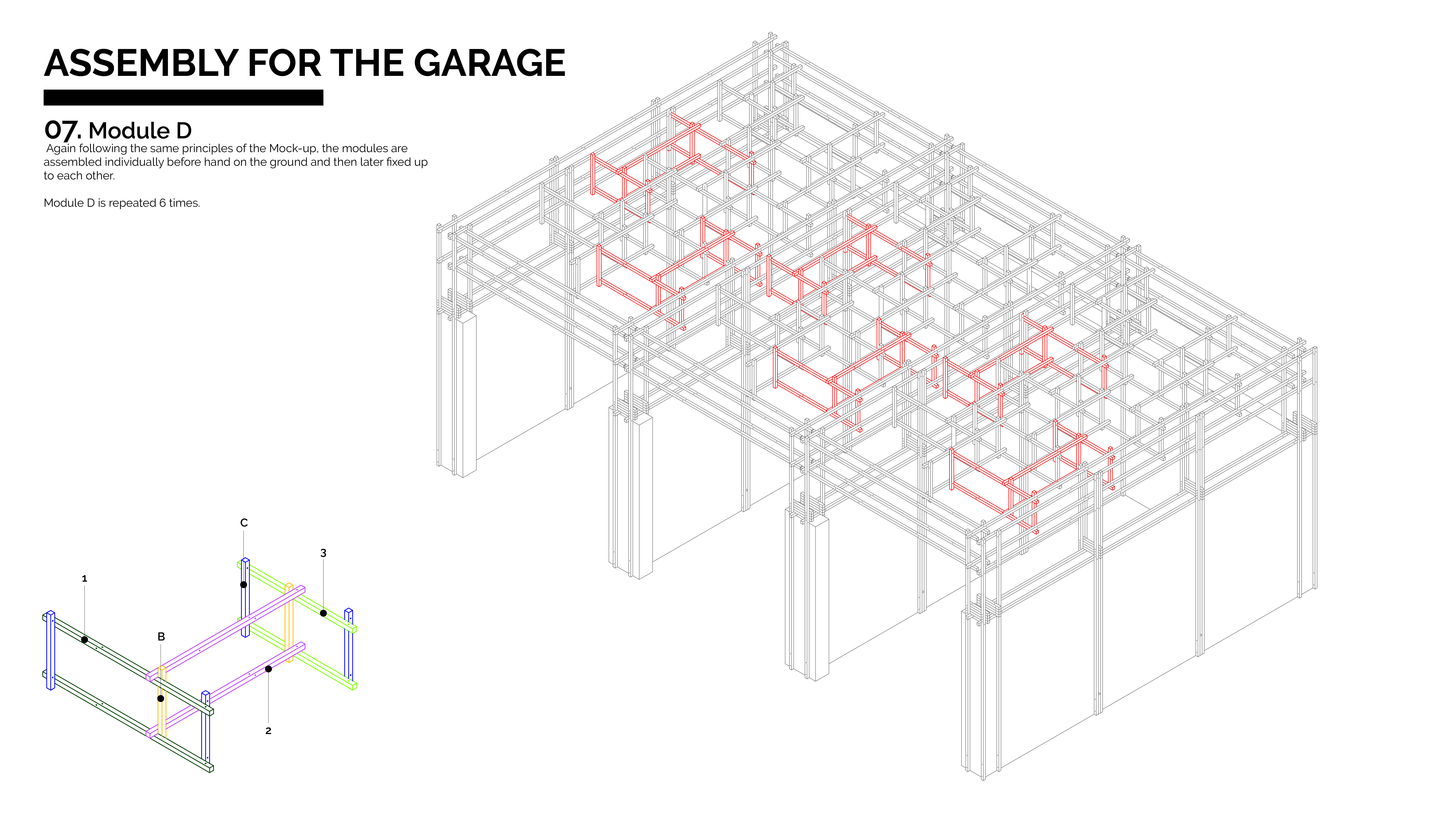
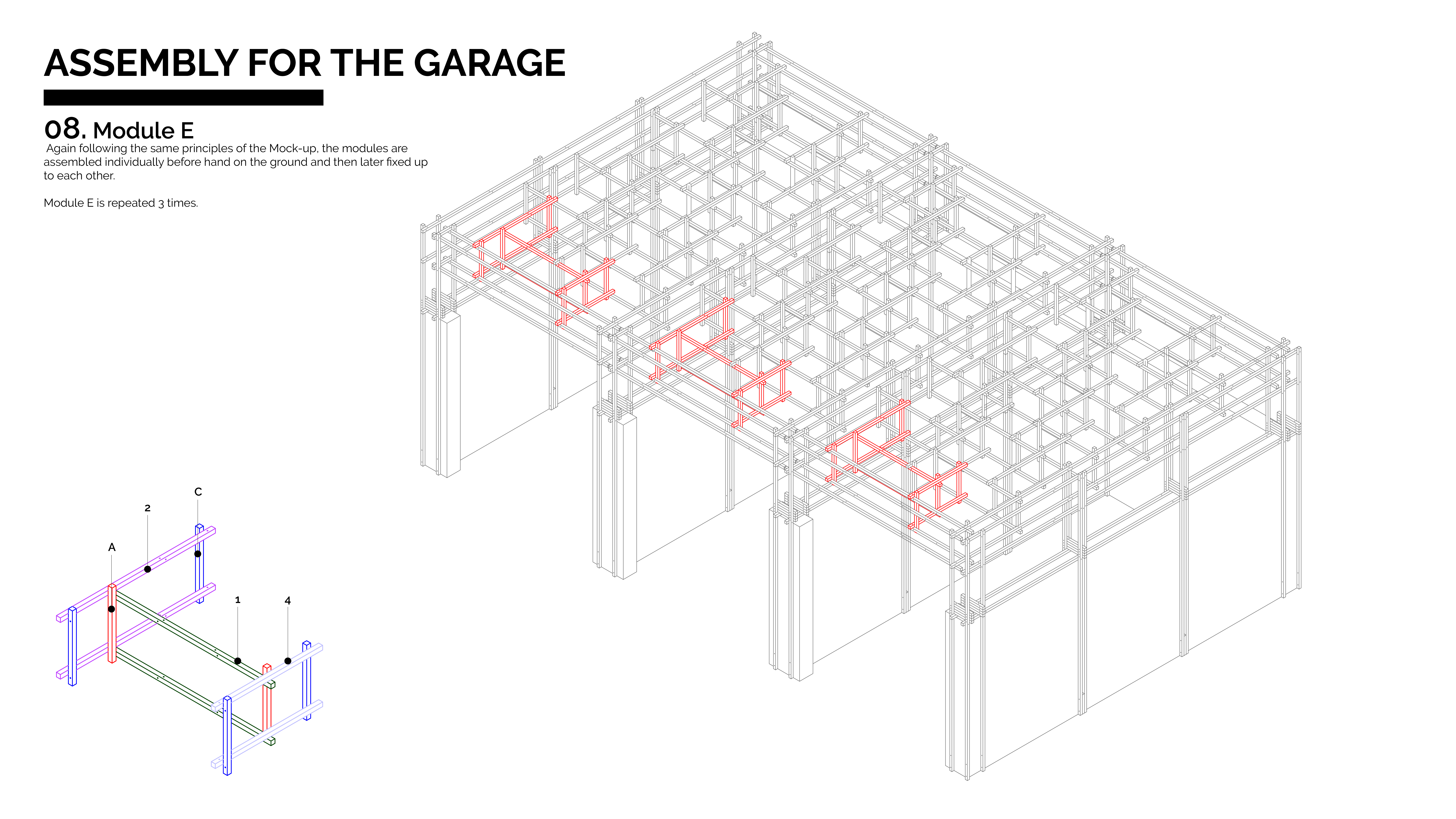
Final result | Built mock-up
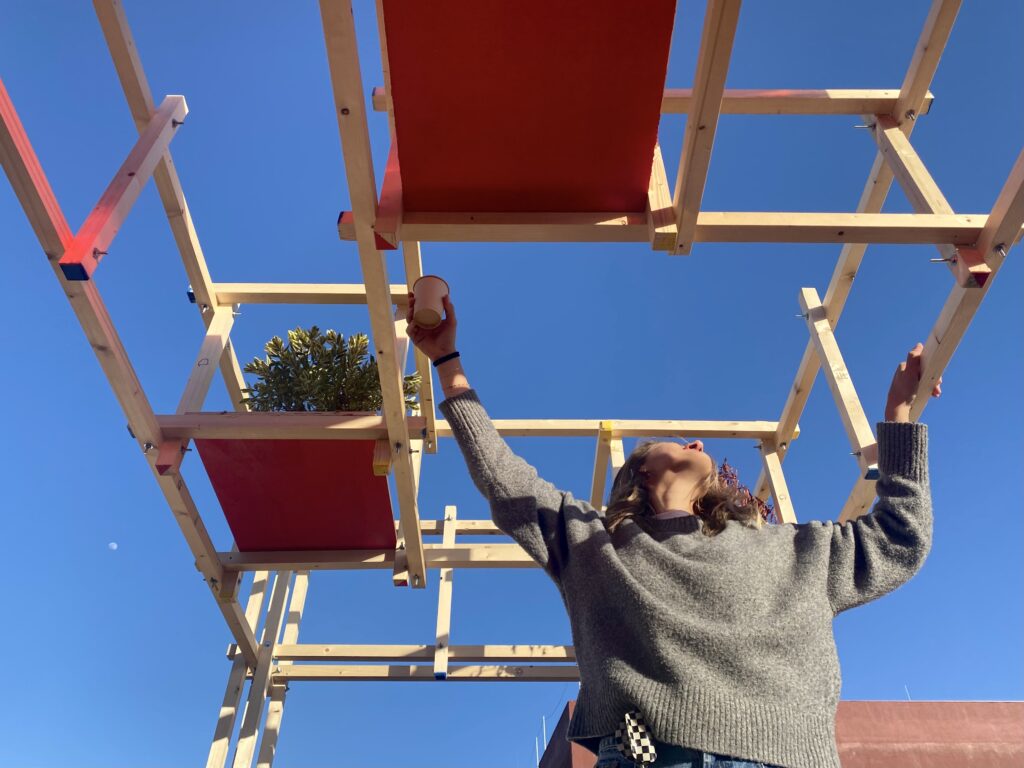
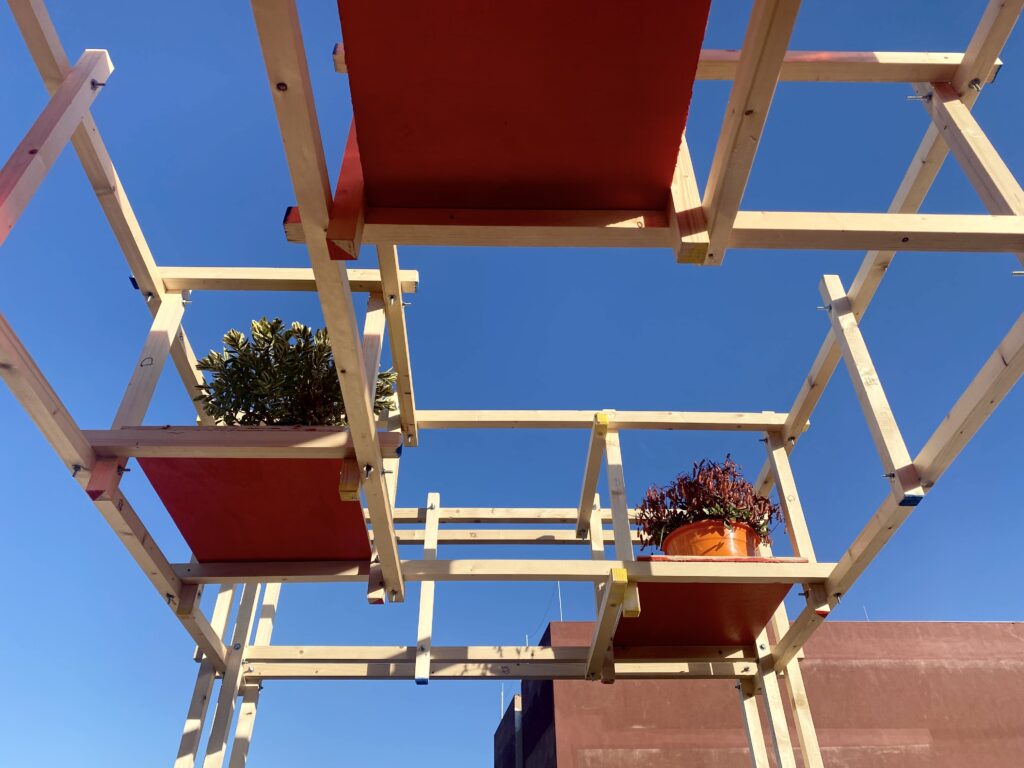
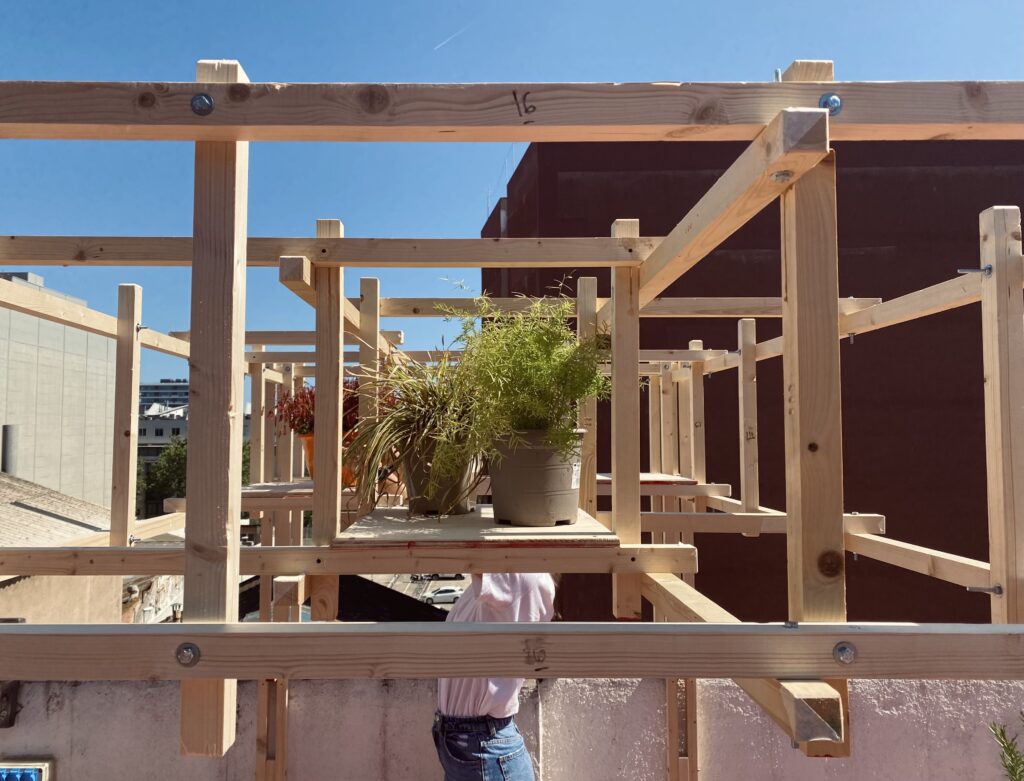
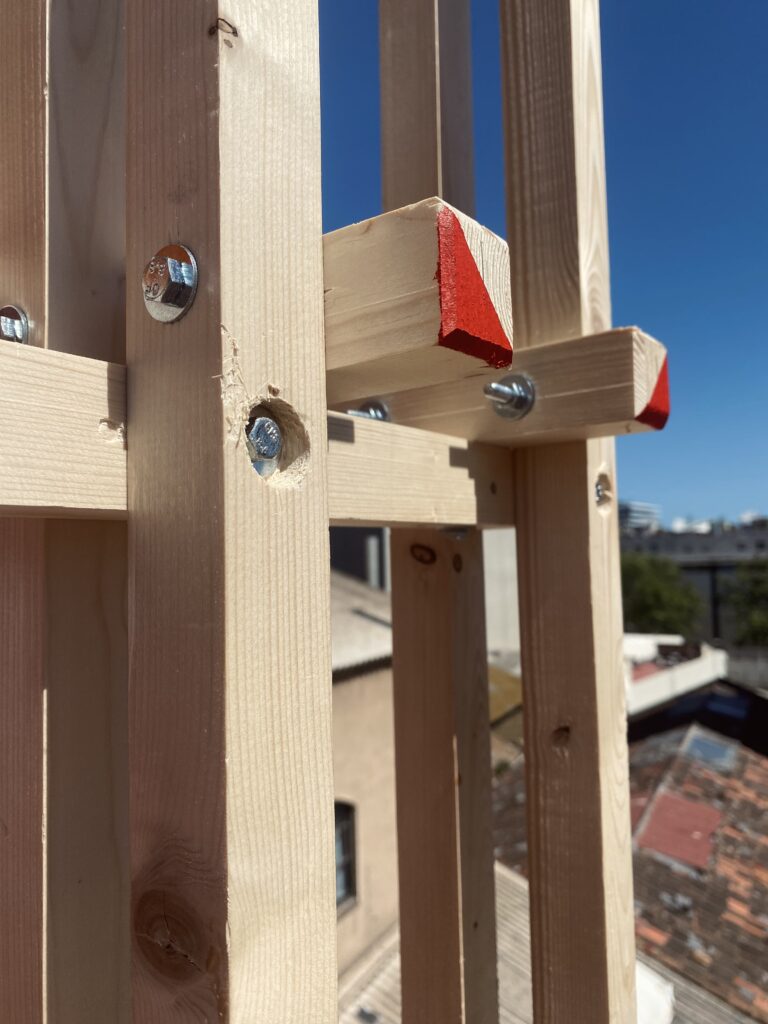
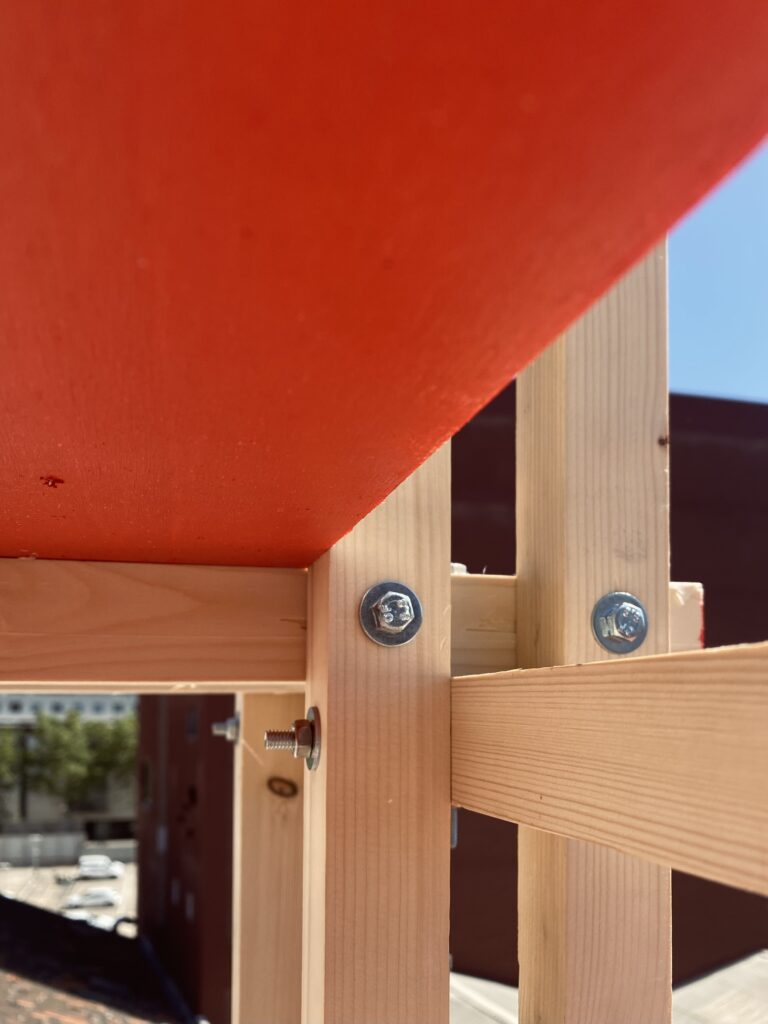