
The Martian Aggreculture project envisions a food production facility for the first colony on Mars. Our combinatorial modelling approach is data driven – flowing from the demands of the program and the realities of building on Mars into our aggregated architecture to provide a decentralized and resilient food production facility. Colonization at the Aggreculture site is planned to proceed in three phases, with Phase 1 welcoming 50 residents, Phase 2 adding another 50 residents and Phase 3 totalling 300 residents.
Although colonizing Mars will require the sustainability of Earth to be assured before it could be successful, there are lessons to be learned from exploring the closed loop sustainable systems that would be required on Mars.
Lava Tubes
Taking advantage of the natural formation of lava tubes to provide protection from radiation and regulation of temperature is a core concept of the Martian Aggreculture project. Our site is situated in the Valles Marineris trench to the east of Tharsis volcano cluster. Lava outflows form giant underground caverns as they cool from the outside, on Mars these are of the order of 60 m tall and 200 m wide.
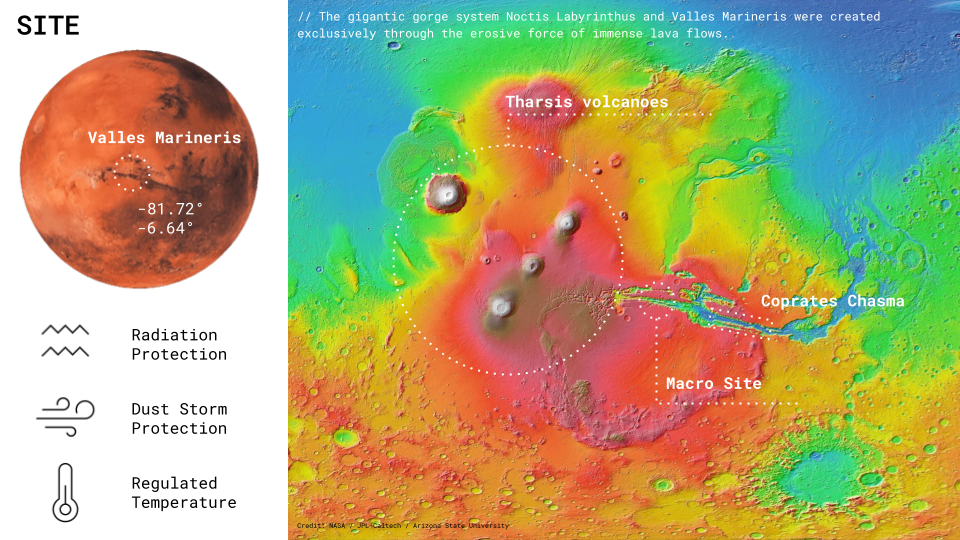
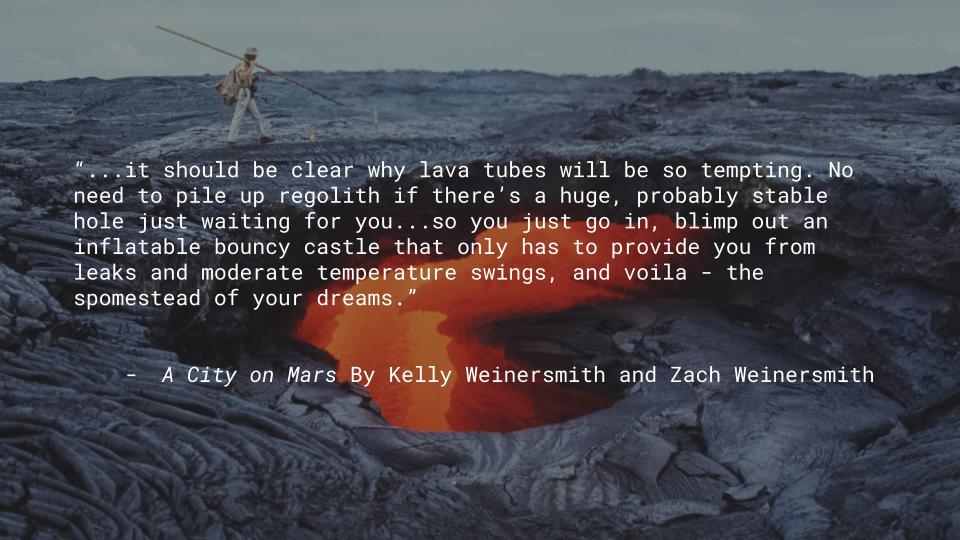
The lava tube is created using volumetric subtractive typologies. The Dendro plug-in was used to create a realistic Martian lava tube and skylight.
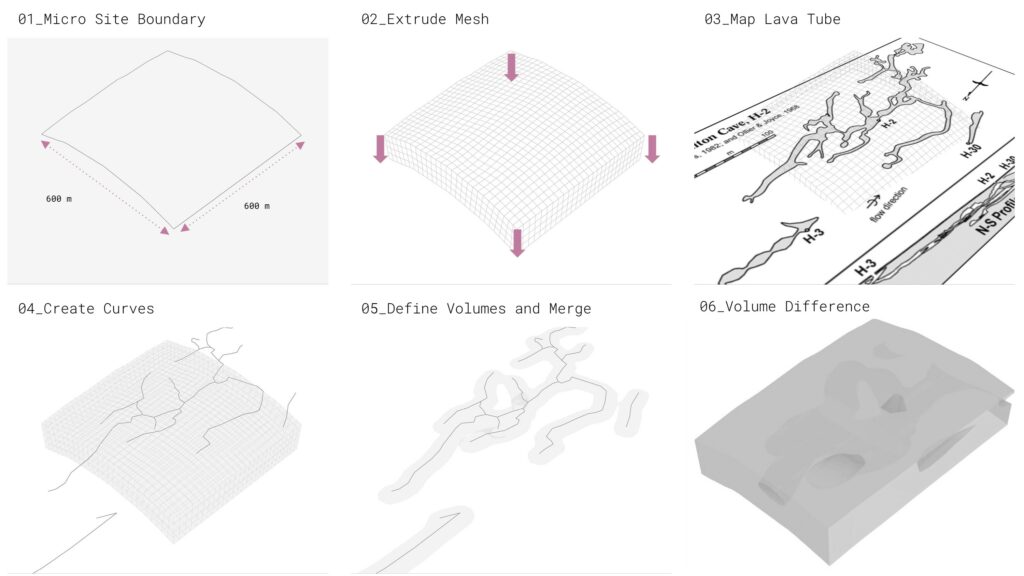
Food Production
To assess the demands for food production we reviewed the literature for studies on long term food production in space and on Mars1,2, particularly the in depth thesis of Sydney Do3 who modelled the needs of Martian astronauts on a long-term mission. The initial estimates from balancing the CO2, O2 and carbohydrate demands of a totally plant based production system arrive at a figure of approximately 50 m2 crop area per astronaut. Adding in fungi and algae-based food, chemical and materials production and including some redundancy we aim to provide 100 m2 per astronaut.
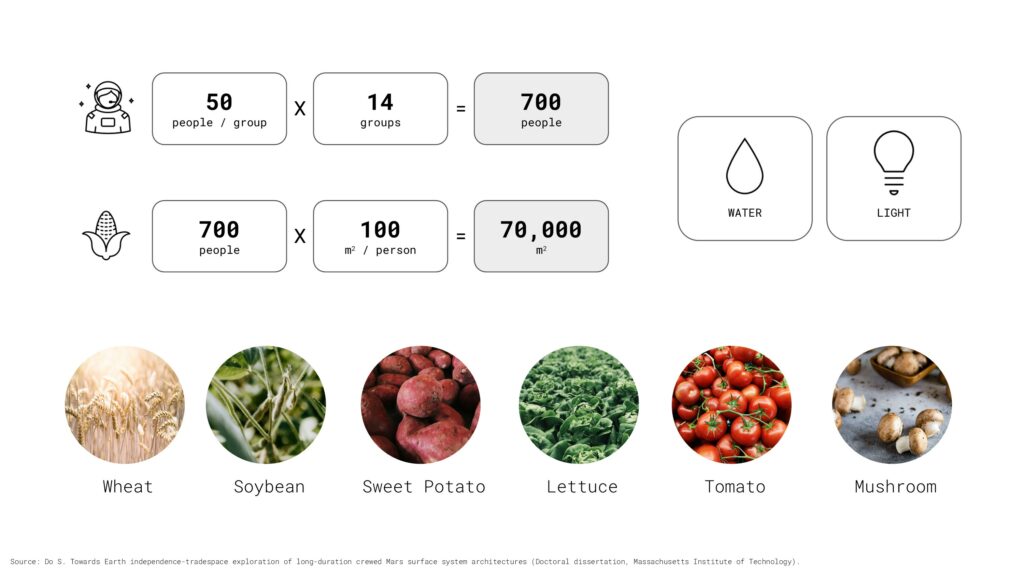
Aggregation
For the computational method of design we utilized aggregation based on the Wasp plugin for Grasshopper developed by Andrea Rossi. Our aggregation utilizes Weaire- Phelan Structures – these are two shapes of equal size that can combine to completely fill a volume – in fact under the right conditions bubbles within a shape will spontaneously form this structure4. The two structures are polyhedrons, with one named a Pyritohedron formed of 12 identical isosceles pentagons and the Tetrakaidecahedron with 14 faces comprised of four of the same isosceles pentagons, two hexagons and eight irregular pentagons, thus the entire structure comprises just three two-dimensional shapes. Henceforth we will refer to the Pyritohedron as the P-unit and the Tetrakaidecahedron as the T-unit.
Using just these two shapes we form our architectural structures as illustrated below. By using these repeated shapes we could make use of block instances in Rhino and Grasshopper, significantly reducing the memory demands of the software.
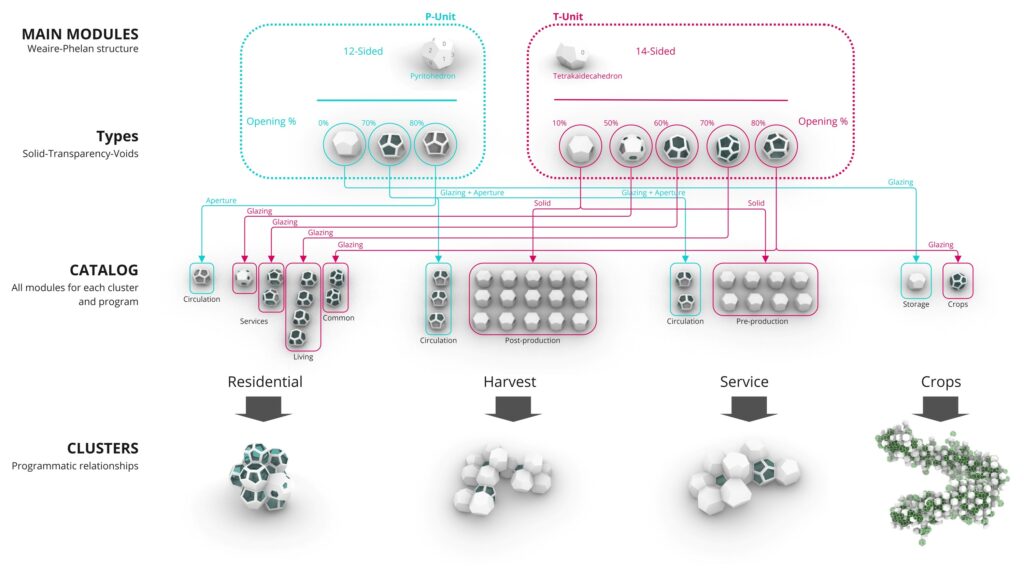
Based on our program we developed four main functions divided into clusters formed using graph-grammar aggregation:
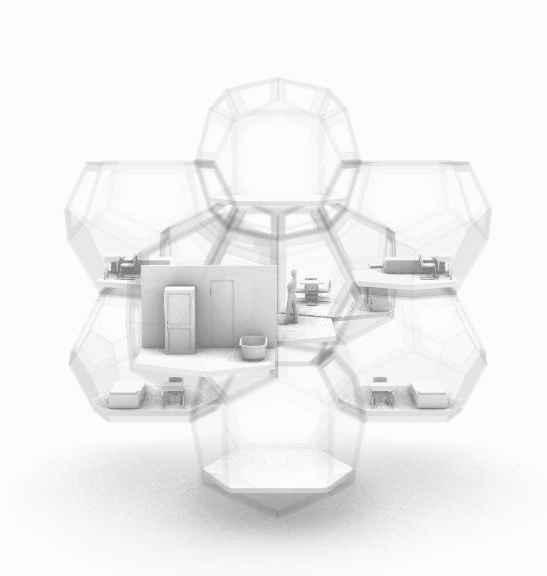
- Residential: A four-person habitat comprising sleeping quarters, kitchen, bathroom and living room.
- Phase 1: 13 clusters
- Phase 2: 25 clusters
- Phase 3: 75 clusters
- Harvest: Functions for harvesting crops, processing and packaging food, seed collection, fermentation, milling, and salt production.
- Phase 1: 3 clusters
- Phase 2: 5 clusters
- Phase 3: 17 clusters
- Service: Functions for supporting crops, composting, water recycling, seed storage and germination.
- Phase 1: 3 clusters
- Phase 2: 5 clusters
- Phase 3: 17 clusters
- Crops: Hydroponic and aeroponic pods for growing crops.
- Phase 1: 600 modules
- Phase 2: 1100 modules
- Phase 3: 3300 modules
Using graph-grammar, the clusters were formed as illustrated below.
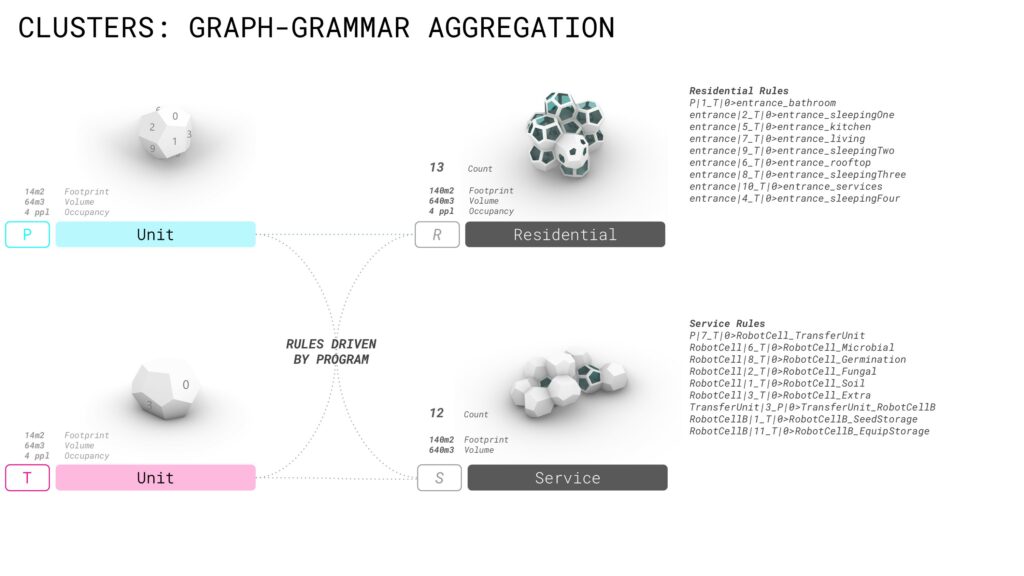
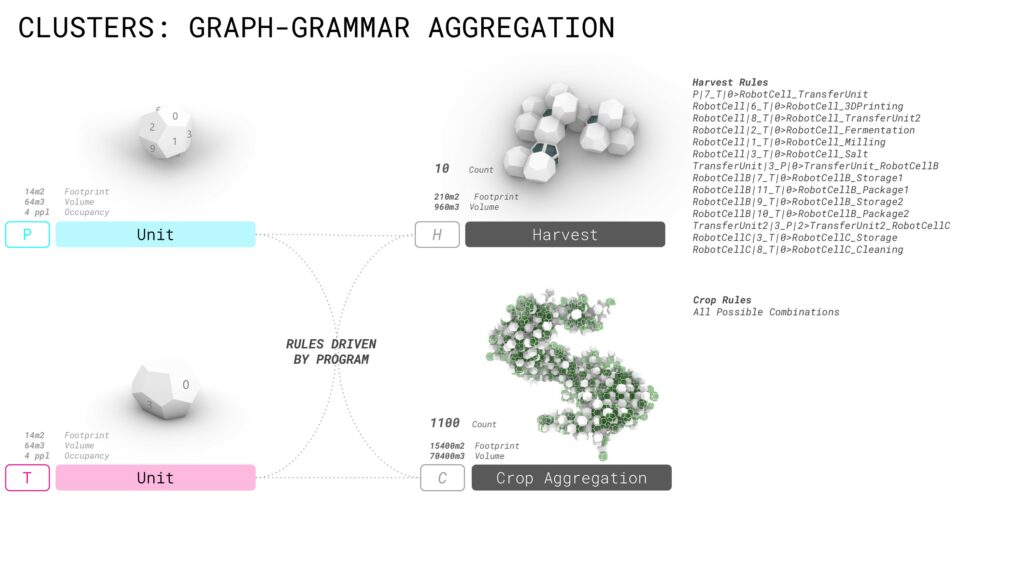
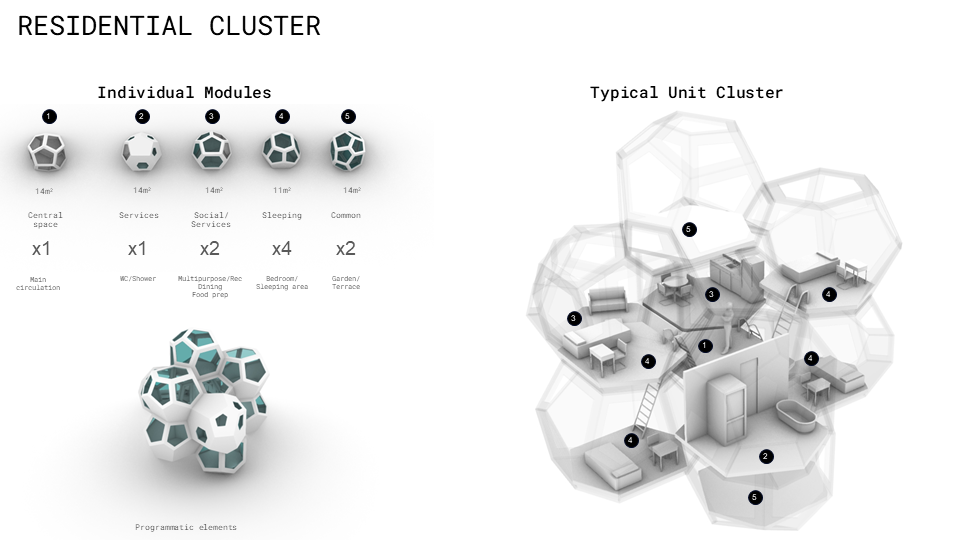
Site Organization
The aggregation is completed utilizing the Wasp plug-in within Rhino and Grasshopper. Graph-grammar rules helped define the three main clusters: residential, service, and harvest. Once the lava tube was formed, field attractors were employed to stochastically aggregate the crop modules around the central skylight and along a helix movement corridor. The movement corridor is generated as a subD mesh based on an array of concentric curves and mathematically defined helix. P-units were strateigcally transformed to pre-defined locations along the movement corridor.
The Aggreculture program was organized around a web of movement corridors that provide vertical circulation from the surface to the invert of the lava tube, and horizontally between the various chunks, while a spiral corridor provides access to the crop units situated within the skylight. Another aggregation forms a protective airlock funnel to provide shielding from gamma radiation while allowing sunlight through.
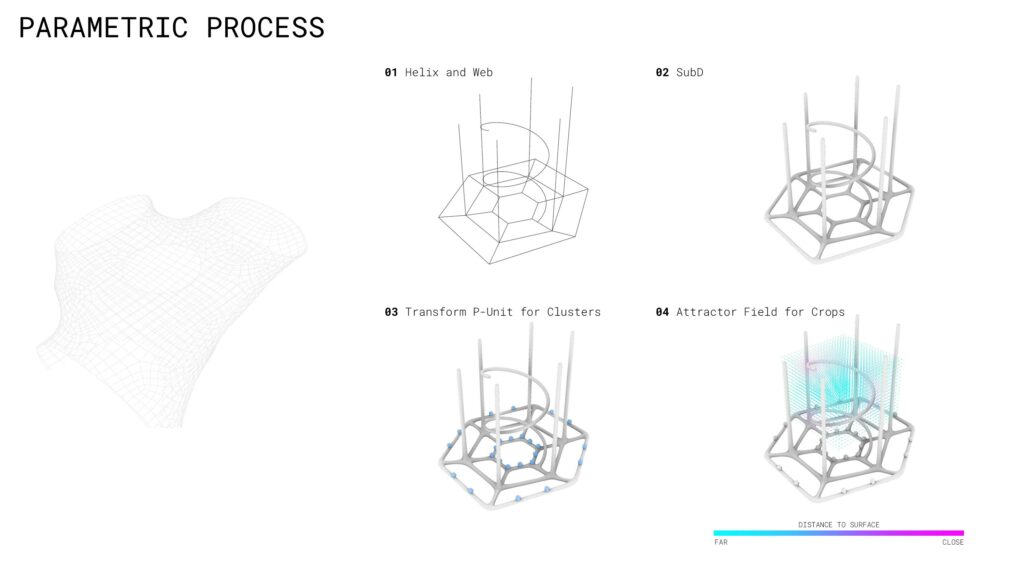
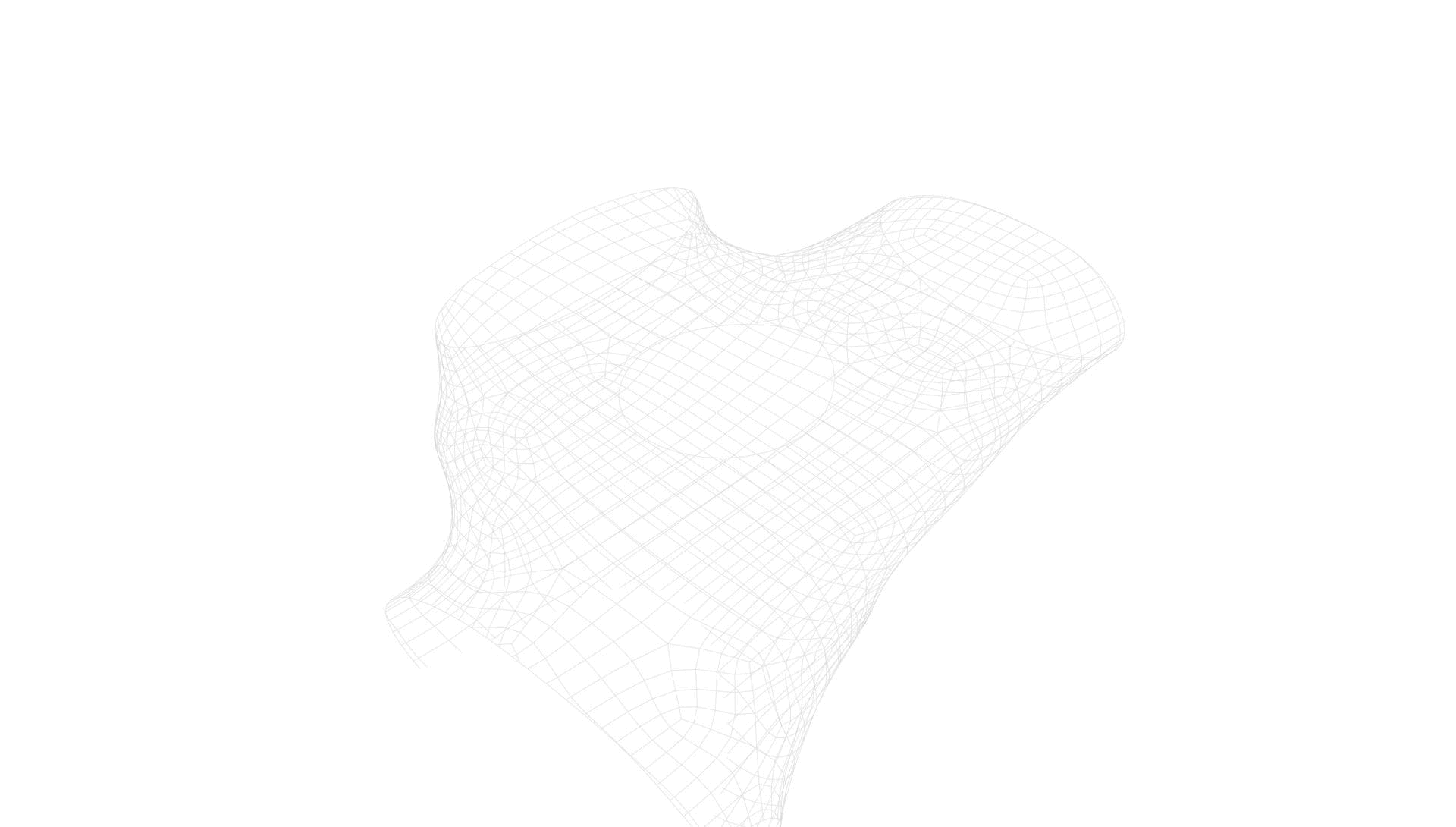
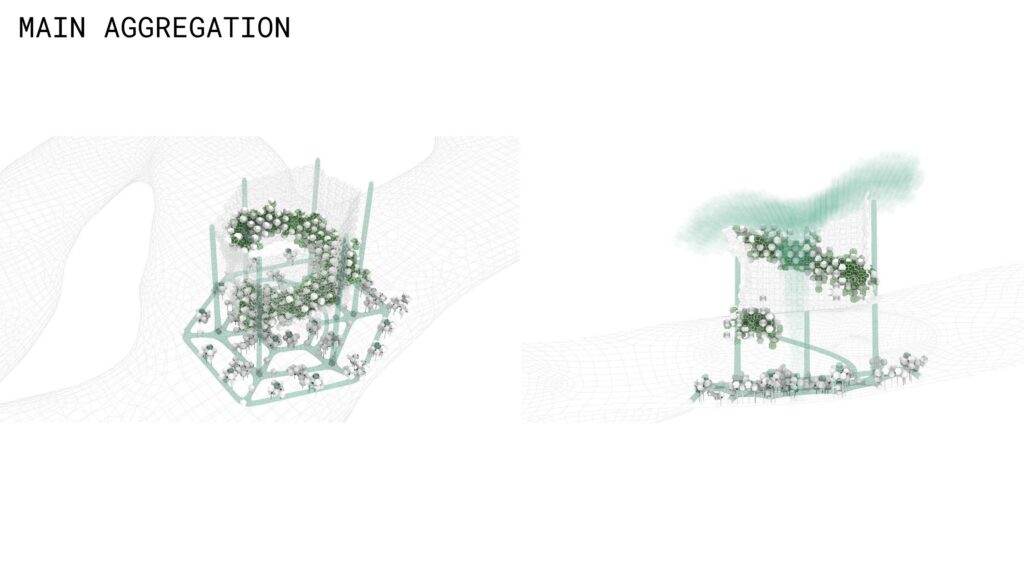
Data-Informed Aggregation: Custom Data Visualization Application
We imagined what people in a Martian food colony might need once crop production is functional. For this reason, we created a custom data visualization tool that Martians could use to track, maintain, and manage their food resources. To develop this, we utilized the Speckle connection to PowerBi which allows for flexible and customizable dashboards.
First, the main aggregation was generated in Grasshopper. ClimateStudio, an environmental analysis plug-in was used to study daylight illuminances on the crop aggregation. The crop aggregation is located in the lava tube skylight which allowed for natural illumination to reach crops, facilitating healthy crop growth with less demand for electricity. We researched the amount of light each type of crop needed, measured in photosynthetic photon flux density (PPFD), and translated into typical lux values based on daylight’s spectrum (here, we assumed an Earth atmosphere and utilized a weather file with similar a longitude and latitude as our Martian colony – this does not directly translate either sun angles, day length, or atmosphere but serves as a proof of concept).
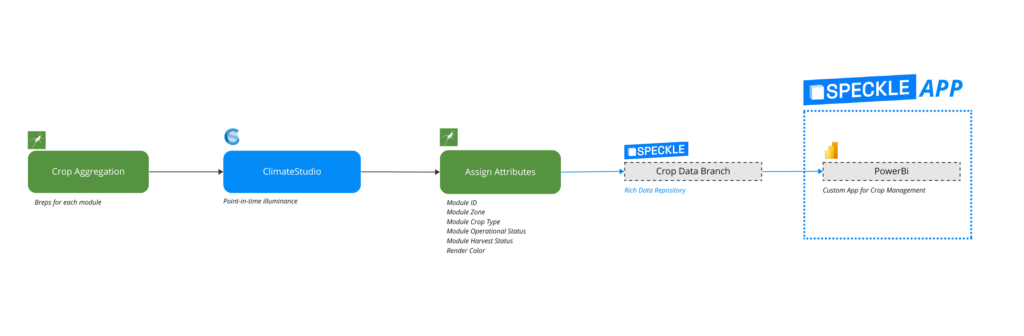
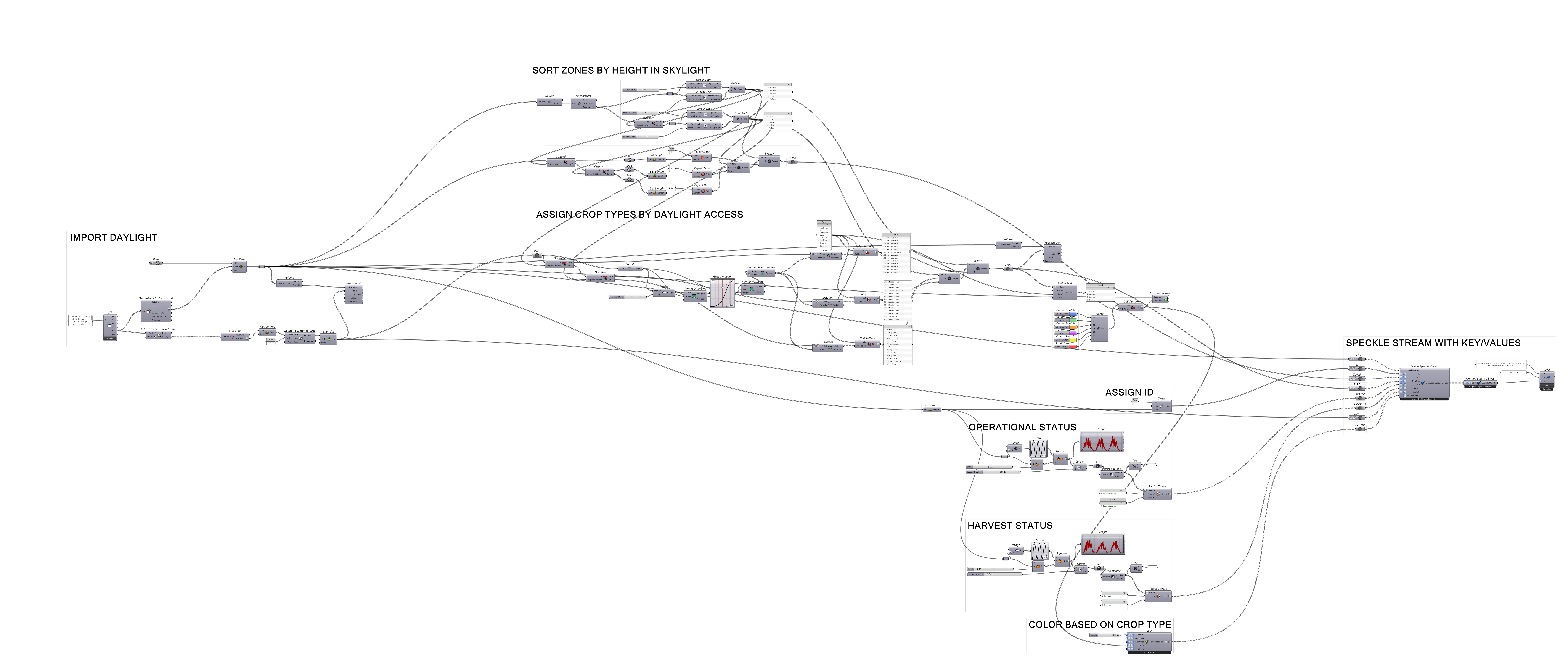
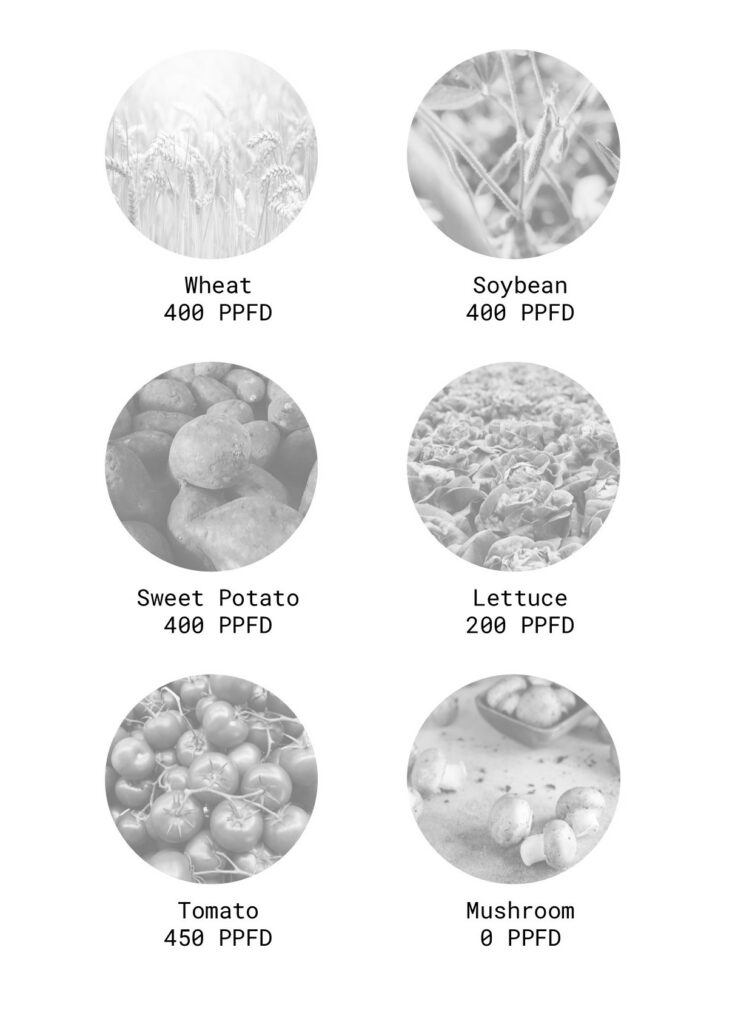
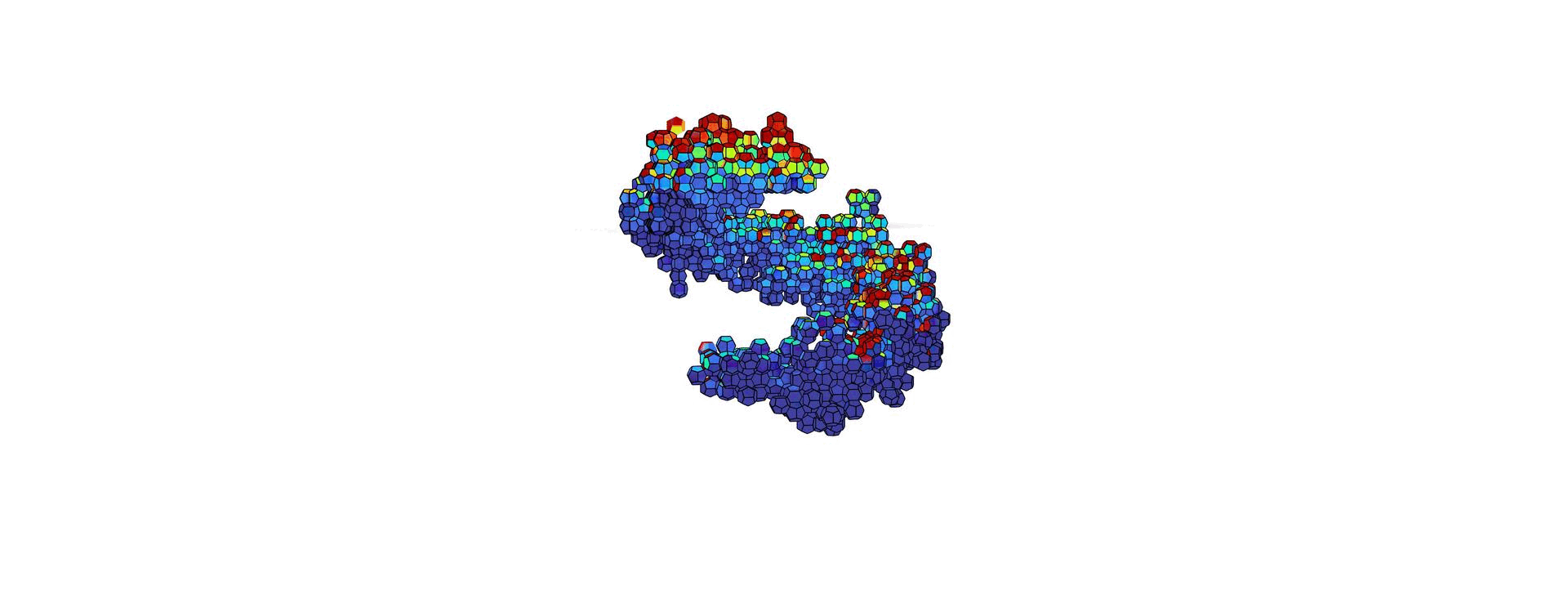

Once the daylight analysis is complete, we used that data to sort and organize the crop modules. For instance, the tomato modules were spatially located where there was the most daylight and mushrooms, the least. Grasshopper was used to manage this data set as well add additional module information, including:
- Daylight Access
- Crop Type
- Crop Module ID
- Crop Module Zone
- Operational Status
- Harvest Status
There attributes were assigned to each respective crop module as a Speckle extended object in Grasshopper. Once streamed to Speckle, PowerBi was used to visualize the 3D geometry and display the above traits in a compelling and interactive way. In this method, Martians crop managers could quickly understand the location, health, and other important information about the crops.
There are promising opportunities for further development. For one, the entire Grasshopper data management script could be automated using something like a Speckle Bot which would “listen” for an aggregation to be streamed to Speckle. The bot would then perform the daylight analysis, automatically sort and assign attributes to the respective crops, and stream the data-rich geometry back to Speckle for use and auto-update in PowerBI.
Secondly, external third-party data sets could be tied into the PowerBi data query and dashboard. For instance, oxygen, H2O, and occupancy sensors in each module would send real-time feedback to the Crop Management app, for a real-time understanding of module health. If crops needed to rotate or modules re-purposed for another crop, more data could be built into the app to allow for each management of complex geometry and layered data sets.
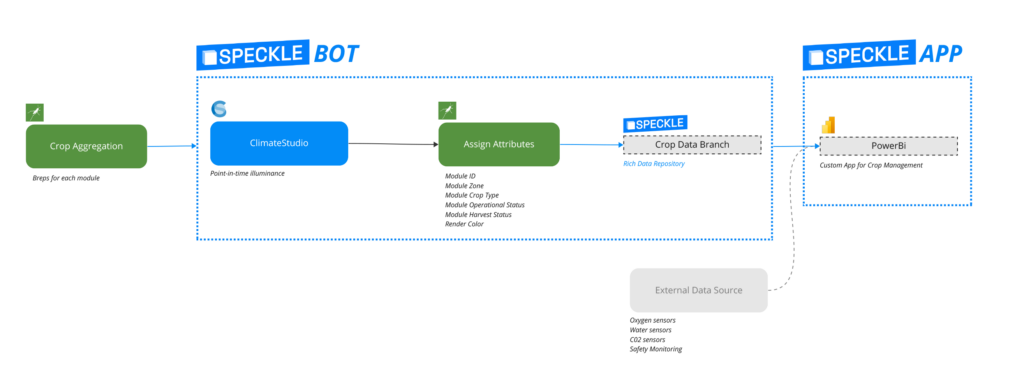
In situ resource utilization
One of the major obstacles to building on Mars is the limited availability of liquid water, this precludes the use of the most ubiquitous construction material on Earth, concrete, and poses a challenge to those additive manufacturing methods reliant on binders. Additive manufacturing methods are also unable to provide the sealed and impervious structures required to establish a safe pressurized habitat for life. Analysis of the resources available locally on Mars finds that the regolith is comprised of around 45% silicon dioxide, and about 20% iron oxide. Utilizing enhanced electrowinning the soil can be refined to provide the raw materials for making steel and glass in the absence of water.
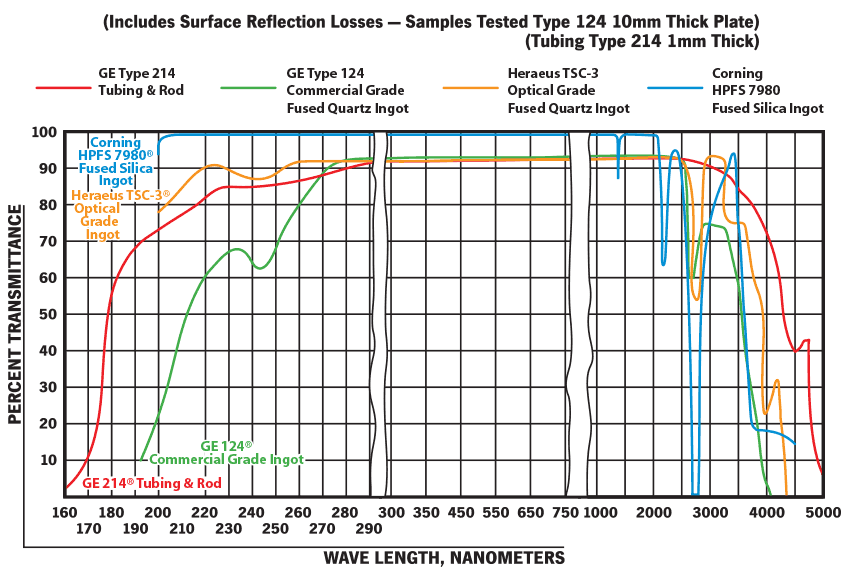
Blown glass provides an inherently pressure holding form well suited to the regular forms of the aggregation, and by crushing glass and mixing it with foaming agents (CaO or carbon black) glass foams can be produced during annealing. Combining glass with glass foam allows us to leverage the high strength of glass and the toughness of glass foams to provide a structural insulating panel. Where gamma radiation protection is required the glass can be doped with bismuth oxide6, which may be required to be sent from Earth. Below we provide an early concept of the combined digger, refining and glass blowing robot, for clarity the annealing chamber and vacuum form are not shown.
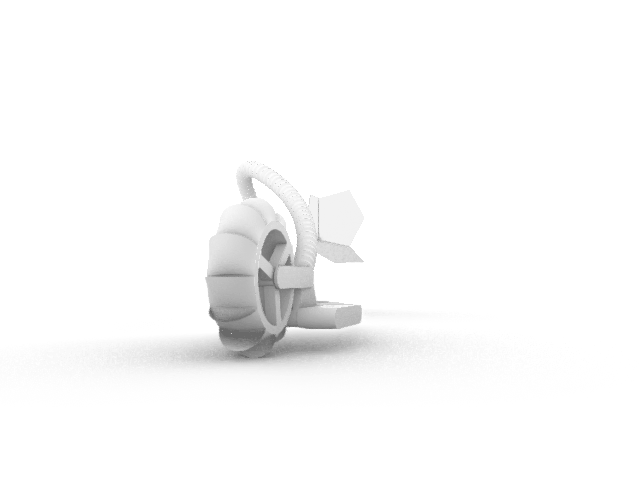
Preliminary structural analysis found that the deflection of glass units is not within acceptable tolerances, so the structural insulating panels are proposed to be combined with 3d printed steel frames. Below we illustrate the manufacturing sequence, this would be undertaken within an insulated pressure and temperature controlled chamber.
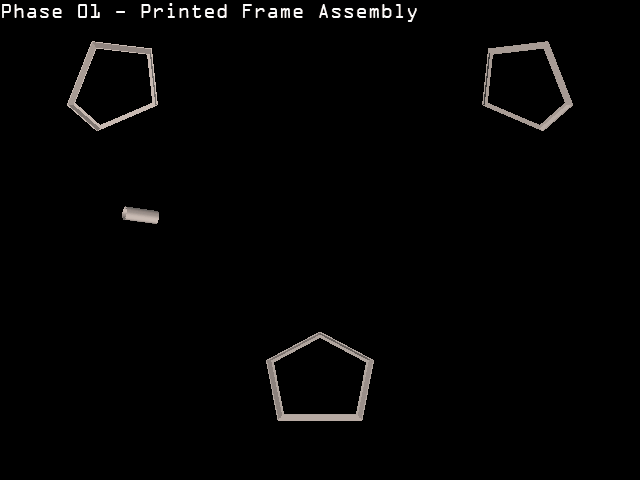
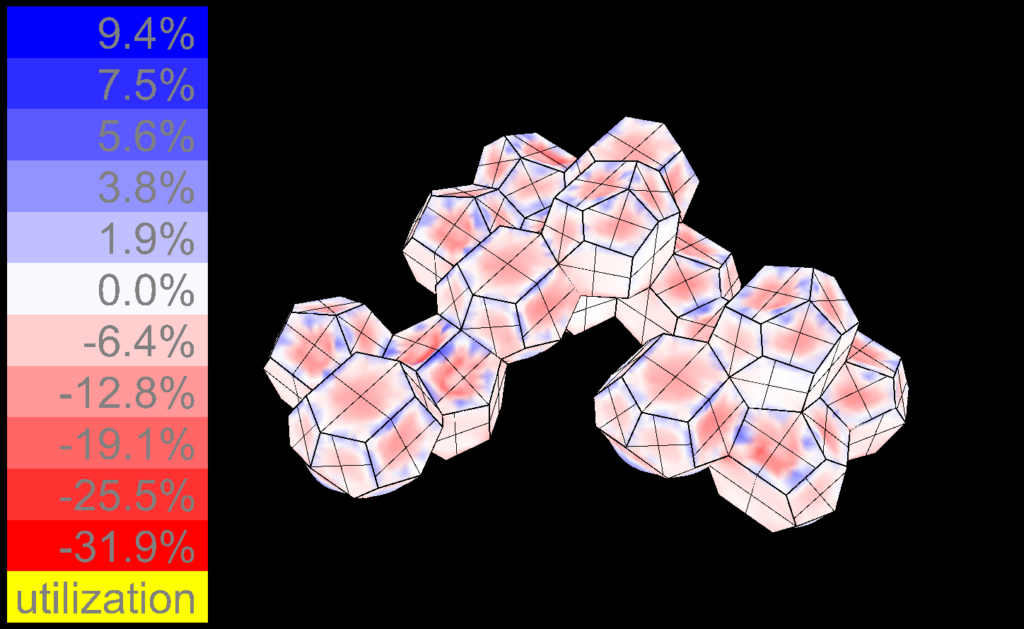
It is noted that the volume of insitu material use would require significant energy input, which we speculate would be provided by one or more Type IV carbon-dioxide cooled modular nuclear reactor delivered from Earth.
Construction Phasing
We aim to excavate down to the lava tube, utilizing the removed material as an insitu resource. This is expected to take almost five years of robotic construction prior to the human based mission. For phasing our initial program allows for 50 farmers feeding the initial 700 residents of the colony. In Phase 2 the program is densified within the lava tube to accommodate 100 farmers feeding 1400 residents. For Phase 3 new skylights are excavated and the parametric design replicated at those locations.
Documentation
Our group utilized Rhino.Inside Revit exclusively to document complex aggregation geometries. Speckle was used to send and receive the aggregated planes so we could recover the geometry’s vertices and centers. Each cluster and crop module is based on six different adaptive families. Our base module shapes allowed us to parametrically design adaptative “penta” and “hexa” panels, both with and without glazing, to construct the geometry. Parametrics include cluster name, shape, materials, solid panel area, and glazing area.
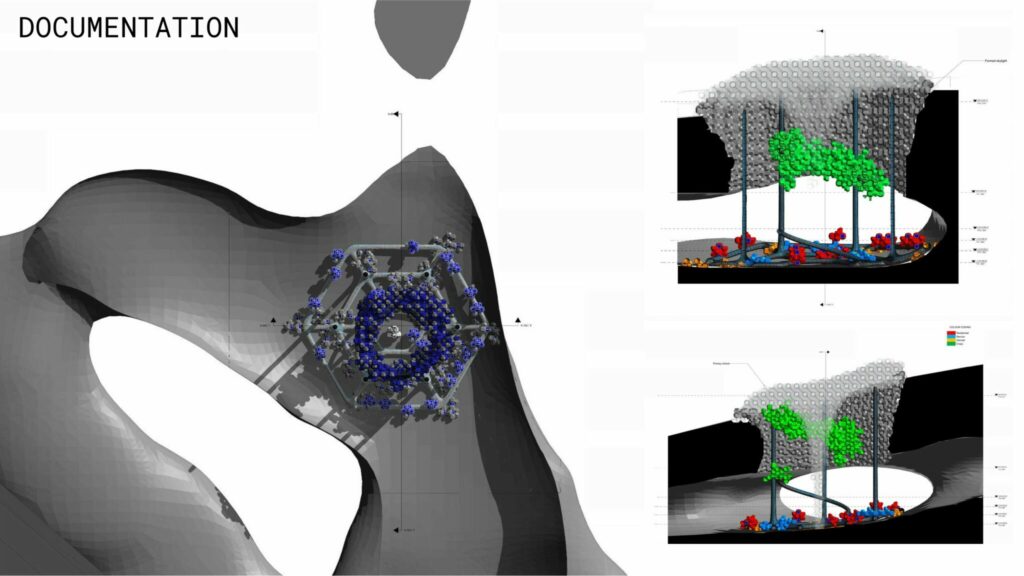
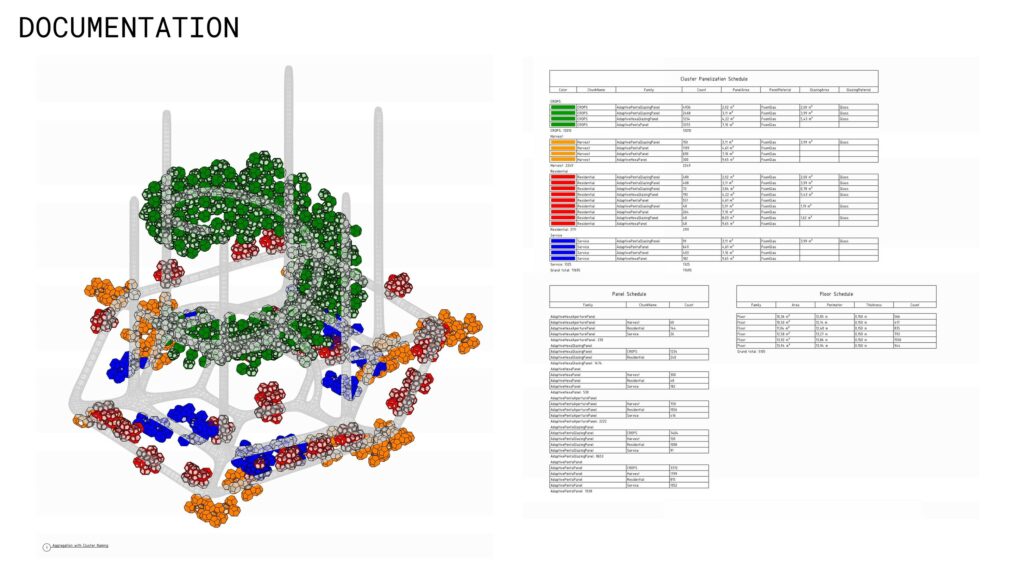
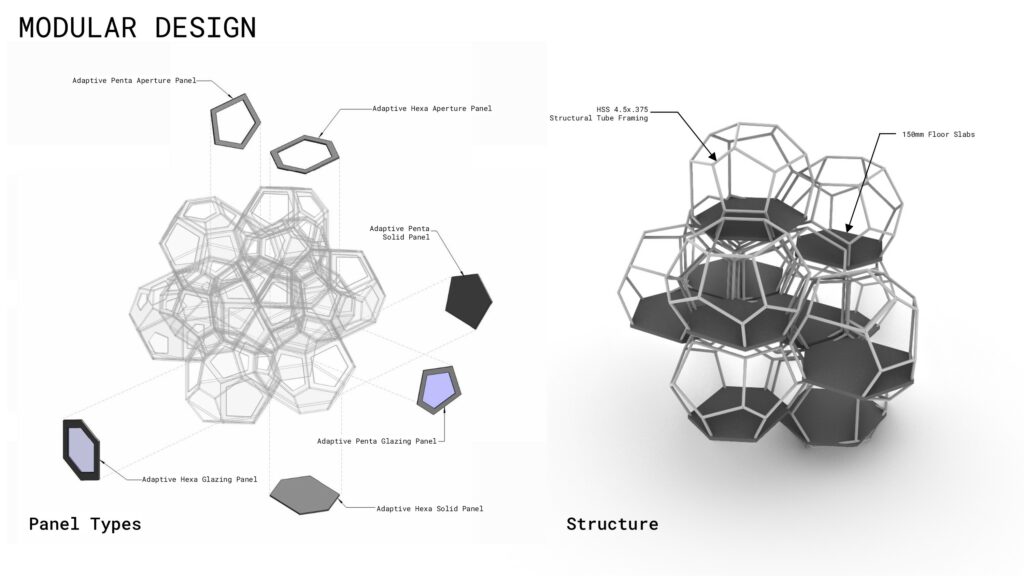
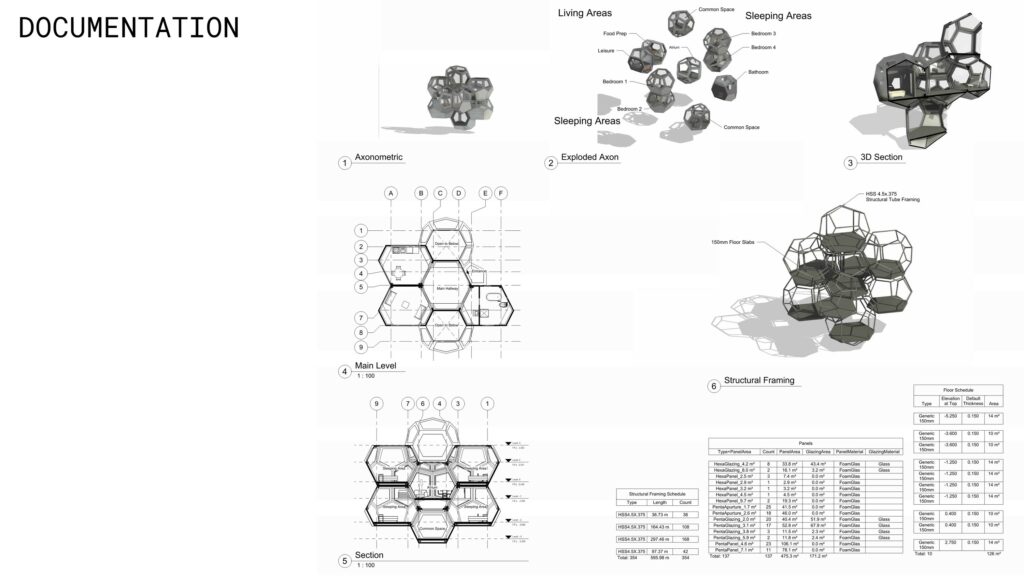
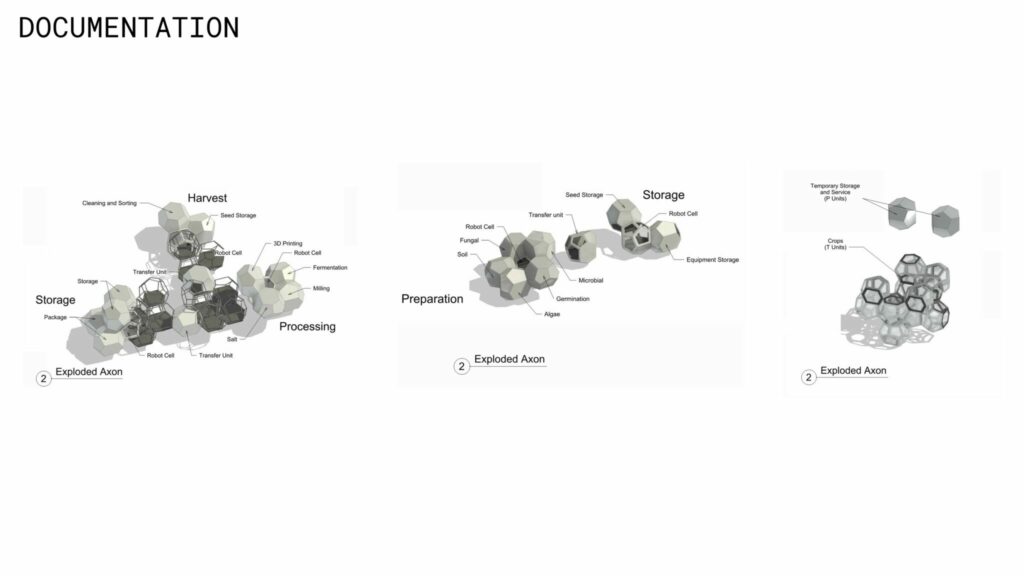
Renders
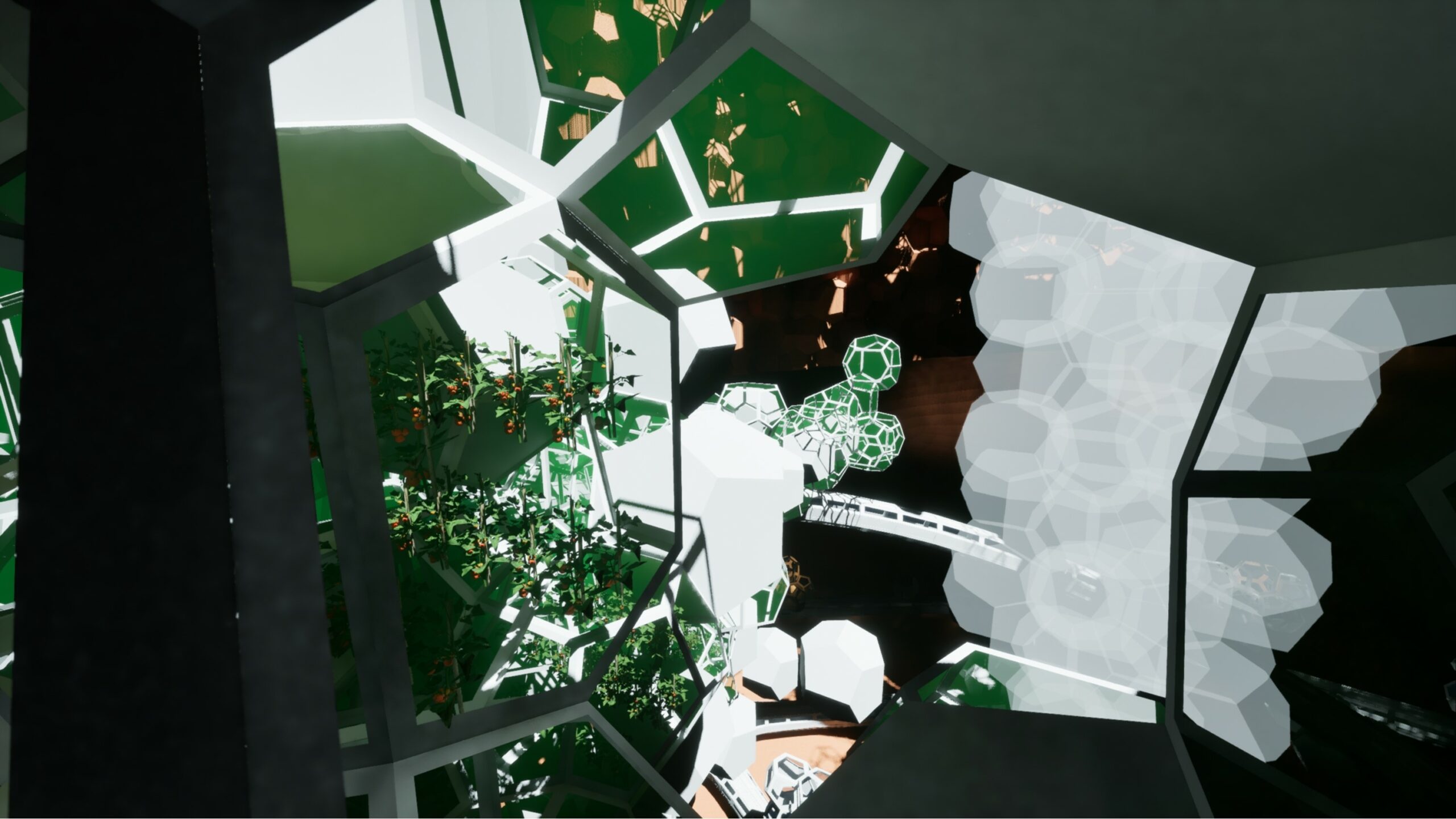
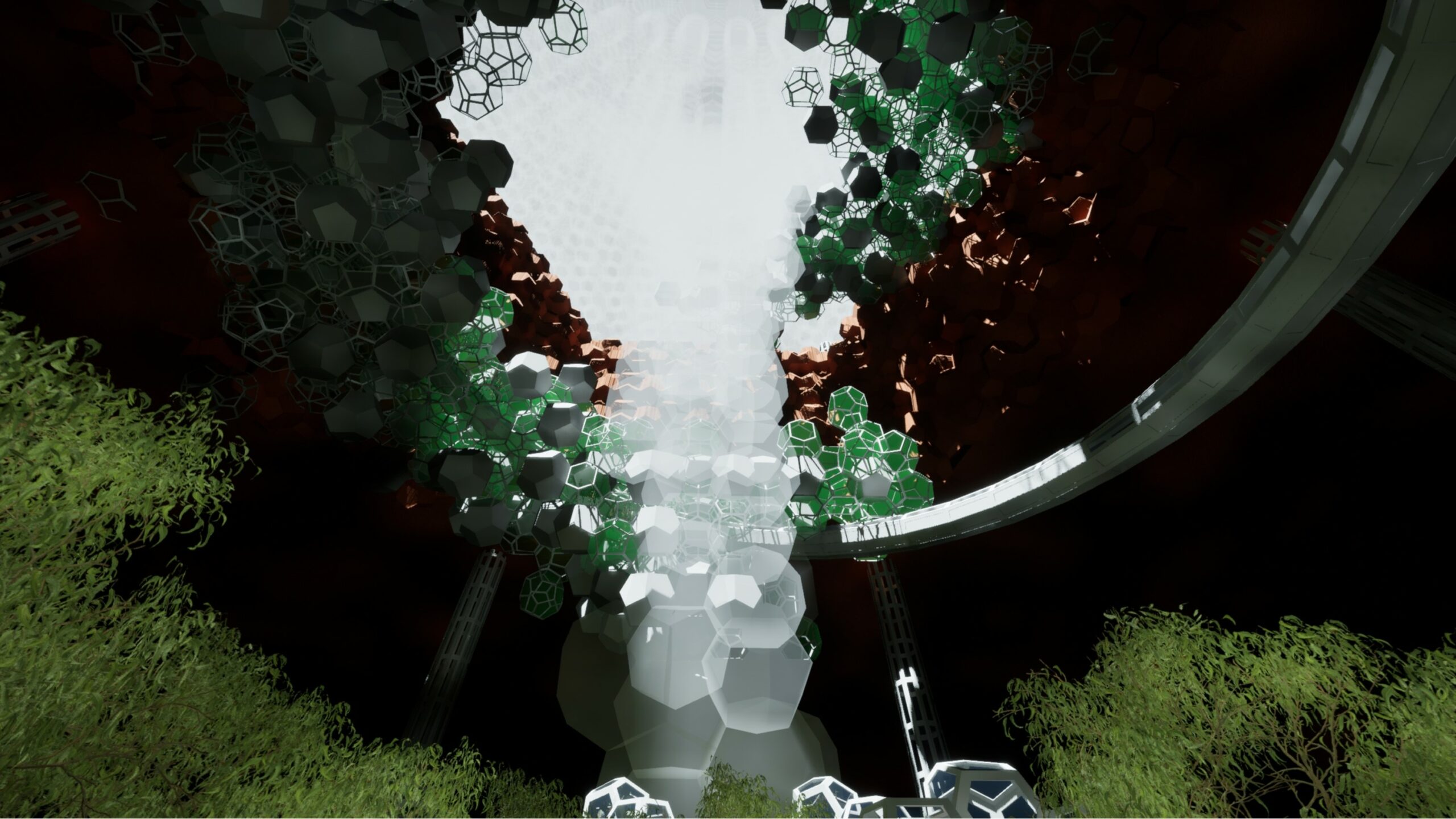
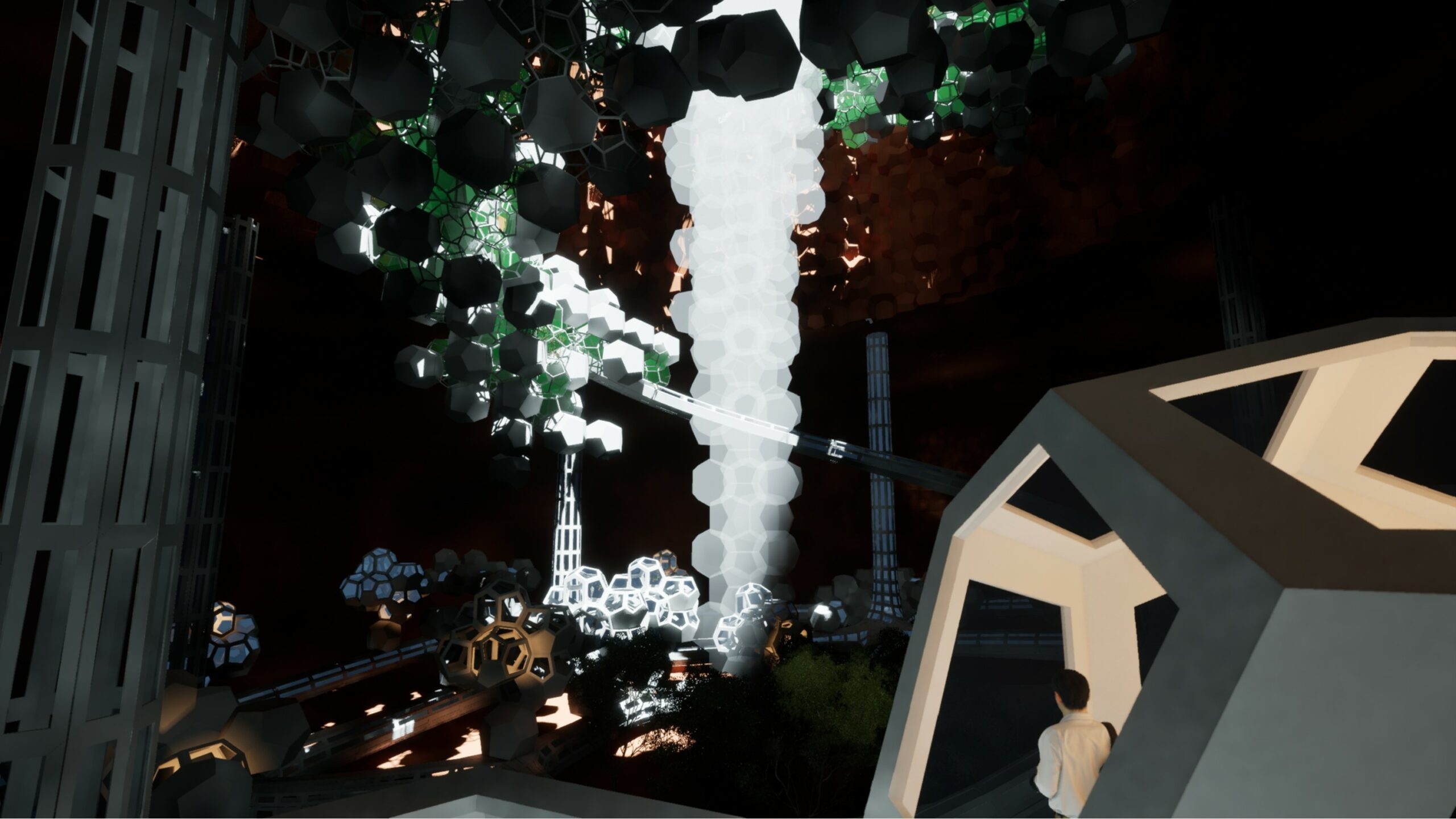
Postscript
Following structural review of the Aggreculture project concerns were raised regarding the integrity of the airlock structure. Analysis undertaken using Karamba3d found deflection that exceeded acceptable tolerances7. We have prepared a concept of tension struts anchored into the skylight to provide additional support for the airlock shown in blue below, conceptually these could be formed from glass fibre.
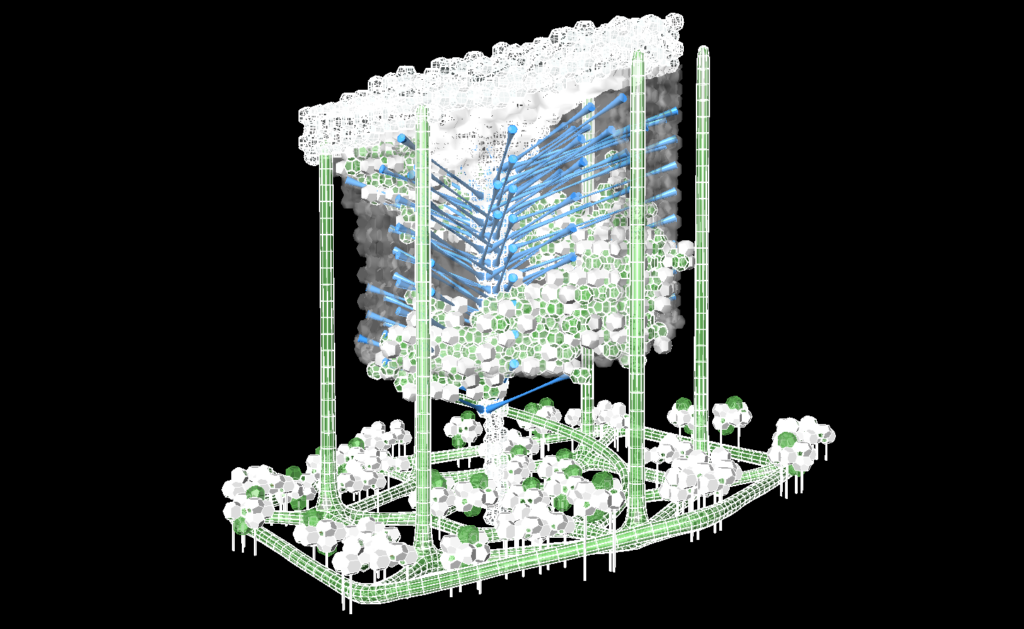
- Jones, H., “Matching Crew Diet and Crop Food Production in BIO-Plex,” SAE Technical Paper 2000-01-2397, 2000,https://doi.org/10.4271/2000-01-2397.
↩︎ - Gutierrez-Jaramillo, Antonio Alberto. “Bioregenerative Food Production System: Using integrated food production systems to feed the future.” PhD diss., The University of Arizona, 2021. ↩︎
- Do S. Towards Earth independence-tradespace exploration of long-duration crewed Mars surface system architectures (Doctoral dissertation, Massachusetts Institute of Technology). ↩︎
- Naga N, Jinno M, Wang Y, Nakano T. The first space-filling polyhedrons of polymer cubic cells originated from Weaire-Phelan structure created by polymerization induced phase separation. Scientific reports. 2022 Nov 9;12(1):19141. ↩︎
- https://technicalglass.com/fused-quartz-transmission/ accessed 2024-04-02 ↩︎
- Rammah YS, Sayyed MI, Ali AA, Tekin HO, El-Mallawany R. Optical properties and gamma-shielding features of bismuth borate glasses. Applied Physics A. 2018 Dec;124:1-9. ↩︎
- Jóźwik A. Introduction to structural design of glass according to current European standards. Archives of Civil Engineering. 2022:147-70. ↩︎