In an era dominated by concrete and steel, the Sticks & Stones project revisits the architectural potential of stone and timber—materials with a rich historical legacy—through the precision of robotic fabrication. This initiative sought to develop a reversible, precise architectural system that bridges traditional craftsmanship with advanced digital tools. By tackling the challenges of natural materials, we aimed to create a methodology that respects their inherent properties while leveraging technology to unlock new possibilities. This post explores the historical context, material choices, technical workflow, joint design, prototype evolution, and the broader implications of this endeavor.
—


Historical Context: The Enduring Legacy of Stone and Timber
Stone and timber have shaped human construction for millennia, their use deeply embedded in the architectural heritage of civilizations worldwide. In Europe, stone formed the backbone of monumental structures—cathedrals like Notre-Dame, bridges like Lisbon’s Ponte de Lima, and fortifications like the walls of Carcassonne—owing to its compressive strength and permanence. Timber, prized for its workability and tensile capacity, complemented stone as framing, roofing, and connective elements. Together, they embodied a synergy of durability and adaptability, honed by artisans whose skills were refined over generations.
The advent of the Industrial Revolution, however, shifted construction toward mass-produced materials like concrete and steel. These offered scalability, uniformity, and speed, enabling the rapid urbanization of the 19th and 20th centuries. Yet this transition came at a cost: the decline of stone and timber sidelined a craft-based knowledge system attuned to local resources and ecological balance. By the mid-20th century, traditional masonry and carpentry had largely been relegated to niche or heritage projects, overshadowed by the efficiency of industrial methods.
The Sticks & Stones project emerged from a desire to reconsider this trajectory. Could stone and timber, with their tactile richness and sustainability, reclaim a place in modern construction? Rather than romanticizing the past, we sought to reframe these materials through robotic fabrication, blending historical wisdom with contemporary precision. This approach positions stone and timber not as relics, but as viable components in a forward-looking architectural paradigm.
—

Material Roles: A Structural Hierarchy
Our design philosophy established a clear structural hierarchy between stone and timber, reflecting their traditional roles while adapting them to a robotic workflow. Stone, with its exceptional compressive strength—typically exceeding 100 MPa for sandstone—was designated as the primary load-bearing element. Its mass and stability made it ideal for anchoring forces, serving as the foundation of our system. Timber, with its tensile strength (around 40-50 MPa for spruce) and flexibility, was cast as the secondary material, acting as connectors between stone components.
This division leveraged the inherent properties of each material. Stone’s rigidity provided a stable base, while timber’s workability enabled precise, adaptable joints. This interplay mirrors historical construction—think of medieval trusses resting on stone piers—but reimagines it through digital precision. By respecting material agency, we allowed stone and timber to perform roles aligned with their natural behaviors, fostering a system that feels both organic and engineered.
—

Reimagining Tradition: Stone and Wood 2.0
The Sticks & Stones project was not about replicating historical methods but about advancing them. Traditional stone and timber construction relied on manual skill: masons carved blocks to fit snugly, while carpenters crafted mortise-and-tenon joints with hand tools. These techniques, while masterful, were time-intensive and constrained by human limitations. Robotic fabrication, by contrast, offers unparalleled accuracy and repeatability, enabling complex geometries and tight tolerances that would challenge even the most skilled artisan.
Our ambition was to harness this precision to create a new vocabulary of joinery. By using robots to chisel stone and CNC machines to mill timber, we developed dry, reversible connections that merge structural integrity with aesthetic refinement. This approach transforms stone and timber into a hybrid system—rooted in tradition yet elevated by technology—capable of meeting modern demands for efficiency and adaptability.
Material Selection: Stone—Embracing the Irregular
Choosing the right stone was pivotal, as its properties shaped both design and fabrication. Stone varies widely: granite is dense and hard (Mohs 7-8), limestone softer and more porous (Mohs 3-4), and sandstone strikes a middle ground (Mohs 6-7). We selected sandstone for its consistent grain and carvability, which minimized tool wear and fracture risk during robotic chiseling. Its compressive strength (typically 60-120 MPa) also suited our load-bearing requirements.
Rather than using uniform quarry blocks, we opted for found stones—irregular, unprocessed pieces sourced locally. This choice embraced natural variability, testing our system’s adaptability to real-world conditions. Found stones introduced challenges: uneven surfaces, unpredictable densities, and hidden flaws complicated scanning and chiseling. Yet they also enriched the project, pushing us to develop a methodology that could handle imperfection, a critical step toward scalability beyond controlled lab settings.

Material Selection: Timber—Standardization for Precision
Timber posed different considerations. Its properties—grain direction, moisture content, and species-specific strength—can vary significantly. To focus on the stone-to-timber interface, we standardized our timber input, selecting softwood profiles. Soft wood, with a compressive strength of 40-50 MPa and shear strength of 6-8 MPa, offered reliability and ease of machining. Its light weight (density ~450 kg/m³) and straight grain reduced warping risks, ensuring consistent CNC milling outcomes.
Standardisation minimised experimental variables, allowing us to refine joint precision without grappling with timber’s natural inconsistencies. Soft wood’s availability and affordability also aligned with practical application, making it a pragmatic choice for a system intended to inspire broader adoption.

Workflow: A Three-Phase Iterative Process
The Sticks & Stones workflow unfolded in three phases—design, fabrication strategy, and fabrication—each linked by iterative feedback loops to refine our approach.
1. Design Phase
We began by scanning found stones with LiDAR, creating high-resolution 3D models or “digital twins.” These meshes, accurate to within 1 mm, captured each stone’s topology, enabling virtual joint design in Rhino and Grasshopper. Simulations tested load paths and fit, ensuring designs were feasible before physical execution.
2. Fabrication Strategy Phase
Using the digital twins, we generated toolpaths tailored to each material. For timber, RhinoCAM produced CNC milling paths, specifying spindle speeds (e.g., 12,000 RPM) and feed rates (e.g., 2,000 mm/min). For stone, we calculated robotic chiseling trajectories, factoring in tool diameter (20 mm), stepover (5 mm), and material removal rates (approximately 50 cm³/min). This phase bridged virtual intent with physical reality.
3. Fabrication Phase
Timber was milled on a 3-axis CNC, while stone was chiseled by a KUKA robotic arm equipped with a custom pneumatic chisel. Post-fabrication, we conducted verification scans to compare outcomes against designs, adjusting toolpaths as needed. This closed-loop process ensured precision despite material variability.
This workflow’s strength lay in its adaptability, allowing us to respond to unexpected challenges—like stone fractures or tool wear—in real time.

Design Logic: Degrees of Freedom
To manage irregular stone, we framed our system around degrees of freedom, classifying stones by their structural roles:
- 1D (Linear Connections): Stones as endpoints for timber beams, transferring loads along a single axis.
- 2D (Planar Surfaces): Stones defining edges or corners of flat assemblies, like walls.
- 3D (Volumetric Enclosures): Stones anchoring spatial frameworks, supporting multi-directional forces.
Starting with 1D connections, we scaled complexity incrementally, isolating variables to refine techniques. This modular logic provided a scalable foundation, adaptable to diverse architectural applications.
—

Digital Tools: Stone Library and Orientation
Designing with irregular stone demanded robust digital infrastructure. We built a library of LiDAR-scanned stones, each stored as a 3D mesh with metadata (volume, mass, surface area). To orient stones for fabrication, we developed an auto-orientation script integrating multiple methods:
- Kangaroo Simulations: A Grasshopper plugin modeled resting positions based on center of mass and contact points, ensuring stability.
- Geometric Analysis: Algorithms minimized overhangs and maximized bed contact, reducing chiseling risks.
- Machine Learning: Trained on prior scans, an ML model predicted optimal orientations for complex stones, improving efficiency.
This hybrid approach ensured stable, repeatable setups, critical for robotic precision.

Joint Design: Bridging Stone and Timber
The joint system was the linchpin of our assembly, mediating between irregular stone and uniform timber. It addressed three priorities:
- Load Transfer: Timber pegs slotted into stone recesses, distributing compressive and shear forces.
- Error Tolerance: Flexible timber elements absorbed minor chiseling deviations (up to 2 mm).
- Assembly Ease: Tapered joint profiles guided insertion, simplifying construction without fasteners.
Our initial design, tested in Prototype 3, balanced these goals, though ongoing iterations explore enhanced geometries for varied loads.
– —

Timber Fabrication: CNC Precision
Timber components were milled on a 3-axis CNC using a 10 mm end mill. Custom jigs and vises ensured multi-face alignment, achieving tolerances of ±0.2 mm. This precision enabled tight, reversible fits with stone joints, minimizing post-processing.

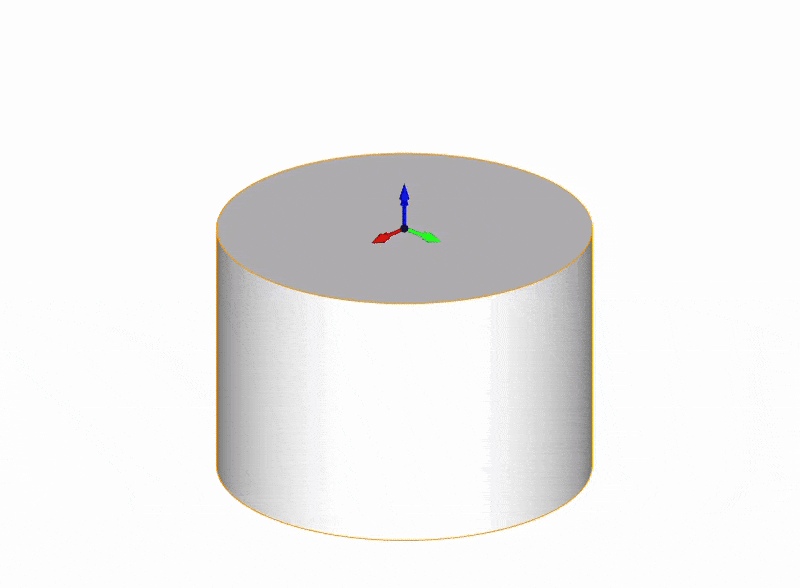
Stone Fabrication: Robotic Chiseling Challenges
To understand manual chiseling, we built a sensor-based chisel system to track movements and forces. Coupled with visual data and insights from a master stonemason, this informed our development of robotic equivalents for stone cutting.



Chiseling revealed material dynamics: vertical cuts sloped due to grain, and removal patterns varied with density. Verification scans post-chiseling adjusted subsequent passes, maintaining tolerances within 1-2 mm. These adaptations highlighted stone’s unpredictability, a key lesson in robotic craft.

A precise robotic setup required accurate stone registration. We used a three-scan method and developed a custom clamping system to maintain stability and allow clear robotic access during chiseling.

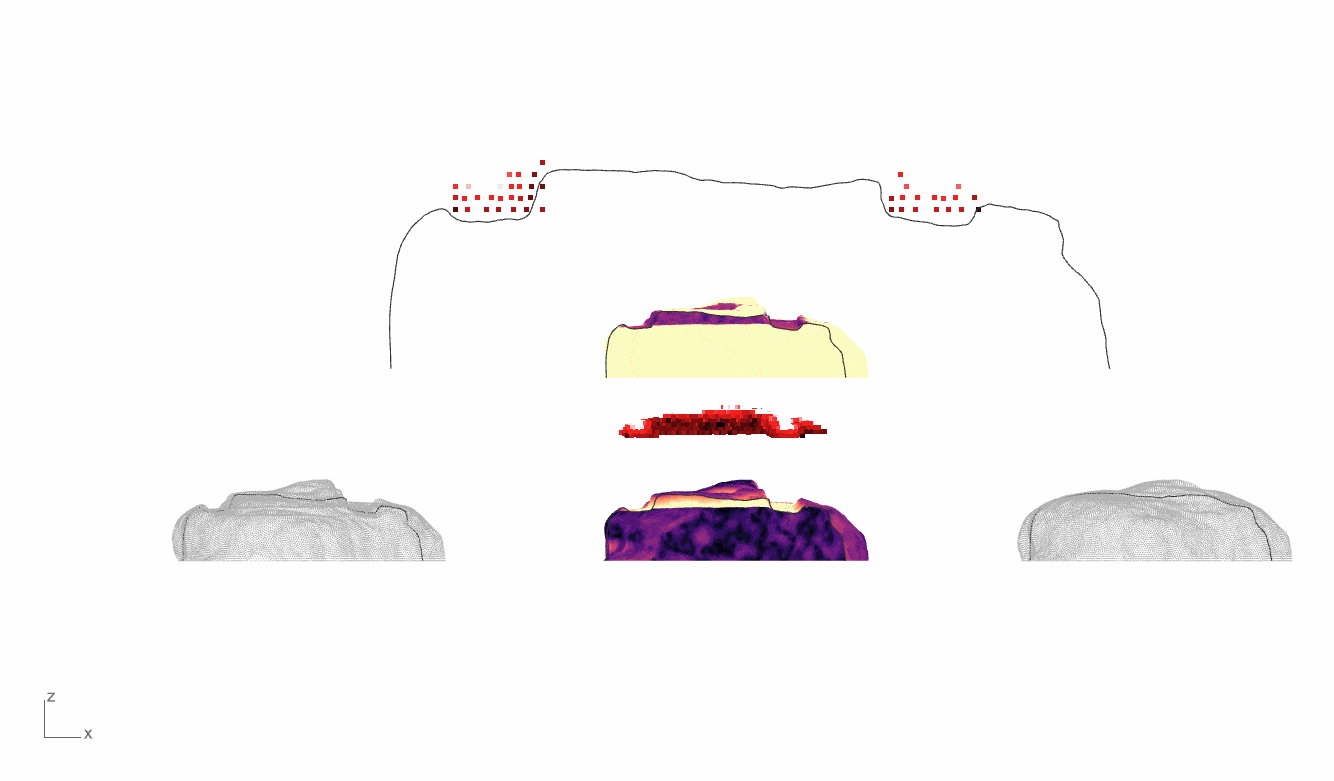
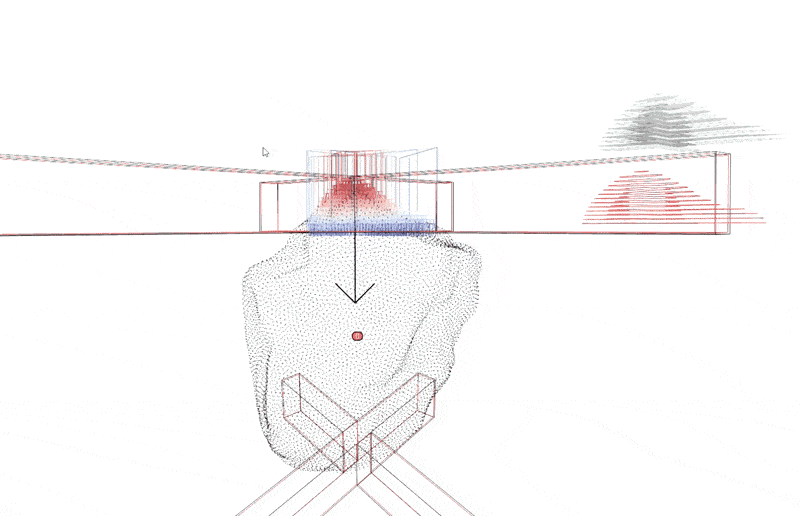
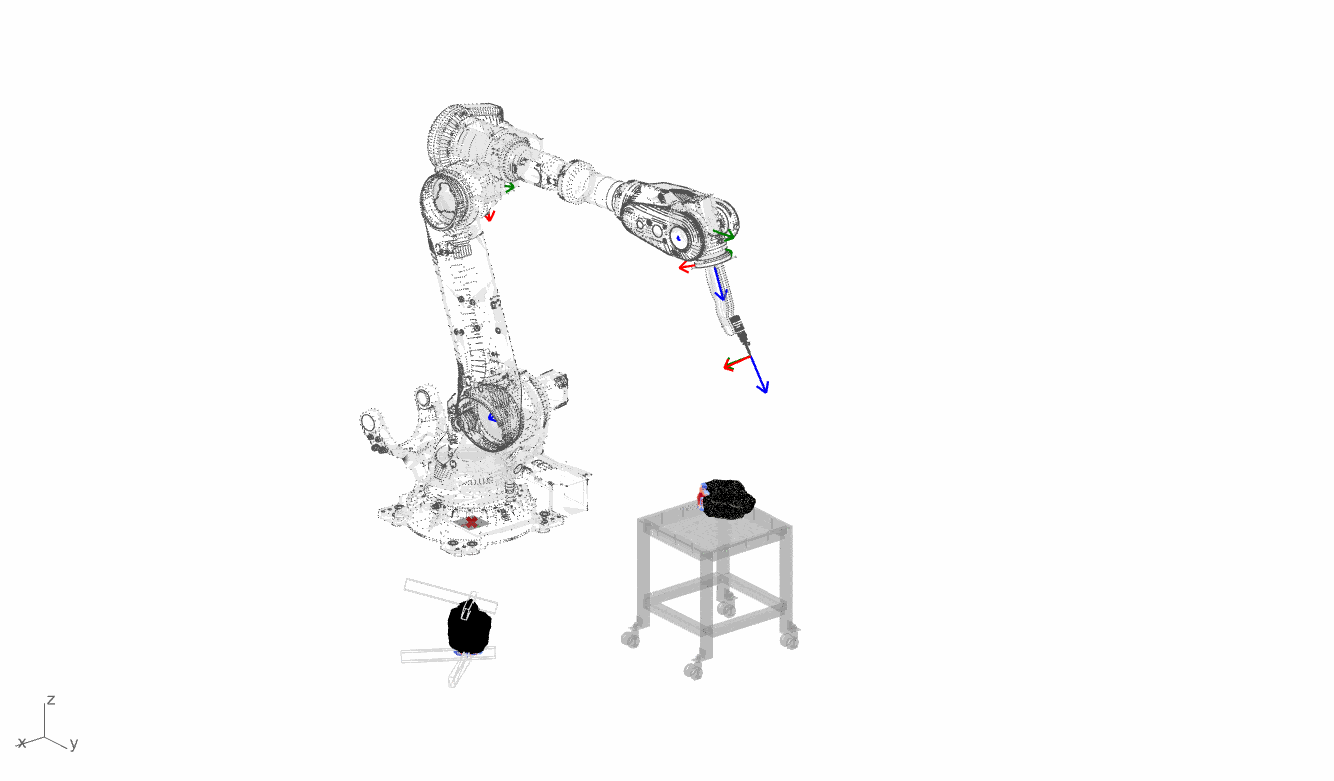
Real-world chiseling revealed inconsistent behaviors, such as sloped cuts and pressure-driven material loss. These dynamics challenge predictive modeling, especially when stone composition varies across a single piece.

Prototypes: Evolution Through Iteration
Three prototypes traced our progress:
- Prototype 1: Surface Fit
A timber groove mirrored a stone’s scanned surface. Limited scan resolution (2 mm) and milling precision caused tight fits, prompting a shift to error-tolerant joints.

- Prototype 2: Error Compounding
Robotic chiseling joined CNC-milled timber, but tolerances (±3 mm in stone, ±0.5 mm in timber) misaligned components. We simplified timber designs to focus on stone accuracy.

- Prototype 3: Reversible Success
Eight joints across four stones connected with timber pegs formed a stable, dry assembly. Minor errors (1-2 mm) persisted, but the system proved functional, validating our approach.

Reflections and Future Directions
Sticks & Stones began with a vision of seamlessly uniting tradition and technology. Prototyping revealed that natural materials resist total control, requiring a balance of precision and flexibility. The final system—precise stone chiseling paired with simplified timber—offers a scalable model for sustainable construction.
For the industry, this suggests robotic fabrication can enhance, not replace, craft. Future work could explore larger assemblies, varied stone types, or automated error correction, pushing the boundaries of robotic craft further.

Project Team
Nacho Monereo, Neil Trouw , Santosh Prabhu
Faculty
Edward Cabay, Pit Siebenaler
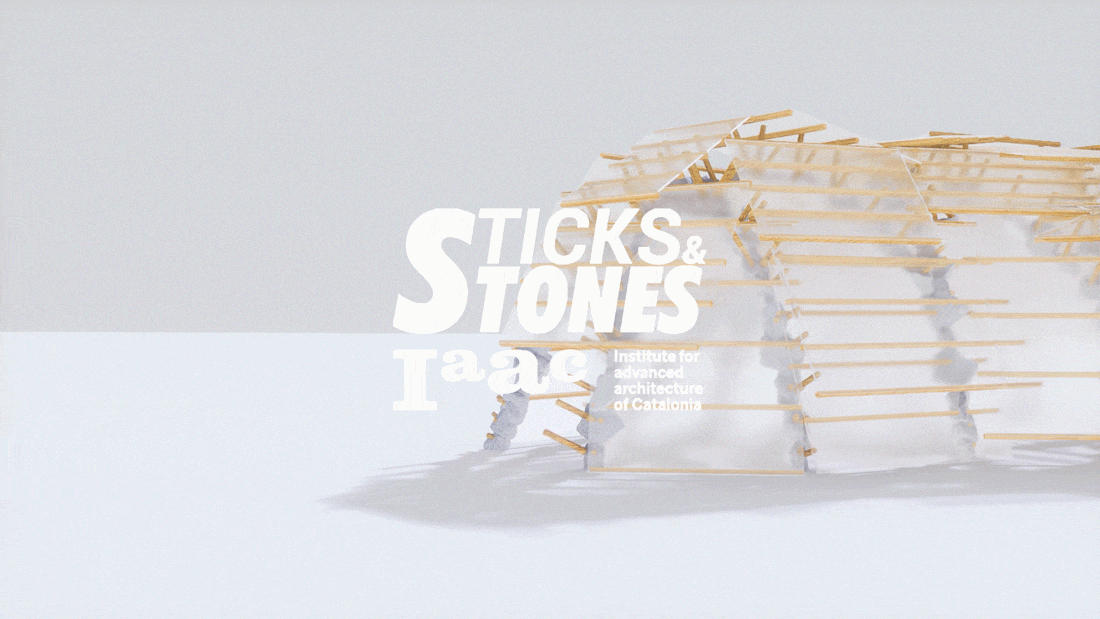