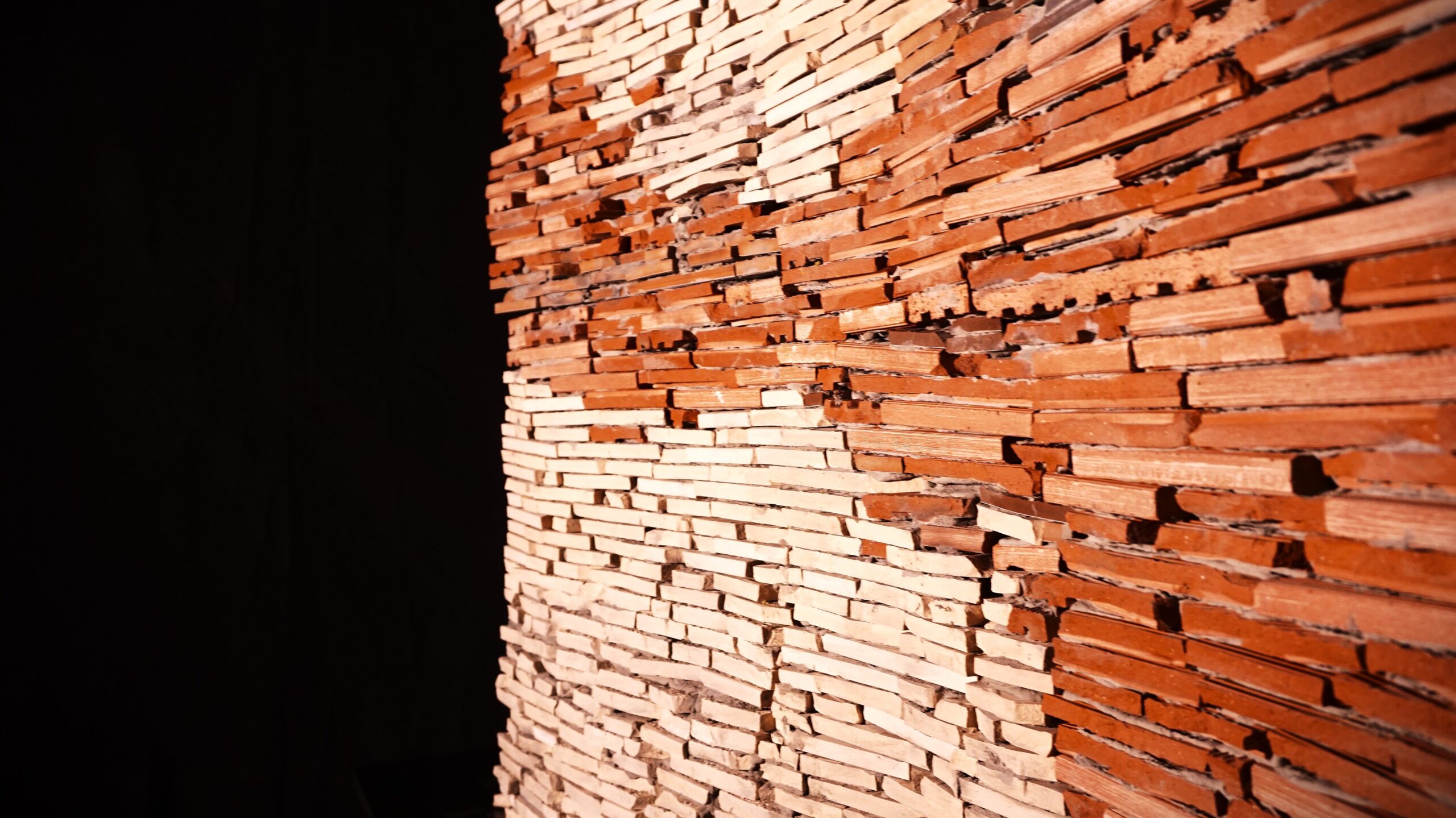
Abstract:
The ReWeave project develops a robotic system to repurpose construction and demolition (C&D) waste into functional, attractive walls, enhancing human-robot collaboration. We created a database by scanning broken tiles to extract shape, size, and color information, then developed custom nesting algorithms to optimize tile arrangement. The workflow includes scanning tiles, exporting outlines via ROS, nesting in Grasshopper, and designing tool paths for robotic pick-and-place and binder applications.
Initial impact printing with clay bullets proved unsuitable due to the brittleness of clay and insufficient pressure. We then tested geopolymer, confirming its reliability for binding tiles. Challenges in 3D printing geopolymer, such as equipment needs and quick setting time, hindered precision. Recognizing the limitations of full automation, we adopted a Human-Robot Collaborative (HRC) approach. Human agents handle quality control, binder application, and real- time adjustments based on projected tile arrangements and depth camera feedback.
This refined workflow integrates automated scanning, nesting, and pick-and- place processes with human oversight for binder application and quality assurance. The collaborative approach combines automation with human ingenuity, ensuring efficient and adaptable construction outcomes using C&D waste.
Context:

Construction and demolition waste (CDW) accounts for around 35% of waste generated in European union, making it the heaviest and most voluminous waste system.
The European Union’s Waste Framework Directive sets a target to achieve an 85% reuse and recycling rate for construction and demolition waste.
Among the construction and demolition wastes, most of them are RANDOM in shape and size, Non MODULAR and UNPREDICTABLE.
Aim:
“To create a robotic fabrication system that repurposes C&D waste into functional, attractive walls, enhancing human-robot collaboration.“
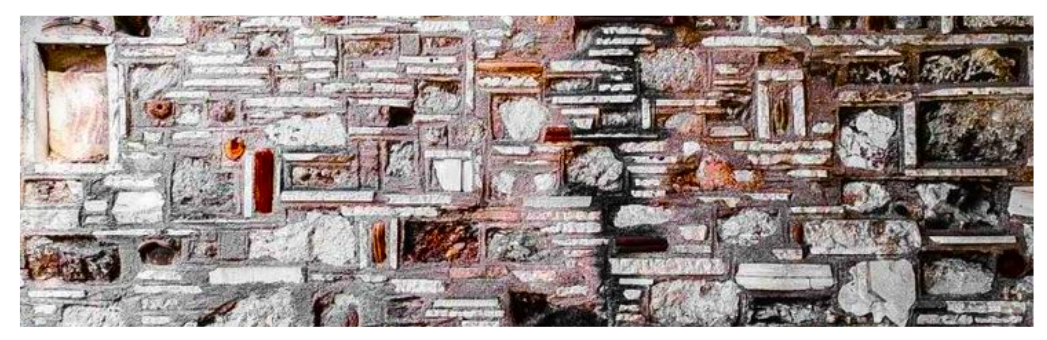
Objectives:
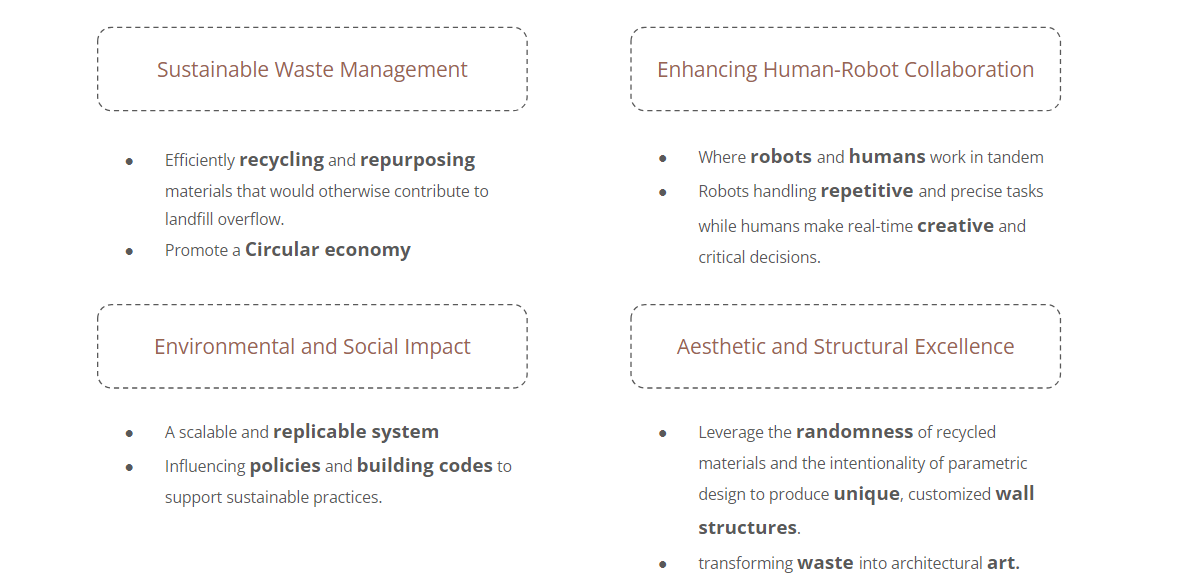
Workflow:
Given the context and purpose, our workflow involves acquiring materials from building demolition sites. Among various waste types, we specifically target planar cementitious waste in this study. Upon sourcing the materials, they go through sorting and segregation based on criteria such as shape, color, or size. In this study, these tasks are outsourced to a third party.
The primary process of the ReWeave system begins with scanning the C&D wastes to extract polylines for nesting using a Packing algorithm. This is done within custom parametrically controlled shapes to generate iterations aligning with desired design parameters.
Once the design and nested patterns are confirmed, the wall will be fabricated robotically using pick n place methods and then binder will be applied to strengthen it.
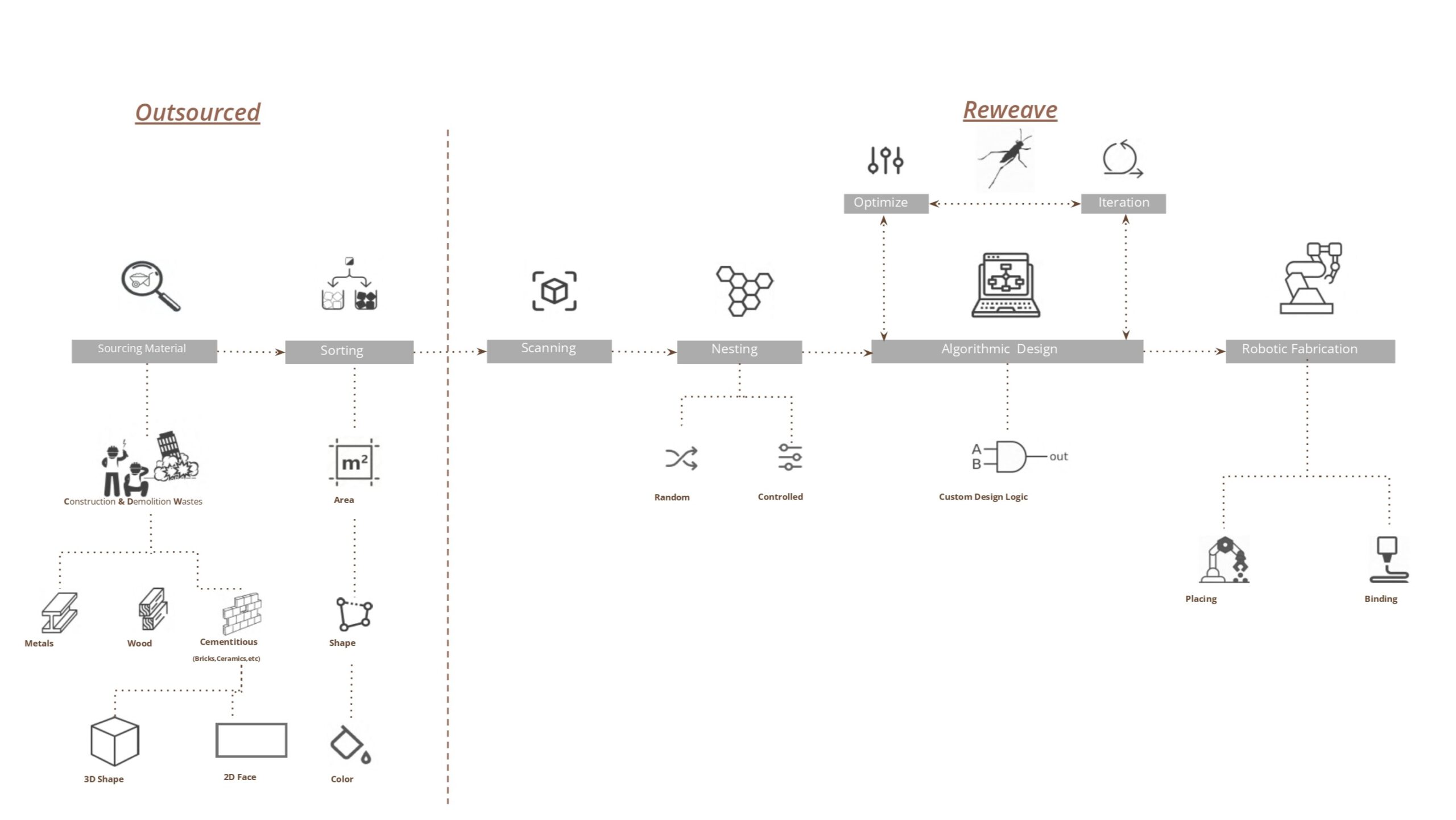
State Of the Art:
1. Design Reference:
In this instance, we found the creative use of various tile types and the playful exploration of different widths and textures of roof tiles to be fascinating.
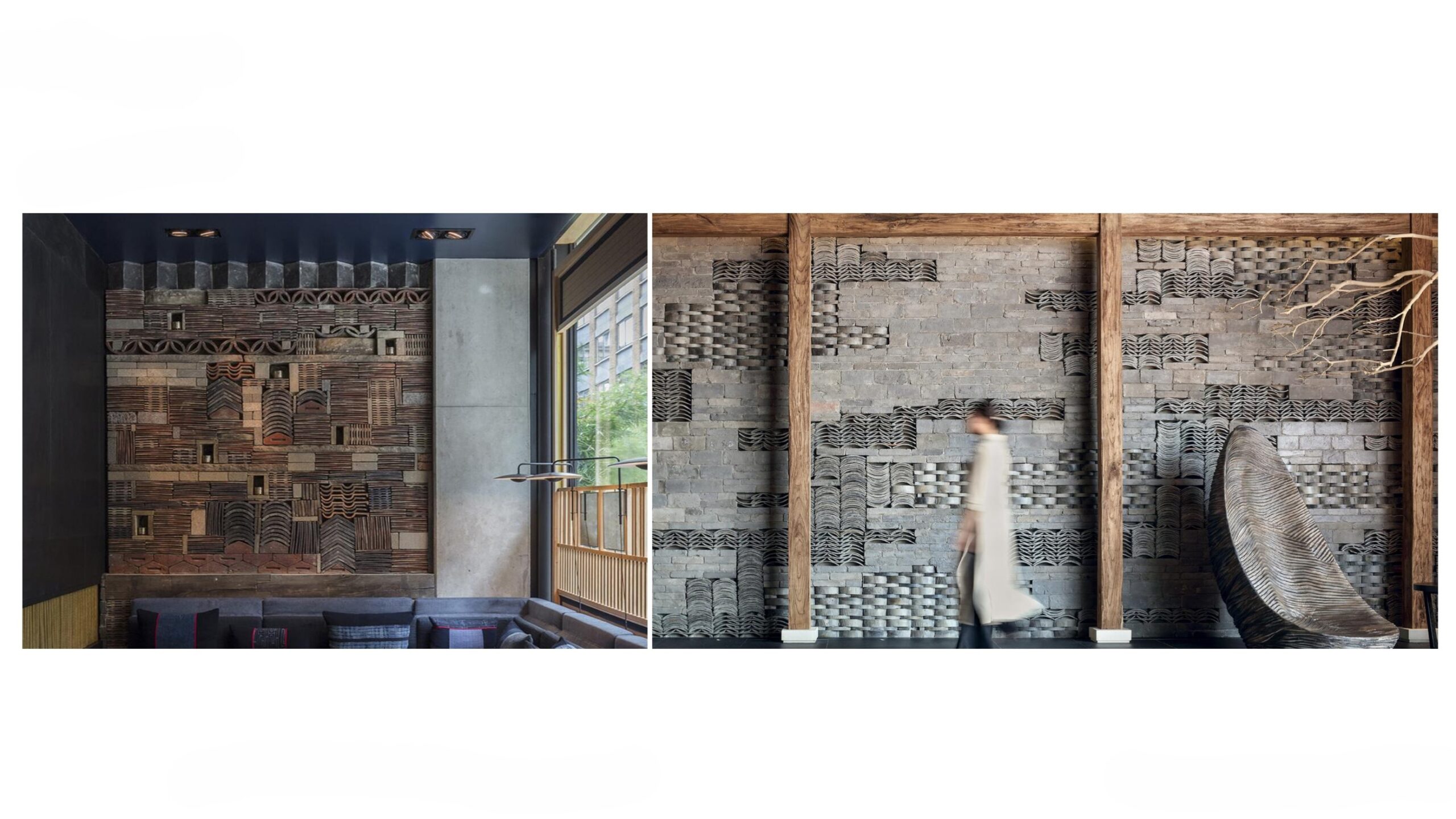
2. Scanning and Nesting references:
Understanding the techniques and appropriate gadgets for the setup within the resources available was a crucial step in our process. Exploring and studying various methods of nesting and conducting in-depth analysis of irregular shape packing algorithms assisted us in gaining a comprehensive understanding of the logic and strategies involved in packing.
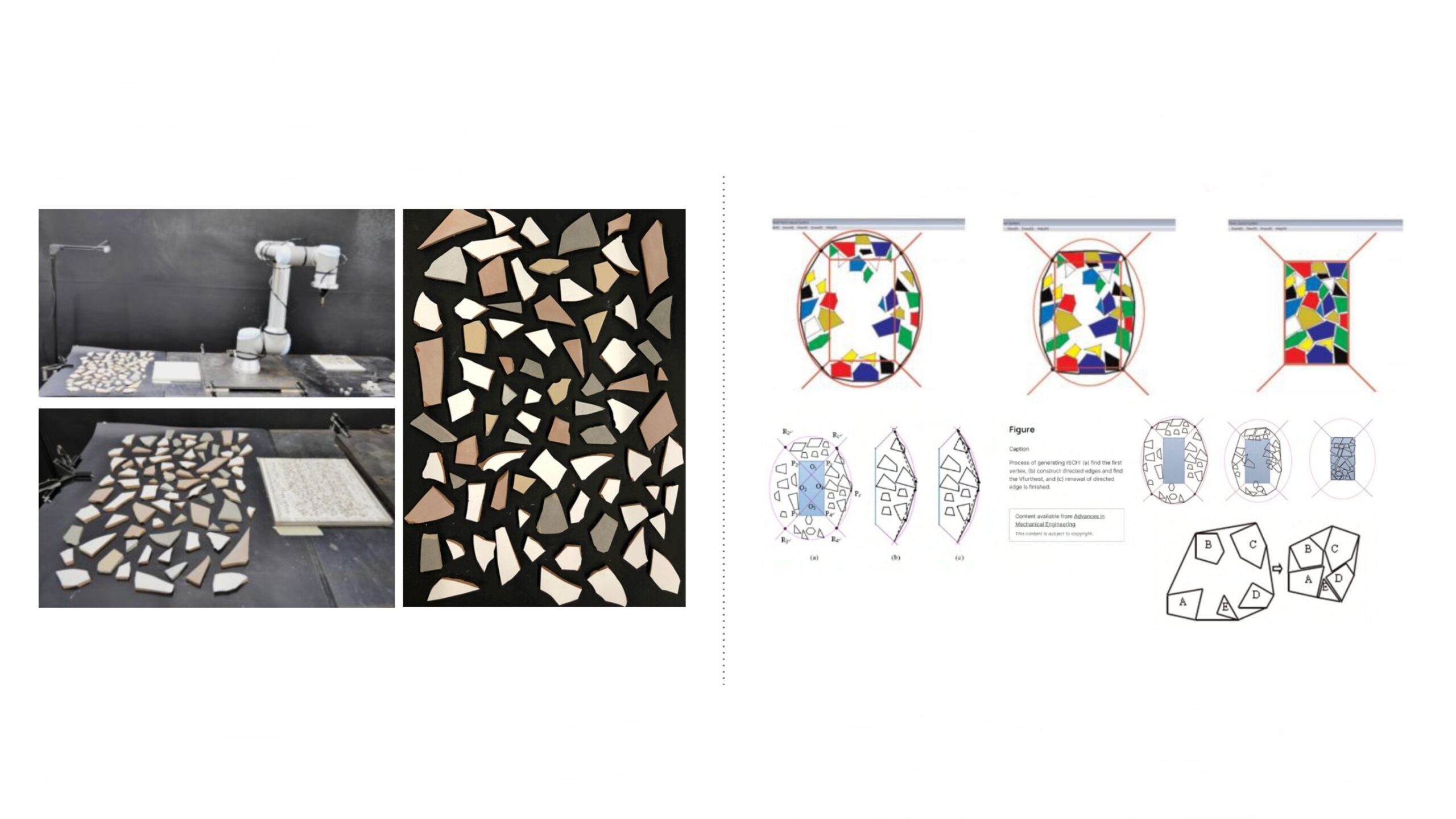
3. Projection Mapping and Depth camera:
To improve gamification and collaboration between humans and robots, you can use projection mapping and depth cameras to project information, implement a feedback system, correct levels, and increase participation.
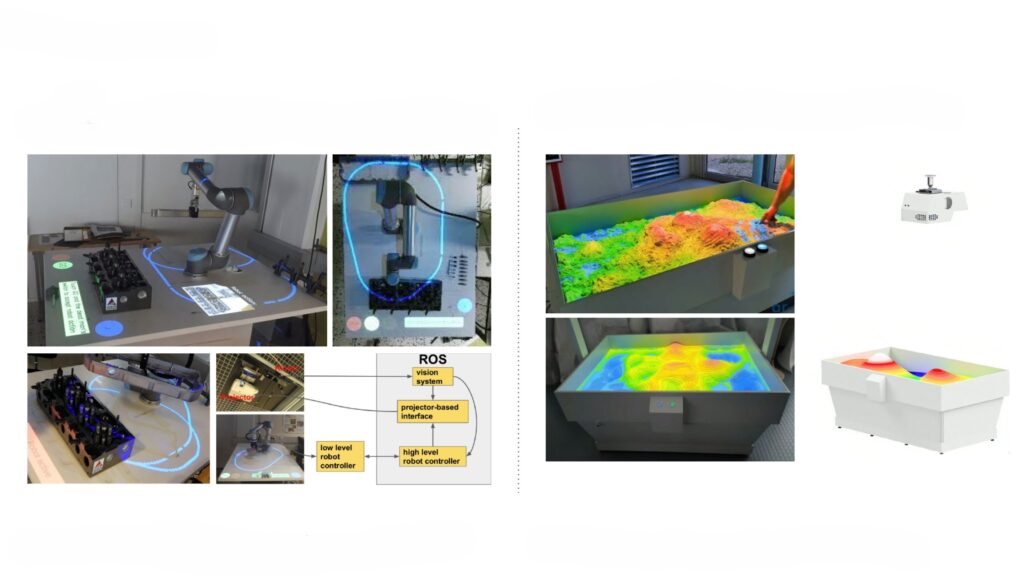
4.Scaling up references:
This project inspired us to dream bigger and consider scaling up. We were particularly impressed by the techniques used to scan and create a digital twin of the blocks, as well as the use of larger cranes for placing bigger blocks for walls. The complexity they managed was truly fascinating to learn.
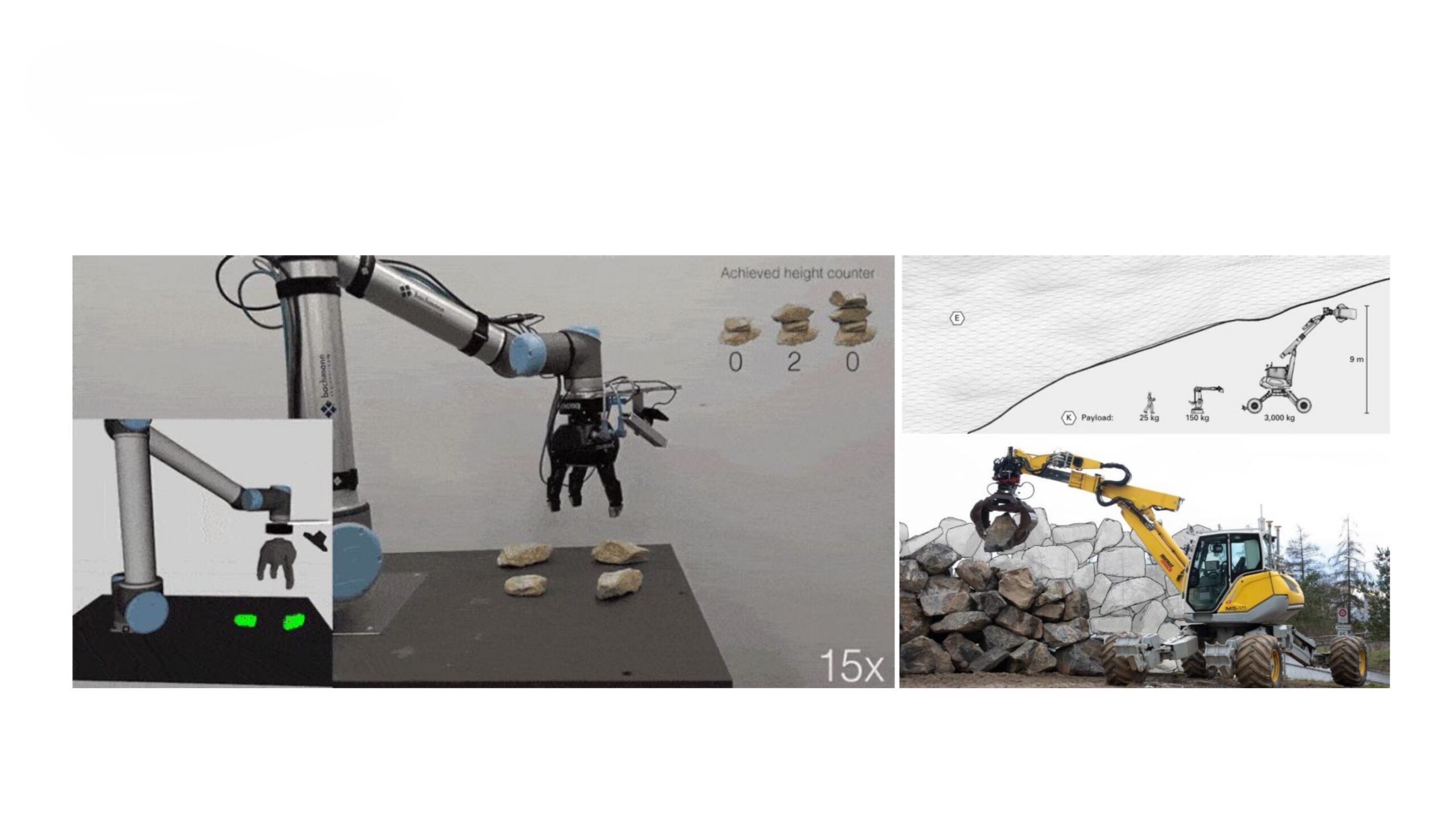
Manual Prototyping:
After careful consideration of all these State-of-the-art references, we conducted some manual experiments to understand the logic and patterns of behavior. Experiments with Geopolymer as a binder gave a clear understanding of the work-ability and behavior.
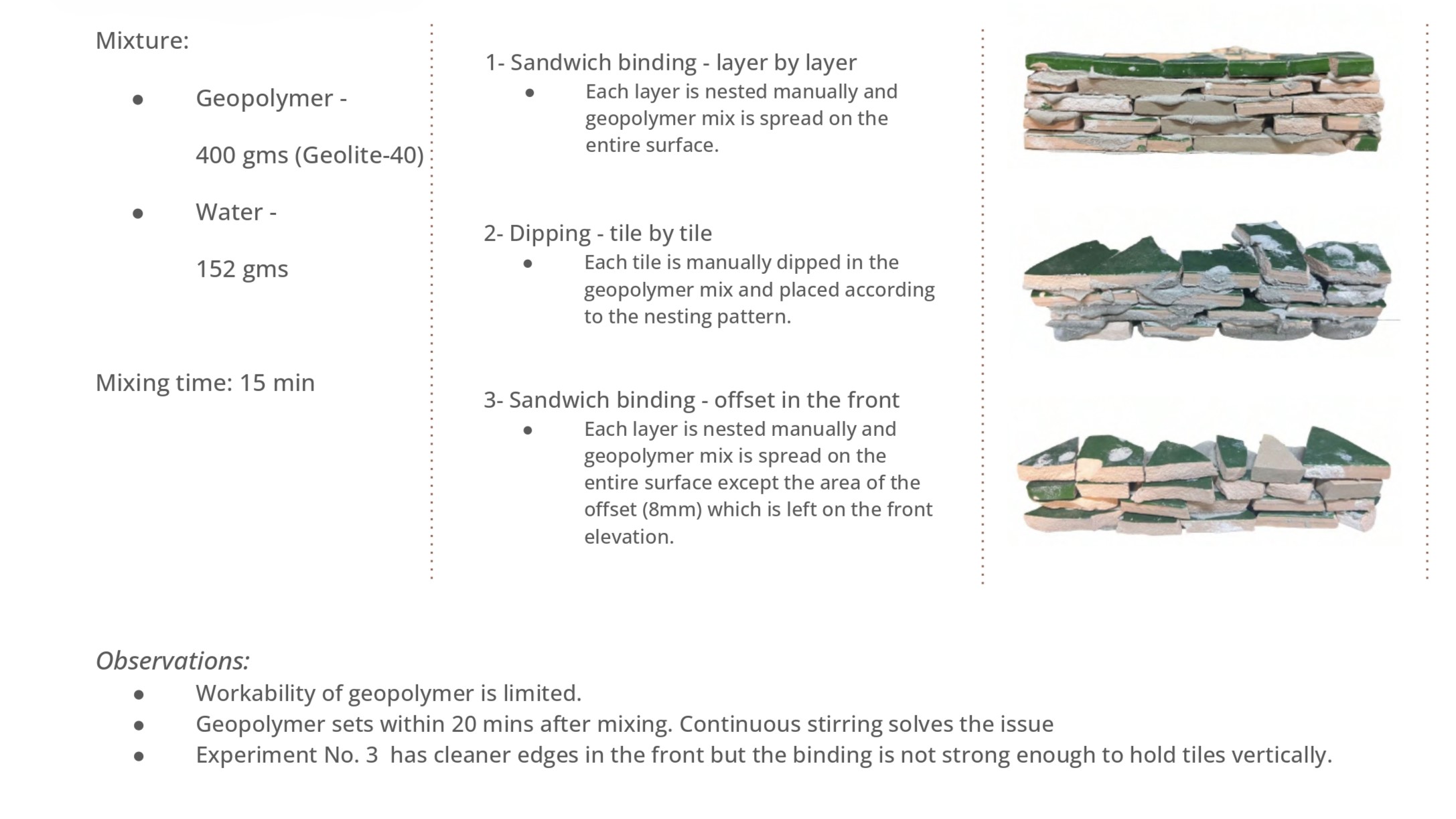
After Geopolymer experiments, numerous explorations of tile stacking based on various logic were tested. Out of these some of them were notable with remarkable observations.
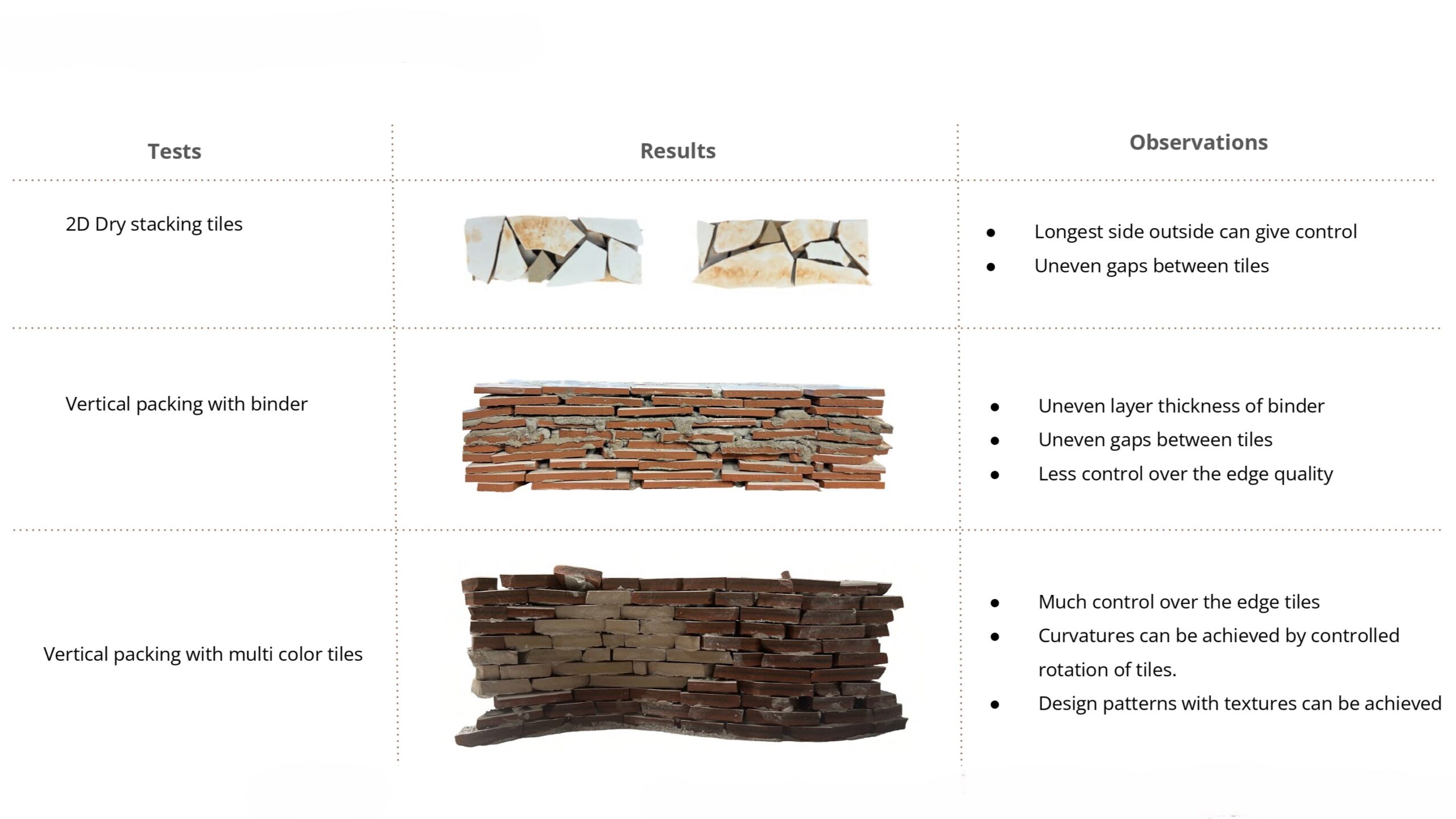
Scanning:
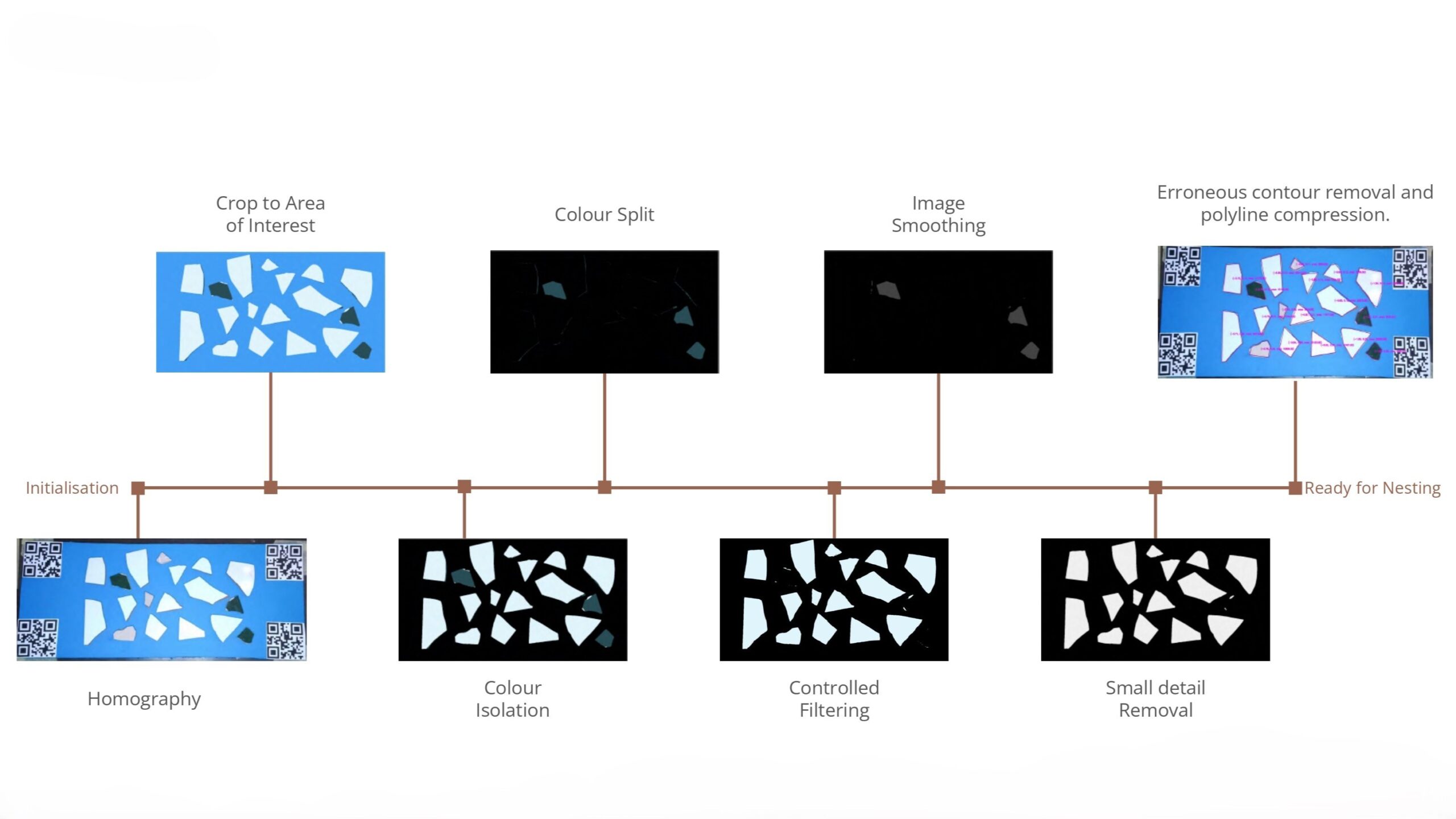
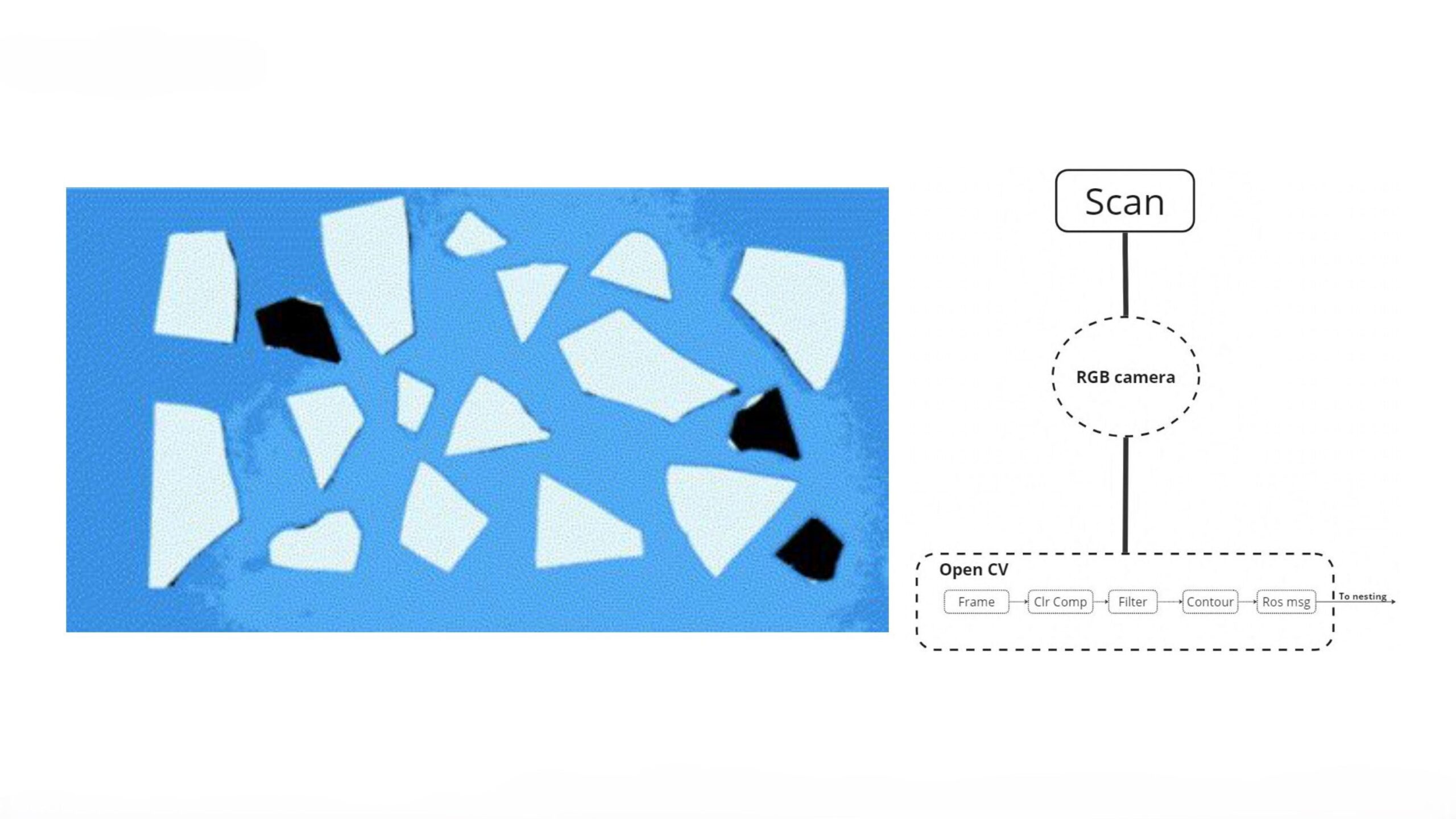
Nesting:
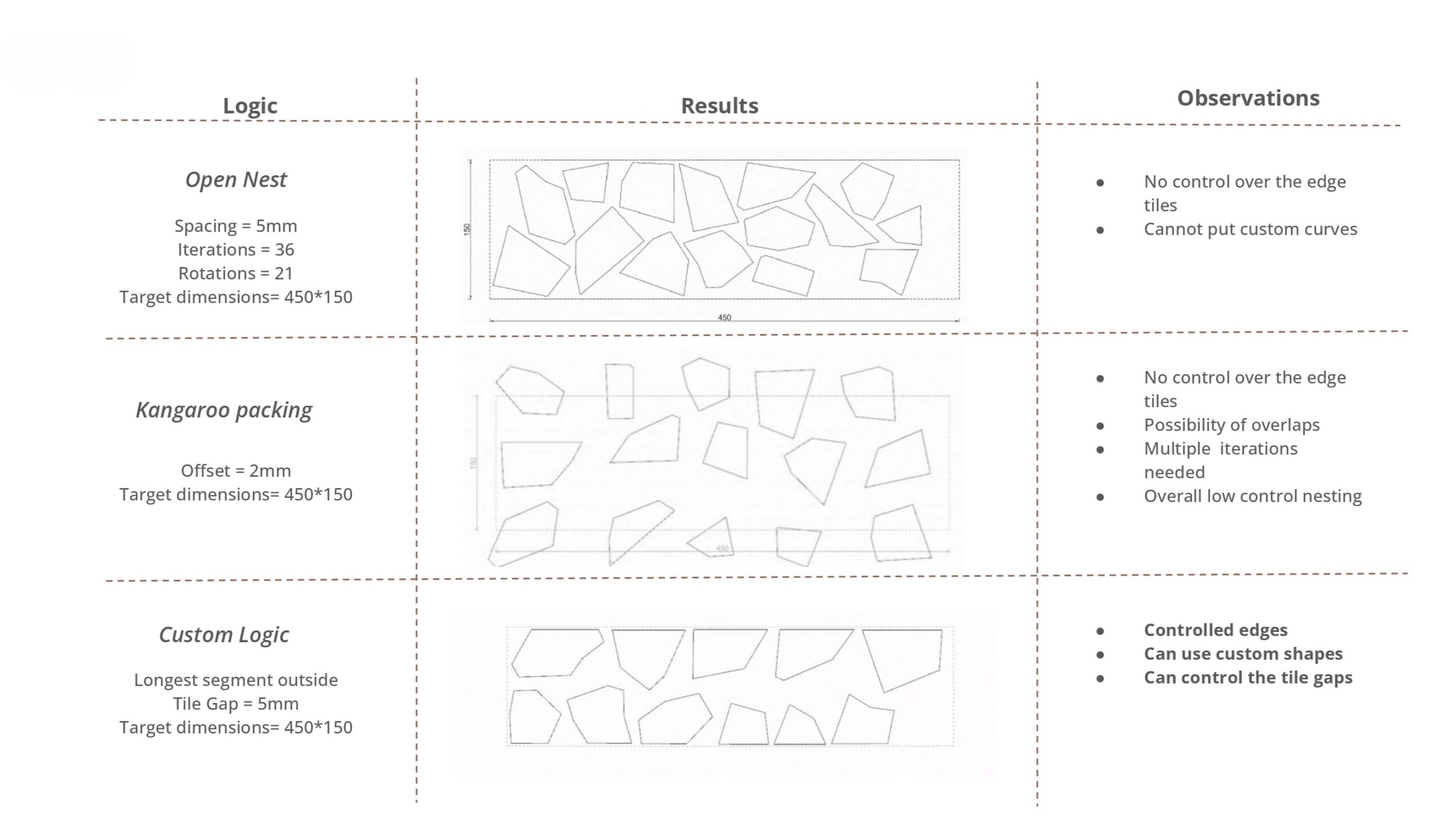
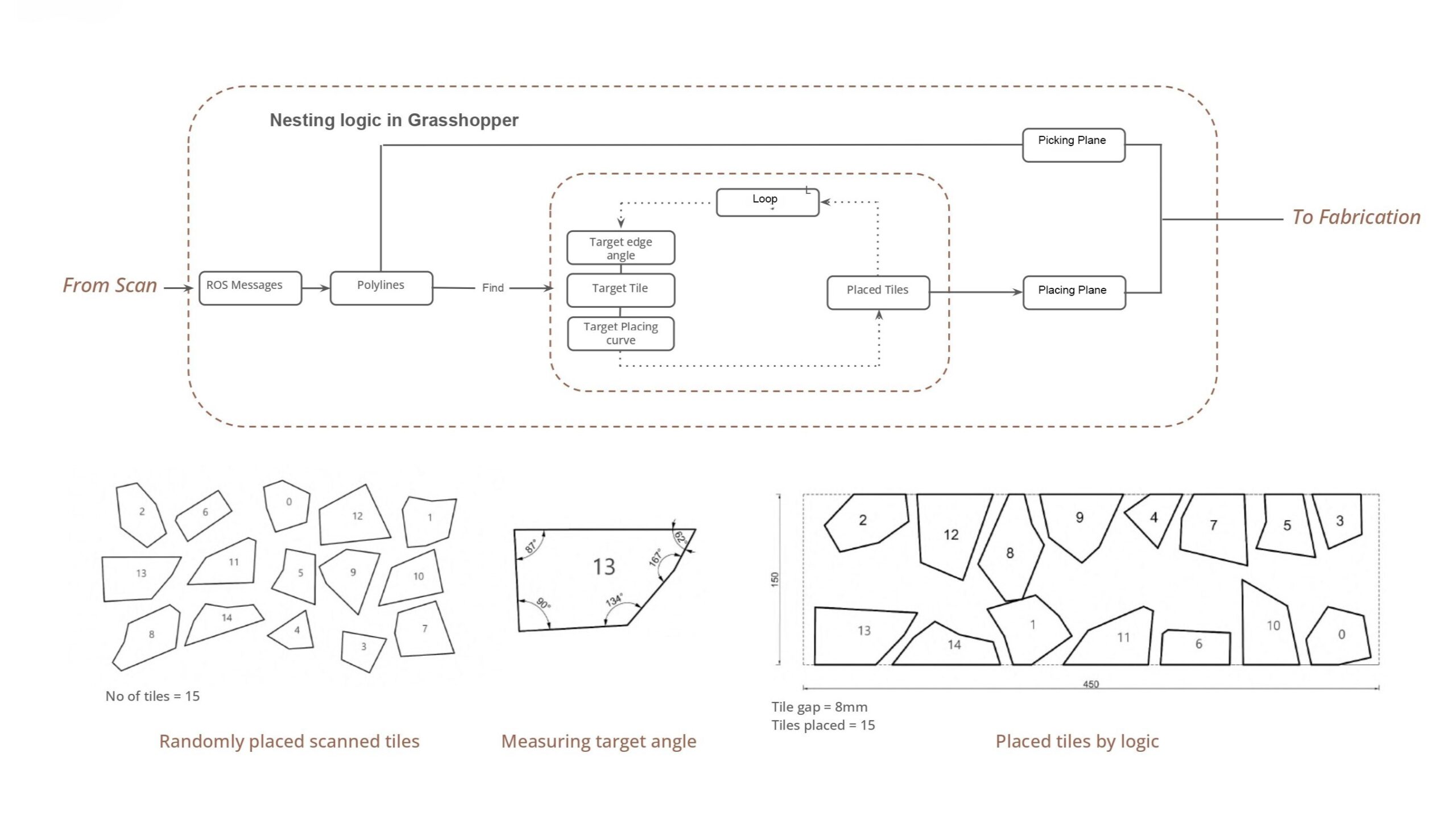
Toolpath Generation:
1. Iteration 01: Dual end effector – Pick n Place and 3d printing
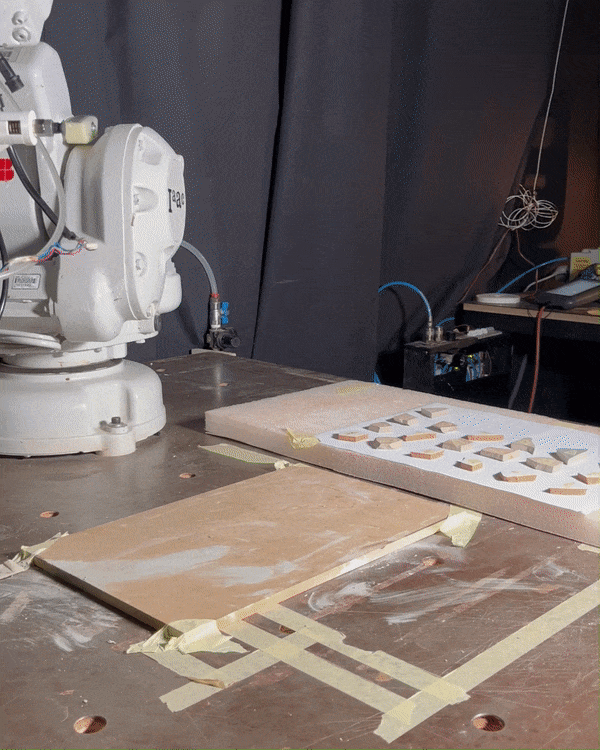
2. Iteration 02: Pump based extrusion – Pick n Place and Fixed station
Depth Analysis and Projection Mapping:
Human – Robot collaboration:
System Architecture:
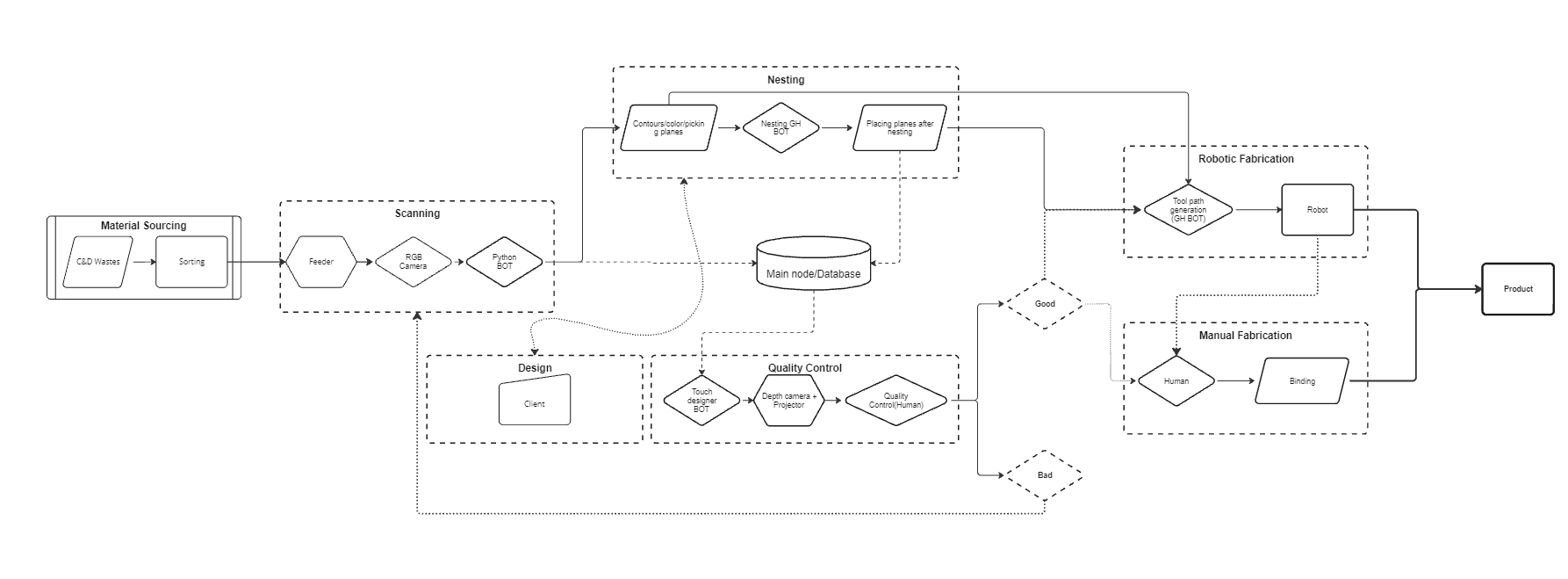
Main Data Node – Error Log:
Robotic Cell:
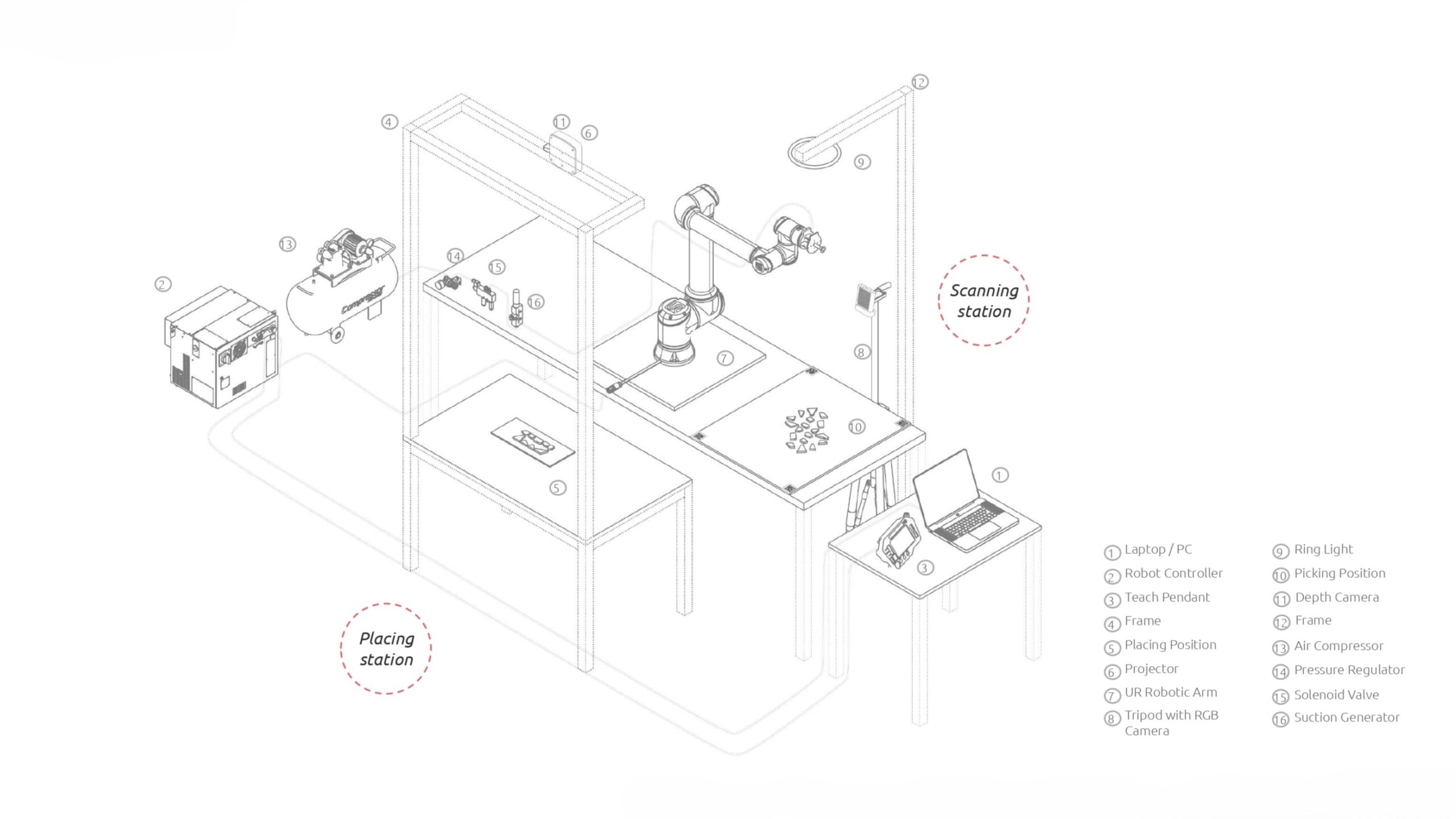
Robotic Cell – Simulation and Fabrication:
Design Iterations:
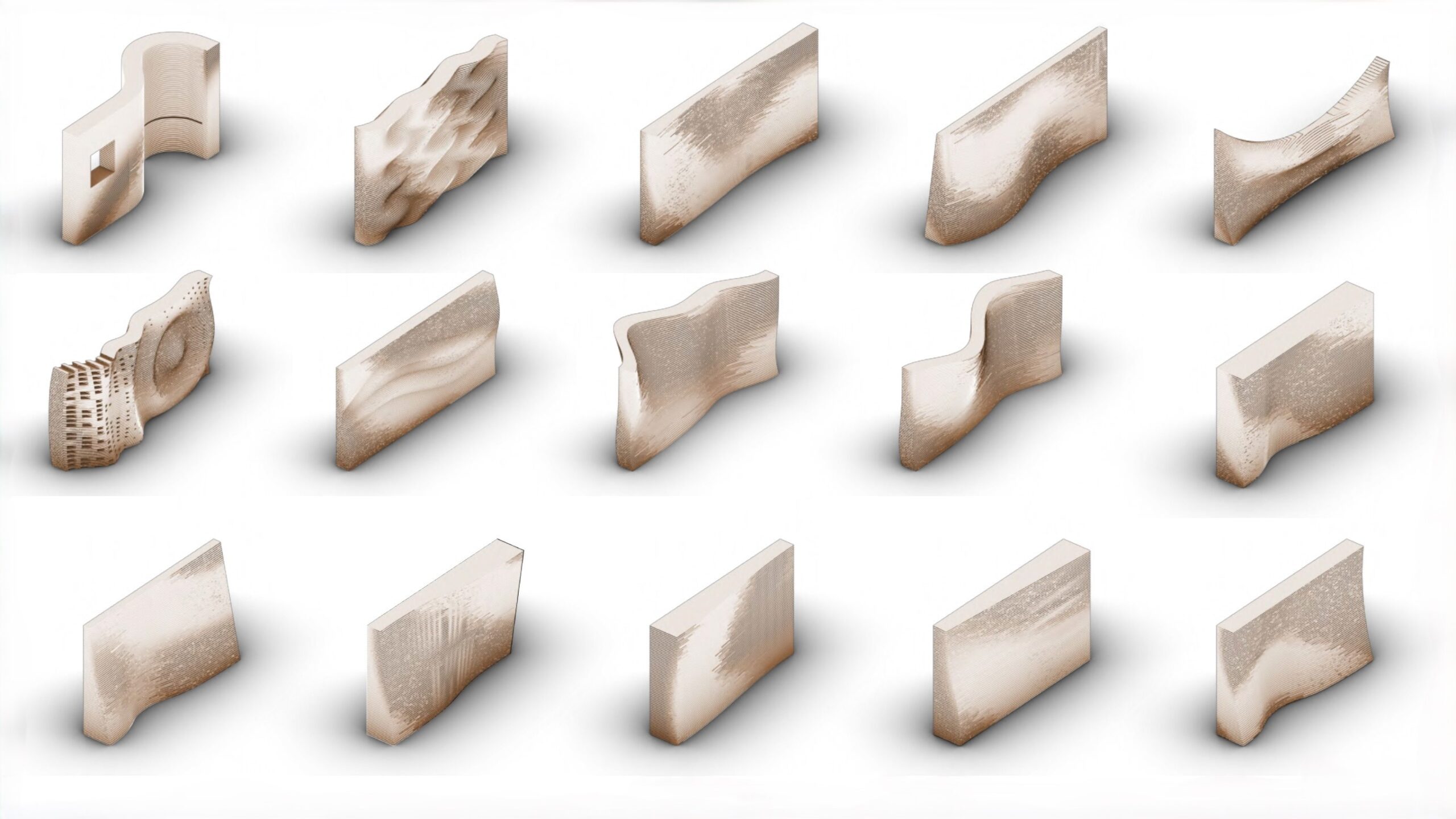
Results – prototypes:
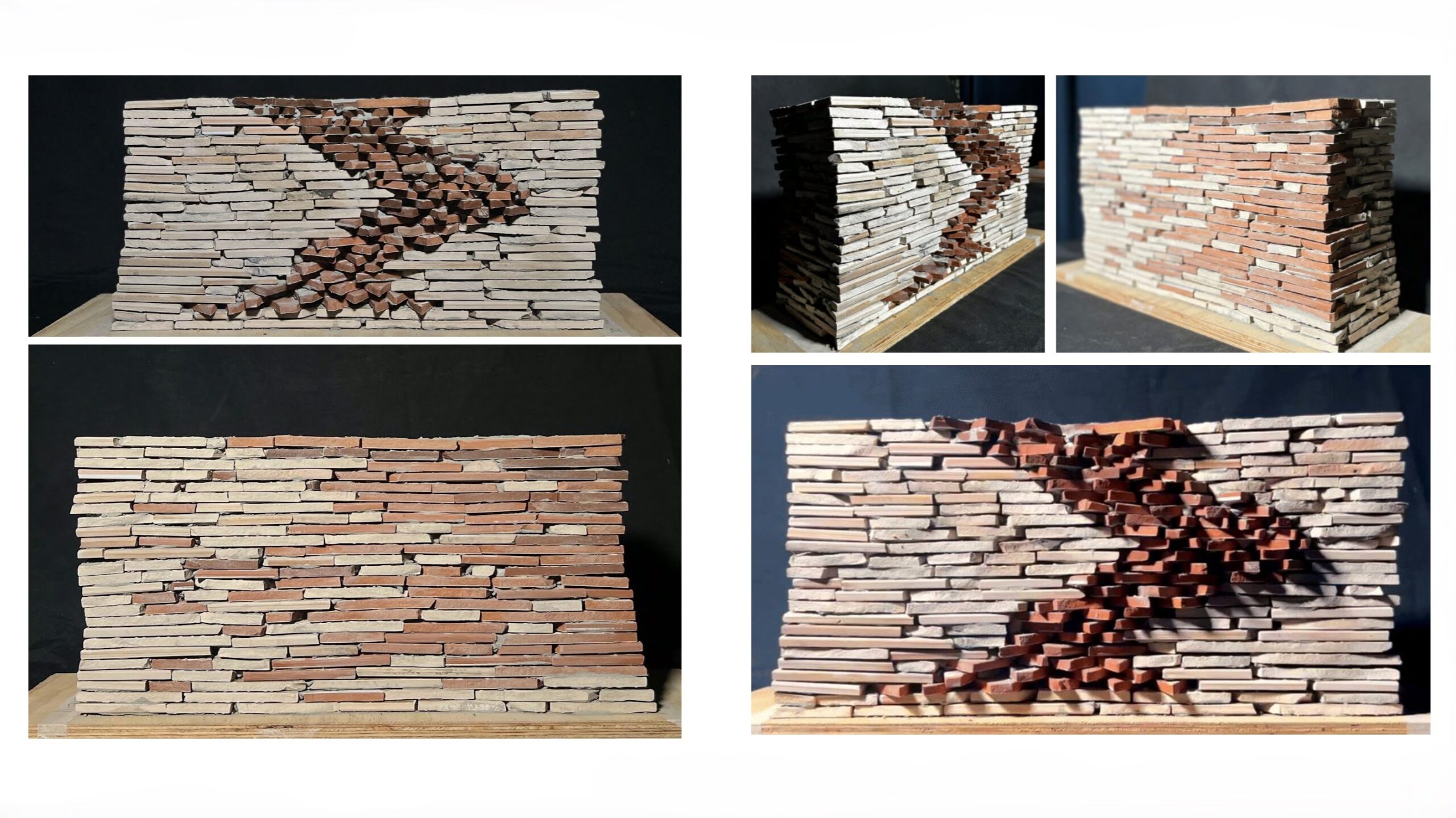
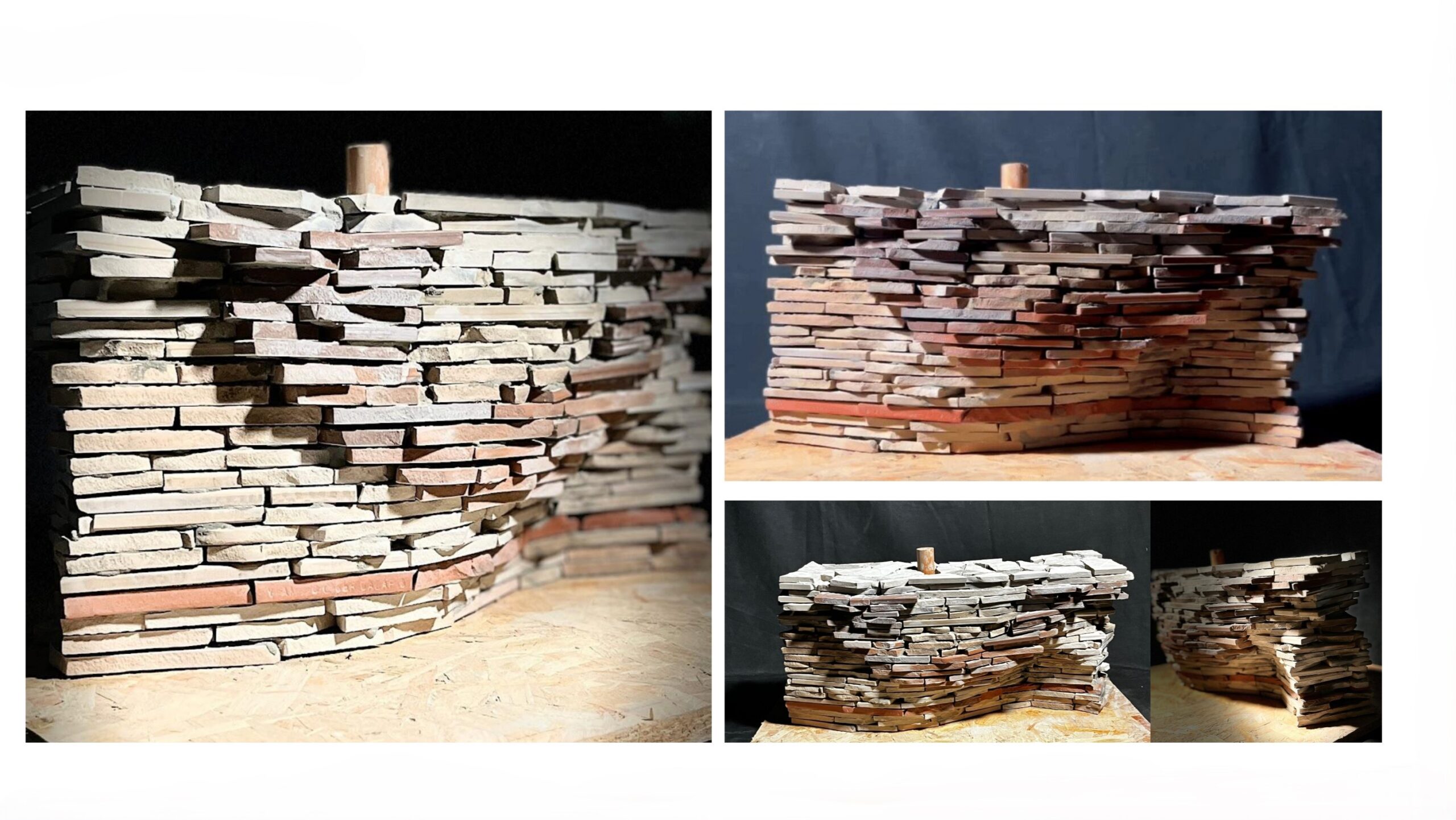
Final Prototype – Design:
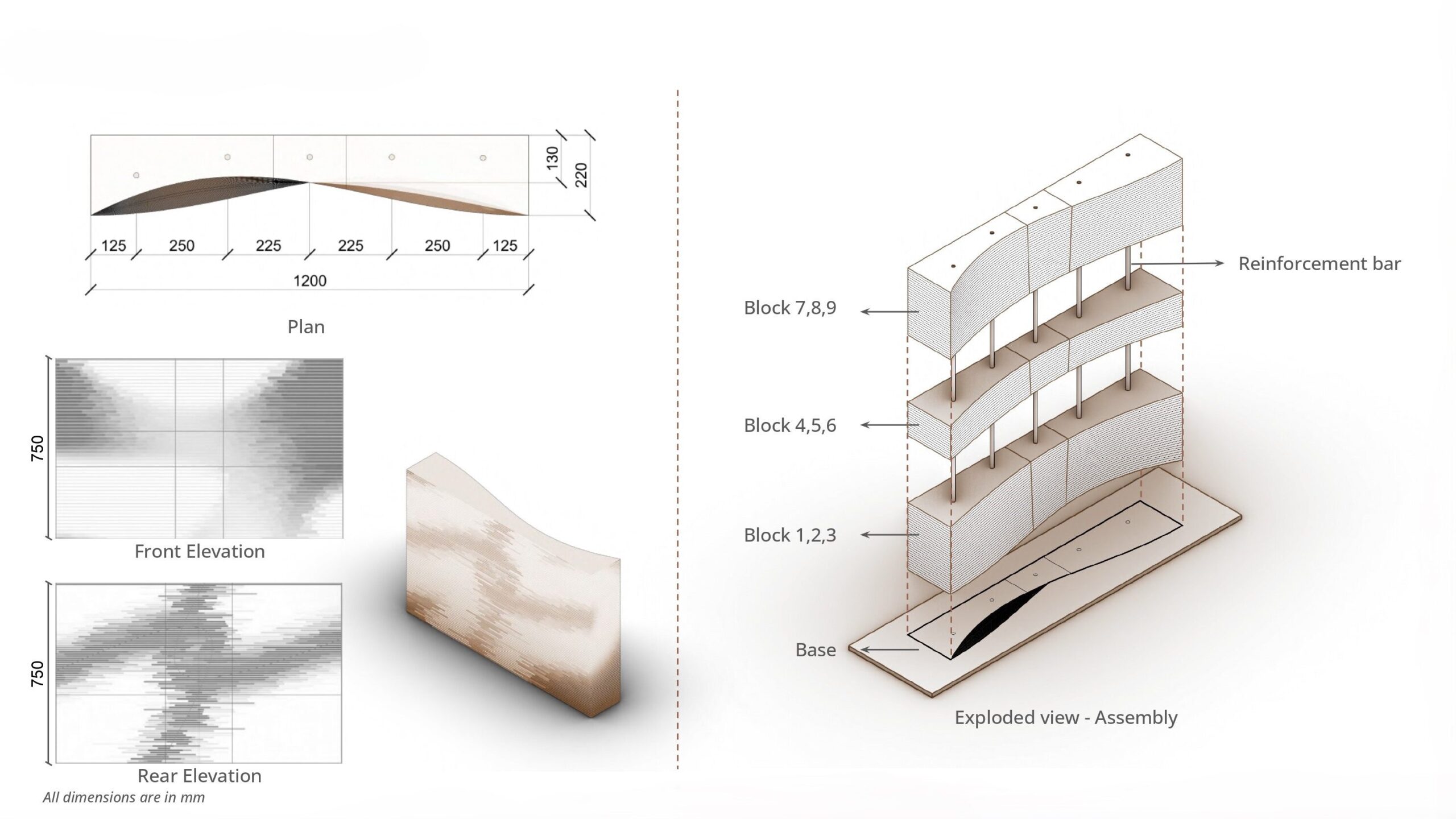
Final Prototype – Human and Robot Collaboration:
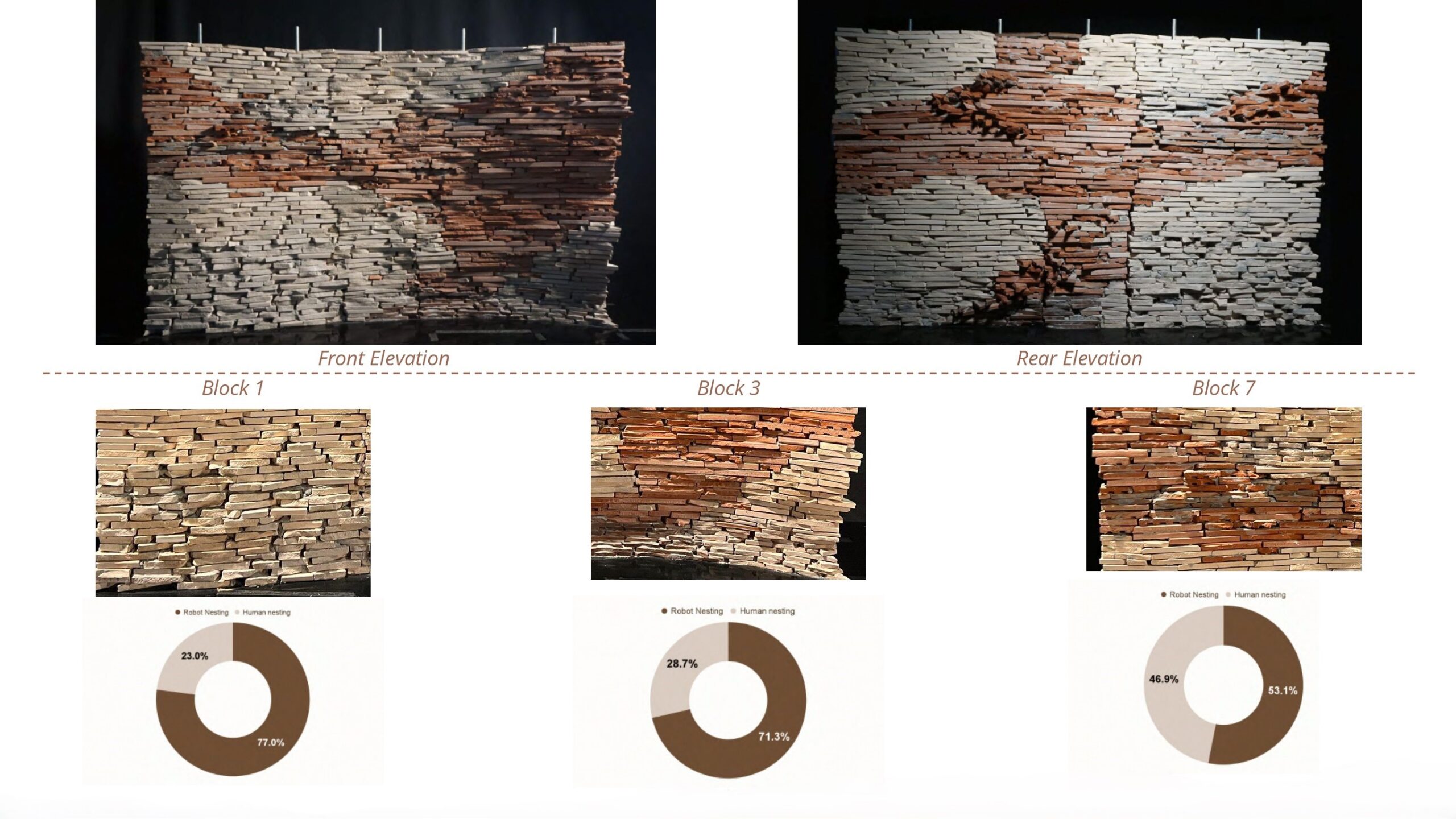
Vision – Prefabrication:
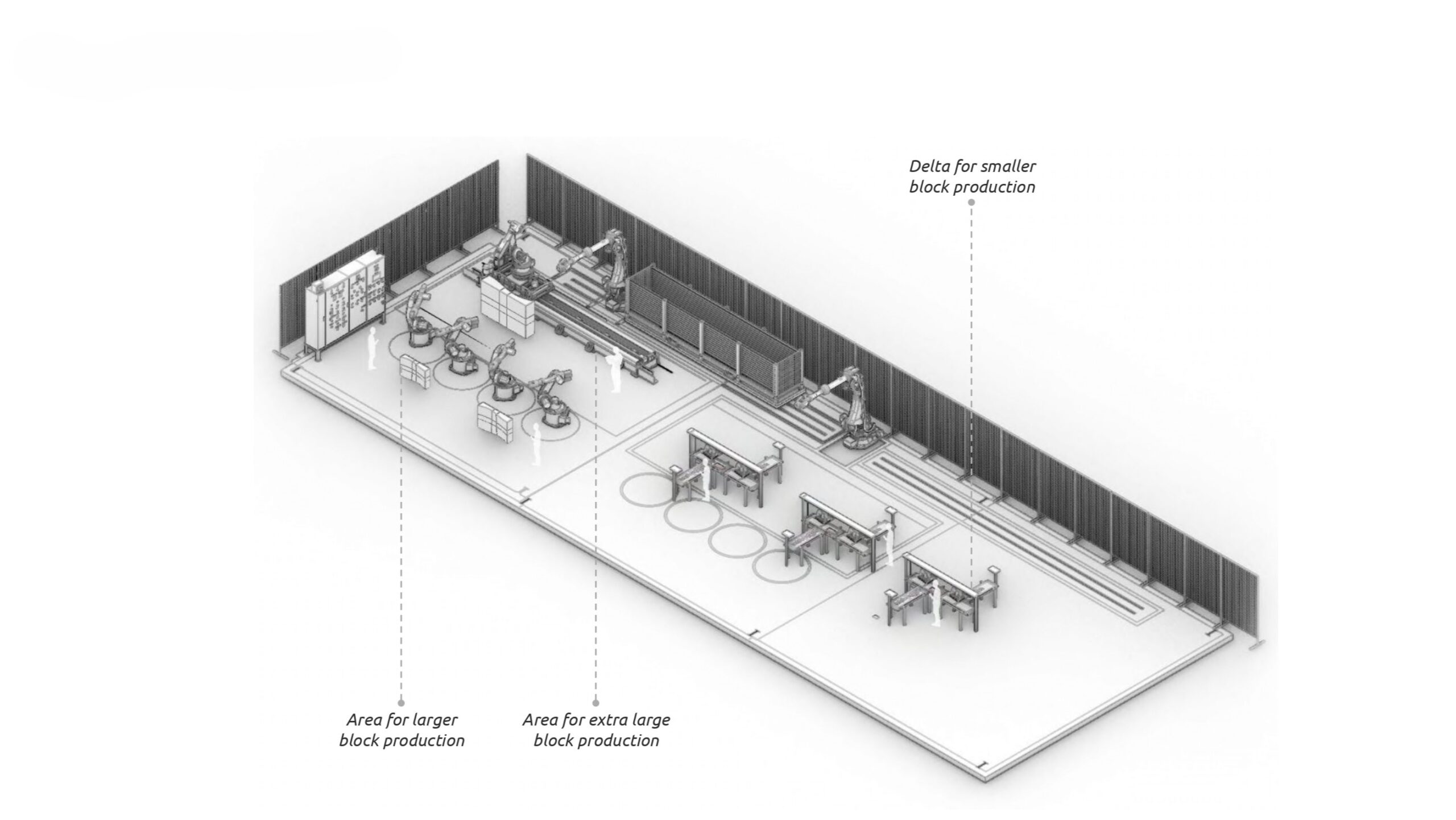
Vision – On-site:
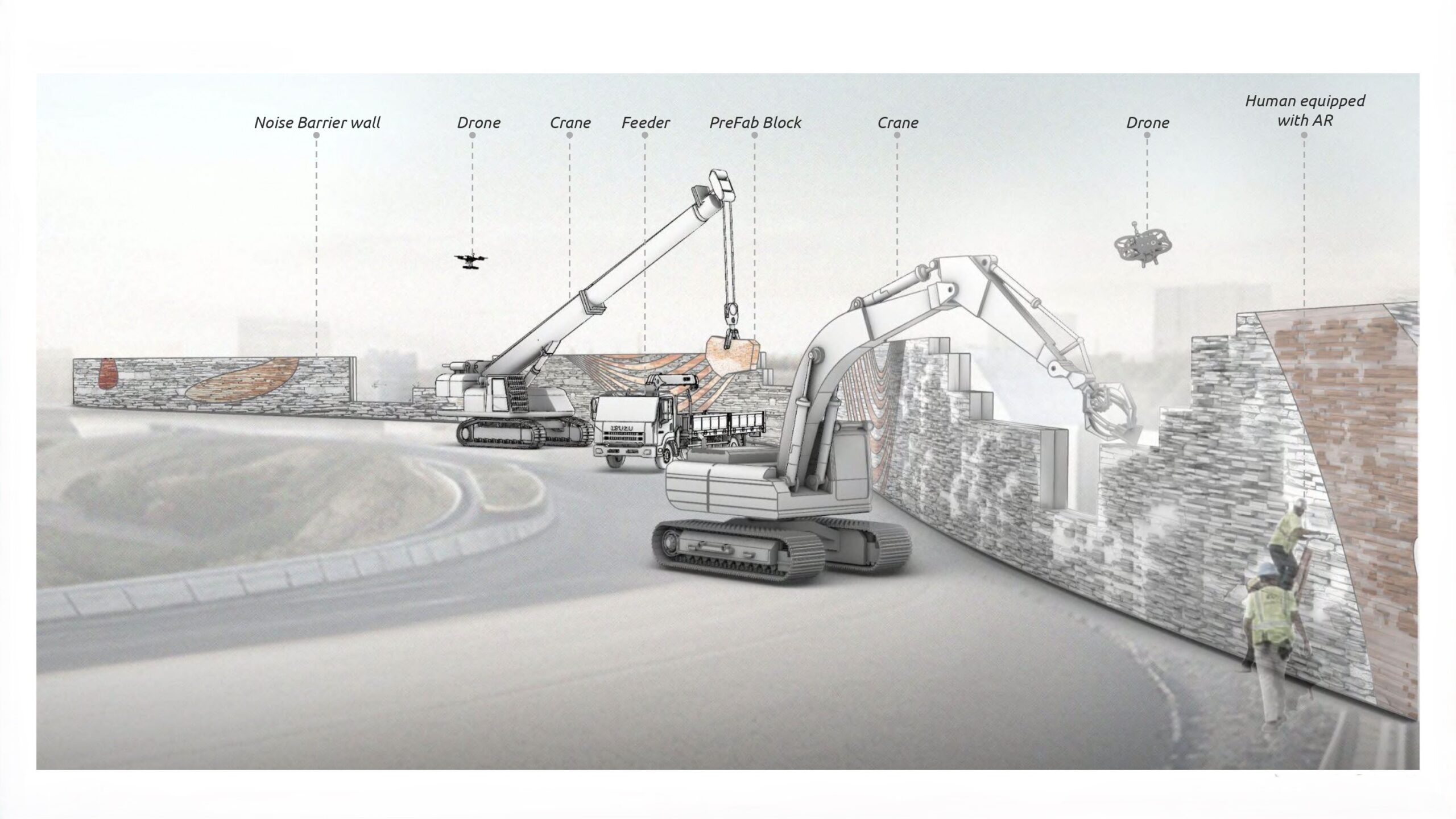
Future Steps:
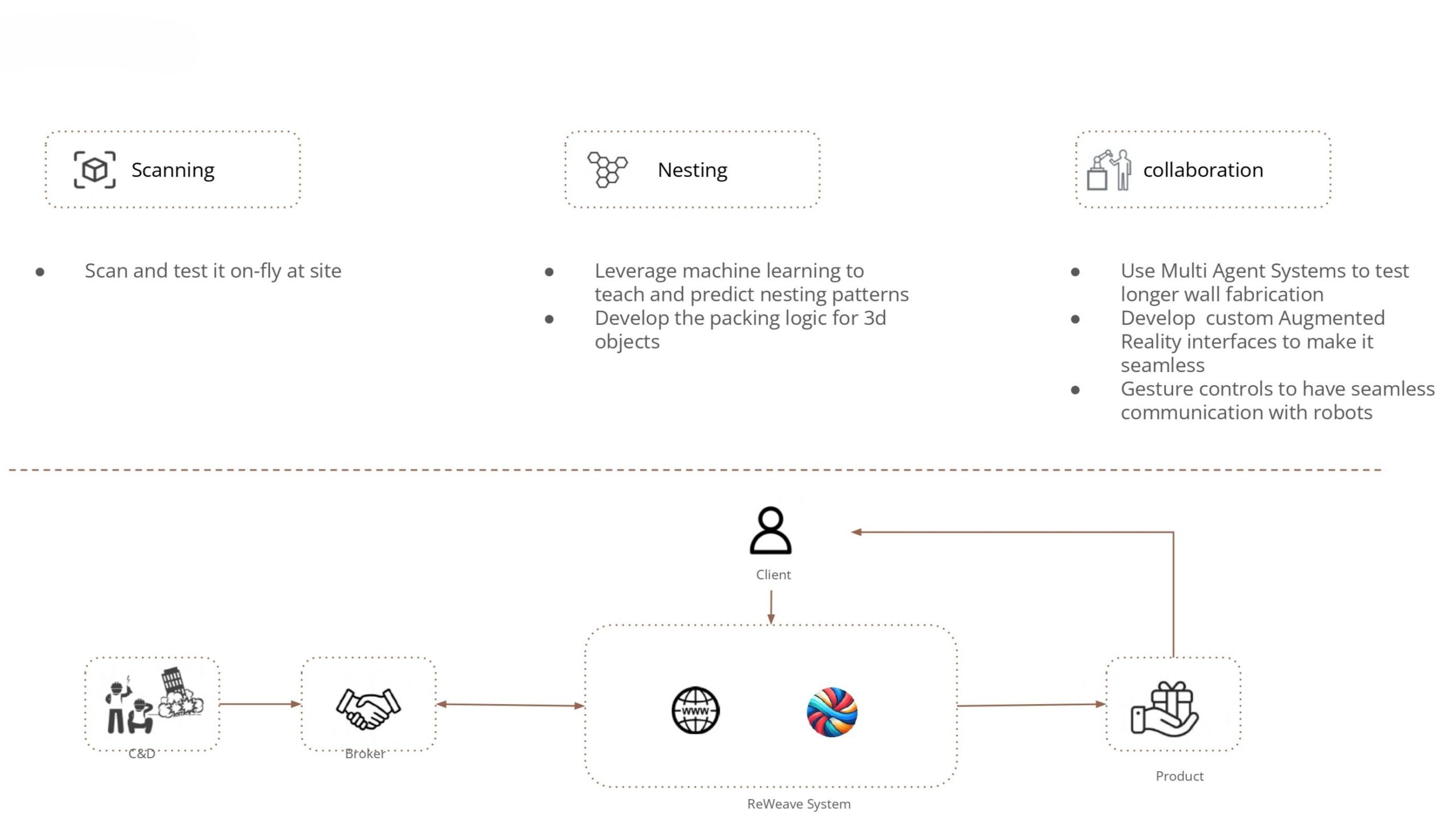
Video:
Credits and Previous Blogposts:
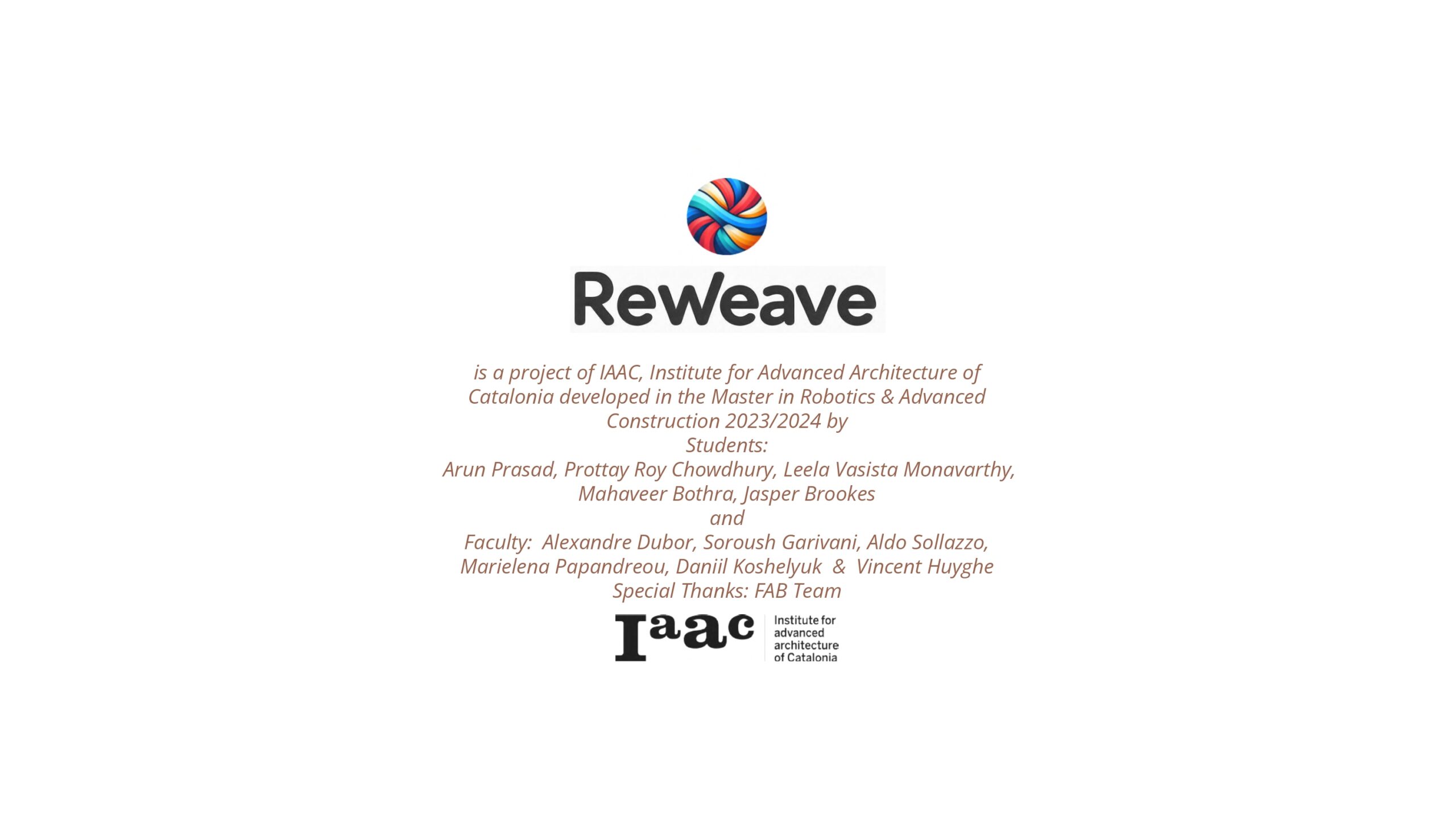